Teknologi Penangkapan dan Penyimpanan Karbon
Teknologi Penangkapan dan Penyimpanan Karbon
Penangkapan dan penyimpanan karbon juga disebut sequestration (CCS) melibatkan penangkapan, pengangkutan, injeksi dan penahanan CO2 (karbon di-oksida) dalam struktur geologi seperti reservoir minyak dan gas yang terkuras, akuifer salin di darat dan lepas pantai yang terletak jauh di dalam kerak bumi, gua garam atau lapisan batubara yang tidak dapat ditambang. Ini merupakan pendekatan untuk meningkatkan produksi dari operasi minyak dan gas yang ada serta cara untuk mengurangi emisi gas rumah kaca (GRK).
CCS memberikan alternatif tambahan dalam pemanfaatan energi berbasis bahan bakar fosil, sekaligus memberikan waktu transisi tambahan bagi sistem energi untuk beralih ke bahan bakar yang dikurangi karbon (C) atau nol C, seperti energi terbarukan. Ada sejumlah manfaat ekonomi dan sosial dari CCS seperti (i) pengurangan emisi CO2 ke atmosfer, sehingga berpotensi mengurangi perubahan iklim yang berbahaya, (ii) inovasi, akses ke teknologi mutakhir, penciptaan lapangan kerja dan pembangunan ekonomi yang berkelanjutan dan lebih berkelanjutan, (iii) aliran pendapatan sekunder karena emisi GRK yang ditangkap dan disimpan dapat diubah menjadi komoditas yang dapat diperdagangkan yang dapat dijual di pasar internasional, (iv) pengurangan polusi udara karena polutan yang berpotensi berbahaya telah harus dihilangkan untuk mengakomodasi penangkapan CO2, dan peluang untuk meningkatkan pemulihan minyak dan gas.
Ada beberapa tantangan untuk penyebaran CCS. Beberapa tantangan untuk CCS termasuk (i) mengurangi biaya penangkapan dan meningkatkan proses penangkapan, (ii) mengidentifikasi dampak lingkungan dari penangkapan, (iii) menentukan implikasi dari peningkatan tekanan dalam formasi penyimpanan, (iv ) menentukan ke mana air yang dipindahkan mengalir dalam injeksi skala besar dan apa risikonya terhadap air tanah, (v) bagaimana memprediksi secara andal ukuran gumpalan CO2 dan ke mana ia bermigrasi, (vi) bagaimana mendapatkan kepercayaan dalam pemilihan lokasi, (vii) mengembangkan strategi pemantauan dan batasan deteksi yang hemat biaya, (viii) melibatkan industri keuangan dan asuransi, (ix) kepastian peraturan dan politik yang lebih besar di semua tingkat pemerintahan, (x) melatih tenaga kerja untuk penyebaran skala besar, dan (xi) meningkatkan kesadaran dan penerimaan publik.
Teknologi CCS dapat diterapkan pada proses dengan emisi skala besar, termasuk pembangkit listrik berbahan bakar batu bara dan gas, pemrosesan gas alam dan produksi pupuk, serta pembuatan bahan industri seperti besi dan baja, semen, serta pulp dan kertas. dll. Penerapan teknologi CCS pada proses ini dapat memainkan peran utama dalam mengurangi emisi GRK. Teknologi pemisahan dan penangkapan karbon telah beroperasi dalam skala besar di industri gas alam dan pupuk selama beberapa dekade. Teknologi yang terlibat dalam sistem CCS memiliki empat komponen yaitu (i) penangkapan, (ii) transportasi, (iii) injeksi, dan (iv) pemantauan.
Tangkapan adalah pemisahan CO2 dari aliran limbah dan kompresinya ke keadaan cair atau superkritis. Dalam kebanyakan kasus saat ini, konsentrasi CO2 yang dihasilkan lebih dari 99%, meskipun konsentrasi yang lebih rendah dapat diterima. Penangkapan biasanya diperlukan untuk dapat mengangkut dan menyimpan CO2 secara ekonomis.
Transportasi terdiri dari pengangkutan CO2 dari sumbernya ke reservoir penyimpanan. CO2 dikeringkan dan biasanya dikompresi sebelum diangkut ke penyimpanan. Kompresi membuat pengangkutan gas lebih efisien. CO2 digunakan secara komersial di sejumlah industri, terutama industri minuman, dan telah diangkut dalam skala besar untuk digunakan dalam pengambilan minyak dari reservoir (enhanced oil recovery). Meskipun pengangkutan dengan truk, kereta api, dan kapal memungkinkan, pengangkutan CO2 dalam jumlah besar paling ekonomis dicapai dengan pipa. Infrastruktur saluran pipa utama perlu dibangun untuk mengimplementasikan CCS dalam skala besar, dan ini menghadirkan tantangan.
Injeksi terdiri dari penyimpanan CO2 ke dalam reservoir penyimpanan. Reservoir penyimpanan bawah tanah tergantung pada formasi geologi. Keamanan penyimpanan CO2 sangat penting. Risiko lokal penyimpanan CO2 mencakup (i) kebocoran CO2 dari lokasi penyimpanan, (ii) perubahan kimia air tanah dan air minum, dan (iii) perpindahan cairan yang berpotensi berbahaya yang dapat berada di reservoir tempat CO2 disimpan. Reservoir potensial meliputi laut dalam, sedimen laut, atau mineralisasi (konversi CO2 menjadi mineral). Sementara beberapa penggunaan komersial CO2 dimungkinkan, jumlah yang dapat digunakan dibandingkan dengan jumlah CO2 yang dipancarkan sangat kecil.
Setelah CO2 disuntikkan, lokasi penyimpanan harus dipantau untuk menunjukkan bahwa CO2 tetap berada di reservoir. CO2 tidak beracun atau mudah terbakar sehingga hanya menimbulkan risiko lingkungan, kesehatan, dan keselamatan yang minimal. Tujuan utama pemantauan adalah untuk memastikan bahwa operasi sekuestrasi efektif, artinya hampir semua CO2 tetap berada di luar atmosfer selama berabad-abad. Program pemantauan dimulai sebelum injeksi untuk menetapkan data dasar. Pemantauan selama fase operasional adalah untuk merekam perilaku dinamis CO2 saat disuntikkan dan di dalam reservoir. Setelah injeksi berhenti, program pemantauan harus dirancang untuk memastikan bahwa penyimpanan CO2 memenuhi kondisi lingkungan dan keselamatan yang diperlukan. Program pemantauan mencakup tiga domain pemantauan yaitu (i) domain bawah permukaan (reservoir), (ii) domain dekat permukaan (zona dangkal dan tanah), dan (iii) domain atmosfer, termasuk sumur, patahan, dan fitur geologi lainnya.
Teknologi penangkapan CO2
CO2 dapat ditangkap dari sumber emisi stasioner besar, seperti fasilitas produksi gas alam (di mana CO2 sudah dipisahkan dari gas lain, sebagai bagian dari proses), pembangkit listrik berbahan bakar fosil, pabrik besi dan baja, pabrik semen dan beberapa pabrik kimia . Tidak seperti dua komponen CCS lainnya, transportasi dan penyimpanan geologis, komponen pertama CCS yaitu penangkapan CO2 hampir seluruhnya bergantung pada teknologi dan merupakan langkah yang paling mahal. Teknologi untuk menangkap CO2 dari sumber-sumber ini diadaptasi dari teknologi pemisahan CO2 yang saat ini digunakan di industri seperti industri gas alam dan produksi amonia (NH3) dan juga dari teknologi yang digunakan dalam industri pemisahan udara. Teknologi baru juga sedang dikembangkan.
Teknologi pemisahan utama untuk menangkap CO2 saat ini adalah (i) menggunakan pelarut cair untuk menyerap CO2 (penyerapan), (ii) menggunakan bahan padat untuk menarik CO2 ke permukaan, di mana ia menjadi terpisah dari gas lain (adsorpsi), dan (iii) menggunakan membran untuk memisahkan CO2 dari gas lainnya. Teknologi lainnya termasuk teknologi perulangan kimia (oksida logam bereaksi dengan bahan bakar, menciptakan partikel logam, CO2 dan uap air), suhu rendah atau proses pemisahan kriogenik (yang bergantung pada suhu perubahan fase yang berbeda untuk berbagai gas untuk memisahkannya) dan padatan kering yang dapat diregenerasi. proses.
Teknologi pesaing utama untuk penangkapan CO2 dari penggunaan bahan bakar fosil adalah (i) penangkapan pasca pembakaran (PCC) dari gas buang pabrik berbasis pembakaran, (ii) penangkapan pra pembakaran dari syngas di pabrik berbasis gasifikasi, dan (iii) oxy pembakaran melalui pembakaran langsung bahan bakar dengan oksigen. Sebagian besar proses pembakaran saat ini menggunakan udara, dan gas buang yang dihasilkan biasanya mengandung konsentrasi CO2 yang rendah (kurang dari 20 %), dan karenanya, lebih cocok untuk teknologi penangkapan pasca-pembakaran
Teknologi penangkapan pasca pembakaran
Penangkapan pasca-pembakaran dapat dianggap sebagai bentuk pembersihan gas buang. Proses ini ditambahkan ke bagian belakang pabrik, setelah sistem pengendalian polusi lainnya. Integrasi panas dengan pembangkit diperlukan agar hemat biaya.
Electric Power Research Institute (EPRI) telah menetapkan pada tahun 2009 bahwa ada lebih dari 50 konsep penangkapan CO2 pasca-pembakaran yang sedang dikembangkan yang dapat dikelompokkan ke dalam beberapa jenis proses fisik/kimia. Kelompok jenis proses ini adalah (i) penyerapan kimia, (ii) adsorpsi, (iii) membran, (iv) biologis, dan (v) lainnya. Masing-masing kelompok yang berbeda ini memiliki manfaat dan kekurangan yang berbeda, serta penerapan dalam situasi yang berbeda. Ada banyak perkembangan sehubungan dengan dua kelompok pertama.
Proses penyerapan kimia – Ini melibatkan satu atau lebih reaksi kimia reversibel antara CO2 dan larutan berair dari penyerap, seperti pelarut berbasis mono-etanol-amina (MEA), dan amina kinerja tinggi (metildietanolamina teraktivasi, aMDEA) dll. Saat memanaskan produk, ikatan antara penyerap dan CO2 dapat diputus, menghasilkan aliran yang diperkaya dengan CO2. Proses penyerapan kimia untuk memisahkan CO2 dari gas buang dipinjam dari industri pengolahan gas. Proses berbasis amina sedang digunakan secara komersial untuk menghilangkan pengotor gas asam (CO2 dan H2S) dari aliran gas proses. Oleh karena itu, ini merupakan teknologi yang telah terbukti dan terkenal.
Rumus mono-etanol-amina adalah H2NCH2CH2OH. Amina adalah sekelompok senyawa organik, yang dapat dianggap berasal dari amonia (NH3) dengan penggantian satu atau lebih atom H2 oleh radikal organik. Gugus pengganti (R) dapat berupa alkil, aril atau aralikl. Bila (R) adalah alkil, amina disebut alkanolamina. Secara umum, dapat dianggap bahwa gugus hidroksil berfungsi untuk mengurangi tekanan uap dan meningkatkan kelarutan dalam air, sedangkan gugus amino memberikan alkalinitas yang diperlukan dalam larutan air untuk menyerap gas asam. Akanolamina menghilangkan CO2 dari aliran gas buang melalui reaksi eksotermik CO2 dengan fungsi amina dari alkanolamina. Amina komersial untuk menangkap CO2 larut dalam air.
Amina diklasifikasikan menurut jumlah atom H2 amonia yang telah digantikan oleh radikal seperti (i) amina primer (RNH2) di mana satu atom H2 telah diganti, (ii) amina sekunder (R2NH) di mana dua atom H2 telah diganti, dan (iii) amina tersier (R3N) di mana ketiga atom H2 telah diganti.
Amina primer termasuk mono-etanol amina (MEA) dan diglikolamin (DGA). MEA telah menjadi pelarut pilihan tradisional untuk penyerapan CO2 dan penghilangan gas asam secara umum. MEA adalah alkanolamina yang paling murah. Kinetika reaksinya cepat dan bekerja dengan baik pada tekanan rendah, dan konsentrasi CO2 rendah. Namun, ada beberapa kelemahan.
Pertama, ia memiliki panas reaksi yang tinggi dengan CO2, yang berarti energi tingkat tinggi harus disuplai dalam langkah regenerasi. Kedua, absorptivitas MEA dengan CO2 tidak tinggi. Dalam kasus alkanolamina primer dan sekunder pembentukan karbamat (RNHCOO-) adalah reaksi utama. Persamaan reaksinya adalah CO2 + 2RNH2 =RNHCOO- + RNH3+. Dalam reaksi ini, dua mol MEA harus digunakan untuk menangkap satu mol CO2. Ketiga, kapasitas penyerapan penuh atas MEA tidak terwujud dalam praktik karena masalah korosi. Efek korosi disebabkan oleh CO2 terlarut dan bervariasi dengan amina yang digunakan.
Konsentrasi MEA dalam fase air dengan adanya O2 dibatasi hingga 20% berat. Selain itu, MEA memiliki tekanan uap tertinggi dari semua alkanolamina dan pelarut yang terbawa tinggi dapat terjadi selama penghilangan CO2 dari aliran gas dan dalam langkah regenerasi. Untuk mengurangi kehilangan pelarut, umumnya diperlukan pencucian air dari aliran gas murni. Selain itu, MEA bereaksi secara ireversibel dengan pengotor kecil seperti COS dan CS2 yang mengakibatkan degradasi pelarut. Busa dari MEA cairan penyerap karena penumpukan kotoran juga bisa menjadi perhatian.
Untuk sistem penyerap MEA saat ini, laju adsorpsi dan desorpsi cukup tinggi, sehingga kinetika reaksi baik. Namun, pengemasan dalam absorber (kontaktor, untuk memfasilitasi perpindahan massa yang efisien) merupakan biaya yang signifikan, dan konsumsi energinya juga signifikan untuk penangkapan CO2 dari gas buang. Selain itu, suhu pengupasan tidak boleh terlalu tinggi (sekitar 150 derajat C). Jika tidak, dimerisasi karbamat dapat terjadi, memperburuk kemampuan penyerapan MEA.
Amina sekunder termasuk diethanolamine (DEA), di-isopropylamine (DIPA). Amina sekunder memiliki keunggulan dibandingkan amina primer. Panas reaksinya dengan CO2 lebih rendah (360 kalori/gram) dibandingkan 455 kalori/gram) untuk amina primer. Ini berarti bahwa amina sekunder membutuhkan lebih sedikit panas dalam langkah regenerasi daripada amina primer. Namun, ia memiliki semua masalah lain dari amina primer.
Amina tersier termasuk trietanolamin (TEA) dan metil-dietanolamin (MDEA). Amina tersier bereaksi lebih lambat dengan CO2 daripada amina primer dan sekunder sehingga membutuhkan laju sirkulasi cairan yang lebih tinggi untuk menghilangkan CO2 dibandingkan dengan amina primer dan sekunder. Ini dapat ditingkatkan melalui penggunaan promotor. Keuntungan utama amina tersier adalah kebutuhan panasnya yang lebih rendah untuk pembebasan CO2 dari pelarut yang mengandung CO2. Amina tersier menunjukkan kecenderungan yang lebih rendah untuk membentuk produk degradasi yang digunakan daripada amina primer dan sekunder, dan lebih mudah diregenerasi. Selain itu, amina tersier memiliki laju korosi yang lebih rendah dibandingkan dengan amina primer dan sekunder. Kelemahan utama adalah laju reaksinya terlalu lambat.
Sebuah flowsheet khas dari proses penyerapan kimia untuk pemulihan CO2 dari gas buang ditunjukkan pada Gambar 1. Selama operasi penyerapan amina, aliran gas limbah dan larutan amina cair dihubungi oleh aliran berlawanan di menara absorpsi (atau penyerap).
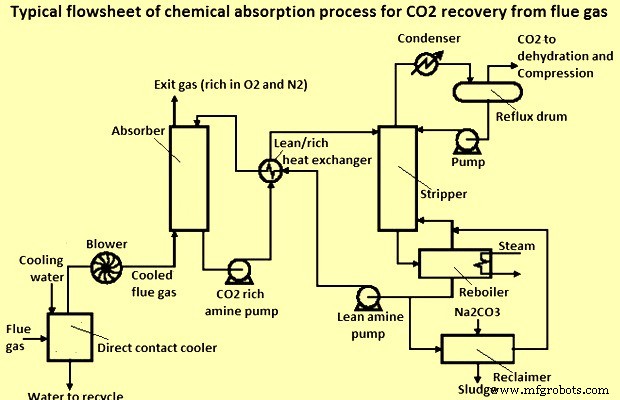
Gbr 1 Flowsheet khas proses penyerapan bahan kimia untuk pemulihan CO2 dari gas buang
Gas buang pembakaran yang keluar dari cerobong panas (sekitar 240 derajat C), dan pada tekanan atmosfer. Gas buang yang masuk ke absorber pada suhu tinggi dapat menyebabkan degradasi pelarut dan penurunan efisiensi penyerapan. Gas buang harus didinginkan sampai titik embun air 50 derajat C, memasuki penyerap. Penyerap biasanya beroperasi pada suhu kurang dari 50 derajat C. Hal ini dicapai dengan menyemprotkan air pendingin ke dalam pendingin kontak langsung.
CO2 dalam gas buang didinginkan sebelum memasuki absorber dimana ia bereaksi dengan amonium karbonat membentuk amonium bikarbonat. NH3 dilepaskan sebagai gas dari larutan pelarut ketika CO2 diserap, dan suhu dijaga tetap rendah untuk meminimalkan hal ini. Gas yang meninggalkan penyerap melewati pencucian air untuk menghilangkan amonia. Amonium bikarbonat dipanaskan dalam regenerator, memisahkan CO2. Pelarut amonium karbonat dikembalikan ke absorber. Air dan NH3 dikeluarkan dari aliran CO2 meninggalkan kolom stripper.
Blower dipasang untuk memberikan tekanan yang cukup pada gas buang agar dapat melewati sistem absorpsi-desorpsi. Gas buang yang akan digosok dari CO2 biasanya masuk ke absorber di bagian bawah, mengalir ke atas, dan keluar di bagian atas, sedangkan pelarut masuk ke bagian atas absorber, mengalir ke bawah (menghubungi gas), dan muncul di bagian bawah. Pengenceran amina yang bersirkulasi dengan air dilakukan untuk mengurangi viskositas fluida yang bersirkulasi. Cairan dengan viskositas yang lebih tinggi membutuhkan lebih banyak daya untuk memompa dan menyediakan sirkulasi. Larutan amina cair yang mengandung gas yang diserap kemudian mengalir ke unit regenerasi (stripper) di mana ia dipanaskan dan gas asam dibebaskan. Regenerasi pelarut dapat dilakukan pada tekanan rendah untuk meningkatkan desorpsi CO2 dari cairan. Beberapa larutan amina biasanya terbawa dalam aliran gas asam dari langkah regenerasi dan larutan amina diperoleh kembali dengan menggunakan kondensor, untuk menghindari kehilangan pelarut yang berlebihan. Larutan lean amine yang panas kemudian mengalir melalui penukar panas di mana ia dikontakkan dengan larutan rich amine dari menara kontak dan dari sana larutan lean amine dikembalikan ke menara kontak gas, yaitu penyerap.
Dalam hal proses scrubber amina, dengan amina kinerja tinggi (metildietanolamina teraktivasi, aMDEA), proses lengkap (amina dan kompresi hingga tekanan 110 kg/sq cm) membutuhkan sekitar 1,6 ton uap bertekanan rendah dan daya 160 kWh per ton CO2 ditangkap.
Ada beberapa keterbatasan proses berbasis amina dan yang telah menghasilkan kemajuan teknologi. Teknologi amine scrubbing di masa lalu berfokus pada penghilangan H2S (hidrogen sulfida) untuk sektor gas alam. Namun, persyaratannya berbeda untuk pemulihan CO2 dari gas buang. Salah satu tantangannya adalah rendahnya tekanan gas buang untuk penyerapan CO2. Selain itu, pengotor dalam gas buang seperti O2, sulfur oksida (SO2,SO3), nitrogen oksida, dan partikel menciptakan tantangan khusus selama proses pemisahan.
Singkatnya, pemulihan CO2 dari gas buang pembakaran memerlukan sejumlah besar pemrosesan pra-perawatan untuk menghindari kesalahan dalam langkah penyerapan pelarut. Ini menambah biaya penangkapan CO2. Namun, perbaikan signifikan dapat dilakukan dalam proses penyerapan pelarut dalam hal mengoptimalkan komposisi amina penyerap dan kontaktor gas-cair, untuk mengelola hal ini.
Penyerapan fisik – Untuk penyerapan fisik, CO2 diserap secara fisik dalam pelarut menurut Hukum Henry. Kapasitas penyerapan pelarut organik atau anorganik untuk CO2 meningkat dengan meningkatnya tekanan dan dengan penurunan suhu. Penyerapan CO2 terjadi pada tekanan parsial CO2 yang tinggi dan suhu rendah. Pelarut kemudian diregenerasi dengan pemanasan atau pengurangan tekanan. Keuntungan dari metode ini adalah membutuhkan energi yang relatif sedikit; tetapi CO2 harus berada pada tekanan parsial tinggi.
Adsorpsi fisik padat – Proses adsorpsi terdiri dari dua langkah utama yaitu (i) adsorpsi, dan (ii) desorpsi. Kelayakan teknis suatu proses ditentukan oleh langkah adsorpsi, sedangkan langkah desorpsi mengontrol kelayakan ekonominya. Adsorpsi membutuhkan afinitas yang kuat antara adsorben dan komponen yang akan dihilangkan dari campuran gas (dalam hal ini, CO2). Namun, semakin kuat afinitasnya, semakin sulit untuk mendesorbsi CO2 dan semakin tinggi energi yang dikonsumsi dalam meregenerasi adsorben untuk digunakan kembali pada siklus berikutnya. Oleh karena itu, langkah desorpsi harus sangat hati-hati diseimbangkan dengan langkah adsorpsi agar proses keseluruhan berhasil.
Proses adsorpsi cukup menarik untuk mekanisme penangkapan CO2, meskipun memiliki kelemahan seperti rendahnya kapasitas adsorben dan pengaruh kontaminan seperti SO2, dan H2O pada proses pemisahan. Ada juga keuntungan dari proses ini seperti ketersediaan, fleksibilitas, operasi proses yang sepenuhnya otomatis dan produksi produk dengan kemurnian tinggi. Pemisahan dapat dilakukan dengan adsorpsi ayunan tekanan (PSA) (Gambar 2), adsorpsi ayunan tekanan vakum (VPSA), adsorpsi ayunan suhu (TSA), adsorpsi ayunan tekanan-suhu (PTSA), atau adsorpsi ayunan listrik (ESA). proses. Tempat tidur instalasi diisi dengan adsorben padat. Selektivitas tergantung pada perbedaan kesetimbangan adsorpsi atau laju adsorpsi dan pada efektivitas (konsentrasi dan pemulihan) memiliki signifikansi pada konfigurasi siklus, waktu adsorpsi, tekanan adsorpsi dan desorpsi, suhu selama proses serta jenis adsorben yang diterapkan.
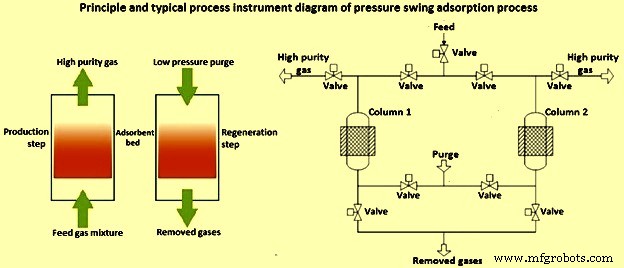
Gbr 2 Proses adsorpsi ayunan tekanan
Keuntungan utama adsorpsi fisik dibandingkan penyerapan kimia adalah operasi dan regenerasinya yang sederhana dan hemat energi, yang dapat dicapai dengan ayunan tekanan atau siklus perubahan suhu (perubahan tekanan atau suhu saat proses melewati siklus penyerapan-desorpsi secara berurutan. untuk mencapai pemisahan). Adsorpsi ayunan tekanan adalah proses komersial untuk pemisahan H2 dari campuran H2 dan CO2 dalam produksi H2.
Ada kemajuan signifikan dalam pengembangan adsorben untuk penghilangan CO2 dari gas buang. Bahan adsorpsi utama yang digunakan adalah zeolit. Zeolit lebih efektif untuk pemisahan CO2 dari spesies yang polaritasnya lebih rendah daripada CO2, sehingga keberadaan air dan SOx dalam aliran gas buang menimbulkan masalah.
Adsorben baru telah dipertimbangkan dan dikembangkan seperti karbon, silika-aluminat mesopori (misalnya kerangka imidazolat zeolitik, ZIF) dan kerangka organik logam (MOF). Adsorben berbasis karbon memiliki potensi untuk diregenerasi dengan menerapkan tegangan listrik, (ESA). Bahan baru yang sedang diselidiki termasuk turunan hidroksida ganda berlapis (LDH dan LDO). Kemajuan lainnya termasuk memfungsikan pori-pori bahan penyerap dengan memasukkan amina untuk meningkatkan pemuatan CO2. Dalam hal ini, CO2 dipisahkan melalui proses kemisorpsi.
Proses baru sedang dikembangkan untuk menangani aliran gas buang kelembaban tinggi dan kotoran. Ini termasuk tempat tidur adsorben berlapis-lapis. Lapisan berlapis-lapis memungkinkan penggunaan adsorben dengan selektivitas CO2 yang tinggi tetapi mereka terdegradasi secara signifikan dengan adanya air.
Teknologi penangkapan pra-pembakaran
Teknologi penangkapan pra-pembakaran melibatkan penghilangan polutan dan CO2 dalam pengolahan hulu bahan bakar fosil sebelum pembakarannya untuk pemulihan panas (melalui uap), atau produksi tenaga listrik atau H2.
Kelemahan dari penangkapan C pasca-pembakaran adalah konsentrasi CO2 yang rendah dalam gas buang yang menyebabkan penalti energi yang relatif tinggi dan biaya penangkapan C yang tinggi. Pra-pembakaran berusaha untuk mengurangi hukuman ini dengan mendekarbonisasi aliran proses yang kaya CO2 sebelum pembakaran bahan bakar kaya H2 yang tersisa. Untuk mencapai dekarbonisasi bahan bakar hidrokarbon, mereka terlebih dahulu diubah menjadi syngas melalui gasifikasi bahan bakar dengan O2 (atau udara). Syngas adalah campuran dari CO (karbon monoksida), H2, CO2, dan air, tergantung pada proses konversi dan bahan bakar dan komponen lainnya.
Syngas adalah produk antara, yang kemudian dapat dikonversi untuk menghasilkan (i) H2, (ii) tenaga listrik terintegrasi, menggunakan reaksi pergeseran air-gas, atau (iii) pembangkitan poli di mana berbagai produk energi dapat berada di sana termasuk listrik, panas, H2 dan synfuels dan bahan kimia lainnya. Proses yang terlibat dengan masing-masing produk energi akhir ini dijelaskan di bawah ini.
Produksi H2 dengan reformasi metana – Metode yang paling banyak digunakan saat ini untuk memproduksi H2 adalah dengan katalitik steam reforming metana (CH4). Reaksi reformasi konversi CH4 dan H2 O menjadi CO dan H2 bersifat endoterm. Reaksi dilakukan di atas katalis Ni (nikel) pada suhu tinggi dalam tungku pembakaran langsung berbahan bakar CH4. Katalis diracuni oleh S (sulfur), sehingga setiap S yang ada dalam umpan harus dihilangkan. Syngas selanjutnya dilewatkan melalui catalytic water-shift converter, di mana CO direaksikan secara eksotermis dengan uap untuk menghasilkan H2 dan produk sampingan CO2. Produk sampingan ini kemudian dihapus dari sistem. Gas buang masih mengandung nilai kalor yang signifikan, sehingga dibakar untuk menghasilkan uap atau tenaga listrik.
Gasifikasi batubara – Teknologi gasifikasi dapat menghasilkan aliran gas, yang tinggi CO2 dan pada tekanan sedang. Batubara umpan digasifikasi dalam O2 (atau udara) untuk menghasilkan syngas. Syngas didinginkan hingga 200 derajat C dalam pendingin syngas yang menghasilkan uap suhu tinggi dan suhu rendah. Kemudian digeser lebih jauh dalam reaktor perpindahan gas air suhu rendah. Reaktor pergeseran gas air adalah reaktor katalitik di mana CO direaksikan dengan uap untuk menghasilkan lebih banyak H2 dan CO2. Gas kemudian didinginkan hingga 35 derajat C dalam persiapan untuk penghilangan gas asam. Kira-kira 99% dari H2S dihilangkan dari syngas dengan penyerapan fisik dan diubah menjadi unsur belerang. Unit PSA dapat digunakan untuk memisahkan 85% H2 dari syngas bebas S. H2 meninggalkan sekitar 60 kg/cm persegi dan kemurnian tinggi (lebih besar dari 99,99%). CO2 dapat dibersihkan dari syngas hilir sistem penangkapan S. Gas pembersih PSA dikompresi dan dibakar dalam siklus gabungan turbin gas untuk menghasilkan tenaga listrik.
Teknologi gasifikasi sudah mapan untuk produksi H2. Pabrik komersial telah dibangun dan berhasil dioperasikan untuk menghasilkan H2 untuk aplikasi kilang dan pembuatan bahan kimia (misalnya produksi NH3 dan metanol) berdasarkan berbagai bahan baku hidrokarbon.
Daya listrik terintegrasi – Syngas dengan kandungan H2 yang tinggi dapat dibakar dalam turbo expander untuk menghasilkan tenaga listrik dalam pengaturan siklus gabungan. Jika syngas diproduksi menggunakan gasifikasi, skema ini disebut siklus gabungan gasifikasi terintegrasi (IGCC). IGCC memungkinkan listrik dihasilkan dengan efisiensi tinggi. Karena gas harus dibersihkan untuk mencegah kerusakan turbin gas, IGCC memiliki emisi lingkungan yang sangat rendah. Selain itu, tanaman IGCC menggunakan lebih sedikit air. IGCC saat ini sedang digunakan secara komersial di banyak pabrik secara global dengan gasifikasi residu minyak bumi untuk menyediakan tenaga, H2, dan uap.
Tiga jenis utama dari gasifier batubara adalah (i) moving bed, (ii) fluidized bed, dan (iii) entrained flow. Namun, sebagian besar gasifier yang dipertimbangkan untuk menangkap CO2 saat ini didasarkan pada gasifier aliran entrained. Penerapan komersial IGCC berbasis batubara telah dibatasi oleh biayanya yang relatif tinggi, ketersediaan pembangkit yang buruk dan persaingan dari pembangkit listrik tenaga batu bara yang dihancurkan. Biaya penangkapan CO2 di IGCC sangat bergantung pada jenis gasifier.
Seperti disebutkan di atas, untuk memungkinkan CO2 ditangkap, gas bahan bakar harus diumpankan ke reaktor pergeseran katalitik di mana sebagian besar CO direaksikan oleh uap untuk menghasilkan H2 dan CO. Untuk gasifier umpan slurry, uap yang cukup sudah ada di bahan bakar gas dari penguapan air bubur batubara dan dari pendinginan pendinginan gas produk gasifier. Namun, untuk gasifier umpan kering, uap harus diambil dari siklus uap dan ditambahkan ke umpan gas bahan bakar ke konverter shift.
Perlu dicatat bahwa IGCC lebih mahal untuk pembangkitan listrik daripada pembakaran batu bara bubuk konvensional, tanpa penangkapan CO2 dalam kedua kasus tersebut.
Pembuatan poli – Syngas adalah bahan pembangun yang baik, karena dapat digunakan untuk menghasilkan berbagai macam produk energi. Fleksibilitas terbesar yang ditawarkan adalah pembangkitan poli, di mana 'syngas' dapat menghasilkan uap, tenaga listrik, H2, dan bahan kimia (seperti metanol, cairan Fischer-Tropsch) dalam satu kompleks pabrik.
Sejumlah teknologi pemisahan yang berbeda termasuk teknologi pelarut, adsorben, dan membran dapat diterapkan untuk memisahkan CO2 dari produk gasifikasi.
Penyerapan – Teknologi konvensional adalah penyerapan fisik dalam proses dua tahap yang menghilangkan H2S dan kemudian menangkap CO2. Namun, gas perlu didinginkan setelah reaksi pergeseran gas air dan kemudian dipanaskan kembali sebelum menghasilkan tenaga. Ini mengurangi efisiensi dan meningkatkan biaya.
Adsorpsi – Adsorben dapat digunakan untuk memisahkan CO2 dari aliran gas buang pasca-pembakaran di bagian hilir dari reaksi perpindahan gas air. Baik adsorpsi ayunan suhu (TSA) dan adsorpsi ayunan vakum/tekanan (VSA/PSA) dapat digunakan untuk memulihkan CO2 dari adsorben. CO2 berada pada tekanan rendah saat dipulihkan melalui VSA/PSA dan perlu dikompresi untuk penyimpanan.
Membran – Sistem pemisahan gas berbasis membran canggih saat ini sedang dikembangkan untuk menggabungkan reaksi pergeseran gas dan pemisahan H2 dalam satu langkah. Sistem berbasis membran menggunakan water gas shift H2 separation membrane reactor (HSMR) untuk menggeser syngas dan mengekstrak H2. Suhu maksimum sekitar 475 derajat C memastikan kinetika kimia yang cepat dan kinerja keseimbangan perpindahan gas air yang baik diperoleh dengan penghilangan produk H2 secara terus-menerus.
Ada tiga kelas utama membran permeabel H2 anorganik yaitu (i) penyaringan molekul keramik, (ii) transportasi ion keramik padat, dan (iii) logam padat.
Keuntungan dan kerugian dari pra-pembakaran (dekarbonisasi) – Keuntungan dari pra-pembakaran (dekarbonisasi) adalah (i) pemisahan CO2 melalui penyerapan pelarut atau PSA terbukti. Gas buang datang pada tekanan tinggi dan konsentrasi CO2 yang tinggi secara signifikan mengurangi biaya penangkapan, (ii) biaya kompresi lebih rendah daripada sumber pasca-pembakaran karena CO2 dapat diproduksi pada tekanan sedang, (iii) teknologi ini menawarkan emisi SOx dan NOx yang rendah , (iv) produk utamanya adalah syngas, yang dapat digunakan untuk aplikasi atau produk komersial lainnya, dan (v) berbagai bahan bakar hidrokarbon dapat digunakan sebagai bahan baku, seperti gas, minyak, batubara, dan kokas minyak bumi, dll. Kerugiannya adalah (i) bahan bakar umpan adalah mengubah bahan bakar menjadi syngas terlebih dahulu, (ii) turbin gas, pemanas, boiler harus dimodifikasi untuk pembakaran H2, (iii) biaya lebih tinggi dan risiko teknologi lebih besar, dan (iv) membutuhkan modifikasi besar pada instalasi yang ada untuk retrofit.
Pembakaran bahan bakar oksi
Pembakaran oxy-fuel merupakan pendekatan baru yang muncul untuk mendekati nol-emisi dan pembakaran bahan bakar fosil yang lebih bersih. Hal ini dicapai dengan membakar bahan bakar dalam O2 murni, bukan udara. Dengan menghilangkan N2 (nitrogen) dalam proses pembakaran, aliran gas buang terutama terdiri dari air dan CO2, tanpa N2. CO2 dengan kemurnian tinggi dapat diperoleh kembali dengan kondensasi air. Namun, ketika bahan bakar dibakar dalam O2 murni, suhu nyala api jauh lebih tinggi daripada di pembakar yang ditiup udara normal dan bahan konstruksi konvensional untuk pembakar tidak mampu menahan suhu tinggi ini. Oleh karena itu, bahan konstruksi harus ditingkatkan atau suhu nyala api harus diturunkan. Pengembangan bahan tahan suhu tinggi berjalan lambat karena ini merupakan usaha R&D (penelitian dan pengembangan) utama. Ada sejumlah metode yang dapat digunakan untuk mengatur suhu nyala api, yang paling umum adalah daur ulang CO2. Dalam daur ulang CO2, sebagian aliran gas buang yang kaya CO2 didaur ulang kembali ke pembakar untuk menurunkan suhu nyala yang serupa dengan pembakar yang ditiup udara normal. Metode lain adalah menggunakan injeksi air daripada daur ulang CO2 untuk mengontrol suhu nyala. Ini sering disebut sebagai pembakaran 'hydroxyfuel'. Secara efektif, kedua opsi ini memungkinkan penggunaan bahan tahan api konvensional secara terus-menerus hingga bahan tahan suhu tinggi yang baru dapat dikembangkan.
A primary benefit of oxy-fuel combustion is the very high-purity CO2 stream which is produced during combustion. After trace contaminants are removed, this CO2 stream is more easily purified and removed than post-combustion capture. There are other benefits also such as reduction in NOx formation etc. When burning oil or coal, only two unit operations are needed for the combined removal of all other pollutants namely an electrostatic precipitator (ESP) or bag filter and a condensing heat exchanger (CHX)/reagent system. It is also possible to simplify the reagent system in the CHX to achieve total removal of SO2 with the CO2 stream for geologic storage. This further reduces the cost of unit operations for pollution abatement. The CHX increases the thermal efficiency of the boiler depending on the type of fossil fuel combusted, being the lowest for high rank bituminous coal and highest for natural gas.
Another benefit is the significant reduction in the size and capital cost of all plant equipment compared to conventional air-based combustion systems. This is due to the almost 5-fold decrease in the fire box volume and exit flue gas flow rates as N2 is eliminated in the combustion process.
The major disadvantage of oxy-fuel combustion is the high capital cost (primarily due to O2 requirements) and large electric power requirement inherent in conventional cryogenic air separation units required to generate O2. Oxy-fuel combustion is not currently used in typical large combustion systems because the air separation system is expensive and flue gas recycling is needed to be practiced in order to moderate flame temperature.