Dolomit – Pengolahan dan Penerapannya di Industri Besi dan Baja
Dolomit – Pemrosesan dan Penerapannya dalam Industri Besi dan Baja
Dolomit adalah mineral karbonat anhidrat. Ini adalah karbonat ganda kalsium dan magnesium (CaCO3.MgCO3). Ini adalah salah satu bahan baku penting yang digunakan dalam produksi besi dan baja.
Dolomit secara teoritis mengandung 54,35% CaCO3 dan 45,65% MgCO3 atau 30,41% CaO, 21,86% MgO, dan 47,73 % CO2. Namun, di alam, dolomit tidak tersedia dalam proporsi yang tepat ini. Oleh karena itu umumnya batuan yang mengandung MgCO3 berkisar antara 40% sampai 45% biasanya disebut dolomit.
Kegunaan utama dolomit dalam industri besi dan baja adalah (i) sebagai bahan fluks (ii) untuk perlindungan lapisan tahan api, dan (iii) sebagai bahan baku tahan api. Dolomit dalam industri besi dan baja biasanya digunakan dalam tiga bentuk. Ini adalah (i) dolomit mentah yang juga merupakan bentuk alami dari dolomit, (ii) dolomit yang dikalsinasi, dan (iii) dolomit yang disinter. Ketika dolomit digunakan sebagai bahan fluks maka digunakan sebagai dolomit mentah atau dolomit yang dikalsinasi. Ketika dolomit digunakan untuk perlindungan refraktori, digunakan dalam bentuk kalsinasi dan ketika dolomit digunakan sebagai bahan baku refraktori, digunakan dalam bentuk dolomit sinter. Kegunaan dan bentuk dolomit dalam industri besi dan baja ditunjukkan pada Gambar 1.
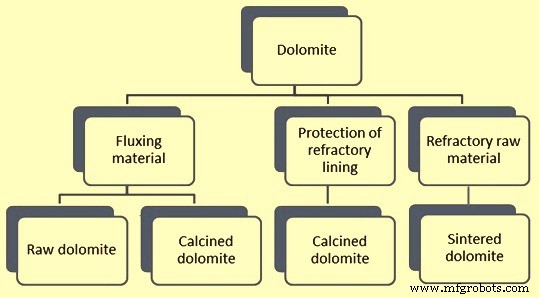
Gbr 1 Kegunaan dan bentuk dolomit dalam industri besi dan baja
Pengolahan dolomit
Dolomit setelah ditambang harus melalui beberapa proses sebelum dapat digunakan dalam berbagai proses. Proses dasar dalam produksi dolomit adalah (i) penggalian dolomit mentah, (ii) mempersiapkan dolomit yang ditambang untuk digunakan dengan menghancurkan dan sizing, (iii) kalsinasi dolomit mentah, (iv) memproses dolomit yang dikalsinasi lebih lanjut dengan menghidrasi ke menghasilkan dolomit terhidrasi jika diperlukan untuk digunakan, (v) sintering dolomit untuk digunakan sebagai bahan tahan api, dan (vi) berbagai operasi transfer, penyimpanan, dan penanganan. Semua proses ini mungkin tidak perlu ada di setiap pabrik.
Pada dasarnya tiga jenis produk dolomit digunakan dalam proses pembuatan besi dan pembuatan baja. Mereka adalah (i) produk dolomit mentah, (ii) produk dolomit terkalsinasi, dan (iii) produk dolomit sinter. Pemrosesan dolomit untuk produk ini dijelaskan di bawah ini.
Proses pertama berlangsung di tambang dolomit di mana bijih yang ditambang menjalani penghancuran dan penyaringan untuk pemisahan fraksi ukuran bijih yang berbeda. Di pabrik besi dan baja, di beberapa tempat, dolomit mentah diproses lebih lanjut. Contohnya adalah pabrik sinter di mana dolomit mentah dihancurkan dalam hammer mill hingga ukuran – 3 mm (umumnya dalam kisaran 85 % hingga 90 %).
Kalsinasi dolomit adalah proses perlakuan termal untuk melakukan dekomposisi termal dolomit mentah dan menghilangkan bagian LOI (loss on ignition) atau karbon di-oksida (CO2) dari komposisinya. Proses kalsinasi merupakan reaksi endotermik dan dilakukan dalam keadaan padat. Dolomit kualitas tinggi umumnya mengandung sekitar 40 % sampai 43 % MgCO3 dan sekitar 57 % sampai 60 % CaCO3. Dibutuhkan sekitar 2 ton dolomit mentah untuk menghasilkan satu ton dolomit terkalsinasi. Karena selama kalsinasi, CO2 dihilangkan dari dolomit mentah, dolomit yang dikalsinasi (i) berpori (ii) memiliki luas permukaan lebih tinggi, (iii) memiliki reaktivitas tinggi, dan (iv) higroskopis.
Ketika dolomit mentah dipanaskan, karbonat yang ada dalam dolomit terurai sesuai persamaan berikut.
CaCO3.MgCO3 + sekitar 725 kkal kalor =CaO.MgO +2 CO2
Kalsinasi dolomit mentah adalah proses pembakaran satu tahap sederhana yang dilakukan di tungku poros atau tungku putar. Dolomit mentah dimasukkan ke dalam kiln dan, saat bergerak melalui kiln, didekomposisi atau dikalsinasi dalam dua langkah. Pada tahap pertama CO2 mulai dilepaskan dari komponen MgCO3 pada dolomit dan pada tahap kedua CO2 mulai dilepaskan dari komponen CaCO3 pada dolomit. Suhu dekomposisi tergantung pada tekanan parsial CO2 yang ada di atmosfer proses.
Dekomposisi dolomit terjadi dalam dua tahap. Tahap pertama dimulai pada sekitar 550 derajat C ketika dekomposisi MgCO3 dimulai dan tahap kedua terjadi pada sekitar 810 derajat C ketika dekomposisi CaCO3 dimulai. Kedua tahap proses kalsinasi diwakili oleh persamaan berikut.
Tahap 1 – CaCO3.MgCO3 =CaCO3. MgO + CO2 (dalam kisaran suhu 550 derajat C hingga 700 derajat C)
Tahap 2 – CaCO3.MgO =CaO.MgO + CO2 (dalam kisaran suhu 810 derajat C hingga 900 derajat C)
Proses kalsinasi dapat dijelaskan dengan menggunakan sepotong dolomit yang terdekomposisi sebagian, yang profil tekanan parsial dan suhu CO2 ditunjukkan pada Gambar 2. Sampel terdiri dari inti karbonat padat yang dikelilingi oleh lapisan berpori. Dalam kiln kalsinasi pada suhu Tgas panas ditransfer oleh radiasi dan konveksi (dilambangkan dengan 'h') ke permukaan padat pada suhu Tsurface. Melalui konduksi termal (A) panas menembus melalui lapisan oksida untuk mencapai bagian depan reaksi, di mana suhu Trc. Karena entalpi reaksi berkali-kali lebih besar daripada energi internal, panas yang mengalir lebih jauh ke dalam inti dapat diabaikan selama reaksi. Oleh karena itu suhu inti hanya sedikit lebih rendah dari suhu depan. Setelah panas disuplai, konstanta reaksi kimia (k) kemudian terjadi di mana gaya penggeraknya adalah deviasi tekanan parsial CO2 dari kesetimbangan (p-eq – p-f). CO2 yang dilepaskan berdifusi (Dp) melalui lapisan oksida berpori ke permukaan dan akhirnya melewati konveksi (B) ke lingkungan di mana permukaan p tekanan parsial CO2 ada. Sifat kimia dan fisika dolomit terkalsinasi dipengaruhi oleh kalsinasi yang selanjutnya dipengaruhi oleh konduktivitas, koefisien perpindahan massa, dan difusivitas lapisan dolomit terkalsinasi.
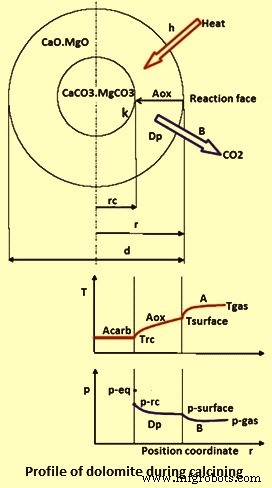
Gbr 2 Profil sampel dolomit selama kalsinasi
Untuk kalsinasi penuh dolomit dan tidak memiliki inti residu dolomit yang tidak dikalsinasi, panas yang disuplai ke permukaan dolomit mentah harus menembus melalui perpindahan panas konduktif ke inti. Suhu 900 derajat C harus dicapai di dalam inti setidaknya untuk waktu yang singkat karena atmosfer di dalam material adalah CO2 murni. Permukaan dolomit mentah harus dipanaskan hingga lebih besar dari 900 derajat C untuk mempertahankan gradien suhu yang diperlukan dan mengatasi efek isolasi bahan terkalsinasi di permukaan dolomit. Namun, ketika memproduksi dolomit terkalsinasi, suhu permukaan tidak boleh melebihi 1.100 derajat C hingga 1.150 derajat C karena jika tidak, kristalisasi ulang CaO akan terjadi dan menghasilkan reaktivitas yang lebih rendah dan dengan demikian mengurangi sifat slaking dari produk yang dikalsinasi.
Retensi atau waktu tinggal tertentu diperlukan untuk mentransfer panas dari gas pembakaran ke permukaan dolomit mentah dan kemudian dari permukaan ke inti dolomit mentah. Potongan dolomit mentah yang lebih besar membutuhkan waktu lebih lama untuk dikalsinasi daripada potongan yang lebih kecil. Pada prinsipnya, kalsinasi pada suhu yang lebih tinggi mengurangi waktu retensi yang dibutuhkan. Namun, suhu yang terlalu tinggi mempengaruhi reaktivitas produk. Hubungan antara suhu kalsinasi dan waktu retensi yang dibutuhkan untuk berbagai ukuran dolomit mentah ditunjukkan pada Tab 1.
Tab 1 Hubungan antara suhu kalsinasi dan waktu tinggal |
No. Sl. | Ukuran dolomit mentah | Suhu kalsinasi | Waktu tinggal (perkiraan) |
Satuan | mm | derajat C | Jam |
1 | 50 | 1000 | 2.2 |
| | 1200 | 0,75 |
2 | 100 | 1000 | 8.5 |
| | 1200 | 3 |
Beberapa jenis kiln yang berbeda digunakan untuk proses kalsinasi. Kiln ini dapat berupa tanur putar atau tanur poros. Jenis kiln yang akan dipilih sangat bergantung pada karakteristik dolomit mentah, tingkat produksi yang diantisipasi, biaya bahan bakar, biaya investasi, bahan bakar yang tersedia, kondisi lokal, infrastruktur dan lain-lain. Secara umum, semua data termasuk uji laboratorium harus dievaluasi sebelum memilih kiln kalsinasi.
Rotary kiln, dengan atau tanpa preheater, biasanya memproses dolomit mentah dengan ukuran material antara 10 mm dan 50 mm. Keseimbangan panas dari jenis kiln ini dikategorikan oleh kerugian yang agak tinggi dengan off-gas dan melalui shell kiln. Nilai tipikal untuk kerugian off-gas berada dalam kisaran sekitar 25% dan untuk kerugian shell kiln berada dalam kisaran sekitar 20% dari total kebutuhan panas. Hanya sekitar 60% energi bahan bakar yang dimasukkan ke dalam kiln dengan preheater yang digunakan untuk proses kalsinasi.
Dalam kasus kiln poros vertikal tunggal, terdapat ketidakseimbangan antara panas yang tersedia dari zona kalsinasi dan panas yang dibutuhkan di zona pemanasan awal. Bahkan dengan proses kalsinasi yang ideal, suhu gas buangan mungkin lebih tinggi dari 100 derajat C. Dalam kasus tipe kiln aliran paralel (PFR), ada pemanfaatan yang lebih baik dari panas zona kalsinasi dan meminimalkan hilangnya panas dalam gas buangan, sehingga konsumsi panas per ton dolomit terkalsinasi menjadi lebih rendah.
Perbandingan data mengenai tanur yang biasanya digunakan untuk kalsinasi dolomit dengan angka konsumsi penting dan ukuran bahan baku tipikal diberikan di Tab 2.
Tab 2 Perbandingan berbagai jenis kiln kalsinasi |
Jenis kiln kalsinasi | Kapasitas Kiln | Ukuran batugamping | Konsumsi bahan bakar spesifik | Konsumsi daya spesifik |
| tpd | mm | kkal/kg | kWh/t |
Tempat pembakaran PFR persegi panjang | 100-400 | 30-120 | 810-870 | Sekitar 20 |
Tempat pembakaran PFR melingkar | 300-800 | 30-160 | 810-870 | Sekitar 20 |
Kiln poros berbentuk lingkaran | 200-600 | 15-200 | 910-980 | Sekitar 30 |
Kiln poros tunggal | 50-300 | 10-100 | 980-1100 | Sekitar 35 |
Kiln putar dengan pemanas awal | 300-1200 | 10-50 | 1150-1350 | Sekitar 30 |
Kiln putar panjang tanpa pemanas awal | 300-1000 | 10-50 | 1600-1700 | Sekitar 20 |
Jenis ketiga pengolahan dolomit terdiri dari sintering dolomit. Proses ini juga terkadang disebut pemanggangan dolomit mentah. Dolomit yang disinter digunakan untuk membuat produk tahan api. Dolomit sinter juga dikenal sebagai dolomit mati terbakar yang dibuat dengan memanaskan dolomit mentah pada suhu yang lebih tinggi dari 1650 derajat C dan sebaiknya melebihi 1800 derajat C. Sintering dolomit mentah dilakukan dengan tujuan untuk mencapai curah spesifik maksimum kepadatan dan ketahanan yang tinggi terhadap hidrasi.
Proses yang paling umum untuk produksi dolomit sinter adalah proses pembakaran satu tahap dalam tungku poros atau tungku putar. Dolomit mentah dimasukkan ke dalam tanur dan, saat melewati tanur, dolomit akan terurai dalam dua langkah. Pada langkah pertama CO2 dilepaskan dari komponen MgCO3 dolomit mulai dari sekitar 550 derajat C dan pada langkah kedua komponen CaCO3 terurai pada suhu sekitar 810 derajat C. Setelah kalsinasi lengkap, dolomit yang telah dikalsinasi selanjutnya dipanaskan sampai suhu sintering . Pada suhu ini, porositas bahan yang sudah dikalsinasi berkurang sehingga menghasilkan peningkatan densitas spesifik produk yang sangat penting untuk aplikasi refraktori. Angka konsumsi tipikal serta beberapa ukuran dolomit mentah pakan kiln dasar diberikan di Tab 3.
Tab 3 Parameter umum untuk sintering dolomit |
No. Sl. | Parameter | Satuan | Kiln vertikal bersuhu tinggi | Kiln putar |
1 | Energi panas | kkal/kg | Sekitar 1200 | Sekitar 2400 |
2 | Energi listrik | kWh/ton | Sekitar 65 | Sekitar 65 |
3 | Ukuran umpan bahan baku | mm | 10-50 | 5-50 |
Kinerja proses sintering sangat bergantung pada sinterabilitas dari dolomit mentah, yang pada gilirannya dipengaruhi oleh karakteristik karakteristik tekstur tertentu seperti komposisi kimia, kemurnian, homogenitas, asal, genesis, porositas dan struktur kristal. Selain itu, bahan bakar (seperti abu bahan bakar padat) untuk proses pembakaran dapat memberikan pengaruh yang signifikan terhadap kualitas produk akhir. Dalam kasus dolomit mentah dengan kemurnian tinggi, kualitas produk yang memuaskan seringkali hanya dapat dicapai dalam kombinasi dengan bahan bakar padat dengan pengotor bahan bakar yang bertindak sebagai 'bantuan sintering'. Karakteristik dolomit mentah dapat mempengaruhi kualitas produk secara negatif sehingga menghasilkan densitas spesifik curah yang rendah dan tidak homogen atau dalam ketahanan yang buruk terhadap hidrasi. Salah satu parameter ini dapat membatasi aplikasi dalam industri tahan api, terutama jika batu bata tahan api berkualitas tinggi akan diproduksi. Hampir tidak mungkin untuk memperbaiki efek ini dengan operasi kiln yang dimodifikasi.
Tanur poros vertikal yang digunakan untuk sintering dolomit menggunakan briket dolomit yang dikalsinasi sebagai bahan umpan. Ia bekerja pada teknologi aliran berlawanan arah dan terdiri dari cangkang baja silinder dengan ketinggian putaran 10 m dan dilapisi dengan refraktori dasar. Briket dolomit yang telah dikalsinasi memasuki kiln melalui feeding hopper yang ditempatkan di bagian atas kiln. Saat melewati zona pemanasan awal di bagian kiln atas, briket dolomit dipanaskan dari suhu sekitar mendekati suhu sintering karena kontak intensif dengan gas kiln hulu yang panas.
Kiln poros tunggal dapat dirancang untuk mencapai suhu kiln jauh lebih dari 2000 derajat C pada konsumsi panas spesifik terendah untuk sintering dolomit untuk produksi refraktori dasar. Hal ini dicapai (i) dengan menggunakan prinsip aliran berlawanan arah, (ii) sistem multi-pembakar radial tertentu, (iii) tabel pelepasan yang beroperasi terus menerus, dan (iv) sistem pendingin produk terintegrasi di zona pelepasan kiln .
Kiln poros vertikal suhu tinggi dapat sepenuhnya memenuhi kriteria kualitas sambil memenuhi persyaratan sulit sehubungan dengan biaya produksi yang rendah. Juga konsep kiln memungkinkan operasi yang stabil bahkan pada kapasitas yang dikurangi. Kiln biasanya berdesain kompak yang memberikan kinerja andal yang diinginkan dan memastikan pengoperasian kiln yang berkesinambungan dan lancar. Waktu retensi yang agak singkat dari produk dalam kombinasi dengan paparan optimum ke atmosfir kiln menjelaskan dimensi kiln yang kecil dibandingkan dengan tingkat produksi spesifik yang tinggi. Berbagai parameter operasi dan profil suhu yang ditentukan dapat dengan mudah disesuaikan yang memberikan fleksibilitas tinggi dalam operasi kiln. Karakteristik ini digabungkan dengan konsumsi panas spesifik yang rendah serta biaya pengoperasian dan investasi yang rendah.
Penerapan dolomit dalam proses pembuatan besi dan baja
Selama produksi besi dengan rute tanur sembur (BF), dolomit ditambahkan baik dalam proses sintering atau sebagai umpan langsung di tanur sembur. Dolomit mentah biasanya digunakan untuk penambahan ini. Penambahan dolomit dilakukan selama pembuatan besi untuk mendapatkan persentase MgO yang diinginkan dalam terak BF. Penambahan dolomit melalui sinter lebih disukai karena CO2 dari dolomit dikeluarkan selama proses sintering. Dalam kasus sintering, dolomit dihancurkan hingga -3 mm (dalam kisaran 85 % hingga 90 %) dalam hammer crusher sebelum mencampurnya dalam campuran sinter. Dalam hal pengumpanan langsung ke tanur sembur, digunakan dolomit lump (ukuran 10 mm hingga 30 mm).
Dalam hal penambahan dolomit melalui sintering, saat ini dolomit yang dikalsinasi juga langsung digunakan. Penggunaan dolomit terkalsinasi dalam proses sintering memiliki keuntungan yaitu (i) Peningkatan karakteristik pengikatan campuran sinter, (ii) peningkatan produktivitas mesin sintering, (iii) peningkatan kekuatan sinter, dan (iv) pengurangan volume gas buang dengan keuntungan terkait.
Kandungan silika (SiO2) yang tinggi dalam dolomit yang digunakan untuk tujuan sintering lebih disukai karena SiO2 melawan efek alumina (Al2O3) dalam tanur tinggi.
Dalam produksi besi tereduksi langsung (DRI) dengan proses tanur putar, dolomit digunakan sebagai agen desulfurisasi. Dolomit mentah digunakan dalam kisaran ukuran 4 mm hingga 8 mm.
Penggunaan utama kedua dolomit adalah dalam pembuatan baja. Dalam pembuatan baja dolomit digunakan baik sebagai bahan fluks dan juga sebagai bahan tahan api. Untuk digunakan dalam pembuatan baja, kandungan SiO2 (karena sifatnya yang asam) dalam dolomit harus sangat rendah, sebaiknya kurang dari 1%. Ketika digunakan sebagai bahan fluks, digunakan dalam bentuk dikalsinasi. Sebagai bahan fluks, ia memiliki peran ganda. Dalam peran pertamanya itu adalah sumber beberapa kapur (CaO) dan dengan demikian mengurangi konsumsi kapur yang dikalsinasi. Namun peran kedua dolomit terkalsinasi adalah peran yang lebih penting. Dalam peran ini digunakan untuk melindungi lapisan magnesium-karbon dari bejana pembuat baja. Hal ini dilakukan dengan membuat terak pembuatan baja yang sangat jenuh dalam MgO pada suhu pembuatan baja.
Saat ini teknologi percikan terak sedang digunakan secara luas untuk meningkatkan umur lapisan bejana BOF (tungku oksigen dasar). Dalam teknologi ini, dolomit yang dikalsinasi ditambahkan ke terak cair yang tertahan yang akan disiramkan ke bejana BOF. Hal ini dilakukan untuk meningkatkan viskositas terak sehingga memiliki sifat lengket yang lebih baik dan juga untuk meningkatkan daya tahan terak.
Dolomit yang dikalsinasi juga semakin banyak digunakan sebagai bagian dari terak sintetis yang biasanya ditambahkan selama metalurgi sendok. Hal ini dilakukan untuk melindungi lapisan ladle terutama pada slag line.
Jika dolomit digunakan sebagai bahan refraktori, maka digunakan dalam bentuk dolomit yang disinter. Dolomit yang disinter digunakan dalam pembuatan baja untuk produksi batu bata tar dolomit, batu bata dolomit yang diresapi pitch atau batu bata dolomit berikat resin untuk lapisan bejana BOF, bejana AOD (argon oxygen decarburization), dan pada tingkat yang lebih rendah tungku busur listrik. Batu bata ini juga digunakan untuk lapisan sendok baja.
Refraktori monolitik berbasis dolomit seperti campuran senjata api juga digunakan untuk pemeliharaan refraktori tungku pembuatan baja. Gunniting biasanya dilakukan di area lapisan tahan api di mana ada keausan yang tinggi. Refraktori ini juga digunakan untuk membentuk perapian dan tepian di EAF, dan untuk memeliharanya secara teratur. Pemeliharaan area ini sering dilakukan dengan menggunakan besi tinggi, dolomit sinter yang diterapkan secara sering antara pemanasan menggunakan mesin pemintalan. Mesin diturunkan ke tungku dan menerapkan beberapa ton bahan fettling dalam beberapa menit di antara pemanasan. Solusi cepat dan berbiaya rendah ini digunakan terutama di bagian tungku di mana refraktori cepat aus.