Proses Peniupan Gabungan dalam Pembuatan Baja Konverter
Gabungan Proses Peniupan dalam Pembuatan Baja Konverter
Ketidakhomogenan dalam komposisi kimia dan suhu dibuat dalam baja cair selama tiupan oksigen (O2) di konverter tiup atas karena kurangnya pencampuran dalam penangas baja cair. Ada zona yang relatif mati langsung di bawah rongga jet di konverter. Kebutuhan untuk meningkatkan proses pembuatan baja di konverter tiup atas telah mengarah pada pengembangan proses tiupan gabungan.
Proses peniupan gabungan juga dikenal sebagai peniupan atas dan bawah atau proses peniupan campuran dicirikan oleh tombak peniup atas dan metode untuk mencapai pengadukan dari bawah. Perbedaan konfigurasi dalam peniupan campuran terutama terletak pada tuyeres bawah atau elemen pembersih. Ini berkisar dari tuyer yang didinginkan sepenuhnya, hingga tuyer yang tidak didinginkan, hingga elemen yang permeabel. Kebutuhan sistem pengadukan bawah diperlukan untuk produksi berbagai mutu baja yang menuntut mutu tinggi dan sangat penting agar proses menjadi ekonomis. Oleh karena itu, fungsi pengadukan yang tepat harus dipastikan di seluruh kampanye konverter oksigen dasar (BOF). Gambar 1 menunjukkan proses pembuatan baja peniupan atas dan peniupan gabungan.
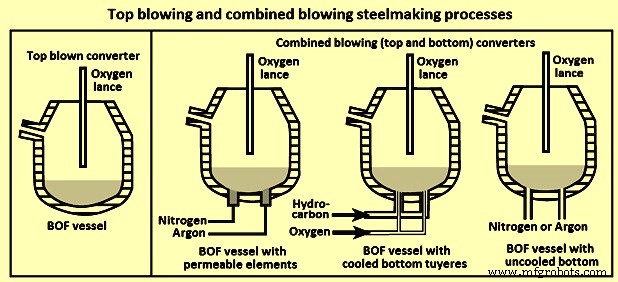
Gbr 1 Proses pembuatan baja peniupan atas dan peniupan gabungan
Saat ini, konverter tiup gabungan atas dan bawah umumnya digunakan di pabrik pembuatan baja primer. Dalam blowing converter gabungan, pengadukan dan pencampuran bak dipaksa oleh pancaran O2 yang ditiup atas dan aliran gas inert bawah, yang dapat mencapai efisiensi pencampuran yang tinggi untuk bak. Dalam kasus yang jarang terjadi, O2 juga disuntikkan dari bawah dengan tuyer tabung ganda konsentris bersama dengan gas selubung untuk mengontrol suhu di outlet tuyere dan keausan bagian bawah. Namun, karena pembersihan gas inert secara umum memberikan kontrol keausan yang lebih tinggi, masa pakai elemen pembersih dan bagian bawah, sebagian besar konverter dilengkapi dengan pengaduk bagian bawah dengan sumbat pembersih gas.
Praktik blowing gabungan pertama yang diterima secara komersial adalah proses LBE (Lance Bubbling Equilibrium) yang dikembangkan oleh ARBED-IRSID. Proses ini jauh lebih erat kaitannya dengan proses BOF di mana semua O2 dipasok dari tombak atas. Aspek hembusan gabungan dicapai dengan satu set elemen berpori yang dipasang di bagian bawah konverter melalui mana argon (Ar) atau nitrogen (N2) dihembuskan. Dalam proses LBE, gas N2 biasanya digunakan hampir secara eksklusif untuk sebagian besar pukulan dalam kisaran 3 meter kubik normal per menit (N cum/menit) hingga 11 N cum/menit. Namun di bagian akhir pukulan, ketika penyerapan N2 dapat menimbulkan masalah, digunakan gas Ar untuk pengadukan. Selain itu, Ar digunakan hampir secara eksklusif sebagai gas inert untuk pengadukan pasca tiup, pada saat ini kecepatan dinaikkan menjadi 10 N cum/menit menjadi 17 N cum/menit. Gambar 2 menunjukkan konverter LBE dengan elemen peniup bawah.
Dalam proses peniupan gabungan, pengadukan bawah dilakukan dengan menggunakan gas inert seperti N2 dan Ar yang digunakan secara ekstensif untuk memperbaiki kondisi pencampuran dalam BOF. Gas inert dimasukkan di bagian bawah tungku dengan menggunakan elemen permeabel (proses LBE) atau tuyeres. Dalam praktek yang khas, gas N2 dimasukkan melalui tuyeres atau elemen permeabel pada 60% o 80% pertama dari hembusan O2, dan gas Ar dinyalakan pada 40% hingga 20% terakhir dari hembusan. Evolusi cepat CO pada bagian pertama dari pukulan O2 mencegah pengambilan N2 dalam baja. Profil elemen berpori ditunjukkan pada Gambar 2
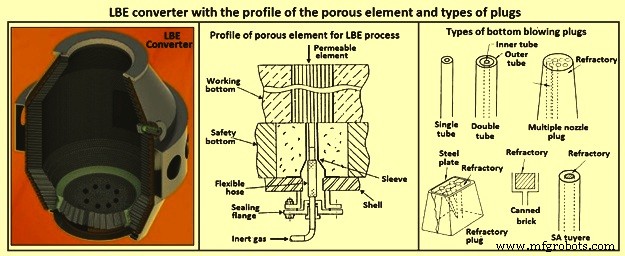
Gambar 2 Konverter LBE dengan profil elemen berpori dan jenis busi
Penumpukan dasar dan hilangnya elemen berpori selanjutnya adalah masalah utama yang terkait dengan proses ini. Kesulitan dalam mempertahankan operasi elemen LBE telah menyebabkan penerapan tuyeres non-pendingin. Di sini juga O2 dikirim melalui tombak atas sementara gas inert dimasukkan ke bak dari dasar konverter melalui elemen desain tabung yang umumnya terdiri dari enam pipa kecil yang dipasang dalam matriks tahan api. Karena area penampang yang lebih besar tersedia, laju aliran yang lebih besar diperlukan untuk dipertahankan agar tuyeres tetap beroperasi.
Konfigurasi steker / nosel bawah
Pengembangan awal blowing gabungan pada dasarnya didasarkan pada tiga jenis sumbat bawah yang digunakan untuk blowing bawah. Pertama, ada elemen tahan api yang berperilaku seperti sumbat berpori. Unit ini terbuat dari batu bata yang dipadatkan dengan celah-celah kecil. Seperti kebanyakan tuyeres, dibutuhkan tekanan gas yang cukup untuk mencegah penetrasi baja. Unit ini lebih menembus daripada busi berpori. Kedua, tuyere yang tidak didinginkan digunakan untuk memasukkan sejumlah besar gas inert per nosel. Ini menghasilkan pengadukan berat lokal, yang dapat lebih mudah menembus build-up. Udara atau O2 tidak dapat digunakan karena tidak ada pendingin dan panas yang dihasilkan membuat umur tuyere terlalu pendek untuk praktis. Tipe ketiga adalah tuyere berpendingin penuh. Di sini, baik gas inert atau O2 dapat dihembuskan, menyebabkan pengadukan yang sangat kuat dan hampir tidak ada masalah untuk menembus lapisan bawah. Dalam semua kasus, pipa gas disalurkan melalui trunnion tungku menggunakan sambungan putar atau segel untuk memungkinkan rotasi penuh tungku. Berbagai jenis sumbat peniup bawah yang dikembangkan untuk peniupan gabungan ditunjukkan pada Gambar 2.
Keadaan desain sumbat saat ini yang digunakan untuk penghembusan bawah gas inert didasarkan pada desain sumbat lubang tunggal (SHP) dan desain sumbat multi lubang (MHP). Desain steker ini telah ditetapkan sebagai desain mutakhir yang diterima secara luas untuk colokan peniup bawah. Steker pembersih SHP dan MHP dirancang dengan diameter pipa dan jumlah pipa yang dioptimalkan untuk laju aliran. Namun, MHP untuk pembersihan dasar gas inert lebih populer. Kedua jenis colokan pembersih dengan desain SHP dan MHP didasarkan pada refraktori magnesia-karbon (MgO-C) dan biasanya terbuat dari 100 % leburan magnesia tingkat tinggi, grafit tingkat tinggi, distribusi ukuran butir yang dioptimalkan, dan terkadang dengan aditif.
Pembersihan yang efisien hingga akhir kampanye pelapisan BOF adalah target dari semua sumbat pembersih gas di toko-toko BOF dan dipengaruhi oleh kisaran laju aliran gas yang diterapkan, potensi penyumbatan, dan laju keausan dalam kondisi proses tertentu. Standar keamanan tertinggi adalah persyaratan penting untuk pembersihan dasar.
Potensi penyumbatan – Berkurangnya ketersediaan colokan pembersih karena penumpukan di bagian bawah sering kali menjadi alasan rendahnya efisiensi pembersihan. Hal ini meningkatkan biaya agen de-oksidasi, menurunkan hasil, dan menyebabkan proses peniupan yang kurang efisien. Alasan utama penyumbatan adalah penumpukan di bagian bawah karena terak yang sangat lengket atau frekuensi percikan terak yang tinggi, masalah dengan pasokan gas inert atau desain steker pembersih yang tidak memadai. Sedangkan laju aliran gas yang tinggi melalui SHP dapat membantu mengurangi potensi penyumbatan terak pada laju percikan terak yang rendah, laju percikan terak yang tinggi dengan potensi pembentukan dasar atau pasokan gas inert yang tidak mencukupi menyebabkan infiltrasi yang agak dalam pada SHP dengan probabilitas yang sangat rendah. pembukaan kembali. Efisiensi pembersihan MHP, bagaimanapun, ditingkatkan dengan banyak pipa dengan jumlah, diameter, dan pengaturan aliran yang dioptimalkan. Laju pembukaan kembali PLTMH dilaporkan secara teratur dan tidak rentan terhadap fluktuasi tekanan gas dan pasokan gas inert.
Keamanan – Standar keselamatan tertinggi umumnya diberikan untuk desain PLTMH. Pipa gas langsung ditekan ke dalam bata MgO-C. Jika pasokan gas ke PLTMH berkurang atau nol karena alasan apa pun, infiltrasi baja hanya berlaku beberapa milimeter ke dalam sumbat pembersih. Risiko pecahnya baja melalui MHP diminimalkan.
Karakteristik pembersihan dan tingkat keausan – Rezim aliran SHP berada di zona transisi antara bubbling dan jetting atau seluruhnya di zona jetting, menghasilkan volume gas yang besar di atas pipa tunggal dan selanjutnya meluruh menjadi gelembung gas yang lebih kecil dengan distribusi ukuran yang besar. Rezim aliran ini secara umum dicirikan oleh peningkatan laju keausan, mis. 0,4 mm/panas menjadi 0,7 mm/panas. Desain MHP memberikan distribusi gelembung gas yang jauh lebih tepat di atas sumbat pembersih dengan bagian gelembung gas kecil yang lebih tinggi. Permukaan spesifik yang lebih tinggi dari gelembung gas kecil meningkatkan pembersihan gas dan efisiensi metalurgi. Tingkat keausan umumnya lebih rendah sebagai akibat dari penurunan fenomena serangan balik dan turbulensi pada kecepatan gas yang lebih rendah. Gambar 3 menunjukkan SHP dan MHP dengan evolusi gelembung gas dalam model air.
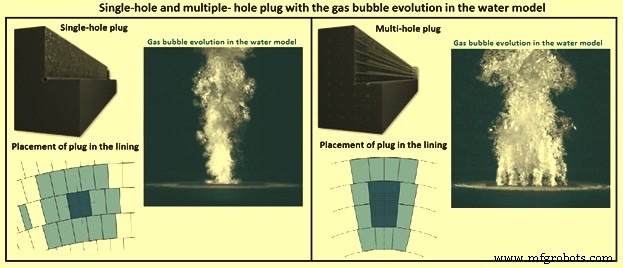
Gbr 3 SHP dan MHP dengan evolusi gelembung gas dalam model air
Proses peniupan gabungan
Dalam proses pembuatan baja gabungan, O2 yang diperlukan untuk menghaluskan baja ditiupkan melalui tombak yang dipasang di atas sedangkan gas inert (N2 atau Ar) yang dibutuhkan untuk proses pengadukan bawah dimasukkan ke dalam lelehan melalui bata pengaduk bawah untuk memperbaiki kondisi proses dengan pencampuran yang dioptimalkan. Laju aliran dan jenis gas pengadukan tergantung pada fase proses dan grade baja. Pendekatan yang lebih cepat dan lebih baik dari keseimbangan terak logam dicapai karena pengadukan bawah. Kesetimbangan dan waktu pencampuran tergantung pada jenis, jumlah, lokasi pengaduk, dan kecepatan aliran. Pengadukan yang lebih kuat menggeser kesetimbangan termodinamika ke arah yang diinginkan dan mengurangi waktu pencampuran. Pergeseran dari N2 ke Ar biasanya diperlukan, tergantung pada kimia baja akhir. Stasiun katup sebagai bagian tengah dari sistem pengadukan bawah memungkinkan kontrol aliran individual per sumbat pembersih individu.
Seperti pada proses peniupan atas, O2 disuntikkan melalui tombak multi lubang ke penangas baja cair dalam proses peniupan gabungan. Tetesan logam dihasilkan sebagai akibat tumbukan pancaran dan aksi geser aliran gas dari daerah tumbukan di mana pancaran menghantam permukaan logam dan gas dibelokkan ke atas. Efek interaksi cairan jet ini dijelaskan dalam tiga mode yaitu (i) lesung pipit, (ii) percikan, dan (iii) penetrasi.
Jumlah tetesan besi yang terciprat ke dalam gas dan terak mempengaruhi hasil logam, keausan tahan api, dan kemajuan dekarburisasi. Ada efek sifat gas dan cairan pada kedalaman depresi mandi dan kedalaman kritis menandai permulaan percikan. Percikan meningkat hingga momentum pancaran tertentu di luar mana ia berkurang. Arah percikan tergantung pada sudut nosel tombak, tinggi tombak, profil rongga pancaran yang diperkirakan dari kedalaman dan diameternya serta tumpang tindih pancaran O2.
Banyak percobaan telah dilakukan untuk memodifikasi ujung tombak untuk mengontrol percikan atau spitting pada konverter BOF. Pentingnya desain yang tepat dari diameter nosel dan sudut kemiringan diperlukan untuk distribusi tekanan yang optimal dari pancaran O2. Studi yang berbeda menunjukkan bahwa hembusan atas dengan pengadukan bawah dari wadah konverter memberikan kinerja yang lebih baik daripada hanya hembusan atas pada konverter BOF sehubungan dengan percikan dan spitting.
Berbagai metode peniupan bawah untuk pengadukan telah diadopsi. Sebuah steker keramik dengan beberapa pipa kecil tertanam atau beberapa celah digunakan di tuyeres bawah. Pengadukan dilakukan dengan elemen pengaduk tahan api khusus atau melalui tuyer kecil tanpa pelindung yang diatur di bagian bawah konverter.
Proses penghembusan bawah secara efektif menaikkan tinggi bak, dan menunjukkan profil keausan tahan api yang berbeda dibandingkan dengan profil keausan yang diperoleh pada konverter BOF peniupan atas. Keausan tuyeres dan area sekitarnya sering kali parah dalam jenis proses ini, dan membutuhkan penggunaan material berdensitas tinggi yang tahan erosi untuk menahan aliran turbulen baja cair.
Proses blowing gabungan menggunakan gas yang mahal (O2, Ar, dan N2) dan pengukuran serta totalisasi yang akurat dari gas-gas ini membantu operasi ekonomi dan kontrol kualitas yang ketat dengan menggunakan nilai-nilai ini dalam pembuatan laporan harian untuk kontrol manajemen. Untuk mengaduk bak konverter, gas Ar atau N2 diinjeksikan melalui sejumlah bata steker pengaduk di dasar konverter. Aliran total dan jenis gas untuk setiap langkah urutan ditentukan sebelumnya dari menu yang dimuat untuk pukulan saat ini. Aliran total dibagi rata ke sejumlah pengontrol, satu untuk setiap bata steker pengaduk untuk menjaga pemerataan, dan menjadi titik setel jarak jauh pengontrol. Aliran terukur dikompensasikan secara massal untuk suhu dan tekanan untuk setiap jenis bata dan gas steker pengaduk dan masukan ke modul kontrol. Output kontrol 4-20 mA kemudian memodulasi posisi katup kontrol.
Jika bata steker pengaduk ditutupi dengan terak berat, tekanan hilir meningkat. Jika meningkat melebihi batas yang telah ditentukan, kontrol berubah dari kontrol aliran ke kontrol tekanan dan katup kontrol kemudian merespons algoritma kontrol yang berbeda. Pada pengurangan tekanan (kurang dari nilai histeresis), kontrol kembali ke kontrol aliran. Pergantian antara mode kontrol harus dilakukan secara otomatis, karena loop nonaktif melacak output dari loop aktif.
Optimalisasi musuh konsumsi gas dan rentang kontrol aliran, kontrol tekanan saluran masuk tambahan dipasang. Kombinasi kontrol tekanan di saluran pengumpan dan kontrol aliran individu dalam saluran pengadukan mempertahankan laju aliran konstan dari masing-masing pengaduk, sehingga menghindari penyumbatan sumbat berpori oleh terak kental. Instrumentasi yang sesuai memberi operator indikasi kondisi sumbat keropos. Keandalan proses sangat penting. Filosofi gagal-aman umumnya disediakan untuk saluran pengumpanan (pengalihan gas jika tekanan masuk rendah) serta aliran individu (pembukaan gagal-aman jika media dan kegagalan daya). Representasi skema dari proses blowing gabungan ditunjukkan pada Gambar 4.
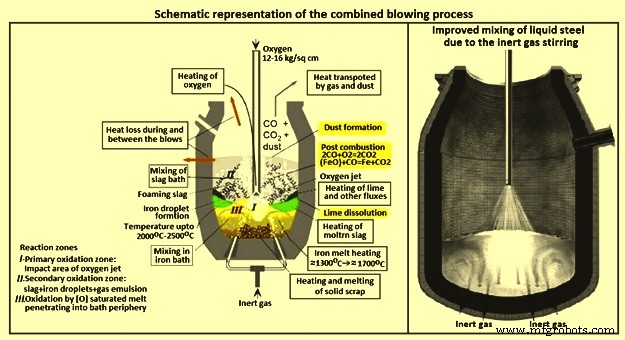
Gbr 4 Representasi skema dari proses blowing gabungan
Sistem pengadukan bawah konverter dikendalikan melalui PLC (pengontrol logika yang dapat diprogram) yang dipasang baik sebagai unit yang berdiri sendiri dengan stasiun HMI (antarmuka mesin manusia) individu atau disediakan untuk integrasi ke jaringan baru atau yang sudah ada. Operasi membutuhkan fleksibilitas. Bergantung pada grade baja yang dipilih, perangkat lunak mengikuti pola pengadukan (tabel parameter set-point) untuk laju aliran Ar dan N2 selama pemanasan total sebagai fungsi dari total kuantitas O2 yang ditiup. Perubahan set-point dan tindakan kontrol berlangsung dalam mode otomatis tanpa interaksi operator, berdasarkan sinyal lapangan.
Selama penyadapan, penghilangan slagging, dan pengisian, laju aliran yang telah ditentukan sebelumnya harus dipastikan untuk mengurangi keausan refraktori dan masa pakai yang tinggi dari sumbat berpori. Desain bata sumbat pengaduk adalah untuk memastikan masa pakai yang lama dengan memiliki kecepatan erosi yang rendah, ketahanan spalling yang canggih, dan panjang bata yang fleksibel.
Penempatan batu bata sumbat pengaduk terhadap pancaran O2 sangat penting untuk keefektifan sistem pengadukan bawah. Untuk optimasi lokasi batu bata steker pengaduk, poin yang harus dipertimbangkan adalah (i) dampak pancaran O2 di bawah berbagai kondisi proses (seperti desain ujung tombak dan variabilitas tinggi tombak, dll.), (ii) rasio aspek tinggi lelehan terhadap diameter konverter, dan (iii) pengaruh terhadap keausan refraktori. Penggunaan simulasi CFD (Computational Fluid Dynamics) terbaru biasanya dilakukan untuk mengoptimalkan lokasi adukan batu bata dengan mempertimbangkan kondisi kompleks pada konverter BOF.
Perkembangan terbaru di bidang ini adalah teknologi pengadukan bolak-balik yang dipatenkan. Dalam praktik pengadukan bolak-balik, kelompok elemen pengadukan dikontrol dengan laju aliran gas pengadukan tinggi dan rendah yang bergantian. Evaluasi statistik hasil proses selama beberapa kampanye, setelah penerapan teknologi ini di toko BOF, telah menunjukkan bahwa ada potensi untuk mengurangi biaya Ar sebesar 30% tanpa pengaruh negatif pada hasil metalurgi.
Efek metalurgi dari tiupan gabungan
Pola pembersihan, terutama jumlah sumbat, laju aliran dan jenis serta kualitas gas pembersih memiliki pengaruh yang luar biasa pada metalurgi BOF. Parameter tersebut harus dikoordinasikan secara ketat jika tidak, proses dapat melampaui kendali dan hasil metalurgi yang diinginkan tidak dapat dicapai. Berikut ini adalah efek metalurgi dari tiupan gabungan.
Karbon/O2 – Sebagai hasil dari pembersihan dasar, kinetika untuk dekarburisasi ditingkatkan dan dengan demikian tingkat karbon (C) yang lebih rendah pada akhir pukulan tanpa rendaman baja selama oksidasi tercapai. Indikator kinerja pembersihan yang efisien adalah produk [C] x [O], yang dibandingkan dengan konverter yang dioperasikan dengan tiup atas jauh lebih rendah dan dalam kisaran rata-rata 0,002 % hingga 0,0025%. Karena proses pemurnian, ada kondisi non-ekuilibrium dalam penangas baja cair dan juga antara terak dan penangas baja cair.
Dengan program pembersihan dasar yang tepat, reaksi dapat didorong lebih dekat ke kesetimbangan pada akhir pukulan dan karenanya efek de-karburasi diperkuat. Durasi pasca pengadukan mengintensifkan efek itu juga. Untuk membidik level C terendah, kandungan C dari lapisan tahan api juga merupakan parameter yang signifikan.
Mengacu pada konverter yang dioperasikan dengan tiup atas, kandungan [O] terlarut pada tingkat [C] yang sama pada penyadapan lebih rendah yang menghasilkan minimalisasi konsumsi zat de-oksidasi dalam sendok. Ada juga peluang untuk melepaskan atau menyimpan perawatan degassing RH (Rurhstahl Heraeus) yang mahal yang disebabkan oleh tingkat pemurnian terendah pada penyadapan.
Hasil besi – Pembersihan dasar, komposisi logam panas (kandungan [Si]), praktik terak, dan program peniupan mempengaruhi tingkat FeO dalam terak dan karenanya potensi reaksi kimia antara terak dan pelapis dan efek pasca pengadukan. BOF dengan sistem pembersihan bawah dicirikan dengan kandungan besi yang lebih rendah dalam terak dan juga volume terak yang lebih rendah dibandingkan dengan konverter BOF yang ditiup atas. Juga kadar FeO dalam terak pada penyadapan bergantung pada C terlarut dalam penangas baja.
Mangan (Mn) – Hasil Mn pada tingkat C yang sama pada penyadapan lebih tinggi daripada proses BOF top-blowing konvensional. Dalam hubungan ini Fe-Mn yang lebih rendah diperlukan untuk paduan metalurgi sekunder tergantung pada nilai baja. Dengan demikian, penyesuaian level Mn dapat dikontrol dengan lebih baik.
Fosfor (P) – Pembersihan dasar dicirikan melalui kapasitas pemasukan P2O5 yang lebih baik dalam terak dan pembubaran kapur yang lebih cepat. Menurut tetesan besi cair yang disemprotkan selama proses pemurnian di konverter BOF, terutama selama fase hard blowing, suhu terak yang terbentuk lebih tinggi daripada bak peleburan. Ini menghasilkan kondisi yang lebih lemah untuk de-fosforisasi. Melalui pembersihan, suhu terak diturunkan secara signifikan yang disebabkan oleh pengadukan rendaman yang sangat baik dan keseimbangan suhu yang lebih baik antara terak dan rendaman baja.
Pengaruh pasca pengadukan – Tujuan utama pasca pengadukan adalah di satu sisi realisasi tingkat C dan P terendah pada penyadapan dan di sisi lain penyesuaian cepat dan tepat dari suhu penyadapan (efek pendinginan). Waktu dan intensitas pembersihan adalah dua parameter yang menentukan untuk pencapaian tingkat elemen tertentu. Pengadukan pasca meningkatkan efek dekarburisasi secara signifikan dengan mengarahkan C dan O2 terlarut dalam penangas baja lebih dekat ke kesetimbangan. Pengadukan pasca menyebabkan pendinginan penangas baja cair ditingkatkan dengan pengisian tambahan terak BOF. Artinya terjadi peningkatan distribusi P pada faktor ketiga dan penurunan kadar P pada penyadapan menjadi 0,005 %.
Pengaruh pengaturan steker pembersih dan jumlah steker – Sistem pembersihan mempengaruhi kondisi kesetimbangan dalam bak baja selama proses pemurnian dan karenanya hasil metalurgi. Pembersihan dasar memungkinkan untuk mendekati atau lebih tepatnya mendekati keseimbangan pada akhir peniupan. Efek dekarburisasi dan defosforisasi sangat meningkat. Untuk efektivitas pembersihan parameter Rp telah ditetapkan. Rp menggambarkan rasio kondisi aktual terhadap kondisi keseimbangan. Jika kesetimbangan tercapai maka parameter Rp adalah satu. Peningkatan jumlah colokan berarti peningkatan agitasi mandi dan karenanya nilai Rp lebih tinggi mendekati satu. Gambar 5 menunjukkan konsekuensi dari berbagai pengaturan sumbat dan angka pada kesetimbangan yang mendekati (didefinisikan oleh parameter pembersihan Rp).
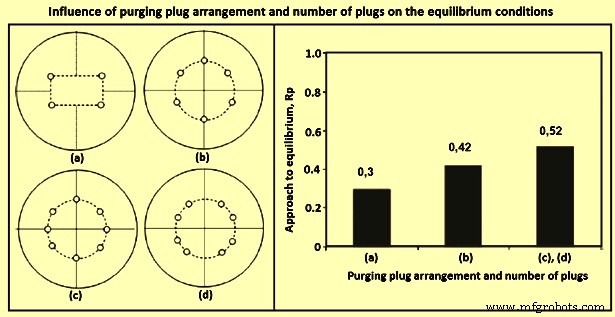
Gbr 5 pengaruh pengaturan purging plug dan jumlah plug pada kondisi kesetimbangan
Indikator untuk pengadukan atau pencampuran mandi adalah waktu pencampuran relatif. Pengurangan waktu pencampuran berarti peningkatan pencampuran / kinetika bath dan oleh karena itu percepatan reaksi kimia (memperpendek cara reaksi). Parameter lebih lanjut untuk deskripsi kinetika bath adalah energi pencampuran. Energi pencampuran melibatkan tinggi tombak, geometri, latihan peniupan, tingkat rendaman logam cair dan untuk konverter tiup atas dengan sistem pembersihan bawah, laju aliran pembersihan juga.
Kunci keberhasilan pengoperasian sistem pembersihan bawah adalah pola pembersihan utama, jumlah colokan, tingkat keausan, dan ketersediaan setiap colokan. Susunan steker pembersih hampir tidak relevan dan hanya merupakan elemen desain.
Pengaruh intensitas pembersihan – Tingkat intensitas pembersihan memainkan peran yang menentukan untuk mencapai produk [C] x [O] terendah dan kehilangan besi dalam rendaman baja. Tingkat pembersihan minimum menyebabkan penurunan yang cukup besar dari produk [C] x [O], terutama di bawah laju aliran yang ditetapkan sebesar 0,06 N cum/t menit.
Manfaat pengoperasian – Proses blowing atas dengan sistem pembersihan bawah juga tercermin dalam pemurnian yang kurang turbulen dan karenanya mengurangi slopping dengan konsekuensi hasil yang lebih tinggi. Selanjutnya konsumsi O2 total sekitar 2% dan suhu sadapan rata-rata 10 derajat C lebih rendah dibandingkan dengan proses BOF konvensional. Hal ini disebabkan oleh hasil pengadukan bath yang lebih baik dan kondisi bath baja yang homogen. Jumlah kapur yang terisi berkurang sekitar 10% hingga 15% dibandingkan dengan konverter yang dioperasikan dengan hembusan atas.
Titik peralihan ideal dari N2 ke Ar
Level N2 pada penyadapan secara fleksibel disesuaikan selama proses pemurnian dengan menggeser titik peralihan dari N2 ke Ar dan khususnya laju aliran pembersihan. Praktik normalnya adalah untuk laju aliran N2 yang lebih rendah pada awal pemurnian dan peningkatan intensitas pembersihan Ar yang signifikan setelah peralihan. Oleh karena itu, diinginkan untuk mewujudkan produk [C] x [O] terendah, pembersihan intensif pada sepertiga terakhir periode pemurnian sudah memadai.
Biasanya, hingga 25% dari jenis gas proses pemurnian dan intensitas pembersihan tidak memiliki pengaruh pada tingkat N2 dalam penangas baja. Pembersihan dengan Ar pada fase pemurnian ini tidak efektif dari segi biaya dan tanpa tujuan. Ar lebih mahal dari N2. Untuk membidik level N2 terendah, perlu untuk beralih dari N2 ke Ar antara 25% dan 50% dari waktu blowing. Pergantian yang lambat, terutama lebih dari 50% pemurnian, menyebabkan tingkat N2 yang sangat tinggi pada penyadapan.
Pengenalan hembusan bawah secara signifikan meningkatkan percikan khususnya di bagian bawah konverter. Pada saat yang sama, ini mengurangi kehilangan logam dan tengkorak kerucut. Keberhasilan proses peniupan gabungan tergantung pada keefektifan alat pengaduk bawah. Perangkat ini harus andal, menyebabkan pengadukan yang efektif, memiliki masa pakai yang cukup lama, dan tidak terhalang selama pengoperasian konverter.
Percikan terak dan tiupan gabungan
Percikan terak adalah teknik yang terbukti digunakan untuk meningkatkan umur kampanye BOF ke tingkat yang sangat tinggi. Setelah penyadapan, terak dalam konverter disiramkan dengan N2 ke area yang berbeda dari lapisan selama jangka waktu mulai dari 2 menit sampai 5 menit. Juga ada praktik seperti pelapisan terak dan pencucian terak. Praktek ini mempertahankan sejumlah kecil terak cair dalam konverter setelah penyadapan. Terak diperkaya dengan dolomit atau dolomit mentah. Setelah itu, konverter diguncang beberapa kali untuk menutupi bagian bawah dan daerah sekitarnya dengan lapisan tipis terak. Penambalan panas dan penembakan adalah tindakan lain untuk meningkatkan masa pakai lapisan tahan api konverter.
Percikan terak bekerja paling baik dengan terak yang kental dan lengket. Tapi terak lengket menyebabkan bagian bawah konverter menumpuk dengan lapisan terak yang menghalangi evolusi bebas dari pancaran gas dari tuyeres/colokan atau bahkan menghalangi mereka sepenuhnya. Ini biasanya bukan kerusakan pada sistem pengadukan bawah itu sendiri tetapi mengakibatkan penurunan yang signifikan dari hasil metalurgi karena distribusi gas yang tidak menguntungkan.
Dengan lapisan terak yang menutupi elemen pengaduk bagian bawah, pengadukan bagian bawah yang efektif tidak dimungkinkan karena gas tidak dapat disuntikkan dengan aliran pancaran terarah. Agak merayap di antara lapisan dan lapisan terak sampai menemukan celah untuk melarikan diri. Dalam hal ini efek pengadukan yang penting tidak lagi dapat sepenuhnya ditetapkan. Dengan lapisan terak yang sangat tebal, gas bahkan dapat merayap di sepanjang laras ke kerucut atas atau mulut, tidak menunjukkan efek pengadukan dan tidak ada efek metalurgi sama sekali. Fenomena ini ditunjukkan pada Gambar 6. Telah diverifikasi dengan menggunakan gas alam, yang dapat diidentifikasi dengan nyala api. Terdeteksi bahwa gas alam keluar di area yang dijelaskan. Sisi kiri Gambar 6 menunjukkan situasi lapisan terak yang hanya menutupi bagian bawah. Sisi kanan menunjukkan situasi dengan lapisan terak yang menutupi bagian bawah, buku jari bagian bawah, dan laras seperti yang dibuat jika terjadi percikan terak yang intensif.
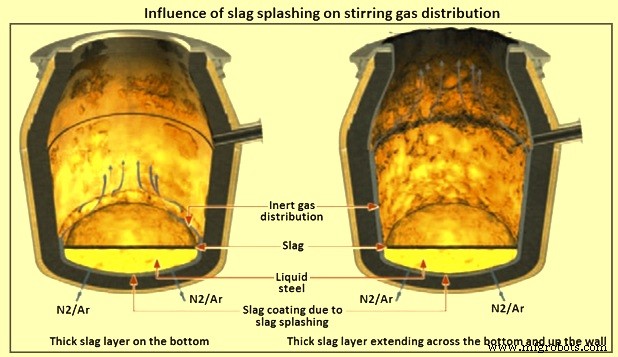
Gbr 6 Pengaruh percikan terak pada distribusi gas pengadukan
Dapat dilihat bahwa dalam kasus ekstrim, gas inert tidak memiliki kontak dengan lelehan maupun dengan terak sama sekali. Oleh karena itu, perlu untuk mengontrol ketebalan dasar secara teratur dan memulai tindakan pencegahan dini untuk mempertahankan fungsi sistem pengadukan bawah.
Keuntungan dari pukulan gabungan
Alasan mendasar untuk menerapkan sistem pembersihan dasar di satu sisi untuk meningkatkan hasil metalurgi dan di sisi lain untuk menjamin produksi baja O2 ekonomis berkualitas tinggi dengan biaya terendah. Manfaat terpenting dari blowing converter gabungan over blowing dalam konverter BOF adalah (i) percepatan siklus blowing yang mengakibatkan pemendekan waktu tap to tap, (ii) pembentukan terak yang lebih pendek dan lebih cepat dan interaksi yang lebih baik antara terak dan bak baja ( kondisi yang lebih baik untuk peleburan penambahan skrap/fluks, rasio skrap/logam panas yang lebih tinggi), (iii) pengurangan pukulan ulang dan peningkatan laju pukulan dalam komposisi dan suhu, (iv) peningkatan homogenisasi / agitasi bak baja dan distribusi suhu, (v ) Peningkatan akurasi dalam mencapai komposisi tertentu, (vi) kontrol proses yang lebih baik (akurasi yang lebih tinggi untuk suhu sadapan dan tingkat elemen), (vii) peningkatan hasil penambahan baja dan fluks (volume terak lebih sedikit dan kehilangan besi yang lebih rendah menjadi terak dan debu leleh), (viii) lebih sedikit percikan dan ludah, dan slopping, (ix) menurunkan kadar (FeO), [P] dan oksidasi [Mn], sehingga konsumsi O2 lebih rendah, (x) menurunkan oksida besi dalam terak, (xi) meningkatkan efisiensi peniupan karena pengadukan lelehan yang sangat intensif, (xii) menurunkan kandungan O2 akhir dalam baja sehingga jumlah de-oksidator yang lebih rendah (paduan besi dan aluminium) diperlukan, (xiii) meningkatkan kualitas baja, karena gas inert bertiup di akhir prosedur mengurangi konsentrasi gas dalam logam, dan (xiv) meningkatkan umur lapisan refraktori dengan menghindari terak kaya FeO yang terlalu panas.
Kerugian dari blowing gabungan adalah (i) peralatan konverter untuk proses tiupan gabungan lebih rumit, yang meningkatkan biaya bengkel, tetapi ini lebih dari dikompensasi oleh keuntungan yang disebutkan di atas, (ii) biaya gas Ar yang tinggi yang dalam banyak kasus mencoba untuk mengganti setidaknya sebagian dengan N2, (iii) ketersediaan nozel pengaduk bawah atau batu bata seringkali kurang dari 100% karena keausan batu bata yang lebih parah dibandingkan dengan lapisan konverter lainnya.