Teknologi Pengurangan Langsung Energiron
Teknologi Pengurangan Langsung Energi
Teknologi reduksi langsung Energiron adalah teknologi reduksi langsung berbasis gas. Proses energiron mengubah pelet atau bongkahan bijih besi menjadi besi metalik. Ini menggunakan teknologi reduksi langsung HYL yang dikembangkan bersama oleh Tenova dan Danieli dan merupakan solusi kompetitif dan bersih lingkungan untuk menurunkan biaya produksi baja cair. Ini menggunakan konfigurasi pabrik yang sederhana, memiliki fleksibilitas untuk menggunakan berbagai sumber gas pereduksi dan memiliki penggunaan bijih besi yang sangat efisien dan fleksibel. Faktor kunci dalam banyak keuntungan proses secara langsung berkaitan dengan operasi bertekanannya.
Energiron adalah nama produk besi tereduksi langsung (DRI) yang diproduksi oleh teknologi reduksi langsung Energiron. Produk ini dinamakan demikian karena membawa energi yang cukup besar yang diwujudkan selama proses pembuatan baja.
Energiron adalah produk yang sangat metalisasi dengan kandungan karbon (C) yang dapat dikontrol dalam kisaran 1,5% hingga 5,0%. Semakin tinggi kandungan C Energiron menghasilkan energi kimia dalam proses peleburan electric arc furnace (EAF). Karakteristik unik yang stabil dari Energiron DRI menjadikannya produk yang dapat dengan aman dan mudah diangkut tanpa briket, mengikuti pedoman standar IMO (Organisasi Maritim Internasional).
Prosesnya fleksibel untuk menghasilkan tiga bentuk produk yang berbeda, tergantung pada kebutuhan spesifik setiap pengguna. Tiga bentuk DRI Energiron adalah DRI dingin, HBI (besi briket panas) atau DRI panas (besi 'Hytemp' dengan suhu pelepasan lebih besar dari 700 derajat C). Debit DRI dingin biasanya digunakan di toko peleburan baja yang berdekatan dekat dengan pabrik reduksi langsung. Itu juga dapat dikirim dan diekspor. HBI adalah DRI yang dibuang panas, dibriket, lalu didinginkan. Ini adalah produk pedagang yang biasanya dimaksudkan untuk ekspor ke luar negeri. Hytemp Energiron adalah DRI pelepasan panas, yang diangkut secara pneumatik dari pabrik reduksi langsung ke toko peleburan baja yang berdekatan untuk umpan langsungnya di tanur busur listrik (EAF).
Pekerjaan pengembangan awal dilakukan oleh Hylsa. Pada tahun 1977, Hylsa mendirikan divisi operasi baru (teknologi HYL) untuk tujuan mengembangkan dan mengkomersialkan teknologi reduksi langsung secara resmi. Pada tahun 2005, Techint Technologies mengakuisisi teknologi HYL. Kemudian divisi ini disebut Tenova HYL. Pada tahun 2006, aliansi strategis dibentuk oleh Tenova dan Danieli untuk desain dan konstruksi pembangkit DR berbasis gas di bawah merek dagang baru 'Energiron'. Skala komersial pertama
Pabrik proses HYL ZR (zero-reformer) dimulai pada tahun 1998. Pabrik Energiron ZR generasi baru pertama berkapasitas 2 juta ton per tahun dipasang di Suez Steel dan pabrik Energiron terbesar pertama di dunia dalam satu modul berkapasitas 2,5 juta ton per tahun dipasang di Nucor Steel.
Proses pengurangan energi langsung
Proses reduksi langsung Energiron menggunakan tungku reduksi poros untuk menghasilkan DRI. Ini dirancang untuk mengubah pelet besi / bijih gumpalan menjadi besi metalik dengan menggunakan gas pereduksi dalam tungku poros unggun bergerak gas padat. Oksigen (O2) dihilangkan dari bijih besi dengan reaksi kimia berdasarkan hidrogen (H2) dan karbon mono oksida (CO), untuk produksi DRI yang sangat metalisasi. Prosesnya fleksibel untuk menghasilkan tiga bentuk produk Energiron yang berbeda agar sesuai dengan pengguna akhir. Aspek kunci dari proses ini adalah kontrol independen dari metalisasi dan karbon produk (C). Proses reduksi langsung Energiron didasarkan pada skema ZR.
Gas pereduksi panas diumpankan di dalam tungku poros di zona reduksi. Di dalam tungku, gas-gas ini mengalir ke atas berlawanan arah dengan tempat tidur beban besi yang bergerak. Distribusi gas seragam dan ada kontak langsung tingkat tinggi antara gas dan padatan, tanpa batasan fisik pada aliran padatan atau gas di dalam unit. Gas buang (gas atas) meninggalkan tungku poros di sekitar 400 derajat C dan melewati recuperator panas gas atas, di mana energi gas dipulihkan untuk menghasilkan uap. Sebagai alternatif, energi gas buang dapat digunakan untuk memanaskan lebih dulu aliran gas pereduksi, dan kemudian gas buang dapat didinginkan melalui proses quenching/ scrubbing dengan air pendingin.
Gas pendingin yang digosok melewati kompresor daur ulang gas pendingin untuk didaur ulang ke tungku poros, setelah dibuat dengan gas alam (NG). NG disuntikkan sebagai make-up ke sirkuit gas pendingin untuk efisiensi optimal dan kontrol proses pendinginan dan karburisasi.
Penghapusan O2 dari bijih besi dilakukan dengan aksi gas pereduksi panas dan kemudian produk dikarburasi. Katup putar, yang terletak di bagian bawah tungku poros, mengatur aliran gravitasi kontinu dari muatan ke bawah melalui tungku reduksi. Energiron dikeluarkan melalui mekanisme otomatis, yang terdiri dari wadah dan kunci bertekanan. Pengumpan aliran yang dirancang khusus memastikan aliran seragam padatan di dalam tungku poros. Untuk DRI dingin, gas pendingin diumpankan ke bagian kerucut bawah tungku pada suhu sekitar 40 derajat C, mengalir ke atas berlawanan arus ke tempat tidur bergerak DRI.
Untuk pelepasan dan penggunaan produk panas, sirkuit pendingin dihilangkan dan DRI panas terus menerus dikeluarkan pada suhu lebih besar dari 700 derajat C. Untuk sistem transportasi pneumatik 'Hytemp', produk diangkut melalui gas pembawa ke tempat penampung yang terletak di toko peleburan baja, untuk pengumpanan terkontrol ke tungku busur listrik. Untuk produksi HBI, DRI panas terus menerus dibuang pada suhu lebih besar dari 700 derajat C ke mesin briket panas yang diatur di bawah ini. HBI didinginkan dalam konveyor pendingin bergetar menggunakan air pendingin dan kemudian dibuang ke konveyor transportasi HBI.
Salah satu karakteristik built-in dari aliran proses Energiron yang memiliki kepentingan lingkungan yang tinggi, adalah eliminasi selektif dari produk sampingan yang dihasilkan dari proses reduksi yaitu air (H2O) dan karbon di-oksida (CO2). Produk sampingan ini masing-masing dihilangkan melalui pembersihan gas atas dan sistem pembuangan CO2. Penghapusan selektif H2O dan CO2 mengoptimalkan persyaratan make-up. H2O yang dihasilkan selama proses reduksi dikondensasikan dan dihilangkan dari aliran gas dan sebagian besar debu yang terbawa bersama gas juga dipisahkan. Gas Scrubbed kemudian dilewatkan melalui kompresor daur ulang gas proses, di mana tekanannya ditingkatkan. Gas terkompresi, setelah dikirim ke unit pembuangan CO2, dicampur dengan make-up NG, sehingga menutup sirkuit gas pereduksi.
Skema Energiron ZR dicirikan oleh (i) pemanfaatan gas pereduksi kaya H2 dengan rasio H2 terhadap CO sekitar 5, (ii) suhu reduksi tinggi biasanya lebih dari 1050 derajat C, dan (iii) tekanan operasi tinggi biasanya dalam kisaran 6 kg/cm² hingga 8 kg/cm² di dalam tungku poros unggun bergerak. Tekanan operasi yang lebih tinggi memungkinkan (i) fluidisasi rendah, (ii) input halus yang lebih tinggi, (iii) produktivitas tinggi sekitar 10 ton per jam per meter persegi, (iv) konsumsi bijih besi yang lebih rendah, (v) pengurangan gas yang rendah kecepatan sekitar 2 meter per detik, dan (vi) konsumsi daya yang lebih rendah karena faktor kompresi yang lebih rendah. Hal ini menghasilkan tungku poros yang lebih kecil, mendorong distribusi gas yang homogen melalui unggun padat, dan meminimalkan kehilangan debu (kurang dari 1%) melalui carry-over gas atas karena gaya tarik yang lebih rendah. Hal ini juga menyebabkan deviasi standar yang sangat rendah dalam kualitas Energiron prima yang dihasilkan selain menurunkan konsumsi bijih besi secara keseluruhan (sekitar 1,4 ton bijih besi per ton DRI dengan penyaringan pada 3,2 mm dan tanpa peleburan kembali). Hal ini pada gilirannya menurunkan biaya operasional secara keseluruhan. Fitur lain yang berbeda dari skema proses ini, tanpa reformer terintegrasi/eksternal, adalah fleksibilitas yang lebih luas untuk karburisasi DRI.
Otomasi proses – Proses Energiron menggabungkan proses fisiko-kimia yang berbeda dan kompleks yang akan dioptimalkan untuk menghasilkan rangkaian reaksi kimia yang diinginkan serta pertukaran panas dan massa di antara berbagai fase gas, cair, dan padat. Untuk alasan ini, sistem otomasi lengkap digunakan yang pada gilirannya menggunakan teknologi terbaru yang tersedia di bidang pengontrol proses, diagnostik perangkat lunak, ketersediaan tinggi, dan fitur failsafe. Proses ini dikendalikan oleh lebih dari 5.500 variabel analog dan digital, yang secara otomatis dianalisis oleh sistem otomasi. Semua variabel proses yang berasal dari instrumen lapangan dikumpulkan secara konstan oleh berbagai sistem akuisisi (PLC, HMI), memberikan serangkaian informasi berharga untuk terus memantau dan mengoptimalkan proses. Perangkat lunak canggih dari proses Energiron memanfaatkan potensi besar ini dengan mengelola pengumpulan data, analisis, dan pelaporan web terintegrasi dengan alat statistik yang kuat untuk mendukung pengambilan keputusan. Hal ini akhirnya memungkinkan untuk lebih mengoptimalkan efisiensi proses, dengan mendeteksi titik setel optimal secara real-time, dengan konsekuensi penghematan energi yang penting.
Sistem kontrol Energiron didasarkan pada arsitektur yang terdiri dari sistem tingkat 1 tradisional untuk kontrol peralatan dengan 'sistem kontrol terdistribusi' (DCS), ditambah sistem tingkat 2, tidak hanya untuk pengawasan proses, pelacakan data, dan pembuatan laporan produksi tetapi juga untuk optimasi proses. Sebuah 'Proses Rekonstruksi Model' (PRM) telah dikembangkan. Ini menggunakan sinyal instrumentasi yang berasal dari PLC dan persamaan fisik untuk memberikan deskripsi lengkap tentang status pabrik. Dengan cara ini dimungkinkan untuk menghitung banyak item yang biasanya tidak dapat diukur seperti komposisi gas teratas dan rasio red/ox yang relevan.
Proses reaksi – Tiga jenis reaksi kimia berlangsung selama proses. Mereka adalah (i) reaksi reformasi, (ii) reaksi reduksi, dan (iii) reaksi karburasi. Reaksi berikut terjadi selama pemurnian insitu.
2CH4 + O2 =2 CO + 4 H2
CH4 + CO2 =2CO + 2H2
CH4 + H2O =CO + 3 H2
2H2 + O2 =2 H2O
CO2 + H2 =CO + H2O
Reaksi yang terjadi selama reduksi dan selama karburisasi DRI adalah sebagai berikut.
Fe2O3 + 3CO =2Fe + 3CO2
Fe2O3 + 3 H2 =2Fe + 3H2O
3Fe + CH4 =Fe3C + 2H2
3 Fe + 2 CO =Fe3C + CO2
3 Fe + CO+ H2 =Fe3C + H2O
Lembar aliran proses Energiron standar ada di Gambar 1.
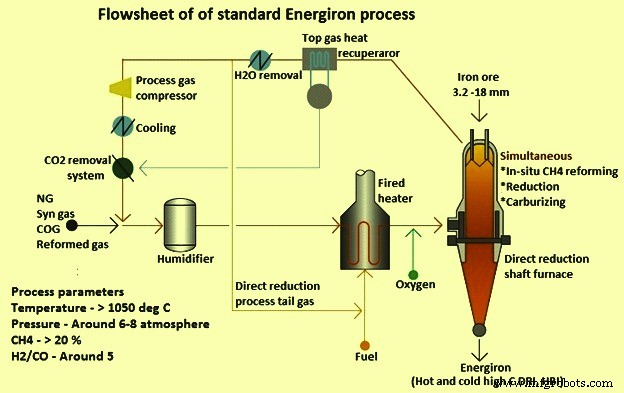
Gbr 1 Flow sheet proses Energiron
Keseimbangan energi khas dari proses Energiron ditunjukkan pada Gambar 2.
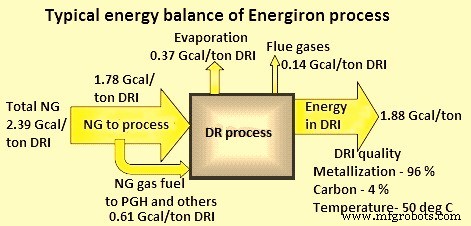
Gbr 2 Keseimbangan energi khas proses Energiron
Pabrik dan peralatan
Pabrik reduksi langsung Energiron terutama terdiri dari pabrik dan peralatan berikut beserta fitur karakteristiknya.
- Tungku poros reduksi yang menahan unggun bergerak. Tungku poros ini memiliki sistem pengisian beban besi dan sistem pelepasan produk.
- Sirkuit pereduksi gas, terdiri dari pemanas gas proses, heat recuperator gas atas, unit pendinginan/penggosok gas atas, kompresor daur ulang gas pereduksi, menara pelembapan, dan drum knock out.
- Pengoperasian tungku dilakukan dengan konsumsi NG dan air minimum, serta injeksi O2.
- Sistem pelepasan produk dapat memiliki (i) pendingin untuk produksi DRI dingin, (ii) mesin briket panas untuk produksi HBI, dan/atau (iii) sistem transportasi pneumatik Hytemp untuk mentransfer DRI panas langsung dari poros tungku ke tungku busur listrik (EAF).
- Sirkuit gas pendingin eksternal, yang terdiri dari unit pendinginan/penggosok dan kompresor daur ulang gas pendingin.
- Sistem adsorpsi, berdasarkan PSA (adsorpsi ayunan tekanan), untuk penghilangan karbon dioksida (CO2) dari aliran gas pereduksi.
- Peralatan penanganan bijih besi termasuk bak penampung bijih besi, konveyor transfer, stasiun penyaringan, sistem pelapisan pelet, konveyor pengumpanan, bersama dengan unit pengambilan sampel dan penimbangan.
- Sistem penanganan DRI yang terdiri dari konveyor dan peralatan terkait untuk pengangkutan DRI dingin.
- Menara pendingin beserta peralatan penyaringan dan pompa.
- Sistem air pendingin proses, berdasarkan sirkuit tertutup untuk meminimalkan konsumsi air, dengan clarifier dan kolam pengendapan.
- Sistem kontrol dan instrumentasi proses, menggunakan kontrol terdistribusi berbasis mikroprosesor.
- Gindu listrik, motor listrik, dan penerangan.
- Sistem gas inert biasanya didasarkan pada gas nitrogen (N2).
- Kompresor udara
Parameter operasi dan konsumsi spesifik
Karakteristik khas produk dari proses Energiron ZR diberikan di Tab 1.
Tab 1 Karakteristik khas produk |
No.Sl. | Barang | Satuan | DRI | HBI | Setrika modern |
1 | Metalisasi | % | 92 – 95 | 92 – 95 | 92 – 95 |
2 | Karbon | % | 1,5 – 5,5 | 1,5 – 2,5 | 1,5 – 5,5 |
3 | Suhu | Deg C | 40 | 40 | > 600 |
4 | Kepadatan massal | ton/cum | 1,60 | 2,50 | 1,60 |
5 | Kepadatan yang terlihat | ton/cum | 3,20 | 5.00 | 3,20 |
6 | Ukuran nominal | mm | 6 – 15 | 110 x 60 X 30 | 6 – 15 |
7 | Fe3 C | % | 25 – 60 | 25 – 30 | 25 – 60 |
Parameter operasi tipikal dan konsumsi spesifik untuk proses Energiron ZR diberikan di Tab 2.
Tab 2 Parameter operasi umum &konsumsi spesifik untuk proses Energiron ZR |
No. Sl. | Item | Satuan | DRI Dingin | HBI | DRI Panas | |
1 | Karbon | % | 4,5 | 2,5 | 2,5 | 4,5 | 4.5 | |
2 | Metalisasi | % | 93 | 93 | 93 | 93 | 93 | |
3 | Suhu DRI | Deg C | 40 | 40 | 700 | 700 | 700 | |
4 | Beban besi | ton/ ton | 1,36 | 1,39 | 1,41 | 1,36 | 1,39 | |
5 | Gas alam | Gkal/ton | 2,25 | 2.20 | 2.23 | 2,35 | 2,25 | |
6 | Listrik | kWh/ton | 65 | 65 | 80 | 65 | 65 | |
7 | Oksigen | N cum/ton | 42 | 53 | 53 | 48 | 53 | |
8 | Air | Cum/ton | 0,8 | 0,8 | 1.1 | 0,8 | 0,8 | |
9 | Nitrogen | N cum/ton | 12 | 12 | 19 | 18 | 18 | |
Emisi tipikal dari proses Energiron ZR diberikan di Tab 3.
Tab 3 Emisi tipikal dari proses Energiron ZR |
No. Sl. | Emisi | Satuan | Nilai |
1 | NOx dengan pembakar NOx yang sangat rendah | mg/N cum | 50 – 80 |
2 | NOx dengan penghilangan katalitik selektif | mg/N cum | 10-50 |
3 | CO | mg/N cum | 20-100 |
4 | Debu dari tumpukan pemanas/reformer | mg/N cum | 1 – 5 |
5 | Debu dari pembersihan material handling | mg/N cum | 5 – 20 |
| | | | |
Fitur proses Energiron ZR
Proses Energiron ZR telah mengurangi ukuran dan meningkatkan efisiensi pabrik reduksi langsung. Gas pereduksi dihasilkan dengan reformasi in-situ dari hidrokarbon gas alam di dalam tungku poros reduksi, dengan memberi makan NG sebagai make-up ke sirkuit gas pereduksi dan injeksi O2 pada saluran masuk tungku poros. Dalam prosesnya, efisiensi reduksi optimum tercapai, karena gas pereduksi dihasilkan di bagian reduksi. Karena itu, reformer gas pereduksi eksternal tidak diperlukan. Biasanya, efisiensi energi keseluruhan dari proses Energiron ZR lebih dari 80%, yang dioptimalkan oleh reformasi in-situ di dalam tungku poros. Produk mengambil sebagian besar energi yang dipasok ke proses, dengan kehilangan energi minimum ke atmosfer.
Dampak pada ukuran pabrik menghilangkan reformer gas eksternal adalah signifikan. Untuk kapasitas 1 juta ton per tahun, kebutuhan lahan berkurang sekitar 60%. Ini juga memudahkan lokasi pabrik DR yang berdekatan dengan toko peleburan baja.
Keuntungan tambahan dari proses Energiron ZR adalah fleksibilitas untuk karburisasi DRI, yang memungkinkan pencapaian level C hingga 5%. Hal ini karena potensi karburasi yang ditingkatkan dari gas di dalam poros, yang memungkinkan produksi terutama Fe3C. DRI dengan kandungan Fe3C yang tinggi memiliki reaktivitas yang jauh lebih rendah daripada DRI normal karena panas disosiasi yang lebih tinggi diperlukan untuk Fe3C.
Kondisi operasi yang ada dalam proses reduksi langsung Energiron dicirikan oleh suhu tinggi (lebih tinggi dari 1050 derajat C), adanya H2O dan CO2 sebagai oksidan yang dihasilkan oleh pembakaran parsial gas pereduksi dengan injeksi O2. Kondisi ini mendorong reformasi in-situ dari hidrokarbon. Setelah H2 dan CO dihasilkan, reduksi simultan dari bijih besi dan karburisasi DRI berikutnya, berlangsung di dalam reaktor, membuat skema proses ini menjadi sangat efisien dalam hal pemanfaatan energi dan konsumsi energi secara keseluruhan.
Skema dasar Energiron ZR memungkinkan penggunaan langsung NG. Pembangkit yang menggunakan proses Energiron untuk reduksi langsung juga dapat menggunakan peralatan reformasi NG uap konvensional sebagai sumber eksternal untuk mengurangi gas, yang telah lama menjadi ciri proses reduksi langsung berbasis gas. Sebagai pengganti NG, gas lain seperti H2, syngas yang dihasilkan dari sistem gasifikasi batubara, pet coke dan bahan bakar fosil sejenis, dan coke-oven gas (COG), antara lain, juga dapat digunakan sebagai sumber potensial gas pereduksi, tergantung pada situasi dan ketersediaan tertentu. Bagaimanapun, skema proses dasar yang sama digunakan terlepas dari sumber gas pereduksi.
Fitur unik dari teknologi Energiron ZR adalah kemampuannya untuk menghasilkan kadar karbon tinggi yang terkontrol dalam DRI dalam bentuk besi karbida (Fe3C) (biasanya lebih besar dari 90%). Kadar karbon DRI hingga 5% dapat diperoleh, karena kondisi yang ada di zona reduksi reaktor. Kondisi ini terdiri dari konsentrasi metana (CH4) yang tinggi (sekitar 20%) bersama dengan H2 dan CO, dan suhu lapisan yang tinggi. Kondisi ini mendukung difusi C ke dalam matriks besi dan pengendapan Fe3C. DRI dengan kandungan Fe3C yang tinggi menunjukkan reaktivitas yang jauh lebih rendah daripada DRI normal.
Salah satu karakteristik penting dari pembangkit reduksi langsung Energiron adalah kemungkinan untuk merancang proses untuk kebutuhan air make-up nol. Hal ini dimungkinkan terutama karena air adalah produk sampingan dari reaksi reduksi karena dikondensasikan dan dikeluarkan dari aliran gas. Akibatnya, dengan penerapan sistem air sirkuit tertutup berdasarkan penggunaan penukar panas air alih-alih menara pendingin konvensional, tidak ada kebutuhan untuk air make-up segar dan sebenarnya hanya sedikit aliran air yang tersisa di baterai. batas.
Emisi dari pembangkit reduksi langsung Energiron
Emisi pembangkit energiron sesuai dengan peraturan lingkungan yang paling ketat. Hal ini dicapai terutama karena sifat dari proses itu sendiri. Teknologi Energiron efisien secara desain karena konfigurasi prosesnya. Oleh karena itu, sementara mencapai efisiensi termal keseluruhan yang tinggi di pabrik, tidak ada kebutuhan yang signifikan untuk pemanasan awal udara pembakaran ke suhu tinggi di reformer (bila digunakan) atau di pemanas, sehingga menghilangkan kemungkinan pembentukan NOx yang tinggi. Emisi NOx juga dapat dikurangi dengan mengadopsi pembakar NOx ultra-rendah. Peningkatan lebih lanjut dapat diperoleh dengan penerapan teknologi SCR (selective catalytic reduction).
Energiron adalah teknologi reduksi langsung yang sangat bersih yang tersedia. Bergantung pada konfigurasinya, pembangkit Energiron dapat menghilangkan dari 60% hingga 90% dari total emisi CO2. Emisi CO2 dapat sangat berbeda antara dua teknologi yang digunakan untuk produksi DRI. Terlepas dari apakah menggunakan NG, syngas, atau COG, make-up gas pereduksi ke pabrik reduksi langsung mengandung C, baik dalam bentuk hidrokarbon dan/atau senyawa karbon (CO, CO2). Selain itu, terlepas dari konfigurasi proses reduksi langsung, hanya 15% hingga 40% (bergantung pada kandungan C dalam DRI) yang meninggalkan proses sebagai C gabungan dalam DRI, sisanya keluar sebagai CO2.
Karena DRI yang dihasilkan dari proses Energiron ZR mengandung persentase C yang lebih tinggi, jumlah C yang dihilangkan dalam bentuk CO2 lebih sedikit. Perbedaan pembangkitan gas CO2 dapat dilihat jika dibandingkan dengan pembangkitan gas CO2 dalam konfigurasi reduksi langsung dengan catalytic reformer eksternal yang terintegrasi dengan tungku poros reduksi langsung yang digunakan sebagai sumber make-up gas pereduksi. Dalam hal pembangkitan dalam konfigurasi reduksi langsung dengan catalytic reformer eksternal yang terintegrasi dengan tungku poros reduksi langsung, dari total proses makeup NG yang mengandung 140 kg C per ton DRI, sekitar 25 kg C per ton DRI ( 17%) meninggalkan proses sebagai bagian dari DRI dan sisanya dilepaskan sebagai gas buang dari reformer. Angka-angka ini dibandingkan dengan 110 kg C per ton DRI, dari mana 40 kg C per ton DRI (36%) ada dalam DRI yang diproduksi dalam kasus proses Energiron ZR. Selain itu, dari sisa 70 kg C per ton DRI, 65 kg C secara selektif dihilangkan sebagai CO2 murni, yang dapat digunakan untuk aplikasi lain atau diasingkan. Penghapusan kedua produk sampingan yang dihasilkan dari proses reduksi H2O dan CO2, meningkatkan pemanfaatan gas dalam proses hingga lebih dari 95%. Singkatnya, proses Energiron menyediakan eliminasi selektif bawaan sekitar 65% dari total input C sebagai CO2 (sekitar 240 kg CO2 per ton DRI).
Pembangkit energiron menawarkan pilihan unik untuk pemulihan selektif CO2. Sistem penyerapan CO2 tidak hanya menangkap CO2, tetapi juga sulfur, setiap kali ada dalam aliran gas proses, mengurangi emisi SO2 keseluruhan dari pembangkit sekitar 99%.
H2 sebagai gas pereduksi
Di pabrik besi dan baja, H2 diharapkan dapat menggantikan C sebagai sumber energi untuk proses reduksi bijih besi dalam waktu dekat. Dalam kasus proses reduksi langsung berbasis gas, H2 akan menggantikan NG. Proses Energiron ZR telah disiapkan untuk menggunakan H2 dalam jumlah berapa pun sebagai pengganti NG tanpa penyesuaian peralatan utama. Bahkan, dalam skema proses Energiron ZR, penggunaan H2 akan tercermin dalam operasi yang lebih lancar dan peningkatan produktivitas karena kebutuhan in-situ reforming gas NG akan lebih rendah.
Penggunaan konsentrasi H2 setinggi 70% pada saluran masuk poros reduksi sudah terbukti dengan baik di pabrik reduksi langsung Energiron yang ada, yang melibatkan reformer uap untuk menghasilkan gas pereduksi (H2 dan CO).
Namun, dengan penggunaan H2 sebagai pengganti NG sebagai input energi, akan terjadi penurunan % C di DRI Karena akan mengencerkan konsentrasi CH4 dalam gas pereduksi, tetapi karena konfigurasi proses yang fleksibel dari Skema Energiron ZR dalam hal distribusi make-up ke sirkuit reduksi dan penggunaan bahan bakar, dimungkinkan untuk mencapai 3,5%C bahkan pada input energi 35% sebagai H2 (atau sekitar 64% sebagai volume – N cum per ton DRI) . Untuk 70 % H2 sebagai energi (sekitar 88% sebagai volume – N cum per ton DRI), C yang diharapkan dalam DRI akan kurang dari 2,0 %.
Aliansi dengan NSENGI
Pada tahun 2014, Tenova HYL dan Danieli, telah menandatangani perjanjian dengan Nippon Steel &Sumikin Engineering Co., Ltd. (NSENGI) untuk menggabungkan dan mengkomersialkan teknologi reduksi langsung Energiron mereka dengan teknologi tanur sembur yang dioptimalkan, serta teknologi syngas (tinggi efisiensi gasifikasi batubara dan teknologi pemanfaatan gas hasil samping pabrik baja) yang dikembangkan dan dimiliki oleh NSENGI. Tujuan aliansi baru adalah untuk menggabungkan kegiatan penelitian dan pengembangan dengan keahlian masing-masing di Energiron DR, teknologi tanur sembur dan syngas, dengan tujuan akhir mengembangkan teknologi pembuatan besi baru yang akan mengurangi emisi CO2 dan biaya operasi, sekaligus meningkatkan produktivitas dan /atau mengurangi pengeluaran modal untuk fasilitas pembuatan baja terintegrasi.