Keandalan Berbasis Operator:Siapa Pemilik Peralatan Pabrik Anda?
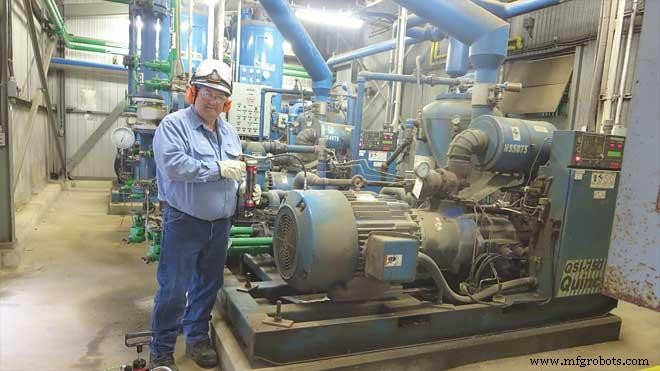
Industri kertas saat ini jauh berbeda dengan industri yang kita kenal lima tahun lalu. Meningkatnya persaingan asing dan ekonomi domestik yang melambat telah memicu konsolidasi industri kertas AS.
Penutupan fasilitas dan PHK karyawan telah menjadi hal yang biasa dan memberi makan mentalitas “hanya yang kuat yang bertahan”, yang telah memaksa pabrik untuk mencari segala cara untuk tetap kompetitif dan layak secara ekonomi. Karena kami tidak dapat mengendalikan harga pasar atau biaya bahan baku di tingkat pabrik, kami terpaksa mencari cara untuk meningkatkan laba kami.
Dengan mempersempit fokus kami ke variabel-variabel yang berada dalam kendali kami, sebagian besar pabrik telah menemukan bahwa peningkatan keandalan adalah area utama peningkatan biaya dan produktivitas. Selama bertahun-tahun, upaya kami untuk menurunkan biaya produksi melalui teknologi telah secara drastis mengubah peran operator di pabrik kami. Suatu kali seorang operator menghabiskan sebagian besar waktunya “di lantai”.
Ini memberikan pengetahuan langsung tentang cara kerja peralatan dan tanda-tanda mulai rusak. Di dunia sekarang ini, sebagian besar operator menjalankan pabrik melalui sistem yang dikendalikan komputer. Meskipun strategi ini berhasil menurunkan biaya produksi dan, dalam beberapa kasus, meningkatkan kualitas produk, strategi ini tidak termasuk strategi keandalan peralatan. Dalam kebanyakan kasus, ini adalah tanggung jawab yang jatuh kembali ke departemen pemeliharaan pabrik.
Sementara kelompok ini memenuhi syarat untuk mengisi tugas, apakah mereka orang yang tepat untuk memegang tanggung jawab untuk mengidentifikasi potensi kegagalan? Apakah mekanik mobil Anda bertanggung jawab untuk mengidentifikasi potensi kegagalan pada mobil Anda?
Di International Paper, kami mengakui keandalan sebagai potensi besar untuk penghematan biaya. Sebagai sebuah perusahaan, kami memutuskan untuk fokus pada pemulihan pendekatan langsung ke keandalan melalui proyek yang disebut Advantage. Dalam proyek ini, kami berfokus pada keandalan, perencanaan dan penjadwalan yang digerakkan oleh operator, analisis akar penyebab kegagalan, dan pemasangan peralatan pemeliharaan yang presisi.
Meskipun sistem tidak seefektif yang seharusnya, perencanaan dan penjadwalan, analisis kegagalan akar penyebab, dan teknik pemeliharaan presisi sudah ada di Pabrik Augusta. Perencanaan dan penjadwalan secara longgar di tempat sebagai harapan tentang bagaimana pekerjaan harus diselesaikan dan program analisis akar penyebab kegagalan kertas memang ada di seluruh pabrik.
Analisis getaran, termografi inframerah, akustik, dan program pemeliharaan preventif kami semuanya menggunakan alat analisis untuk mengidentifikasi masalah dan memfokuskan upaya pemeliharaan kami sebelum terjadi kegagalan besar. Keandalan yang digerakkan oleh operator, di sisi lain, belum ada sejak zaman operator langsung.
Kami memang memiliki “putaran proses” yang mengharuskan operator untuk melihat pengukur dan pengukur untuk mengoptimalkan parameter proses, tetapi tidak ada pemeriksaan keandalan formal yang disertakan dalam sistem itu. Sepertinya hari-hari seorang operator memeriksa bantalan dengan gagang sapu dan menangkapnya sehari sebelum menutup kami sudah lama berlalu.
Hal ini membawa kami pada pemahaman bahwa satu-satunya cara kami dapat mempertahankan posisi kompetitif kami di pasar adalah dengan memiliki operator yang tidak hanya menjalankan peralatan kami, tetapi SENDIRI. Sama seperti kita semua harus bertanggung jawab untuk menjaga agar mobil kita tetap berjalan, operator juga harus bertanggung jawab untuk menjaga agar peralatan proses tetap berjalan di area mereka.
Setelah organisasi Anda melihat bahwa bola lampu menyala, bagian tersulit dari memulai program keandalan yang digerakkan oleh operator seperti ini ada di belakang Anda. Dengan sumber daya khusus dan jangka waktu yang ditentukan dengan baik, program ini dapat memberikan hasil finansial yang kita semua cari.
Perencanaan strategis
Jadi, sekarang setelah kami memutuskan untuk mengembangkan program keandalan yang digerakkan oleh operator ini, apa yang pertama kali kami lakukan? Komponen paling penting dari program keandalan yang digerakkan oleh operator yang sukses adalah dukungan manajemen. Tanpa dukungan dari tingkat tertinggi organisasi, program tidak akan pernah menerima waktu, uang, dan dukungan yang diperlukan untuk melihat hasil yang positif.
Langkah pertama dalam menerapkan program keandalan yang digerakkan oleh operator adalah pengembangan pernyataan misi dan tujuan keandalan yang digerakkan oleh operator di pabrik. Dikembangkan oleh tim pimpinan pabrik, ini harus mencakup metrik program, pencapaian, anggaran, serta peran dan tanggung jawab di seluruh pabrik.
Selanjutnya, tim pimpinan harus memilih seorang juara untuk mengawal pelaksanaan program. Orang yang dipilih harus menjadi individu yang dihormati dari posisi yang sangat terlihat. Mereka akan diminta untuk memiliki kepemimpinan yang kuat dan keterampilan fasilitator tim karena mereka akan mengelola sebagian besar melalui pengaruh.
Orang ini harus segera dipilih dan dipromosikan di dalam pabrik sebagai orang yang bertanggung jawab untuk mengimplementasikan program. Ini akan memudahkan mereka untuk mengarungi perairan politik khusus wilayah. Tim kepemimpinan harus memastikan bahwa sang juara menyadari peran yang diminta untuk diisi dan batasan yang harus dilaluinya dalam keberhasilan pelaksanaan program.
Sebagai aturan praktis, orang ini bertanggung jawab untuk mengidentifikasi dan memperbaiki hambatan pabrik, memberi tahu tim pimpinan pabrik tentang kemajuan, memilih tim pabrik untuk mengimplementasikan program, dan menjaga visibilitas dan harapan untuk program tersebut.
Selanjutnya, juara keandalan yang digerakkan oleh operator perlu mengidentifikasi area operasi utama pabrik dan memilih anggota tim untuk mewakili setiap area dalam tim keandalan yang digerakkan oleh operator pabrik. Di Augusta , kami mengidentifikasi enam area operasi kritis – woodyard, pabrik pulp, pembangkit tenaga listrik, pabrik kertas, finishing dan pengiriman, serta air dan limbah, dan memilih anggota tim untuk masing-masing.
Anggota tim bertanggung jawab untuk mengidentifikasi peralatan yang akan ditempatkan pada rute operator, mengembangkan urutan berjalan dari rute dan kemudian mengatur frekuensi inspeksi. Mereka juga bertanggung jawab atas metrik area, rencana komunikasi area, mengidentifikasi kebutuhan alat analitik, dan rencana pengenalan departemen. Seperti juara program, anggota tim harus dihormati di wilayahnya, memiliki motivasi diri, dan memiliki kemampuan untuk mengerjakan banyak tugas sekaligus.
Anggota terakhir dari tim pengembangan harus merupakan kelompok tambahan yang terdiri dari karyawan bergaji atau karyawan per jam yang dipilih untuk mengembangkan rute. Di Augusta , kami menggunakan dua strategi berbeda untuk pengembangan rute. Kami memulai peluncuran dengan berfokus pada woodyard kami.
Untuk fase ini, kami memilih dua karyawan operasi per jam untuk pengembangan rute. Kami merasa mereka akan memiliki pengetahuan yang lebih baik tentang peralatan dan perspektif operator dan pada saat yang sama memberikan kredibilitas lebih untuk rute ke operator area yang tersisa. Meskipun ini telah terbukti menjadi cara yang berhasil untuk menerapkan rute woodyard, itu sangat memakan waktu. Karyawan per jam memiliki keinginan untuk membuat program ini berhasil, tetapi mereka tidak memiliki keterampilan komputer dan rasa yang kuat untuk memecahkan masalah.
Kami mengembangkan strategi baru untuk area selanjutnya. Kami mengambil empat insinyur yang baru direkrut dan mengatur mereka untuk menyelesaikan pengembangan pabrik lainnya. Ini ternyata memiliki dua manfaat utama. Mereka membantu kami mengembangkan rute dengan cepat dengan keterampilan komputer dan pelatihan pemecahan masalah, serta membantu mereka mempelajari area dan personel di dalam pabrik.
Kedua taktik bisa sangat efektif tetapi akan bervariasi dari pabrik ke pabrik berdasarkan personel. Ini adalah keputusan yang sangat baik untuk membiarkan tim proyek keluar. Mereka tidak hanya akan membawa pengetahuan dari semua personel area operasi ke keputusan, tetapi mereka juga akan membentuk kepemilikan yang kuat dalam proyek dengan diizinkan untuk menyuarakan pendapat mereka.
Alat analisis
Banyak program keandalan yang digerakkan oleh operator terhenti karena masalah alat analisis dan biaya serta pelatihan terkait. Ada banyak manfaat yang bisa didapat dengan menggunakan alat analisis yang stabil penuh. Anda dapat memberikan pembacaan yang lebih akurat, sarana pelaporan pengecualian yang lebih baik, tren data real-time di lapangan, meminimalkan kemampuan untuk "mencambuk pensil" rute, dan memberikan rasa kredibilitas pada program baru.
Meskipun semua ini “bagus untuk dimiliki”, mereka sama sekali bukan penghalang dalam hal penerapan program ODR dan dapat dengan mudah ditambahkan ke program saat program tersebut matang.
Meskipun demikian, ada berbagai peralatan yang tersedia untuk membantu menyempurnakan pengumpulan data Anda.
· Senjata suhu inframerah: Ini memberikan suhu yang tepat dengan peningkatan keamanan, karena memberikan pembacaan yang akurat kepada operator tanpa bersentuhan dengan peralatan yang berpotensi panas.
· Stroboskop: Ini digunakan untuk mencari kopling atau sabuk yang longgar, menemukan baut yang hilang atau cacat material pada peralatan berputar yang sedang digunakan. Mereka memang membutuhkan akses ke pasangan atau sabuk dengan memiliki pintu inspeksi pada pelindung atau pelindung logam yang diperluas.
· Pena getar: Ini memeriksa kondisi dan tingkat getaran bantalan tren. Mereka membutuhkan penggunaan titik dan sudut yang sama untuk pembacaan untuk memberikan tren yang akurat.
· Asisten digital pribadi (PDA): Ini adalah unit genggam untuk rute elektronik. Mereka menyediakan tren lapangan, pembacaan kode batang untuk memastikan pemeriksaan peralatan yang tepat selesai, kepatuhan rute elektronik dan perekaman pengecualian satu tombol. Kerugiannya termasuk biaya, pelatihan ekstensif yang diperlukan, dan kemungkinan alasan untuk rute yang tidak lengkap.
Pabrik Augusta telah menerapkan program keandalan yang digerakkan oleh operator hanya dengan senjata suhu dan rute kertas. Keputusan ini dibuat dengan risiko keselamatan yang terlibat dalam menyentuh peralatan panas potensial dan pengetahuan bahwa kami akan maju ke alat yang lebih analitis seiring program matang dan harga terus menurun.
Komunikasi
Seperti halnya program yang akan melibatkan sejumlah besar karyawan, komunikasi sangat penting untuk mempertahankan program sampai menjadi bagian dari budaya. Jika karyawan tidak menerima umpan balik yang konsisten tentang rute mereka, mereka akan menganggap bahwa rute tersebut adalah item dengan prioritas rendah dan akan segera memulai "mencambuk pensil" rute tersebut. Jika mereka terus tidak menerima umpan balik, mereka akhirnya akan berhenti menjalankannya sama sekali. Oleh karena itu, penting untuk memiliki rencana komunikasi dan pengakuan tertulis untuk pabrik.
Di Augusta , kami menemukan bahwa setiap departemen memiliki sarana komunikasi yang matang yang telah mereka gunakan untuk menyampaikan umpan balik dan informasi. Beberapa area menggunakan percakapan pribadi dengan mandor sementara yang lain menggunakan papan buletin dan pembaruan mingguan. Mengizinkan mereka membantu mengembangkan rencana dengan manajer komunikasi di pabrik meningkatkan kepemilikan mereka dalam program dan menunjukkan alternatif terbaik untuk setiap area.
Terlepas dari metode yang digunakan, rencana komunikasi keandalan yang digerakkan oleh operator harus mencakup:peran dan tanggung jawab departemen, waktu rute dan dokumen tindak lanjut, sistem umpan balik, harapan, pelatihan, dan bagaimana pengakuan akan ditangani di area tersebut.
Pengembangan rute
Daging dari program ini didasarkan pada pengembangan rute. Ada banyak filosofi berbeda dalam pengembangan rute, mulai dari hanya menyertakan peralatan penting hingga menyertakan semua peralatan dan semua yang ada di antaranya. Pada kenyataannya, para pemimpin keandalan yang digerakkan oleh operator area harus menentukan berapa banyak waktu yang dimiliki operator mereka untuk melihat kondisi peralatan dan mengembangkan rute mereka untuk memanfaatkan waktu itu sepenuhnya. Orang sering mengabaikan waktu yang dibutuhkan untuk berpindah dari satu peralatan ke peralatan berikutnya.
Ini sangat penting, terutama di daerah terpencil di mana waktu antar peralatan bisa lebih dari dua kali lipat waktu yang dihabiskan untuk menyelesaikan rute. Pada akhirnya, setiap rute harus diatur waktunya untuk memastikan operator dapat menyelesaikan rute yang ditugaskan sambil mempertahankan peran mereka saat ini. Anda juga harus menyadari waktu tambahan yang mungkin diperlukan untuk menggunakan alat analisis. Pada awalnya, penggunaan alat dapat menambah waktu secara signifikan, tetapi akan berkurang seiring dengan semakin akrabnya karyawan dengan peralatan dan alat tersebut.
Di Augusta , kami menetapkan 20 menit sebagai aturan praktis untuk panjang rute, meskipun panjangnya bervariasi menurut posisi di seluruh pabrik. Kami kemudian menggunakan anggota tim area untuk mengidentifikasi peralatan yang "benar" untuk disertakan dalam rute. Berdasarkan tenaga kerja pabrik saat ini, beberapa area hanya memeriksa peralatan kritis yang dapat menyebabkan waktu henti proses area, sementara area lainnya juga mencakup peralatan perbaikan berulang dan berbiaya tinggi.
Frekuensi rute merupakan faktor lain yang perlu dipertimbangkan dalam pengembangan. Idealnya, kami akan menggunakan periode pengembangan kegagalan dari semua kegagalan yang dapat kami deteksi dengan keandalan yang digerakkan oleh operator dan menyetel frekuensi inspeksi kami pada setengah interval waktu tersebut untuk memastikan kami menangkap kegagalan sebelum terjadi. Meskipun ini adalah tujuan yang bagus, sebagian besar tenaga kerja pabrik saat ini hanya akan memungkinkan kami untuk fokus pada apa yang paling mungkin terjadi dan kemudian menyesuaikan jika kami menemukan kewajiban yang tidak dapat diterima di masa mendatang.
Rute juga jauh lebih mudah untuk dikelola jika semua peralatan diperiksa pada saat yang sama, daripada frekuensi rute yang berbeda untuk beberapa peralatan dalam suatu area. Di Augusta , kami memutuskan untuk mengembangkan sejarah frekuensi melalui pengalaman. Rute dikembangkan untuk dijalankan setiap minggu, dan kami akan menggunakan program kegagalan akar penyebab untuk mengidentifikasi kapan inspeksi dihentikan dari rute yang harus diselesaikan.
Pelatihan
Ini adalah komponen lain yang banyak diabaikan saat memulai program keandalan yang digerakkan oleh operator. Terlalu sering, kita merasa operator sudah mengetahui peralatan mereka dan, selama pemeriksaan dilakukan di atas kertas, mereka tidak memerlukan pelatihan tambahan. Di Augusta , kami menemukan ini jauh dari kebenaran. Kami menemukan bahwa operator mengetahui peralatan dengan nama yang sama sekali berbeda dari apa yang diidentifikasi pada sistem manajemen pemeliharaan terkomputerisasi.
Hal ini membuat sangat sulit untuk mengidentifikasi dengan tepat perbaikan apa yang perlu dilakukan tanpa menelusuri rute dengan operator yang mengidentifikasinya. Dengan jadwal shift 12 jam Augusta, ini bisa berarti menunggu hampir sebulan untuk mendapatkan karyawan itu kembali pada hari-hari dalam seminggu. Kami juga menemukan bahwa hanya sedikit operator yang mengetahui cara kerja peralatan dan mengapa penting untuk melakukan pemeriksaan yang diminta untuk mereka selesaikan. Alasan dan cara pelatihan sangat penting agar operator memiliki kepemilikan atas program dan peralatan area mereka.
Dua kelompok berbeda harus dilatih agar berhasil menerapkan dan mempertahankan program keandalan yang digerakkan oleh operator – manajer dan operator. Manajer harus memahami tujuan program, bagaimana program itu diatur dan harapan mereka untuk membuat program berjalan. Operator perlu dilatih tentang:
- apa itu rute
- cara menggunakan alat analisis
- cara melakukan pemeriksaan dengan benar
- cara melengkapi dokumentasi yang memadai
- rencana komunikasi area
Untuk karyawan per jam kami, kami mengembangkan kursus empat jam di Augusta menggunakan standar pemantauan kondisi IDCON sebagai tulang punggung. Ini menyediakan:
- apa fungsi peralatan yang dirancang
- pemeriksaan apa yang harus dilakukan pada peralatan tertentu
- cara melakukan pemeriksaan
- mengapa pemeriksaan itu penting
Pelatihan ini juga mencakup perjalanan langsung dari suatu rute dan waktu sesudahnya untuk mengajukan pertanyaan dan mendiskusikan apa yang mereka alami.
Untuk manajer, kami melakukan sesi satu lawan satu dengan anggota tim area mereka. Ini termasuk peralatan rute, alur proses, rencana komunikasi dan pengenalan, serta peran dan tanggung jawab mereka sebagai manajer program.
Keberlanjutan
Program keandalan yang digerakkan oleh operator harus menjadi bagian dari budaya pabrik agar berkelanjutan. Ini harus menjadi cara termudah bagi operator untuk mengerjakan peralatan di areanya. Umpan balik yang konstan sangat penting untuk membantu mereka memahami pekerjaan apa yang sedang diselesaikan, kapan dan mengapa. Ini juga membantu memastikan bahwa rute tersebut adalah rute terbaik untuk area tersebut.
Pada akhirnya, sumber daya khusus di awal program akan dipindahkan dan program harus memiliki momentum yang cukup untuk membuat departemen memikul tanggung jawab untuk mempertahankan rute keandalan yang digerakkan oleh operator.
Kami menyertakan garis waktu untuk mengembangkan program keberlanjutan pabrik di Augusta dalam upaya untuk memastikan bahwa pekerjaan yang dilakukan oleh tim keandalan yang digerakkan oleh operator diambil dan diambil alih oleh area tersebut. Pengakuan adalah aspek penting dari keberlanjutan kami. Sertifikat hadiah $5 ke kafetaria untuk setiap karyawan ODR departemen bulan ini akan membantu menjaga visibilitas program dan memperkuat upaya area untuk menanamkan kepemilikan di operator. Di bawah $500 per tahun untuk dipertahankan, ini adalah program pengakuan yang menarik untuk memperkuat ODR.
Tata graha
Housekeeping adalah "pemblokiran dan penanganan" dunia keandalan peralatan. Tanpa peralatan yang bersih, suhu meningkat, kebocoran tidak terdeteksi dan kesalahan peralatan kecil menjadi kegagalan peralatan yang mahal. Untuk beberapa pabrik, ini bukan masalah. Mereka sudah memiliki harapan dan budaya tata graha.
Bagi yang lain, ini bisa menjadi penghalang jalan yang cukup besar yang berpotensi membuat sistem yang dikembangkan dengan baik pun gagal. Jika tata graha adalah masalah di pabrik Anda, jangan mengabaikannya. Ini harus didiskusikan dan sebuah rencana dirumuskan untuk bagaimana menangani masalah-masalah nyata. Sayangnya, housekeeping adalah masalah yang sangat emosional. Kita cenderung menuding orang lain atau mencari alasan mengapa hal itu “tidak bisa” dilakukan.
Di Augusta, kami mengenali tata graha sebagai masalah yang harus kami tangani. Kami mengintegrasikan housekeeping ke dalam pelatihan dan menekankan pentingnya menjaga kebersihan peralatan. Sikat kawat, kain lap, dan lampu senter disertakan dalam kit keandalan yang digerakkan oleh operator dalam upaya membantu rumah tangga menjadi bagian dari budaya pabrik. Beberapa area telah mengambil alih aspek ini dengan mengambil gambar digital dari masalah tata graha di area tersebut dan mendiskusikan serta membahasnya pada pertemuan kru mingguan.
Ini jelas merupakan masalah sebesar gajah:Anda harus memakannya satu per satu. Dalam pelatihan kami, kami memberi tahu mereka untuk meluangkan waktu untuk benar-benar membersihkan peralatan terakhir di rute mereka. Setelah peralatan itu dibersihkan, bersihkan peralatan kedua hingga terakhir pada putaran berikutnya, dan seterusnya. Dengan empat kru yang berbeda menjalankan rute, tidak perlu waktu lama untuk membuat mereka semua dalam kondisi yang layak.
Pelatih pabrik kami melakukan percobaan dan keluar serta membersihkan satu set motor dan pompa secara menyeluruh. Mereka mengatakan butuh sekitar setengah jam untuk menyelesaikannya. Sejauh ini, itu tetap relatif bersih selama empat bulan terakhir. Akan ada beberapa peralatan yang akan tercakup dalam stok secara teratur karena beberapa masalah lain (misalnya, lubang di saluran atau peti yang melindas). Ini harus ditulis pada rute mereka dalam upaya untuk membenarkan memperbaikinya. Tidak ada yang akan mendapatkan dukungan lebih cepat dari karyawan per jam Anda selain melihat keandalan yang digerakkan oleh operator memperbaiki sesuatu yang telah mengganggu mereka selama bertahun-tahun.
Kesimpulan
Tekanan pasar tidak menunjukkan tanda-tanda surut, dan kita harus menjelajahi semua jalan untuk menyediakan produk dengan kualitas terbaik dengan biaya terendah. Keandalan peralatan telah diidentifikasi sebagai komponen kunci dari persamaan biaya dan mudah untuk melihat bahwa keandalan yang digerakkan oleh operator harus menjadi bagian dari strategi keandalan pabrik. Tanpa kepemilikan peralatan pabrik Anda di tangan operator, Anda tidak dapat berharap dapat diandalkan. Menggunakan pendekatan terencana yang melibatkan semua karyawan pabrik, keandalan peralatan akan berdampak langsung dan positif pada keuntungan Anda.
Tentang penulis:
Chris Hykin adalah direktur keandalan berbasis operator untuk International Paper di Augusta, Ga.