Proses Aglomerasi Bijih Besi dan Perkembangan Historisnya
Proses Aglomerasi Bijih Besi dan Perkembangan Historisnya
Ada empat jenis proses aglomerasi yang telah dikembangkan (Gambar 1). Mereka adalah (i) briket, (ii) nodulizing, (iii) sintering, dan (iv) pelletizing.
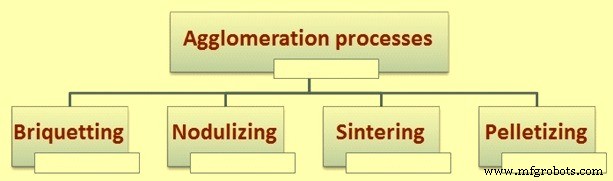
Gambar 1 Proses aglomerasi
Briket adalah proses yang paling sederhana dan paling awal diterapkan. Bijih besi berbutir halus ditekan ke dalam briket berbentuk bantal dengan penambahan air atau pengikat lain di bawah tekanan tekan mekanis yang tinggi. Dalam proses pembentukan nodul, butiran halus atau konsentrat bersama dengan bahan karbon dilewatkan melalui tanur putar miring yang dipanaskan oleh gas atau minyak. Suhu di dalam kiln cukup untuk melunakkan tetapi tidak cukup tinggi untuk melebur bijih. Nodul sangat bervariasi dalam komposisi dan terlalu padat, terak, tidak memiliki porositas yang diperlukan dan karenanya proses ini tidak banyak disukai. Briket dan nodulisasi adalah proses pengikatan dingin dan sebagian besar digunakan untuk daur ulang limbah bijih besi yang dipulihkan di pabrik baja. Sintering dan pelletizing adalah proses yang sangat penting untuk produksi besi.
Selama tahun 2014, menurut Asosiasi Baja Dunia, produksi besi tanur tinggi dan besi reduksi langsung masing-masing adalah 1183 juta ton dan 73 juta ton. Sebagian besar produksi ini berasal dari bijih besi dalam bentuk sinter dan pellet. Sementara bahan baku yang disukai untuk besi tanur sembur adalah sinter dan/atau pelet, bahan baku besi tereduksi langsung adalah pelet saja. Meskipun data produksi yang akurat untuk sinter dan pelet tidak dikompilasi, tetapi produksi sinter dan pelet dunia bersama-sama dapat diperkirakan dengan aman lebih dari 1300 juta ton per tahun untuk mendukung produksi besi sebesar 1256 juta ton.
Secara historis, bahan baku untuk tanur sembur dunia adalah bijih bongkahan yang terbentuk secara alami. Selama penambangan bijih besi, sejumlah besar dihasilkan. Denda ini karena tidak dapat digunakan dalam tanur tinggi sedang dibuang. Menipisnya deposit bijih lump berkualitas tinggi memaksa pengembangan sintering dari butiran halus yang dihasilkan untuk menggunakannya di tanur tinggi. Menipisnya deposit bijih lump berkualitas tinggi juga memaksa eksplorasi bijih kadar rendah yang membutuhkan penggilingan halus untuk konsentrasi. Mikro halus dari konsentrat bermutu tinggi ini harus diaglomerasi untuk digunakan dalam tanur sembur dan ini telah mengarah pada pengembangan proses peletisasi. Aglomerat ini, pada gilirannya, meningkatkan kinerja tanur sembur secara tajam dan menyebabkan perubahan besar dalam beban tanur sembur.
Sejarah sintering bijih besi
Pertengahan abad kesembilan belas, panci sintering kecil digunakan untuk dibangun di pertambangan tembaga di Inggris. Asal usul proses sintering kembali ke tahun 1887 ketika F. Haberlein dan T. Huntington dari Inggris menemukan proses aglomerasi untuk sintering bijih sulfida. Dalam proses ini, sintering dilakukan dengan sintering bed ditiup dengan udara dari bawah ke atas. Proses ini juga dikenal sebagai proses up-draft sintering. Proses tersebut dipatenkan pada tanggal 11 April 1905 (Paten no. 786814). Metode pot sintering yang digunakan ditunjukkan pada Gambar 2.
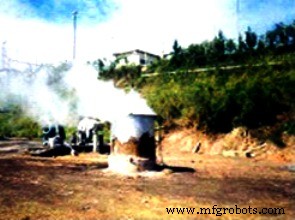
Gbr 2 Metode sintering pot
Pada tahun 1902, W. Job menemukan sintering sinter pirit dan bijih besi berdebu dengan penambahan batubara dan udara bertiup melalui tempat tidur dari bawah ke atas (nomor paten Jerman 137438). Pada tahun 1905, EJ Savelsberg mengembangkan proses sintering bijih besi dengan campuran sintering yang mengandung batubara dan kokas angin (nomor paten Jerman 210742). Pada tahun 1906, AS Dwight dan RL Lloyd keduanya dari USA menemukan mesin sinter tipe sabuk untuk sintering vakum. Pada tahun 1909 Von Schlippenbch menemukan mesin sintering tipe putar (nomor paten Jerman 226033). Pada tahun 1913, W. Barth merancang sabuk sintering untuk operasi dengan hembusan udara dari bawah ke atas (paten Jerman 276424). Pada tahun 1914, JE Greenawalt diberikan paten (nomor paten AS 1103196) untuk panci miring persegi panjang untuk sintering vakum. Jenis mesin sintering melingkar ditemukan pada tahun 1930 oleh VA Sakharnov.
Proses Huntington dan Haberlein adalah metode sintering terbaik sebelum paten Dwight Lloyd nomor 882517 tanggal 17 Maret 1908. Proses ini mampu menghasilkan beberapa bahan sinter, tetapi massa produk tidak memuaskan dalam komposisi dan mahal untuk ditangani. Itu diproduksi dalam pot besar, di mana berton-ton bijih dicampur dengan kapur dibakar di bawah aliran yang dipaksa ke atas melalui material. Di bawah kondisi ini produk yang seragam tidak dapat diproduksi. Bagian bawah muatan, karena tekanan yang diberikan oleh berat bahan yang ditumpangkan, direduksi menjadi terak yang tidak berpori, dan sementara di bagian atas muatan, sejumlah besar butiran halus tetap tidak disinter, karena pengadukan bijih. partikel, yang disebabkan oleh arus udara yang mengalir ke atas. Bahan yang tidak disinter memerlukan perlakuan ulang dan sejumlah besar bahan yang tidak berpori dan menyatu secara menyeluruh tidak dapat digunakan dalam tanur sembur sampai dipecah, dengan biaya besar, dan bahkan kemudian tidak memuaskan, karena struktur fisik dan kimianya.
Proses pemanggangan pot yang canggung dari Huntington dan Haberlein tidak sebanding dengan proses yang diungkapkan oleh paten Dwight Lloyd nomor 882.517. Proses yang dijelaskan dalam paten ini menghilangkan berbagai tingkat tekanan di seluruh massa, dan mempertahankan partikel bijih dalam keadaan diam selama pembakaran. Cara untuk mencapainya sederhana, tetapi efektif. Tekanan di seluruh massa dihindari dengan memperlakukan bijih dalam lapisan tipis. Keheningan partikel selama pembakaran dicapai, baik dengan menggunakan down draft dengan pengapian di permukaan atas, di mana agitasi partikel ditahan oleh bejana di mana mereka terkandung dan tekanan draft ke bawah, atau, jika draft ke atas digunakan, dengan menggunakan layar untuk menjaga ketenangan partikel di dekat permukaan atas. Dalam porositas, kerapuhan, dan struktur kimia, produk sinter Dwight Lloyd cukup ideal untuk pengolahan di tanur tinggi, dan prosesnya lebih unggul daripada metode apa pun dari penemuan sebelumnya untuk menyiapkan bijih halus untuk perawatan di tanur tinggi.
Mesin operasi pertama menurut metode ini dikembangkan oleh Arthur Smith Dwight (1864 – 1946) dan Richard Lewis Lloyd pada bulan Juni 1906 di tambang tembaga di Cananea dibangun, Meksiko dan pada tahun 1907 paten terkait. Pada tahun 1908 Dwight Lloyd memasang peralatan sintering di pabrik Ohio Colorado Smelting Company di Salida, Colorado. Aparatus ini adalah jenis mesin kontinu, di mana unggun bijih terus-menerus dipindahkan di bawah penyala dan melintasi ruang bagian, yang mempertahankan draft ke bawah selama proses sintering. Produk sinter secara otomatis dibuang oleh mesin setelah bahan dinyalakan, dipindahkan melintasi ruang isap, dan disinter.
Sebelum tahun 1910, JE Greenawalt, yang merupakan ahli metalurgi dengan pengalaman yang cukup, terlibat dalam studi proses desulfurisasi bijih sulfida. Dalam pekerjaannya, ia menemukan penggunaan tungku berpori, di mana bijih dipanggang di bawah aliran udara ke bawah, menghasilkan desulfurisasi yang efisien, dan bahwa aliran bawah dapat digunakan untuk menghemat elemen nilai yang mudah menguap dalam produk. pembakaran, biasanya dibawa melalui tumpukan tungku. Dia telah mencatat efek sintering dari proses ini pada bijih yang sedang dirawat, tetapi itu bukan tujuannya untuk menghasilkan sinter, dan dalam pengembangan proses pemanggangan, usahanya adalah untuk mencegah sintering, yang menghambat desulfurisasi total. Untuk tujuan ini, dalam dua paten down draft-nya, No. 839.064 dan 839.065 (18 Desember 1906), ia mempekerjakan rakyat jelata.
Greenawalt mengembangkan peralatan sintering intermiten berdasarkan draft ke bawah yang dipasang di Perusahaan Pemurnian Peleburan Modern, di Denver, Colorado sekitar tahun 1909. Proses Greenawalt ditemukan oleh Greenawalt beberapa bulan sebelum Proses Dwight Lloyd. Fitur dari proses ini adalah kebocoran udara yang sangat sedikit dan bagian bawah pot terbuat dari pelat baja parut atau berlubang. Feeding dan ignition furnace dapat digerakkan dengan sinter yang biasanya turun karena rotasi pot di atas hopper. Mesin ini terdiri dari panci yang dipasang di atas trunnion, di mana bahan disinter, aliran ke bawah dipertahankan oleh ruang hisap di panci di bawah tempat tidur di mana bijih disinter. Produk yang disinter dibuang dengan memutar panci di atas trunnionnya, ketika diisi ulang dan prosesnya diulang. Proses ini dipasang untuk sintering debu asap tanur sembur. Ini adalah pabrik sintering komersial pertama dari proses Greenawalt. Greenawalt mematenkan proses ini dan sejak tahun 1910, peralatannya telah digunakan secara luas dalam pengolahan bijih sulfida dan sejak tahun 1912 dalam pengolahan bijih besi.
Proses sintering Dwight Lloyd dengan down draft menjadi populer dan sebagian besar sinter yang diproduksi saat ini adalah dengan proses ini. Kedua penemu, yang mendirikan "Dwight and Lloyd Metallurgical Company" pada tahun 1907 di New York, tidak hanya membangun sendiri sejumlah besar pabrik ini, tetapi juga melisensikan dunia proses, antara lain di pabrik pabrik Lurgi. Mesin pertama yang mensinter bijih besi proses Dwight-Lloyd dibangun pada tahun 1910 di Amerika Serikat. Pabrik sintering Dwight-Lloyd pertama di Jerman dibangun pada tahun 1917.
Meskipun sejumlah besar perbaikan telah dilakukan sejak saat itu dalam desain mekanis mesin dan dalam proses sintering bijih besi, prinsip dasar prosesnya tetap sama.
Sejarah pembuatan pelet
Pelletizing berbeda dari sintering dalam bentuk pelet atau bola hijau yang belum dipanggang dan kemudian dikeraskan dengan pemanasan. Selama pengembangan proses sintering, upaya awal diarahkan untuk lebih meningkatkan proses penggunaan bijih halus mikro. Hal ini telah menyebabkan pengembangan proses yang merupakan alternatif untuk sintering. Proses ini dinamakan proses pelletizing. Di Swedia dan Jerman, penggunaan sejumlah besar butiran halus dalam campuran sinter menyebabkan produktivitas terbatas, dan dengan demikian membawa tahap pertama pengembangan dalam proses pembuatan pelet. Paten pertama untuk pembuatan pelet diberikan kepada AG Andersson dari Swedia pada tahun 1912 (Nomor paten 35124) dan pada tahun 1913 kepada CA Brackelsberg di Jerman. Pabrik pelet percontohan dengan kapasitas 120 ton per hari dibangun pada tahun 1926 untuk Krupp di pabrik Rheinhausen Steel. Pabrik ini dibongkar pada tahun 1937 untuk membuat ruang bagi pabrik sinter besar.
Tahap kedua pengembangan proses pelletizing berlangsung di Amerika Serikat. Pembibitan utama dari teknik ini dan sumber dari mana aliran perkembangan modern yang sukses muncul adalah Stasiun Percobaan Pertambangan di Universitas Minnesota, AS. Selama tahun 1940-an, para pekerja penelitian di stasiun ini di bawah arahan Dr. EW Davis dan rekan-rekannya meneliti masalah penggunaan bijih besi kadar rendah di Minnesota. Perhatian khusus diberikan pada batuan mengandung besi yang berdekatan dengan badan bijih utama Pegunungan Mesabi. Bijih berkadar rendah ini (25% sampai 30% Fe) sangat keras dan abrasif dan dikenal secara lokal sebagai ?taconites?. Bijih ini adalah bahan asli dari mana hematit Mesabi bermutu tinggi telah dikembangkan melalui pencucian dan oksidasi alami. Mineral besi yang dapat diperoleh kembali adalah magnetit yang disebarluaskan secara halus dan bijih harus digiling hingga berukuran sekitar 80% – 325 mesh untuk pembebasan, konsentratnya mengandung sekitar 65% besi dan 8% silika.
Pada tahun 1945 penelitian dan pengembangan di Stasiun telah membuat kemajuan yang cukup besar. Di sini tidak hanya teknik konsentrasi yang menjanjikan telah dikembangkan tetapi cara-cara baru telah diselidiki menggunakan konsentrat yang sangat halus yang dihasilkan. Konsentrat basah dibulatkan dalam drum yang berputar dan kemudian dikeraskan dengan perlakuan panas yang sesuai dalam tungku poros. Pelet keras (berdiameter sekitar 15 mm sampai 25 mm) dianggap sebagai bahan umpan tanur sembur yang cocok dan pengujian selanjutnya dalam tanur sembur eksperimental kecil sangat menggembirakan. Hasil ini menarik perhatian produsen besi dunia dan mengilhami beberapa pekerjaan yang sangat energik dan sukses di Swedia. Di AS, perusahaan baja dan bijih melihat dalam teknik ini sebagai sarana untuk memperpanjang sumber daya bijih yang kaya tetapi semakin berkurang di Minnesota dan Michigan dengan menyediakan bahan yang sampai sekarang tidak dapat digunakan. Perusahaan baru dibentuk untuk mengeksplorasi kemungkinan ini, dan penelitian diintensifkan. Pada tahun 1949, secara umum disepakati di Amerika Serikat dan Swedia bahwa cara terbaik untuk menyiapkan bola dari konsentrat adalah dalam drum yang berputar, tetapi pendapat berbeda tentang metode perlakuan panas.
Adalah penting bahwa peralatan yang digunakan, apapun bentuknya, harus (i) memberikan kontrol suhu yang ketat, (ii) membutuhkan jumlah bahan bakar minimum, yaitu harus memulihkan panas yang masuk akal, (iii) memiliki operasi yang cukup bebas masalah dan dapat diandalkan, dan (iv) memiliki unit output yang memadai.
Pada awalnya, 'shaft kiln' vertikal digunakan secara eksklusif dalam penelitian pabrik percontohan, bola konsentrat lembab dimasukkan ke atas dan bergerak ke bawah melawan aliran gas panas yang mula-mula mengeringkannya, dan kemudian menaikkan suhunya ke daerah pengerasan. Pelet yang mengeras ditarik dari dasar kiln.
Pekerjaan Davies mencapai puncaknya pada tahun 1943 ketika pelet eksperimental ditembakkan di tungku poros. Setelah Perang Dunia II, pada tahun 1947, unit percobaan serupa dibangun di Swedia. Pada tahun 1950-an, menjadi jelas bahwa pelletizing adalah metode yang layak secara ekonomi untuk mengaglomerasi konsentrat berbutir halus. Pabrik pelet pertama ditugaskan di Swedia di mana pelet ditembakkan di tungku poros dengan kapasitas 10 hingga 60 ton per hari.
Meskipun prosesnya secara intrinsik sederhana, dan karena itu menarik, dalam praktiknya terbukti memiliki beberapa fitur yang canggung. Di antara kesulitan yang paling akut pada awal 1950-an adalah (i) kesulitan mengamankan distribusi gas yang merata, (ii) kesulitan mengamankan penurunan stok yang merata, perawatan pelet yang seragam dan pelepasan produk yang bebas masalah, (iii) kesulitan mengamankan output tinggi dari satu unit, dan (iv) ketidakpastian tentang 'peningkatan skala' dan bentuk kiln yang paling tepat.
Masalah-masalah ini menyebabkan Reserve Mining Company di AS mencari jalan lain ke depan. Garis kemajuan baru berawal dari 'proses pembakaran Lepol', yang digunakan dalam industri semen. Proses ini, yang dikembangkan di Eropa, terdiri dari unit balling yang memberi makan jeruji yang bergerak di mana bola dikeringkan dan sebagian dikeraskan. Grate dibuang ke kiln berputar di mana proses pembakaran selesai, gas panas dari kiln disalurkan kembali ke grate di mana mereka melakukan fungsi pengeringan dan pengerasan yang baru saja disebutkan.
Mitchell telah melaporkan bahwa Dr. Lellep dari Allis-Chalmers Company menyarankan agar balling drum dan grate dapat digunakan dengan baik untuk memproduksi pelet yang dibakar dari konsentrat magnetit halus. Jika pengaturan seperti itu dapat dirancang untuk mengeringkan dan menembakkan pelet dan untuk memulihkan panas sensibel produk, itu mungkin memecahkan masalah aglomerasi magnetit halus dengan relatif murah.
Penelitian dilanjutkan di laboratorium Allis-Chalmers dengan hasil yang menggembirakan, dan pada tahun 1954 Perusahaan Penambangan Cadangan menugaskan mesin eksperimental 1.000 ton per hari berdasarkan prinsip-prinsip ini, tetapi dirancang secara mekanis pada jalur mesin sinter oleh Perusahaan Arthur G. McKee. Pelet dikeringkan dengan meniupkan udara panas ke atas melalui unggun, dan kemudian dikeraskan dengan menarik gas panas ke bawah dari tungku khusus. Pengaturan dibuat untuk mendinginkan pelet ini pada untai dan udara panas yang diperoleh digunakan untuk mengeringkan bola basah di ujung umpan, sehingga mengurangi konsumsi bahan bakar. Pengalaman pengoperasian yang berguna diperoleh dan setelah beberapa bulan percobaan, manajemen Cadangan memesan (April 1954) untuk desain enam mesin besar yang akan dipasang di Silver Bay, di tepi barat Danau Superior.
Perusahaan lain, bagaimanapun, bertahan dengan pengembangan proses tanur vertikal, sekali lagi untuk konsentrat magnetit, dan kemajuan mereka juga membenarkan pendirian beberapa instalasi besar:Pabrik Erie Mining Company di Hoyt Lakes, yang terbesar dari jenisnya, ditugaskan di 1957 dan termasuk 24 tungku poros vertikal.
Oleh karena itu, pada tahun 1950-an, baik kiln poros vertikal dan mesin parut bergerak sedang dikembangkan dan diterapkan pada peletisasi konsentrat magnetit halus. Konsentrat magnetit relatif mudah dibuat pelet. Partikelnya berbentuk butiran (bukan seperti pelat), dengan luas permukaan yang tinggi, dan dengan permukaan yang tidak terkontaminasi oleh zat flotasi. Jika dirawat dengan benar, mereka teroksidasi selama pembakaran, memberikan pelepasan panas yang berguna. Oksidasi juga terkait dengan pertumbuhan butir dan rekristalisasi yang berkontribusi pada pengembangan kekuatan akhir yang diperlukan. Namun, tidak semua konsentrat besi adalah magnetit. Di negara bagian Michigan ada deposit besar jaspilite di mana mineral besi adalah hematit specular yang terbagi halus. Bijih ini telah disebut mitra Michigan dari taconites Minnesota, tetapi mineral besi dapat diperoleh kembali dengan metode flotasi dan gravitasi, bukan dengan konsentrasi magnetik.
Konsentrat hematit tersebut menimbulkan masalah khusus dan eksploitasinya telah menjadi perhatian utama Perusahaan Besi Cleveland Cliffs. Pada tahun 1956 mereka mulai beroperasi di Eagle Mills (Michigan) dengan mesin parut, tetapi sejak itu dua pabrik besar yang sangat sukses telah dibangun menggunakan sistem tungku pembakaran, ini sebenarnya, proses Lepol secara keseluruhan diterapkan langsung ke masalah bijih besi. Sistem telah dikembangkan oleh Allis-Chalmers dan pabrik itu sendiri telah direkayasa dan dibangun oleh Perusahaan McKee. Secara umum dapat dikatakan bahwa proses Lepol (pengeringan dan pemanasan awal pada parutan dan pengerasan dalam tungku) telah terbukti sangat berhasil dengan konsentrat hematit (yang tidak memiliki keuntungan dari panas oksidasi eksotermis) sedangkan untuk magnetit proses 'lurus' parut' atau poros vertikal adalah alat yang biasa.
Pelletizing bijih besi adalah metode asal Swedia, dipatenkan pada tahun 1912 oleh AG Andersson (Yamaguchi et al ., 2010). Proses ini dikembangkan di AS pada tahun 1940-an, dan pabrik komersial pertama mulai beroperasi di Babbitt, Minnesota pada tahun 1952. Pabrik pelet bijih besi pertama dari jenis tungku pembakaran didirikan di Tambang Humboldt, Michigan pada tahun 1960. Allis-Chalmers (perusahaan pendahulu Metso) telah membangun sekitar 50 pabrik semacam itu. Namun, sangat sedikit dari pabrik tua yang dibangun sebelum tahun 1975 yang masih digunakan. Konstruktor lain dari pabrik grate-kiln adalah Kobe Steel, yang membangun pabrik pertama mereka pada tahun 1966 di Kobe Works, Nadahama, dan sejak itu telah membangun lebih dari sepuluh pabrik, yang sebagian besar masih digunakan.
Sejak tahun 2000, proses tungku pembakaran yang dikembangkan oleh Grup Shougang telah diadopsi dengan cepat di Cina. Pendirian pabrik grate-kiln baru di Cina sangat menonjol dalam dekade terakhir, dengan munculnya fabrikator baru seperti Jiangsu Hongda dan Citic. Ada peningkatan eksponensial sejak tahun 2000, terutama didorong oleh instalasi di China.