Epoxy 2 bagian untuk meningkatkan produksi aerostruktur komposit melalui RTM
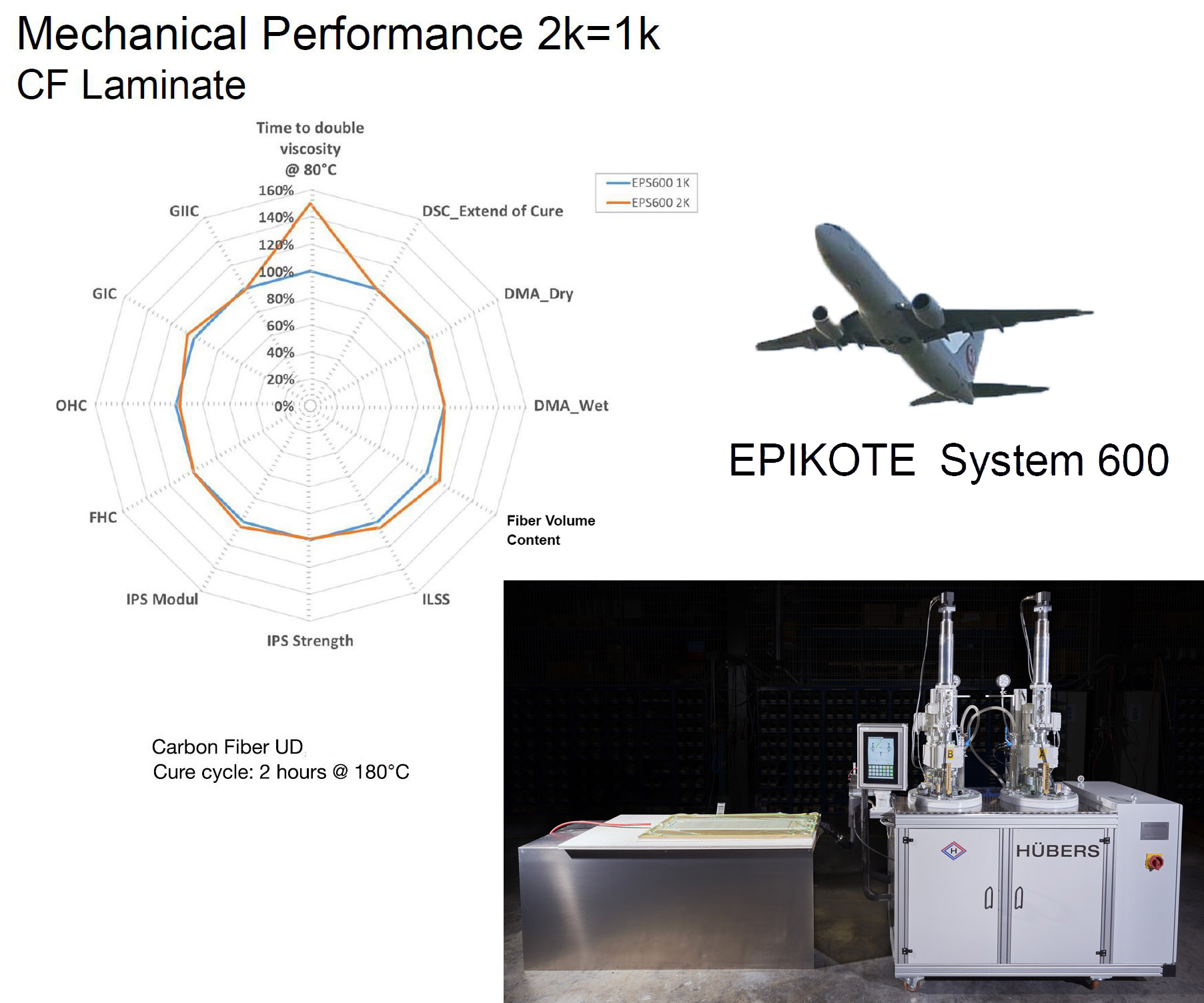
Ini adalah yang ketiga dari seri blog saya tentang teknologi yang harus Anda lihat di CAMX 2019 (23-26 Sep, Anaheim, CA, A.S.). Hexion (Columbus, Ohio, AS) telah mengembangkan sistem dua komponen (2K) untuk RTM aerostruktur berdasarkan resin epoksi Sistem Epikote 600. Pendahuluan di bawah ini akan menjelaskan mengapa perkembangan ini penting. Setelah itu, saya memberikan detail lebih lanjut tentang sistem 2K baru ini dan bagaimana Hexion memenuhi tuntutan OEM dirgantara untuk jaminan kualitas in situ dari resin campuran. Di bagian bawah, saya juga membahas 2K infus/RTM epoxy Hexion untuk aplikasi tahan api (FR).
Mengapa resin 2K untuk RTM?
Awal tahun ini, saya menulis tentang program di spesialis perkakas Alpex Technologies (Mils, Austria) dan anak perusahaan Airbus, Composites Technology Center (CTC, Stade, Jerman) untuk memproduksi suku cadang pesawat komposit menggunakan resin transfer moulding (RTM) . Menggunakan RTM di ruang angkasa bukanlah hal baru. Ada dan telah beragam suku cadang pesawat yang dibuat menggunakan RTM, antara lain:
- Kemudi untuk jet bisnis Gulfstream G250 (Israel Aerospace Industries dan North Coast Composites)
- Pisau dan casing kipas untuk mesin pesawat turbofan LEAP (Albany Engineered Composites)
- Kusen pintu A350 (Helikopter Airbus Donauworth)
- Demonstrasi pintu penumpang A350 (Elbit Cyclone)
- Demonstrasi flap multispar A320 (Airbus Bremen)
- Matrix Composites memproduksi lebih dari 6.000 komponen untuk F-22 menggunakan RTM.
Namun, RTM dalam aplikasi kedirgantaraan secara tradisional merupakan proses bertekanan rendah dengan waktu siklus yang diukur dalam jam. Program di Alpex dan CTC berfokus pada pemanfaatan otomatisasi, injeksi cepat, dan waktu siklus 15 hingga 20 menit ditawarkan oleh RTM tekanan tinggi (HP-RTM). Dalam artikel saya “HP-RTM untuk produksi serial aerostruktur CFRP yang hemat biaya”, saya membahas masalah penggunaan resin epoksi 2 komponen (2K) versus norma saat ini dalam menggunakan sistem 1 komponen (1K) yang sudah dicampur sebelumnya:
“Schiller [Jan Schiller, pemimpin proyek CTC untuk sistem produksi dan kontak utama untuk teknologi RTM] mengamati bahwa semua RTM sebelumnya struktur pesawat hanya menggunakan sistem 1K dicampur oleh pemasok, yang kemudian mensertifikasi campuran dan bertanggung jawab untuk memastikan resin memenuhi persyaratan kualifikasi. “Sekarang kami sedang mempertimbangkan sistem 2K, tetapi tantangannya adalah memastikan kualitas pencampuran ," dia menjelaskan. Sistem 1K premix memerlukan pengiriman dan penyimpanan dingin untuk mencegah reaksi hingga pemrosesan bagian. Dengan demikian, keuntungan sistem 2K mencakup penghapusan biaya ini serta reaktivitas yang lebih tinggi untuk pemrosesan yang lebih cepat.”
“Namun, satu masalah adalah jaminan kualitas (QA) akan ditransfer dari pemasok resin ke produsen suku cadang. “QA ini memerlukan deteksi rasio pencampuran dan kualitas resin campuran . Keduanya dibutuhkan untuk kualifikasi Airbus dari material baru. Jadi, ini berarti pengukuran kedua komponen sesaat sebelum pencampuran dan resin setelah pencampuran . Saat ini, kami hanya memiliki sensor sebelum kepala campuran, yang menunjukkan berapa banyak resin dan berapa banyak pengeras yang dimasukkan ke dalam campuran. Ini tidak cukup untuk kualifikasi.”
Hexion (Columus, Ohio, AS), pemimpin dalam pengembangan epoksi penyembuhan cepat untuk HP-RTM dalam komposit otomotif (lihat “HP-RTM yang sedang naik daun”), mengumumkan pada Maret 2019 bahwa mereka telah mengembangkan sistem 2K untuk RTM aerostruktur berdasarkan resin epoksi Epikote System 600. Saya mewawancarai pemimpin Segmen Epoxy Global Aerospace Hexion, Jean Rivière, untuk mempelajari lebih lanjut tentang sistem 2K mereka untuk kedirgantaraan dan bagaimana mereka memenuhi permintaan ini untuk QA in situ dari resin campuran.
Mengatasi batasan sistem 1K
“Sama seperti prepreg, sistem 1K untuk RTM dan infus di ruang angkasa harus tetap dingin dan memiliki umur simpan yang terbatas,” kata Riviere. “Dengan menggunakan sistem epoksi 2 komponen (2K), Anda menghilangkan kendala ini. Kami telah melihat resin epoksi 2K dan sangat reaktif digunakan dalam pembuatan bilah angin dan struktur otomotif. Jadi mengapa tidak di luar angkasa?”
Rivière menjelaskan bahwa setelah berbicara dengan banyak pelanggan tentang hal ini, Hexion memahami perhatian utama — Anda memerlukan validasi bahwa rasio pencampuran benar setiap saat sebelum injeksi ke dalam cetakan. Tanpa ini, Anda memiliki risiko yang tidak dapat diterima bagi produsen suku cadang,” catatnya. Ia menambahkan, sebelumnya tidak ada permintaan untuk jenis volume produksi yang terlihat pada kincir angin dan otomotif. Namun, sekarang Airbus dan Boeing ingin melampaui tingkat produksi saat ini sambil menargetkan lebih banyak suku cadang komposit per pesawat. “Jadi, sekarang ada kebutuhan untuk beralih dari persiapan persiapan dan menuju epoksi 2K untuk RTM atau infus dirgantara,” kata Rivière.
Dalam diagram rantai pasokan di bawah, teknologi 2K tidak hanya menghilangkan langkah penyimpanan dingin dan penghangatan ulang, tetapi juga menghilangkan batasan ukuran wadah resin untuk pengiriman. “Anda harus menjaga massa resin yang sudah dicampur hingga 20 liter dan menjaga drum tersebut pada suhu yang sangat rendah,” kata Riviere, “atau resin dapat mulai bereaksi. Untuk sistem 2K, drum standar 200 liter dapat dikirim tanpa batasan suhu rendah. Jadi, risikonya lebih kecil, tidak perlu pendinginan yang kuat, dan tindakan pencegahan yang lebih sedikit.”
Rantai pasokan di atas menunjukkan bagaimana kontrol analitik berubah. Sementara hanya kontrol awal yang dilakukan di lokasi manufaktur untuk sistem resin 1K, kontrol diterapkan di beberapa titik kontrol untuk sistem 2K. Selain mengontrol komponen A dan B selama produksi pabrik, rasio pencampuran A:B juga dikontrol secara digital dalam peralatan mix, meter and dispense (MMD) dan sekali lagi sesaat sebelum injeksi resin ke dalam cetakan. SUMBER | Hexion.
Kontrol analitis
Untuk mengembangkan teknologi 2K ini, Hexion bekerja sama dengan Hübers (Bocholt, Jerman), produsen peralatan mix, meter and dispense (MMD), dan Composyst (Hurlach, Jerman) yang memiliki lisensi eksklusif untuk Proses Bantuan Vakum yang dipatenkan Airbus ( VAP) untuk infus. Hübers memiliki reputasi yang kuat untuk sistem MMD berkinerja tinggi yang digunakan dalam pembuatan komponen listrik dan elektronik (misalnya, resin cor dan komponen impregnasi untuk transformator, dll.) sementara Composyst adalah ahli dalam injeksi resin dan infus untuk aplikasi Airbus, dan karenanya , memahami apa yang dicari OEM pesawat sehubungan dengan pemrosesan dan jaminan kualitas (QA) resin campuran.
“Kontrol analitik mulai berlaku setelah komponen A dan B dari epoksi dicampur secara tepat oleh peralatan Hübers dan bersiap untuk dimasukkan ke dalam cetakan,” Rivière menjelaskan. Tabung hitam antara sistem Hübers MMD dan penyetelan infus VAP kantong vakum pada gambar di bawah ini adalah komponen kunci dari sistem kontrol analitik ini. “Di sinilah kami memiliki perangkat analitik yang mengontrol rasio campuran secara real time,” kata Riviere. “Kami telah mendemonstrasikan pengukuran rasio campuran setiap 12 detik, tetapi pengukuran yang lebih sering juga dimungkinkan. Memang, teknologi ini memungkinkan kontrol rasio pencampuran yang berkelanjutan, yang dilaporkan dan dicatat.”
Perhatikan selang hitam antara peralatan MMD Hübers dan pengaturan infus VAP di mana Hexion telah mengembangkan pengukuran rasio campuran resin in-line sebelum injeksi.Sumber | Hexion
“Dengan sistem ini,” lanjutnya, “ada kontrol ganda:kontrol normal di unit MMD dan kontrol analitis pra-injeksi kami di atas. Pertama, Rivière menunjukkan bahwa mesin MMD Hübers terkenal dengan presisi dan akurasinya. “Mereka memiliki sistem pemompaan ganda untuk dua komponen dan harus menjaga akurasi dalam volume dan suhu serta rasio campuran untuk aplikasi yang mereka suplai. Sistem kami kemudian menambahkan pengukuran kedua setelah pencampuran dan sesaat sebelum injeksi di mana Anda dapat menetapkan target untuk alarm.” Jika rasio campuran yang diukur tidak memenuhi target dan memicu alarm, sistem kemudian akan mengevakuasi resin campuran ke dalam wadah terpisah, melewati cetakan sehingga tidak dimasukkan ke dalam bagian yang diinfuskan. “Kemudian dimungkinkan untuk memulihkan proses dan melanjutkan injeksi,” catat Riviere.
Dia mengatakan sistem kontrol analitik pra-pencampuran pasca-pencampuran Hexion memberikan catatan independen untuk keterlacakan dan juga dapat diintegrasikan ke dalam unit MMD, tergantung pada kebutuhan pelanggan. Rivière mencatat bahwa unit MMD Hübers juga melakukan degassing resin secara menyeluruh, yang diperlukan oleh industri elektronik, di mana tidak boleh ada rongga atau porositas dalam komponen aplikasi. “Sistem ini juga menyediakan kontrol portabel dari tekanan pada cetakan dengan mengatur aliran resin pada tingkat tinggi atau rendah,” dia menunjukkan. “Anda dapat mencapai impregnasi yang sangat baik dengan jenis kontrol ini, dan Anda juga dapat mempersingkat waktu proses infus sambil memenuhi persyaratan kualitas dirgantara dalam hal porositas dan volume serat.”
Foto yang menunjukkan penyiapan infus menggunakan peralatan Hübers MMD dan kontrol analitik Hexion 2K serta laminasi UD serat karbon setebal 2 sentimeter yang disiapkan menggunakan penyiapan ini, menghasilkan lebih dari 60% volume serat. SUMBER | Hexion
Jendela pemrosesan yang lebih baik
“Karena pencampuran dilakukan dengan mixer statis dan dalam waktu singkat sebelum injeksi, campuran resin menawarkan masa pakai pot yang lebih lama (hingga 40% jika dibandingkan dengan 1K),” catatan Riviere . Ini memberikan jendela pemrosesan yang lebih baik dan kami telah memproduksi laminasi serat karbon tebal dengan volume serat 60%. Performa mekanis sistem 2K versus 1K adalah sama karena chemistry-nya sama. Kami yakin ini akan menjadi proses yang lebih andal dan nilai lengkapnya adalah saat Anda menghubungkan kontrol pencampuran ke pengaturan injeksi resin.”
SUMBER | Hexion
Hexion akan menyajikan informasi terperinci tentang sistem 2K Epikote 600 untuk RTM dan epoksi EPON FlameX untuk memenuhi persyaratan kebakaran, asap, dan toksisitas (FST) pesawat (lihat di bawah) di Teater CAMX di lantai pameran:
- Teknologi 2K Baru untuk Manufaktur Epoxy Aerospace
Selasa, 24 September — 11:00 -11:25
- Sistem Epoxy FlameX untuk Aplikasi Keselamatan Kebakaran
Selasa, 24 September — 11:30 – 11:55
Anda juga bisa mendapatkan detail lebih lanjut di stan Hexion Y24.
EPON FlameX epoxy untuk infus/RTM komposit tahan api
Hexion juga telah mengembangkan epoksi 2 komponen untuk infus/RTM suku cadang yang harus memenuhi persyaratan ketahanan api (FR) dan api, asap, toksisitas (FST). Ditujukan untuk menggantikan prepreg fenolik dengan cetakan cair epoksi, pendorong pengembangan ini meliputi:
- Peningkatan tingkat produksi
- Peraturan REACH untuk sistem non-fenolik bebas halogen
- Resin yang lebih kuat dan lebih keras dibandingkan fenolat rapuh
- Biaya kompetitif dengan fenolat tetapi jauh lebih murah daripada termoplastik.
Sistem EPON FlameX Hexion tidak menggunakan aditif halogen atau partikulat untuk mencapai ketahanan api, melainkan membangun kinerja itu ke dalam tulang punggung molekul resin. Tidak ada penyaringan partikulat selama infus, resin meresap dengan baik dengan viskositas 250 cps pada 60-70 °C (140-158 °F) dan sembuh dalam 1,5 jam pada 150 °C (302 °F). Post-cure berdiri bebas atau yang didukung alat pada 180°C direkomendasikan untuk sifat struktural maksimum.
Suku cadang yang dibuat dengan sistem ini lulus berikut ini tanpa pelapis tambahan atau tindakan FR:
- Pembakaran vertikal 60-an FAR25,853(a)
- Keracunan asap BSS7239
- Kepadatan asap BSS7238
Ini juga akan melewati pelepasan panas OSU 65/65, dalam konfigurasi tertentu dengan lapisan atau lapisan gel intumescent bersertifikat. Ini diperlukan hanya untuk bagian yang dapat disentuh selama taksi pesawat, lepas landas, dan mendarat.
“Kami telah mendemonstrasikan tempat sampah yang saat ini membutuhkan 10-12 jam untuk diproduksi menggunakan proses prepreg fenolik konvensional tetapi dapat diproduksi dalam 90 hingga 120 menit dengan infus atau RTM menggunakan sistem FlameX,” kata Nathan Bruno, spesialis pengembangan produk dan aplikasi epoksi Hexion. . “Juga, karena tidak ada pengisi, kepadatannya lebih rendah dibandingkan epoksi FR yang diisi.”
Aplikasi termasuk interior pesawat, area kargo, toilet, dapur dan komponen kursi, serta interior laut, rel, dan arsitektur.