Hari-hari pencetakan 3D hanya sebagai alat prototipe cepat untuk industri otomotif telah berakhir. Kemajuan dalam manufaktur aditif (AM) berarti bahwa, saat ini, pembuat mobil semakin mengintegrasikan pencetakan 3D ke dalam lini produksi mereka.
Faktanya, 94 persen pemangku kepentingan otomotif berencana untuk memperluas kemampuan pencetakan 3D mereka, kata survei Jabil yang dilakukan pada tahun 2018.
Dalam artikel ini, kita akan menyelami manfaat yang ditawarkan pencetakan 3D kepada pembuat mobil dan mengeksplorasi bagaimana teknologi tersebut diintegrasikan ke dalam proses produksi otomotif saat ini. Selain itu, kita akan melihat tantangan saat ini dalam mengadopsi pencetakan 3D untuk suku cadang mobil penggunaan akhir, serta apa yang akan terjadi di masa depan untuk pencetakan 3D di sektor otomotif.
Manfaat pencetakan 3D untuk industri otomotif
1. Inovasi desain
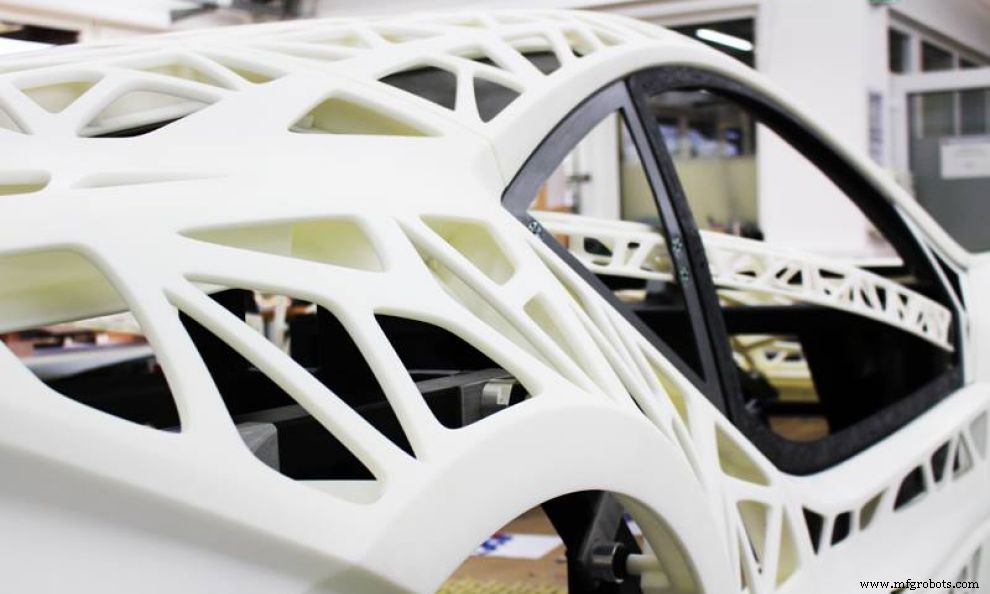
Pencetakan 3D dapat digunakan untuk membuat desain rumit dan rumit yang tidak mungkin dilakukan dengan metode manufaktur tradisional. Kemampuan ini sangat bermanfaat saat membuat bagian fungsional yang disesuaikan.
Karena pengurangan berat adalah area utama yang menjadi perhatian OEM otomotif – kendaraan yang lebih ringan biasanya memiliki konsumsi bahan bakar yang lebih rendah – insinyur desain juga dapat mengambil manfaat dari menggabungkan pencetakan 3D dengan alat seperti pengoptimalan topologi dan desain generatif. Ini dapat digunakan untuk menghilangkan material di area tertentu dan membuat suku cadang dengan bobot dan kinerja yang dioptimalkan.
2. Perakitan yang disederhanakan
Konsolidasi bagian adalah cara lain di mana OEM otomotif bisa mendapatkan keuntungan dari pencetakan 3D. Karena metode manufaktur tradisional tidak memiliki kebebasan desain pencetakan 3D, beberapa komponen biasanya harus diproduksi untuk membuat komponen akhir.
Dengan konsolidasi bagian, beberapa bagian dari suatu komponen dapat diintegrasikan ke dalam satu komponen pada tahap desain. Karena kerumitannya, desain gabungan seringkali hanya dapat diproduksi dengan bantuan pencetakan 3D.
Dengan pendekatan ini, pencetakan 3D dapat menyederhanakan proses perakitan dengan mengurangi jumlah komponen yang dibutuhkan pada tahap perakitan. Mengatasi kebutuhan akan banyak suku cadang membantu mengurangi penggunaan material dan waktu atau biaya perakitan.
3. Penyesuaian
Dengan manufaktur yang semakin condong ke arah kustomisasi massal, OEM otomotif harus semakin menemukan cara untuk membuat kendaraan yang disesuaikan dengan kebutuhan pelanggan mereka. Pencetakan 3D menawarkan cara yang hemat biaya dan fleksibel untuk menghasilkan suku cadang yang disesuaikan.
Dalam segmen industri mewah dan olahraga motor, perusahaan telah menggunakan teknologi untuk memproduksi suku cadang yang dipersonalisasi untuk bagian interior dan eksterior kendaraan.
Menawarkan opsi penyesuaian kepada pelanggan adalah salah satu cara pembuat mobil bertujuan untuk meningkatkan pengalaman pelanggan dan meningkatkan keunggulan kompetitif mereka.
Salah satu segmen industri otomotif yang telah mengadopsi pencetakan 3D untuk kustomisasi, adalah segmen kendaraan mewah. Di segmen di mana produksi kecil berjalan adalah norma, pencetakan 3D dapat digunakan untuk membuat suku cadang, yang disesuaikan dengan kebutuhan pelanggan tertentu, dalam jangka waktu yang relatif singkat.
Mini adalah contoh yang baik:pembuat mobil Jerman-Inggris beralih ke pencetakan 3D untuk memungkinkan pelanggan memesan suku cadang yang disesuaikan, seperti komponen trim dan gagang pintu.
Porsche 3D mencetak kursi khusus
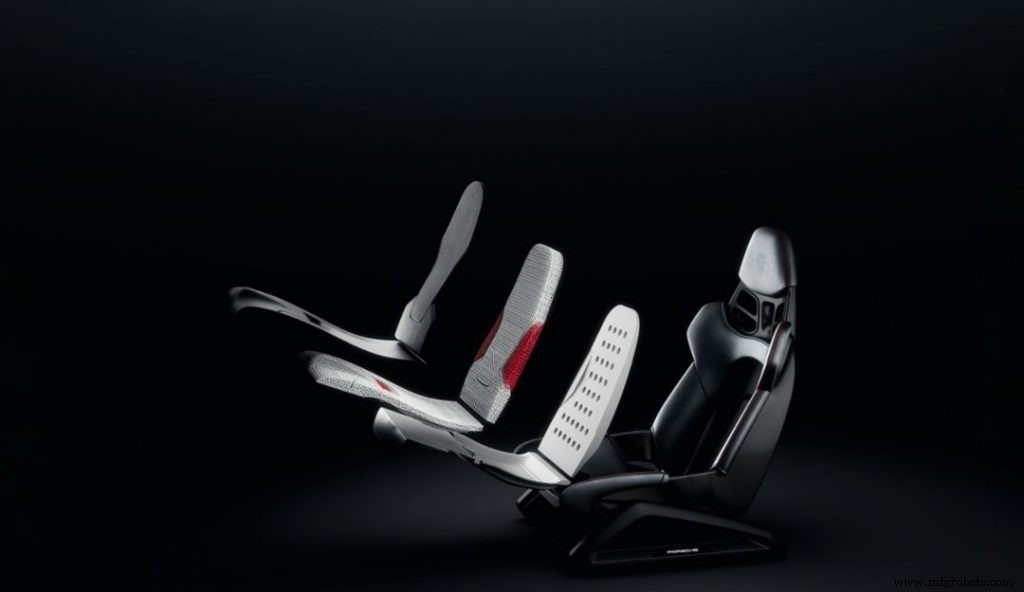
Dalam contoh lain, Porsche telah memperkenalkan konsep baru untuk jok mobil sport yang memanfaatkan pencetakan 3D untuk penyesuaian.
Kursi baru ini memiliki bagian kursi tengah yang dicetak dengan poliuretan 3D dan bantalan sandaran, yang dapat disesuaikan dengan tiga tingkat kekencangan:keras, sedang, dan lembut.
Porsche berencana untuk mencetak 40 kursi prototipe 3D untuk digunakan di trek balap Eropa, paling cepat Mei 2020, dengan umpan balik pelanggan digunakan untuk mengembangkan model legal jalanan akhir untuk pertengahan 2021.
Pada akhirnya, Porsche ingin memperluas kustomisasi kursi di luar ketegasan dan warna, dengan mempersonalisasi kursi sesuai kontur tubuh khusus pelanggan.
Pencetakan memiliki potensi untuk mengubah tahap desain produk, dengan pelanggan memiliki pendapat yang lebih besar tentang tampilan kendaraan mereka.
Material pencetakan 3D untuk aplikasi otomotif
Banyak aplikasi otomotif membutuhkan bahan yang menggabungkan ketangguhan dan keuletan dengan panas dan ketahanan kimia. Pencetakan 3D dengan polimer berkekuatan tinggi (nilon, MENGINTIP), plastik (ABS, ASA) dan logam (aluminium, paduan baja, titanium), oleh karena itu merupakan pilihan paling umum untuk memproduksi komponen dan perkakas mobil yang fungsional.
Sekarang, ada juga kemungkinan pencetakan 3D dengan komposit serat karbon, yang membuka pintu lain untuk membuat komponen mobil yang lebih ringan.
Mengintegrasikan pencetakan 3D ke dalam proses produksi otomotif
Pengembangan dan validasi produk
Dengan kemungkinan menghasilkan beberapa iterasi desain dalam waktu yang lebih singkat (dan dengan sedikit biaya tambahan), pencetakan 3D adalah alat yang efektif untuk pengembangan produk. Biasanya, bagian harus melalui beberapa siklus desain sebelum desain akhir disepakati.
Dengan pencetakan 3D, tahap ini dapat dipercepat secara dramatis. Selain itu, perbaikan desain yang hemat biaya dapat dilakukan dengan relatif cepat karena teknologinya tidak memerlukan peralatan yang mahal untuk menghasilkan prototipe.
Menggunakan pencetakan 3D untuk pembuatan prototipe, pengujian, dan validasi kinerja saat ini merupakan salah satu aplikasi teknologi yang paling populer dalam industri otomotif.
Biaya produksi yang rendah, dimungkinkan oleh pencetakan 3D, berarti bahwa insinyur desain dapat memeriksa kecocokan dan fungsi komponen terlebih dahulu sebelum berinvestasi dalam cetakan yang mahal dan biasanya padat karya untuk produksi bagian akhir.
Verifikasi desain dengan pencetakan 3D di Audi
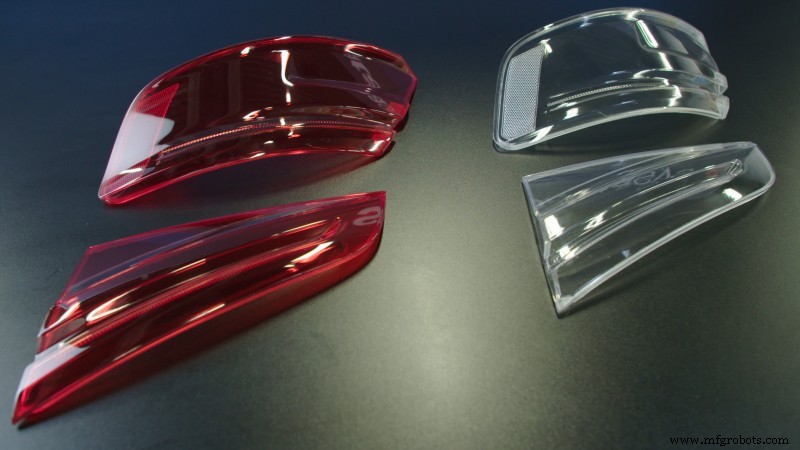
Sebelum kendaraan baru masuk ke produksi, Audi Pre-Series Center di Ingolstadt, membangun model fisik dan prototipe untuk merek tersebut, untuk dapat mengevaluasi desain dan konsep baru.
Penggunaan pencetakan 3D polimer telah menjadi bagian integral dari proses desain otomotif di Audi Pre-Series Center, memungkinkan tim mengatasi keterbatasan proses konvensional dan mempercepat verifikasi desain.
Ambil penutup lampu belakang, misalnya. Secara tradisional, prototipe bagian-bagian ini diproduksi menggunakan penggilingan atau pencetakan. Tantangan utama dengan teknik produksi ini adalah bahwa penutup multi-warna dari rumah lampu belakang harus diproduksi secara terpisah dan kemudian dirakit. Hal ini meningkatkan waktu tunggu untuk verifikasi desain dan selanjutnya menunda waktu pemasaran.
Menggunakan teknologi pencetakan 3D multi-warna dari Stratasys, memungkinkan tim untuk membuat penutup lampu belakang multi-warna yang sepenuhnya transparan dalam satu cetakan, menghilangkan kebutuhan untuk apa yang sebelumnya merupakan proses multi-langkah.
Untuk memproduksi penutup lampu belakang, Audi berharap dapat mengurangi waktu pembuatan prototipe hingga 50 persen, berkat pencetakan 3D.
Perkakas
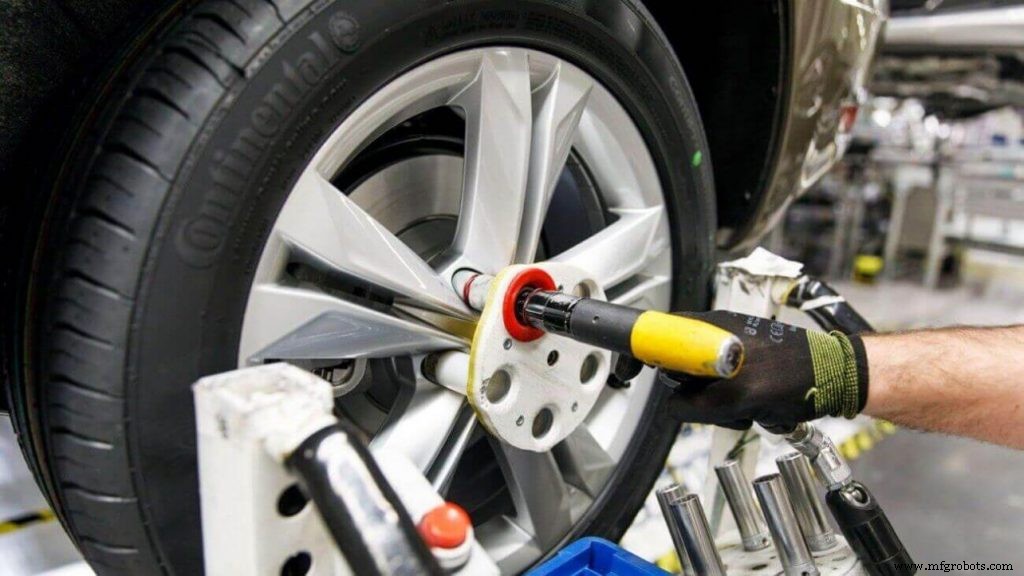
Meskipun pembuatan prototipe tetap menjadi aplikasi utama pencetakan 3D dalam industri otomotif, penggunaan teknologi untuk perkakas sedang berkembang pesat.
Pabrik perakitan Volkswagen Europa sudah menggunakan AM untuk memproduksi peralatan perkakas sendiri, daripada mengambilnya dari penyedia pihak ketiga.
Perusahaan mulai menggunakan pencetakan 3D untuk perkakas pada tahun 2014, untuk proyek percontohan. Keberhasilan pilot meyakinkan Volkswagen untuk mengalihkan sebagian besar produksi perkakasnya ke pencetakan 3D.
Menggunakan teknologi untuk aplikasi ini membawa banyak keuntungan.
Memproduksi perkakasnya secara internal mengurangi biaya produksi perkakas untuk pabrikan mobil hingga 90 persen – dan memangkas waktu tunggu dari berminggu-minggu menjadi hanya beberapa hari. Sebagai contoh, alat seperti lencana liftgate dilaporkan membutuhkan waktu 35 hari untuk dikembangkan menggunakan manufaktur tradisional dan menelan biaya hingga €400. Dengan pencetakan 3D, alat yang sama dapat diproduksi dalam empat hari dengan biaya hanya €10.
Menggunakan pencetakan 3D untuk perkakas dikatakan telah menghemat hampir €325.000 Volkswagen pada tahun 2017, sekaligus meningkatkan ergonomi, produktivitas, dan kepuasan operator.
Ketika datang ke alat bantu manufaktur, pencetakan 3D berkembang pesat sebagai alternatif cara alat manufaktur yang lebih mapan. Dalam beberapa tahun, kita mungkin akan melihat lebih banyak OEM otomotif beralih ke perkakas cetak 3D untuk meningkatkan efisiensi produksi dan kinerja perkakas mereka.
Suku cadang
Pembuat mobil dapat memanfaatkan manfaat pencetakan 3D untuk membuat suku cadang sesuai permintaan.
Dengan biaya inventaris yang tinggi terkait dengan penyimpanan suku cadang (dan sering kali jarang dipesan), pencetakan 3D menyediakan sarana hemat biaya untuk memproduksi suku cadang yang dibutuhkan tepat waktu dan sesuai permintaan, sehingga meningkatkan waktu pengiriman, mengurangi biaya inventaris, dan rantai pasokan yang disederhanakan.
Daimler Bus mencari suku cadang cetak 3D
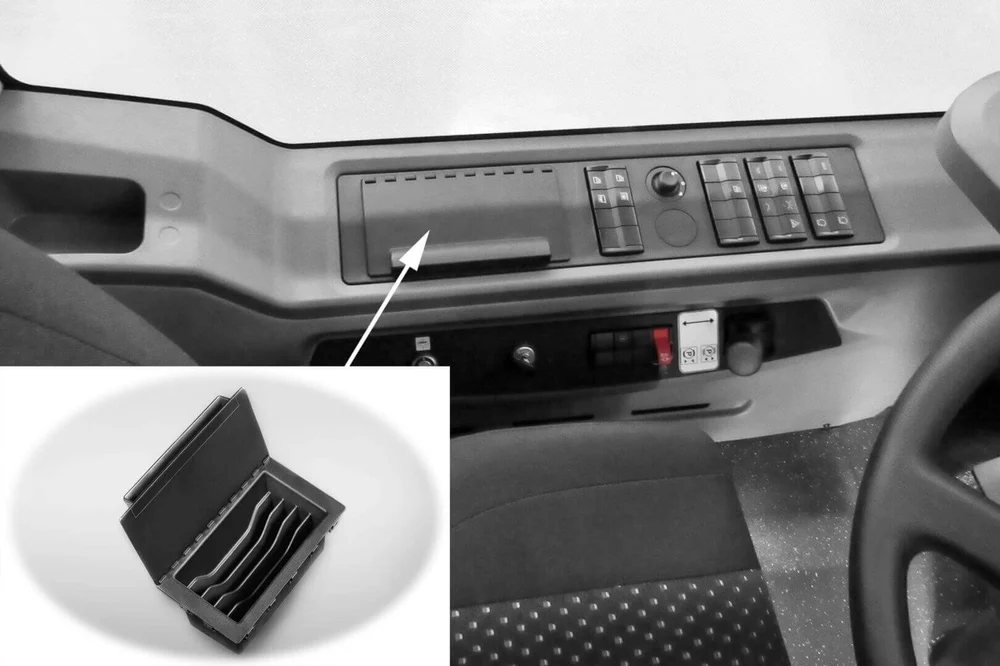
Pada awal tahun 2020, Daimler Buses mengumumkan rencananya untuk mengembangkan model bisnis baru:secara langsung memproduksi suku cadang sendiri untuk pelanggan melalui pencetakan 3D.
Saat ini Pusat Kompetensi Bus Daimler untuk pencetakan 3D sedang memeriksa lebih dari 300.000 suku cadang bus secara rinci untuk pencetakan tersebut. Sekitar 200 sejauh ini telah diidentifikasi sebagai yang cocok, seperti penutup, pegangan, dan beragam braket.
Salah satu pendorong utama beralih ke pencetakan 3D untuk suku cadang tersebut adalah kemampuan untuk mempercepat produksi dan pengiriman suku cadang. Bus Daimler menyatakan bahwa proses ini hanya memakan waktu beberapa hari dibandingkan dengan beberapa bulan.
Manfaat tambahan dari pencetakan 3D, yang dikutip oleh Daimler Buses, mencakup peningkatan efisiensi bahan:teknologi ini menghasilkan limbah yang jauh lebih sedikit dan bahan yang tidak terpakai dapat segera digunakan untuk pesanan pencetakan 3D berikutnya.
Produksi bagian akhir
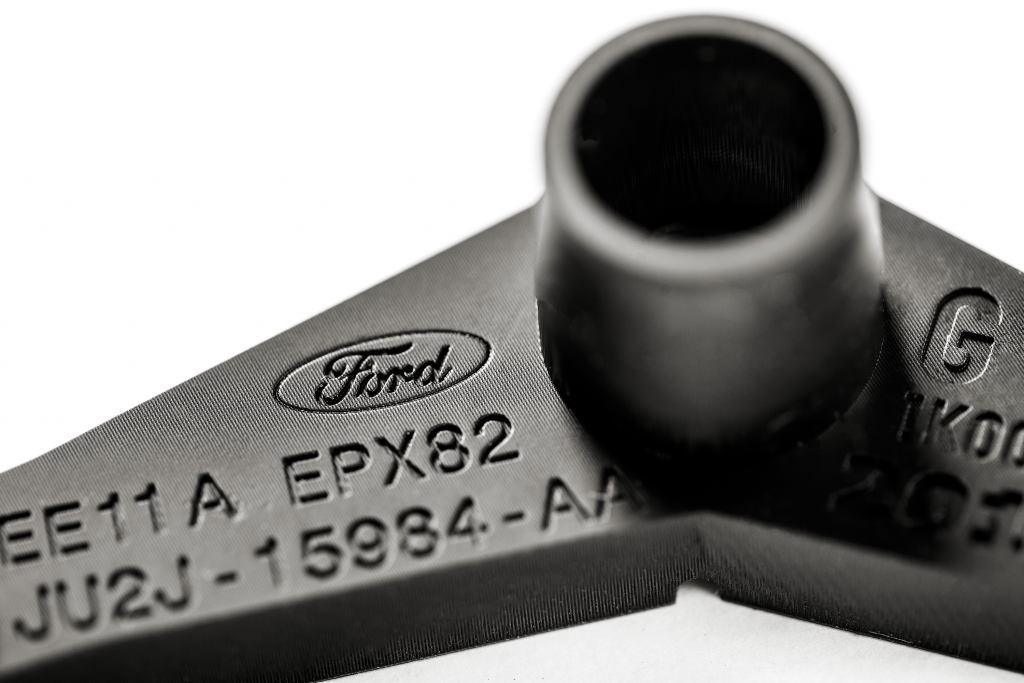
Kemajuan terbaru dalam teknologi dan bahan AM membuka kunci pencetakan 3D untuk menghasilkan suku cadang penggunaan akhir ukuran kecil dan menengah. Menurut survei OEM otomotif Jabil pada 2018, 40 persen membayangkan bahwa pencetakan 3D akan membantu produksi komponen mobil yang dapat digunakan kembali.
Suku cadang otomotif cetak 3D penggunaan akhir dapat berkisar dari komponen eksterior hingga suku cadang dalam, seperti bellow, saluran kompleks, braket pemasangan, dan komponen mesin.
Salah satu contohnya adalah Ford:tahun lalu, perusahaan mengumumkan dimulainya produksi pencetakan 3D untuk komponen struktural.
Suku cadang yang dimaksud termasuk Suku Cadang Servis Lengan Tuas Ford Focus HVAC (Pemanasan, Ventilasi, dan Pendinginan), Konektor Bantu Ford F-150 Raptor, dan Braket Rem Parkir Listrik Ford Mustang GT500.
Komponen ini diproduksi menggunakan teknologi pencetakan 3D Carbon Digital Light Synthesis (DLS) dan material EPX (epoxy) 82 dan telah melewati semua standar dan persyaratan kinerja Ford.
Pencetakan 3D dalam olahraga motor
Penggunaan AM sebagai keunggulan kompetitif untuk pengembangan mobil balap adalah praktik standar saat ini.
Dalam olahraga motor, pencetakan 3D telah menjadi alat yang sangat diperlukan untuk memproduksi suku cadang yang tahan lama dan akurat untuk pengujian terowongan angin. Keuntungan lainnya adalah kecepatan:jika perubahan desain diperlukan, AM mempermudah produksi komponen yang dapat diuji di terowongan angin, jauh lebih cepat.
Banyak tim mobil balap juga mengeksplorasi pencetakan 3D dalam produksi komponen mobil penggunaan akhir. Misalnya, tim 3D Alfa Romeo Sauber F1 mencetak ring roll logam – struktur keselamatan penting yang melindungi pengemudi jika terguling.
Khususnya, bagian ini terbuat dari Scalmalloy, logam ringan yang dikembangkan khusus untuk AM. Dengan menggabungkan bahan ini dengan teknologi Selective Laser Melting (SLM), Sauber F1 dapat menghasilkan roll hoop yang jauh lebih ringan dengan fitur internal yang kompleks untuk integritas struktural. Itu juga telah mampu mengurangi waktu tunggu produksi sekitar 25 persen.
Tantangan pencetakan 3D di industri otomotif
Produksi massal
Sementara OEM otomotif semakin menggabungkan sistem AM ke dalam pengembangan dan produksi, satu tantangan untuk adopsi yang lebih luas adalah volume produksi. Dengan lebih dari 92 juta mobil yang diproduksi pada tahun 2019 saja, industri otomotif sangat bergantung pada produksi seri massal.
Pada tahap saat ini, pencetakan 3D tidak dapat menghasilkan suku cadang dengan volume dan kecepatan yang dibutuhkan oleh industri otomotif. Oleh karena itu, teknologi tidak boleh menjadi pengganti metode manufaktur tradisional, yang sangat cocok untuk volume massal, tetapi sebagai alat pelengkap untuk volume yang lebih rendah, produksi yang disesuaikan.
Meskipun demikian, produsen perangkat keras pencetakan 3D sedang mengembangkan metode produksi volume tinggi untuk memenuhi persyaratan industri otomotif. Salah satunya adalah metal binder jetting yang dikembangkan oleh HP, Desktop Metal, ExOne dan juga GE Additive.
Selain logam, printer 3D pengikat binder dapat menggunakan bahan bubuk, seperti plastik, pasir dan keramik, dan bahan pengikat, untuk dengan cepat membuat bagian lapis demi lapis, menggunakan data dari file desain digital.
Tidak seperti printer 3D yang menggunakan laser atau berkas elektron dan membuat satu atau dua bagian sekaligus, mesin binder jetting, misalnya, dapat membuat lusinan braket sekaligus, karena area pencetakan jauh lebih besar dan lapisannya lebih tipis. dibangun jauh lebih cepat.
Namun, pengaliran pengikat logam hanya dalam tahap awal adopsi di industri otomotif. Menurut Matthias Schmidt-Lehr, mitra pengelola di firma konsultan Ampower GmbH &Co, teknologi binder jetting membutuhkan waktu antara lima dan sepuluh tahun untuk dapat memproduksi suku cadang dengan volume otomotif.
Ukuran bangunan
Tantangan lain yang dihadapi oleh pembuat mobil adalah ukuran build yang terbatas dari banyak sistem AM. Meskipun bagian yang lebih besar dapat diproduksi dengan teknologi pencetakan 3D, ini harus dilakukan dalam bentuk bagian modular. Ini, pada gilirannya, saat ini harus dirakit atau dilampirkan melalui proses lain, seperti pengelasan.
Namun, manufaktur aditif skala besar adalah area penelitian yang penting dan berkembang, dengan teknologi yang dapat mendukung ukuran build yang lebih besar, seperti Wire Arc Additive Manufacturing (WAAM) dan Big Area Additive Manufacturing (BAAM), yang secara aktif diteliti dan dikembangkan.
Kesenjangan keterampilan AM
Investasi tambahan dalam mengembangkan keterampilan khusus AM juga harus ditangani jika teknologi ingin berkembang lebih luas. Desain untuk AM, serta pengoperasian dan pemeliharaan sistem AM, bahan dan pasca-pemrosesan, adalah semua keterampilan penting yang harus dikembangkan dan dipelihara.
Sementara banyak yang telah dikatakan tentang kesenjangan keterampilan saat ini untuk AM, kemitraan dengan universitas dan program pelatihan internal adalah salah satu cara untuk memastikan kumpulan bakat yang terampil, mampu bekerja dengan kekhasan teknologi AM.
Pencetakan 3D dalam otomotif:jalan di depan
Seiring pembuat mobil terus menemukan aplikasi baru untuk pencetakan 3D, satu hal yang jelas:penggunaan pencetakan 3D untuk produksi bagian akhir semakin menarik. Laporan terbaru dari SmarTech Analysis, firma riset pencetakan 3D, mendukung tren ini dengan menyatakan bahwa penggunaan AM untuk produksi otomotif akan menjadi bisnis senilai $10 miliar pada tahun 2030.
Dalam konteks ini, industri otomotif kemungkinan akan menyaksikan lebih banyak lagi komponen fungsional cetak 3D, seperti braket, rangka, dan bahkan suku cadang mesin.
Dan mungkin visi masa depan yang lebih jauh, prospek pencetakan 3D seluruh mobil mungkin tidak terlalu mengada-ada.
Produsen mobil AS, Local Motors, telah menguji pesawat ulang-alik listrik otonom yang dicetak 3D, yang disebut Ollie, yang dirancang untuk transportasi lokal berkecepatan rendah.
Sebagian besar komponen Ollie telah dicetak 3D, termasuk atap dan bodi bawah kendaraan.
Meskipun perlu waktu untuk melihat kendaraan yang sepenuhnya dicetak 3D di jalan, proyek seperti Ollie Motor Lokal dapat membawa kita selangkah lebih dekat ke kemungkinan yang menarik itu.