Batu Kapur – Pengolahan dan Aplikasinya dalam Industri Besi dan Baja
Batu Kapur – Pengolahan dan Aplikasinya dalam Industri Besi dan Baja
Batugamping adalah batuan sedimen yang terbentuk secara alami dan melimpah yang terdiri dari kalsium karbonat (CaCO3) tingkat tinggi dalam bentuk mineral kalsit. Beberapa batugamping mungkin mengandung persentase kecil magnesium karbonat (MgCO3). Batugamping ini dikenal sebagai batugamping dolomit.
Batu kapur juga merupakan mineral industri yang sangat penting. Sifat kimianya menjadikannya mineral berharga untuk berbagai keperluan industri/manufaktur. Batu kapur juga merupakan salah satu bahan baku vital yang digunakan dalam produksi besi dan baja.
Batu kapur, menurut definisi, adalah batuan yang mengandung setidaknya 50% CaCO3 dalam bentuk kalsit menurut beratnya. Mungkin ada partikel kecil kuarsa (silika), feldspar (alumino-silikat), mineral lempung, pirit (besi sulfida), siderit (besi karbonat), dan mineral lain yang terkait dengan batu kapur. Semua batugamping mengandung setidaknya beberapa persen bahan lain. Kotoran dalam batugamping dapat terdiri dari silika (SiO2), alumina (Al2O3), oksida besi (Fe2O3), belerang (sebagai sulfida atau sulfat), fosfor (P2O5), kalium (K2O), dan soda (Na2O). Silika dan alumina merupakan pengotor utama batugamping. Batu kapur yang digunakan dalam pembuatan besi harus mengandung setidaknya 85% kalsium karbonat dan persentase alumina yang rendah. Demikian pula batu kapur yang digunakan untuk pembuatan baja harus mengandung setidaknya 92% kalsium karbonat dan persentase pengotor yang sangat rendah terutama persentase silika.
Kegunaan utama batugamping dalam industri besi dan baja adalah (i) sebagai bahan fluks, dan (ii) penggunaan lain yang terdiri dari agen desulfurisasi, pelapis cetakan mesin pig casting, penetralisir air asam, pengolahan air, air limbah ( limbah), pengolahan gas buang, dan pengolahan lumpur dan limbah. Ini juga merupakan komponen terak sintetis. Batu kapur biasanya digunakan dalam tiga bentuk. Ini adalah (i) batugamping mentah yang juga merupakan bentuk alami dari batugamping, (ii) batu kapur yang dikalsinasi atau kapur tohor, atau hanya kapur, dan (iii) sebagai kapur terhidrasi. Ketika batu kapur digunakan sebagai bahan fluks maka digunakan baik sebagai batu kapur mentah atau sebagai batu kapur yang dikalsinasi. Kapur terhidrasi umumnya dihasilkan dari kapur tohor berkalsium tinggi dan mengandung 72% hingga 74% kalsium oksida dengan 23% hingga 24% air yang dikombinasikan secara kimiawi.
Pengolahan batu kapur
Batu kapur setelah ditambang harus melalui beberapa proses pengolahan sebelum dapat digunakan dalam berbagai proses. Proses dasar dalam produksi batu kapur adalah (i) penggalian batu kapur mentah, (ii) penyiapan batu kapur yang ditambang untuk digunakan dengan penghancuran dan ukuran, (iii) pengapuran batu kapur mentah, (iv) pengolahan batu kapur yang telah dikalsinasi lebih lanjut dengan menghidrasi menjadi menghasilkan kapur terhidrasi jika diperlukan untuk digunakan, dan (v) berbagai operasi pemindahan, penyimpanan, dan penanganan. Semua proses ini mungkin tidak perlu ada di setiap pabrik.
Pada dasarnya tiga jenis produk batu kapur digunakan di pabrik besi dan baja. Mereka adalah (i) produk batu kapur mentah, (ii) batu kapur yang dikalsinasi atau produk kapur tohor, dan (iii) produk kapur terhidrasi. Pemrosesan batu kapur untuk produk ini dijelaskan di bawah ini.
Proses pertama berlangsung di tambang batu kapur di mana bijih yang ditambang menjalani penghancuran dan penyaringan untuk pemisahan fraksi ukuran bijih yang berbeda. Di pabrik besi dan baja, di beberapa tempat, batu kapur mentah diproses lebih lanjut. Contohnya adalah pabrik sinter dimana batu kapur mentah dihancurkan dalam hammer mill dengan ukuran – 3 mm (umumnya berkisar 85 % sampai 90 %).
Kalsinasi batu kapur adalah proses perlakuan termal untuk melakukan dekomposisi termal batu kapur mentah dan menghilangkan bagian LOI (loss on ignition) atau karbon di-oksida (CO2) dari komposisinya. Proses kalsinasi terdiri dari reaksi endotermik yang dilakukan dalam keadaan padat. Kapur kualitas tinggi yang digunakan dalam pembuatan baja umumnya mengandung sekitar 90% sampai 95% CaO. Secara teoritis 56 kg CaO dihasilkan dari 100 kg CaCO3 selama kalsinasi lengkap. Namun, dalam praktiknya sebenarnya bervariasi karena beberapa faktor. Selama kalsinasi batugamping, karena CO2 dihilangkan, kapur (i) berpori (ii) memiliki luas permukaan lebih tinggi, (iii) memiliki reaktivitas tinggi, dan (iv) higroskopis. Sekitar 1,8 t batu kapur diperlukan untuk menghasilkan 1 t kapur tohor.
Kalsinasi batugamping, karena reaksi kimia endotermik, membutuhkan masukan energi yang cukup besar. Ketika batu kapur dipanaskan, kalsium karbonat terurai sesuai persamaan berikut.
CaCO3 + sekitar 42,5 kkal kalor =CaO + CO2
Kalsinasi batu kapur adalah proses pembakaran satu tahap sederhana yang dilakukan di tungku poros atau tungku putar. Ini terdiri dari lima langkah proses. Ini adalah (i) perpindahan panas dari lingkungan ke permukaan partikel, (ii) konduksi panas dari permukaan ke bagian depan reaksi, (iii) kinetika kimia di bagian depan, (iv) difusi CO2 melalui lapisan oksida berpori ke permukaan, dan (v ) kemudian transfer ke ambient. Batu kapur dimasukkan ke dalam kiln dan, saat melewati kiln, sedang didekomposisi atau dikalsinasi. Penguraian CaCO3 dimulai pada 810 derajat C.
Proses kalsinasi dapat dijelaskan dengan menggunakan sepotong batu kapur yang terdekomposisi sebagian, yang profil tekanan parsial dan suhu CO2 ditunjukkan pada Gambar 1. Sampel terdiri dari inti karbonat padat yang dikelilingi oleh lapisan berpori. Dalam kiln kalsinasi pada suhu Tgas panas ditransfer oleh radiasi dan konveksi (dilambangkan dengan 'h') ke permukaan padat pada suhu Tsurface. Melalui konduksi termal (A) panas menembus melalui lapisan oksida untuk mencapai bagian depan reaksi, di mana suhu Trc. Karena entalpi reaksi berkali-kali lebih besar daripada energi internal, panas yang mengalir lebih jauh ke dalam inti dapat diabaikan selama reaksi. Oleh karena itu suhu inti hanya sedikit lebih rendah dari suhu depan. Setelah panas disuplai, konstanta reaksi kimia (k) kemudian terjadi di mana gaya penggeraknya adalah deviasi tekanan parsial CO2 dari kesetimbangan (p-eq – p-f). CO2 yang dilepaskan berdifusi (Dp) melalui lapisan oksida berpori ke permukaan dan akhirnya melewati konveksi (B) ke lingkungan di mana permukaan p tekanan parsial CO2 ada. Sifat kimia dan fisika kapur dipengaruhi oleh kalsinasi yang selanjutnya dipengaruhi oleh konduktivitas, koefisien perpindahan massa, dan difusivitas lapisan kapur.

Gambar 1 Profil sampel batugamping selama kalsinasi
Untuk kalsinasi penuh batugamping dan tidak memiliki inti residu batu kapur yang tidak dikalsinasi, panas yang disuplai ke permukaan batu kapur harus menembus melalui perpindahan panas konduktif ke inti. Suhu 900 derajat C harus dicapai di dalam inti setidaknya untuk waktu yang singkat karena atmosfer di dalam material adalah CO2 murni. Permukaan batu kapur harus dipanaskan hingga lebih besar dari 900 derajat C untuk mempertahankan gradien suhu yang diperlukan dan mengatasi efek isolasi dari bahan yang dikalsinasi di permukaan batu kapur. Namun, saat memproduksi kapur tohor, suhu permukaan tidak boleh melebihi 1.100 derajat C hingga 1.150 derajat C karena jika tidak, terjadi kristalisasi ulang CaO dan menghasilkan reaktivitas yang lebih rendah sehingga mengurangi sifat slaking dari kapur tohor.
Retensi atau waktu tinggal tertentu diperlukan untuk memindahkan panas dari gas pembakaran ke permukaan batugamping dan kemudian dari permukaan ke inti batugamping. Potongan batu kapur yang lebih besar membutuhkan waktu lebih lama untuk dikalsinasi daripada potongan yang lebih kecil. Pada prinsipnya, kalsinasi pada suhu yang lebih tinggi mengurangi waktu retensi yang dibutuhkan. Namun, suhu yang terlalu tinggi mempengaruhi reaktivitas produk. Hubungan antara suhu kalsinasi dan waktu retensi yang dibutuhkan untuk berbagai ukuran batugamping ditunjukkan pada Tab 1.
Tab 1 Hubungan antara suhu kalsinasi dan waktu tinggal |
No. Sl. | Ukuran batugamping | Suhu kalsinasi | Waktu tinggal (perkiraan) |
Satuan | mm | derajat C | Jam |
1 | 50 | 1000 | 2.1 |
| | 1200 | 0,7 |
2 | 100 | 1000 | 8,3 |
| | 1200 | 2,9 |
Beberapa jenis kiln yang berbeda digunakan untuk proses kalsinasi. Kiln ini dapat berupa tanur putar atau tanur poros. Jenis kiln yang akan dipilih sangat bergantung pada karakteristik batugamping, perkiraan laju produksi, biaya bahan bakar, biaya investasi, bahan bakar yang tersedia, kondisi lokal, infrastruktur, dan lain-lain. Secara umum, semua data termasuk uji laboratorium harus dievaluasi sebelum memilih kiln kalsinasi.
Rotary kiln, dengan atau tanpa preheater, biasanya mengolah batu kapur dengan ukuran material antara 10 mm dan 50 mm. Keseimbangan panas jenis kiln ini agak dikategorikan oleh kerugian tinggi dengan off-gas dan melalui shell kiln. Nilai tipikal untuk kerugian off-gas berada dalam kisaran sekitar 25% dan untuk kerugian shell kiln berada dalam kisaran sekitar 20% dari total kebutuhan panas. Hanya sekitar 60% energi bahan bakar yang dimasukkan ke dalam kiln dengan preheater yang digunakan untuk proses kalsinasi.
Dalam kasus kiln poros tunggal vertikal, terdapat ketidakseimbangan antara panas yang tersedia dari zona kalsinasi dan panas yang dibutuhkan di zona pemanasan awal. Bahkan dengan proses kalsinasi yang ideal, suhu gas buangan mungkin lebih tinggi dari 100 derajat C. Dalam kasus tipe kiln aliran paralel (PFR), ada pemanfaatan yang lebih baik dari panas zona kalsinasi dan meminimalkan hilangnya panas dalam gas buangan, sehingga konsumsi panas per ton kapur menjadi lebih rendah.
Diagram skema kiln poros tunggal vertikal yang menunjukkan aliran material dan aliran gas, komponen utama tanur kapur putar, dan mekanisme perpindahan panas dalam tanur putar ditunjukkan pada Gambar 2.
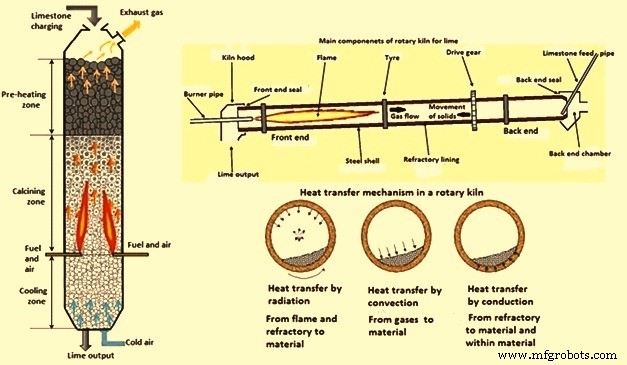
Gbr 2 Diagram skema kiln poros tunggal vertikal, komponen tanur putar dan mekanisme perpindahan panas dalam tanur putar
Perbandingan data untuk kiln berbeda yang biasanya digunakan untuk kalsinasi batu kapur dengan angka konsumsi penting dan ukuran bahan baku yang khas diberikan di Tab 2.
Tab 2 Perbandingan berbagai jenis kiln kalsinasi |
Jenis kiln kalsinasi | Kapasitas Kiln | Ukuran batugamping | Konsumsi bahan bakar spesifik | Konsumsi daya spesifik | Keterangan |
| tpd | mm | kkal/kg | kWh/ton | |
Tempat pembakaran PFR persegi panjang | 100-400 | 30-120 | 810-870 | Sekitar 20 | Kapur yang sangat reaktif dihasilkan |
Kiln PFR melingkar | 300-800 | 30-160 | 810-870 | Sekitar 20 | Kapur yang sangat reaktif dihasilkan |
Tempat pembakaran kapur halus | 200-400 | 15-40 | 790-850 | Sekitar 20 | Kapur yang sangat reaktif dihasilkan |
Kiln poros berbentuk lingkaran | 200-600 | 15-200 | 910-980 | Sekitar 30 | Kandungan CO2 yang tinggi dalam gas buang |
Kiln poros tunggal | 50-300 | 10-100 | 980-1100 | Sekitar 35 | Menghasilkan kapur bakar sedang |
Kiln putar dengan pemanas awal | 300-1200 | 10-50 | 1150-1350 | Sekitar 30 | Kapur yang sangat reaktif dihasilkan, tingkat produksi tinggi dan belerang rendah |
Kiln putar panjang tanpa pemanas awal | 300-1000 | 20-50 | 1600-1700 | Sekitar 20 | Tingkat produksi tinggi, kapur reaktif, dan belerang rendah |
Kalsinasi suspensi | 300-1200 | 0,03-2 | 1300-1400 | | Bahan baku yang sangat halus |
Berikut ini adalah faktor dan parameter operasi yang berpengaruh pada kalsinasi batugamping.
Jenis tungku pembakaran – Ada dua jenis kiln yang digunakan untuk kalsinasi batugamping. Mereka adalah kiln poros vertikal atau kiln putar horizontal. Tergantung pada jenis tungku, ukuran muatan batu kapur berbeda. Dalam tanur vertikal, batu kapur bergerak ke bawah, dan gas panas mengalir ke atas melalui batu kapur, oleh karena itu batu harus cukup besar untuk menyediakan saluran bagi gas pembakaran untuk bergerak ke atas. Kiln ini biasanya menggunakan batugamping dengan ukuran mulai dari 130 mm hingga 200 mm. Dalam jenis kiln ini, kenaikan suhu harus lambat dan oleh karena itu waktu tinggal yang dihasilkan lama. Tanur vertikal hemat bahan bakar, tetapi kapasitasnya terbatas. Dalam kasus kiln horizontal, tubuh kiln berputar, memungkinkan batu kapur jatuh dan memaparkan semua permukaan ke gas panas. Ukuran khas batu kapur untuk jenis kiln ini berkisar antara 25 mm hingga 40 mm. Keseragaman ukuran batugamping untuk pengisian kiln sangat penting untuk proses kalsinasi yang seragam. Namun, dari sudut pandang praktis, ukuran yang ketat itu mahal karena memerlukan banyak penyaringan. Batugamping ukuran kecil seperti 6 mm dan lebih kecil dengan persentase halus tertentu dalam tanur horizontal, cenderung jatuh secara massal, sehingga mengurangi paparan partikel ke gas panas. Proses ini menghasilkan eksposur yang tidak merata, sehingga mengurangi kualitas kapur tohor. Pada tanur vertikal, keberadaan batugamping berukuran sangat kecil menghalangi rongga antara batugamping, mengganggu aliran gas, dan dengan demikian dengan perpindahan panas, menyebabkan kalsinasi yang tidak merata. Selain itu, partikel batu kapur kecil (kurang dari 3 mm) cenderung terdegradasi dan menyebabkan terbentuknya butiran halus yang perlu dihilangkan oleh pengumpul debu.
Ukuran dan gradasi batugamping -Selama proses kalsinasi, disosiasi batugamping biasanya berlangsung secara bertahap dari permukaan ke bagian dalam batugamping. Semakin besar ukuran batugamping, semakin sulit untuk dikalsinasi dan juga membutuhkan lebih banyak waktu. Berbagai macam distribusi ukuran partikel di kiln feed juga mengganggu distribusi panas di kiln. Batu-batu kecil menumpuk di antara rongga yang dibentuk oleh batu-batu besar di tungku pembakaran poros, sehingga menghalangi angin dan aliran api dan gas pembakaran. Juga, selama kalsinasi dari berbagai ukuran batugamping, suhu yang mengkalsinasi ukuran yang lebih kecil secara memadai tanpa kalsinasi berlebihan, hanya mengkalsinasi kulit terluar dari batugamping dengan dimensi yang lebih besar. Oleh karena itu, batugamping dengan gradasi terbatas, terlepas dari ukurannya, jauh lebih mudah untuk dikalsinasi. Ukuran batugamping juga merupakan elemen penting dalam proses kalsinasi. Saat batu kapur memasuki kiln, ia terkena gas panas di dalam kiln. Tingkat penetrasi panas tergantung pada suhu batu kapur dan gas sekitarnya. Selain itu, dibutuhkan waktu panas untuk menembus batu kapur. Semakin kecil ukuran batugamping, semakin pendek waktu penetrasi panasnya. Dalam kasus batu kapur yang dihancurkan, waktu ini bisa menjadi sepersekian menit.
Struktur kristal dan kerapatan batugamping – Struktur kristal batugamping mempengaruhi laju kalsinasi, kekuatan internal batugamping, serta ukuran kristal CaO yang dihasilkan dalam kapur. Kristal yang lebih kecil menggumpal selama kalsinasi, membentuk kristal yang lebih besar, sehingga menyebabkan penyusutan dan pengurangan volume. Temperatur kiln yang lebih tinggi membantu proses aglomerasi. Semakin banyak aglomerasi, semakin banyak penyusutan volume produk akhir. Kepadatan batu kapur dan struktur kristalnya agak terkait. Bentuk kristal menentukan ruang kosong antara kristal, dan dengan demikian, kepadatan batu kapur. Rongga yang lebih besar memungkinkan masuknya gas CO2 dengan mudah selama kalsinasi, tetapi juga menghasilkan pengurangan volume selama kalsinasi. Beberapa jenis batu kapur, karena struktur kristalnya, hancur dalam proses kalsinasi. Jenis batu kapur ini tidak cocok untuk kalsinasi. Ada beberapa jenis batugamping lain yang berperilaku sebaliknya dan menjadi sangat padat selama kalsinasi sehingga mencegah pelepasan CO2 dan menjadi tidak berpori. Sekali lagi, jenis batu kapur ini tidak cocok untuk kalsinasi.
Suhu kalsinasi – Kalsinasi batu kapur dimulai pada sekitar 810 derajat C pada tekanan atmosfer dan dalam atmosfer yang terdiri dari 100% CO2. Disosiasi berlangsung secara progresif dari permukaan luar menuju permukaan dalam. Agar disosiasi menembus bagian dalam batugamping, diperlukan suhu yang lebih tinggi. Temperatur memerlukan peningkatan lebih lanjut agar disosiasi inti batugamping dapat berlangsung. Semakin tinggi ukuran batugamping, semakin tinggi suhu yang diperlukan untuk disosiasi inti karena tekanan internal yang meningkat karena gas CO2 memaksa pelepasannya. Peningkatan suhu memberikan pengaruh yang jauh lebih besar pada laju disosiasi daripada retensi suhu. Selanjutnya, suhu teoritis yang dibutuhkan untuk kalsinasi adalah sekitar 1.000 derajat C. Namun, dalam praktiknya, suhu yang dipertahankan dalam kiln jauh lebih tinggi (sekitar 1350 derajat C). Temperatur yang tepat dalam kiln tergantung pada ukuran batugamping serta jenis kiln dan jenis bahan bakar yang digunakan. Operator tanur biasanya bereksperimen untuk menentukan suhu yang tepat untuk ukuran dan kualitas tertentu dari batu kapur yang digunakan. Secara umum, lebih baik menggunakan suhu terendah dengan waktu tinggal sesingkat mungkin untuk mencapai kalsinasi penuh. Temperatur kalsinasi yang lebih tinggi menyebabkan peningkatan penyusutan dan pengurangan volume. Temperatur kalsinasi yang lebih tinggi juga menyebabkan karbonasi pada permukaan batu kapur yang dikalsinasi, dengan adanya CO2 yang dilepaskan dari batu serta produk sampingan pembakaran, yang membuat kapur tidak berpori, dan dengan demikian kurang reaktif.
Laju kenaikan suhu – Kenaikan suhu harus bertahap dan merata. Ini sangat penting ketika menggunakan batu kapur ukuran besar (100 mm hingga 150 mm). Saat mengkalsinasi batugamping ukuran besar, batugamping harus tetap porous selama proses berlangsung. Saat suhu naik, lapisan luar batu kapur dipanaskan sampai suhu disosiasi, di mana CO2 keluar dari batu kapur, meninggalkan saluran kapiler yang membuat kapur berpori. Saat gas keluar, batu kapur menyusut volumenya sebanyak 40%. Penyusutan volume ini membatasi aliran gas dari pusat batu kapur, mencegah keluarnya gas CO2 tambahan. Waktu tinggal yang terlalu lama memfasilitasi penggabungan CaO dan CO2 kembali ke CaCO3 (karbonasi) pada suhu di atas 1350 derajat C. Jika kenaikan suhu sangat cepat, lapisan luar potongan batugamping terkalsinasi dengan sangat cepat. Saat suhu naik, permukaan potongan batu kapur menyusut dan pori-pori yang dibuat oleh pelepasan CO2 ditutup. Ini menghasilkan peningkatan tekanan internal di dalam batugamping. Karena gas tidak dapat keluar, menyebabkan batu kapur meledak dan hancur. Hal ini menyebabkan produksi butiran halus yang tidak diinginkan mengurangi kualitas kapur tohor yang dihasilkan.
Waktu kalsinasi – Diketahui bahwa terlepas dari jenis batu kapur dan kualitasnya, suhu pembakaran yang lebih tinggi dan periode kalsinasi yang lebih lama menghasilkan kapur yang lebih keras terbakar yang memiliki penyusutan tinggi, kepadatan tinggi, porositas rendah dan reaktivitas kimia rendah. Kebalikannya terjadi pada suhu pembakaran yang lebih rendah dengan durasi kalsinasi yang lebih pendek yang menghasilkan produksi kapur yang sangat reaktif dan terbakar lunak dengan penyusutan dan densitas rendah dan porositas tinggi. Kalsinasi batu kecil dan besar dalam hal pemanasan relatif dan waktu kalsinasi berbanding lurus dengan kuadrat ketebalan (atau diameter rata-rata untuk batu berbentuk tidak beraturan. Waktu retensi di kiln tergantung pada ukuran batu kapur serta kalsinasi suhu Ukuran batugamping adalah elemen yang paling penting untuk kalsinasi. Saat batu kapur memasuki kiln, ia terkena gas panas di dalam kiln. Laju penetrasi panas didasarkan pada perbedaan suhu batu kapur dan suhu gas. Selain perbedaan suhu ini, dibutuhkan waktu panas untuk menembus batugamping. Semakin kecil ukuran batugamping, semakin pendek waktu penetrasi panas. Dalam kasus batugamping yang dihancurkan, waktu ini dapat mengurangi kurang dari 1 menit. Jika retensi terlalu pendek, inti batugamping tetap tidak terkalsinasi, sedangkan permukaan luar terkalsinasi. Jika waktu retensi terlalu lama, n permukaan potongan batu kapur menyusut dan pori-pori yang dibuat oleh gas CO2 keluar dari dekat, menghasilkan permukaan yang kedap air. Kapur jenis ini disebut kapur bakar keras atau kapur bakar mati. Kapur ini memiliki reaktivitas yang sangat rendah dan tidak terkelupas dengan baik. Selain itu, waktu retensi yang lebih lama berarti produksi yang lebih sedikit dan biaya produksi yang lebih tinggi.
Konsentrasi CO2 dalam kiln – Konsentrasi CO2 di atmosfer kiln meningkat dengan pelepasannya dari batu kapur selama kalsinasi. Untuk kalsinasi yang tepat, CO2 harus dihilangkan secara terus menerus. Jika CO2 tidak dihilangkan maka kombinasi konsentrasi CO2 yang tinggi dan suhu kalsinasi yang tinggi menyebabkan karbonasi potongan batugamping yang terkalsinasi dan mengubah CaO kembali menjadi CaCO3. Selain itu, CO2 juga bereaksi dengan pengotor batu kapur.
Reaktivitas kimia – Terdapat hubungan timbal balik antara porositas, densitas dan distribusi ukuran pori. Faktor-faktor ini memberikan pengaruh besar pada sifat terukur standar kapur tohor seperti reaktivitas, kapur yang tersedia dan distribusi ukuran partikel dan luas permukaan. Telah diperhatikan bahwa waktu retensi 1 jam sampai 4 jam memiliki pengaruh yang sangat kecil atau tidak ada sama sekali pada porositas, luas permukaan, atau reaktivitas dalam kisaran suhu kalsinasi dari 950 derajat C sampai 1070 derajat C dan kerapatan curah kapur tohor tetap konstan. . Temperatur kalsinasi yang berlebihan dan periode kalsinasi yang berkepanjangan menyebabkan batu kapur terbakar dengan keras dan ini menghasilkan produksi kapur dengan reaktivitas rendah.
Karakteristik penyusutan – Penyusutan kapur tohor dapat dihitung dari densitas batugamping dan kapur setelah memperhitungkan loss on ignition (LOI). Dihitung dengan rumus S =100*{[100/Ds-(100-L)/Dl]/100*Ds} Dimana S adalah susut dalam persentase, Ds adalah massa jenis batugamping dalam gram/cc, Dl adalah densitas kapur tohor dalam gram/cc dan L adalah kehilangan pengapian batugamping dalam persentase. Penyusutan batugamping memiliki pengaruh besar pada kerapatan curah muatan batu kapur di kiln. Semakin tinggi susut semakin kecil rongga dalam muatan batugamping. Hal ini menyebabkan pengepakan batu kapur di kiln yang menyebabkan penurunan tekanan tinggi di tempat tidur kiln dengan pengaruh yang menyertainya pada aliran gas buang dari kiln.
Kualitas dan jenis bahan bakar – Kualitas dan jenis bahan bakar memiliki pengaruh besar pada efisiensi kiln dan kualitas kapur yang dihasilkan. Bahan bakar mentah padat seperti kayu, arang dan batu bara telah digunakan sejak awal. Batubara bubuk, gas produser, gas alam dan bahan bakar minyak digunakan di kiln. Gas alam adalah bahan bakar yang paling nyaman dan gas produser adalah yang paling merepotkan. Pilihan akhir bahan bakar juga ditentukan oleh pertimbangan lingkungan karena beberapa bahan bakar memiliki kecenderungan lebih tinggi untuk mencemari lingkungan melalui emisi berbahaya. Biasanya, tanur vertikal menggunakan minyak atau gas alam untuk bahan bakar, sedangkan tanur putar horizontal menggunakan batu bara. Namun, kedua jenis kiln dapat menggunakan bahan bakar ini. Minyak dan batubara mengandung persentase tertentu dari senyawa belerang yang dapat bervariasi dari 0,5% hingga 3%. Sulfur biasanya bergabung dengan CaO pada suhu yang sesuai dan menghasilkan kalsium sulfida atau kalsium sulfat. Hal ini umumnya terjadi pada permukaan bahan yang dikalsinasi dan membuat bahan tidak berpori, sehingga mengurangi reaktivitasnya. Selain itu, persentase abu yang tinggi dalam batubara mengakibatkan penumpukan pada refraktori di rotary kiln, sehingga mengganggu aliran muatan batu kapur di kiln. Kiln harus didinginkan secara berkala dan abu yang menumpuk dihilangkan secara manual yang merupakan operasi yang sangat membosankan dan mahal. Gas alam adalah bahan bakar terbersih dan sebagian besar digunakan dalam tanur vertikal.
Jenis ketiga pengolahan batu kapur terdiri dari produksi kapur terhidrasi, yang merupakan bubuk kering yang diperoleh dengan mengolah kapur dengan air yang cukup untuk memenuhi afinitas kimianya terhadap air, sehingga mengubah oksida menjadi hidroksida. Kapur terhidrasi juga kadang-kadang disebut kapur mati. Untuk desulfurisasi gas buang, karakteristik kapur terhidrasi memerlukan peningkatan kehalusan rata-rata, luas permukaan yang lebih tinggi, dan volume pori yang lebih besar. Reaksi hidrasi secara kimia sederhana tetapi sangat eksotermik, dengan pembangkitan panas sekitar 276 kkal/kg CaO. Reaksi diberikan di bawah ini.
CaO + H2O =Ca(OH)2 + kalor
Sebagai perbandingan, panas eksotermis yang dihasilkan dari hidrasi 1.000 ton kapur berkalsium tinggi sama dengan nilai panas total sekitar 35 ton batu bara. Istilah hidrasi dan slaking cukup sering digunakan secara bergantian. Namun, ada perbedaan yang pasti dan berbeda. Hidrasi biasanya didefinisikan sebagai proses di mana sekitar jumlah stoikiometrik air dan kapur bereaksi untuk membentuk produk, hidrat, yang merupakan bubuk kering. Ini mengandung kurang dari 1% dari kelembaban bebas dan ditangani sebagai bubuk. Slaking di sisi lain didefinisikan sebagai proses di mana kapur direaksikan dengan sejumlah air berlebih untuk membentuk bubur kapur yang ditangani sebagai cairan.
Hidrasi yang cepat cenderung menghasilkan partikel yang lebih halus, karena kristal hidrat memiliki peluang yang lebih kecil untuk menggumpal. Namun, reaksi paling cepat belum tentu merupakan kondisi terbaik. Pada prinsipnya reaksi kapur reaktif tinggi yang khas berkembang dalam tiga fase yang berbeda (Gambar 3). Fase-fase ini disebut sebagai (i) kinetik, (ii) sementara, dan (iii) difusi. Fase kinetik biasanya sangat singkat (kurang dari 10 detik), dan menunjukkan peningkatan suhu yang tajam, yang dapat mencapai 50% dari total kenaikan suhu. Panjang fase peralihan (seringkali kurang dari satu menit) dapat berubah karena ukuran gumpalan kapur yang diumpankan ke hidrator. Ini menunjukkan tikungan yang terlihat dari kenaikan suhu. Pada fase difusi, suhu kembali meningkat tajam hingga merata dengan cepat untuk menunjukkan akhir reaksi.
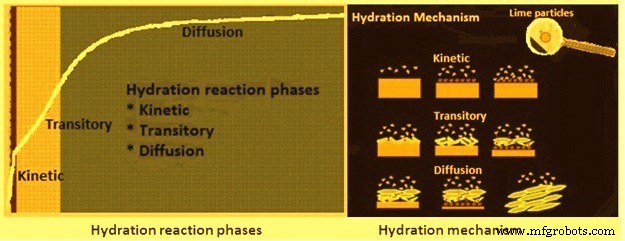
Gbr 3 Fase reaksi hidrasi dan mekanisme hidrasi
Mekanisme hidrasi juga ditunjukkan pada Gambar 3. Mekanisme hidrasi partikel kapur menunjukkan bahwa setelah kontak awal dengan air reaksi dimulai sangat kuat dalam beberapa detik karena kontak terhalang antara kapur dan air. Setelah lapisan pertama kapur terhidrasi sebagian terbentuk di permukaan, ia bertindak sebagai pelindung lapisan kapur cepat di bawahnya karena cenderung tetap berada di dekat permukaan partikel. Oleh karena itu, lapisan kapur yang terhidrasi sebagian menunda penetrasi air. Ketika kristal Ca(OH)2 secara bertahap terbentuk ke bentuk akhirnya, mereka mulai terpisah. Ini meningkatkan penetrasi air yang melanjutkan tren reaksi. Faktor lain yang penting adalah perkembangan reaksi merupakan fungsi dari ukuran gumpalan kapur tohor.
Aplikasi kapur dan kapur di pabrik besi dan baja
Selama produksi besi dengan rute tanur sembur (BF), batu kapur ditambahkan baik dalam proses sintering atau sebagai umpan langsung di tanur sembur. Batu kapur biasanya ditambahkan selama pembuatan besi untuk mendapatkan terak BF dasar netral atau sedikit. Penambahan batugamping melalui sinter lebih disukai karena CO2 dari batugamping dikeluarkan selama proses sintering. Dalam kasus sintering, batu kapur dihancurkan hingga -3 mm (dalam kisaran 85 % hingga 90 %) dalam hammer crusher sebelum mencampurnya dalam campuran sinter. Dalam hal umpan langsung ke tanur sembur, gumpalan batu kapur berukuran 10 mm hingga 40 mm digunakan.
Dalam hal penambahan batugamping melalui sintering, saat ini juga langsung digunakan batugamping terkalsinasi (kapur). Penggunaan kapur tohor dalam proses sintering memiliki keuntungan antara lain (i) Peningkatan sifat pengikatan campuran sinter, (ii) peningkatan produktivitas mesin sintering, (iii) peningkatan kekuatan sinter, dan (iv) pengurangan volume gas buang dengan keuntungan terkait.
Kandungan silika (SiO2) yang tinggi pada batugamping yang digunakan untuk tujuan sintering lebih disukai karena SiO2 melawan efek alumina (Al2O3) dalam tanur tinggi.
Penggunaan utama kedua dari batu kapur adalah dalam pembuatan baja. Ini digunakan untuk menjaga kebasaan terak (CaO/SiO2) sekitar 3. Dalam pembuatan baja, batu kapur digunakan dalam bentuk terkalsinasi. Untuk digunakan dalam pembuatan baja, kandungan SiO2 (karena sifatnya yang asam) dalam batugamping harus sangat rendah, sebaiknya kurang dari 1%. Juga, reaktivitas kapur menjadi sangat baik, karena waktu yang tersedia lebih sedikit karena proses pembuatan baja adalah proses yang sangat cepat. Seluruh proses pembuatan baja membutuhkan waktu kurang dari 20 menit untuk diselesaikan.
Penggunaan kecil kapur (baik yang dikalsinasi atau terhidrasi) terdiri dari zat desulfurisasi, pelapis cetakan mesin pig casting, penetralan air asam, pengolahan air, pengolahan air limbah (efluen), pengolahan gas buang, dan pengolahan lumpur dan limbah dll. Kapur kadang-kadang juga ditambahkan sebagai komponen terak sintetis.