cetakan CFRP pencetakan 3D untuk flaperon RTM, exoskeleton, dan lainnya
Kredit Foto:Ketua Komposit Karbon (LCC) TU Munich dan Komposit QPoint
Ketua Komposit Karbon (Lehrstuhl für Carbon Composites atau LCC) didirikan pada tahun 2009 di departemen Teknik Mesin di Technical University of Munich (TUM, Munich, Jerman) dengan dana dari SGL Carbon (Wiesbaden, Jerman). Misinya adalah melakukan R&D dalam material, proses, dan aplikasi yang diperkuat serat karbon (CFRP), termasuk proyek dalam simulasi dan pengujian. Sebuah "kursi" dalam sistem universitas Jerman adalah unit terkecil yang terdiri dari seorang profesor dan timnya. Tim LCC dipimpin oleh Prof. Dr. -Ing. Klaus Drechsler dan saat ini mempekerjakan 30 peneliti penuh waktu. Meskipun pendanaan SGL berakhir pada tahun 2016, LCC telah melanjutkan kepemimpinannya dalam R&D komposit, yang mencakup pembuatan cetakan untuk bagian bawah Multifungsi Fuselage Demonstrator (MFFD), lihat bilah samping di bawah, dan sekarang juga mencakup pencetakan/aditif 3D manufaktur.
Blog ini dimulai ketika CEAD (Delft, Belanda) memberi tahu saya bahwa LCC telah membeli salah satu sistem flexbot AM berbasis extruder untuk pencetakan 3D menggunakan lengan robot. Wawancara saya berikutnya dengan peneliti LCC Patrick Consul, bagaimanapun, mengungkapkan harta karun proyek, termasuk COMBO3D, dalam Clean Sky 2, untuk mencetak 3D cetakan RTM komposit termoplastik untuk produksi flaperon pesawat komposit termoset, dan EMOTION untuk memproduksi alat untuk mencetak bagian bawah dari komposit termoplastik Multifungsi Fuselage Demonstrator (MFFD) dari Clean Sky 2 serta alat parsial sekunder untuk menunjukkan bagaimana badan pesawat yang sama dapat diproduksi melalui konsolidasi langsung di tempat (di luar autoklaf). Saya menemukan seluruh diskusi tentang bagaimana TUM telah mencapai titik ini dan ke mana arahnya menjadi menarik.
MMFD setengah cetakan bawah
Lihat blog Februari 2020 saya:“Membuktikan pengelasan LM PAEK untuk Demonstrator Pesawat Multifungsi”. Bilah samping ini diambil dari makalah Februari 2020, “Pengembangan Demonstran Pesawat Multifungsi” oleh Bas Veldman, manajer program untuk MFFD di GKN Fokker (Hoogeveen, Belanda).
Cangkang bagian bawah MFFD terdiri dari kulit termoplastik, dikakukan dengan stringer, klip, dan bingkai yang dilas. Proses manufaktur yang akan didemonstrasikan terdiri dari tiga langkah utama:
- Pita prepreg untuk kulit besar demonstran diletakkan di atas meja datar yang dimiringkan oleh mesin AFP laser NLR yang ada.
- Layup diangkut secara robotik dengan cangkir hisap ke cetakan konsolidasi betina dan dimasukkan ke dalamnya tanpa pemanasan.
- Setelah mengantongi vakum, kulit dikonsolidasikan dalam autoklaf.
Menggunakan cetakan konsolidasi perempuan menawarkan permukaan (datar) yang jauh lebih sederhana daripada alat laki-laki sambil secara langsung mengendalikan kendala aerodinamis pada kualitas permukaan luar kulit.
Proyek MFFD juga membutuhkan out-of-autoclave proses yang akan diselidiki — dimulai secara paralel dengan demonstran pesawat multifungsi besar — dalam demonstran ukuran yang lebih kecil berikutnya. Secara khusus, komposit termoplastik in-situ manufaktur di mana konsolidasi dicapai selama lay-up, akan dipertimbangkan, karena dapat sepenuhnya menghilangkan langkah autoklaf, dan karenanya mengurangi pembuatan menjadi prosedur satu langkah.
Cetakan yang Ditingkatkan untuk Badan Termoplastik masuk dan keluar dari Konsolidasi Autoclave, atau EMOTION (https://cordis.europa.eu/project/id/864474), adalah proyek Clean Sky 2 untuk memproduksi perkakas cangkang bawah MFFD. “Kedengarannya sederhana,” kata Patrick Consul dari koordinator proyek, TU Munich, “tetapi sebenarnya cukup menantang karena perlu dipanaskan hingga 400 °C. Ini jauh di atas kisaran suhu di mana Invar36 tidak memiliki CTE [koefisien ekspansi termal] yang signifikan.” Invar umumnya digunakan untuk alat cetakan komposit karena ekspansinya yang rendah selama siklus penyembuhan suhu tinggi. Namun, CTE Invar meningkat seiring suhu. “Tantangannya,” kata Konsul, “adalah untuk mengontrol ekspansi termal selama pemanasan dan pendinginan untuk cetakan 8 meter kali 4 meter dan kulit badan pesawat selama penyembuhan.” 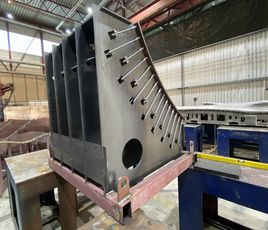
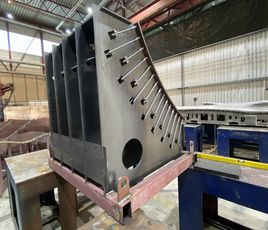
Kredit Foto:Ketua Komposit Karbon
Kemajuan dalam pembuatan aditif
“Kami adalah 8-9 orang yang bekerja pada manufaktur aditif di dalam LCC,” kata Konsul. Dia memulai sejarah pekerjaan ini dengan pembelian LCC atas mesin penempatan pita komposit termoplastik berbantuan laser dari AFPT (Dörth, Jerman) pada tahun 2012. Kemudian LCC menambahkan mesin Coriolis Composites (Quéven, Prancis) untuk memungkinkan penempatan serat otomatis (AFP ) dari prepreg termoset. Printer desktop berbasis filamen pertama dibeli pada tahun 2017. “Saya juga bergabung pada tahun 2017 untuk membantu mengembangkan aplikasi dan proyek penelitian baru, termasuk penulisan proposal, misalnya, untuk Clean Sky 2.” Dia menjelaskan bahwa proyek Clean Sky 2 diberikan berdasarkan proposal yang diajukan kepada manajer topik sebagai tanggapan atas Call for Proposals (CFP) yang dirilis secara publik. LCC berhasil dalam proposal untuk proyek COMBO3D CFP08 dan proyek EMOTION CFP09. Keduanya dibahas di bawah ini.
“Kami memiliki beberapa proyek lain, beberapa melihat pencetakan 3D dengan penguatan serat berkelanjutan,” kata Konsul. “Yang lain menggunakan kepala cetak terintegrasi laser untuk memanaskan substrat komposit untuk mencetak pada bagian CFRP yang sudah dikonsolidasikan atau untuk meningkatkan kekuatan geser interlaminar (ILSS) di antara lapisan yang dicetak. Proyek lain mengeksplorasi aplikasi perkakas, misalnya, di mana Anda memiliki sedikit suku cadang komposit khusus.”
“Proyek-proyek ini terus didukung oleh simulasi numerik untuk memprediksi perilaku aditif suku cadang yang diproduksi selama dan setelah proses pencetakan,” lanjutnya. “LCC juga terlibat dalam proyek dengan Imperial College of London yang bertujuan untuk memproduksi kerangka luar menggunakan CFRP cetak 3D. Proyek lain meneliti struktur kisi untuk mengoptimalkan sifat bagian cetakan 3D sehubungan dengan kekakuan, kekuatan, atau penyerapan energi.”
Progres di printer
”Kami memulainya dengan menggunakan printer 3D sederhana berbasis FDM (fused depositionmodeling) dari Apium (Karlsruhe, Jerman) untuk mencetak perlengkapan uji khusus yang membutuhkan kekakuan tinggi,” jelas Konsul. “Printer ini memiliki panjang 3 meter kali lebar 1 meter dengan output material yang tinggi untuk mengurangi waktu cetak. Meskipun tidak dapat menggunakan serat kontinu, namun dirancang dengan baik untuk pencetakan dengan MENGINTIP, PEKK, dan PEEK yang diperkuat serat karbon cincang. Ini tidak hanya menggunakan alas berpemanas tetapi juga pelat berpemanas di sekitar kepala cetak yang membantu menghasilkan distribusi suhu yang homogen dalam cetakan, mengurangi tekanan termal dan memastikan kristalisasi.”
“Kami juga memiliki printer Markforged (Cambridge, Mass., A.S.) untuk sementara waktu dan kemudian mendapatkan Anisoprint [Esch-sur-Alzette, Luksemburg],” kata Konsul. Meskipun printer Markforged memang mengaktifkan FDM dengan serat kontinu, tim LCC memilih untuk tidak menyimpannya. “Masalah yang kami miliki adalah sistemnya sangat tertutup,” jelas Konsul. “Perangkat lunak pengiris dari Markforged terlalu sulit digunakan untuk penelitian karena sangat membatasi apa yang bisa kami lakukan. Kami hanya dapat mencetak lapisan bahan serat kontinu dan kemudian lapisan filamen termoplastik yang diperkuat serat pendek di atasnya. Pemotong yang menghasilkan kode tidak akan menerima kode-G dari kami. Jadi, tidak ada cara untuk memberi tahu mesin untuk mencetaknya seperti yang kami inginkan dengan serat kontinu di setiap lapisan, dll.”
Ketika ditanya tentang hal ini, Markforged menjelaskan bahwa sistemnya tidak pernah dimaksudkan untuk digunakan untuk penelitian, tetapi dirancang untuk menjadi sederhana dan kuat untuk digunakan secara luas dalam pembuatan suku cadang, memanfaatkan jalur serat berbasis aturan dan membutuhkan sedikit usaha dan waktu untuk mengonfigurasi alat pengiris. . Ini Perangkat lunak Eiger memang memungkinkan pengguna untuk mengonfigurasi lapisan satu per satu, dan Markforged menerima masukan dan memprioritaskan peningkatan pengalaman pengguna bagi pelanggannya.
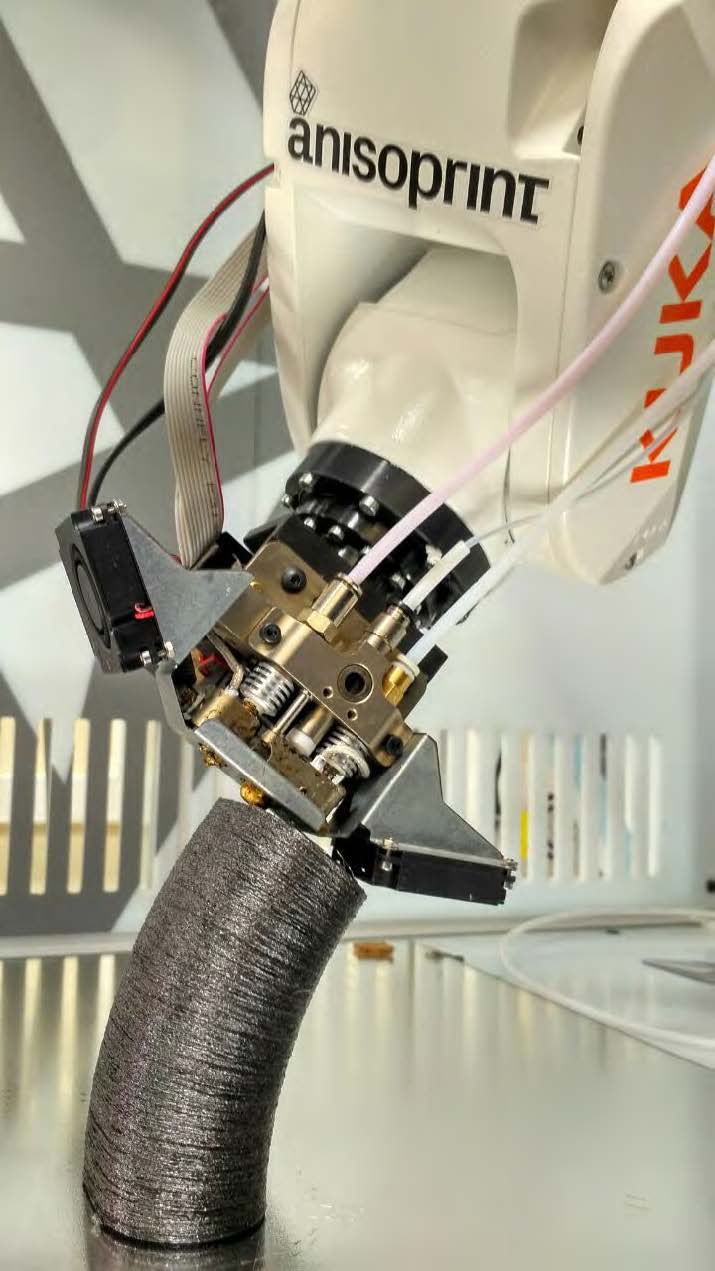
Kredit Foto:Ansoprint
“Anisoprint, yang menggunakan alat pengiris kode-G yang sepenuhnya terbuka, memberi kami lebih banyak akses ke prosesnya,” kata Konsul. “Ini juga mampu mencetak serat karbon terus menerus dan tidak hanya dalam lapisan 2D, tetapi juga di luar bidang, dalam kurva 3D. Kami memiliki kepala cetak Anisoprint untuk robot Kuka kecil, yang mampu menghasilkan bagian berukuran 1 meter kali 1 meter, yang lebih besar dari kebanyakan desktop, tetapi kecil untuk sistem robot."
Tapi bagaimana dengan matriks ganda Anisoprint bahan termoset-termoplastik (TS-TP)? Seperti yang dijelaskan dalam blog saya tahun 2019 di Anisoprint “… pertama-tama ia menanamkan penguatan serat berkelanjutan dengan termoset polimer dan kemudian mengekstrusi ini ke dalam filamen termoplastik yang meleleh selama pencetakan.” Konsul menjawab bahwa adhesi antara filamen TS dan TP cukup bagus. “Pada uji coba pertama kami, kami bisa mendapatkan konten volume serat yang lebih tinggi dibandingkan dengan printer Markforged, tetapi ini karena kami dapat memodifikasi kode-G. Kepala cetak Anisoprint mendorong filamen TS ke dalam TP dan kemudian meletakkannya. Kami berencana menggunakan printer itu untuk bagian exoskeleton. Ini cara mudah untuk mengintegrasikan serat berkekuatan lebih tinggi."
Printer pelet yang diekstrusi
Perkembangan selanjutnya adalah ke printer skala besar, pertama dengan TP yang diperkuat serat pendek dan kemudian TP serat berkelanjutan. “Kami pertama kali mengembangkan ekstruder yang dipasang pada robot, dan kemudian minat kami pada mesin CEAD mengikuti dengan cepat. Kami berharap serat berkelanjutan dapat diintegrasikan ke dalam kedua sistem ini tahun depan.”
Tetapi mengapa Anda membutuhkan mesin CEAD jika Anda sudah memiliki ekstruder di lengan robot? “Ekstruder awal adalah versi beta dari ekstruder pelet Dyze Pulsar, yang menghasilkan maksimum sekitar 2kg/jam dan kira-kira 1kg/jam dengan PAEK, tetapi ia berjuang dengan lebih dari 20% pemuatan serat karbon,” kata Konsul. “Namun, output rata-rata lebih rendah karena robot sering melakukan akselerasi dan deselerasi selama pencetakan. Untuk COMBO3D, setengah cetakan skala kecil awal sudah membutuhkan setidaknya 36 kilogram, jadi kami membutuhkan sekitar 48 jam untuk mencetak setengahnya. Kami juga harus selalu didampingi oleh seseorang karena kesalahan, seperti saluran pengumpanan material yang terhalang atau bagian yang melengkung, dapat terjadi kapan saja.”
Karena demonstrator akhir COMBO3D sekitar 10 kali lebih besar dari suku cadang skala kecil awal, mencetaknya menggunakan sistem ekstruder pertama ini tidak layak, kata Konsul. “Selain itu, beberapa bahan yang diberikan Victrex kepada kami memiliki viskositas yang lebih tinggi dan ekstruder pertama ini tidak dapat memberikan torsi yang cukup untuk mengekstrusi polimer tersebut. Dengan printer CEAD, kami memiliki output maksimum sekitar 12,5 kg/jam, dan setelah beberapa jam uji coba, kami memiliki output rata-rata yang stabil sekitar 5-6 kg/jam. Hal ini memungkinkan kami untuk mencetak setengah cetakan skala kecil dalam waktu kurang dari 8 jam dan memungkinkan kami menggunakan kandungan serat yang lebih tinggi untuk mengurangi lengkungan, membuat proses secara keseluruhan lebih mudah dikendalikan.”
“Jadi, meskipun Pulsar sudah memungkinkan kami untuk menggunakan pelet, mencapai keluaran material yang tinggi, dan memanfaatkan tingkat kebebasan robot,” lanjutnya, “printer CEAD memperluas kemampuan kami ke bagian yang lebih besar, kandungan serat yang lebih tinggi, dan jangkauan polimer yang lebih luas. . Pulsar menjembatani kesenjangan antara printer berbasis filamen kami dan CEAD, tidak hanya dalam output tetapi juga dalam ukuran nozzle dan detail hasil cetakan.”
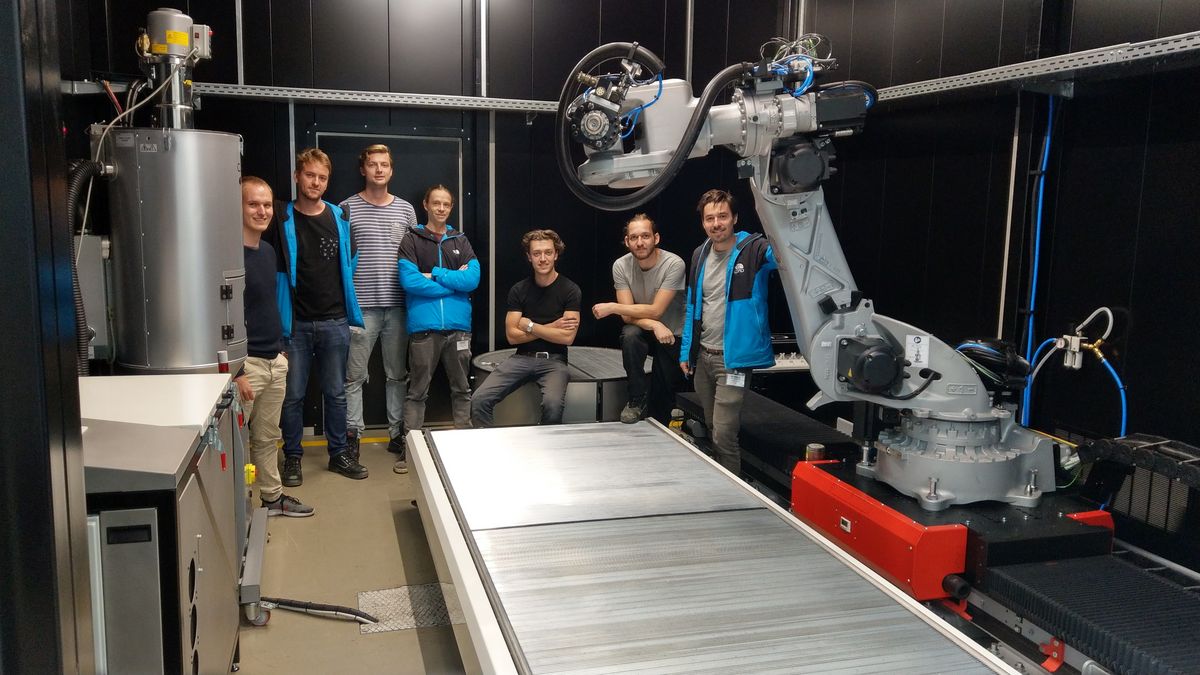
Kredit Foto:Ketua Komposit Karbon
Data teknis CEAD AM Flexbot:
- Data teknis AM Flexbot:
- Cetak ekstrusi berbasis pelet hingga 12,5 kg/jam (tanpa perkuatan dan perkuatan serat pendek)
- Pemrosesan bahan hingga 450 °C
- Volume bangunan 3000 x 1200 x 1700 milimeter
- Bangun pelat di atas meja putar atau meja datar (dapat dipanaskan)
- Pengerjaan ulang dengan kepala penggilingan.
COMBO3D
Tujuan dari proyek Clean Sky 2 ini adalah untuk mencetak cetakan 3D untuk menghasilkan flaperon komposit demonstrator (1,5 x 3 meter) untuk pesawat penumpang besar, bagian dari Paket Kerja A-3.1:Sayap multidisiplin untuk kecepatan tinggi dan rendah. Tujuan penggunaan manufaktur aditif adalah untuk mempersingkat waktu tunggu untuk produksi alat. Proyek ini dimulai pada Januari 2019 dan akan berakhir Maret 2021. Mitra termasuk Alpex Technologies (Mils bei Hall, Austria), spesialis logam ringan Leichtmetallkompetenzzentrum Ranshofen (Ranshofen, Austria) dan Victrex (Thornton Cleveleys, Inggris), pemasok termoplastik berkinerja tinggi poliariletherketon (PAEK).
Bagian penting lainnya dari proyek ini adalah untuk menunjukkan bahwa flaperon serat karbon/epoksi ini dapat dibuat dengan resin transfer moulding (RTM) alih-alih prepreg yang diawetkan dengan autoklaf. Bagian RTM akan mengering pada suhu 180°C yang sama dengan bagian autoklaf. Untuk memastikan stabilitas termal, alat ini akan dicetak dengan PAEK pendek yang diperkuat serat karbon, yang memiliki suhu leleh 305°C.
Untuk mempersingkat siklus penyembuhan, cetakan cetak 3D akan mengintegrasikan kontrol suhu aktif. “Kita harus bisa memanaskan dan mendinginkan cetakan lebih cepat dibandingkan dengan autoklaf,” catatan Konsul. “Kami akan menggunakan jaring elemen pemanas listrik 3 milimeter di bawah permukaan cetakan dan juga mengintegrasikan saluran cetak untuk minyak atau udara yang dipanaskan pada 6 milimeter di bawah permukaan cetakan. Dengan cara ini, kita dapat memanaskan permukaan cetakan dengan sangat cepat, tetapi juga menggunakan saluran untuk memanaskan seluruh volume alat. Kami menargetkan tingkat pemanasan dan pendinginan 50% lebih cepat daripada autoklaf dan merasa yakin kami dapat mencapai tingkat setidaknya 30% lebih cepat.”
Elemen pemanas apa yang akan diintegrasikan ke dalam cetakan 3D? “Kami telah menggunakan penempatan serat yang disesuaikan (TFP) dari roving karbon pada tekstil serat kaca sebagai elemen pemanas untuk mewujudkan zona pemanas yang berbeda dalam cetakan CFRP untuk bilah rotor helikopter,” jelas Konsul. “Ini untuk proyek Clean Sky 1 yang kami selesaikan bekerja sama dengan QPoint Composite (Dresden, Jerman). Kami akan bekerja dengan konsep serupa pada cetakan COMBO3D.”
Seluruh pengembangan alat cetak didukung oleh simulasi. Desain alat akan dioptimalkan dengan menerapkan sistem pemanas dan pendingin dalam simulasi termal. Proses manufaktur juga akan disimulasikan, mendukung proses pencetakan dengan menghasilkan pengetahuan tentang distribusi suhu selama pencetakan dan menghubungkannya dengan perencanaan jalur.
Pemasangan mesin CEAD dan kemajuan proyek
“Sistem CEAD dikirimkan dengan sangat cepat — dari pemesanan hingga pemasangan hanya 6 bulan,” kata Konsul. “Pada saat ini, kami telah menyelesaikan pengujian bahan, merancang perkakas pelat dan mulai mencetak bagian-bagian kecil. Kami khawatir akan membutuhkan waktu lama untuk menjalankan proses dengan baik dengan CEAD AM Flexbot, tetapi ini bekerja dengan baik dengan uji coba pertama.”
Perkakas piring? “Ini cetakan kecil, sudah mengintegrasikan saluran pendingin dan elemen pemanas untuk menghasilkan pelat CFRP untuk pengujian kupon,” jelasnya. “Pengujian ini untuk memastikan bahwa kualitas cetakan CFRP RTM cetak 3D kami akan sebanding dengan CFRP saat ini yang diproduksi Saab dengan proses autoklaf mereka.”
Sayangnya, proyek itu terganggu oleh COVID-19, "tetapi sekarang semuanya berjalan dengan baik dan kami mengejar ketinggalan," kata Konsul. Dan bagaimana dengan menggunakan PAEK untuk cetakan cetak 3D? “Satu-satunya masalah saat ini adalah bahwa Tg [suhu transisi gelas] untuk PAEK adalah 130-140 °C, yang lebih rendah dari penyembuhan 180 °C untuk bagian demonstrasi,” catat Konsul. “Jadi, kita masih harus melihat berapa banyak siklus yang bisa kita selesaikan pada temperatur curing sebelum terjadi creep atau permukaan rusak.”
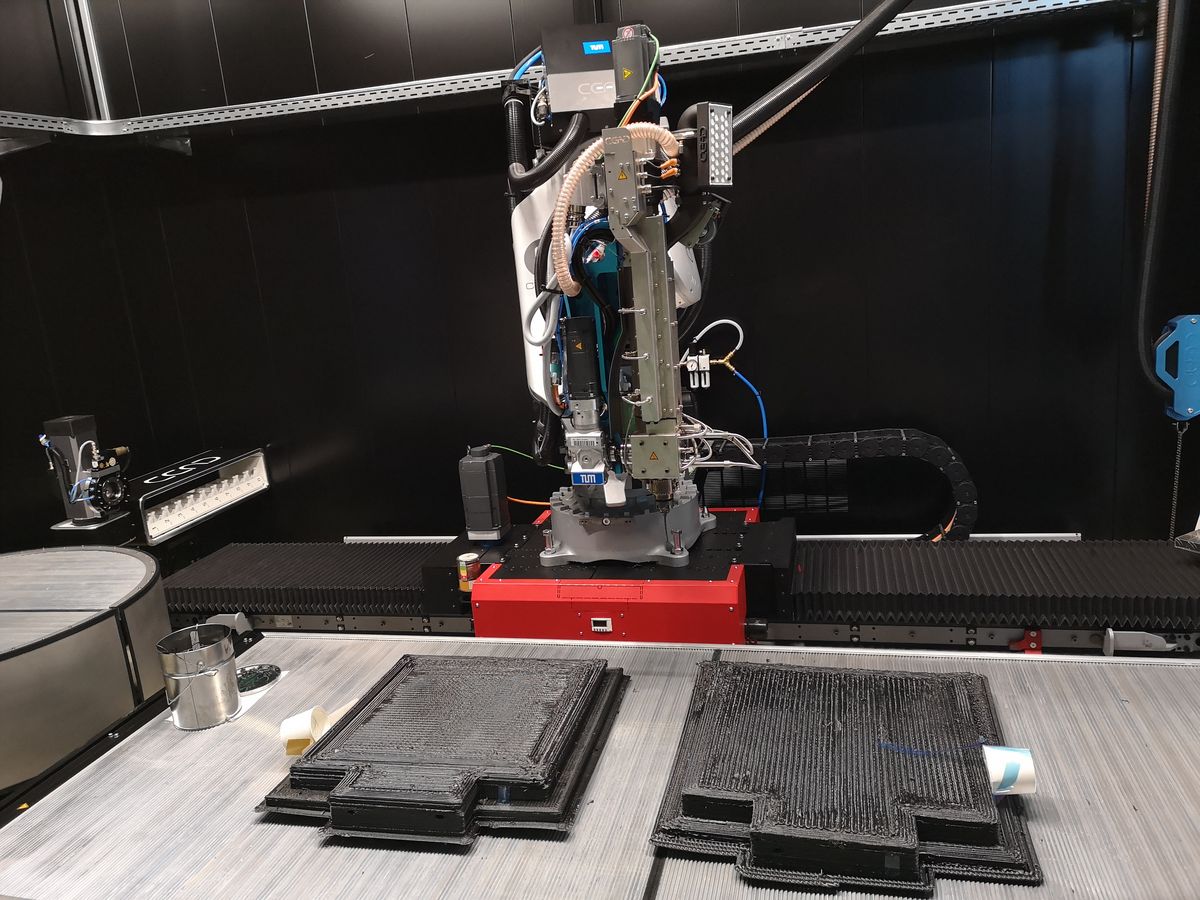
Kredit Foto:Ketua Komposit Karbon
Mesin CEAD di proyek lain?
“Kami melamar proyek di bidang peralatan kedirgantaraan yang dimulai tahun depan dengan GKN Aerospace Deutschland (Munich) menggunakan mesin CEAD dan polietersulfon (PESU),” kata Konsul. [Catatan:GKN di Jerman membuat flap sayap komposit untuk A330 dan A350 serta aileron untuk keluarga jet bisnis Bombardier Global.] “CEAD akan menjadi bagian dari tanggung jawab ini untuk pengembangan mesin untuk serat karbon berkelanjutan. Kami juga berencana untuk menggunakan mesin CEAD secara internal untuk membuat cetakan prototipe untuk RTM yang jika tidak, akan disubkontrakkan. Ini memberi kami manfaat dalam mempercepat pekerjaan.”
Konsul mencatat bahwa PESU memiliki Tg lebih tinggi dari PAEK. “Ini juga amorf, bukan semi-kristal, jadi seharusnya lebih mudah untuk dicetak, meskipun ketahanan mulur mungkin menjadi masalah. Yang kami coba lakukan adalah menghindari PEI (polyetherimide). Di masa lalu, kami melihat masalah ikatan PEI ke resin epoksi. RTM6 [epoksi untuk RTM] melarutkan PEI yang mendorong adhesi yang baik antara keduanya. Inilah yang tidak Anda inginkan dalam cetakan cetak 3D yang perlu melepaskan bagian-bagiannya, bukan menempelkannya.”
Komposit cetak 3D industri (dan terbang) masa depan
Dalam membahas beberapa proyek lain yang sedang dikejar LCC di bidang manufaktur aditif, saya bertanya kepada Konsul apa yang menahan CFRP di exoskeletons? “Karena exoskeleton perlu disesuaikan dengan masing-masing pemakainya, bagian-bagiannya khusus sehingga volumenya tidak besar,” jawabnya. “Proyek kami bertujuan untuk memungkinkan produksi komponen eksoskeleton ekstremitas bawah spesifik pasien untuk memungkinkan produksi eksoskeleton spesifik pasien dalam waktu kurang dari 24 jam. Eksoskeleton ini akan mendukung rehabilitasi pasien stroke berdasarkan profil biofisik mereka dan kebutuhan rehabilitasi medis yang unik.” (Lihat artikel CW, “kerangka luar C-FREX bergantung pada CFRP …”)
“Orang-orang memiliki konsep bahwa pencetakan 3D dapat mencetak bagian mana pun, tetapi Anda harus terlebih dahulu memiliki pengalaman dengan pencetakan 3D dan komposit. Misalnya, sering ada masalah dengan adhesi lapisan ke lapisan dan anisotropi yang harus dipahami. Bagian komposit yang dicetak 3D tidak akan memiliki desain yang sama dengan yang saat ini terbuat dari plastik dan logam.”
Dia mencatat masih ada masalah yang harus diatasi untuk menggunakan komposit cetak 3D untuk produksi suku cadang pesawat berperforma tinggi, misalnya:Bagaimana Anda merancang suku cadang ini untuk manufaktur aditif? Bagaimana Anda mengidentifikasi bagian di mana manufaktur aditif menambah nilai? “Perkakas kedirgantaraan adalah bidang utama aplikasi yang sedang dilihat oleh tim kami saat ini,” kata Konsul. “Pencetakan 3D cetakan sangat cocok. Cetakan ini harus tahan terhadap semua kondisi pengeringan yang sama seperti suku cadang, tetapi risiko terkait dengan cetakan vs. bagian yang beterbangan lebih kecil. Contoh yang baik adalah pengaku tulang rusuk untuk sayap, di mana ada banyak bagian yang berbeda tetapi tidak banyak siklus per bagian. Jadi, ini adalah cara yang baik untuk menghasilkan pengalaman dengan teknologi. Masih terlalu dini untuk mencoba bagian struktural yang akan terbang. Kami akan menargetkan jangka panjang ini, tetapi alat pencetakan akan memungkinkan kami untuk membuat proses pencetakan 3D cukup stabil dengan properti performa tinggi dan juga mengembangkan kemampuan untuk memprediksi bagian dan proses ini secara akurat dalam simulasi.”