Ada berbagai analisis kegagalan dan metode pemecahan masalah yang digunakan untuk menganalisis peralatan dan kegagalan proses. Berbagai metode dijelaskan dan dibandingkan sehingga profesional pemeliharaan dan keandalan dapat memilih analisis kegagalan atau alat pemecahan masalah yang tepat untuk menghasilkan solusi terbaik dengan biaya terendah.
Siapa yang Anda inginkan untuk mengerjakan peralatan Anda? Orang yang memilih alat yang tepat dari kotak alat yang dilengkapi dengan baik dan dengan terampil menggunakannya untuk menyelesaikan pekerjaan dengan cepat tanpa kesalahan atau orang yang memiliki beberapa alat dasar tetapi berjuang untuk menyelesaikan pekerjaan tepat waktu dan tanpa kesalahan.
Alat apa yang paling cocok, mikrometer atau penjepit? Mikrometer diperlukan untuk mengukur kecocokan bantalan, tetapi penjepit C mungkin diperlukan saat mengelas dua potong baja menjadi satu.
Kotak peralatan mental Anda juga harus berisi berbagai alat analisis. Anda harus memilih metode analisis yang paling cocok untuk memecahkan masalah yang dihadapi. Ingat, setiap alat memiliki kekuatan, kelemahan, dan area aplikasi yang disukai.
Masalah dan kegagalan terjadi setiap hari. Biasanya kami hanya memiliki waktu dan sumber daya untuk memberikan bantuan. Tidak setiap masalah memerlukan analisis akar penyebab.
Tugas kita adalah memisahkan masalah dan kegagalan yang membutuhkan bantuan dari masalah yang perlu kita cegah agar tidak terjadi di masa depan. Untuk membantu memisahkannya, tanyakan pada diri Anda beberapa pertanyaan:
-
Apa dampak aktual dari masalah tersebut?
-
Apa dampak potensial jika masalah tidak diselesaikan?
-
Tingkat risiko apa yang dapat kita hadapi yang didukung dari sudut pandang moral/hukum/kontrak?
-
Apa hasil yang dapat diterima yang menyeimbangkan risiko, biaya, dan manfaat?
Saat kita fokus pada respons yang memberikan bantuan yang dibutuhkan dan, jika perlu, menemukan akar permasalahan, kita menjadi lebih produktif.
Mari kita lihat beberapa alat analisis akar penyebab yang tersedia, termasuk kekuatan dan kelemahannya, sehingga Anda dapat memilih dan menggunakannya untuk mendapatkan wawasan yang Anda butuhkan untuk memecahkan masalah Anda.
Analisis akar penyebab (RCA) bukanlah satu metode yang terdefinisi dengan baik; ada banyak proses dan metode berbeda untuk melakukan analisis RCA yang ditentukan oleh pendekatan atau bidang asalnya :
-
Keamanan – analisis kecelakaan, keselamatan dan kesehatan kerja
-
Produksi – kontrol kualitas di industri manufaktur
-
Proses – ruang lingkup produksi diperluas untuk mencakup praktik bisnis
-
Kegagalan peralatan – terinspirasi oleh militer kemudian disesuaikan dengan industri dan digunakan dalam rekayasa dan pemeliharaan
-
Sistem – menggabungkan semua hal di atas dan menambahkan manajemen perubahan
Pencarian "analisis akar masalah" akan menghasilkan lusinan hasil. Sayangnya, tidak ada definisi yang seragam, sehingga metode atau proses mendasar mungkin memiliki beberapa nama dan deskripsi yang berbeda. Metode ini bervariasi dalam ruang lingkup dan kompleksitas. Menggunakan metode analisis yang tepat sama pentingnya, sehingga cocok dengan ruang lingkup dan kompleksitas masalah.
Beberapa teknik analisis akar penyebab (RCA) yang umum adalah:
-
Lima alasannya – Menanyakan mengapa, mengapa, mengapa sampai penyebab mendasar diidentifikasi.
-
Diagram Ishikawa/tulang ikan – Penyebab dan akibat terdaftar dalam kategori.
-
Analisis sebab dan akibat/pohon faktor penyebab – Faktor penyebab ditampilkan pada pohon sehingga dependensi sebab-akibat dapat diidentifikasi.
-
Mode kegagalan dan analisis efek/kekritisan – Mode kegagalan yang mungkin ditentukan; efek dan probabilitas dari kegagalan tersebut dijelaskan untuk mengidentifikasi tindakan pencegahan yang tepat dimulai dengan peralatan yang paling kritis.
-
Analisis pohon kesalahan atau logika – Sebuah kegagalan diidentifikasi dan mode kegagalan dijelaskan dan diuji sampai akar diidentifikasi.
-
Analisis penghalang – Memeriksa jalur yang melaluinya bahaya dapat memengaruhi target dan hambatan di jalur tersebut.
-
Analisis perubahan/Kepner-Tregoe – Membandingkan situasi yang tidak menunjukkan masalah dengan situasi yang ada untuk mengidentifikasi perubahan atau perbedaan yang menjelaskan apa yang terjadi.
-
Bagan pareto – Menunjukkan frekuensi relatif masalah atau kegagalan dalam urutan peringkat sehingga aktivitas peningkatan proses dapat difokuskan pada beberapa yang signifikan.
-
Analisis data – Adalah proses transformasi dan pemodelan data dengan tujuan menemukan informasi yang berguna.
Selanjutnya, mari kita jelaskan masing-masing metode ini secara lebih rinci dan jelaskan kelebihan dan keterbatasannya.
Lima Mengapa
Lima mengapa adalah teknik bertanya yang digunakan untuk menentukan sebab dan akibat dari suatu masalah atau kegagalan tertentu. Ini bertanya mengapa. Jawabannya menjadi dasar untuk pertanyaan berikutnya. Anda terus berjalan sampai Anda mencapai sesuatu yang mendasar atau benar-benar di luar kendali Anda. Nomor lima didasarkan pada pengamatan bahwa menanyakan "mengapa" lima kali biasanya menyelesaikan masalah. Mungkin hanya perlu tiga iterasi, atau Anda mungkin masih bertanya "mengapa" sebulan dari sekarang. Tergantung masalahnya.

Gambar 1 . Skenario lima alasan
Tidak semua kegagalan memiliki satu akar penyebab. Untuk menentukan penyebab tambahan, pertanyaan harus diulang dimulai dengan pengamatan yang berbeda.
Keuntungan
Tidak perlu kelompok besar untuk menyelesaikan analisis. Seringkali, satu atau dua orang sudah cukup. Untuk kegagalan komponen, mekanika, kimia dan fisika didefinisikan dengan baik, sehingga bekerja paling baik pada tingkat ini. Ini tidak bekerja dengan baik untuk tujuan manusia dan organisasi.
Metode ini fleksibel tanpa aturan tentang baris pertanyaan apa yang harus dijelajahi atau berapa lama untuk mencari akar penyebab tambahan. Akibatnya, hasilnya tergantung pada pengetahuan dan ketekunan orang-orang yang terlibat.
Batasan
Metode ini didasarkan pada konsep bahwa setiap akibat memiliki satu sebab. Jika beberapa penyebab dapat menghasilkan efek yang sama atau kombinasi penyebab diperlukan untuk menghasilkan efek, ini mungkin diabaikan. Jarang sekali satu penyebab di setiap tingkat mengapa cukup untuk menjelaskan efek yang dimaksud.
Ketika beberapa jalur lima mengapa digunakan, mungkin ada lebih dari satu jawaban untuk beberapa alasan, dan sangat mudah untuk analisis menjadi terlalu kompleks. Untuk mengatasi masalah ini, analisis pohon faktor penyebab dikembangkan. Jika salah satu jawaban Anda salah, itu mungkin saja terjadi, tetapi bukan penyebab sebenarnya dan sama sekali lain.
Diagram Ishikawa/Tulang Ikan
Diagram Ishikawa/tulang ikan (Gambar 2) adalah alat grafis yang digunakan untuk mengidentifikasi akar penyebab potensial dan kategori input proses apa yang mewakili sumber variabilitas terbesar dalam output. Diagram tulang ikan yang lengkap mencakup tulang belakang tengah dan cabang-cabang yang menyerupai kerangka ikan. Cabang digunakan untuk mengkategorikan penyebab, baik dengan urutan proses atau fungsi. Di setiap kategori, penyebab potensial dicantumkan dan kemudian diuji validitasnya menggunakan bukti atau alat analisis lainnya.
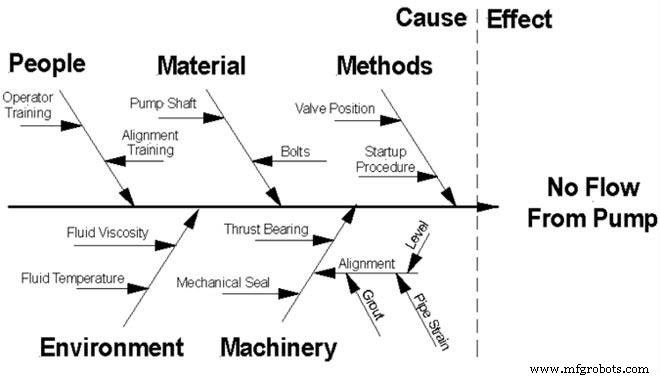
Gambar 2 . Diagram Ishikawa/Tulang Ikan
Keuntungan
Diagram tulang ikan berguna karena menunjukkan hubungan antara penyebab potensial dan merupakan cara yang baik untuk melibatkan orang dalam pemecahan masalah. Ini juga efektif bila digunakan oleh satu orang.
Batasan
Melibatkan banyak orang dalam diagram tulang ikan dapat membatasi keefektifannya, karena mendorong pendekatan yang berbeda di mana godaan untuk mengidentifikasi dan memperbaiki segala sesuatu yang mungkin menyebabkan masalah sangat kuat. Agar diagram tulang ikan berhasil, diperlukan pemusnahan penyebab yang tidak cukup, diperlukan atau ada untuk menghasilkan masalah.
Analisis Sebab Akibat/Pohon Faktor Penyebab
Analisis sebab-akibat menggabungkan pertanyaan yang digunakan dalam lima mengapa dengan struktur pohon logika atau pohon kesalahan. Ini membantu untuk menganggapnya sebagai perluasan dari metode lima mengapa dalam format pohon logika. Itu dapat memeriksa banyak penyebab pada satu efek.
Masalah, kegagalan atau penyimpangan (efek) ditempatkan di bagian atas pohon atau satu item di sebelah kiri halaman. Dengan menanyakan “mengapa”, faktor-faktor yang merupakan penyebab langsung dari efek ini ditampilkan di bawahnya dan dihubungkan menggunakan cabang. Penyebab-penyebab ini diuji untuk kebutuhan, kecukupan dan keberadaan. Penyebab yang tidak memenuhi tes ini dikeluarkan dari pohon.
Selanjutnya, penyebab langsung dari masing-masing faktor ini ditambahkan. Setiap penyebab yang ditambahkan ke dalam struktur harus memenuhi persyaratan yang sama untuk kebutuhan, kecukupan dan keberadaan.
Beberapa analis memulai dengan pernyataan masalah yang menjawab siapa, apa, kapan, dan di mana dan diikuti dengan daftar tujuan yang dipengaruhi oleh peristiwa tersebut. Kemudian pohon faktor penyebab dikembangkan untuk masing-masing tujuan yang terkena dampak. Konstruksi simultan ini membantu mengungkap kesenjangan dalam pengetahuan.
Pohon faktor penyebab biasanya memiliki banyak titik akhir. Titik akhir yang memerlukan tindakan korektif adalah penyebab utama.
Beberapa keuntungan dihasilkan dari membangun pohon faktor penyebab:
-
Menyediakan struktur untuk mencatat penyebab dan bukti yang mudah diikuti.
-
Dapat menangani banyak skenario.
-
Berfungsi dengan baik sebagai teknik analisis utama.
-
Dapat menggabungkan hasil dari alat lain.
Pohon faktor penyebab juga memiliki keterbatasan:
-
Sulit untuk menangani dan menampilkan peristiwa yang bergantung pada waktu.
-
Kompleksitas mempersulit penanganan dependensi urutan.
-
Akan mengidentifikasi kesenjangan pengetahuan, tetapi tidak memiliki sarana untuk mengisinya.
-
Titik pemberhentian bisa berubah-ubah.
Dalam contoh pohon faktor kausal pada Gambar 3, ada beberapa penyebab potensial untuk satu efek. Di baris ketiga dari bawah, ada dua penyebab yang mengakibatkan kekuatan daya tahan material terlampaui. Pertama adalah konsentrasi tegangan yang disebabkan oleh keausan bantalan pada poros. Kedua adalah peningkatan ketegangan sabuk yang disebabkan oleh peningkatan kecepatan mesin beberapa bulan sebelum kegagalan. Meskipun salah satu bisa menjadi penyebab, kehadiran keduanya mempercepat patah lelah poros. Hal ini mengakibatkan kegagalan drive yang fatal saat poros retak.
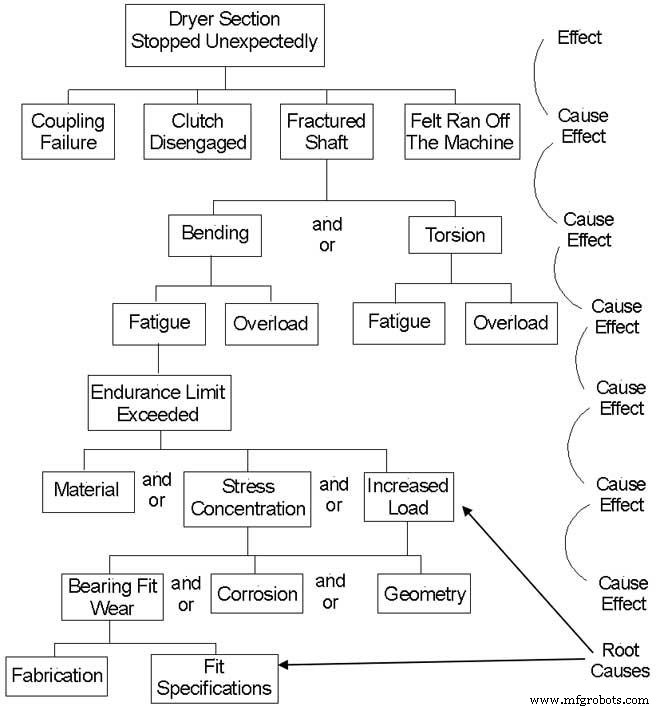
Gambar 3. Pohon faktor penyebab bagian mesin pengering kertas
Mode Kegagalan dan Analisis Efek
Mode kegagalan dan analisis efek (FMEA) sejauh ini merupakan alat analisis akar penyebab paling komprehensif dan kompleks yang tersedia. Ini dapat dikombinasikan dengan analisis kekritisan atau analisis pohon kesalahan untuk lebih mengidentifikasi mode kegagalan dengan kemungkinan terbesar keparahan konsekuensi. Ini adalah proses induktif yang dapat dimulai pada tingkat komponen (poros, roda gigi bantalan, dll.) atau pada tingkat fungsional (pompa pengisian, hidrolik tekan, dll.).
FMEA adalah tingkat tinggi, rinci, "bagaimana jika" analisis masalah. Analisis dasar “bagaimana jika” ditunjukkan pada Gambar 4. Ini mencakup metode curah pendapat menggunakan pertanyaan “bagaimana jika” untuk mengidentifikasi kemungkinan variasi dan kekurangan dalam suatu sistem. Setelah diidentifikasi, kekhawatiran ini dan konsekuensi potensialnya dievaluasi untuk risiko.
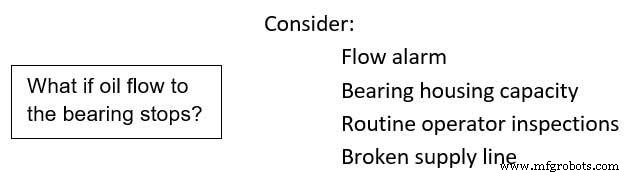
Gambar 4 . Pernyataan sederhana "bagaimana jika"
Ini membantu untuk memikirkan proses FMEA sebagai proses "bagaimana jika" yang sangat rinci dan ketat.
Analisis FMEA dimulai dengan definisi sistem yang akan dipelajari dan berkembang melalui serangkaian langkah sampai koreksi dibuat dan tindak lanjut untuk menilai efektivitasnya selesai. FMEA dikembangkan untuk mengevaluasi dampak kegagalan komponen dalam suatu sistem. Ini digunakan untuk mengidentifikasi di mana kegagalan dapat terjadi (mode kegagalan) dan dampak dari kegagalan tersebut (efek).
Keuntungan
FMEA paling berguna dalam perencanaan kontinjensi dimana digunakan untuk mengevaluasi dampak dari berbagai kemungkinan kegagalan (kontinjensi). FMEA dapat digunakan sebagai pengganti analisis “bagaimana jika” jika diperlukan detail yang lebih besar.
Ketika dikombinasikan dengan analisis kekritisan, analisis secara sistematis akan membangun hubungan antara penyebab dan efek kegagalan, serta kemungkinan terjadinya, dan akan menunjukkan mode kegagalan individu untuk tindakan korektif. Ketika FMEA digunakan untuk melengkapi analisis pohon kesalahan, lebih banyak mode dan penyebab kegagalan dapat diidentifikasi.
Batasan
FMEA banyak digunakan dalam penerbangan dan beberapa industri, tetapi memiliki keterbatasan sebagai berikut:
-
Waktu dan upaya yang diperlukan untuk menyelesaikan analisis
-
Pengenceran upaya dengan kasus-kasus yang tidak penting
-
Ketidakmampuan untuk menangani peristiwa kegagalan gabungan
-
Biasanya tidak menyertakan interaksi manusia
-
Ini memeriksa bahaya yang terkait dengan kegagalan, bukan selama operasi normal
Analisis Pohon Kesalahan atau Logika
Sebuah kesalahan atau pohon logika adalah proses untuk menemukan akar fisik, manusia, dan laten dari sebuah kegagalan. Ini dimulai dengan pernyataan masalah yang menggambarkan kegagalan. Deskripsi yang akurat dari kegagalan sangat penting untuk keberhasilan konstruksi pohon logika. Deskripsi kegagalan bersifat fungsional atau komponen.
Kegagalan fungsional menggambarkan variasi dari keadaan yang diinginkan, seperti pompa tidak memasok tekanan yang diperlukan atau tidak dapat mempertahankan kecepatan desain tanpa getaran yang meningkat. Mereka harus dijelaskan secara kuantitatif. Analisis pohon kesalahan pada Gambar 4 dimulai dengan kegagalan fungsional pompa; tidak ada aliran dari pompa. Jika pompa mampu menghasilkan beberapa aliran, aliran atau tekanan harus disertakan.
Kegagalan komponen menggambarkan keadaan komponen tertentu. Dalam hal ini, analisis akan dimulai dengan pernyataan, seperti poros girboks patah atau bantalan konveyor tempel gagal.
Langkah kedua mencantumkan mode kegagalan tepat di bawah deskripsi kegagalan. Kesalahan umum adalah mendaftar setiap kemungkinan mode kegagalan. Kebijaksanaan diperlukan untuk membuat daftar yang relevan dengan kegagalan. Misalnya, fraktur adalah mode kegagalan bantalan, tetapi jika bantalan tidak retak, itu bukan mode kegagalan. Akan sangat membantu untuk bertanya, “Bagaimana bisa …?”
Sebuah hipotesis untuk setiap mode dibuat, dan kemudian setiap hipotesis diuji menggunakan bukti. Jika bukti tidak dapat mendukung hipotesis, hipotesis tidak digunakan.
Proses ini diulang sampai akar fisik tercapai. Iterasi tambahan akan diperlukan untuk sampai pada akar manusia dan akar laten. Seseorang harus bertanya, “Bagaimana bisa…?” diikuti oleh “ Apa yang dikonfirmasi oleh bukti?” Ingat, setiap hipotesis harus diuji dan diverifikasi dengan bukti. Di sinilah banyak upaya analisis akar masalah mendapat masalah.
Keuntungan
Analisis pohon kesalahan sangat baik untuk menunjukkan seberapa tahan sistem terhadap satu atau beberapa kesalahan awal. Itu bisa dimulai pada tingkat fungsional atau komponen. OSHA mengakui analisis pohon kesalahan sebagai metode yang dapat diterima untuk analisis bahaya proses dalam standar manajemen keselamatan prosesnya.
Batasan
Pohon kesalahan dan logika memerlukan definisi masalah yang cermat. Tergantung pada definisi masalah, tidak selalu menemukan semua kemungkinan kesalahan awal. Jika cakupan masalahnya terlalu besar, proses menjadi macet dalam analisis elemen non-konsekuensial, dan ini menjadi pendekatan senjata pencar untuk mencoba dan mengatasi akar yang bukan penyebab kegagalan.
Contoh pada Gambar 5 adalah pohon logika untuk pompa yang berhenti memompa. Pembongkaran pompa mengungkapkan poros retak. Fraktur kelelahan yang menyebabkan pompa gagal dimulai pada konsentrasi tegangan. Ini adalah akar fisik. Penyelidikan lebih lanjut menemukan poros pompa telah dibuat dari cetakan yang tidak menentukan jari-jari di lokasi kritis. Penghilangan jari-jari adalah salah satu akar manusia. Pencetakan poros pompa telah dibuat sebagai langkah pemotongan biaya, sehingga poros pompa dapat dibuat oleh penawar biaya terendah. Upaya untuk memotong biaya adalah salah satu akar organisasi atau laten.
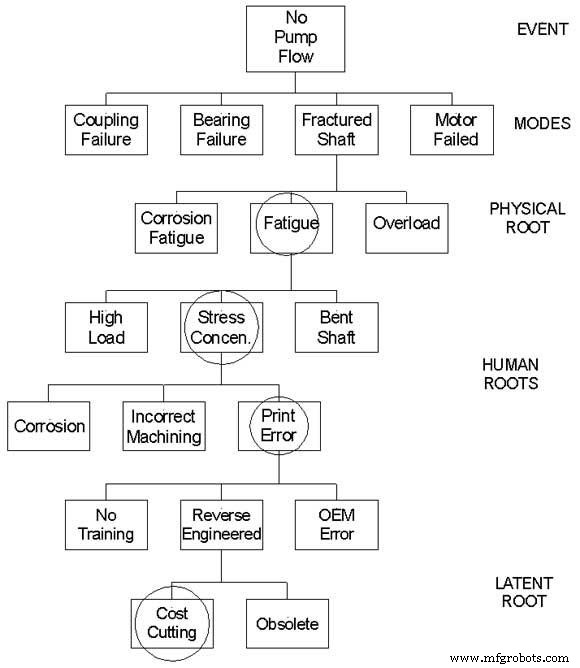
Gambar 5 . Analisis pohon kesalahan dari kegagalan fungsi pompa
Analisis Hambatan
Analisis penghalang memeriksa jalur melalui mana bahaya dapat mempengaruhi target. Ini mengidentifikasi hambatan atau kontrol aktual atau potensial yang digunakan untuk melindungi target. Target harus ada dalam serangkaian kondisi tertentu. Gagasan tentang target berarti bahwa hampir semua hal bisa menjadi target — peralatan, data, bangunan, atau orang.
Selanjutnya, cara target terkena dampak buruk disebut bahaya. Efek samping adalah segala sesuatu yang menggeser target di luar rangkaian kondisi yang ditentukan. Kemudian menjadi mungkin untuk mengidentifikasi pasangan target dan bahaya secara unik melalui jalur di mana bahaya mempengaruhi target.
Setelah bahaya, target, dan jalur di mana bahaya mempengaruhi target diidentifikasi, kontrol dan penghalang yang digunakan untuk melindungi, mengurangi kerusakan, dan/atau mempertahankan target dalam serangkaian kondisi tertentu dapat dijelaskan.
Hambatan dan kontrol biasanya dirancang ke dalam sistem untuk melindungi orang, peralatan, data, dll. Semua bahaya mungkin tidak diidentifikasi selama desain atau ada jalur yang tidak dikenali. Hambatan dan kontrol yang ada mungkin tidak ada, atau bahkan jika ada, mungkin tidak seefektif yang semula dimaksudkan. Akibatnya, target mungkin tidak memiliki perlindungan yang memadai.
Tujuan dari analisis penghalang adalah untuk mengidentifikasi jalur yang tidak terlindungi atau penghalang dan kontrol yang tidak lagi efektif. Secara historis, energi yang dapat menyebabkan kerusakan telah digunakan untuk mengkarakterisasi jalur. Jalur dapat mencakup listrik, mekanik, cairan, kimia, panas, radiasi, dll. Akibatnya, penghalang dan kontrol bersifat fisik atau berhubungan dengan bahaya fisik.
Analisis penghalang pada Gambar 6 adalah sistem pemantauan pelumasan tipikal yang ditemukan di banyak turbin. Bahayanya adalah hilangnya bantalan film cairan dari aliran oli yang tidak mencukupi. Hambatan pencegahan termasuk instrumentasi untuk memantau suhu, aliran dan level minyak reservoir. Selain pemantauan, penghalang tambahan dari pompa minyak siaga dan darurat digunakan. Mitigasi dimulai ketika tingkat alarm terlampaui, yang memerlukan intervensi operator. Hambatan terakhir adalah penghentian turbin darurat yang dapat dipicu oleh suhu bantalan dan hilangnya aliran oli.
Perubahan kondisi target, baik fisik maupun non fisik, dapat merugikan atau tidak diinginkan. Sekarang, pertimbangan mekanisme selain fisik mengarahkan perhatian ke area yang lebih berbasis pengetahuan, perangkat lunak, kebijakan atau administratif.
Keuntungan
Analisis hambatan memiliki keuntungan karena secara konseptual sederhana, mudah digunakan, membutuhkan sumber daya minimal dan bekerja dengan baik dengan metode analisis akar penyebab lainnya. Hasil analisis segera diterjemahkan ke dalam tindakan korektif.
Batasan
Namun, analisis hambatan bersifat subjektif. Tidak ada dua analis yang sama dan tidak akan selalu mencapai kesimpulan yang sama atau serupa. Hal ini juga mudah membingungkan penyebab dan tindakan pencegahan, sehingga tidak boleh digunakan sebagai metode tunggal untuk menentukan akar penyebab.
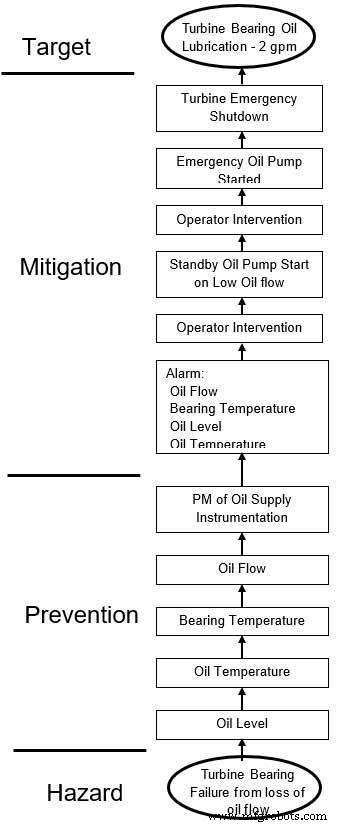
Gambar 6. Analisis penghalang sistem pemantauan pelumasan turbin
Analisis Perubahan/Kepner-Tregoe
Analisis perubahan membandingkan spesifikasi masalah atau peristiwa tunggal dengan situasi yang diinginkan sehingga perubahan dan/atau perbedaan dapat ditemukan dengan membandingkannya. Situasi yang diinginkan dapat berupa tugas atau operasi yang telah dilakukan dengan benar sebelumnya, tugas atau operasi serupa, atau model rinci atau simulasi tugas atau operasi.
Penyebab potensial dipelajari, dan mereka yang membutuhkan asumsi atau kondisi tambahan paling sedikit diuji untuk memverifikasi penyebab yang sebenarnya. Keberhasilan bergantung pada keakuratan spesifikasi penyimpangan dan pengujian verifikasi.
Keuntungan dari analisis perubahan adalah:
- Kemampuan untuk menemukan penyebab langsung penting yang tidak jelas atau tersembunyi.
- Hasil analisis bermigrasi dengan mudah ke tindakan korektif.
- Ini melengkapi metode lain.
- Ini berfungsi paling baik untuk menganalisis kegagalan fungsional.
Batasan analisis perubahan adalah:
- Harus ada dasar untuk membandingkan.
- Ini hanya berfungsi untuk satu penyimpangan tertentu.
- Ini hanya mengidentifikasi penyebab langsung penyimpangan.
- Hasilnya mungkin tidak konklusif, dan pengujian akan diperlukan.
Kepner-Tregoe adalah analisis perubahan yang disempurnakan yang menggunakan empat kategori (siapa, di mana, kapan dan sejauh mana) dan dua filter (ada dan tidak) untuk mengembangkan daftar karakteristik yang menggambarkan kondisi menyimpang. Masing-masing karakteristik menyimpang atau kombinasinya menjadi penyebab potensial dari kondisi menyimpang secara keseluruhan. Dalam sistem Kepner-Tregoe, analisis perubahan disebut analisis masalah. Ini adalah salah satu dari tiga alat yang digunakan untuk mengevaluasi suatu masalah.
Proses Kepner-Tregoe biasanya dimulai dengan penilaian situasi untuk memperjelas situasi masalah (apa yang terjadi) dan kemudian menggunakan salah satu dari himpunan bagian berikut untuk menyelesaikan analisis. Hubungan metode ini ditunjukkan pada Gambar 7.
-
Analisis masalah:Di sini penyebab sebenarnya dari masalah dan hubungan antara sebab dan akibat dicari (mengapa itu terjadi).
-
Analisis keputusan:Berdasarkan kriteria pengambilan keputusan, pilihan dibuat untuk sampai pada penyelesaian masalah potensial (bagaimana kita harus bertindak).
-
Analisis masalah potensial:Potensi masalah di masa depan diantisipasi, dan tindakan pencegahan dikembangkan (apa hasilnya).
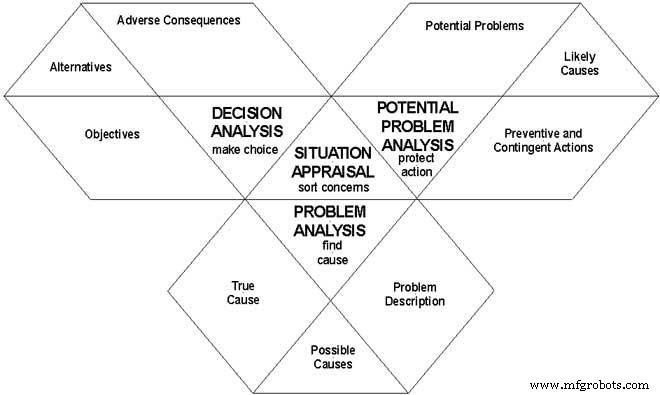
Gambar 7 . Model Kepner-Tregoe
Alat Statistik
Ada lusinan metode dan alat statistik yang tersedia. Mereka biasanya digunakan untuk menggambarkan proses dan variasi produk. Informasi statistik berguna untuk mengidentifikasi tren kinerja peralatan seperti mean time between failure (MTBF), mean time to repair (MTTR), kepatuhan jadwal, backlog perintah kerja, usia perintah kerja, dll. Alat statistik biasanya tidak dianggap sebagai alat analisis kegagalan, tetapi pentingnya mereka dalam mengidentifikasi tren dan penyimpangan dari hasil yang diinginkan sangat penting untuk upaya pemeliharaan yang berhasil. Salah satu alat statistik penting yang sering digunakan dalam analisis kegagalan peralatan adalah bagan Pareto.
Analisis Pareto
Teori Pareto dikembangkan oleh ekonom Italia Vilfredo Pareto pada tahun 1897 untuk menjelaskan distribusi kekayaan yang tidak merata. Dr. J.M. Juran mulai menerapkan prinsip ini pada analisis cacat, memisahkan "beberapa yang vital" dari "banyak yang sepele", dan menyebutnya "bagan Pareto". Ini sering disebut sebagai aturan 80-20, karena 20 persen masalah menyebabkan 80 persen masalah, atau jumlah masalah yang relatif kecil menyebabkan bagian masalah yang sangat besar.
Bagan Pareto menunjukkan frekuensi relatif cacat dalam urutan peringkat, memungkinkan seseorang untuk mengatur upaya keandalan untuk "mendapatkan hasil maksimal" atau "memilih buah yang menggantung rendah".
Anda dapat membuat bagan Pareto menggunakan hampir semua spreadsheet atau perangkat lunak bagan. Bagan pada Gambar 8 menunjukkan hasil analisis Pareto yang sebenarnya. Fixing the first item in the chart decreased maintenance expenditures by more than $1 million per year and most importantly allowed maintenance resources to be used for other reliability work. The first five items in the chart resulted in $18 million in increased revenue per year.
The Pareto chart is a simple-to-use and powerful graphic to identify where most problems in a plant originated. It won’t help with catastrophic failures but is an extremely useful tool for finding the chronic problems that over time consume as much of reliability and maintenance resources as catastrophic failures.
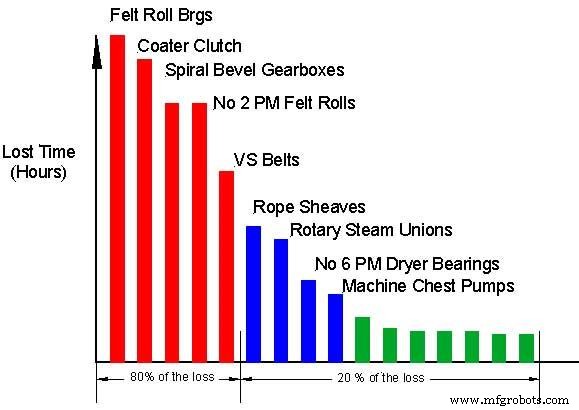
Figure 8. Pareto chart
Data Analytics
In manufacturing and process industries, the Internet of Things (IoT) or data analytics is an application of statistical methods to process data. Data analytics in failure analysis is typically confirmation or disproving of an existing hypothesis or discovering new information in the data.
Data analytics is a process of inspecting, cleansing, transforming and modeling data with the goal of discovering useful information, suggesting conclusions and supporting decision-making (Figure 9).
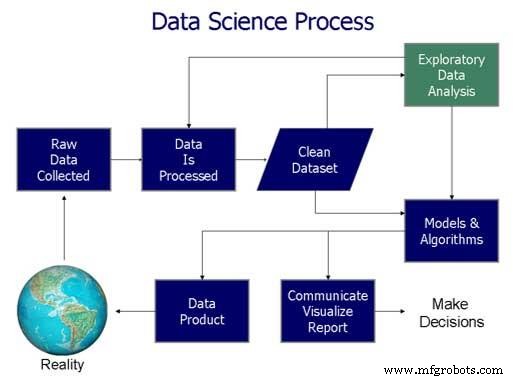
Figure 9. Data science process flow chart from "Doing Data Science" by Cathy O'Neil and Rachel Schutt
When one hears about “big data,” Google, Facebook, Amazon, Apple and other consumer companies come to mind, as organizations that gather enormous amounts of data about us and through data science use it to predict how we will behave in the future. Targeted ads are just one example.
In manufacturing and process industries, the situation is different. The development of wireless sensors has enabled us to inexpensively collect vast amounts of data. We can quickly gather process data and use statistical methods to confirm or discover new relationships in our factories and plants. A decade ago, monitoring a process variable, such as temperature, required installation and wiring a temperature RTD with power and a connection back to a PLC or DCS so data could be captured. Now, it is possible to install a self-powered RTD and transmitter with a wireless data link to the IoT.
A variety of statistical tools can be applied to the data to confirm or refute hypothesis or discover new relationships between process variables. This ability adds a powerful tool to a root cause analysis, particularly of functional failures. Depending on the data quality in maintenance history, it is also possible to discover hidden relationships within the maintenance data using text analytics.
The number of people employed in industry is shrinking. Experience and knowledge is walking out the door in the form of retiring baby boomers. Data analytics shows promise to help close the gap between a shrinking knowledge base and the need for better root cause analysis. In the world of mechanical failure analysis, a gap between the need for spectral vibration data and data analytics still exists. Overall vibration levels can be processed, but data analytics software has considerable room for improvement in the treatment of spectral vibration data.
In the next decade, you can expect to see an accelerating shift toward smart instruments, the IoT and data analytics. For example, think how a control valve positioner can automatically calibrate and configure itself, do diagnostics to maintain loop performance levels, improve control accuracy to reduce process variability, and tell you about it.
Pitfalls in Root Cause Analysis
There is a strong temptation to place blind faith in particular root cause analysis models. After all, they have been proven to work, and why reinvent the wheel? Predefined structured processes can save valuable time. However, it is important to remember that the answers may lie outside a chosen process. Models can be useful because they help strip away unimportant data. If we use models without knowledge of their assumptions and limitations, we may miss important facts and misdirect our analysis.
Do not try to include too much in your analysis. The temptation is strong to add in every possible cause even when they are not necessary, sufficient or present to cause an effect. Remember, inclusivity does not guarantee you are effective or correct.
Verify all the evidence and hypothesis. It is very easy to take the wrong path if a hypothesis is wrong. Be aware that just because the boss has a hypothesis, it isn’t necessarily correct.
Deciding where to start and how you describe the failure has an enormous impact on the time effort and outcome of your investigation. Starting with a functional failure when there has been environmental impact, injury or substantial cost helps with the discovery of the human and organizational root causes that with few exceptions are present and play significant roles in the failure. When a failure does not result in environmental, injury or significant expense, beginning at the component level helps streamline the analysis and typically makes identification of the physical roots easier. As the analysis progresses, the degree of investigation into human and organizational causes can be balanced against the level of risk and cost acceptable to you and the organization.
Making It Happen
Ideally, it would be nice to have a full complement of root cause analysis tools in your plant. Choices must be made because one doesn’t have unlimited time and money. The choices become easier to make if one takes a moment to consider where the need is, how often a root cause analysis will be needed, and what resources are available. If the need is greatest for functional failures or product quality and efficiency problems, the tools used will be different than those used for component failures. If you are reading this article, it is reasonable to conclude your focus will be on component failures. Table 1 summarizes the time required.
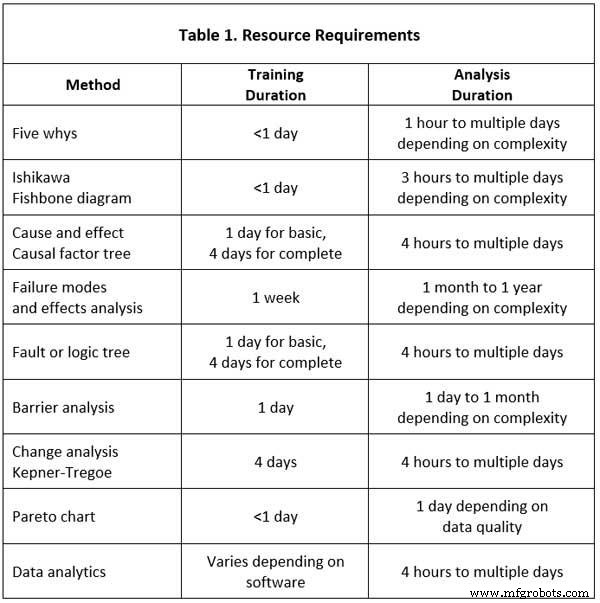
Identifying and understanding the root causes of component failures is best when started on the shop or production floor. Technicians and front-line supervisors who can identify physical failure modes and use basic but powerful analysis tools are often the best means to prevent failures from happening in the future. Technicians and front-line supervisors would have the following skills:
-
Five whys – Learning five why analysis can be done in less than a day. The CMMS must be able to support what is learned from a Five Why analysis either with failure modes or a means to capture causes.
-
Ishikawa/fishbone diagram – This also can be taught in less than a day. It introduces people to a broader cause and effect analysis to identify effects that may have multiple causes.
-
Barrier analysis – An introduction to barrier analysis helps shift culture from simplistic solutions to the concept of risk and risk reduction.
-
Causal factor tree or fault tree analysis – Not everyone needs to be able to construct a tree, but they should be able to participate in the development of one when led by a facilitator. People closest to the point of action have information and insights that are frequently vital to identify root causes and more importantly make changes to prevent future failures. Training to introduce people to either causal factor or fault trees typically takes one day to complete.
-
Failure mode identification – This is frequently considered as a subset of the root cause analysis methods. Frequently, incorrectly identified failure modes lead analysis efforts astray. Technicians, front-line supervisors and reliability engineers must be able to correctly identify physical failure modes. This training takes four days to complete. It also helps a Pareto analysis because failure modes are correctly identified.
In every plant, there should be at least one person who has received facilitator training on causal factor or fault tree analysis and change analysis. This helps ensure consistency and reinforces the use of root cause analysis. Vendors of these methods frequently tout their system as superior to others. They all have certain strengths and weaknesses. Causal factor and fault tree analysis are very similar, so having both may lead to confusion. It is important that one is selected and used. Training for each of these methods usually takes four or five days to complete.
Reliability engineers should receive training on the following:
-
Five whys
-
Ishikawa/fishbone diagrams
-
Cause and effect/causal factor tree
-
Fault or logic tree
-
Pareto chart
-
Change analysis
-
Statistical methods - If they are involved in production issues, training on statistical methods including data analytics should be included.
Unless there is personal injury, an environmental accident or a large cost involved, don’t start every effort with an expensive analysis. You can often be more effective by using the five whys, Ishikawa/fishbone or a simple cause and effect analysis to solve many problems. A situation appraisal may help you select another method when it appears the problem can be solved with a simpler method. Causal factor trees, fault or logic trees can take a substantial amount of time to complete. This can range from a day to several weeks. Failure mode and effect analysis takes weeks or months to complete.
Additional Resource
A resource you may find useful for additional information on root cause analysis:
The Rootisseriet. This website has a wealth of articles on root cause analysis as well as links to additional resources.