Proses Romelt untuk Pembuatan Besi
Proses Peleburan untuk Pembuatan Besi
Proses Romelt untuk pembuatan besi adalah proses reduksi peleburan untuk produksi logam panas (besi cair). Proses ini telah dikembangkan oleh Universitas Nasional Sains &Teknologi 'MISiS', Rusia (sebelumnya dikenal sebagai Institut Baja dan Paduan Moskow). Pekerjaan pengembangan proses dimulai pada tahun 1978 ketika sekelompok ilmuwan 'MISiS' yang dipimpin oleh Vladimir Romes mulai merancang proses ini. Paten pertama di Rusia diperoleh pada 1979.
Pabrik produksi percontohan yang memiliki area perapian 20 meter persegi dan dengan kapasitas 40.000 ton logam panas per tahun ditugaskan pada tahun 1985 di Pekerjaan Besi dan Baja Novolipetsk (NLMK). Pabrik percontohan dirancang oleh Moscow Gipromez. Desain tungku Vanyukov yang andal diambil sebagai prototipe untuk metode baru pembuatan logam panas ini. Proses tersebut diuji dan dikuasai di pabrik percontohan ini antara 1985 dan 1998. Selama periode ini, empat puluh satu kampanye dilakukan, yang masing-masing mencakup startup dan perlambatan, dengan penyadapan penuh logam panas dan terak dari tungku. Lebih dari 40.000 ton logam panas diproduksi di pabrik percontohan selama periode ini dan digunakan lebih lanjut di tungku oksigen dasar (BOF) untuk pembuatan baja.
Pabrik industri pertama untuk produksi logam panas berdasarkan teknologi Romelt sedang dibangun di Myanmar. Pabrik telah dirancang oleh Leningrad Gipromez dan dipasok oleh Tyazpromexport, anak perusahaan Rostec. Pabrik ini memiliki kapasitas 200.000 ton per tahun dan berbasis pada pengolahan bijih besi tanpa memanfaatkan deposit bijih Pang Pet. Deposit bijih Pang Pet memiliki kandungan Fe hingga 29%. Pembangkit tersebut akan menggunakan batu bara non-coking dari ladang batu bara Kye Thee. Pemandangan panorama pabrik Romelt di Myanmar ada di Gambar 1.
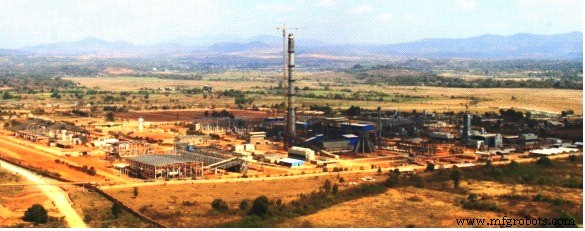
Gbr1 Pemandangan panorama pabrik Romelt di Myanmar
Bahan mentah dan fitur khusus dari proses
Umpan oksida besi ke proses Romelt dapat berupa bahan yang mengandung besi, mis. butiran halus dan konsentrat bijih besi, tanur sembur dan debu dan lumpur BOF, kerak pabrik, terak bantalan besi, limbah dan bubutan syal, dan debu besi dll. Batubara non-coking basah dari 15% hingga 20% bahan yang mudah menguap dan sekitar 8% hingga 10% abu dapat digunakan. Umpan padat (batubara, oksida besi, dan fluks) dibebankan oleh gravitasi di tungku.
Fitur khusus dari proses Romelt termasuk (i) fleksibilitas untuk menggunakan berbagai macam bahan bantalan besi, (ii) tidak ada persiapan yang diperlukan untuk bahan baku, (iii) penggunaan batubara non-coking sebagai bahan bakar dan sebagai agen pereduksi, (iv ) unit produksi pendukung seperti coke-oven dan pabrik sintering tidak diperlukan, (v) memiliki kapasitas untuk menghasilkan daya yang cukup untuk memenuhi kebutuhan pabrik secara keseluruhan termasuk pabrik oksigen, (vi) mengurangi biaya logam panas dibandingkan dengan tanur sembur (BF ) rute, dan (vii) dapat digunakan untuk pengolahan limbah sehingga biaya logam panas semakin berkurang.
Prinsip proses
Proses Romelt adalah proses reduksi besi fase cair satu tahap. Dalam prosesnya, bahan bantalan besi dipasok ke bak terak oleh gravitasi dan diaduk oleh gas. Mereka larut dalam terak. Oksida besi direduksi dari terak dengan bantuan karbon batubara, yang juga disuplai oleh gravitasi dan ditiupkan ke bak mandi. Untuk mengintensifkan panas dan perpindahan massa terak mandi menggelegak dengan gas pengoksidasi, yang disuntikkan di bawah permukaan terak, dilakukan. Gas yang mengandung CO dan H2 berevolusi dari terak yang meleleh. Gas yang berevolusi dibakar di bagian atas. Panas dari pembakaran pasca ini sebagian besar menyediakan energi panas untuk reaksi yang terjadi di bak terak. Elemen kunci dari proses yang efektif untuk berlangsung adalah perpindahan panas aktif antara zona pasca-pembakaran dan mandi terak.
Deskripsi proses
Proses Romelt menggunakan teknologi reduksi peleburan satu tahap untuk produksi logam panas. Proses ini menggunakan batubara non-coking untuk reduksi oksida besi dari bijih besi dan bahan limbah. Skema proses ditunjukkan pada Gambar 2.
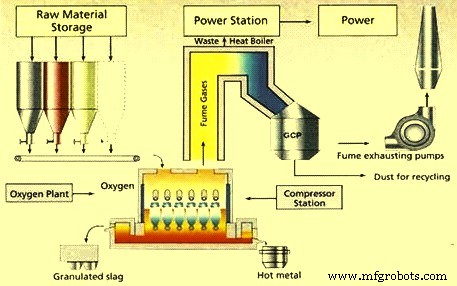
Gbr 2 Skema proses Romelt
Bahan yang mengandung besi, batu bara, dan fluks diumpankan, menggunakan timbangan hopper, dari tempat sampah yang relevan ke konveyor umum. Pengisian ke dalam tungku dilakukan melalui lubang di atap tungku. Pencampuran awal bahan pengisi tidak diperlukan karena bahan setelah pengisian langsung masuk ke bak terak karena pengadukannya yang intensif. Pengaturan pintu air, yang digunakan dalam unit untuk proses lain yang beroperasi di bawah tekanan, tidak diperlukan dalam tungku Romelt. Ruang kerja tungku Romelt berada di bawah tekanan negatif kolom air 1 mm hingga 5 mm yang dipastikan oleh kipas angin yang diinduksi. Tampilan skema tungku peleburan tungku Romelt ditunjukkan pada Gambar 3.
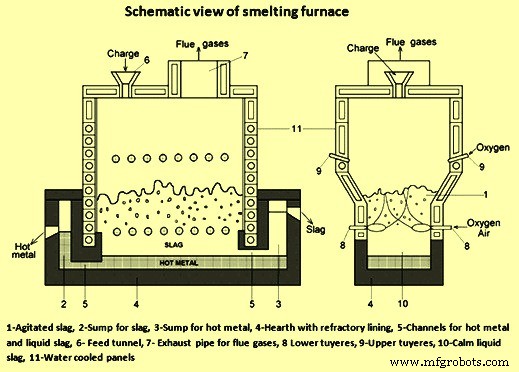
Gbr 3 Tampilan skema tungku Romelt
Pemandian terak cair ditiup dengan oksigen atau campuran oksigen-udara melalui tuyer bawah yang terletak di bawah lapisan terak. Tuyeres memiliki struktur sederhana dan dapat diandalkan dalam pengoperasiannya. Mereka memastikan agitasi yang diperlukan dari mandi terak. Batubara non-coking yang ada dalam terak cair yang diaduk mengurangi oksida besi yang ada dalam beban bantalan besi. Besi cair yang dihasilkan oleh reduksi oksida besi menjadi kaya akan karbon. Tetesan besi cair bergerak menuju perapian tungku karena gravitasi.
Ada tiga zona di tungku peleburan. Zona pertama adalah zona terak yang diaduk. Ini adalah zona di mana semua reaksi berlangsung. Zona kedua adalah bagian bawah perapian tempat logam panas yang dihasilkan dikumpulkan. Zona ketiga adalah zona terak yang tenang dan terletak di antara zona pertama dan kedua. Zona kedua dan ketiga harus memiliki kapasitas yang cukup untuk menampung logam panas dan terak yang dihasilkan.
Dua ruang berjajar (sumps) terletak masing-masing di salah satu sisi ujung tungku. Mereka digunakan untuk penyadapan terpisah dari logam panas dan terak cair. Sumps dihubungkan dengan ruang kerja dengan saluran dengan ketinggian berbeda. Ini memastikan pengangkutan logam panas dan terak cair secara terpisah ke dalam wadah logam dan terak. Ada lubang keran untuk penyadapan logam panas dan terak cair, yang terletak di ketinggian yang berbeda. Pengaturan ini memastikan penyadapan terus menerus dan bebas dari produk cair (logam panas dan terak) pada kecepatan yang sesuai dengan kapasitas tungku.
Dalam slag bath, panas yang dibutuhkan untuk peleburan dan pengurangan material beban lebih tinggi daripada panas yang tersedia karena pembakaran karbon dari batubara non-coking menjadi CO di dekat tuyer yang lebih rendah. Dengan demikian, fitur utama dari proses ini adalah pasca-pembakaran CO, H2 dan bahan yang mudah menguap dari batubara yang berkembang dari bak oleh oksigen yang dihembuskan melalui tuyer atas. Pasca pembakaran gas menjadi CO2 dan H2O memberikan panas tambahan ke dalam bak terak yang diperlukan untuk mempertahankan pemrosesan bahan mentah.
Perapian dan bagian bawah bak tungku, yang berisi logam panas permanen dan terak cair yang tenang, dilapisi dengan batu bata tahan api. Di zona ini lapisan tahan api berada di bawah kondisi yang menguntungkan yang terdiri dari suhu yang sesuai dan sifat atmosfer non-pengoksidasi. Di zona terak yang diaduk, dinding tungku dibangun dengan panel berpendingin air yang terbuat dari tembaga. Pembentukan lapisan scull terak pada mereka mengurangi kehilangan panas dan menghilangkan kemungkinan keausan mereka. Ini juga menghindari keausan lapisan di tempat-tempat serangan paling agresif dari emulsi logam terak gas. Di atas bak terak, dinding terbuat dari panel berpendingin air yang terbuat dari baja. Atap tungku juga didinginkan dengan air.
Setelah pasca-pembakaran, gas pada suhu hingga 1700 derajat C mengalir melalui pipa knalpot berpendingin air ke boiler limbah panas. Di sana gas dibakar sepenuhnya dengan aliran udara alami dan didinginkan hingga 250 derajat C hingga 300 derajat ?. Setelah energi diperoleh kembali dan gas didinginkan, gas dibersihkan dalam sistem pembersihan gas dan didesulfurisasi sebelum dibuang ke atmosfer melalui cerobong asap. Pembentukan debu buangan dari tungku Romelt yang diukur dalam pipa pembuangan adalah sekitar 3% dari rata-rata berat bahan yang diisi.
Perilaku batubara di bak mandi terak
Terlepas dari mekanisme reduksi, batubara adalah satu-satunya sumber reduktor dalam prosesnya. Tidak ada batasan utama pada kisaran batubara yang digunakan untuk menjalankan proses dalam kondisi normal. Setiap salah satu batubara dengan kandungan karbon tetap, abu dan bahan yang mudah menguap yang berbeda dapat digunakan sebagai zat pereduksi. Namun, konsumsi batubara dan oksigen spesifik sangat bergantung pada komposisi batubara yang digunakan.
Batubara basah yang tidak disiapkan dalam proses Romelt jatuh dari atas ke dalam bak terak. Zat yang mudah menguap dihasilkan dalam rendaman terak dan memiliki pengaruh yang merangsang pada kemajuan proses. Baik keseimbangan material dan keseimbangan panas dari proses bergantung pada bagaimana dan dalam bentuk apa materi yang mudah menguap dihasilkan dan perannya dalam berlangsungnya proses utama di tungku. Itulah mengapa perilaku volatile matter batubara adalah salah satu poin paling kritis untuk proses Romelt terlepas dari kualitas batubara yang digunakan.
Laju batubara dalam proses Romelt terdiri dari dua bagian yaitu (i) konsumsi batubara yang dibutuhkan untuk reaksi dengan oksigen yang disuntikkan pada tuyer yang lebih rendah untuk menghasilkan CO, dan (ii) konsumsi batubara yang dibutuhkan untuk reduksi oksida. Kekurangan batubara dapat menjadi alasan peningkatan potensi pengoksidasi dari rendaman terak, yang dapat menyebabkan pendidihan yang tidak terkendali. Namun, laju batubara yang berlebihan selain meningkatkan biaya produksi logam panas, juga memperburuk kondisi termal di dalam tungku Romelt.
Secara umum terlihat bahwa jumlah batubara yang dibutuhkan hanya bergantung pada kandungan karbon tetap dalam batubara. Namun, dalam tungku Romelt bahan yang mudah menguap juga berpartisipasi sebagian dalam proses yang berlangsung di dalam penangas terak cair. H2, CO dan N2 dari bahan yang mudah menguap tidak mengalami perubahan dalam rendaman terak karena gas-gas ini berevolusi dari batubara untuk menghasilkan fase gas. Namun, CH4 dan CO2 dari zat yang mudah menguap berpartisipasi dalam reaksi kimia seperti dalam persamaan CH4 =C + 2H2 dan CO2 + C =2CO. Jika jumlah CO2 kecil dan jumlah metana (CH4) yang sama banyak, maka transformasi kimia ini mengarah pada ketersediaan jumlah tambahan karbon untuk reduksi oksida. Karbon yang dihasilkan oleh dekomposisi metana terdispersi halus dan sangat aktif serta meningkatkan kinetika reaksi reduksi.
Dalam proses Romelt digunakan batubara basah dengan kadar air sekitar 10% sampai 12%. Dalam tungku, uap air ini diuapkan dan sebagian terurai sesuai persamaan H2O + C =CO + H2. Hal ini memerlukan tambahan karbon untuk melanjutkan reaksi dekomposisi air untuk menghasilkan gas air yang terdiri dari CO dan H2.
Ketiga reaksi tersebut yaitu dekomposisi metana, reduksi CO2 menjadi CO, dan dekomposisi air berlangsung di slag bath secara bersamaan.
Aspek kimia dan metalurgi dari proses
Sebagian besar proses reduksi terjadi di zona terak yang diaduk. Oksigen atau campuran oksigen dan udara dihembuskan melalui tuyeres bawah untuk menghasilkan rendaman yang sangat gelisah. Umpan bahan baku jatuh ke terak yang diaduk di mana peleburan dan pengurangan terjadi. Slag bath dipertahankan pada sekitar 1400 derajat C sampai 1500 derajat C. Batubara non kokas bertindak baik sebagai reduktor dan sebagai sumber bahan bakar di zona ini. Reaksi berikut terjadi di zona terak yang diaduk.
- Reduksi oksida besi. x C + FeOx =x CO +Fe
- Gasifikasi karbon. 2 C + O2 =2CO
- Pemecahan bahan volatil dalam batubara. 2 CxHy =2x C + y H2
- Pengurangan air. H2O + C =CO + H2
Besi tereduksi membentuk tetesan kecil yang menyatu dan terpisah dari terak bergerak ke perapian tungku di bawah zona terak tenang karena kepadatannya yang lebih tinggi. Interaksi antara logam dan terak di zona terak yang bergejolak dan tenang memungkinkan logam dimurnikan melalui partisi elemen kecil di antara fase.
Gas yang dihasilkan di bak mandi, terutama CO dan H2, memasuki zona pembakaran. Di sini gas bereaksi dengan oksigen yang dihembuskan melalui tuyer atas dan melepaskan energi yang digunakan untuk reaksi peleburan. Reaksi yang terjadi di zona pembakaran adalah sebagai berikut.
- Setelah pembakaran. CO + O2 =CO2 dan 2 H2 + O2 =2 H2O
- Pembakaran bahan volatil dari batubara. 4 CxHy + (4x+y) O2 =4x CO2 + 2y H2O
Energi yang dibebaskan dari reaksi pembakaran ditransfer kembali ke bak mandi. Perpindahan panas ditingkatkan oleh tingginya tingkat turbulensi yang dihasilkan dalam rendaman terak oleh tuyer yang lebih rendah. Off-gas hanya dibakar sebagian di tungku yang memungkinkan pemulihan energi lebih lanjut dalam sistem boiler panas limbah konvensional.
Proses Romelt terutama didasarkan pada reduksi fase cair besi. Oleh karena itu proses memiliki keseimbangan yang lebih baik dari aspek kimia dan energi dari dua tahap reduksi yaitu fase padat dan fase cair. Dalam proses Romelt, sebagian besar pemanasan dan reduksi dipindahkan ke tahap fase cair.
Reduksi besi dari oksidanya dalam terak dilakukan oleh partikel batubara dan oleh karbon yang dilarutkan dalam inklusi logam dalam terak. Ada dua cara berikut yang menunjukkan keterlibatan batubara dalam reduksi oksida besi di tungku.
- Pengurangan terjadi pada permukaan gelembung gas yang mengandung partikel batubara. Peran partikel-partikel ini adalah untuk meregenerasi atmosfer pereduksi dalam gelembung (kondisi termodinamika yang ada dalam proses membuat gelembung gas yang tidak mengandung partikel batubara sulit untuk mereduksi oksida besi).
- Reduksi terjadi dengan partikel batubara yang kontak langsung secara acak dengan terak. Di sini, reduksi terjadi di bawah kondisi yang serupa dengan yang ada saat besi direduksi oleh bahan pembawa karbon yang berputar dan gelembung gas dikeluarkan secara paksa dari permukaan material.
Pengurangan di tungku Romelt terjadi (i) ketika partikel batubara bersentuhan langsung dengan terak (60% hingga 80%), (ii) ketika karbon bersentuhan langsung dengan logam turun (10% hingga 15%). dan (iii) pada antarmuka 'gas–slag' (10 % hingga 25%). Biasanya, 85% sampai 90% besi direduksi dengan partisipasi langsung dari partikel batubara. Hal ini membedakan reduksi fase cair yang terjadi pada proses Romelt dari proses reduksi peleburan lainnya dimana karbon terlarut dalam logam berperan penting (DIOS) atau berperan utama (Hlsmelt) dalam operasi reduksi.
Dalam proses Romelt, terdapat nilai optimum tertentu untuk kandungan partikel batubara dalam slag bath, meskipun parameter ini dapat bervariasi dalam rentang nilai yang luas. Tungku Romelt tidak dapat kelebihan atau kekurangan muatan dengan batubara. Pengisian jumlah batubara yang kurang optimal menyebabkan oksidasi berlebihan pada lelehan terak dan buihnya yang tidak terkendali. Jadi, batu bara yang melebihi jumlah yang dihitung sering kali dimasukkan ke dalam tungku untuk mencegah oksidasi berlebih, dan ini terkadang membantu dalam stabilisasi proses. Namun, ada batas untuk kelebihan jumlah partikel batubara dalam slag. Batas ini juga dapat menyebabkan gangguan pada proses seperti penurunan suhu penangas terak, peningkatan kandungan oksida besi dalam terak, penurunan derajat pembakaran sekunder gas keluar, dan pelepasan lebih banyak panas di boiler limbah panas.
Pemberian oksigen tambahan ke dalam tungku tidak mendorong pembakaran sekunder karena oksigen tidak sepenuhnya bereaksi dengan batubara yang mengapung di permukaan terak. Lapisan batubara yang padat ini terbentuk sebagai akibat dari pengisian batubara yang berlebihan atau pengisian bahan baku yang mengandung oksida. Kehadiran lapisan menekan penyemprotan dan adhesi terak ke dinding, yang mempengaruhi perpindahan panas dari zona pembakaran gas primer ke bak terak karena perpindahan panas terjadi terutama melalui tetesan terak dan film terak yang mengalir. menyusuri dinding di zona pembakaran sekunder.
Terlihat bahwa dalam tungku Romelt, jika kandungan batubara dari lapisan permukaan terak adalah sekitar 20% sampai 30%, proses transit ke rezim yang tidak diinginkan di mana batubara menghalangi perpindahan panas dari zona pembakaran sekunder ke bak. Terjadinya rezim ini tidak tergantung pada jumlah dan komposisi batubara yang terakumulasi dalam terak, tetapi juga pada laju sirkulasi turbulen terak karena turbulensi ini menentukan efisiensi pencampuran batubara dengan komponen lain dari lelehan terak. .
Karakteristik produk dan konsumsi spesifik
Analisis tipikal logam panas dari proses Romelt terdiri dari karbon – 4,5%, silikon – 0,1%, mangan – 0,08%, belerang – 0,05%, dan fosfor – 0,1%.
Analisis tipikal terak dari proses Romelt terdiri dari CaO – 39 %, MgO – 7 %, SiO2 – 36 %, Al2O3-11 %, FeO – 3,0 %, MnO – 3 %, TiO2 – 0,1 %, dan S – 0,04 %.
Angka konsumsi spesifik tipikal dalam per ton logam panas adalah sekitar 940 kg – 1200 kg untuk batubara kering non-coking, dan 750 N cum hingga 850 N cum untuk oksigen.
Keuntungan dari proses Romelt
Berikut ini adalah keuntungan dari proses Romelt.
- Biaya modal rendah karena operasi tekanan rendah dan penggunaan peralatan tambahan konvensional.
- Tidak ada persyaratan untuk coke atau coking coal sehingga biaya operasional lebih rendah.
- Dapat memproses semua bahan yang mengandung besi termasuk limbah metalurgi, tanpa pengolahan sebelumnya.
- Tidak ada persyaratan untuk menggumpalkan oksida besi.
- Memiliki tingkat pemulihan zat besi yang tinggi.
- Memungkinkan pembentukan sumber logam panas skala kecil yang efektif untuk pabrik yang lebih kecil.
- Ramah lingkungan karena menghilangkan oven kokas dan tanaman aglomerasi (sintering dan pelletizing).