Menempatkan Mesin pada Rencana Kebugaran yang Kuat Dimulai dengan Pemantauan Waktu Nyata
Memiliki rencana untuk memelihara dan meningkatkan kinerja dan keandalan setiap mesin di lantai bengkel sangat penting untuk operasi manufaktur. Mesin yang andal memungkinkan produksi dalam waktu singkat. Dan semakin fleksibel pabrikan, semakin banyak pelanggan baru yang akan mereka tarik.
Dasar dari strategi paling efektif untuk mendapatkan tingkat produktivitas lantai toko yang lebih tinggi dimulai dengan pemantauan waktu nyata. Memiliki aliran data real-time yang kaya kontekstual dari setiap mesin di lantai pabrik sangat berharga untuk meningkatkan setiap proses produksi dan memungkinkan desain hingga manufaktur mencapai potensi penuhnya. Artikel ini membahas:
- peran pemantauan waktu nyata dalam menentukan kinerja dasar mesin,
- bagaimana pemantauan waktu nyata membantu strategi design-to-manufacturing (DTM) agar berhasil,
- manfaat menggunakan pemantauan waktu nyata untuk menyempurnakan rencana kebugaran mesin Anda,
- cara memulai menyiapkan rencana kebugaran mesin, dan
- strategi untuk menyelaraskan mesin dengan proses desain-ke-manufaktur yang gesit.
Mendefinisikan Kinerja Dasar
Rencana kebugaran yang kuat yang memberikan perubahan yang langgeng dimulai dengan dasar kinerja yang sebenarnya, dan hal yang sama berlaku untuk siapa pun yang mulai berolahraga seperti halnya untuk mesin di seluruh lantai toko. Untuk membuat rencana kebugaran untuk mesin mereka yang mendorong hasil, produsen mengandalkan pemantauan waktu nyata untuk data dasar yang mereka butuhkan. Dengan menjadikan pemantauan waktu nyata sebagai bagian integral dari setiap proses produksi, mereka membuat peningkatan permanen menjadi normal baru.
Dua survei terbaru yang dilakukan oleh Analis Keputusan bersama dengan IQMS/Dassault Systèmes menggambarkan bagaimana produsen sekarang mengandalkan pemantauan waktu nyata untuk meningkatkan produktivitas lantai bengkel termasuk menetapkan dasar kinerja alat berat yang menjadi dasar pembuatan rencana kebugaran alat berat individual.
Khususnya, survei Analis Keputusan terhadap 150 produsen Amerika Utara pada tahun 2019 mengungkapkan bahwa 82% responden manufaktur menempatkan prioritas utama untuk meningkatkan mesin yang ada atau membeli mesin baru untuk mendapatkan wawasan dari pemantauan waktu nyata. Perusahaan-perusahaan ini mengganti mesin produksi yang terdepresiasi sepenuhnya dengan mesin canggih yang terhubung dan cerdas yang dapat mendiagnosis sendiri kondisi mereka dan melaporkan masalah—menyediakan data real-time dalam konteks kondisi operasi mereka yang sangat berharga dalam hal- menyetel rencana kebugaran. Selain itu, untuk mengoptimalkan pemantauan waktu nyata mereka, 38% produsen yang disurvei berinvestasi dalam perangkat lunak sistem eksekusi manufaktur (MES), seperti yang terlihat pada Gambar 1, tepat di bawah.
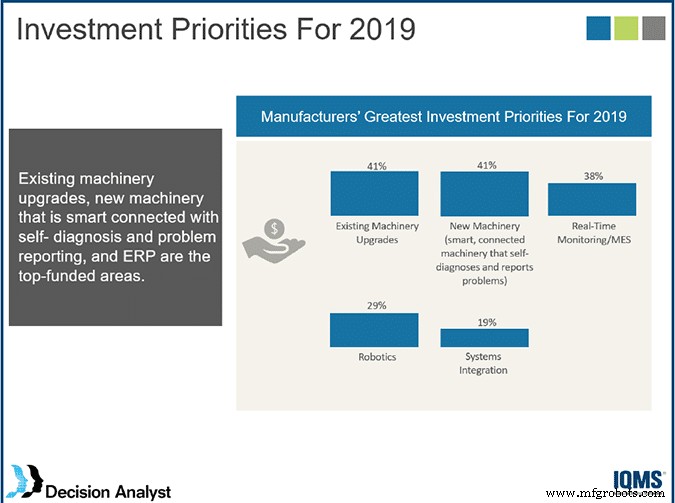
Sementara itu, dalam survei Analis Keputusan dari akhir 2018, 81% dari semua produsen menyatakan bahwa pemantauan waktu nyata meningkatkan bisnis mereka. Dan dalam industri yang padat proses, khususnya manufaktur plastik, 87% produsen melaporkan bahwa pemantauan waktu nyata sangat penting untuk operasi mereka. Secara keseluruhan, 63% produsen mengantisipasi bahwa mereka akan dapat melacak kebugaran individual setiap alat berat dengan lebih baik melalui pemantauan waktu nyata, seperti meninjau tingkat pemanfaatan menurut jenis pelaporan run produksi, scrap, dan waktu henti, seperti yang diilustrasikan pada Gambar 2, langsung di bawah.
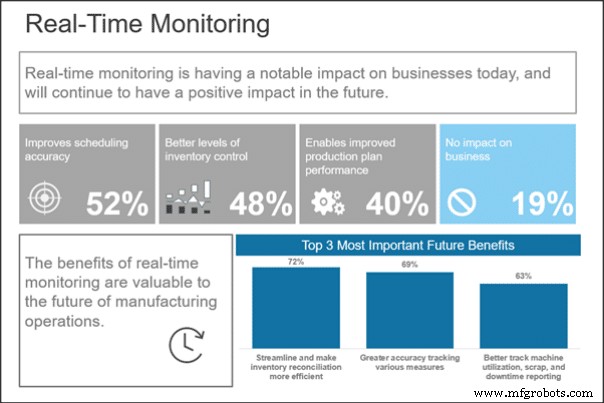
Membantu Kesuksesan Desain-ke-Manufaktur
Pemantauan waktu nyata sangat penting untuk menyinkronkan beragam basis sistem manufaktur dan proses yang diperlukan untuk menciptakan lingkungan desain-ke-manufaktur tunggal di mana desainer, insinyur, manajemen kualitas, dan tim produksi dapat berkolaborasi bersama. Desain hingga manufaktur didasarkan pada tim teknik, kualitas, dan manufaktur yang terintegrasi pada model data produk yang sama. Pemantauan real-time dari mesin produksi berkontribusi pada model data ini dengan memberikan umpan balik penting kepada setiap tim mengenai kemampuan manufaktur, kualitas, dan skala setiap produk baru yang dihasilkan. Ini merupakan umpan balik yang penting bagi semua orang dalam proses desain-ke-manufaktur, yang secara langsung berkontribusi untuk memperpanjang masa pakai mesin di lantai pabrik.
Desainer, insinyur, manajemen kualitas, dan tim produksi memperoleh wawasan berharga tentang bagaimana mengubah model produk memengaruhi efisiensi dan keandalan mesin produk, termasuk waktu rata-rata di antara kegagalan (MTBF). Tim desain-ke-manufaktur mengambil pendekatan yang lebih gesit dan berulang untuk menciptakan produk baru yang didorong oleh wawasan yang mereka peroleh dari data pemantauan waktu nyata. Yang paling penting adalah kontribusi pemantauan waktu nyata untuk memungkinkan beragam anggota tim ini disinkronkan pada model produk umum. Mengambil pendekatan yang lebih kolaboratif untuk menciptakan produk baru yang didasarkan pada desain hingga manufaktur meningkatkan kualitas produk dan profitabilitas dengan mengurangi kesalahan dalam produksi sekaligus meningkatkan tingkat hasil.
Menyesuaikan Rencana Kebugaran Mesin
Ada tiga alasan utama mengapa rencana kebugaran yang didasarkan pada pemantauan waktu nyata adalah tempat yang tepat untuk mulai menyusun strategi desain-ke-manufaktur yang menetapkan dasar untuk pertumbuhan pendapatan yang solid.
Buat prototipe lebih cepat berdasarkan desain model awal sambil mengevaluasi kualitas dan skala produksinya berdasarkan umpan balik pemantauan waktu nyata. Misalnya, produsen plastik yang berspesialisasi dalam produk kelautan bergantung pada desain hingga manufaktur untuk menentukan model produk awal kemudian menghasilkan prototipe dalam hitungan jam menggunakan printer 3D berkecepatan tinggi yang dikombinasikan dengan perangkat pencitraan berbasis stereolitografi. Setelah prototipe model produk disetujui oleh pelanggan, model yang sama diproduksi menggunakan perangkat lunak computer-aided manufacturing (CAM) untuk membuat cetakan produk awal. Dari sana, proses produksi dimulai. Membuat dan menguji kualitas dan daya tahan produk secara digital pertama-tama menghemat ribuan jam dan dolar bagi pelanggan dan produsen produk kelautan. Ini menunjukkan bagaimana pendekatan desain-ke-manufaktur mengatasi masalah lebih awal dan membawa produk baru ke pasar lebih cepat.
Bantu bangun permintaan untuk produk baru sebelum mereka mengirim dengan mengambil pendekatan desain-ke-manufaktur untuk produksi di mana data real-time dari setiap mesin membantu perencana produksi menentukan alur kerja yang optimal untuk setiap produk baru. Misalnya, penyedia terkemuka produk OEM berbasis serat karbon untuk industri manufaktur otomotif, barang kemasan konsumen, dan proses plastik pertama kali membuat model prototipe pelanggan, memberikan gambar produk baru yang ditampilkan jauh sebelum tanggal pengiriman. Pelanggan menggunakan gambar yang diberikan untuk merencanakan kampanye pemasaran dan penjualan mereka, mengumpulkan materi pemberdayaan penjualan, dan menentukan kemasan. Di sini, desain hingga manufaktur memungkinkan untuk memberikan nilai lebih kepada pelanggan OEM dan membantu mereka berhasil dalam menjual produk baru mereka.
Berikan lebih banyak pilihan kepada pelanggan dengan model produk dasar mereka melalui peningkatan konfigurasi-harga-kutipan (CPQ) dan strategi konfigurasi produk. Di sini, pemantauan waktu nyata memberikan umpan balik ke desain kepada tim manufaktur mengenai produk yang dapat dikonfigurasi mana yang paling efisien, dapat diproduksi, dan menguntungkan untuk dibuat. Contohnya adalah pendekatan BMW yang sangat sukses untuk menjual Mini Coopers yang disesuaikan menggunakan konfigurator produk secara online dan di dealer, didukung oleh pendekatan berbasis model untuk manufaktur. CPQ dan konfigurasi produk unggul ketika semua sistem yang mendukung strategi ini disinkronkan dan menjalankan irama yang sama. Desain hingga manufaktur mewujudkannya. Dan itu berita bagus bagi produsen yang dapat meningkatkan tingkat pemanfaatan pusat produksi dengan memproduksi produk yang lebih disesuaikan—dan margin lebih tinggi—untuk pelanggan daripada sebelumnya.
Menyiapkan Rencana Kebugaran Mesin
Untuk menyusun strategi pertumbuhan yang sukses, produsen harus mengikatnya kembali ke rencana kebugaran untuk setiap peralatan mesin. Hal ini tidak hanya akan memperpanjang masa pakainya, data tambahan tentang kesehatan mesin juga akan meningkatkan penjadwalan produksi. Menugaskan teknisi yang paling berkualifikasi ke kombinasi mesin terbaik untuk menjalankan produksi tertentu sangat disederhanakan ketika setiap mesin memiliki tingkat kebugaran produksi yang tinggi secara konsisten.
Sama seperti seseorang yang bergabung dengan gym untuk mendapatkan bentuk tubuh yang lebih baik, jutaan produsen saat ini memiliki awal rencana kebugaran yang kuat untuk mesin mereka. Tantangannya adalah menempatkan mereka ke dalam tindakan dan mendapatkan hasil. Empat langkah berikut adalah cara yang bagus untuk memulai:
Tangkap data dasar untuk setiap mesin di beberapa shift untuk memeriksa variasi output yang terlihat dan mudah ditentukan. Membuat kumpulan data kinerja setiap alat berat di seluruh lantai bengkel adalah titik awal untuk setiap rencana kebugaran alat berat individual.
Pilih kumpulan metrik awal bahwa setiap mesin mampu melaporkan hari ini untuk menyelesaikan perbandingan dasar. Setiap mesin dapat dianalisis pada empat metrik:waktu siklus, waktu set-up, tingkat scrap/rework, dan hasil. Perbedaan antara mesin akan segera muncul. Mengetahui seberapa baik kinerja setiap mesin terhadap keempat kriteria ini memberikan wawasan yang sangat berharga tentang bagaimana masa pakainya dapat diperpanjang.
Identifikasi mesin yang paling banyak dan paling sedikit bentuknya dengan menganalisis data dasar dan aktivitas mesin pengindeksan sebelumnya terhadap pengembalian pelanggan dan masalah kualitas. Mesin yang bertanggung jawab atas persentase tertinggi pengembalian pelanggan dan masalah kualitas sering kali merupakan mesin yang sama yang menunjukkan tingkat keausan yang sangat tinggi. Memeriksa untuk memastikan perkiraan waktu rata-rata untuk perbaikan (MTTR) dan MTBF akurat adalah prasyarat untuk memperpanjang masa pakai alat berat dan meningkatkan kualitas produk dan tingkat hasil.
Gabungkan pemantauan waktu nyata dengan peningkatan mesin untuk mengungkap bagaimana urutan produksi memengaruhi keandalan dan kinerja mesin dari waktu ke waktu. Mengetahui mengapa mesin tertentu mulai gagal mungkin lebih berkaitan dengan posisi relatif mereka dalam alur kerja produksi daripada yang terlihat pada awalnya. Itulah sebabnya pemantauan real-time yang dikombinasikan dengan pemutakhiran terbaru ke mesin cerdas yang terhubung masuk akal. Bersama-sama, langkah-langkah tersebut menghilangkan dua sumber variasi yang berpotensi besar dari pemahaman tentang cara memperpanjang masa pakai mesin.
Menyelaraskan Mesin dengan DTM
Ketika tim memanfaatkan kinerja dan skala mesin yang lebih tinggi yang dikelola dengan rencana kebugaran yang lebih ketat dan menyeluruh, mereka diposisikan untuk mengambil proyek desain-ke-manufaktur yang lebih ambisius. Mengetahui skala, kecepatan, dan keandalan setiap alat berat yang terlibat dalam memproduksi produk baru membawa kelincahan yang lebih besar pada desain, pengembangan, teknik, kualitas, dan proses produksi secara bersamaan yang bersama-sama menciptakan kerangka kerja desain-ke-manufaktur.
Di mana produsen melihat manfaat terbesar dari komitmen terhadap rencana kebugaran mesin yang ketat dan berkelanjutan adalah dalam mempercepat jadwal pengembangan produk baru sekaligus mengurangi biaya. Mengetahui bagaimana setiap mesin akan bereaksi terhadap persyaratan produksi baru sangat berharga dalam mengurangi kesalahan dalam segala hal mulai dari konsep desain awal hingga instruksi kerja.
Manfaat utama lainnya dari menggabungkan rencana kebugaran dengan desain hingga manufaktur adalah bahwa tim kolaboratif mengetahui seberapa banyak tingkat hasil mesin yang telah meningkat dan apa artinya itu untuk proses produksi di masa depan.
Terakhir, rencana kebugaran untuk mesin menciptakan fondasi terkuat bagi produsen untuk memberikan CAM, desain berbantuan komputer (CAD), simulasi/analisis elemen hingga (FEA), listrik, inspeksi, dan tim manufaktur jaminan yang mereka butuhkan bahwa mereka dapat mengejar siklus pengembangan, pengujian, dan rilis produk yang lebih cepat daripada sebelumnya. Ketika setiap sistem dalam proses manufaktur berjalan pada irama atau kecepatan clock yang berbeda, mencapai konkurensi adalah hal yang harus dimiliki, dan desain untuk manufaktur yang dikombinasikan dengan rencana kebugaran mesin yang berkelanjutan sangat penting. (Catatan Editor:Artikel ini adalah versi tambahan dari kolom Sudut Pandang yang muncul di Teknik Manufaktur edisi September 2019 )
Tentang Penulis
Louis Columbus adalah kepala di perusahaan perencanaan sumber daya perusahaan manufaktur IQMS (sekarang DELMIAWORKS, bagian dari keluarga Dassault Systèmes). Michael Buchli adalah senior SolidWorks manajer produk dan portofolio di Dassault Systèmes.