Desain bilah turbin hidroelektrik yang digerakkan oleh komposit
Istilah "pembangkit listrik tenaga air" sering mengingatkan operasi besar yang didorong oleh infrastruktur yang dibangun khusus seperti sistem bendungan dan turbin besar dengan bilah turbin berbasis baling-baling logam tradisional. Namun, banyak daerah yang kehabisan kapasitas baru untuk pembangkit listrik tenaga air yang besar dan berdaya tinggi. Pada saat yang sama, permintaan untuk pembangkit energi terbarukan yang lebih banyak dan berbiaya lebih rendah terus meningkat.
Departemen Energi AS (DOE), dalam laporan “Hydropower Vision” 2018 yang menguraikan keadaan pembangkit listrik tenaga air saat ini di Amerika Serikat dan tujuannya untuk masa depan, memperkirakan bahwa pertumbuhan di pasar pembangkit listrik tenaga air AS — dari 101 gigawatt (GW) kapasitas energi pada tahun 2018 hingga kapasitas potensial hampir 150 GW pada tahun 2050 — akan membutuhkan teknologi canggih baru yang dapat menyediakan lebih banyak energi dengan biaya lebih rendah.
Salah satu solusi potensial adalah pembangkit listrik tenaga air yang lebih kecil yang menangkap energi yang belum dimanfaatkan dari sistem air dengan aliran rendah seperti saluran irigasi dan sungai, menurut Darren Wren, manajer umum di Kinetic NRG (Gold Coast, Australia). Didirikan pada tahun 2016 oleh mendiang pendirinya, Paul Camilleri, Kinetic NRG adalah perusahaan energi terbarukan yang didanai swasta yang berfokus pada pengembangan teknologi pembangkit listrik tenaga air baru untuk menghasilkan listrik yang andal dan berbiaya rendah.
Teknologi pertama perusahaan ini disebut sistem Hydro-kinetic Energy Generator (HEG), yang berdiameter 1,5 meter dengan output hingga 30 kilowatt (kW) dari aliran air 2,0 meter per detik. Output ini menjadikannya sistem tenaga air “mikro” menurut badan klasifikasi seperti DOE AS, yang mendefinisikan sistem mikro sebagai sistem dengan kapasitas hingga 100 kW. Ditujukan untuk penggunaan langsung di sungai, saluran irigasi, atau jalur ekor yang menyalurkan air dari bendungan yang ada, HEG dirancang untuk pembangkit listrik tenaga air low-head — artinya "head", atau jarak antara saluran air dan turbin, kurang dari 20 meter.
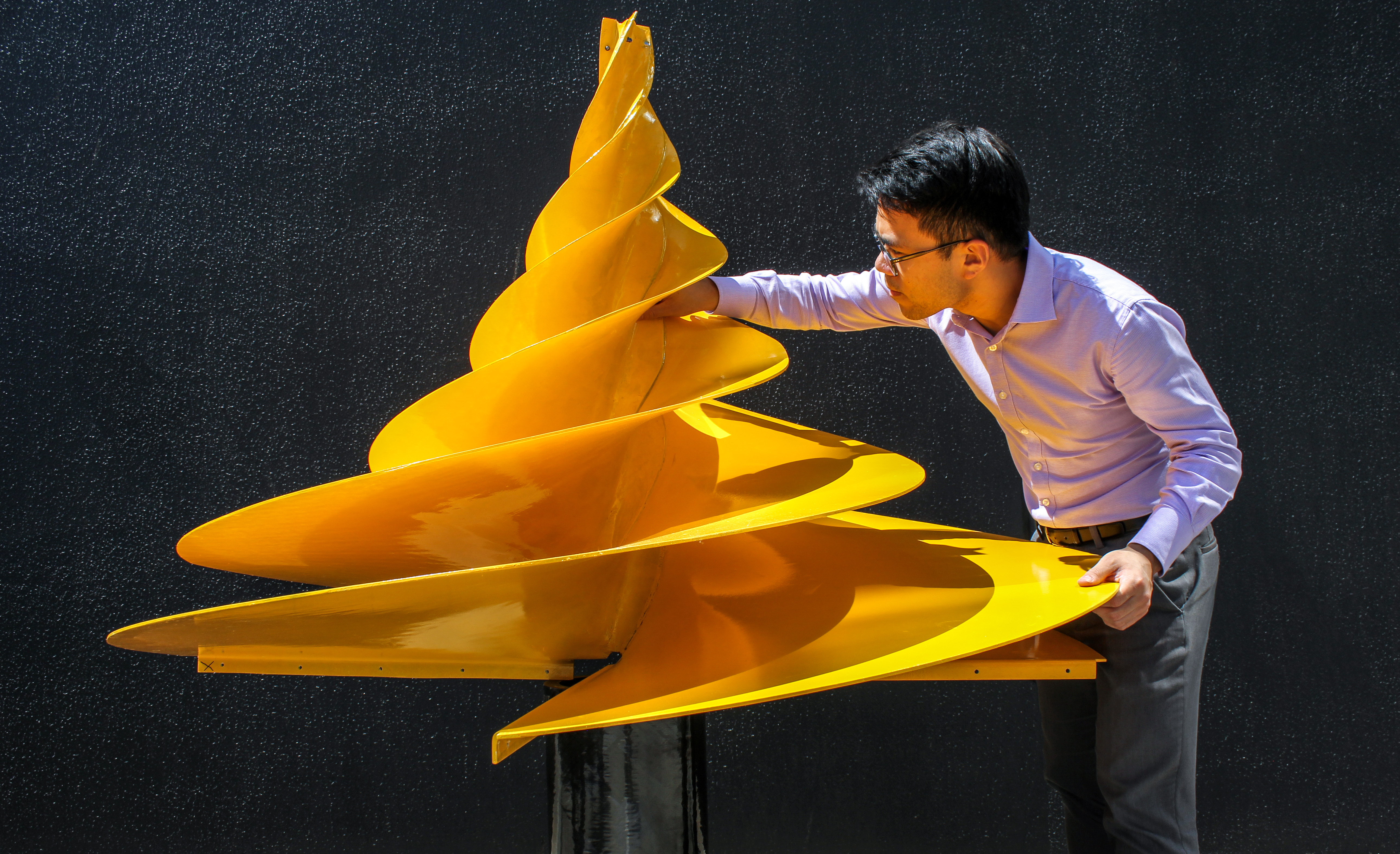
Pengembangan HEG dan bilah turbin spiralnya telah dikerjakan selama sekitar lima tahun, kata Wren. “Ini adalah perjalanan yang cukup melelahkan. Desain yang kami miliki sekarang muncul secara harfiah melalui coba-coba.”
Mendesain blade modular yang dapat diproduksi
Kinetic NRG pertama, model pisau spiral skala kecil dibentuk dari logam, tetapi ketika saatnya tiba untuk memproduksi prototipe skala penuh berdiameter 1,5 meter, “kami benar-benar menemukan bahwa kami tidak dapat membuatnya,” kata Wren. Konsepnya adalah memulai dengan sepotong logam datar dan kemudian membentuk atau menempa satu set spiral yang memancar keluar dari pusat. “Kami tidak dapat menemukan cara untuk mengakses titik-titik tertentu dari bagian tersebut untuk menciptakan kekuatan yang kami butuhkan,” jelasnya.
Perusahaan akhirnya meninggalkan upaya logamnya, tetapi bukan desain itu sendiri. Wren mengatakan Kinetic NRG bermitra dengan universitas lokal untuk mengeksplorasi teknik dan bahan manufaktur alternatif seperti nilon atau keramik, dan mulai berbicara dengan perusahaan percetakan 3D untuk melihat apakah manufaktur aditif bisa menjadi pilihan yang layak. Namun, tidak ada solusi yang memberikan kombinasi yang tepat antara kemampuan manufaktur dan sifat mekanik. Akhirnya, setelah perjalanan tiga tahun, Kinetic NRG diperkenalkan melalui koneksi jaringan suplai ke tim di perusahaan teknik Advanced Composite Structures Australia (ACS-A, Melbourne), yang berspesialisasi dalam desain dan pembuatan volume rendah, bernilai tinggi -menambahkan komponen komposit untuk berbagai pasar akhir.
Wren menyebut apa yang terjadi selanjutnya sebagai "pertemuan pikiran", menjelaskan bahwa Kinetic NRG bekerja dengan Paul Falzon, manajer umum di ACS-A, dan timnya dalam berbagai metode untuk memproduksi dan mendesain bagian menggunakan bahan komposit — bahan yang diketahui ACS-A dari pengalaman akan dapat memberikan persyaratan bentuk, berat, dan kekakuan yang dibutuhkan Kinetic NRG.
Bentuk blade yang inovatif merupakan tantangan desain utama untuk proyek tersebut, dengan persyaratan mekanis untuk blade berdasarkan, menurut Wren, pada standar yang ditetapkan oleh DOE A.S. dan International Electrotechnical Commission. Komponen sistem lainnya — transmisi, manajemen daya, komunikasi, dll. — adalah produk standar yang diketahui memenuhi semua peraturan yang diperlukan.
Menurut Falzon, ACS-A pertama-tama mengevaluasi upaya logam pada desain bilah, dan kemudian menentukan cara mencapai bentuk, toleransi dimensi, dan berat bilah yang diperlukan. Bilahnya juga harus mampu bertahan di lingkungan perairan, dan cukup kaku untuk menopang poros baja turbin tempat bilah itu dipasang. Tim ACS-A memulai dengan desain logam asli dan "merekayasa terbalik" bilah komposit serat kaca agar sesuai dengan kekakuan aslinya, kata Falzon. Namun, beberapa perubahan desain perlu dilakukan saat beralih dari struktur logam yang dilas ke laminasi komposit. Seperti yang dijelaskan Falzon, “Kami mundur selangkah dan bertanya, 'Oke, jika kami akan memanfaatkan sepenuhnya material komposit, seperti apa benda ini?'"
Setelah beberapa iterasi dan diskusi, desain saat ini yang terbentuk terdiri dari empat bilah komposit identik yang saling mengunci untuk membentuk bentuk spiral akhir. “Pisau komposit sebenarnya lebih tebal daripada desain baja, tetapi lebih ringan karena kepadatan material yang kami kerjakan lebih rendah,” kata Falzon. “Menjadi lebih tebal juga berarti kami mendapatkan lebih banyak kekakuan lentur dibandingkan dengan desain baja, jadi Anda sebenarnya mendapatkan produk yang jauh lebih kaku secara keseluruhan.”
Perkakas terbalik
Mengembangkan bentuk untuk perkakas, kata Falzon, adalah bagian proses yang paling menantang. Tim ACS-A mengevaluasi bentuk rakitan blade asli menggunakan perangkat lunak CATIA dari Dassault Systèmes (Waltham, Mass., A.S.). Ini mengarah pada pengembangan permukaan pisau dan desain konsep perkakas. “Ketika Anda melihat bagian-bagian seperti sekarang, mereka sebenarnya dibuat dengan orientasi terbalik. Model bilah harus dibalik untuk membuat perkakas, dan itu aneh sampai Anda melihat perkakas yang sebenarnya ketika tiba. Ini cukup kompleks, ”kata Falzon. Dia menjelaskan bahwa perkakas harus dibalik "untuk memastikan kami dapat mencapai permukaan akhir yang diperlukan di sisi bilah yang terkena aliran air," dan untuk memastikan setiap komponen bilah yang diproduksi dapat dibongkar dalam satu bagian. Perkakasnya juga harus presisi:komponen bilah yang saling mengunci harus dapat sejajar dengan tepat saat dirakit, satu sama lain, dan dengan poros tengah turbin. Untuk prototipe, perkakas, yang dipasok oleh Sykes Australia (Sydney), dibuat dari pasta perkakas murah yang diendapkan ke alas busa dan kemudian dikerjakan dengan mesin CNC hingga bentuk akhir.
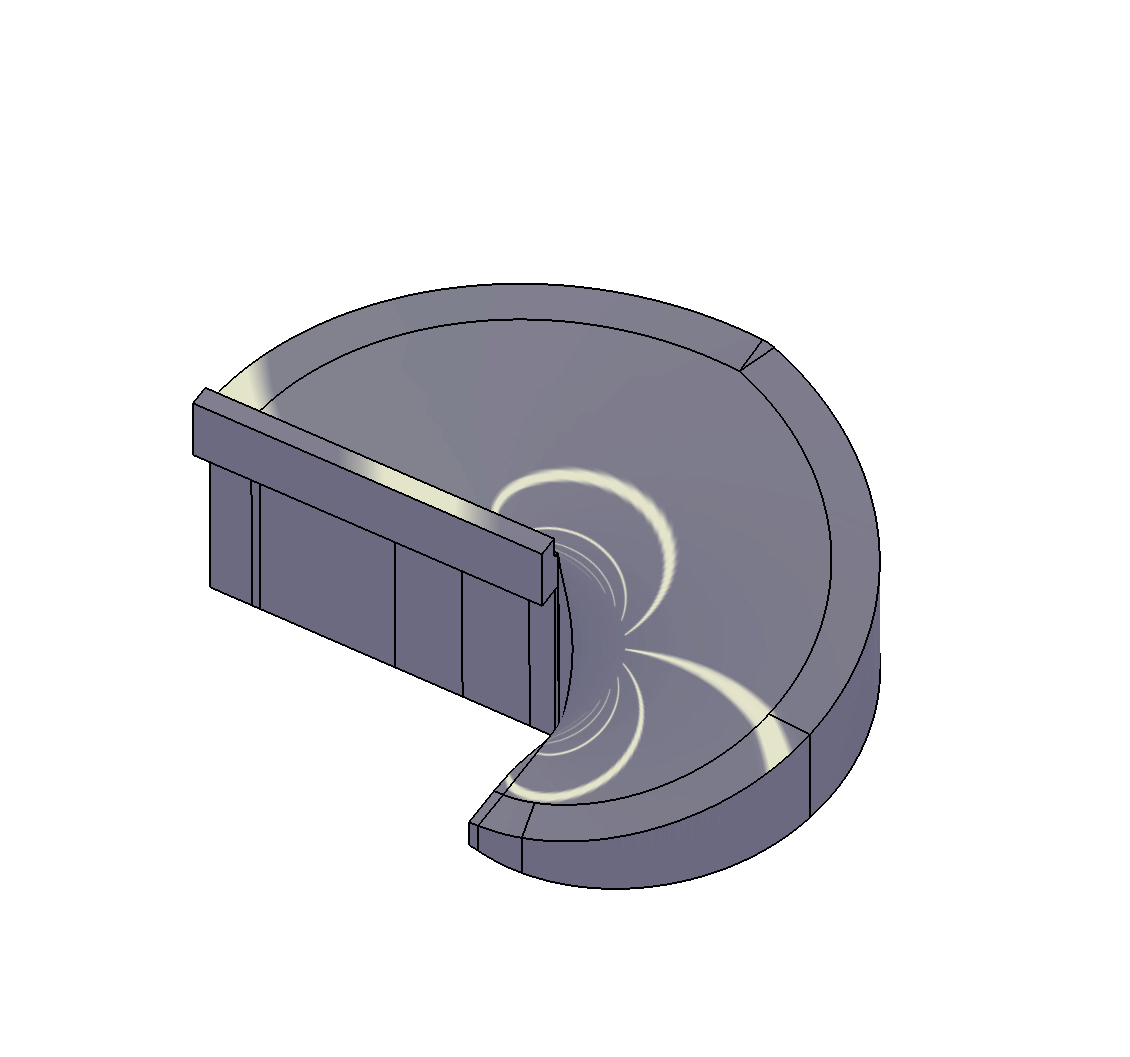
Bagian bawah perkakas sudu turbin.
Setelah perkakas dikembangkan, bilah prototipe skala penuh saat ini dibuat dari serat kaca noncrimp fabric (NCF) dan resin epoksi, diproduksi melalui hand layup dan dikeringkan pada suhu kamar, diikuti dengan pengeringan pasca dalam oven pada suhu tinggi dan aplikasi dari cat kelas laut. Bahan yang dipilih, Falzon mencatat, untuk memenuhi persyaratan struktural dan biaya untuk bagian tersebut. Subkomponen yang saling terkait diikat dengan perekat — dipilih daripada pengikat mekanis untuk kontrol yang lebih baik dan akurasi dimensi dalam perakitan. “Trik sebenarnya,” katanya, “adalah untuk memastikan bahwa bilah dapat saling mengunci, tetapi setelah kami melaminasi semuanya dan mengikatnya bersama-sama, ia membentuk rakitan yang sangat kaku yang mencapai kinerja bentuk struktural dan hidrodinamik yang diperlukan.”
Analisis digital dari kekakuan struktur dan sifat mekanik lainnya dilakukan dengan menggunakan alat dari Perangkat Lunak MSC (Newport Beach, California, AS). “Sistem ini jauh lebih efisien, lebih ringan, dan mampu melakukan lebih banyak pekerjaan daripada desain aslinya,” tambah Falzon.
Berdaya menuju produksi komersial
Menurut Wren, target produksi awal Kinetic NRG akan menjadi 950 unit selama periode tiga tahun, dan kemudian ditingkatkan dari sana menjadi beberapa ribu per tahun. Pelanggan potensial, kata Wren, dapat mencakup individu dan perusahaan swasta, perusahaan listrik dan kotamadya — berbagai macam, yang menggarisbawahi keserbagunaan konsep HEG. Sistem tersebut dapat dipasang sebagai “pembangkit listrik tenaga air mini” di dalam saluran irigasi, atau ditempatkan di hilir dari pembangkit listrik tenaga air yang ada untuk menghasilkan daya dari aliran yang kurang dimanfaatkan, atau sebagai daya tambahan untuk komunitas atau bisnis terpencil, katanya.
Saat ini, prototipe HEG skala penuh sedang menjalani pengujian mekanis dalam air; sementara itu, proses manufaktur skala besar sedang dievaluasi untuk produksi komersial.
ACS-A berharap untuk terus menyempurnakan desain blade, sesuai kebutuhan, bergantung pada hasil pengujian mekanis dan persyaratan untuk pembuatan yang paling hemat biaya. Secara khusus, Falzon mengatakan ACS-A sedang menjajaki proses preforming otomatis “sehingga kita bisa mendapatkan bentuk yang tepat dengan tenaga tangan yang minimal”, diikuti dengan light resin transfer moulding (L-RTM) atau proses berkecepatan lebih tinggi lainnya.
Metode untuk perakitan turbin juga sedang dievaluasi, tujuannya adalah, kata Wren, agar subkomponen blade diproduksi secara modular dan dirakit secara lokal, untuk menghindari biaya dan tantangan dalam pengiriman seluruh unit skala penuh sekaligus menciptakan peluang kerja lokal dan menurunkan biaya pemasangan . Untuk memungkinkan hal ini, ACS-A mungkin perlu memodifikasi cara bilah saling mengunci dan jumlah subkomponen di setiap rakitan juga. “Kami masih akan memiliki bilah penuh dalam bentuk aslinya, itu akan tetap menjadi bagian penting dari itu,” kata Wren, “tetapi kami dapat mengubah tempat transisi terjadi untuk membuat bentuk yang sama dalam komponen yang lebih sedikit agar lebih mudah. perakitan di tempat.”
Kedua perusahaan juga sedang mengevaluasi konversi komponen logam turbin menjadi komposit, untuk mengurangi berat perakitan keseluruhan. “Kami akan menggunakan kaca jika sesuai dan serat karbon jika sesuai, tetapi pada akhirnya, kami perlu mencapai titik harga untuk teknologi agar biaya pembangkitan energi untuk sistem menjadi kompetitif,” kata Falzon.
Saat proses desain dan manufaktur mendekati optimalisasi, tantangan berikutnya, menurut Wren, adalah mengamankan investasi yang tepat dan kemitraan manufaktur untuk meningkatkan volume komersial.