Konsep Dasar Korosi Besi dan Baja
Konsep Dasar Korosi Besi dan Baja
Bahan besi dan baja dalam penggunaan praktis biasanya terkena korosi di lingkungan atmosfer dan air. Korosi adalah kerusakan bahan-bahan ini oleh interaksi kimia dengan lingkungannya. Ini adalah salah satu masalah yang sering dihadapi dalam masyarakat industri saat ini. Sesuai ISO 8044:2010, 'korosi adalah interaksi fisiko-kimiawi antara logam dan lingkungannya, yang mengakibatkan perubahan sifat logam dan yang dapat menyebabkan gangguan fungsional yang signifikan dari logam, lingkungan, atau sistem teknis di mana mereka menjadi bagiannya'.
Ilmu korosi modern dimulai pada awal abad kedua puluh dengan model sel lokal dan model potensi korosi. Kedua model telah bergabung ke dalam teori korosi elektrokimia modern, yang menggambarkan korosi logam sebagai reaksi elektrokimia gabungan yang terdiri dari oksidasi logam anodik dan reduksi oksidan katodik. Teori elektro-kimia dapat diterapkan tidak hanya untuk korosi basah logam pada suhu normal tetapi juga untuk oksidasi kering logam pada suhu tinggi.
Bahan besi dan baja menimbulkan korosi di berbagai lingkungan gas dan air. Korosi besi dan baja yang paling umum terjadi dalam larutan berair dan di udara basah di atmosfer. Secara umum, korosi logam besi dan baja pada tahap awal menghasilkan ion logam yang larut dalam air, dan kemudian, ion logam tersebut berkembang menjadi endapan korosi padat seperti oksida logam dan hidroksida.
Besi dan baja ditemukan di alam sebagai bijih. Proses manufaktur mengubah bijih ini menjadi logam melibatkan input energi. Bahan besi dan baja karenanya dapat dianggap berada dalam keadaan metastabil dan mereka cenderung kehilangan energinya dengan kembali ke senyawa yang kurang lebih mirip dengan keadaan aslinya. Bahan menimbulkan korosi karena secara kimiawi tidak stabil di lingkungan alami - udara, tanah, dan air. Selama reaksi korosi, energi yang ditambahkan dalam manufaktur dilepaskan, dan logam dikembalikan ke keadaan oksidanya. Karena sebagian besar senyawa logam, dan terutama produk korosi, memiliki kekuatan mekanik yang kecil, material baja yang terkorosi parah tidak berguna untuk tujuan aslinya.
Hampir semua reaksi korosi adalah elektro-kimia di alam, di situs anodik di permukaan baja masuk ke dalam larutan sebagai ion besi, ini merupakan reaksi anodik. Saat atom besi mengalami oksidasi menjadi ion, mereka melepaskan elektron yang muatan negatifnya dengan cepat menumpuk di logam dan mencegah reaksi anodik lebih lanjut, atau korosi. Oleh karena itu pembubaran ini hanya berlanjut jika elektron yang dilepaskan dapat melewati suatu tempat pada permukaan logam di mana reaksi katodik dimungkinkan. Di situs katodik elektron bereaksi dengan beberapa komponen elektrolit yang dapat direduksi dan dengan sendirinya dikeluarkan dari logam. Laju reaksi anodik dan katodik harus setara menurut hukum Faraday, ditentukan oleh total aliran elektron dari anoda ke katoda yang disebut 'arus korosi'.
Ada perbedaan antara jenis korosi yang biasanya menggambarkan interaksi antara logam dan lingkungan, dan bentuk korosi yang menggambarkan penampilan fenomenologis.
Reaksi kimia – Ini adalah reaksi korosi kimia khas yang terjadi pada suhu tinggi, di mana logam bereaksi dengan gas panas dan membentuk lapisan oksida.
Reaksi metalo-fisik – Contoh reaksi metalo-fisik adalah penggetasan yang disebabkan oleh hidrogen yang berdifusi ke dalam logam, yang mungkin menyebabkan kegagalan suatu komponen. Embrittlement bisa menjadi hasil dari proses manufaktur yang ceroboh. Hal ini juga dapat dimulai oleh proses korosi (larutan logam) seperti perengkahan yang dibantu oleh hidrogen yang disebabkan oleh korosi.
Reaksi elektrokimia - Ini adalah jenis reaksi korosi yang paling umum. Reaksi tersebut menyiratkan pertukaran listrik melalui elektron dalam logam dan ion dalam elektrolit konduktor, seperti lapisan air pada permukaannya.
Karena arus korosi juga mengalir melalui elektrolit dengan konduksi ionik, konduktivitas elektrolit mempengaruhi cara sel korosi beroperasi. Potongan baja yang terkorosi digambarkan sebagai 'elektroda campuran' karena reaksi anodik dan katodik secara simultan berlangsung di permukaannya. Elektroda campuran adalah sel elektrokimia lengkap pada satu permukaan baja.
Di lingkungan, proses korosi biasanya terjadi dalam larutan berair dan karena itu bersifat elektro-kimia. Empat persyaratan untuk pembentukan sel korosi adalah (i) anoda (korosi), (ii) katoda (terlindung), (iii) elektrolit (biasanya tanah atau air), dan (iv) jalur balik logam (produk baja)
Korosi melibatkan ionisasi atom logam dan hilangnya ion-ion ini ke dalam larutan atau menjadi produk korosi. Karena reaksi ionisasi berarti melepaskan elektron, aliran elektron menjauh dari tempat reaksi ini harus terjadi untuk menghindari penumpukan muatan negatif. Jadi, korosi adalah reaksi elektrokimia. Tempat terjadinya pelepasan logam disebut anoda, atau daerah anodik, dan elektron mengalir melalui logam ke tempat yang disebut katoda, tempat elektron dikonsumsi dalam reaksi katodik.
Reaksi anodik biasanya Fe =Fe2+ + 2e- dan reaksi katodik, dengan adanya air dan oksigen yang cukup, biasanya 2H2O + O2 + 4e- =4OH-. Produk korosi, karat, terbentuk dari Fe2+ + 2OH- =Fe(OH)2.
Mekanisme elektro-kimia yang sebenarnya dapat dihargai jika seseorang mempertimbangkan bagaimana lubang karat terbentuk. Sebuah lubang dimulai pada beberapa ketidakhomogenan di permukaan, seperti partikel pengotor, dan reaksi di atas terjadi. Geometri tipe lubang terbentuk karena reaksi anodik terus terjadi di bawah lapisan karat. Gambar 1 menunjukkan mekanisme korosi.
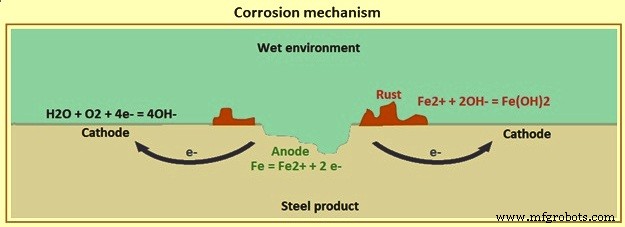
Gbr1 Mekanisme korosi
Konsekuensi dari korosi sangat banyak dan beragam dan efeknya pada operasi peralatan atau struktur yang aman, andal dan efisien seringkali lebih serius daripada kehilangan massa logam yang sederhana. Berbagai macam kegagalan dan kebutuhan akan penggantian yang mahal dapat terjadi meskipun jumlah logam yang dihancurkan cukup kecil.
Jenis korosi
Ada beberapa bentuk korosi (Gambar 2). Ini termasuk (i) korosi antar butiran, (ii) korosi yang disebabkan oleh lingkungan, (iii) korosi lubang, (iv) dealloying atau pelindian selektif, (v) korosi erosi, (vi) korosi pada beton bertulang, (vii) korosi galvanik, (viii) korosi celah, (ix) korosi yang disebabkan oleh mikroba, (x) korosi seragam atau umum. Jenis korosi ini dijelaskan di bawah ini.
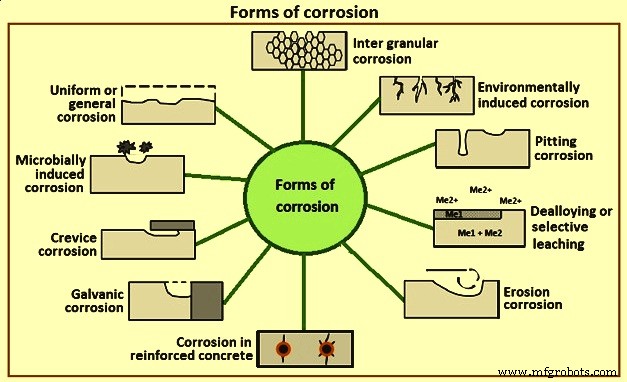
Gbr 2 Bentuk korosi
Korosi antar butiran
Ini juga dikenal sebagai korosi antar kristal. Ini adalah bentuk khusus dari korosi lokal, di mana serangan korosif terjadi di jalur yang cukup sempit terutama di sepanjang batas butir dalam struktur logam. Efek paling umum dari bentuk korosi ini adalah disintegrasi mekanis yang cepat (kehilangan daktilitas) material. Biasanya dapat dicegah dengan menggunakan bahan dan proses produksi yang tepat.
Pada tingkat mikroskopis, Besi dan baja memiliki daerah kecil yang dapat dibedakan yang disebut butiran. Dalam butir individu, orientasi susunan atom (disebut kisi) adalah sama. Butir individu memiliki orientasi yang berbeda dan batas antar butir disebut batas butir. Biasanya, batas butir tidak lebih reaktif dalam korosi daripada butir itu sendiri. Namun, dalam kondisi tertentu batas butir diubah dari butir itu sendiri oleh pengotor dan/atau pengayaan (atau penipisan) salah satu elemen paduan. Perlakuan panas dan pengelasan dapat menyebabkan perubahan komposisi yang dapat menyebabkan korosi antar butiran. Dalam kasus yang parah, korosi antar butiran dapat menyebabkan penurunan yang nyata dalam sifat mekanik dan dapat, dalam kasus yang ekstrim, mengubah baja menjadi tumpukan butiran individu.
Salah satu contoh korosi antar butiran yang paling umum adalah yang terjadi pada baja tahan karat. Selama pengelasan baja tahan karat, atau pemanasan dalam kisaran suhu 500 derajat C sampai 800 derajat C, baja tahan karat menjadi peka atau rentan terhadap korosi antar butiran seperti yang ditunjukkan pada Gambar 3. Kromium karbida (Cr23C6) tidak larut dalam hal ini. kisaran suhu dan mengendap keluar dari butir ke batas butir. Akibatnya, area butir yang berdekatan dengan batas butir kehabisan kromium dan menjadi anodik terhadap sisa butir dan batas butir. Akibatnya, batas butir memiliki tingkat ketahanan korosi yang lebih rendah daripada bahan sisa, yang menyebabkan serangan korosif lokal. Solusi paling sederhana untuk masalah korosi antar butiran baja tahan karat adalah memiliki komposisi dengan kandungan karbon kurang dari 0,03%. Kandungan karbon rendah mencegah pembentukan kromium karbida dan kromium tetap dalam larutan. Korosi pada daerah batas butir yang terdeplesi sangat parah dan terjadi di lingkungan asam.
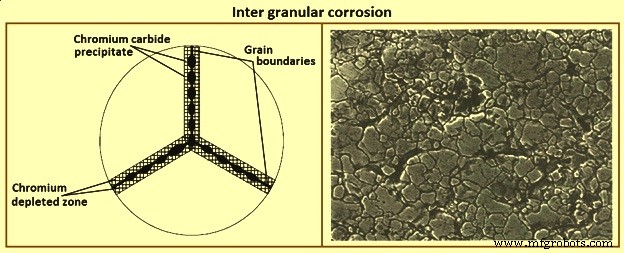
Gbr 3 Korosi antar butiran
Korosi yang disebabkan oleh lingkungan
Korosi yang diinduksi lingkungan juga disebut retak yang diinduksi lingkungan. Ada dua jenis retak akibat lingkungan. Ini adalah (i) retak korosi tegangan, dan (ii) retak dengan bantuan hidrogen. Retak yang disebabkan oleh lingkungan juga terjadi karena kelelahan korosi. Gambar 4 menunjukkan korosi yang disebabkan oleh lingkungan.

Gbr 4 Korosi yang disebabkan oleh lingkungan
Stress-corrosion-cracking (SCC) terjadi pada baja di bawah beberapa kondisi ambang seperti (i) komposisi larutan lingkungan korosif tertentu, (ii) tingkat tegangan tarik minimum, (iii) suhu, (iv) komposisi baja, dan (v) struktur baja. Contohnya adalah baja tahan karat. Baja tahan karat retak dalam larutan klorida. Interaksi kondisi yang mengarah ke SCC tidak dipahami dengan baik. Dipercaya bahwa korosi menyebabkan terbentuknya lubang atau diskontinuitas permukaan pada logam yang kemudian berfungsi sebagai konsentrator tegangan. Adanya tegangan tarik ambang minimum, ditambah dengan korosi, menyebabkan retakan merambat. Selain itu, selama korosi awal, tegangan tarik dapat menyebabkan film pelindung di permukaan pecah, sehingga logam terpapar lingkungan korosif.
Ini adalah jenis korosi yang berbahaya yang dapat disebabkan oleh faktor lingkungan atau tekanan siklik. Jenis utama dari serangan retak adalah karena (i) korosi kelelahan yang merupakan kegagalan dipercepat dari baja yang mengalami pembebanan siklik karena kehadirannya di lingkungan korosif, dan (ii) SCC yang merupakan korosi yang disebabkan retak yang terjadi di baja di bawah tegangan tarik tinggi. Retakan dimulai dari permukaan dan masuk ke dalam. Perlu dicatat bahwa tegangan dapat merupakan hasil dari pengerjaan dingin, pembentukan, atau pembebanan eksternal.
SCC adalah gabungan proses korosi mekanik dan elektro-kimia yang menghasilkan retak bahan tertentu. Hal ini dapat menyebabkan kegagalan getas mendadak yang tidak terduga dari logam yang biasanya ulet yang mengalami tingkat tegangan jauh di bawah kekuatan luluhnya. Tegangan internal dalam material dapat cukup untuk memulai serangan retak korosi tegangan.
SCC bukan sekadar tumpang tindih antara korosi dan tekanan mekanis, tetapi dapat dipahami sebagai proses auto-katalitik, percepatan sendiri yang mengarah pada laju disolusi logam yang tinggi (reaksi anodik). Awalnya, lubang kecil terbentuk dan berkembang menjadi retakan karena tegangan yang diterapkan atau sisa pada material. Formasi retak membuka permukaan logam aktif (non-pasif) baru, yang sekali lagi menimbulkan korosi dengan sangat mudah. Hal ini menyebabkan perambatan retak lebih lanjut dan sekali lagi pada paparan permukaan logam baru yang sangat aktif di dalam retakan. Pelarutan logam dalam retakan berlangsung cepat sampai terjadi kegagalan mekanis.
SCC adalah bentuk korosi yang sangat spesifik yang terjadi hanya ketika tiga persyaratan berbeda berikut ini dipenuhi secara bersamaan (Gambar 4) yaitu (i) mekanis (beban, tegangan), (ii) material (paduan rentan, misalnya baja), dan (iii) lingkungan (sangat korosif, klorida). Telah diketahui dengan baik bahwa baja dengan kadar tertentu dapat mengalami SCC di lingkungan yang keras seperti kolam renang dalam ruangan. Dalam sebagian besar kasus ini, korosi diprakarsai oleh klorida yang menyerang lapisan pasif.
Perengkahan berbantuan hidrogen juga dikenal sebagai penggetasan hidrogen. Hal ini disebabkan hilangnya keuletan baja karena saturasi atom hidrogen di batas butir. Itu terjadi di situs katodik lokal dan diperparah oleh stres dan senyawa seperti hidrogen sulfida.
Retak berbantuan hidrogen disebabkan oleh difusi atom hidrogen ke dalam baja. Kehadiran hidrogen dalam kisi melemahkan integritas mekanik logam dan menyebabkan pertumbuhan retak dan patah getas pada tingkat tegangan di bawah kekuatan luluh. Seperti SCC, ini dapat menyebabkan kegagalan mendadak pada bagian baja tanpa tanda peringatan yang terdeteksi. Dalam aplikasi umum, kerusakan hidrogen biasanya hanya relevan untuk baja berkekuatan tinggi dengan kekuatan tarik sekitar 1 MPa atau lebih tinggi. Adapun perengkahan yang dibantu hidrogen, tiga kondisi berbeda (Gbr. 4) harus ada pada saat yang sama. Ini adalah (i) mekanik (beban, tegangan), (ii) material (struktur kekerasan), (iii) lingkungan (hidrogen eksternal, hidrogen internal).
Sumber hidrogen dapat berupa proses produksi seperti pembuatan baja, pengawetan dan elektro-galvanisasi (hidrogen primer). Sumber sekunder dapat berupa hidrogen yang terbentuk selama proses korosi. Selama proses korosi, hidrogen terbentuk dan berdifusi ke dalam material. Asupan hidrogen ini menyebabkan penurunan ketangguhan atau keuletan baja.
Korosi lubang
Korosi pitting adalah serangan yang sangat terlokalisasi yang pada akhirnya mengakibatkan terciptanya lubang atau lubang kecil pada baja. Bentuk korosi ini terutama ditemukan pada logam pasif terutama yang memiliki ketahanan korosi pada lapisan oksida tipis di permukaan dengan ketebalan hanya beberapa nanometer.
Korosi lubang adalah salah satu bentuk korosi yang paling merusak dan berbahaya. Pada dasarnya, objek baja untuk pitting adalah mereka yang mengandalkan film oksida untuk perlindungan, seperti baja tahan karat. Inisiasi lubang dapat disebabkan oleh salah satu alasan yaitu (i) serangan kimia, seperti besi klorida atau air laut aerasi pada baja tahan karat, (ii) serangan mekanis seperti benturan atau goresan yang menghilangkan area kecil lapisan pelindung, dan (iii) korosi celah akibat endapan kecil di permukaan, terutama di air laut yang tergenang. Beberapa teori menyatakan bahwa pitting hanyalah kasus khusus korosi celah.
Proses awal korosi dimulai dengan kerusakan lokal dari lapisan pasif. Serangan korosif lokal dapat dimulai pada baja, misalnya, oleh ion klorida. Korosi pitting bisa sangat bermasalah. Sedangkan korosi seragam dapat dilihat dengan jelas di permukaan, korosi pitting sering kali hanya muncul sebagai lubang kecil di permukaan. Jumlah material yang dihilangkan di bawah lubang kecil biasanya tidak diketahui, karena rongga tersembunyi dapat terbentuk, membuat korosi pitting lebih sulit untuk dideteksi dan diprediksi. Secara teknis, tidak ada cara yang masuk akal untuk mengendalikan korosi pitting. Bentuk korosi ini harus dikecualikan sejak awal melalui pertimbangan desain dan penggunaan material yang tepat. Gambar 5 menunjukkan korosi pitting.
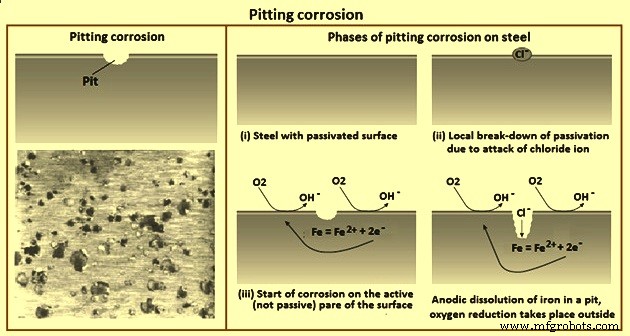
Gbr 5 Korosi sumuran
Dealloying atau pelindian selektif
Dealloying atau korosi pelindian selektif hasil dari area permukaan logam yang berbeda secara metalurgi dari area lain yang berdekatan. Jenis korosi ini lebih banyak terjadi pada logam dan paduan non-ferrous. Misalnya, kuningan adalah paduan dengan seng dan tembaga dalam 'larutan padat'. Hal ini dapat menimbulkan korosi dengan seng yang selektif dihapus dari paduan, meninggalkan tembaga. Itu membuat paduan berpori dan membahayakan sifat mekaniknya. Dalam kuningan dapat diidentifikasi ketika warna alami kuning berubah menjadi kemerahan atau tembaga dalam penampilan. Akan sangat membantu untuk menambahkan sedikit timah ke paduan untuk mencegah dealloying. Pencucian selektif semacam itu dikenal sebagai 'dezincification'.
Besi tuang dapat menimbulkan korosi sedemikian rupa sehingga besi terkorosi secara selektif, meninggalkan lapisan grafit lunak. Ini disebut sebagai 'grafitisasi'. Contoh lain dirujuk sebagai dealuminifikasi, denikkelifikasi, dan dekobaltifikasi, dll. di mana istilah tersebut merujuk pada elemen logam yang terkorosi secara selektif. Dealloying atau pelindian selektif ditunjukkan pada Gambar 6.
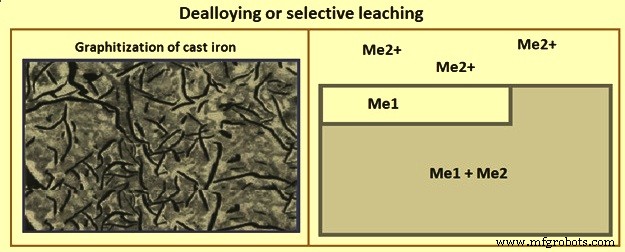
Gbr 6 Dealloying atau pelindian selektif
Mekanisme pelindian selektif telah dijelaskan dengan contoh paduan kuningan. Dalam hal ini pertama-tama kuningan terkorosi. Kemudian ion seng tetap dalam larutan, dan pelat tembaga kembali sebagai lapisan padat. Masalah dengan teori ini adalah bahwa korosi terjadi bahkan di bawah kecepatan aliran elektrolit yang tinggi ketika seseorang menduga bahwa ion tembaga tersapu sebelum mereka dapat keluar.
Teori kedua, sekali lagi untuk kuningan, adalah bahwa seng terkorosi secara istimewa, meninggalkan tembaga dalam struktur kisi. Ini adalah proses korosi di mana logam yang kurang mulia dalam paduan diserang secara istimewa dan digantikan dalam matriks oleh produk katodik. Contoh paling umum dari ini terjadi dengan kuningan dan disebut dezincification. Dalam dezincifikasi kuningan, seng dalam matriks paduan diserang dan tembaga tetap ada.
Korosi erosi
Korosi erosi dihasilkan dari aliran elektrolit berkecepatan tinggi yang aksi abrasifnya mempercepat korosi. Korosi ini sangat parah ketika elektrolit mengandung padatan dalam suspensi. Efeknya adalah untuk menghilangkan oksida pelindung dari permukaan film, sehingga mengekspos paduan baru untuk menimbulkan korosi. Korosi erosi dapat dianggap sebagai lubang pada skala yang jauh lebih besar. Faktanya, ada batas kecepatan elektrolit yang dapat ditoleransi oleh logam tertentu.
Paduan tembaga-nikel dipilih untuk layanan air laut berdasarkan ketahanannya terhadap erosi-korosi (di antara persyaratan lainnya). Selain erosi, bentuk serangan lain yang berhubungan dengan efek kecepatan adalah sebagai berikut.
Kavitasi - Ini adalah kerusakan permukaan yang disebabkan oleh pembentukan tiba-tiba dan runtuhnya gelembung dan rongga karena turbulensi dalam cairan. Biasanya ditandai dengan permukaan logam yang berlubang atau kasar.
Serangan pelampiasan - Ini adalah korosi lokal yang disebabkan oleh turbulensi atau aliran yang menimpa. Biasanya ada kecepatan kritis yang di bawahnya tidak terjadi pelampiasan dan di atasnya serangan meningkat dengan cepat. Dalam banyak kasus, ketiga proses korosi dapat terjadi secara bersamaan. Gambar 7 memberikan korosi erosi.
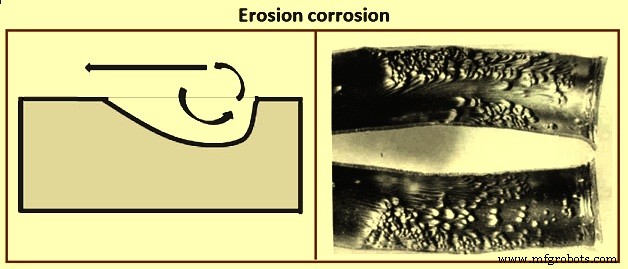
Gbr 7 Korosi erosi
Korosi pada beton bertulang
Beton Bertulang (RC) adalah material komposit yang terdiri dari batang tulangan baja (rebars) yang tertanam dalam massa beton. Tulangan memikul sebagian besar beban tarik dan memberikan tingkat ketahanan retak pada beton yang dibebani dengan sendirinya secara tekan. Baja dalam beton biasanya dalam kondisi pasif yang tidak menimbulkan korosi. Namun, kondisi pasif non-korosi tidak selalu tercapai dalam praktik karena korosi tulangan terjadi. Korosi tulangan memiliki konsekuensi fisik seperti penurunan kekuatan ultimit dan kemampuan layan struktur beton. Korosi tulangan baja pada beton merupakan masalah universal yang besar. Kerusakan yang terjadi akibat korosi sebagian besar dapat mengurangi kemampuan servis dan integritas struktural RC. Kerusakan akibat korosi pada struktur beton memerlukan perbaikan dini atau dalam beberapa kasus penggantian total struktur beton.
Setiap kali batang tulangan yang tertanam dalam baja terkorosi, produk korosi meningkatkan volumenya. Semua bentuk oksida besi dan hidro-oksida memiliki volume spesifik yang lebih besar dari baja. Gaya ekspansif yang dihasilkan oleh korosi baja menyebabkan retak tarik dan pewarnaan karat pada beton. Hal ini, pada gilirannya, menyebabkan penurunan kemampuan servis dan integritas struktural beton selain mempengaruhi estetikanya. Setelah korosi dimulai, hanya masalah waktu sebelum jumlah kumulatif kerusakan terjadi pada struktur beton dan gagal sebelum umur desainnya.
Dua penyebab utama korosi tulangan pada beton adalah (i) kegagalan lokal dari film pasif pada baja oleh ion klorida dan (ii) kegagalan umum pasif oleh netralisasi alkalinitas beton karena reaksi dengan atmosfer. CO2 (karbon dioksida). Faktor utama yang mempengaruhi korosi tulangan di RC adalah (i) hilangnya alkalinitas karena karbonasi, (ii) hilangnya alkalinitas karena klorida, (iii) retak pada beton karena pembebanan mekanis, (iv) arus menyimpang, ( v) polusi atmosfer, (vi) jalur kelembaban, (vii) rasio air-semen, (viii) kekuatan tarik beton yang rendah, (ix) kontak listrik dengan logam yang berbeda, dan (x) korosi karena perbedaan lingkungan.
Dalam media keseragaman sempurna, korosi sangat tidak mungkin terjadi. Namun, beton bertulang sama sekali bukan merupakan bahan yang homogen dan sel-sel korosi terbentuk ketika kondisi tertentu ada. Ada banyak alasan untuk ketidakseragaman beton yang meningkatkan korosi. Beton dapat menjadi sarang lebah, keropos, dan tidak merata basah dan kering. Retak menyebabkan perbedaan tegangan baja, aerasi diferensial, dan pengendapan garam. Selalu ada ketidakseragaman yang melekat pada tulangan itu sendiri karena tegangan sisa terkunci awal dan proses manufaktur. Akibatnya, daerah dengan potensi lebih rendah menjadi anodik dan daerah dengan potensi lebih tinggi menjadi katodik. Beton basah bertindak sebagai elektrolit, tindakan yang lebih dipercepat jika ion garam ada. Korosi pada beton bertulang biasanya terbagi dalam dua kelompok umum yaitu (i) beton retak, dan (ii) beton tidak retak.
Dalam kasus beton segar yang tidak retak biasanya ada ketahanan yang cukup terhadap serangan korosif. Penutup beton di atas tulangan sangat efektif dalam menghambat penetrasi agen korosif ke tingkat baja. Jelas bahwa semakin tebal dan padat penutup beton, semakin efektif dalam menahan korosi. Juga, beton segar memiliki nilai pH yang sangat tinggi yang biasanya menghambat reaksi korosi. Bilangan pH adalah indeks keasaman atau kebasaan suatu medium. Angka dari 0 sampai 7 menunjukkan keasaman larutan (di mana korosi dipromosikan), dan angka dari 7 sampai 14 menunjukkan alkalinitas larutan (di mana korosi diperlambat). Beton segar memiliki kandungan Ca(OH)2 (kalsium hidroksida) tinggi yang memberikan pH sekitar 13. Pertahanan terakhir terhadap korosi ditawarkan oleh film oksida biru (skala pabrik) di sekitar permukaan tulangan. Film oksida ini mencegah agen korosif bersentuhan langsung dengan logam telanjang. Dengan demikian, kerak pabrik memberikan perlindungan korosi lokal.
Namun, seiring berjalannya waktu kondisi di atas cenderung berubah. Air, garam, oksigen, CO2, dan gas industri (jika ada) perlahan mulai menembus beton, yang kecepatannya tergantung pada permeabilitas penutup beton. CO2, yang menembus beton melalui pori-pori dan retakan, bereaksi dengan Ca(OH)2 dan menghasilkan kalsium karbonat. Dengan demikian, nilai pH dan kualitas pelindung beton berkurang. Mekanisme umum terjadinya korosi pada beton bertulang ditunjukkan pada Gambar 8.
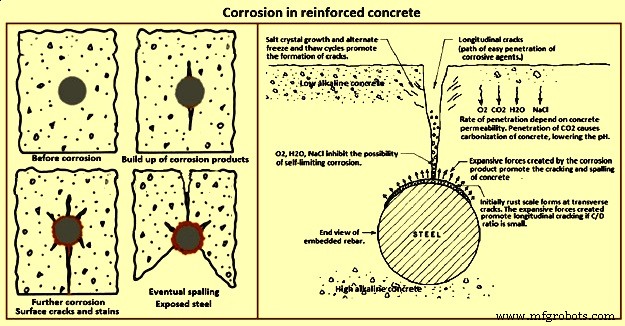
Gbr 8 Korosi pada beton bertulang
Korosi galvanik
Ketika dua logam yang berbeda terkena lingkungan korosif, perbedaan potensial listrik ada. Jika kedua logam dihubungkan secara elektrik, logam yang lebih aktif menjadi anoda dalam sel galvanik yang dihasilkan dan korosinya meningkat. Contoh sel korosi semacam itu adalah penggunaan baut baja untuk menyatukan pelat tembaga.
Korosi galvanik mengacu pada kerusakan korosi di mana dua logam yang berbeda memiliki koneksi konduktor listrik dan bersentuhan dengan elektrolit korosif yang umum. Dalam model korosi elektrokimia, salah satu dari dua reaksi parsial (pelarutan logam anodik dan reduksi oksigen katodik) terjadi hampir secara eksklusif pada satu logam. Biasanya, logam yang kurang mulia dilarutkan (larutan logam anodik), sedangkan bagian yang lebih mulia tidak diserang oleh korosi (hanya berfungsi sebagai katoda untuk reduksi oksigen). Di mana korosi galvanik terjadi, laju korosi dari logam yang kurang mulia lebih tinggi daripada di lingkungan bebas korosi tanpa kontak dengan logam lain.
Dengan menggunakan data termodinamika dan mempertimbangkan pengalaman umum yang diperoleh dalam aplikasi tipikal, adalah mungkin untuk memprediksi kombinasi material mana yang dipengaruhi oleh korosi galvanik. Contoh positif dari fenomena korosi galvanik adalah cara seng melindungi baja karbon dan baja paduan rendah. Seng adalah logam yang kurang mulia yang secara aktif melindungi baja dari korosi itu sendiri.
Tidak semua korosi galvanik merugikan. Baja berlapis seng, atau galvanisasi, digunakan untuk melindungi baja, bukan karena baja tahan terhadap korosi, tetapi karena seng, yang bersifat anodik terhadap baja, lebih disukai terkorosi. Oleh karena itu, baja dilindungi secara katodik dengan membuat area baja yang terbuka menjadi katoda.
Biasanya praktik yang baik untuk tidak menggunakan logam yang berbeda kecuali jika diperlukan, tetapi jika akan digunakan maka tindakan pencegahan yang diperlukan adalah (i) mencoba mengisolasi logam secara elektrik, (ii) menggunakan lapisan pelindung pada logam. permukaan (s), biasanya katoda, (iii) untuk melindungi logam kurang mulia secara katodik, (iv) untuk menempatkan inhibitor korosi ke dalam sistem, (v) menggunakan desain di mana bagian anodik dapat diganti dengan mudah, (vi) untuk menjaga kelembaban, (vi) menggunakan logam yang berdekatan satu sama lain dalam seri galvanik, (vii) untuk menjaga rasio area anoda / katoda tinggi dalam desain, dan (viii) menggunakan kelonggaran desain untuk memperhitungkan korosi. Gambar 9 menunjukkan korosi galvanik.
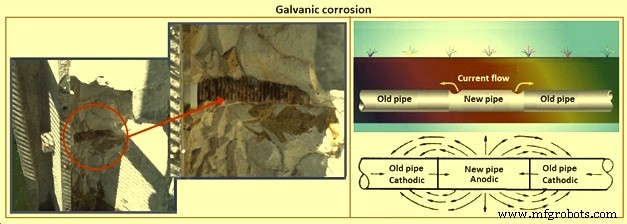
Gbr 9 Korosi galvanik
Korosi celah
Korosi celah mengacu pada korosi yang terjadi pada retakan atau celah yang terbentuk antara dua permukaan (terbuat dari logam yang sama, logam yang berbeda atau bahkan logam dan non-logam). Jenis korosi ini dimulai dengan masuknya oksigen dari udara secara terbatas melalui difusi ke area celah yang mengarah ke konsentrasi oksigen terlarut yang berbeda dalam elektrolit umum (yang disebut sel aerasi).
Korosi celah adalah serangan lokal yang terjadi ketika celah-celah, yang dibentuk oleh sambungan yang tersusun, atau area pelindung parsial, terkena lingkungan korosif. Sel-sel yang dihasilkan seperti itu disebut sebagai sel konsentrasi. Dua kasus umum adalah sel oksigen dan sel ion logam. Sel konsentrasi oksigen terjadi ketika daerah terlindung menjadi terkuras oksigen dan daerah bertindak sebagai anoda relatif terhadap daerah oksida. Seperti yang ditunjukkan pada Gambar 10, korosi menjadi cukup cepat karena area terlindung kecil dibandingkan dengan area tanpa pelindung. Dalam kasus sel oksigen, ada 'gradien' oksigen yang memaksa pembentukan anoda dan katoda sehubungan dengan tingkat oksigen.
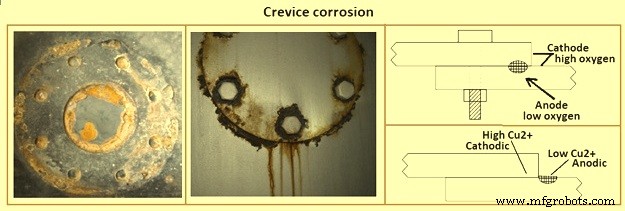
Gbr 10 Korosi celah
Korosi celah mengacu pada korosi yang terjadi pada retakan atau celah yang terbentuk antara dua permukaan (terbuat dari logam yang sama, logam yang berbeda atau bahkan logam dan non-logam). Jenis korosi ini diprakarsai oleh masuknya oksigen dari udara secara terbatas melalui difusi ke area celah yang mengarah ke konsentrasi oksigen terlarut yang berbeda dalam elektrolit umum (yang disebut sel aerasi). Sekali lagi, dua reaksi parsial terjadi pada bagian permukaan yang berbeda. Pengurangan oksigen terjadi di daerah terluar dengan konsentrasi oksigen yang lebih tinggi yang mudah diakses oleh udara sekitarnya, sedangkan pelarutan logam anodik terjadi di daerah celah yang mengakibatkan serangan lokal (misalnya pitting). Hal ini juga dapat terjadi di bawah mesin cuci atau gasket, ketika masuknya air di bawahnya tidak dicegah). Ada batas bawah dan batas atas untuk ukuran celah di mana korosi diinduksi. Jika celah terlalu kencang, tidak ada elektrolit untuk korosi yang terjadi. Jika celah terlalu lebar untuk mengurangi masuknya oksigen, sel aerasi dan akibatnya konsentrasi oksigen yang berbeda tidak dapat berkembang. Namun, lebar celah kritis tergantung pada beberapa faktor seperti jenis logam yang terlibat, lingkungan korosi dan siklus basah/kering.
Kekuatan pendorong awal korosi tersebut adalah sel oksigen. Pertumbuhan yang berkelanjutan didorong oleh akumulasi (seringkali disebabkan oleh faktor-faktor yang sama yang menghasilkan kadar oksigen yang rendah dari garam terhidrolisis asam di dalam celah. Paduan, seperti baja tahan karat 18-8, dapat mengalami korosi celah sel oksigen.
Sel ion logam dibentuk terutama dengan paduan tembaga. Daerah terlindung mengakumulasi produk korosi dan menjadi katodik ke daerah di luar celah di mana produk korosi tetap hanyut. Gambar 10 menunjukkan jenis sel konsentrasi ini.
Contoh lain dari korosi sel ion logam terjadi ketika kecepatan relatif elektrolit di atas permukaan logam lebih besar di satu titik daripada di titik lain, sehingga menghasilkan korosi celah ion logam. Contoh yang baik adalah di mana piringan logam berputar dengan kecepatan tinggi di air laut. Korosi terjadi di dekat tepi di mana kecepatan linier tertinggi dan konsentrasi ion logam rendah (karena ion berulang kali tersapu). Kecepatan tinggi, lebih tinggi daripada di daerah yang lebih dekat ke pusat cakram, menyapu ion-ion logam, sehingga membentuk daerah anoda. Di bagian tengah piringan, di mana kecepatannya lebih rendah, logam bertindak sebagai katoda dan dilindungi.
Namun, dua sel konsentrasi menimbulkan korosi di berbagai daerah celah. Sel oksigen terkorosi di bawah area terlindung sementara sel ion logam terkorosi di luar area. Kekuatan pendorong awal di balik korosi adalah baik oksigen atau sel ion logam. Pertumbuhannya yang berkelanjutan diatur oleh akumulasi produk korosi, endapan berkapur, dan garam di dalam celah.
Sekali lagi, dua reaksi parsial terjadi pada bagian permukaan yang berbeda. Pengurangan oksigen terjadi di daerah terluar dengan konsentrasi oksigen yang lebih tinggi yang mudah diakses oleh udara sekitarnya, sedangkan pelarutan logam anodik terjadi di daerah celah yang mengakibatkan serangan lokal (misalnya pitting). Hal ini juga dapat terjadi di bawah mesin cuci atau gasket, ketika masuknya air di bawahnya tidak dapat dicegah.
Korosi yang disebabkan oleh mikroba
Organisme biologis dapat memainkan peran utama dalam serangan logam. Korosi disebabkan atau dipercepat oleh mikroorganisme. Itu dapat terjadi dengan atau tanpa kehadiran oksigen. Tindakan biologis dapat meningkatkan keparahan korosi (i) sebagai akibat dari bio-deposit pada permukaan material, (ii) produksi spesies kimia korosif (yaitu hidrogen sulfida dari bakteri pereduksi sulfat – SRB), dan (iii) gangguan reaksi elektrokimia normal dan pembentukan film.
Microbially (microbiologically) induced corrosion (MIC) adalah korosi yang disebabkan oleh keberadaan dan aktivitas mikroorganisme. Mikroorganisme adalah organisme yang tidak dapat dilihat secara individu dengan mata manusia, termasuk mikroalga, bakteri, dan jamur. Korosi yang diinduksi mikroba dapat menyebabkan berbagai bentuk korosi lokal, termasuk pitting, dealloying, korosi erosi yang ditingkatkan, korosi galvanik yang ditingkatkan, retak korosi tegangan, dan penggetasan hidrogen. Akibat MIC, korosi dapat terjadi di lokasi yang tidak diperkirakan sebelumnya, dan dapat terjadi dengan laju yang sangat tinggi. Bahan besi dan baja mengalami MIC. Selanjutnya, MIC juga dapat terjadi di air laut, air tawar, air suling/demineral, bahan bakar hidrokarbon, bahan kimia proses, makanan, tanah, plasma manusia, air liur, dan limbah.
Meskipun SRBs, yang hanya aktif dalam lingkungan anaerobik (bebas oksigen), merupakan penyebab korosi yang sangat umum, MIC juga dapat disebabkan oleh jenis mikroorganisme lainnya. Sebagai contoh, 'thiobacilli' yang merupakan bakteri pengoksidasi belerang (SOB), mengoksidasi senyawa belerang menjadi asam sulfat. Mikroorganisme penghasil asam lainnya Termasuk bakteri dan jamur. Mikroba dapat menempel pada permukaan logam membentuk bio-film, yang terdiri dari komunitas mikro-organisme, yang menyebabkan korosi. Ketika produk asam dari aksi bakteri terperangkap di antarmuka bio-film-logam, dampaknya terhadap korosi meningkat.
Meskipun besi tidak menimbulkan korosi yang berarti dalam air yang mengalami deaerasi, laju korosi di beberapa lingkungan alami yang mengalami deaerasi ternyata sangat tinggi. Tingkat tinggi ini telah ditelusuri ke keberadaan SRB (misalnya, desulfovibrio desulfuricans). Hubungannya dengan laju korosi dipercepat yang diamati di tanah yang rendah oksigen terlarut pertama kali diamati di Belanda. Bakteri berbentuk melengkung, berukuran sekitar 1 × 4 mikrometer, dan banyak ditemukan di perairan dan tanah. Mereka berkembang hanya dalam kondisi anaerobik dalam kisaran pH sekitar 5,5 hingga 8,5. Varietas tertentu berkembang biak di air tawar dan di tanah yang mengandung sulfat, sementara yang lain tumbuh subur di air payau dan air laut, dan yang lain lagi dinyatakan ada di tanah dalam pada suhu setinggi 60 derajat C hingga 80 derajat C.
SRB dengan mudah mereduksi sulfat anorganik menjadi sulfida dengan adanya hidrogen atau bahan organik, dan mereka dibantu dalam proses ini dengan adanya permukaan besi. Bantuan yang diberikan besi dalam reduksi ini mungkin untuk memasok hidrogen, yang biasanya teradsorpsi pada permukaan logam dan yang digunakan bakteri dalam mereduksi SO4. Untuk setiap ekivalen atom hidrogen yang mereka konsumsi, satu ekivalen Fe 2+ memasuki larutan untuk membentuk karat dan FeS. Oleh karena itu, bakteri mungkin pada dasarnya bertindak sebagai depolarisasi.
Besi hidroksida dan besi sulfida terbentuk dalam proporsi 3 mol hingga 1 mol. Analisis karat di mana SRB aktif menunjukkan perkiraan rasio oksida terhadap sulfida ini. Secara kualitatif, aksi BPRS sebagai penyebab korosi pada air yang awalnya bebas sulfida dapat dideteksi dengan menambahkan beberapa tetes asam klorida ke dalam karat dan mencatat bau hidrogen sulfida.
Kerusakan parah oleh BPRS telah terjadi terutama di casing sumur minyak, pipa yang terkubur, rolling mill berpendingin air, dan pipa dari sumur air dalam. Dalam 2 tahun, air sumur dapat menyebabkan kegagalan pipa air galvanis berdiameter 50 mm oleh tindakan BPRS.
Kombinasi suhu rendah dan kelembaban rendah adalah salah satu pendekatan untuk mengendalikan pertumbuhan bakteri, tetapi jamur dapat tumbuh dalam kondisi seperti itu. Pembersihan secara teratur adalah praktik yang baik untuk mencegah pembentukan bio-film dan korosi berikutnya. Klorinasi digunakan untuk menghilangkan bakteri penyebab korosi, tetapi perlakuan ini dapat menghasilkan produk samping yang tidak dapat diterima lingkungan. Aerasi air mengurangi aktivitas bakteri anaerob karena mereka tidak dapat berkembang dengan adanya oksigen terlarut. Penambahan biosida tertentu dapat bermanfaat, tetapi mikroorganisme mampu menjadi resisten terhadap bahan kimia tertentu setelah penggunaan jangka panjang. Pemberantasan populasi mikroba dapat dicapai dengan menggabungkan beberapa bahan kimia atau dengan meningkatkan konsentrasi biosida. Gambar 11 menunjukkan contoh korosi yang disebabkan oleh mikroba.
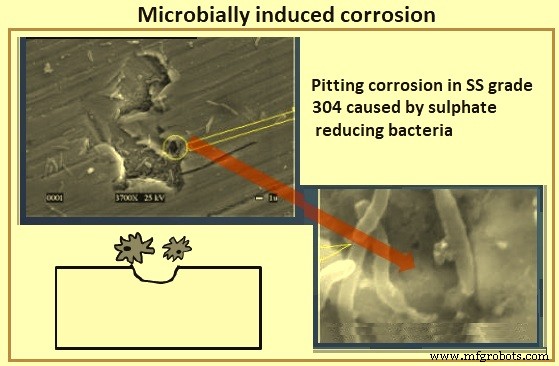
Gbr 11 korosi yang disebabkan oleh mikroba
Korosi seragam atau umum
Korosi seragam (Gbr 12) adalah bentuk korosi di mana permukaan dihilangkan hampir merata. Reaksi parsial (larutan logam dan reduksi oksigen) terdistribusi secara statistik di atas permukaan, yang mengarah pada pelarutan logam yang kurang lebih homogen dan pembentukan produk korosi yang seragam (misalnya karat merah pada baja karbon). Korosi ini dihasilkan dari pergeseran terus-menerus daerah anoda dan katoda pada permukaan logam yang bersentuhan dengan elektrolit dan menyebabkan serangan korosif yang hampir seragam di seluruh permukaan. Contoh korosi tersebut adalah berkaratnya pelat baja di air laut. Meskipun disebut korosi seragam, ini ditandai dengan hilangnya permukaan rata-rata.
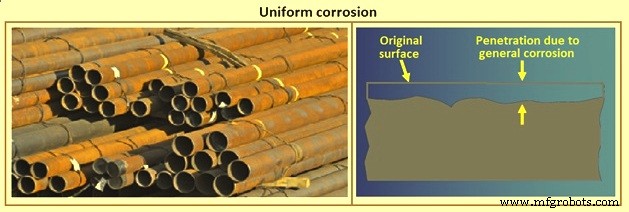
Gbr 12 Korosi seragam
Jika tingkat kehilangan logam diketahui, kelonggaran dapat dibuat dalam desain dan pemeliharaan untuk mengakomodasi korosi. Luasnya bentuk korosi ini biasanya dapat diperkirakan dengan baik berdasarkan pengalaman sebelumnya. Laju korosi biasanya diberikan dalam mikrometer per tahun. Dengan menggunakan nilai rata-rata ini, adalah mungkin untuk menghitung harapan hidup suatu komponen, dan dengan demikian meningkatkan harapan hidupnya dengan meningkatkan ketebalannya.
Korosi seragam terjadi pada baja karbon yang tidak terlindungi dan pada baja berlapis seng dalam kondisi atmosfer. Pada kenyataannya, serangan korosi homogen murni tidak mungkin terjadi. Selalu ada area, terutama pada bagian baja kompleks, yang terkorosi lebih cepat daripada yang lain yang mengarah ke permukaan yang kurang lebih kasar dengan penutup produk korosi yang tidak teratur.