Perusahaan pembangkit listrik tenaga angin sampai ke akar masalah es
Dengan angin sepoi-sepoi, turbin angin – membentang setinggi 262 kaki – dengan anggun memutar tiga bilahnya yang kuat, menghasilkan listrik yang cukup bersih dan terbarukan untuk memberi daya pada 750 rumah selama 24 jam. Saat angin sepoi-sepoi berubah menjadi angin kencang yang dikombinasikan dengan es, hujan yang membekukan, salju, dan bahkan kabut yang membekukan, anemometer turbin, yang mengukur kecepatan dan kekuatan angin, dapat membeku dan mengakibatkan waktu henti yang mahal bagi perusahaan tenaga angin seperti Clipper Windpower.
Tentang Clipper Windpower
Berkantor pusat di Carpinteria, California, Clipper Windpower adalah perusahaan yang berkembang pesat yang bergerak di bidang teknologi energi angin, manufaktur turbin angin, dan pengembangan proyek angin. Clipper mempekerjakan lebih dari 850 orang di Amerika Serikat, Denmark dan Inggris. Di jantung operasi manufakturnya adalah fasilitas manufaktur dan perakitan bersertifikat ISO 9001 yang mulai beroperasi di Cedar Rapids, Iowa, pada Maret 2006.
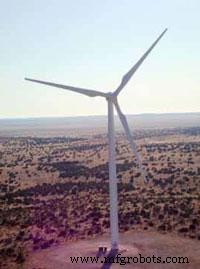
Beralih ke Kualitas untuk Meningkatkan Ketersediaan Turbin
Saat turbin angin pertama Clipper mulai beroperasi di barat laut Iowa, Illinois barat, dan New York barat dekat Buffalo, musim dingin 2007-2008 melanda dengan keras dan cepat, dengan hujan dan kabut beku yang menyebabkan unit anemometer gagal. Sementara menara terus berjalan, tanpa anemometer, tidak ada panduan ke arah mana untuk menggerakkan bilah sepanjang 153 kaki untuk memanfaatkan angin dengan paling efektif. Clipper awalnya mencoba mengatasi masalah melalui peningkatan perangkat lunak, tetapi segera anemometer tambahan mulai membeku, menambah masalah dan memengaruhi ketersediaan turbin.
Tanpa solusi cepat yang tersedia dan dengan bertambahnya jumlah anemometer yang terpengaruh setiap hari, Clipper memprakarsai root cause analysis (RCA), bagian integral dari proses penyelesaian masalah Six Sigma define, measure, analyze, improve, dan control (DMAIC). Pendekatan DMAIC yang ketat mendefinisikan langkah-langkah yang diikuti tim, dimulai dengan mengidentifikasi masalah dan diakhiri dengan menerapkan solusi jangka panjang. Untuk mengevaluasi proyek RCA potensial, Mike Trueg, manajer jaminan kualitas lapangan/peningkatan berkelanjutan di pabrik Cedar Rapids Clipper, menggunakan matriks yang mengukur dampak keselamatan, kualitas, dan ketersediaan turbin.
“Untuk proyek ini, penilaian memenuhi kriteria karena dampak besar pada ketersediaan turbin,” kata Trueg, anggota senior ASQ.
Sebuah proyek RCA disewa untuk mengatasi masalah anemometer terkait cuaca. Tujuan proyek adalah untuk mengidentifikasi akar penyebab kegagalan anemometer yang menyebabkan downtime dan penurunan ketersediaan turbin. Sebuah tim proyek ditugaskan untuk membuat rencana tindakan dan menerapkan tindakan korektif pada awal musim dingin berikutnya.
Mengikuti Pendekatan DMAIC
Memilih anggota tim untuk proyek RCA ini agak sulit, kenang Ellen Sennett, yang menjabat sebagai co-leader proyek.
“Kami mulai dengan orang-orang yang memiliki pengalaman dengan masalah listrik karena tampaknya itulah masalahnya,” kata Sennett, seorang karyawan Clipper selama dua tahun.
Secara keseluruhan, tujuh bidang pemangku kepentingan terwakili dalam tim perbaikan, seperti yang ditunjukkan pada tabel di Gambar 1.
Gambar 1
Tidak semua anggota tim berpartisipasi selama setiap tahap proyek; misalnya, perwakilan vendor datang setelah akar permasalahan diidentifikasi. Tim bekerja melalui langkah-langkah seperti yang dijelaskan pada Gambar 2.
Gambar 2
Mendefinisikan Masalah
Segera setelah kegagalan awal terkait cuaca, perusahaan mulai mengumpulkan data setiap kali cuaca buruk membuat turbin offline. Pengumpulan data awal ini menghasilkan piagam proyek RCA.
Mengukur untuk Mengukur Masalah
Data yang dikumpulkan menunjukkan bahwa, meskipun kondisi cuaca musim dingin sangat buruk, curah hujan dan suhu berada dalam spesifikasi pemasok untuk anemometer. Tim RCA mengembangkan matriks pemasok-input-proses-keluaran-pelanggan (SIPOC) untuk mengukur masalah dan setiap aspek yang dirasakan dari akar penyebab. Untuk menentukan kemungkinan akar penyebab kegagalan peralatan, mereka juga menyelesaikan diagram tulang ikan, yang menghasilkan 45 item untuk studi lebih lanjut. Selanjutnya, anggota tim RCA memasukkan penyebab potensial ke dalam matriks sebab dan akibat untuk fokus pada penyebab yang paling mungkin. Alat matriks memungkinkan tim untuk mengurangi penyebab potensial menjadi sembilan item untuk mode kegagalan dan analisis efek (FMEA).
Menganalisis Data untuk Menentukan Akar Penyebab
Langkah selanjutnya untuk Sennett dan timnya adalah mengembangkan rencana pengumpulan data yang mencakup penyebab potensial dengan nomor prioritas risiko tertinggi dari FMEA. Secara keseluruhan, data dikumpulkan dari pengujian yang dilakukan pada 13 penyebab potensial FMEA – mulai dari pelatihan yang tidak tepat tentang instruksi kerja untuk memasang kabel sirkuit pemanas hingga masalah dengan memanaskan tutup transduser pada anemometer.
Setelah pengumpulan data dan pengujian anemometer, tim RCA menyimpulkan bahwa desain pemasok sirkuit pemanas tidak memenuhi spesifikasi yang diiklankan. Kegagalan ini menyebabkan sirkuit pemanas yang tidak mencukupi untuk aplikasi Clipper dan, dengan demikian, menyebabkan kegagalan terkait cuaca pada turbin angin perusahaan.
Sennett ingat bahwa membuat pemasok anemometer mengakui bahwa produknya tidak berfungsi di lapangan seperti yang dijanjikan adalah tantangan nyata. Akhirnya, data dari lapangan dan proyek RCA meyakinkan pemasok. Jika dipikir-pikir, Sennett merasa bahwa mungkin timnya bisa melibatkan pemasok dalam proyek lebih cepat.
“Akan bermanfaat jika pemasok menjalani langkah-langkah DMAIC bersama kami dan menemukan akar masalahnya, alih-alih kami menemukannya dan memberi tahu mereka bahwa mereka memiliki masalah,” katanya.
Mengidentifikasi dan Menerapkan Solusi
Dengan akar permasalahan yang ada, tim mulai mengevaluasi peningkatan pada sirkuit pemanas anemometer melalui serangkaian tes validasi simulasi cuaca musim dingin.
Trueg melaporkan bahwa, memiliki 405 unit untuk diganti, analisis data sangat penting:“Itulah sebabnya kami menciptakan lingkungan cuaca musim dingin kami sendiri dengan mesin angin dan perangkat gerimis untuk memverifikasi solusi kami. Kami tidak ingin memulihkan semua situs ini dan kemudian harus melakukannya lagi.”
Mengikuti standar militer 810F seksi 521.2 untuk hujan es/beku, tim Clipper mengarahkan tiga putaran pengujian laboratorium untuk menganalisis kinerja tiga prototipe untuk anemometer yang ditingkatkan. Prototipe baru pertama segera ditolak karena simulasi kondisi musim dingin menciptakan penumpukan es, yang dengan cepat menyebabkan anemometer gagal. Prototipe kedua juga gagal sebelum versi ketiga akhirnya bertahan dalam kondisi cuaca ekstrem di lab.
Setelah pengujian selesai, tim membuat rencana tindakan. Tujuan rencananya adalah agar semua anemometer pada masing-masing dari 405 turbin di seluruh negeri diganti dengan versi yang baru dirancang pada 30 Maret 2010.
Mengontrol untuk Mengonfirmasi Peningkatan
Selain peningkatan sirkuit pemanas berdasarkan pengujian laboratorium, beberapa kontrol lain juga diperkenalkan:
- Vendor melakukan pemeriksaan 100 persen produk melalui uji pembakaran tiga hari pada sistem pemanas unit. Ini menghilangkan pengiriman produk yang cacat.
- Semua anemometer diuji dengan unit kontrol turbin di fasilitas manufaktur untuk memvalidasi fungsionalitas.
- Desain anemometer baru juga menggabungkan konektor yang hanya dapat dipasang satu arah ke kotak sambungan, sehingga menghilangkan kabel yang tidak sesuai di lapangan.
- Pengkabelan diberi kode warna untuk operator yang memasang konektor.
Desain Baru Sesuai dengan Alam Semesta
Sementara pengujian lapangan dimulai pada akhir musim dingin 2008-2009, Clipper menyadari pentingnya membawa pengujian ke musim dingin 2009-2010 untuk mengkonfirmasi efektivitas rencana perbaikannya. Sekali lagi, Alam bekerja sama dengan melemparkan sekantong penuh trik musim dingin, karena angin 40 hingga 50 mph, es setengah inci, salju 4 hingga 8 inci, dan suhu minus-15 derajat ke bawah dilaporkan pada berbagai ladang angin.
Terlepas dari kondisi ini, Clipper hanya mencatat dua masalah anemometer terkait cuaca, dengan tingkat kegagalan 1,6 persen. Clipper segera menemukan bahwa kedua kegagalan tersebut disebabkan oleh masalah tim perakitan pemasok dan tidak secara langsung terkait dengan peningkatan yang dihasilkan oleh proyek RCA. Dengan perbaikan dan kontrol yang diverifikasi, proyek RCA secara resmi ditutup.
Tim RCA terus memberi informasi kepada pelanggan turbin selama proses DMAIC dengan presentasi tentang langkah-langkah perbaikan untuk mengurangi kegagalan terkait cuaca. Anggota tim berjalan melalui seluruh proses DMAIC dengan pelanggan utama dan menjelaskan bagaimana akar penyebab ditentukan, serta rencana untuk menerapkan tindakan korektif. Sennett menambahkan bahwa banyak pelanggan Clipper sudah familiar dengan alat Six Sigma, sehingga proses RCA adalah jenis pemecahan masalah yang mereka ingin lihat.
“Proses ini membantu kepuasan pelanggan karena (pelanggan) tahu bahwa kami meluangkan waktu untuk menemukan akar masalah dan menggunakan orang yang terlatih untuk melakukan [tindakan korektif] dengan cara yang benar pertama kali,” kata Sennett.
Pelanggan eksternal bukan satu-satunya yang mendapat manfaat dari proyek RCA ini. Karyawan di pusat pengiriman pemantauan jarak jauh Clipper, yang mengontrol turbin dari fasilitas Cedar Rapids, Iowa, mengalami penurunan beban kerja karena lebih sedikit turbin yang memerlukan perhatian selama cuaca buruk.
Sennett percaya bahwa proyek RCA ini dan proyek lainnya yang mengikutinya membantu karyawan Clipper berpikir lebih proaktif dan mengatasi masalah sebelum menjadi masalah di seluruh armada.
“Tujuan kami adalah menjadi lebih preventif dan melihat berbagai hal sebelum mulai gagal, dan dengan proses Six Sigma Anda dapat melakukan pekerjaan yang lebih baik dalam merancang cacat di awal sebelum implementasi,” kata Sennett.
Membangun Budaya Kualitas
Baik Trueg maupun Sennett memuji proyek RCA ini karena membuka mata mereka terhadap isu-isu utama seperti pengujian internal dan memperluas basis pemasok perusahaan. Sebagai hasil dari proyek peningkatan ini, Clipper membuat rencana untuk memperkenalkan pemasok baru untuk menghindari potensi masalah yang disebabkan oleh sumber tunggal.
“Kami juga telah mengembangkan pengujian di sini di lokasi produksi, jadi jika kami memiliki masalah kualitas, kami dapat menguji sebelum mengirim sesuatu ke lapangan yang berpotensi menyebabkan kegagalan atau memerlukan suku cadang pengganti,” kata Trueg.
Sennett mengatakan bahwa sementara beberapa anggota tim awalnya skeptis tentang proses DMAIC, mereka dengan cepat belajar pentingnya meluangkan waktu untuk setiap langkah, menyadari bahwa tanpa proses terstruktur, orang cenderung mengumpulkan data yang tidak perlu yang tidak terkait dengan masalah tersebut. Untuk beberapa anggota tim, mengerjakan proyek ini memicu minat untuk mempelajari lebih lanjut tentang peningkatan proses dan mendorong mereka untuk meminta pelatihan lebih lanjut dan kesempatan untuk mendapatkan sertifikasi sabuk hijau Six Sigma.
Trueg kagum dengan perubahan staf Clipper setelah mereka bertugas di tim RCA:“Sikap dan fokus pada pemecahan masalah dengan data adalah bagian kuat dari budaya Clipper.”
Untuk informasi lebih lanjut:
- Sennett dan Trueg merekomendasikan buku-buku berikut untuk memandu aktivitas peningkatan proses Anda:The Lean Six Sigma Pocket Toolbook oleh Michael L. George, David Rowlands, Mark Price dan John Maxey, dan Statistics for the Utterly Confused oleh Lloyd Jaisingh.
- Kunjungi Pusat Pengetahuan di www.asq.org/knowledgecenter untuk menemukan sumber daya tambahan tentang analisis akar penyebab dan Six Sigma.
Tentang penulis
Janet Jacobsen adalah seorang penulis lepas yang mengkhususkan diri dalam topik kualitas dan kepatuhan. Lulusan Universitas Drake, dia tinggal di Cedar Rapids, Iowa. Artikel ini disediakan oleh American Society for Quality (ASQ, www.asq.org).