Penggabungan otomatis struktur komposit termoplastik logam-logam
Mengaktifkan penggabungan skala industri
FlexHyJoin mendemonstrasikan proses produksi massal untuk memproduksi pengaku atap komposit termoplastik dengan braket logam yang dilas untuk dirakit menjadi bodi logam berwarna putih, seperti kasus penggunaan proyek, Fiat Panda mobil kota. Sumber | IVW
Struktur komposit logam hibrida terus menarik untuk aplikasi otomotif dan dirgantara, menawarkan pengurangan bobot dan peningkatan kinerja dengan menempatkan "bahan yang tepat di tempat yang tepat." Komposit termoplastik (TPC) menarik untuk struktur multi-material seperti itu karena pemrosesannya yang cepat, termasuk kemampuan untuk dilas dan dibentuk secara termoplastik. Namun, menggabungkan komposit ke logam, sampai sekarang, sebagian besar mengandalkan pengencang mekanis, yang membutuhkan lubang pengeboran yang merusak serat bantalan beban. Ikatan perekat juga telah digunakan, tetapi sejumlah termoplastik sulit untuk merekat dengan cara ini; juga, perekat menambah bahan dan berat. Misalnya, BMW i3 , yang menggunakan sasis plastik yang diperkuat serat karbon (CFRP) dan panel bodi plastik, menggunakan 16 kilogram perekat, yang sebagian menangkal potensi penghematan berat komposit.
FlexHyJoin adalah proyek yang didanai oleh program penelitian dan inovasi Horizon 2020 Uni Eropa, yang dilakukan dari Oktober 2015 hingga Desember 2018, yang berupaya mengatasi tantangan bergabung dengan TPC dan suku cadang logam. Dikoordinasikan oleh Institut für Verbundwerkstoffe (IVW) — lembaga penelitian nirlaba dari negara bagian Rhineland-Palatinate dan Universitas Teknik Kaiserslautern, Jerman — FlexHyJoin mengumpulkan 10 mitra dari seluruh Eropa untuk mengembangkan proses otomatis yang memungkinkan atap otomotif TPC struktur yang akan dirakit menjadi metal body-in-white (BIW). Strateginya adalah menghasilkan sambungan berkekuatan tinggi dan netral berat — tanpa perekat atau pengencang — dengan pra-perawatan laser braket logam dan menempelkannya ke pengaku atap melalui induksi dan penyambungan laser. Hal ini dicapai dalam satu sel produksi otomatis dengan kontrol proses terintegrasi dan pengujian tak rusak (NDT) sebaris.
Demonstrator hibrida dalam 140 detik
Mitra proyek Centro Richerche Fiat (Pomigliano d'Arco/Naples, Italia) menyediakan spesifikasi untuk bagian demonstran — pengaku atap untuk Fiat Panda city car yang saat ini dibuat dari baja. Untuk FlexHyJoin, bagian tersebut dibentuk secara termoplastik dari komposit termoplastik (Gbr. 1) oleh Gubesch Thermoforming (Wilhelmsdorf, Jerman) menggunakan organosheet Tepex Dynalite 102 anyaman serat gelas/poliamida 6 (PA6) setebal 1,5 milimeter yang dipasok oleh Bond-Laminates (Brilon, Jerman). Untuk menggabungkan pengaku atap TPC ini ke Panda baja BIW, satu set braket samping (kiri dan kanan) yang terbuat dari baja DC04 setebal 0,7 milimeter yang disambungkan dengan laser ke ujungnya. Braket tengah yang terbuat dari bahan yang sama dipasang menggunakan penyambungan induksi. FlexHyJoin menunjukkan bahwa kedua metode penyambungan dapat digunakan untuk produksi struktur hibrid industri.
Gbr. 1 Penataan permukaan untuk penggabungan hibrida
FlexHyJoin mendemonstrasikan penyambungan laser dan induksi dari braket baja ke pengaku atap GF/PA6 yang dicap (atas ). Sambungan hibrida ini mengandalkan perawatan permukaan braket logam untuk membuat undercut, yang diisi dengan plastik leleh selama langkah proses penyambungan (bawah ).
Sumber | IVW
Hanya dengan melelehkan matriks PA6 ke braket baja tidak akan menghasilkan sambungan dengan kekuatan yang cukup untuk memenuhi persyaratan struktural. Dengan demikian, perawatan permukaan laser diperlukan sebelum bergabung. “Permukaan braket disusun oleh laser untuk membuat undercut,” jelas Johannes Voithofer, manajer proyek di Fill Gesellschaft (Gurten, Austria), yang ditugaskan untuk merakit dan mengintegrasikan sel produksi otomatis. “Kurung yang dirawat ditempatkan ke bagian komposit. Panas dan tekanan kemudian diterapkan selama penyambungan, menyebabkan matriks PA6 dari komposit mengalir ke undercut yang diinduksi laser [lihat Gambar 1].” Proses penataan dikembangkan oleh mitra lain, Institut Teknologi Laser Fraunhofer (ILT, Aachen, Jerman), dan menghasilkan sambungan komposit logam yang menggabungkan adhesi material serta penguncian mekanis.
Bagian yang digabungkan kemudian ditransfer ke stasiun NDT di mana mereka dipindai untuk cacat menggunakan jenis termografi. “Lampu sorot halogen digunakan untuk pemanasan termodulasi pada permukaan komposit,” jelas Vitalij Popow, rekan peneliti IVW dan pemimpin pengembangan FlexHyJoin NDT dan kontrol proses. “Ini mengarah ke medan suhu berosilasi dalam struktur komposit. Kami menganalisis respons termal di permukaan dari waktu ke waktu dan mengidentifikasi cacat pada sambungan.” Pengujian otomatis sepenuhnya diselesaikan dalam sel produksi untuk setiap komponen yang diproduksi. Validasi proses dilakukan pada sekitar 400 sambungan.
Sel produksi otomatis FlexHyJoin, seperti yang dikonfigurasi saat ini, menjalankan penataan laser, penyambungan, dan NDT secara paralel dengan waktu siklus masing-masing 81 detik, 98-108 detik, dan 100 detik, tidak termasuk waktu untuk transfer robotik suku cadang antar stasiun. Voithofer mengatakan waktu siklus per bagian hibrida yang telah selesai kira-kira 140 detik.
Gbr. 2 Mengaktifkan penggabungan skala industri
Sel produksi percontohan FlexHyJoin memiliki tiga stasiun modular untuk penataan permukaan, penyambungan, dan NDT. Robot penanganan tunggal sel memindahkan komponen dari laci pemuatan ke masing-masing stasiun ini, menempatkan komponen hibrida yang sudah jadi di laci yang bersebelahan. Sumber | IVW dan Isi
Penataan laser
Proses penataan laser menghasilkan garis dengan geometri undercut pada permukaan penyambungan braket logam. Untuk FlexHyJoin, undercut berukuran lebar 75 mikrometer dan kedalaman 215 mikrometer. Pengukuran ini, serta jumlah garis dan pola garis keseluruhan dapat disesuaikan, dan idealnya disesuaikan untuk memenuhi persyaratan waktu paruh dan siklus.
“Posisi serta jumlah struktur mikro pada permukaan penyambungan dapat disesuaikan dengan beban dalam komponen,” jelas Stefan Weidmann, rekan peneliti IVW dan pemimpin tim pengembangan untuk unit penyambungan induksi FlexHyJoin. “Jarak antara struktur mikro dapat dikurangi di area dengan beban tinggi pada permukaan penyambungan dan ditingkatkan di area dengan beban lebih sedikit untuk memungkinkan proses mikrostruktur yang efisien.”
Penataan dicapai dengan mengikis permukaan braket logam menggunakan laser serat mode tunggal berdaya tinggi yang dipasok oleh IPG Photonics (Burbach, Jerman). Laser YLR-1000-WC ini memiliki output maksimum 1.000 watt pada panjang gelombang emisi 1.070 nanometer. “Kami menggunakan laser serat mode tunggal untuk proses mikrostruktur karena kemampuan fokusnya yang tinggi, mempertahankan ukuran titik sekitar 40 mikrometer,” jelas Christoph Engelmann, pemimpin tim pemrosesan polimer di Fraunhofer ILT.
Laser terkandung dalam kepala optik yang dipasang ke lengan robot ABB 1200. “Di dalam kepala optik, kami memiliki dua cermin galvanometrik untuk membelokkan sinar dalam bidang kerja 240 milimeter kali 240 milimeter,” Engelmann merinci. “Selain itu, ada satu lensa bergerak untuk melacak ketinggian-z (z-shifter). Kami hanya menggunakan robot untuk memposisikan kepala pemindai di atas komponen logam, dan kemudian sinar dibelokkan oleh cermin dan posisi z untuk setiap garis tunggal dari struktur mikro disesuaikan dengan z-shifter. Dengan demikian, tidak ada gerakan kepala selama pemrosesan. Dengan cara ini, kami dapat menangani bagian 2.5D, tetap pada posisi z yang sama untuk setiap garis terpisah tetapi dapat menyesuaikan antar garis.”
“Untuk alasan keamanan, baik unit penataan dan penyambungan tertutup,” jelas Voithofer, mencatat lemari hitam di sel produksi percontohan (Gbr. 2). Dengan demikian, gerbang/pintu otomatis tetap diturunkan selama operasi laser, membuka untuk melepas bagian yang sudah jadi dan memasukkan yang baru.
Gbr. 3 Induksi dan laser bergabung dengan sel
Pada sel penyambung, penyambungan induksi digunakan untuk memasang braket tengah sedangkan penyambungan laser digunakan untuk menyambungkan braket samping di setiap ujung busur atap komposit. Sumber | IVW dan Isi
Induksi dan penyambungan laser
Berdekatan dengan sel penataan adalah sel penyambung, yang terdiri dari dua operasi berbeda:penyambungan induksi pada braket tengah dan penyambungan laser pada braket sisi kiri dan kanan. “Untuk bagian yang lebih besar dengan kompleksitas sedang seperti braket tengah, penyambungan induksi adalah metode penyambungan yang lebih cocok,” kata Weidmann. “Alat konsolidasi keramik dengan induktor memberikan tekanan pada area penyambungan dan permeabel untuk medan elektromagnetik, yang mengarah ke input energi yang efisien ke braket logam untuk pemanasan. Ini nyaman untuk bentuk datar, tetapi lebih menantang untuk bentuk kompleks, seperti geometri kurung samping. Jadi, lebih efektif menggunakan sambungan laser untuk ini.” Weidmann menambahkan, “Penggabungan induksi paling baik untuk suku cadang besar dan kompleksitas sedang, sedangkan penyambungan laser lebih cocok untuk suku cadang dengan kompleksitas tinggi.”
Sebuah lubang bor di pengaku atap komposit menyelaraskannya di atas perkakas pendukung, dibentuk agar sesuai dengan kelengkungan pengaku thermoformed. Lubang yang dipotong laser di braket tengah menempatkannya di pengaku atap sementara braket samping disejajarkan dengan bentuknya yang cocok dengan ujung pengaku atap.
“Bracket tengah digabungkan menggunakan discontinuous bergabung dengan induksi. “Ini pada dasarnya adalah penyambungan pers kuasi-statis,” kata Weidmann, “yang secara sederhana berarti ini adalah proses statis, mencapai sambungan areal di satu tempat, tetapi ada gerakan dalam arah-z karena ketebalan komposit sedikit berubah karena terhadap tekanan konsolidasi yang diterapkan selama penyambungan (induksi).”
Unit penyambung induksi berisi generator frekuensi tinggi KGR (Brandizzo, Italia) untuk memasok medan listrik bolak-balik ke koil induksi. Kepala digerakkan melalui motor listrik dan spindel (Gbr. 3) sehingga alat konsolidasi keramik menekan braket logam ke bawah. Kumparan induksi pada alat konsolidasi menyebabkan logam menjadi panas, yang melelehkan matriks komposit dan menciptakan sambungan. “Tekanan diterapkan selama pemanasan dan pendinginan,” catat Weidmann.
Penyambungan laser pada braket samping dimulai secara bersamaan hingga penyambungan induksi. Dua perangkat penjepit, yang terletak di kedua sisi perkakas pendukung, dapat menerapkan 4.000 Newton gaya penjepit ke braket samping. “Penjepitan diperlukan untuk meminimalkan celah antara komposit dan komponen logam,” jelas Voithofer. "Ini mencegah rongga di sendi." Setelah gaya penjepit diterapkan, kepala laser bergerak ke posisinya. Dilengkapi dengan laser dioda LineBeam yang dipasok oleh Leister Technologies (Kägiswil, Swiss). Johannes Eckstaedt dari Leister menjelaskan bahwa laser ini memiliki daya keluaran maksimum 600 watt pada panjang gelombang pancaran 980 nanometer. Sinar dibentuk menjadi garis 27 milimeter kali 1 milimeter oleh lensa optik, dan difokuskan pada braket logam. Kepala laser dipasang ke lengan robot yang memungkinkannya bergerak di sepanjang permukaan braket berbentuk. “Kami menetapkan kecepatan yang berbeda untuk setiap area braket untuk mencapai suhu penyambungan yang homogen, mengurangi tekanan termal untuk hasil penyambungan terbaik,” kata Ecstaedt.
Secara umum, penyambungan laser dapat menggunakan penyambungan transmisi atau konduksi panas. Untuk penyambungan transmisi laser, komposit yang disambung harus transparan untuk panjang gelombang laser yang dipilih. Laser kemudian melewati komposit, mengenai permukaan logam braket dan memanaskannya. Namun, metode ini tidak digunakan dalam demonstrator FlexHyJoin karena laminasi organosheet pengaku atap tidak transparan laser. Sebagai gantinya, metode alternatif penyambungan konduksi panas digunakan. Ini hanya menerapkan laser langsung ke permukaan logam, yang menghantarkan panas melalui bahan dasar logam ke komposit, melelehkan matriks PA6 pada 220-300ºC dan membuat sambungan. “Karena konduktivitas termal yang tinggi dari braket baja, panas laser menyebar dengan cepat, secara efisien bergabung dengan braket samping,” kata Voithofer.
Langkah 1. Busur atap TPC dan braket logam dimuat secara manual ke laci bagian sel FlexHyJoin. Laci ditutup dan produksi dimulai.
Langkah 2. Robot mengambil satu set kurung logam dan menempatkannya di sel penataan. Pintu perlindungan laser menutup.
Langkah 3. Di dalam sel penataan, laser serat berdaya tinggi menciptakan undercut pada permukaan braket untuk digabungkan ke pengaku atap komposit.
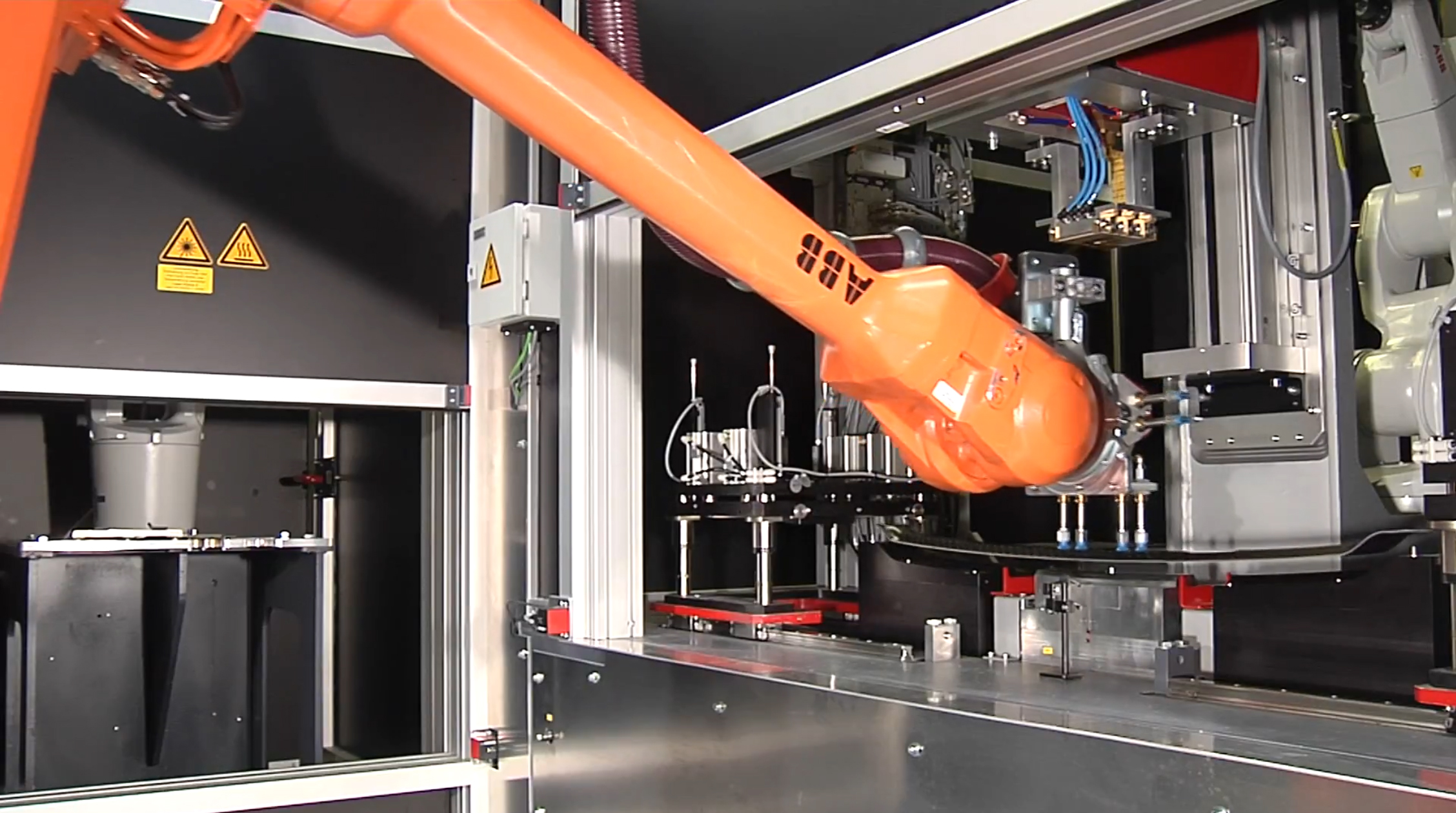
Langkah 4. Sementara braket dirawat dengan laser, robot mengambil busur atap TPC dari laci bagian dan menempatkannya di sel penyambung, di sebelah kanan sel penataan.
Langkah 5. Robot kembali ke sel penataan, mengambil braket yang dirawat dan menempatkannya, dengan struktur menghadap ke bawah, ke haluan atap TPC.
Langkah 6. Robot kemudian menempatkan unit penjepit pada tiga braket. Unit penyambung induksi diturunkan ke braket tengah. Kumparan induksi menyebabkan braket logam menjadi panas, melelehkan matriks PA6 komposit yang mendasarinya.
Langkah 7. Saat penyambungan induksi selesai, unit penyambung laser diturunkan untuk menyambungkan braket sisi kiri dan kanan. Laser memanaskan logam, menyebabkan matriks PA6 di bawahnya meleleh ke bagian bawah, menciptakan sambungan berkekuatan tinggi.
Langkah 8. Struktur hibrid yang lengkap ditempatkan ke dalam sel NDT di mana termografi penguncian digunakan untuk mendeteksi cacat. Lampu halogen memanaskan permukaan komposit dan kamera IR mengukur respons dari waktu ke waktu. Analisis data ini diproses untuk memberikan penilaian kualitas visual.
Bergabung dengan kontrol proses
Metode dasar untuk mengontrol kedua proses penyambungan adalah dengan mengukur suhu dan waktu versus seperangkat parameter yang dioptimalkan yang ditentukan melalui pengujian. “Oleh karena itu, kami memproduksi sampel uji gabungan dengan parameter yang berbeda dan melakukan pengujian mekanis untuk setiap set parameter menggunakan set-up pengujian khusus. Untuk braket samping, kombinasi uji geser dan uji kupas dikembangkan, dan untuk braket tengah kami menggunakan uji beban tekanan, yang sebanding dengan uji geser putaran, tetapi Anda mendorong alih-alih menarik, untuk mendapatkan beban geser di area bergabung, ”kata Popow. Pengaturan pengujian khusus ini dirancang bersama dengan EDAG Engineering GmbH (EDAG, Fulda, Jerman), yang juga melakukan analisis hasil pengujian. Mengikuti prosedur ini, set parameter terbaik untuk proses penyambungan diidentifikasi dan kemudian digunakan dalam sel produksi percontohan.
“Proses penyambungan induksi telah dikalibrasi sebelumnya,” kata Weidmann. “Kami tahu kami mencapai suhu penyambungan setelah sekitar 30 detik, tetapi kami juga mengukur suhu di tempat untuk alasan keamanan guna menghindari panas berlebih.” Sebuah pirometer, yang mengukur radiasi permukaan dari jarak jauh, digunakan untuk mengukur titik panas yang diketahui di area sambungan induksi. “Tapi itu tidak dapat memberikan pengukuran yang akurat dari penyambungan laser karena tingginya tingkat cahaya yang diiradiasi dan panas di tempat,” jelasnya. Namun, sensor kontak dapat digunakan pada sisi komposit dari area penyambungan laser, meskipun tidak berlaku untuk proses penyambungan induksi karena biasanya terbuat dari logam dan akan memanas dengan induksi dan mendistorsi pengukuran.
“Area yang dipanaskan untuk semua sambungan juga ditutupi oleh alat pengepres dan perlengkapan penjepit,” catat Weidmann. “Dengan demikian, kami telah memvalidasi perubahan ketebalan komponen karena tekanan dan panas sebelum dan sesudah bergabung sebagai metode jaminan kualitas.” Perubahan ketebalan ini diukur dengan sensor jarak yang terintegrasi ke dalam alat pemosisian untuk pengaku atap (juga ditunjukkan pada Gambar 3). “Saat kami menekan bagian-bagiannya bersama-sama, sensor jarak dipindahkan,” jelasnya. “Ketika kita menerapkan panas dan tekanan penyambungan, polimer matriks cair mengalir ke dalam rongga struktur laser dan sedikit diperas keluar dari zona penyambungan sampai sambungan mendingin. Ini mengarah pada perubahan ketebalan yang dicatat oleh sensor jarak.” Weidmann dan tim IVW telah menghubungkan jarak ini dengan kualitas bagian. “Perubahan ketebalan — dengan kata lain, pemadatan — lebih besar dari 0,1 milimeter berarti kualitas sambungannya bagus,” catat Weidmann.
NDT sebaris
IVW mengembangkan metode lain untuk jaminan kualitas — pengujian termografi inline. “Untuk jaminan kualitas, tujuan utamanya adalah melihat properti di area join,” jelas Popow. “Tapi ini sangat sulit, jadi kami melakukan termografi pada sisi komposit sambungan setelah bagian itu selesai.”
IVW memilih teknik termografi aktif yang disebut Lock-In Thermography karena menawarkan rasio signal-to-noise yang lebih baik daripada metode aktif lainnya (misalnya, Pulse Phase Thermography) dan juga dapat memeriksa cacat yang lebih dalam. “Ide dasarnya adalah memasukkan panas ke dalam komposit, yang kemudian mengalir ke area sambungan dan kembali ke permukaan,” kata Popow. “Dengan Termografi Terkunci, komponen dirangsang dengan frekuensi yang ditentukan selama beberapa periode. Kami kemudian menganalisis respons ini dari waktu ke waktu. Jika Anda memiliki area antara permukaan komposit dan area sambungan yang tidak homogen karena adanya rongga atau cacat, hal itu akan terlihat dalam respons termal.”
Respons termal ditangkap sebagai gambar. Titik-titik yang membentuk gambar-gambar ini adalah piksel, kependekan dari elemen gambar. Setiap piksel juga merupakan titik pengukuran. Dengan demikian, sinyal suhu untuk setiap piksel di seluruh area inspeksi dianalisis. “Akibatnya, Anda mendapatkan informasi amplitudo dan fase untuk setiap piksel, dan perangkat lunak kemudian merekonstruksinya menjadi gambar lagi, yang dapat diperiksa secara visual,” tambahnya. Tapi itu juga menyediakan set besar pengukuran untuk 126 bagian yang diuji. “Kami telah mengkorelasikan hasil NDT ini dengan hasil pengujian mekanis yang dilakukan oleh EDAG,” kata Popow. Timnya juga menguji area sambungan setelah melepas tanda kurung — yaitu, pengujian destruktif. “Dengan demikian, kami telah mengkorelasikan tiga rangkaian hasil pengujian dan sekarang dapat mengidentifikasi area ikatan kekuatan rendah versus kekuatan tinggi dari analisis visual hasil termografi,” katanya.
Sel terintegrasi untuk produksi massal
Salah satu pencapaian terbesar FlexHyJoin, kata Weidmann, adalah mengintegrasikan semua unit teknologi, masing-masing dikembangkan oleh mitra proyek yang berbeda, ke dalam jalur produksi otomatis yang dioptimalkan. Voithofer, yang mengintegrasikan peralatan di Fill, menjelaskan bahwa “setiap set peralatan yang dikirimkan kepada kami menggunakan pengontrol yang berbeda. Saya harus merancang master PLC untuk mengontrol semua unit proses yang berbeda.” Ini termasuk penutup laser dan robot penanganan sel, yang dipasok oleh Fill. “Juga sangat sulit untuk membuat semua langkah proses ini bekerja bersama karena mereka membutuhkan waktu yang berbeda,” tambahnya.
Voithofer memulai dengan mengembangkan arsitektur untuk setiap unit proses dan robot, dengan mempertimbangkan bagaimana memposisikannya untuk aliran terbaik. “Konsep kami adalah menjaga tiga stasiun — penataan, penyambungan, dan NDT — modular, dalam tiga wadah terpisah,” katanya. “Dengan cara ini, kami dapat mengekstrak unit tunggal dan menggunakannya di pameran dagang atau proyek demonstrasi lainnya, dan kemudian mengembalikannya. Jadi, sel kerja bersifat modular, namun terintegrasi.”
Pengalaman puluhan tahun Fill dalam jenis integrasi sistem untuk produksi komposit serial ini membantu mencapai apa yang dilihat Popow sebagai prestasi terbesar FlexHyJoin:beralih dari skala lab ke skala industri. “Kami adalah konsorsium pertama yang merealisasikan proses seperti ini, yang cocok untuk produksi massal komposit yang disambung dengan logam,” katanya. “Proses ini dapat digunakan untuk banyak suku cadang otomotif seperti tautan stabilizer, bumper, dan pintu,” catat Voithofer. “Ada banyak bagian komposit yang terhubung ke bagian logam dalam BIW yang ringan.”
Adaptasi untuk beberapa industri
Namun, ada beberapa perubahan yang diperlukan sebelum sel dimasukkan ke dalam produksi serial. “Kami tidak akan lagi menyimpan struktur dan penyambungan laser dalam selungkup terpisah, tetapi menggabungkannya menjadi satu,” kata Voithofer. “Ini akan menghilangkan kebutuhan pintu penutup untuk membuka dan menutup di antara proses-proses ini, mengurangi waktu siklus.” Dia juga akan menghubungkan semua stasiun secara linier pada ban berjalan. Jalur tersebut akan berjalan terus menerus, dengan bagian-bagian diambil dan ditempatkan kembali pada konveyor untuk setiap stasiun sebelum keluar dari sel yang siap untuk dirakit menjadi BIW. Ini selanjutnya akan memotong waktu siklus. Selain itu, laci yang diperluas yang mampu mengumpankan ratusan bagian akan memungkinkan saluran bekerja melalui seluruh shift tanpa perlu memasok ulang.
Meskipun sel produksi percontohan ini ditargetkan untuk industri otomotif, Popow mencatat bahwa sel ini dapat dengan mudah disesuaikan dengan kedirgantaraan, barang olahraga/konsumen, dan aplikasi industri. “Itu sebenarnya salah satu pedoman utama,” kata Weidmann, “bahwa itu harus bisa menggabungkan geometri dan bagian yang berbeda. Satu-satunya perubahan yang harus dilakukan adalah alat pemadatan penyambung induksi, perlengkapan penjepit untuk penyambungan laser, dan perkakas pendukung. Bagian utama sel harus tetap sama.” Dia mencatat bahwa IVW juga telah mendemonstrasikan penggabungan hibrida titanium dan baja menjadi komposit organosheet serat karbon/polifenilen sulfida (PPS) dan sekarang sedang mengembangkan demonstrasi polieterketon (PEEK) dan polieterketonketon (PEKK). “Ini hanya membutuhkan adaptasi proses penggabungan untuk suhu yang lebih tinggi dan mendefinisikan ulang parameter proses yang optimal,” kata Weidmann. “Sel ini terbuka untuk berbagai bahan, termasuk aluminium dan tembaga serta sistem matriks komposit termoplastik lainnya seperti polipropilen dan polietilen.”
“Para mitra proyek telah bekerja sama dengan baik dan bersemangat untuk melangkah lebih jauh dalam pengembangan,” katanya. “Kami pikir jenis produksi ini sangat menjanjikan, dan tanggapan yang kami terima dari industri sejauh ini menunjukkan bahwa ada berbagai perusahaan yang melihat janji ini juga.”