Pencetakan 3D Logam:Panduan Definitif (2021)
Pencetakan 3D logam berkembang pesat di semua lini :teknologi menjadi lebih maju, kecepatan cetak meningkat dan terdapat lebih banyak bahan industri daripada sebelumnya. Kemajuan ini membuka aplikasi baru yang menarik untuk teknologi.
Namun, memahami teknologi yang tersedia dan mengintegrasikannya ke dalam alur kerja yang ada dapat menjadi tantangan bagi banyak perusahaan.
Panduan ini bertujuan untuk membantu Anda lebih memahami pencetakan 3D logam, mulai dari teknologi yang tersedia saat ini hingga manfaat, keterbatasan, dan aplikasi utama teknologi tersebut.
Pencetakan 3D Logam:Teknologinya
Ada sejumlah teknologi pencetakan 3D logam yang berbeda saat ini tersedia di pasaran. Meskipun masing-masing memiliki kelebihan dan keterbatasan, semuanya disatukan oleh prinsip dasar pencetakan 3D untuk membuat bagian logam lapis demi lapis.
Teknologi pencetakan 3D logam yang umum digunakan meliputi:
- Perpaduan Tempat Tidur Bubuk
- Deposisi Energi Langsung
- Pengaliran Pengikat Logam
- Laminasi Lembaran Ultrasonik
Teknologi Penggabungan Tempat Tidur Bubuk

Dari semua teknologi pencetakan 3D logam, Powder Bed Fusion logam mungkin yang paling mapan.
Dengan teknologi Powder Bed Fusion, lapisan bubuk logam didistribusikan secara merata ke platform pembuatan mesin dan secara selektif digabungkan bersama oleh sumber energi — baik laser atau berkas elektron.
Ada dua proses pencetakan 3D logam utama yang termasuk dalam kategori Powder Bed Fusion:
- Selective Laser Melting (SLM) / Direct Metal Laser Sintering (DMLS)
- Pencairan Sinar Elektron (EBM)
Pencairan Laser Selektif dan Sintering Laser Logam Langsung
SLM dan DMLS adalah teknologi pencetakan 3D logam yang paling dominan, dengan DMLS memiliki basis terpasang terbesar di seluruh dunia, menurut laporan oleh IDTechEx Research.
Dengan SLM dan DMLS, laser yang disetel dengan baik dan kuat diterapkan secara selektif ke lapisan bubuk logam. Dengan cara ini, partikel logam menyatu menjadi satu bagian.
Persyaratan penting untuk kedua teknologi tersebut adalah ruang bangunan tertutup yang diisi dengan gas inert, seperti argon. Ini mencegah kontaminasi oksigen dari bubuk logam dan membantu menjaga suhu yang benar selama proses pencetakan.
Pencairan Sinar Elektron
Proses pencetakan 3D lainnya dalam keluarga Powder Bed Fusion adalah Electron Beam Melting (EBM). EBM beroperasi mirip dengan SLM di mana bubuk logam juga dilebur untuk membuat bagian logam yang sepenuhnya padat.
Untuk mencegah kontaminasi dan oksidasi serbuk, proses EBM berlangsung di lingkungan vakum.
Perbedaan utama antara teknologi SLM/DMLS dan EBM adalah sumber energinya:alih-alih laser, sistem EBM menggunakan berkas elektron berdaya tinggi sebagai sumber panas untuk melelehkan lapisan serbuk logam.
EBM juga cenderung menghasilkan part logam dengan tingkat akurasi yang lebih rendah jika dibandingkan dengan SLM dan DMLS. Ini karena ketebalan lapisan dalam proses SLM biasanya lebih tipis (antara 20 dan 100 mikron) daripada di EBM (antara 50 dan 200 mikron), sehingga menghasilkan cetakan yang lebih akurat.
Karena berkas elektron biasanya lebih kuat daripada laser, EBM sering digunakan dengan superalloy logam bersuhu tinggi untuk membuat suku cadang untuk aplikasi yang sangat menuntut seperti mesin jet dan turbin gas. Bagian logam yang dihasilkan sangat padat, dan karenanya ideal untuk industri dirgantara.
Tingginya biaya sistem EBM adalah sesuatu yang perlu dipertimbangkan bagi perusahaan yang ingin berinvestasi dalam teknologi ini. Selain itu, karena teknologinya bergantung pada muatan listrik, EBM hanya dapat digunakan dengan logam konduktif, seperti titanium dan paduan kromium-kobalt.
Baik SLM/DMLS atau EBM, semua bagian logam yang diproduksi dengan teknologi Powder Bed Fusion akan memerlukan beberapa bentuk pasca-pemrosesan. Pasca-pemrosesan diperlukan, tidak hanya untuk meningkatkan estetika bagian, tetapi juga untuk meningkatkan sifat mekaniknya dan memenuhi parameter desain yang tepat, terutama untuk aplikasi yang menuntut.
Deposisi Energi Langsung
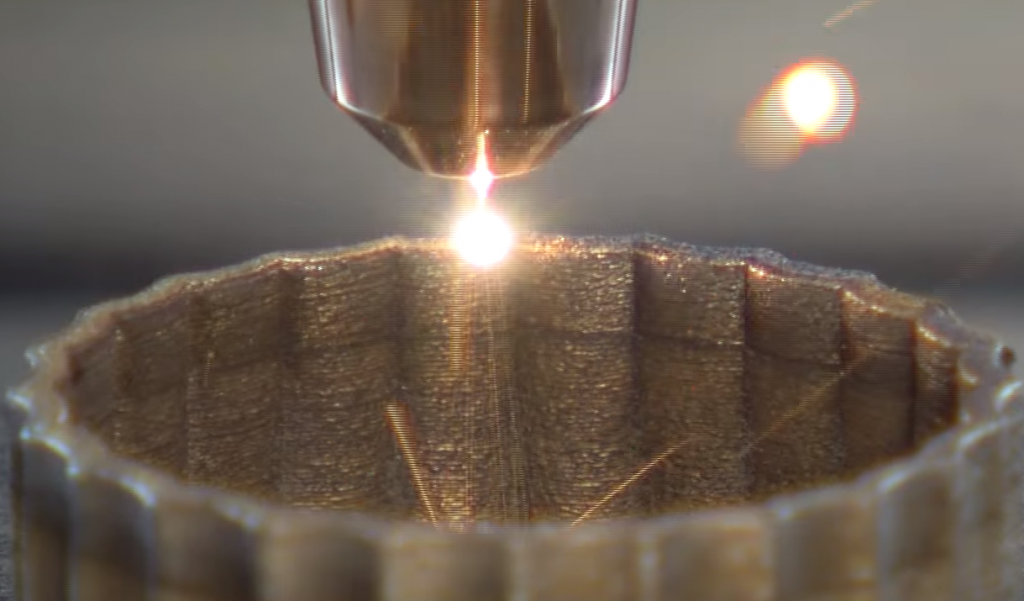
[Gambar milik Teknologi Manufaktur Hibrida ]
Direct Energy Deposition (DED) bekerja dengan melelehkan material logam dengan laser atau berkas elektron saat diendapkan melalui nozzle ke platform build. Biasanya, mesin DED memiliki tingkat pengendapan material yang tinggi dan dapat bekerja dengan material logam baik dalam bentuk bubuk atau kawat, sehingga menghasilkan bagian yang sangat padat dengan bentuk yang hampir mendekati jaring.
Berbeda dengan proses Powder Bed Fusion, yang biasanya menghasilkan komponen yang lebih kecil namun sangat akurat, beberapa metode DED eksklusif dapat menghasilkan bagian logam yang lebih besar.
Salah satu contohnya adalah teknologi Electron Beam Additive Manufacturing (EBAM) milik Sciaky milik perusahaan AS, yang dikatakan mampu memproduksi suku cadang yang panjangnya lebih dari 6 meter.
Teknologi DED sangat cocok untuk memperbaiki bagian yang rusak seperti bilah turbin dan sisipan alat cetakan injeksi, yang akan sulit atau tidak mungkin diperbaiki menggunakan metode manufaktur tradisional.
Pengaliran Pengikat Logam
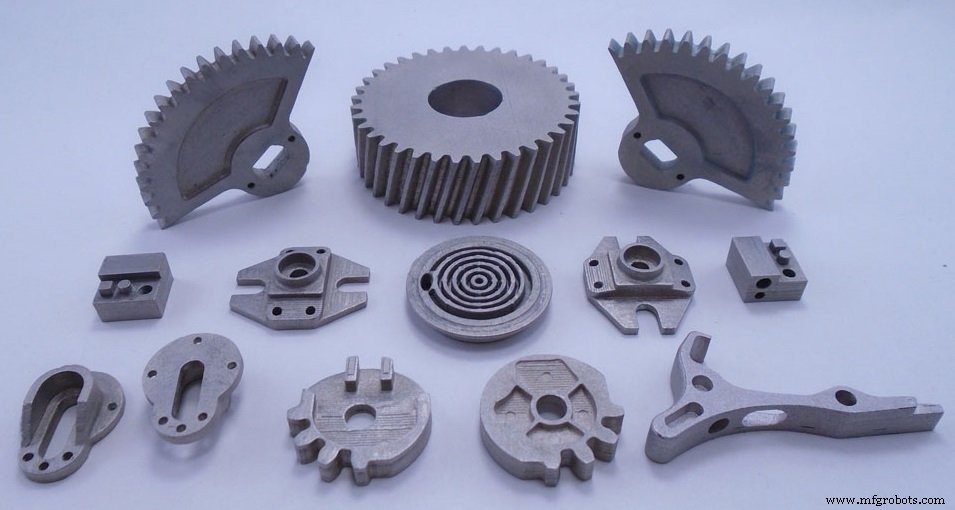
Metal Binder Jetting adalah salah satu teknologi pencetakan 3D logam paling hemat biaya yang tersedia di pasaran.
Mirip dengan pencetakan tinta di atas kertas, Metal Binder Jetting melibatkan penggunaan print head. Kepala cetak ini bergerak di atas platform pembuatan, menyimpan tetesan zat pengikat ke lapisan bubuk logam. Melalui proses ini, partikel logam menyatu menjadi satu bagian.
Beberapa kepala cetak dapat digunakan untuk mempercepat proses pencetakan.
Mesin Metal Binder Jetting menawarkan kecepatan pencetakan yang lebih cepat dan volume pencetakan yang besar. Mereka juga cenderung jauh lebih murah daripada sistem tempat tidur bubuk.
Namun, karena sifat proses pencetakannya, suku cadang yang diproduksi menggunakan Pengikat Pengikat Logam memiliki sifat mekanis yang terbatas:sangat berpori karena pengikatnya terbakar selama proses pencetakan.
Akibatnya, suku cadang akan membutuhkan pasca-pemrosesan yang signifikan sebelum penggunaan akhir. Langkah-langkah ini termasuk curing, pengerasan bagian, dan sintering dan infiltrasi perunggu untuk mengurangi porositas dan meningkatkan kekuatan.
Laminasi Lembaran Ultrasonik
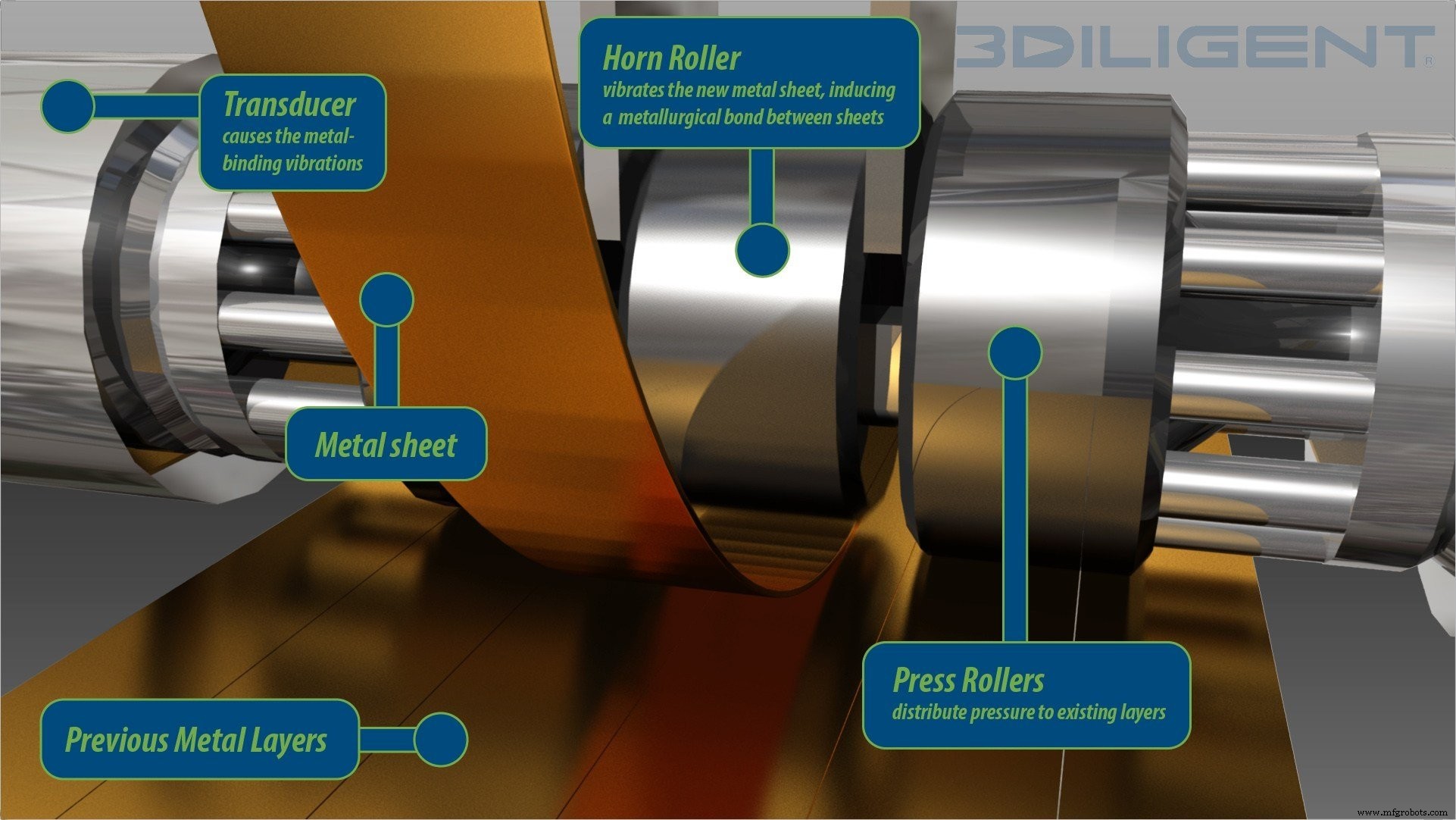
Ultrasonic Sheet Lamination adalah proses manufaktur aditif logam hibrid bersuhu rendah.
Teknologi ini bekerja dengan mengelas foil logam tipis bersama dengan getaran ultrasonik di bawah tekanan. Setelah proses pencetakan selesai, penggilingan CNC diterapkan untuk menghilangkan bahan berlebih dan menyelesaikan bagiannya.
Karena ini adalah proses suhu rendah, Ultrasonic Sheet Lamination tidak melelehkan material logam. Proses ini juga mampu menggabungkan jenis logam yang berbeda menjadi satu.
Keuntungan utama dari teknik ini adalah biayanya yang rendah, kecepatan pencetakan yang cepat, dan kemampuan untuk membuat komponen dengan elektronik dan sensor tertanam dari berbagai logam.
Proses pencetakan 3D logam baru
Dengan evolusi pesat pencetakan 3D logam, produsen perangkat keras terus mencari cara untuk mengembangkan proses baru. Di bawah ini, kami telah menguraikan beberapa teknologi pencetakan 3D logam yang baru dikembangkan yang memiliki potensi untuk merevolusi pencetakan 3D logam, baik dari segi kecepatan maupun biaya.
Pencetakan 3D logam berbasis ekstrusi
Memproduksi suku cadang secara aditif melalui ekstrusi filamen logam adalah pendekatan yang relatif baru.
Dua perusahaan terkemuka yang bekerja di bidang ini adalah Markforged dan Desktop Metal. Kedua perusahaan pertama kali meluncurkan sistem pencetakan 3D logam mereka, (Metal X Markforged dan Sistem Studio Desktop Metal) pada tahun 2017.
Pencetakan 3D logam berbasis ekstrusi bekerja mirip dengan Fused Deposition Modeling (FDM), di mana filamen dipanaskan dan diekstrusi melalui nosel, menciptakan bagian lapis demi lapis.
Namun, tidak seperti filamen plastik yang digunakan dalam FDM, ekstrusi logam menggunakan filamen yang terbuat dari bubuk logam atau pelet yang terbungkus dalam pengikat plastik.
Setelah bagian dicetak, itu tetap dalam 'kondisi hijau' dan perlu menjalani langkah pasca-pemrosesan tambahan:debinding untuk membakar sisa plastik dan sintering untuk menyatukan partikel logam.
Pencetakan 3D logam berbasis ekstrusi adalah salah satu proses manufaktur aditif logam yang paling terjangkau. Ini sebagian karena menggunakan bahan metal-injection-molding (MIM), yang secara signifikan lebih murah daripada bubuk logam yang digunakan dalam proses powder-bed.
Pengaliran Bahan
Material Jetting adalah proses pencetakan inkjet di mana kepala cetak digunakan untuk menyimpan bahan fotoreaktif dalam bentuk cair ke platform pembuatan, lapis demi lapis.
Material Jetting biasanya digunakan sebagai teknologi pembuatan prototipe untuk membuat model plastik penuh warna yang sangat akurat.
Namun, satu perusahaan telah mengakui potensi teknologi untuk pencetakan 3D logam:Perusahaan Israel, XJet, telah mengembangkan teknik inkjetting baru untuk logam yang dapat mencapai tingkat detail dan penyelesaian yang tinggi.
Teknologi NanoParticle Jetting™ (NPJ) XJet menggunakan kepala cetak untuk menyimpan tinta logam yang tersuspensi dalam formulasi cair. Prosesnya berlangsung di ruang berpemanas.
Saat tinta logam diendapkan, mereka diendapkan ke baki bangunan yang panas, menguapkan formulasi cair untuk hanya menyisakan partikel logam. Partikel-partikel tersebut memiliki lapisan kecil zat pengikat, yang memungkinkan mereka untuk mengikat satu sama lain di ketiga sumbu.
Setelah pencetakan selesai, bagian tersebut kemudian dipindahkan ke oven untuk menjalani proses sintering. Teknologi ini dapat digunakan baik untuk pembuatan prototipe fungsional dan pembuatan komponen logam berukuran kecil dan menengah sesuai permintaan.
Metal Jet (HP)
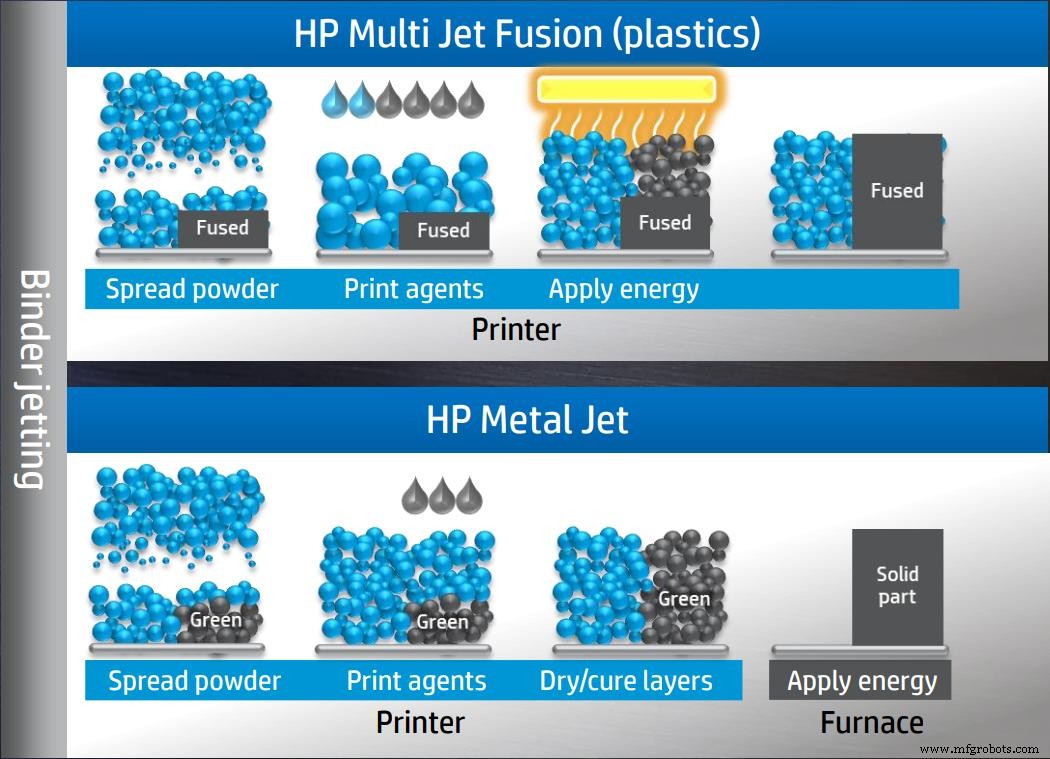
HP pertama kali membuat gelombang dengan pindah ke pasar pencetakan 3D pada tahun 2016, dengan peluncuran sistem Multi Jet Fusion polimer. Pada tahun 2018, perusahaan mengambil teknologi binder jetting satu langkah lebih jauh dengan mengumumkan sistem pencetakan 3D logam barunya:Metal Jet.
Sistem Metal Jet didasarkan pada proses pengaliran binder HP, yang telah ditingkatkan untuk memungkinkan pencetakan yang lebih cepat dan lebih murah.
Meskipun cara kerjanya mirip dengan mesin pengaliran binder lainnya, sistem ini menggunakan binder eksklusif yang dikembangkan dengan bantuan teknologi Tinta Lateks HP. Formulasi pengikat baru ini dikatakan membuatnya lebih cepat, lebih murah dan lebih sederhana untuk mensinter suatu bagian.
Selain itu, Metal Jet menggunakan serbuk Metal Injection Moulding (MIM) dan mampu menghasilkan komponen isotropik yang memenuhi standar ASTM.
Salah satu fitur utama dari teknologi ini adalah peningkatan jumlah printhead, yang dikatakan membuat Metal Jet hingga 50 kali lebih produktif daripada mesin pengikat dan laser sintering yang sebanding di pasaran saat ini.
Pencetakan Joule (Paduan Digital)
Meskipun rilis komersialnya tidak akan sampai tahun 2020, teknologi Joule Printing yang dipatenkan Digital Alloys adalah proses pencetakan 3D logam lain yang layak disebutkan di sini.
Joule Printing adalah teknologi berkecepatan tinggi yang menggunakan kawat logam sebagai pengganti bubuk.
Kawat logam dimasukkan ke dalam sistem gerak presisi dengan umpan kawat presisi. Setelah kawat diposisikan, arus dilewatkan melalui kawat dan selanjutnya ke alas cetak dan bagian itu sendiri. Kawat logam dilelehkan oleh arus saat kepala cetak bergerak, dengan tetesan logam menyatu untuk membentuk bagian akhir.
Teknologi Joule Printing dikatakan memungkinkan produksi suku cadang berbentuk hampir bersih dan dapat digunakan untuk perkakas dan aplikasi lain dalam industri otomotif, dirgantara, dan barang konsumsi.
MELD (Manufaktur MELD)
MELD Manufacturing Corporation telah mengembangkan proses pencetakan 3D logam solid-state baru untuk memproduksi suku cadang logam. Itu solid-state berarti prosesnya tidak memerlukan peleburan bahan logam selama proses pencetakan.
Sebaliknya, prosesnya melibatkan melewatkan material logam melalui alat berongga yang berputar, di mana tekanan dan gesekan ekstrem bekerja untuk mengubah bentuk material yang ditambahkan, serta material yang telah diendapkan.
Proses tersebut memastikan bahwa suku cadang yang dihasilkan memiliki kekuatan dan sifat mekanik yang tinggi, seperti ketahanan terhadap korosi.
Bagian yang dicetak dengan teknologi MELD sangat padat dan tidak memerlukan perlakuan panas berikutnya. Selain itu, teknologi ini tidak hanya cocok untuk membuat suku cadang, tetapi juga untuk melapisi dan memperbaiki komponen yang ada.
Membuat Kasus Bisnis untuk Pencetakan 3D Logam
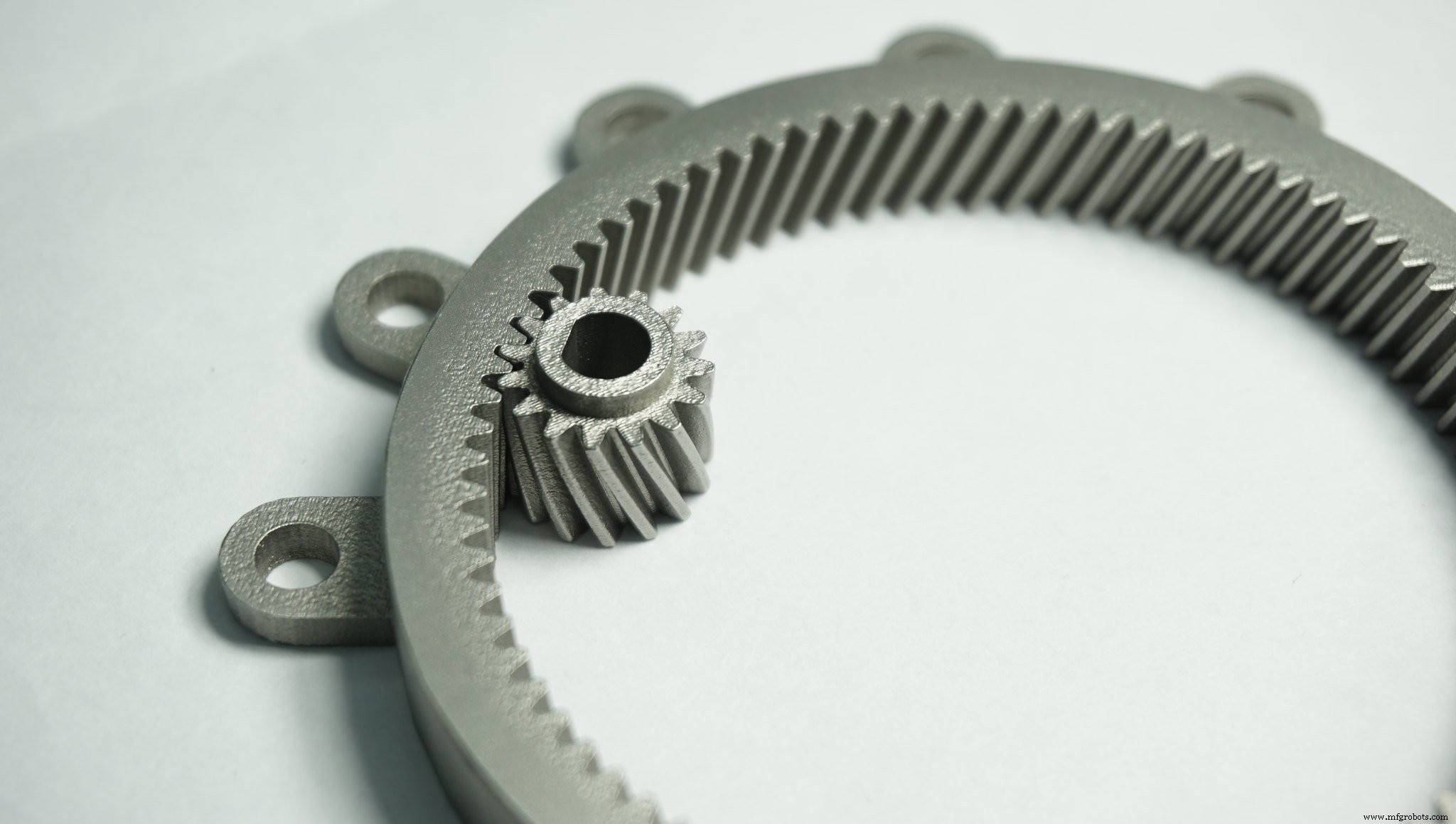
Pencetakan 3D logam berpotensi mengubah cara pembuatan suku cadang dengan memberikan tingkat kerumitan dan penyesuaian yang tidak mungkin dilakukan dengan proses manufaktur tradisional.
Saat memutuskan apakah akan berinvestasi dalam pencetakan 3D logam, penting untuk menilai apakah perusahaan Anda dapat memperoleh manfaat dari teknologi tersebut. Di bawah, kami telah menguraikan beberapa manfaat utama pencetakan 3D logam.
Menghemat waktu dan mengurangi biaya
Pertama, pencetakan 3D menghilangkan kebutuhan akan perkakas dan cetakan yang mahal, memungkinkan produsen untuk menghilangkan biaya penyiapan yang mahal dan memakan waktu. Kedua, kemampuan untuk beralih dari desain ke produksi dapat secara signifikan memangkas waktu tunggu dari berminggu-minggu atau berbulan-bulan menjadi berhari-hari.
Terakhir, kemampuan untuk menggabungkan rakitan komponen dengan pencetakan 3D dapat membantu menghemat waktu dan biaya tenaga kerja secara signifikan.
Mengurangi limbah material
Metode manufaktur subtraktif tradisional melibatkan pemborosan material yang ekstensif, dengan satu penelitian menunjukkan bahwa penggunaan mesin penggilingan CNC untuk memotong material dari balok logam dapat menyebabkan pemborosan material hingga 95%.
Sebagai perbandingan, proses pencetakan 3D logam menghasilkan lebih sedikit limbah karena bahan disinter atau dilebur hanya jika diperlukan. Dalam beberapa kasus, bubuk logam yang tidak disinter bahkan dapat digunakan kembali.
Akibatnya, penggunaan material dengan pencetakan 3D menjadi sangat efisien, dengan tingkat scrap material biasanya di bawah 5 persen.
Mencapai inovasi desain yang lebih baik
Pencetakan 3D logam dapat digunakan untuk menghasilkan geometri yang kompleks, mendorong batas-batas dari apa yang mungkin dilakukan dengan manufaktur. Desain kompleks ini dapat diproduksi dengan biaya lebih efektif dibandingkan dengan proses tradisional.
Digabungkan dengan alat desain seperti pengoptimalan topologi dan desain generatif, pencetakan 3D dapat digunakan untuk membuat bagian logam ringan dengan fungsionalitas dan sifat mekanik yang ditingkatkan.
Oleh karena itu, alat desain perangkat lunak ini dapat membantu membuka segudang kemungkinan desain baru yang inovatif. Misalnya, struktur kisi dapat dimasukkan ke dalam desain untuk mengurangi berat bagian logam dan oleh karena itu meningkatkan kinerja kendaraan atau pesawat terbang.
Produksi volume rendah yang hemat biaya
Dengan pencetakan 3D, produksi volume rendah menjadi layak secara ekonomi.
Karena biaya perkakas yang tinggi, metode manufaktur tradisional bisa sangat mahal untuk diterapkan untuk memproduksi suku cadang dalam volume rendah.
Sebaliknya, pencetakan 3D tidak memerlukan perkakas, dan karena itu merupakan pilihan yang lebih hemat biaya untuk produksi volume rendah. Salah satu contoh kuncinya adalah dalam hal suku cadang yang disesuaikan, di mana produk mungkin perlu diproduksi sebagai satu kali produksi atau sebagai bagian dari batch kecil.
Pencetakan 3D juga dapat digunakan untuk membuat suku cadang sesuai permintaan. Misalnya, perusahaan dapat mencetak alat dan suku cadang 3D secara internal sesuai kebutuhan — yang keduanya mengurangi kebutuhan untuk menimbun suku cadang dalam inventaris fisik dan menyederhanakan logistik dan keseluruhan rantai pasokan.
Tantangan Pencetakan 3D Logam
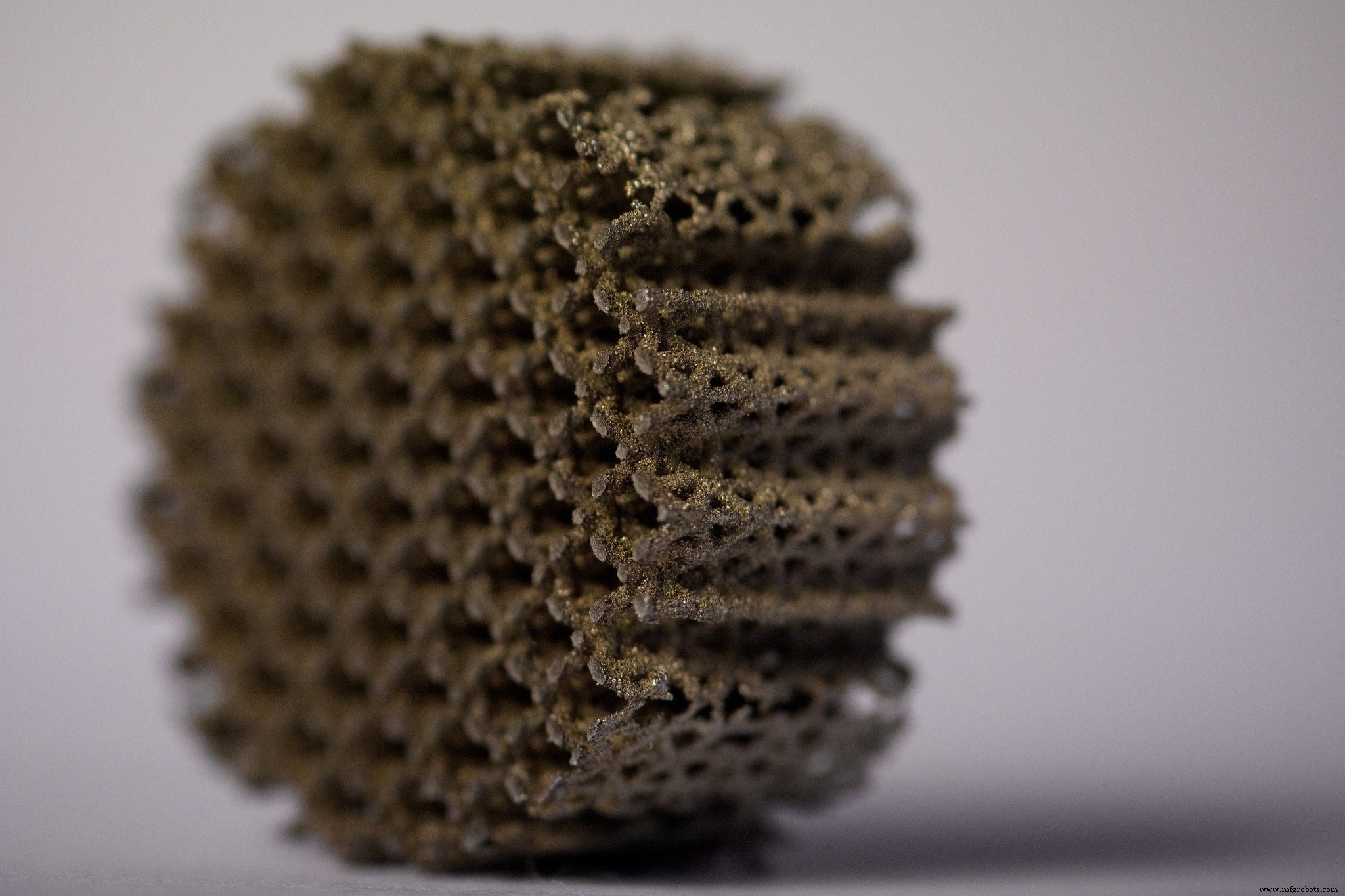
Sementara manfaat pencetakan 3D logam jelas, ada tantangan untuk berhasil menerapkan teknologi tersebut. Di bawah ini, kami membahas beberapa tantangan utama yang saat ini dihadapi pasar pencetakan 3D logam.
Biaya tinggi
Meskipun harga printer 3D telah turun secara signifikan selama dekade terakhir, biaya sistem AM logam masih tetap menjadi salah satu tantangan utama bagi perusahaan yang ingin berinvestasi dalam teknologi.
Saat ini, printer 3D logam dapat dengan mudah berharga ratusan ribu dolar dan bahkan lebih dari $ 1 juta.
Pada saat yang sama, bahan logam saat ini yang tersedia di pasar umumnya cukup terbatas, dengan biaya yang jauh lebih tinggi daripada logam yang digunakan dalam pembuatan logam tradisional.
Meskipun demikian, selama beberapa tahun ke depan, kami berharap kemajuan dalam ilmu material logam akan memperluas pilihan logam yang dapat dicetak 3D dan menurunkan biaya.
Kompleksitas yang lebih besar
Berbagai variabel yang terlibat dalam pencetakan 3D logam menjadikannya proses yang jauh lebih kompleks daripada pencetakan 3D polimer. Saat ini, banyak perusahaan tidak memiliki keahlian yang diperlukan untuk berhasil mengoperasikan printer 3D logam secara internal.
Salah satu cara yang mungkin untuk memulai teknologi ini adalah melalui kolaborasi dengan penyedia layanan pencetakan 3D logam. Biro layanan dapat menawarkan keahlian mereka dalam memilih teknologi dan material AM logam yang tepat.
Bagi perusahaan yang ingin membawa teknologi AM secara internal, mengembangkan dan menerapkan strategi AM akan menjadi langkah pertama yang penting dalam perjalanan ini.
Memastikan kualitas suku cadang
Kualitas bagian dan pengulangan proses adalah perhatian utama bagi produsen. Ketika berbicara tentang pencetakan 3D logam, ada berbagai variabel yang dapat mempengaruhi kualitas suatu bagian. Variabel ini mencakup seluruh alur kerja AM, mulai dari desain hingga persiapan build dan pasca-pemrosesan.
Namun, mengendalikan variabel-variabel ini untuk mengaktifkan bagian logam berkualitas tinggi yang dapat diulang tetap menjadi tantangan.
Bahan
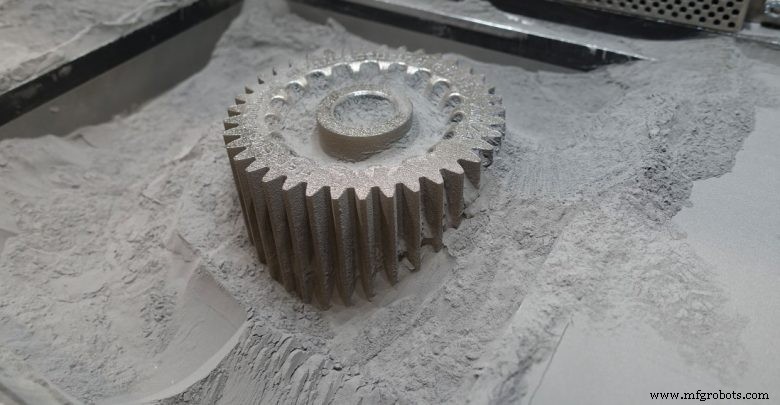
Logam telah menjadi segmen pasar bahan cetak 3D yang tumbuh paling cepat sejak 2012.
Proses pencetakan 3D logam menggunakan bahan logam berkualitas tinggi. Mereka biasanya diproduksi dalam bentuk bubuk dan harus memenuhi karakteristik tertentu, seperti bentuk dan ukuran partikel, dan kepadatan bubuk.
Dibandingkan dengan proses manufaktur tradisional, kisaran logam cetak 3D yang tersedia masih terbatas.
Hal ini disebabkan oleh fakta bahwa bahan khusus yang diadaptasi atau diproduksi untuk teknologi pencetakan 3D logam membutuhkan waktu bertahun-tahun untuk dikembangkan.
Namun, beberapa proses seperti DED dapat menggunakan logam yang awalnya dikembangkan untuk proses tradisional, misalnya, dalam bentuk kawat.
Saat ini, bahan yang paling umum digunakan untuk pencetakan 3D logam termasuk logam ringan seperti aluminium, titanium, dan baja tahan karat.
Namun, penggunaan logam tahan api dan paduan krom kobalt juga berkembang, sebagian besar didorong oleh aplikasi di industri kedirgantaraan dan minyak &gas.
Pada tabel di bawah, kami telah mengidentifikasi bahan cetak 3D logam yang lebih umum dan aplikasi tipikalnya.
Materi | Deskripsi | Aluminium
(AlSi10Mg, AlSi12, paduan AlSi12Mg, Scalmalloy) Bahan ringan dengan sifat paduan yang baik
Ketahanan korosi yang tinggi
Pemrosesan akhir yang mudah (misalnya untuk mesin, pengelasan, dan pemolesan)
Rasio kekuatan-terhadap-berat yang tinggi
Ketahanan suhu tinggi dan konduktivitas termal dan listrik
Aplikasi Utama:Aluminium dapat digunakan untuk memproduksi bagian-bagian yang ringan dan kompleks secara geometris dan terutama digunakan dalam industri otomotif dan dirgantara.
Titanium
Titanium murni (Kelas 1 dan 2)
Paduan titanium Ti6Al4V (Kelas 5)
Paduan titanium Ti 6AL-4V ELI (Kelas 23) Biokompatibilitas yang sangat baik
Kekuatan dan ketangguhan yang baik
Ketahanan korosi yang tinggi
Kepadatan tinggi
Aplikasi Utama:Titanium sangat cocok untuk motorsport, penerbangan dan aplikasi medis/gigi.
Baja tahan karat
(paduan 17-4PH dan 316L) Kekerasan dan ketangguhan tinggi
Ketahanan tinggi terhadap korosi
Kemampuan las yang baik
Daktilitas tinggi
Alternatif yang lebih murah untuk titanium atau nikel
Aplikasi Utama:Baja tahan karat khususnya telah ditemukan di industri kedirgantaraan, minyak &gas, pengolahan makanan, dan medis.
Cobalt chromium alloy (CoCrMo) Kekuatan luar biasa
Ketahanan korosi yang tinggi
Tahan suhu
Non-magnetik
Biokompatibel
Aplikasi Utama:Medis (bedah implan sebagai sendi buatan termasuk sendi lutut dan pinggul) dan gigi. Logam ini juga telah digunakan untuk memproduksi suku cadang untuk turbin gas dan angin, serta komponen mesin.
Paduan nikel (Inconel 625, Inconel 713, Inconel 718, Inconel 738, Hastelloy X) Ketahanan korosi yang tinggi
Kekuatan dan ketangguhan luar biasa pada suhu yang lebih tinggi
Kemampuan las yang sangat baik
Aplikasi Utama:Paduan nikel ideal untuk aplikasi bersuhu tinggi dalam ruang angkasa, proses kimia dan industri tenaga, serta bilah turbin gas mesin jet.
Paduan berbahan dasar tembaga Konduksi termal dan listrik yang sangat baik
Kekakuan yang baik
Aplikasi Utama:aplikasi manajemen termal (mis. penukar panas mikro), teknik elektro, sisipan pahat
Baja maraging (baja perkakas) Kekuatan, kekerasan, dan kelenturan tinggi (dapat diberi perlakuan panas tambahan untuk meningkatkan kekerasan dan stabilitas)
Aplikasi Utama:Perkakas (inti dan sisipan alat die casting dan cetakan injeksi), prototipe fungsional
Logam tahan api (tantalum, niobium, dan tungsten) Kekerasan tinggi
Tahan panas dan aus
Ketahanan korosi yang tinggi
Inert secara kimia
Stabilitas termal tinggi
Biokompatibilitas tinggi
Toksisitas rendah (tantalum)
Aplikasi Utama:Kelompok logam ini berharga untuk aplikasi tegangan tinggi seperti nozel, katup, dan manifold pendorong rudal dan roket; implan (tantalum)
Logam mulia (emas, perak, platinum) ulet
Konduktif
Relatif mudah untuk pascaproses (misalnya untuk mesin, enamel, dan poles)
Menantang untuk mencetak 3D secara langsung. Biasanya diproses hanya dengan DMLS/SLM
Aplikasi utama:Logam mulia digunakan untuk aplikasi khusus seperti aksesori (perhiasan dan jam tangan), gigi (mahkota, tatahan, dan onlay)
Mesin
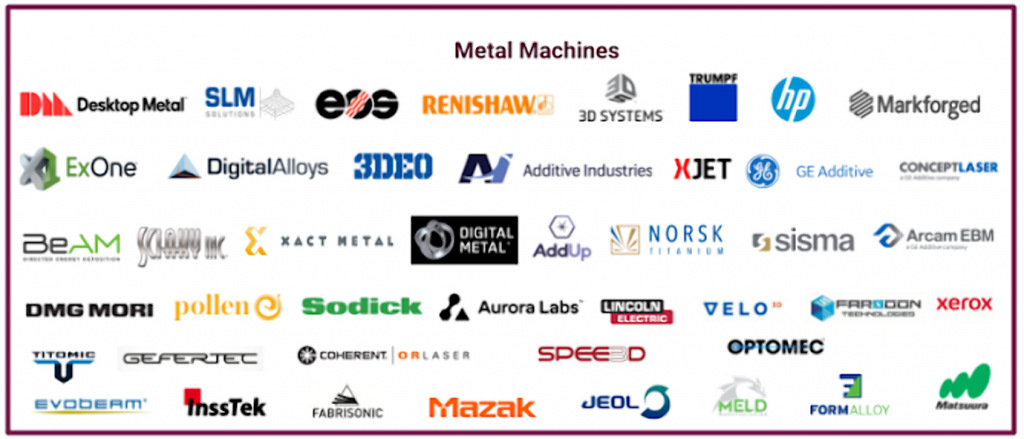
Dengan meningkatnya pencetakan 3D logam, jumlah printer 3D logam yang tersedia di pasar bertambah.
Menurut Laporan Wohlers 2018, penjualan sistem AM logam tumbuh sebesar 80% pada tahun 2017, dengan peningkatan jumlah produsen sistem AM logam yang memasuki pasar.
Dalam tabel yang tersedia untuk diunduh, kami telah merangkum produsen utama printer 3D logam, menggunakan teknologi powder-bed, DED, Binder Jetting, dan pencetakan 3D logam berbasis ekstrusi. Meskipun bukan daftar yang lengkap, ini memberikan gambaran umum tingkat tinggi dari produsen mesin utama di pasar.
Teknologi | Produsen | Nama Sistem | Volume Bangun (mm) | Materi yang kompatibel | Sistem DMLS &SLM3DDMP Flex 100100 x 100 x 80 mmLaserForm 17-4PH (B),
LaserForm CoCr (B) atau (C) Sistem DMLS &SLM3DProX DMP 200140 x 140 x 100 mmLaserForm Ni625 (B)
LaserForm 17-4PH (B)
LaserForm Maraging Steel (B)
LaserForm 316L (B)
LaserForm CoCr (B) atau (C)
LaserForm AlSi12 (B) DMLS &SLM3D SystemsProX DMP 300250 x 250 x 300 mmLaserForm 17-4PH (B),
LaserForm Maraging Steel (B),
LaserForm CoCr (B)
LaserForm AlSi12 (B)
( Paduan kobalt Chrome, Baja tahan karat, Baja Maraging, Paduan aluminium (AlSi12)) Sistem DMLS &SLM3DProX DMP 320275 x 275 x 380 mmLaserForm Maraging Steel (A)
LaserForm 17-4PH (A)
LaserForm Ni625 ( A)
LaserForm AlSi10Mg (A)
LaserForm CoCrF75 (A)
LaserForm Ti Gr5 (A)
LaserForm Ti Gr23 (A)
LaserForm Ti Gr1 (A)
LaserForm 316L (A)
LaserForm Ni718 (A)
(Paduan titanium, Aluminium, Paduan nikel, Baja tahan karat, Krom Cobalt, Baja Maraging) Sistem DMLS &SLM3DDMP Factory 500 Solution500 x 500 x 500mm DMLS &SLMEOSEOS M 100100 mm x 95 mmCobalt Chrome
Stainless Steel 316L
Titanium Ti64 DMLS &SLMEOSEOS M 290250 x 250 x 325 mmAluminium
Cobalt Chrome
Baja Maraging
Paduan Nikel
Paduan Baja Tahan Karat
Paduan Titanium dan Titanium DMLS &SLMEOSEOS M 400400 x 400 x 400 mmAluminium, Baja Maraging, Paduan Nikel, Paduan Titanium DMLS &SLMEOSEOS M 400-4400 mm x 400 mm x 400 mmAluminium, Paduan Nikel, Baja Maraging, Baja Tahan Karat, Titanium Ti64, Titanium Grade 2 DMLS &SLMEOSEOSINT M 280250 mm x 250 mm x 325 mmEOS MaragingSteel MS1
EOS CobaltChrome MP1
EOS StainlessSteel GP1
EOS StainlessSteel PH1
EOS StainlessSteel 316L
EOS Titanium Ti64
EOS Titanium Ti64ELI
EOS Aluminium AlSi10Mg
EOS NickelAlloy IN718
EOS NickelAlloy IN625
EOS NickelAlloy HX DMLS &SLMEOSPRECIOUS M 08080 x 80 x 95 mmPaduan emas, perak, platinum, dan paladium DMLS &SLMRenishawRenAM250250 mm x 250 m m x 300 mmTi6Al4V ELI
AlSi10Mg
Baja tahan karat 316L
Baja perkakas
Paduan nikel
Paduan kromium kobalt. DMLS &SLMRenishawRenAM400250 mm × 250 mm × 300 mmTi6Al4V ELI
AlSi10Mg
Baja tahan karat 316L
Baja perkakas
Paduan nikel
Paduan kromium kobalt. DMLS &SLMRenishawRenAM 500M250 mm × 250 mm × 350 mmTi6Al4V ELI
AlSi10Mg
Baja tahan karat 316L
Baja perkakas
Paduan nikel
Paduan kromium kobalt. DMLS &SLMRenishawRenAM 500Q250 mm x 250 mm x 350 mmTi6Al4V ELI
AlSi10Mg
Baja tahan karat 316L
Baja perkakas
Paduan nikel
Paduan kromium kobalt. Solusi DMLS &SLMSLMSLM 125125 x 125 x 75Stainless Steel
Baja Perkakas
Cobalt-Chromium
Inconel
Aluminium
Titanium Solusi DMLS &SLMSLMSLM 280 2.0280 x 280 x 350Stainless Steel
Baja Perkakas,
Cobalt-Chromium
Paduan Super
Aluminium
Titanium Solusi DMLS &SLMSLMSLM 500500 x 280 x 325Paduan aluminium
Stainless Steel
Alat Baja
Titanium
Inconel
Cobalt-Chrome DMLS &SLMConcept Laser (GE Additive)Mlab cusing50 x 50 x 80 mmStainless steel
Perunggu
Emas
Paduan perak
Cobalt-chromium alloy DMLS &SLMConcept Laser (GE Additive)Mlab menggunakan R50 x 50 x 80 mmStainless steel
Perunggu
Emas
Paduan perak
Paduan kobalt-kromium
Titanium dan paduan titanium DMLS &SLMConcept Laser (GE Additive)Mlab menggunakan 200R100 x 100 x 100 mmBaja tahan karat
Aluminium
Paduan titanium
Titanium Murni Komersial Grade 2
Baja Maraging
Perunggu
Baja tahan karat,
Paduan berbahan dasar nikel
Cobalt-chromium alloy DMLS &SLMConcept Laser (GE Additive)M1 cusing250 x 250 x 250 mmStainless steel
Maraging tool steel,
Stainless tool steel
Paduan berbasis nikel
Paduan kobalt-kromium DMLS &SLMConcept Laser (GE Additive)M2 cusing250 x 250 x 350 mmBaja tahan karat
Paduan aluminium
Paduan titanium
Titanium Murni Grade 2
Baja Maraging
Baja pengerasan presipitasi tahan korosi
Baja tahan karat pengerasan presipitasi
Paduan berbasis nikel
Paduan kobalt-kromium DMLS &SLMKonsep Laser (GE Additive)M2 cusing Multilaser250 x 250 x 350 mmStainless steel
Paduan aluminium
Paduan titanium
Titanium Murni
Baja Maraging
Baja pengerasan presipitasi
Paduan berbasis nikel
Paduan kobalt-kromium DMLS &SLMConcept Laser (GE Aditif)Pabrik M LINE500 x 500 x hingga 400 mmPaduan aluminium
Paduan titanium
Paduan berbasis nikel
Paduan kobalt-kromium DMLS &SLMConcept Laser (GE Additive )X LINE 2000R800 x 400 x 500 mmAluminium (AlSi10Mg)
Paduan titanium (TiAl6V4)
Paduan berbasis nikel EBMArcam (GE Additive)Arcam EBM A2X200x200x380 mmTiAl,
Nikel Alloy 718 EBMArcam (GE Additive )Arcam EBM Q10plus200 x 200 x 180mmTitanium Ti6Al4V
Cobalt-Chrome EBMArcam (GE Additive)Arcam EBM Q20plus350 x 380mmTitanium Ti6Al4V
Cobalt-Chrome EBMArcam (GE Additive)Arcam EBM Spectra H250 x 250 x 430mmTitanium )
Paduan 718. DMLS &SLMSismamysint100100 mm x h100 mmCobalt Chrome
Logam mulia
Perunggu
Paduan baja
Paduan nikel
Tembaga murni
Tembaga paduan
Titanium
Paduan aluminium DMLS &SLMSismamysint300300 x 400 mmLogam Mulia
Perunggu
Krom Kobalt
Stainless Steel
Baja Maraging
Paduan nikel
Paduan aluminium
Titanium DMLS &SLMDMG MoriLASERTEC 30 SLM 2nd Gen.300 x 300 x 300mmAluminium
Titanium
Baja perkakas
Cobalt-chrome
Inconel DMLS &SLMXact MetalXM200C127x 127 x 127 mmStainless Steel,
Super Alloys,
Cobalt Chrome,
Hastelloy® X,
Baja Perkakas DMLS &SLMXact MetalXM200S127 x 127 x 127 mmAluminum Si10Mg,
Perunggu,
Baja Tahan Karat,
Paduan Super,
Krom Kobalt,
Hastelloy® X,
Titanium Ti64,
Baja Perkakas DMLS &SLMXact MetalXM300C254 x 330 x 330 mmStainless Steel,
Super Alloys,
Cobalt Chrome,
Hastelloy® X,
Tooling Steels,
Bronze DMLS &SLMAddUpFormUp™ 350350 x 350 x 350 mmBaja tahan karat ,
Baja Maraging,
Paduan Nikel,
Paduan Titanium,
Paduan Aluminium DMLS &SLMTRUMPFTruPrint Tinggi 1000100 mm x 100 mmBaja tahan karat,
Baja perkakas,
Aluminium,
Berbasis Nikel,
Krom kobalt,
Tembaga,
Titanium,
Paduan logam mulia DMLS &SLMTRUMPFTruCetak Tinggi 3000300 mm x 400 mmBaja tahan karat,
Baja perkakas,
Aluminium,
Berbasis nikel,
Krom kobalt,
Tembaga,
Titanium,
Pra paduan logam mulia
Perunggu DMLS &SLMTRUMPFTruCetak Tinggi 5000300 mm x 400 mmBaja tahan karat,
Baja perkakas,
Aluminium,
Berbasis nikel,
Krom kobalt,
Tembaga,
Titanium,
Paduan logam mulia DMLS &SLMVELO3DSapphire315 mm diameter x 400 mmInconel 718, Titanium (6Al4V) DEDSciakyEBAM® 68711 x 635 x 1600 mmTitanium
Paduan titanium
Inconel 718, 625,
Tantalum,
Tungsten,
Niobium,
Baja Tahan Karat (seri 300),
Aluminium,
Baja Zirkal,
Copper Nickel,
Nickel Copper DEDSciakyEBAM® 881219 x 89 x 1600 mmTitanium
Titanium alloys
Inconel 718, 625,
Tantalum,
Tungsten,
Niobium,
Stainless Steels (300 series),
Aluminum,
Steel Zircalloy,
Copper Nickel,
Nickel Copper DEDSciakyEBAM® 1101778 x 1194 x 1600 mmTitanium
Titanium alloys
Inconel 718, 625,
Tantalum,
Tungsten,
Niobium,
Stainless Steels (300 series),
Al uminum,
Steel Zircalloy,
Copper Nickel,
Nickel Copper DEDSciakyEBAM®1502794 x 1575 x 1575 mmTitanium, Titanium alloys, Inconel 718, 625, Tantalum, Tungsten, Niobium, Stainless Steels (300 series),
Aluminum, Steel Zircalloy, Copper Nickel, Nickel Copper DEDSciakyEBAM® 3005791 x 1219 mm x 1219 mmTitanium, Titanium alloys, Inconel 718, 625, Tantalum, Tungsten, Niobium, Stainless Steels (300 series),
Aluminum, Steel Zircalloy, Copper Nickel, Nickel Copper DEDOptomecLENS 450100 x 100 x 100 mmTitanium, Nickel, Tool Steel, Stainless Steel, Refractories, Composites, Cobalt, Aluminium, Copper DEDOptomecLENS MR-7300 x 300 x 300 mmTitanium, Nickel, Tool Steel, Stainless Steel, Refractories, Composites, Cobalt, Aluminium, Copper DEDOptomecLENS 850-R900 x 1500 x 900 mmTitanium, Nickel, Tool Steel, Stainless Steel, Refractories, Composites, Cobalt, Aluminium, Copper DEDOptomecLENS 860 Hybrid860 x 600 x 610 mmTitanium, Stainless Steel, Tool Steel, Inconel DEDOptomecLENS C S 600600 x 400 x 400 mmInconel Alloys, Stainless Steels, Titanium Alloys DEDOptomecLENS CS 800800 x 600 x 600 mmInconel Alloys, Stainless Steels, Titanium Alloys DEDBeAMModulo 250400 x 250 x 300Titanium Alloys, Steels, Nickel Alloys, Cobalt Alloys, and more DEDBeAMModulo 400650 x 400 x 400Titanium Alloys, Steels, Nickel Alloys, Cobalt Alloys, and more DEDBeAMMagic 8001200 x 800 x 800Titanium Alloys, Steels, Nickel Alloys, Cobalt Alloys, and more DEDInnsTekMX-600450 x 600 x 350 mmInconel, Steel DEDInnsTekMX-10001,000 x 800 x 650 mmInconel, Steel DEDInnsTekMX-Grande4,000 X 1,000 X 1,000 mmInconel, Steel DEDDMG MoriLASERTEC 65 3D735 x 650 x 560 mm Metal Binder JettingExOneM-Flex400 x 250 x 250 mmStainless steel, bronze, tungsten Metal Binder JettingExOneM-Print800 x 500 x 400 mmStainless steel (420 and 316) Metal Binder JettingExOneInnovent+160 x 65 x 65 mmStainless steel Metal Binder JettingExOneX1 25 PRO400 x 250 x 250 mmSteel (136L, 304 L and 17-4PH), Stainless steels, Inconel 718 and 625, M2 and H11 tool steels, Cobalt chrome, Copper, Tungsten carbide cobalt Metal Binder JettingDigital MetalDM P2500203 x 180 x 69 mmStainless steel (316L, 17-4PH), Titanium Ti6Al4V Metal Binder JettingHPMetal Jet430 x 320 x 200 mmStainless steel powders (developed for metal injection molding) Metal Binder JettingDesktop MetalProduction System337 x 337 x 330 mmAluminium, titanium, high-performance alloys Material ExtrusionDesktop MetalStudio System300 x 200 x 200 mmAlloy steel, Aluminium Carbide, Copper, Heavy alloy, High performance steel, Magnetics, Stainless steel, Super alloy, Titanium, Tool steel Material ExtrusionMarkforgedMetal X300 x 220 x 180 mmStainless Steel, Aluminum, Tool Steel, Inconel, Titanium
Industrial Applications
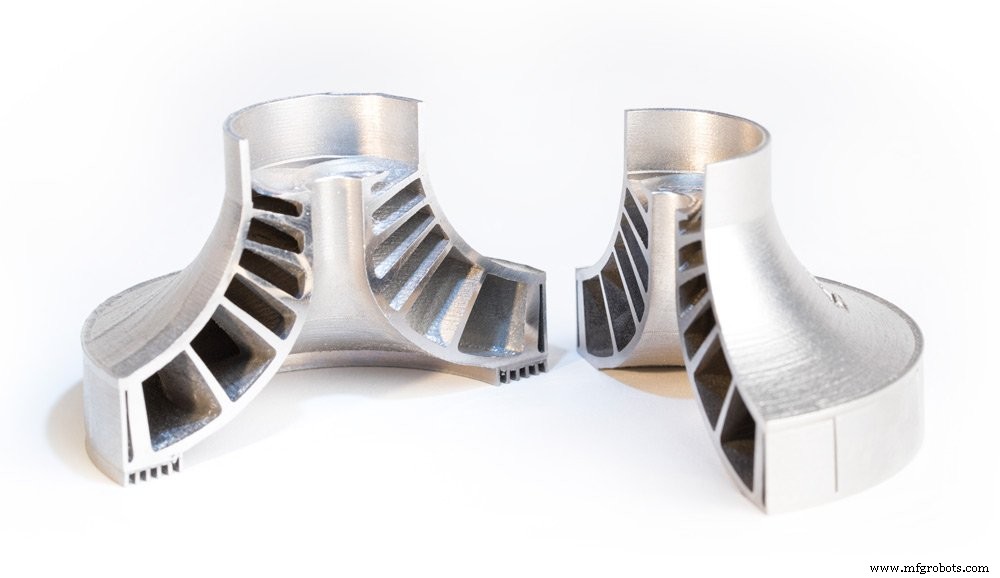
Metal 3D printing has found its niche in a number of industries, with players in the aerospace, automotive and medical industries at the forefront of driving innovation with the technology.
In this section, we take a look at the most common applications for the technology, as well as key use cases that have unlocked the benefits of metal 3D printing.
Industry | Common applications | Aerospace Fuel injectors, blades, combustor liners, rocket engine manifolds, brackets, functional prototypes Automotive Air ducts, brackets, uprights, knuckles, turbochargers, suspension assemblies, transmission plates, brake calipers, manifolds Medical and dental Custom-fit dental restorations, such as stages, crowns, and bridges; customised orthopaedic implants (hip, knee, and spinal), surgical tools Industrial goods Tool inserts with conformal cooling channels, industrial pump components, bearings, stators, heat exchangers, impellers, tooling repair
Aerospace
The aerospace industry has been a huge pioneer of metal 3D printing. By using the technology, aerospace companies hope to produce more efficient, lightweight aircraft parts to improve aircraft performance.
Within the aerospace industry, metal 3D printing is used in a range of applications, from functional prototypes to tooling, replacement parts and structural aircraft components.
General Electric
A great example is General Electric (GE), which is extensively using metal 3D printing to make and develop new products. GE’s subsidiary, GE Aviation, is producing fuel nozzles for the LEAP family of jet engines, with an aim to manufacture 100,000 fuel nozzles by 2020.
Having achieved the milestone of 30,000 3D-printed fuel nozzles in October 2018, GE looks like it’s well on its way to fulfilling this goal.
Using advanced design tools and Electron Beam Melting technology, GE’s engineers were able to create a fuel nozzle 25% lighter and 15% more fuel efficient than its traditionally produced counterpart.
The breakthrough in this case is that the fuel nozzle was printed as a single unit, whereas previous models incorporated 20 separate parts which needed to be subsequently assembled.
But GE has not stopped here. The company is also building its GE Catalyst, an advanced turboprop engine that has more than a third of its components 3D printed in various metals.
Similar to its fuel nozzles, the engineers behind the turboprop have achieved considerable part consolidation, reducing the number of parts produced from 855 to just 12. A redesign will also help to reduce the fuel burn of an engine by as much as 20%.
Automotive
Automakers have been using 3D printing since the technology’s early days — Ford Motor Company, for example, notably bought the third 3D printer ever made.
For many years, metal 3D printing has proved to be a cost-effective tool for prototyping and producing jigs and fixtures. However, advancements with the technology mean that more opportunities are opening up for end-part production.
Automotive companies can use metal 3D printing to create lightweight metal parts, leading to enhanced vehicle performance and lower fuel consumption. This is particularly beneficial for the motorsports industry, where 3D-printed car parts can offer racing teams significant performance advantages.
Another area of interest for the industry is also using 3D printing to produce spare parts that are typically produced in low volumes. 3D printing spare parts on demand enables automakers to receive parts at the point of need, reducing inventory costs and increasing agility.
BMW
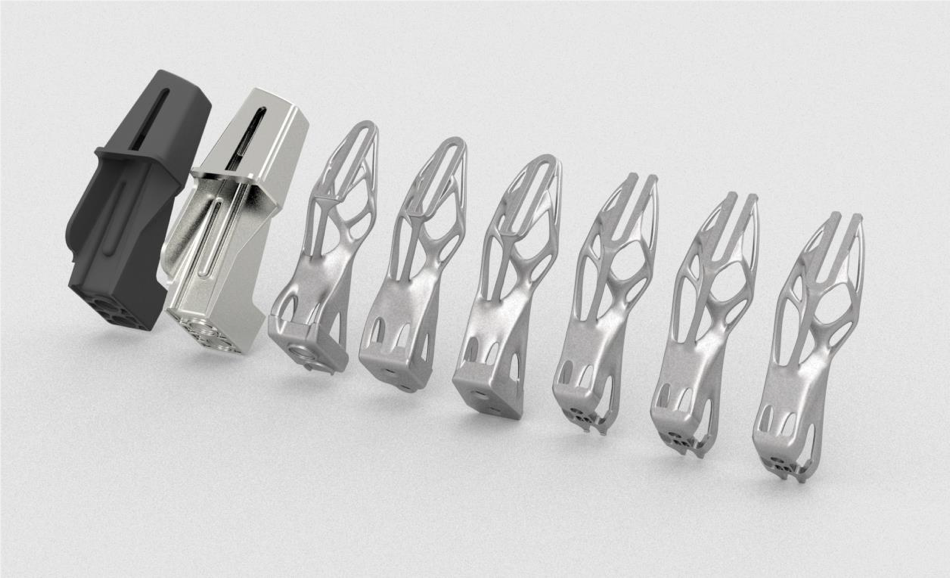
BMW is another company using 3D printing extensively. Most notably, the company has recently moved into the series production of a 3D-printed metal component for its 2018 BMW i8 Roadster vehicle.
Using topology optimisation, designers were able to optimise the vehicle’s roof bracket — a fixture for the folding/unfolding mechanism of the vehicle’s soft top. 3D printed in aluminium alloy powder (AlSi10Mg), the new roof bracket is 44% lighter than its conventionally made counterpart.
Furthermore, engineers optimised the design of the bracket to eliminate support structures. By doing so, the team was able to increase throughput from 51 to 238 of these parts per platform. This makes BMW’s roof bracket the first automotive component to be mass-produced with the help of metal 3D printing.
Bugatti
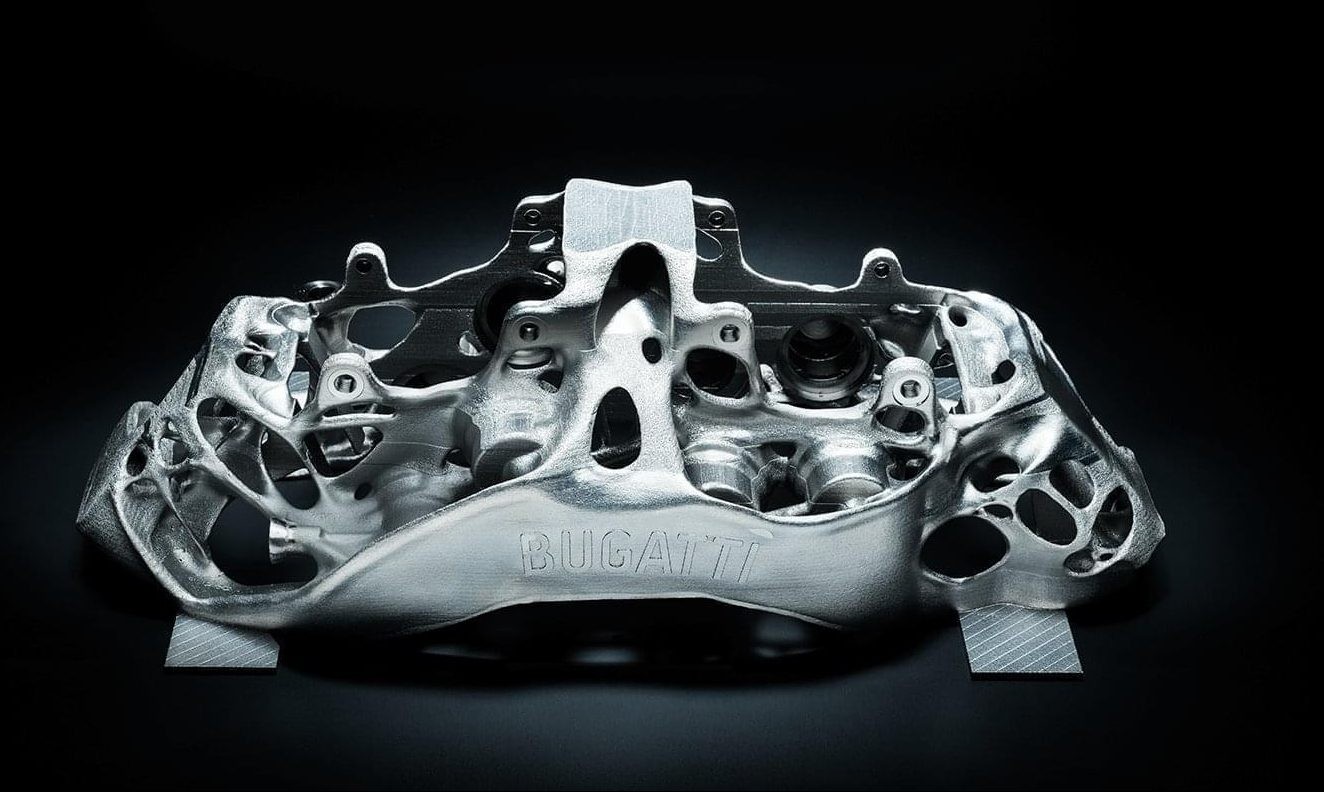
An exciting application of metal 3D printing comes from luxury car manufacturer, Bugatti. The French automaker has developed a 3D-printed brake caliper to be used on its Bugatti Chiron supercar.
An essential part of the braking system, the brake caliper has been made lighter and stronger thanks to 3D printing. Measuring 41 x 21 x 13.6 cm, the part took 45 hours to print using SLM technology and titanium powders.
By using 3D printing, Bugatti also achieved a 40% weight reduction for the caliper, when compared to machined aluminium alternative.
In 2018, the company successfully tested the brake caliper, proving that it can meet extreme strength, stiffness and temperature requirements.
Audi
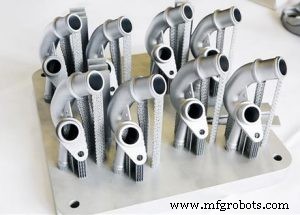
Audi presents a different business case for metal 3D printing. In this case, the German automaker is using the technology to produce spare parts that are in low demand.
Metal 3D printing allows Audi to produce these parts on demand, producing and supplying spare parts as they are needed. This in turn greatly simplifies logistics and warehousing.
Audi identified that smaller, complex components would be most suited for metal 3D printing. A good example of a component is water adapters, which Audi is already producing for the Audi W12 engine. The company says that the load capacity of the components is comparable to that of parts manufactured using traditional methods.
Medical
In the medical field, metal 3D printing allows highly customised medical devices, like orthopedic implants, to be created.
It’s far from unusual for off-the-shelf orthopaedic implants to be used for replacement surgeries. However, prefabricated implants can sometimes cause problems after the surgery as they don’t always fit properly.
To avoid this, 3D printing is increasingly being used to create customised, patient-specific implants with improved functionality.
For example, implants can be designed with improved porosity and surface texture, facilitating the growth of the tissue around the implant. This level of complexity can only be achieved with 3D printing. SmarTech Publishing predicts that more than 2 million implants will be 3D printed in metal by 2025.
Additionally, metal 3D printing can be used to create hip and knee joint replacements, cranial reconstruction implants and spinal implants.
Lima Corporate
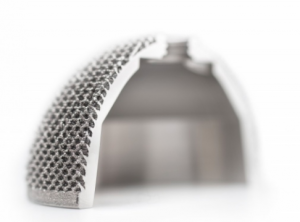
Italian medical device manufacturer Lima Corporate has been bringing additively manufactured hip implants to market for 10 years, using Electron Beam Melting (EBM) technology.
The company developed a technology for 3D printing biocompatible titanium in cellular solid structures that resemble natural bone. Such structures are used to coat an implant, allowing it to be better integrated with human tissue.
The technology is said to have helped almost 100,000 patients, enabling better implant performance and outcomes.
Industrial Goods
When it comes to the design and manufacture of tooling equipment, 3D printing can empower engineers to overcome traditional limitations. This can mean being able to create a mould or core in a matter of days instead of months, significantly reducing lead times.
Within the injection moulding industry, moulds are typically CNC-machined. Here, production costs can range from from $20,000 to hundreds of thousands of dollars. Lead times can last between 2 to 4 months. Additionally, moulds can often require multiple design iterations to achieve the final design, a costly and time-intensive process.
However, metal 3D printing can overcome these inefficiencies in several ways. First, the technology enables rapid design iterations, enabling changes to be made with relative ease.
Second, the performance of tooling aids and components can be enhanced with additive manufacturing.
For example, conformal cooling channels, lattice structures, and complex core/cavity shapes, which are too expensive or impossible to manufacture traditionally, can be factored into a mould design and 3D printed.
Conformal cooling channels are particularly beneficial as they help to achieve more homogenous heat transfer within the mould, compared to traditionally drilled straight-line cooling channels, resulting in greater cooling characteristics.
GW Plastics 3D prints moulds with conformal cooling
GW Plastics, US-based mould maker, has invested in hybrid metal 3D printing with the goal of building injection moulds with conformal cooling. One of the key reasons for this investment is faster cycles and better part quality enabled by 3D-printed moulds.
In fact, the company says 3D-printed moulds can save up to 30% of the cycle time by reducing cooling time. Furthermore, metal 3D printing allows GW Plastics to print a mould as a single piece, thus eliminating the need to assemble multiple components.
Post-processing
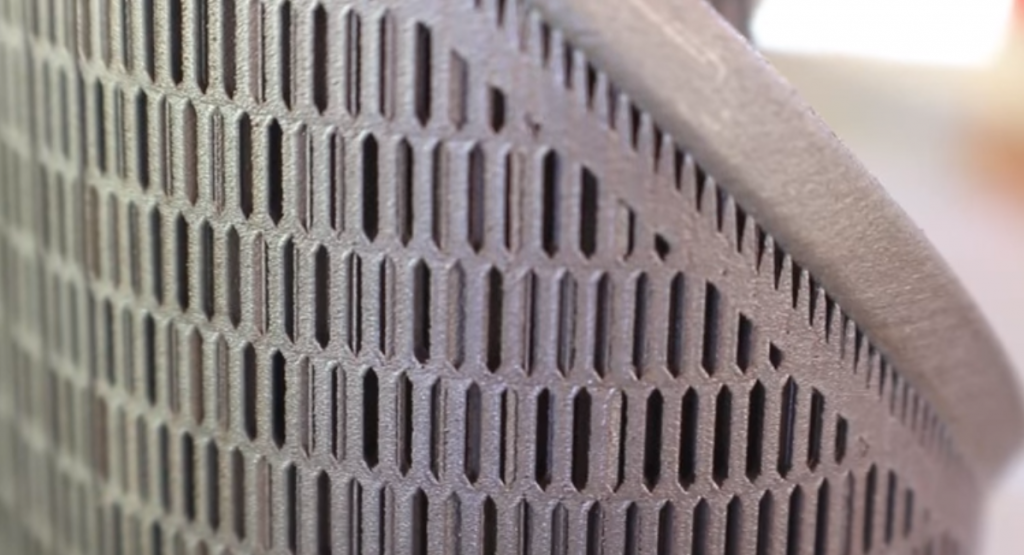
Post-processing is an unavoidable step when 3D printing metal parts. Post-processing helps to improve the mechanical properties, geometrical accuracy and aesthetics of a part, ensuring that a part meets the required design specifications.
Before printing your part, it’s important to understand the various post-processing methods that can be used to finish a metal part.
In this section, we’ll be looking at some of the main post-processing steps that can help to achieve the necessary finish for metal 3D-printed parts.
Stress relief
High temperatures and subsequent cooling are a common occurrence during the metal 3D printing process. However, when a metal part is subjected to such extreme temperature changes, this can lead to residual stress.
To avoid deformations that can occur as a result of a build-up of residual stress, parts produced with powder bed processes must undergo a stress relieving cycle. The number of stress relief cycles depends on the metal or alloy used to produce a part.
In order to protect the surface of a part from oxidation, the stress relieving heat treatment takes place in an inert (typically argon) atmosphere. Parts are typically heat treated while still attached to the build platform.
During the stress relieving cycle, the whole platform is placed in a furnace, where the part is heated to a temperature range between 550-675°C for 1 to 2 hours and then cooled down slowly. Stress corrosion cracking can also be reduced through this stress relief process.
Hot Isostatic Pressing (HIP)
Secondary heat treatment like Hot Isostatic Pressing (HIP) helps to improve the microstructure and mechanical properties of a metal part.
With HIP, high temperatures (up to 2200ºC) and isostatic inert gas pressure (from 100 to 3100 bar) are applied to a part to achieve the highest possible density, reduce porosity and eliminate internal voids.
The HIP treatment of metal parts results in optimum mechanical properties that can be compared with wrought and cast alloys.
Important to note is that the natural cooling in an HIP system can take between 8 and 12 hours. However, HIP systems powered by uniform rapid cooling technologies have been developed, allowing for the parts to be cooled from 1,260 to 300°C in less than 30 minutes.
Powder removal
With powder bed processes, a printed part is encapsulated in the unused powder which needs to be removed once the printing process is complete. The excess powder can be removed manually or automatically with the help of specialised equipment, and then recycled for later use.
The removal of any unmelted powder trapped inside a part should also be taken into consideration. For this reason, at least two escape holes should be factored into the design to help easily remove powder after printing.
Part removal
Once a part has been printed, it will need to be removed from the build platform. Build plates are then machined separately to remove excess material and return them to a usable state.
Wire Electrical Discharge Machining (WEDM) is the process of choice for cutting metal parts away from their build plates. WEDM involves creating electrical dischargers, releasing sparks which rapidly cut away material. Although the process is comparatively slow and used only with electrically conductive metals , it leaves a clean, smooth surface.
Cutting parts away with a bandsaw is another, considerably faster method. However, the process lacks the precision of wire EDM. However, if a part is going to be CNC machined afterwards, this precision can be sacrificed in favour of a faster post-processing time.
Support removal
Support structures are often considered a necessary evil when it comes to 3D printing, and this is particularly the case with metals.
Powder bed fusion technologies, like SLM and DMLS, will always require supports to ensure that they are anchored to the base plate and to mitigate the effects caused by residual stresses.
These supports are typically made from the same material as the part itself and help to minimise defects such as warping or cracking resulting from the high processing temperatures.
Supports are typically removed with the help of CNC machining. However, it’s a good practice to design as few supports as possible. In the Designing for Metal 3D printing section, we look at some of the ways to reduce the amount of support structures.
Surface finishing
As we’ve seen, a metal part that has just been printed won’t have the necessary properties required of the finished part. To achieve a smooth finish for a metal part, there are a number of common surface finishing techniques, including machining, sand blasting, media blasting and polishing.
For example, metal polishing can be used to achieve a ‘mirror-like’ finish for your part. Typically, polishing will be required before other surface treatments are conducted, in order to prevent corrosion and improve the appearance of the part. Applications are typically in the aerospace and automotive industries, as well as medical.
Abrasive blasting methods, such as sandblasting, bead blasting and media blasting, involves an abrasive material being forcibly sprayed onto a part to achieve a smooth surface.
Designing for Metal 3D Printing
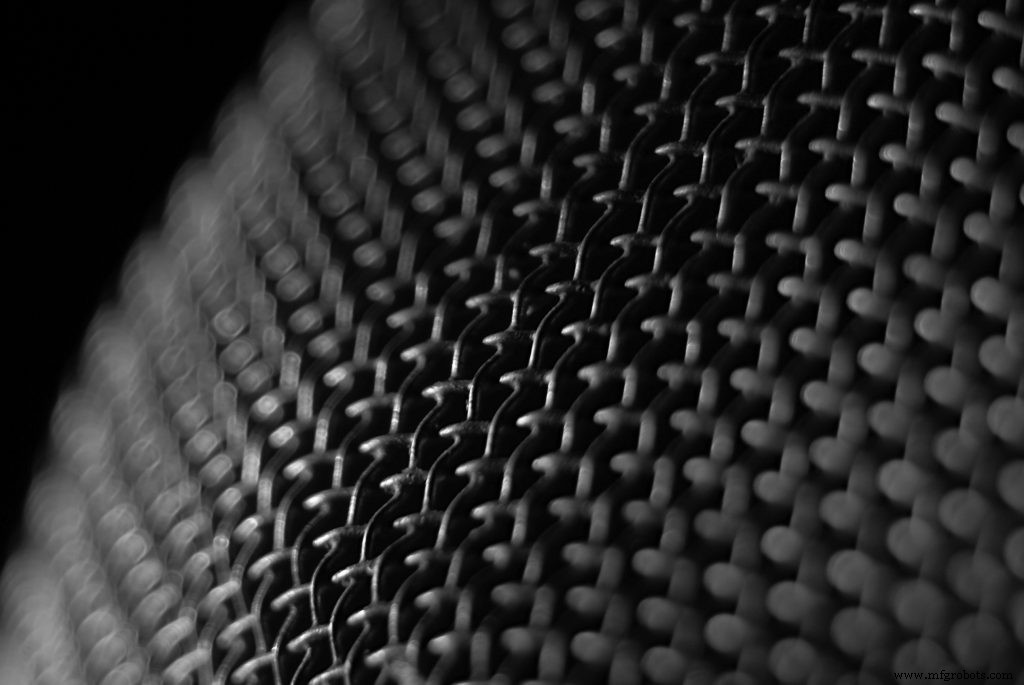
Key Considerations
Metal additive manufacturing gives us the freedom and flexibility to produce parts with complex shapes and intricate features. However, as with any technology, it does have its own set of capabilities and limitations. Understanding the basics of design for metal 3D printing is therefore crucial to obtain a successful print.
Below are some of the key considerations to keep in mind when designing for metal 3D printing.
1. Wall Thickness
Choosing the right wall thickness can make the difference between a successful and a failed print.
As a general rule of thumb, it’s recommended to design walls with a minimum wall thickness of 0.4mm.
It’s also important to ensure that the wall thickness of your parts are not too thin or thick, as this can result in deformation during the printing process or cause damage after removal from the build plate.
In the case of thick walls, the mass can be minimised by applying lattice or honeycomb structures, making the overall printing process cheaper and faster.
2. Support structures
While it’s ideal to design a part with the minimum amount of supports necessary, support structures will virtually always be required with metal 3D printing technologies (except for DED).
Supports play two main roles:first, they are used to anchor a metal part to the base plate to draw away heat, which could otherwise cause residual stresses and build failures.
Second, supports are required to successfully print complex features such as holes, angles and overhangs. For these features, angle measures should be noted:overhangs with an angle less than 45° will require supports.
For features located inside a part, such as horizontal holes along the X or Y axis, it’s generally recommended to design angled support structures.
Angled supports can help maintain a solid connection with the printing bed while minimising the amount of contact the supports have with your part’s surface area. This will make post-processing much easier.
Finally, make sure to check that all support structures will be accessible after printing. Any supports that are difficult to reach will be hard to remove cleanly.
3. Overhangs and Self-Supporting Angles
Overhangs are unsupported downward-facing surfaces, and will need to be carefully considered when designing a part.
Large overhangs (typically over 1mm) will require support structures to prevent them from collapsing during the printing process. The maximum length of an unsupported horizontal overhang is typically 0.5mm, and it is important to keep your overhangs below this length.
If your design requires overhangs, you can also design fillets and chamfers under the downfacing surfaces to make the overhang self-supporting.
Angled features can be designed self-supporting. For this, the angle of a feature should not be less than 45°.
4. Part Orientation
Part orientation is another critical consideration with metal 3D printing. Experimenting with the orientation of your part is the best way to minimise the amount of support structures needed.
For example, if you want to make a metal part with hollow tubular features, a horizontal orientation will take up more space, while a vertical or angled orientation will save space and reduce the amount of supports needed.
Part orientation is also important in determining the accuracy and surface roughness of a part. When selecting your part orientation, keep in mind that downward and upward facing surfaces will have different surface roughness (so-called down-skins tend to have inferior surface finish). If you want to produce detailed features with the best accuracy, make sure to orientate these on the upward facing surface of the part.
5. Channels and Holes
Metal additive manufacturing is notable for its ability to produce parts with internal complex channels for improved fluid flow and holes. A general rule of thumb is to not design such features under 0.4mm in powder-bed processes and under 0.2mm in Metal Binder Jetting. Holes and tubes larger than 10mm in diameter will require support structures.
Keep in mind that perfectly round horizontal holes are still a challenge to 3D print. Consider redesigning such shapes into a self-supporting teardrop or diamond shape.
Additionally, if you are designing a hollow part, you need to factor in the design escape holes to ensure the removal of the unmelted powder. A recommended diameter for escape holes is 2-5mm.
Conclusion
Metal 3D printing:a viable manufacturing technology
Metal 3D printing is emerging as a viable manufacturing technology, as advancements across the spectrum of hardware, materials and software continue to be made.
The technology could help to drive new business models and product development strategies by enabling economic low-volume and on-demand production, innovative design possibilities and, of course, mass customisation.
Of course, it will take some time for companies to become fully confident with the technology. However, an increase in knowledge sharing and education will not only help to further the potential of metal 3D printing, but will also spur a wider adoption of the technology across industries.
Discover More Metal 3D Printing Resources:
Expert Interviews
Digital Alloys CEO Duncan McCallum on Joule Printing and the Future of Metal 3D Printing
HP’s Global Head of Metals on the Impact of HP Metal Jet
ANSYS’ Chief Technologist on Achieving Metal 3D Printing Success with Simulation
Sintavia President Doug Hedges on Achieving Serial Production with Metal 3D Printing
APWORKS CEO Joachim Zettler on Finding the Right Business Case for Metal 3D Printing
SmarTech Analysis’ Scott Dunham on the Future of Metal 3D Printing, Service Bureaus and the AM Materials Market [Part Two]
MELD Manufacturing CEO Nanci Hardwick on Fulfilling the Potential of Metal Additive Manufacturing
3DEO’s President Matt Sand on Taking Metal 3D Printing Into High-Volume Production
VELO3D’s VP of Technology Partnerships on Expanding the Capabilities of Metal 3D Printing
Metal 3D Printing Technologies
Metal 3D Printing:Where are We Today?
All You Need to Know About Metal Binder Jetting
Metal 3D Printing:What is Direct Energy Deposition?
An Introduction to Electron Beam Melting
An Introduction to Wire Arc Additive Manufacturing
Your Guide to the Top DMLS Machines [2018]
Designing for Metal 3D Printing
6 Important Design Considerations for Metal 3D Printing
Making Metal Parts Lighter with Metal 3D Printing
Metal 3D printing Materials
Why Materials are the Key to Metal 3D Printing Success:Expert Interview with voestalpine’s Armin Wiedenegger
3D Printing Precious Metals – a New Approach?
Scalmalloy:The Latest High-Performance Material for Metal 3D Printing
A Quick Guide to 3D Printing Metals
A Guide to 3D Printing With Titanium
Metal 3D Printing Challenges
5 Common Problems Faced with Metal 3D printing – and How You Can Fix Them
Quality Assurance for Metal 3D Printing:Solving 3 Common Challenges
Metal 3D Printing Applications
5 Innovative Use Cases for Metal 3D Printing
How Can 3D Printing Benefit Metal Casting? Here Are 3 Ways