RTM Kompresi untuk produksi aerostruktur masa depan
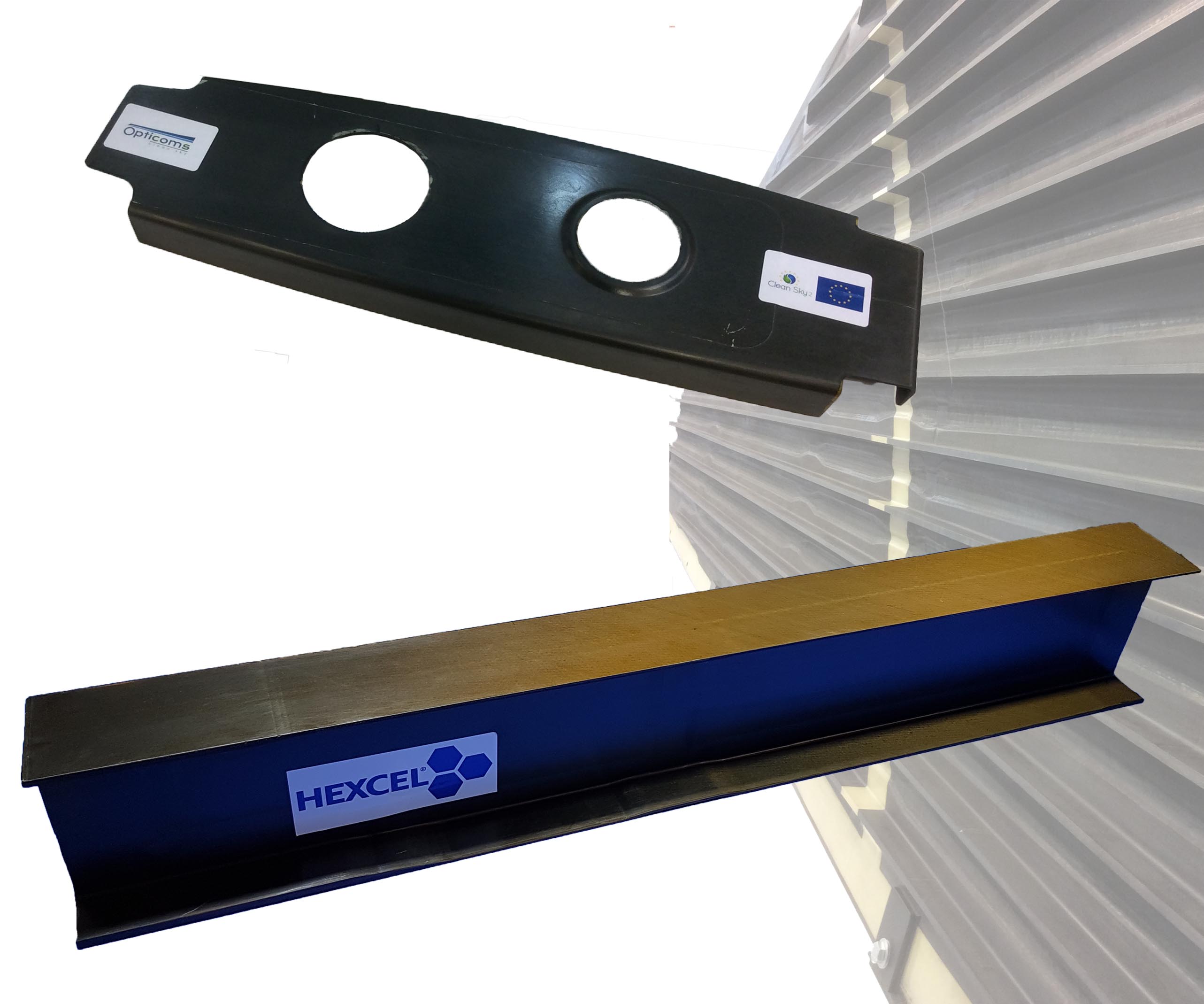
Komposit telah mendapatkan tempat permanen di badan pesawat komersial karena mereka memungkinkan struktur ringan berkekuatan tinggi yang memberikan biaya perawatan lebih rendah dibandingkan dengan logam. Proyeksi saat ini untuk generasi berikutnya dari pesawat berbadan lebar dan sempit menunjukkan pertumbuhan yang berkelanjutan dalam rangka pesawat komposit, tetapi hanya jika bahan dan proses dapat memenuhi target yang menantang untuk biaya rendah dan tingkat produksi yang tinggi. Meskipun prepreg epoksi yang diawetkan dengan autoklaf telah menjadi yang tertinggi dalam kerangka udara polimer yang diperkuat serat karbon (CFRP) hingga saat ini, pengembang pesawat generasi berikutnya secara agresif mengejar teknologi out-of-autoclave (OOA) dengan otomatisasi terintegrasi dan inspeksi inline sebagai faktor utama untuk produksi Industri 4.0 masa depan.
Pemasok peralatan dan otomasi Techni-Modul Engineering (Coudes, Prancis) dan anak perusahaannya di AS, Composite Alliance Corp. (Dallas, Texas, AS) telah bermitra dengan unit bisnis Inggris dan Prancis dari pemasok bahan canggih Hexcel (Stamford, Conn., AS) untuk mendemonstrasikan produksi OOA otomatis dari rusuk dan stringer CFRP. Suku cadang dibuat dengan preforming otomatis dari penguatan serat karbon kering Hexcel dan proses pencetakan transfer resin kompresi (C-RTM) yang menawarkan infiltrasi cepat resin epoksi cair Hexcel HexFlow RTM6 untuk menghasilkan suku cadang dengan volume serat 60% dan rongga kurang dari 1% dalam siklus 2,5 hingga 3,0 jam yang dapat diskalakan untuk menghasilkan banyak bagian untuk produksi tingkat tinggi.
Pengembangan tulangan kering
“Kami melihat cetakan komposit cair (LCM) menawarkan jawaban atas tantangan tiga arah untuk mengurangi biaya, siap untuk menilai dan memberikan kinerja struktur utama,” jelas Rémy Pagnac, Insinyur dukungan teknis Hexcel untuk cetakan komposit cair. Hexcel telah mengembangkan bahan serat karbon HiMax noncrimp fabric (NCF) dan HiTape unidirectional (UD) untuk memenuhi kebutuhan kinerja struktur utama saat menggunakan proses LCM. HiMax memungkinkan struktur besar dan datar seperti kulit sayap untuk diletakkan dengan cepat, sementara HiTape memungkinkan layup yang disesuaikan untuk struktur besar dan kompleks dengan limbah minimal. “Kami dapat mencapai properti yang setara dengan prepreg UD generasi terbaru,” tambah Pagnac.
Hexcel telah bekerja untuk mengurangi jumlah besar dan meningkatkan daya serap dengan HiMax NCF, termasuk benang jahitan 20 dTex yang halus. Material HiMax dibuat di fasilitas Formax sebelumnya di Leicester, Inggris, yang diakuisisi Hexcel pada 2016. Multiaksial spread-tow ringan yang diproduksi di fasilitas ini telah memiliki sejarah panjang dalam menyediakan solusi untuk aplikasi yang menuntut seperti yacht balap, supercar, dan Formula 1 mobil balap. Sekarang bahan NCF telah digunakan dalam proyek demonstrasi sayap yang diselesaikan oleh Airbus Defence and Space (Airbus DS, Cadiz, Spanyol) dan Danobat (Elgoibar, Spanyol) menggunakan teknologi Automated Dry Material Placement (ADMP) yang terakhir — sejenis penempatan serat otomatis (AFP) untuk NCF (lihat “Membuktikan kelayakan untuk infus kain kering untuk aerostruktur besar”) — dan dalam proyek ZAero yang disponsori Airbus untuk struktur CFRP tanpa cacat seperti sayap yang kaku dengan stringer (lihat “Pembuatan suku cadang komposit tanpa cacat” ”).
Dengan HiMax dan HiTape, Hexcel mengintegrasikan lapisan tipis, selubung filamen termoplastik dengan berat areal rendah yang bertindak sebagai pengikat, menghilangkan kebutuhan akan pengikat bubuk yang secara historis digunakan dalam bahan kering untuk preforming dan cetakan cair. Untuk HiMax, kerudung ini disisipkan di antara lapisan NCF; untuk HiTape, kerudung diterapkan pada kedua sisi unitape serat karbon. “Dengan ini, Anda tidak perlu menggunakan pengikat bubuk untuk menahan lapisan UD di tempatnya,” jelas Pagnac. “HiTape dikalibrasi, dan bukan slit tape, jadi tidak ada fuzz dan variasi lebar yang lebih sedikit untuk pemrosesan AFP yang lebih baik. Selubung termoplastik juga menambah ketangguhan pada laminasi akhir, dan kami telah menunjukkan bahwa kami dapat mencapai tingkat pengendapan material yang tinggi dengan mesin AFP generasi berikutnya.” Dalam makalah SAMPE Mei 2015, Hexcel menjelaskan bentuk awal kurvatur tunggal yang diproduksi menggunakan HiTape selebar 0,25 inci yang diaplikasikan dengan mesin AFP Coriolis Composites (Quéven, Prancis) yang dilengkapi laser pada kecepatan layup 1 meter/detik. Ia juga bekerja dengan peralatan AFP Electroimpact (Mukilteo, Wash., U.S.) untuk menunjukkan tingkat pengendapan hingga 150 kilogram/jam untuk aerostruktur tiang ukuran penuh.
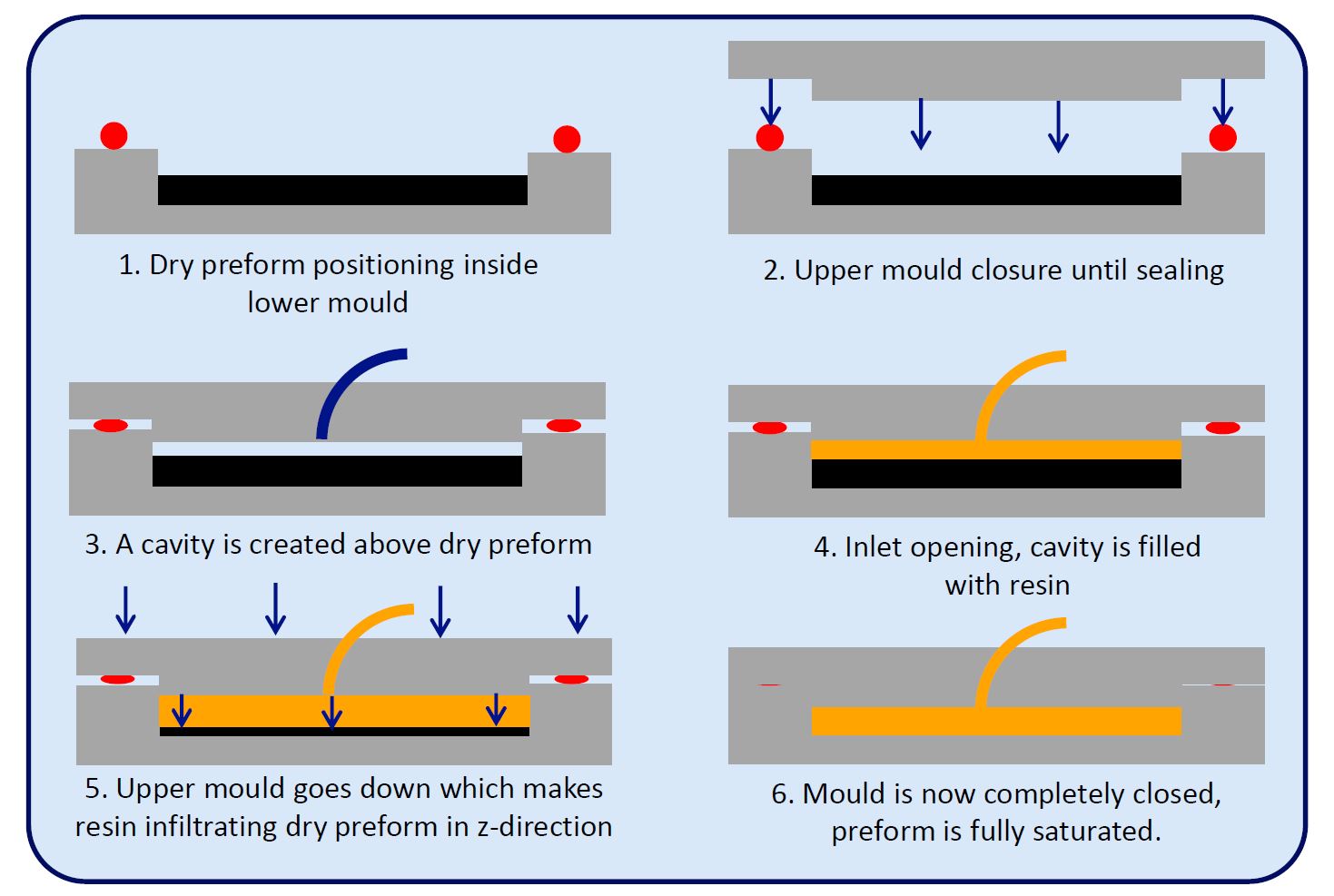
Gbr. 1 Kompresi RTM
Dalam C-RTM, preform kering ditempatkan ke dalam cetakan RTM, tetapi cetakan hanya sebagian ditutup, meninggalkan celah antara preform kering dan permukaan cetakan atas. Vakum kemudian diterapkan, resin disuntikkan dan pers menutup celah di cetakan, mendorong resin cair ke dalam bentuk awal dalam arah-z di seluruh bagian. Sumber | Hexel
Mengadaptasi C-RTM untuk kedirgantaraan
C-RTM pertama kali diperkenalkan dengan RTM tekanan tinggi (HP-RTM) untuk komposit otomotif. Seperti pada RTM konvensional, C-RTM memerlukan penempatan prabentuk serat kering ke dalam cetakan logam yang sesuai, menyuntikkan resin cair ke dalam bentuk awal dan kemudian menerapkan panas dan tekanan menggunakan penekan yang digerakkan. Namun, dalam C-RTM, cetakan hanya sebagian ditutup, meninggalkan celah antara preform kering dan permukaan cetakan atas (Gbr. 1). Vakum kemudian diterapkan, dosis yang tepat dari resin campuran disuntikkan dan pers menutup celah di cetakan, memaksa resin cair turun ke bentuk awal dalam arah-z di seluruh bagian. “Ini jauh lebih cepat daripada menyuntikkan resin ke dalam pesawat melalui bagian tersebut,” jelas insinyur proses Techni-Modul Engineering Thomas Chevallet. 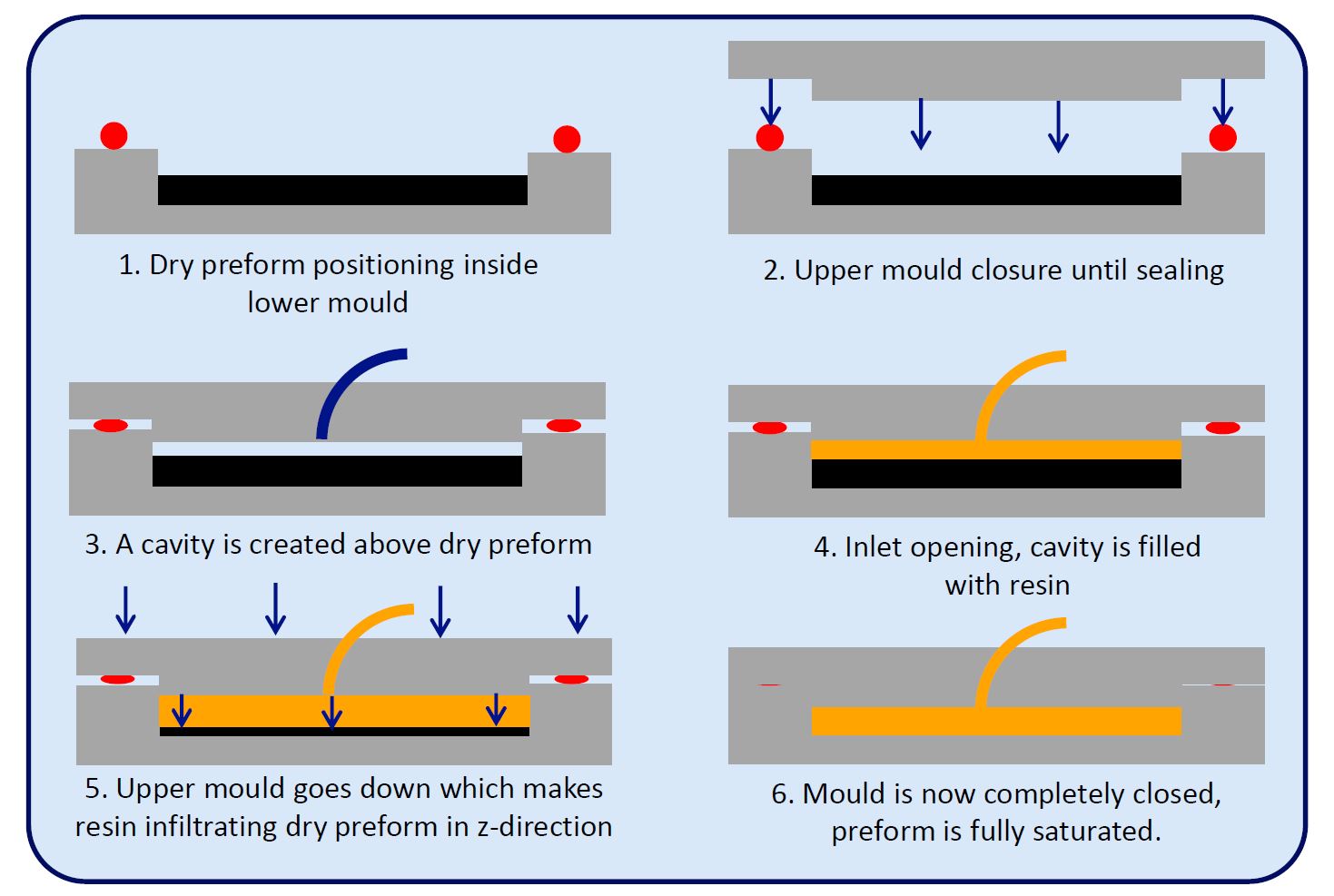
Techni-Modul Engineering melihat peluang untuk mengadaptasi C-RTM untuk kedirgantaraan selama perannya sebagai mitra dalam proyek Clean Sky 2 “Optimized Composite Structures” (OPTICOMS). Diselenggarakan dalam Paket Kerja B-1.2 ("Struktur komposit yang lebih terjangkau"), OPTICOMS bertujuan untuk mengurangi biaya produksi pesawat kecil (misalnya, pesawat jet regional) melalui struktur terintegrasi dan manufaktur otomatis, mengeksplorasi metode prepreg dan resin cair. OPTICOMS telah merancang demonstran sayap komposit yang terdiri dari kulit sayap atas dengan tiga tiang, diproduksi sebagai struktur terintegrasi dalam proses satu tembakan. Sayap skala penuh (Gbr. 2) adalah bagian dari AIRFRAME Innovative Technology Demonstrator (ITD) untuk mengevaluasi dan mematangkan teknologi menuju tingkat kesiapan teknologi (TRL) 6 untuk pesawat generasi berikutnya yang diproduksi mulai tahun 2025 dan seterusnya. Israel Aerospace Industries (Lod, Israel) terpilih sebagai koordinator OPTICOMS pada Juli 2016. Konsorsium tersebut juga mencakup pesawat kecil OEM Piaggio Aerospace (Savona, Italia), Techni-Modul Engineering dan pemasok peralatan AFP Coriolis Composites dan Danobat.
Gbr. 2 Clean Sky 2 OPTICOMS rib
Techni-Modul adalah mitra dalam proyek Clean Sky 2 “Optimized Composite Structures” (OPTICOMS), yang telah merancang demonstrator sayap komposit yang terdiri dari kulit sayap bawah, beberapa rusuk, dan kulit sayap atas dengan tiga tiang. Yang terakhir ini diproduksi sebagai struktur terintegrasi dalam proses one-shot. Demonstran akan dievaluasi untuk pesawat generasi berikutnya yang diproduksi mulai tahun 2025 dan seterusnya. Sumber | Bersihkan Langit 2
“C-RTM sudah terkenal di industri ini,” jelas Chevallet, “tetapi dengan HP-RTM, press besar masih dibutuhkan. Pengembangan kami adalah untuk mengadaptasi C-RTM untuk injeksi cepat menggunakan tekanan yang lebih rendah, memungkinkan produksi suku cadang kedirgantaraan yang lebih murah dengan persyaratan yang sangat ketat untuk volume serat tinggi, penyelarasan serat, dan rongga rendah. Waktu injeksi untuk rusuk sayap sepanjang 0,7 meter dengan lebar 0,2 meter di proyek OPTICOMS dipotong dari 40 menjadi lima menit. Dalam program pengujian terpisah untuk stringer balok-I berukuran panjang 900 milimeter dan tinggi 150 milimeter, waktu injeksi dipersingkat dari satu jam menjadi kurang dari lima menit.
“Pengurangan waktu injeksi yang ditawarkan oleh C-RTM ini akan lebih besar untuk bagian besar seperti kulit sayap penuh atau bilah rotor helikopter,” tambah Chevallet. Dia mencatat bahwa C-RTM juga memungkinkan injeksi resin viskositas tinggi serta sistem injeksi tekanan rendah dan tekanan rendah tonase, yang mengurangi biaya. “Tekanan cetakan selama C-RTM hanya 6 bar, jauh lebih rendah daripada yang digunakan di HP-RTM,” jelas Chevallet. “Proses ini menghasilkan komposit berkualitas ruang angkasa namun bekerja dengan baik untuk bagian yang besar dan tipis serta bagian yang lebih kecil dan berbentuk kompleks.”
Pembentukan awal otomatis
Meskipun lebih cepat, injeksi resin berbiaya lebih rendah dan pencetakan OOA adalah bagian penting dari pendekatan ini untuk produksi aerokomposit yang lebih terjangkau, rantai proses masih memerlukan beberapa langkah untuk memotong dan meletakkan bahan dan membentuk sebelumnya. “Bagi kami, OPTICOMS juga tentang otomatisasi,” kata Chevallet. Techni-Modul Engineering tidak hanya memasok sistem injeksi C-RTM untuk proyek OPTICOMS, tetapi juga robot pick-and-place dan mesin hot drape forming (HDF), semuanya terintegrasi ke dalam sel produksi yang sepenuhnya otomatis.
Tak lama setelah OPTICOMS dimulai pada tahun 2016, anak perusahaan Techni-Modul Engineering CAC memenangkan ACE Equipment and Tooling Innovation Award dalam kategori manufaktur untuk sel preforming 3D otomatisnya di CAMX 2016 (26-29 September, Anaheim, California, AS). Mampu menghasilkan preform 3D dari serat kering atau prepreg, sel menggunakan gripper penghisap vakum untuk mengambil, menempatkan, dan melipat lapisan potongan ke cetakan preform yang dipanaskan. Techni-Modul Engineering dan CAC mengembangkan perangkat lunak untuk menyiapkan lapisan potongan bahan 2D untuk dibentuk menjadi permukaan yang kompleks dan dapat dikembangkan. Sel ini dikembangkan lebih lanjut di OPTICOMS dan proyek uji balok-I.
Langkah 1
Sumber, semua gambar langkah | Teknik-Modul Rekayasa
Dalam sel otomatis Techni-Modul Engineering, robot pick-and-place menghilangkan lapisan dari pemotong otomatis dan menerapkannya ke alat preforming yang dipanaskan.
Langkah 2
Alat preforming diletakkan di atas meja pemadatan dengan membran vakum berengsel yang dapat digunakan kembali (biru, di kiri) yang digunakan untuk menyelesaikan debulk yang dipanaskan setiap 5-8 lapisan selama layup.
Langkah 3
Setiap siklus preforming stringer menghasilkan satu preform C-beam (dua terdiri dari web I-beam) dan satu preform flensa datar. Dua set yang diperlukan untuk setiap stringer I-beam ditampilkan di sini.
Langkah 4
Empat preform stringer I-beam ditempatkan ke dalam cetakan RTM, vakum diterapkan dan injeksi resin selesai dalam 5 menit.
Langkah 5
Setelah penyembuhan 90 menit, stringer dibongkar dan flash resin dipangkas untuk siklus bagian lengkap 4,5 jam.
Langkah 6 – Pembentukan tulang rusuk 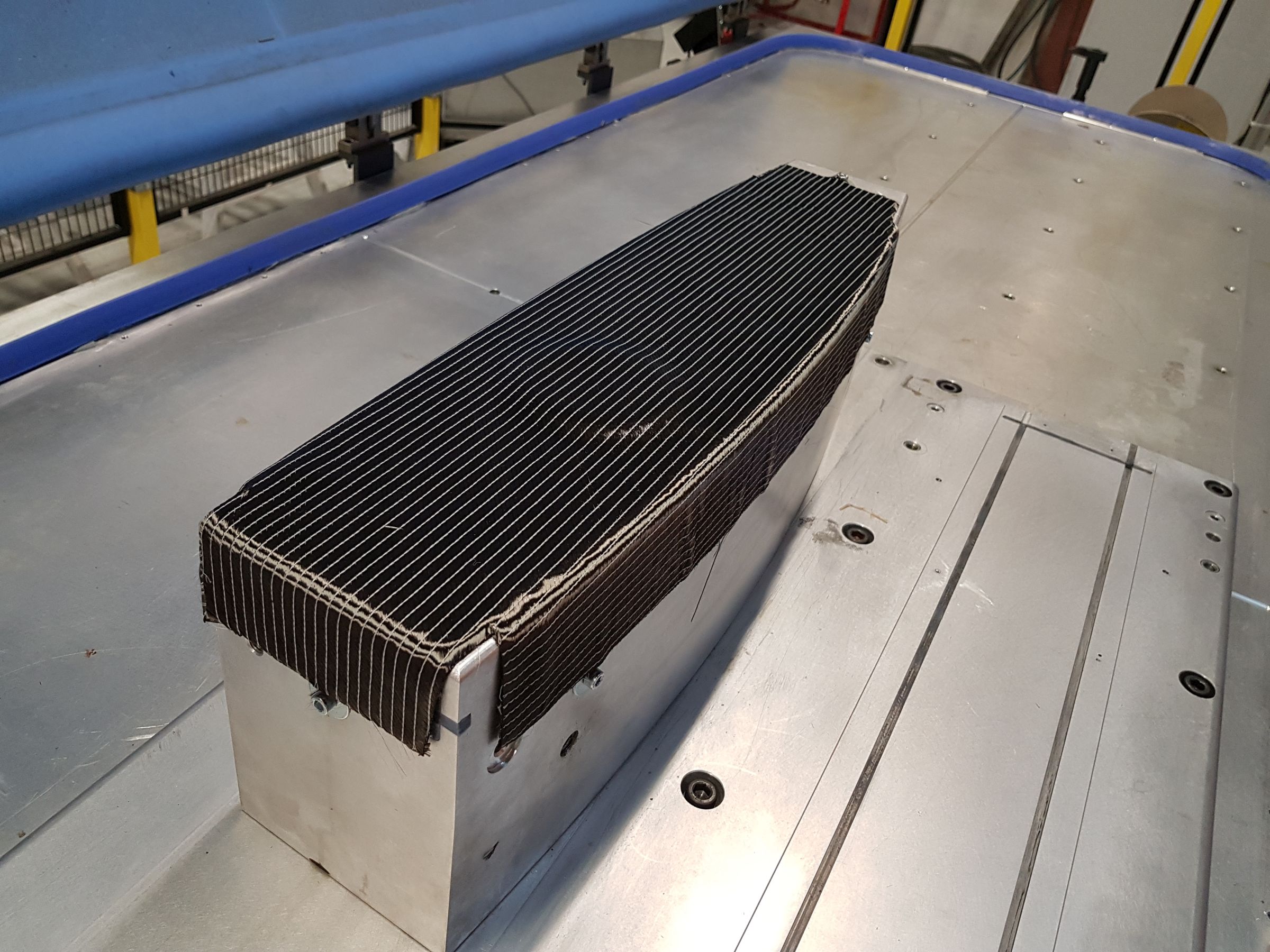
Sebuah robot menempatkan lapisan yang dipotong pada alat preform yang dipanaskan. Setiap 5-8 lapisan, debulk yang dipanaskan diselesaikan untuk memadatkan bentuk awal.
Sebelum debulking, film rilis biru diterapkan.
Breather digunakan untuk mengekstrak udara di seluruh preform.
Setelah debulk terakhir, bentuk awal didinginkan pada pahat dan potongan dipotong (di bawah).
“Kami telah mengotomatiskan penumpukan lapisan manual klasik menggunakan pick and place robotik,” kata Chevallet. “Robot mengambil lapisan dari pemotong otomatis dan mentransfernya ke alat bentuk awal yang dipanaskan yang berada di atas meja pemadatan [Langkah 1 dan 6].” Lapisan kupas (film biru pada Langkah 6), penghisap udara (bahan putih pada Langkah 6) dan membran vakum berengsel yang dapat digunakan kembali (biru muda di sebelah kiri pada Langkah 2 dan 6) diterapkan, diikuti dengan vakum dan panas untuk membentuk dan menghilangkan udara dari tumpukan tekstil (hot drape forming, HDF) sambil melelehkan selubung termoplastik tipis untuk membuat bentuk awal yang dipadatkan.
“Berapa banyak lapisan yang dapat Anda padatkan pada satu waktu tergantung pada bahan dan bentuk bagiannya,” jelas Chevallet. “Untuk bagian dengan kelengkungan rendah, seperti kulit sayap, maka Anda mungkin bisa memadatkan setiap 50 lapisan. Namun, rusuk OPTICOMS memiliki sudut 90 derajat, dan stringer balok-I uji memiliki bentuk-T, jadi Anda harus berhati-hati agar tidak membentuk kerutan pada lapisan selama pembentukan awal.” Dia menambahkan bahwa bentuk kompleks seperti itu mungkin memerlukan pemadatan setiap 5-8 lapisan, tetapi masih dapat menjadi bagian dari proses industri bervolume tinggi:Lapisan tumpukan, HDF 2 menit pemadatan, membuka kembali dan menumpuk lagi, diikuti dengan siklus pemadatan berulang dengan pendinginan akhir bentuk awal pada pahat sebelum dipindahkan ke cetakan RTM.
“Sel otomatis kami dapat ditempatkan pada kecepatan 15 detik per lapis,” catat Chevallet. “Layar untuk rusuk OPTICOMS, dengan total kurang dari 20 lapisan, selesai dalam 20 menit.” Layup untuk stringer I-beam lebih lama — 45 menit karena bentuknya yang kompleks dan tumpukan laminasi, termasuk variasi ketebalan dari 1,2 hingga 6 milimeter. “Ini masih jauh lebih cepat daripada proses manual dan mengurangi risiko kesalahan, meningkatkan pengulangan dan kualitas sekaligus menurunkan biaya,” tambahnya.
Langkah 7
Alat RTM untuk rusuk OPTICOMS terdiri dari beberapa bagian.
Langkah 8
Preform tulang rusuk ditempatkan ke dalam alat RTM. 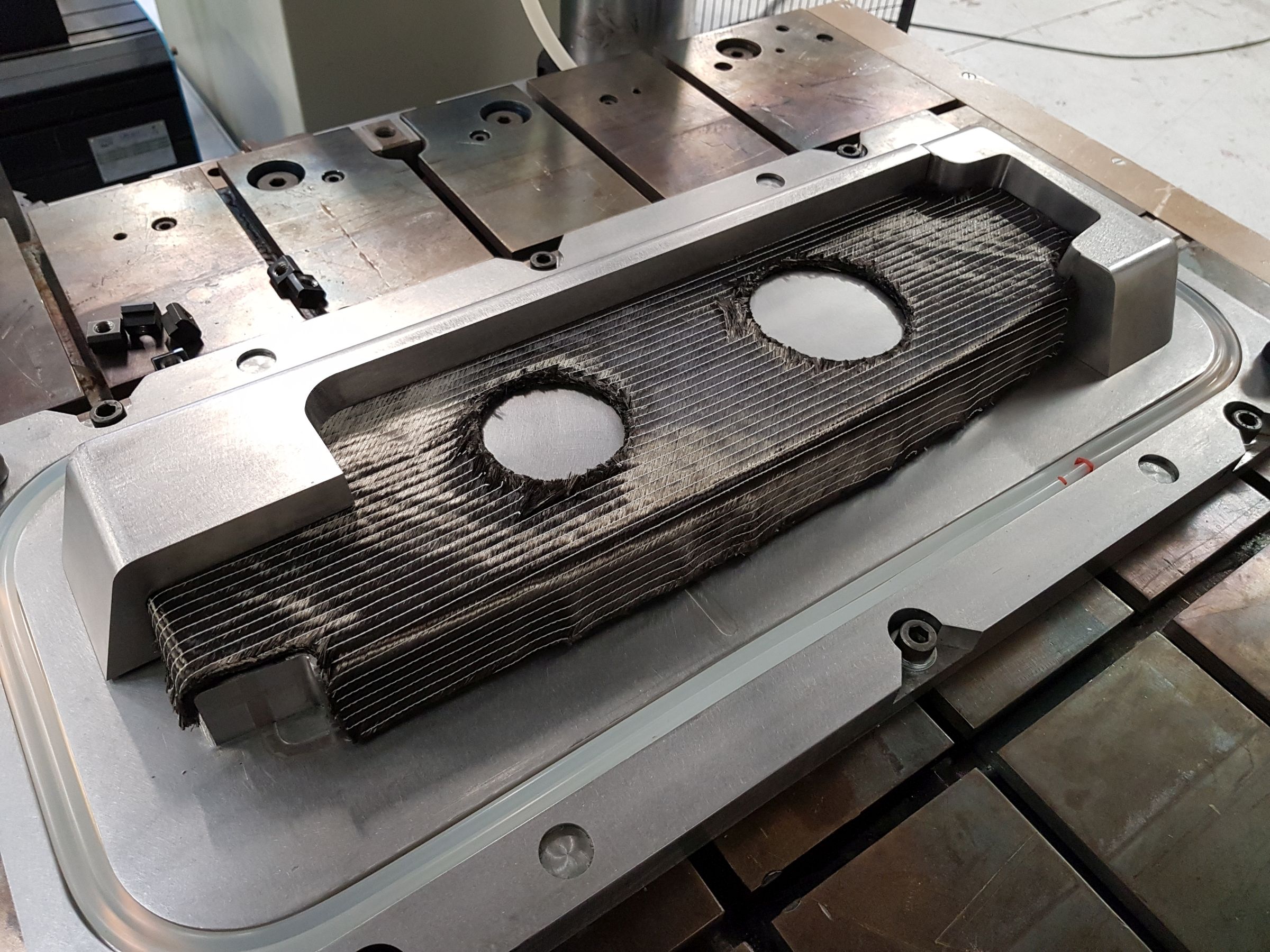
Langkah 9
Vakum diterapkan, resin disuntikkan dan menyusup ke bentuk awal, diikuti dengan penyembuhan 90 menit. Di sini, pers telah dibuka untuk mengungkapkan bagian yang disembuhkan.
Langkah 10
Setelah pembongkaran selesai, kilatan resin akan dihilangkan selama siklus bagian lengkap selama 4 jam.
Kontrol cerdas
Fitur utama lainnya dari sel preforming otomatis Techni-Modul Engineering adalah sistem kontrol terintegrasinya. Disebut sebagai SMART CONTROL, tulang punggungnya adalah sistem kamera dan perangkat lunak multi guna yang membandingkan gambar yang diambil selama pemrosesan dengan basis data CAD bagian, memungkinkan pengenalan bentuk awal, kontrol orientasi serat, pemosisian lapis, dan deteksi cacat dan serpihan benda asing (FOD ). Umpan balik SMART CONTROL menginstruksikan robot cara mengambil dan menempatkan lapisan dalam urutan dan waktu yang tepat, tetapi juga memperingatkan operator seluler ketika mendeteksi kesalahan. “Sistem dapat dikonfigurasi sehingga operator kemudian secara manual menghapus lapisan dan memulai ulang sistem untuk menggantinya,” jelas Chevallet, “atau kami dapat bekerja dengan pelanggan untuk membuat solusi otomatis untuk menghilangkan lapisan cacat dan memperbaiki kesalahan.”
Gambar optik yang sama yang digunakan untuk mendeteksi tepi dan kontur lapisan juga digunakan untuk mengontrol orientasi serat. Chevallet mengakui bahwa jika bagiannya sangat besar (misalnya, panjang 2 meter dibandingkan dengan 200 kali 200 milimeter), “Anda mungkin memerlukan kamera yang mengambil gambar [dari] posisi vertikal yang lebih tinggi untuk mendeteksi tepi lapisan, dan kemudian bergerak lebih dekat ke bagian untuk memeriksa orientasi serat. Anda mengkalibrasi urutan ini untuk setiap jenis bagian. Untuk mendeteksi kerutan dan FOD, ada database cacat yang berbeda dan Anda dapat menambahkannya, sehingga algoritme pembelajaran mendalam meningkat seiring waktu. Idenya adalah untuk memiliki sistem yang adaptif.”
Waktu siklus dan produksi di masa mendatang
Bentuk awal untuk rusuk OPTICOMS dibuat menggunakan HiMax, dan stringer balok-I menggunakan HiTape. Sistem resin untuk keduanya adalah hexcel's HexFlow RTM6 satu komponen (1K) epoksi cair, yang memiliki siklus penyembuhan 90 hingga 120 menit pada 180 °C. Penyembuhan ini adalah langkah terpanjang dalam waktu paruh siklus untuk rusuk OPTICOMS dan stringer balok-I uji, seperti yang dapat dilihat pada Tabel 1.
Sumber | Teknik-Modul Rekayasa
Sampai saat ini, ini adalah satu-satunya epoksi yang memenuhi syarat untuk RTM struktur kedirgantaraan. Namun, minat tumbuh pada sistem dua komponen yang memenuhi syarat yang dicampur pada kepala injeksi, menawarkan peningkatan fleksibilitas siklus penyembuhan dan meniadakan kebutuhan pengiriman dan penyimpanan berpendingin yang diperlukan untuk mencegah reaksi prematur dari RTM6 yang telah dicampur sebelumnya.
Airbus Helicopters (Donauworth, Jerman) bekerja dengan Alpex Technologies (Mils, Austria) dalam proyek SPARTA untuk mendemonstrasikan proses HP-RTM menggunakan versi dua komponen HexFlow RTM6 untuk mencapai penyembuhan 30 menit pada 180 °C untuk pintu A350 rangka, yang merupakan struktur utama berbentuk kompleks berukuran tinggi 2 meter, lebar 200-250 milimeter, dan tebal 8-10 milimeter (lihat “HP-RTM untuk produksi serial aerostruktur CFRP yang hemat biaya”). Airbus juga telah mendemonstrasikan rusuk CFRP 1,5 meter kali 0,5 meter yang dibuat menggunakan HP-RTM oleh anak perusahaan Pusat Teknologi Komposit (CTC, Stade, Jerman), mencapai siklus pencetakan 20 menit untuk suku cadang dengan volume serat 60% dan kurang dari 2 % kekosongan. Pada tahun lalu, CTC telah bekerja dengan sejumlah pemasok tingkat untuk mentransisikan suku cadang prepreg hand layup ke HP-RTM untuk A320. Namun, sistem resin 2K harus memenuhi syarat untuk produksi aerostruktur, dan CTC memperhatikan kemampuan untuk terus memastikan kualitas campuran sistem resin 2K in situ. Alpex menggunakan sensor cetakan dari Netzsch (Selb, Jerman) dan Kistler (Winterthur, Swiss) untuk membantu mencapai hal ini, dan solusi lain sedang dikembangkan (lihat “epoksi 2 bagian untuk meningkatkan produksi aerostruktur komposit”).
Bahkan tanpa sistem 2K, volume produksi yang lebih tinggi dapat dimungkinkan. Kusen pintu dalam proyek SPARTA dilepas setelah pengeringan awal 30 menit pada 180 °C dan perawatan pasca-pers, di bawah vakum untuk menghilangkan tekanan termal dan memastikan sifat mekanik. Menurut kepala R&D Alpex Bernhard Rittenschober, ini membutuhkan set alat tambahan, tetapi hanya satu unit tekan dan injeksi. Dia menjelaskan biaya alat tambahan diimbangi dengan proses dan biaya tekan yang lebih rendah dan dapat diperoleh kembali dengan cepat, bahkan dengan volume rendah 500-1.000 suku cadang/tahun.
“Pencapaian utama dari para demonstran ini adalah kemampuan untuk membuat aerostruktur primer dengan injeksi resin pendek versus proses RTM kedirgantaraan konvensional, di mana merupakan proses yang sulit dan panjang untuk menyusupkan resin ke dalam bagian besar dengan penguatan serat karbon UD,” kata Pagnac . “Kami baru saja memulai dari apa yang dapat kami capai dengan jenis preforming otomatis yang cerdas dan pemrosesan C-RTM ini,” tambah Chevallet. “Ini memiliki potensi untuk mencapai produksi struktur kulit terintegrasi pengaku yang lebih hemat biaya dan berkelanjutan seperti yang diharapkan untuk pesawat masa depan.”