Penempaan Karbon dan Baja Paduan
Penempaan Karbon dan Baja Paduan
Penempaan baja karbon (C) dan paduan merupakan proses pengerjaan logam, yang memiliki kemampuan untuk membentuk material ke bentuk komponen yang diinginkan, sambil menyempurnakan struktur cor dari material tempa, menyembuhkan rongga susut, dan meningkatkan sifat mekanik dari bahan tempa. bahan. Jumlah pemesinan berikutnya juga berkurang, meskipun ini tergantung pada geometri bagian yang telah selesai dan proses penempaan yang digunakan.
Ingot cor telah menjadi titik awal tradisional untuk penempaan, baik penempaan langsung dari ingot, atau dari mekar atau billet yang telah dikerjakan panas dari ingot. Dengan penggunaan yang luas dari baja cor kontinyu, produk cor kontinyu sekarang biasanya digunakan sebagai stok awal. Selain ingot cor, roll dan cor mekar dan billet, bahan awal lainnya untuk tempa adalah pelat, batang dan batang kecil, dan coran baja.
Penempaan besi dan baja dimulai dengan awal Zaman Besi. Pada saat itu pengerjaan panas dengan cara hammering merupakan bagian dari proses produksi besi tempa, dan pembuatan produk besi tempa dan baja. Tungku peleburan mentah menggunakan bijih besi bermutu tinggi, arang, dan fluks menghasilkan sejumlah kecil besi yang harus ditempa bersama-sama dengan tangan untuk menghasilkan stok yang berguna. Awalnya, inilah tujuan utama penempaan saat itu. Secara umum diakui bahwa awal revolusi industri dimulai dengan sungguh-sungguh dari penempaan baja. Terlepas dari (atau mungkin karena) sejarah panjang ini, penempaan baja adalah proses empiris yang intuitif.
Forging biasanya diklasifikasikan dalam beberapa cara, dimulai dengan klasifikasi umum open die forging dan closed die forging. Mereka juga diklasifikasikan dalam hal faktor hampir selesai, atau jumlah stok (penutup) yang harus dihilangkan dari penempaan dengan pemesinan untuk memenuhi persyaratan dimensi dan detail dari bagian yang sudah jadi. Akhirnya, tempa diklasifikasikan lebih lanjut dalam hal peralatan tempa yang diperlukan untuk pembuatannya, seperti tempa palu, tempa linting cincin, dan tempa tekan multi-ram. Dari berbagai klasifikasi, yang didasarkan pada faktor mendekati akhir paling erat kaitannya dengan sifat-sifat yang melekat pada penempaan, seperti kekuatan dan ketahanan terhadap korosi tegangan. Secara umum, jenis penempaan yang membutuhkan pemesinan paling sedikit untuk memenuhi persyaratan bagian jadi memiliki sifat terbaik.
Sesuai spesifikasi ASTM A 788, penempaan baja adalah produk dari operasi kerja plastik tekan yang substansial yang mengkonsolidasikan material dan menghasilkan bentuk yang diinginkan. Pekerjaan plastik dapat dilakukan dengan palu, mesin tempa tekan, atau mesin ring rolling dan harus merusak bahan untuk menghasilkan struktur yang pada dasarnya tempa. Operasi rolling panas dapat digunakan untuk menghasilkan mekar atau billet untuk reforging. Tempa dapat dibagi lagi menjadi tiga kelas berikut berdasarkan suhu tempanya.
- Tempa yang dikerjakan dengan panas – Tempa yang dihasilkan dengan bekerja pada suhu di atas suhu rekristalisasi untuk material.
- Tempa dengan pengerjaan panas-dingin – Penempaan bekerja pada suhu tinggi sedikit di bawah suhu rekristalisasi untuk meningkatkan kekuatan mekanik. Penempaan kerja panas-dingin dapat dibuat dari bahan yang sebelumnya dikerjakan panas dengan penempaan atau penggulungan. Penempaan pengerjaan panas-dingin dapat dilakukan dalam satu operasi kontinu dimana bahan pertama-tama dikerjakan panas dan kemudian dikerjakan dingin dengan mengontrol suhu akhir. Karena perbedaan dalam pembuatan canai panas, atau batangan jadi panas dan dingin (setengah jadi atau jadi), billet atau mekar tidak dianggap sebagai tempa.
- Tempa dengan pengerjaan dingin – Tempa yang diproduksi oleh plastik bekerja dengan baik di bawah kisaran suhu di mana rekristalisasi material terjadi. Tempa yang dikerjakan dengan dingin harus dibuat dari bahan yang sebelumnya dikerjakan panas dengan cara ditempa atau digulung.
Bentuk produk tempa untuk baja meliputi pelat, bentuk, batangan, lembaran, strip, tabung, pipa, ekstrusi, dan tempa. Umumnya, ekstrusi disertakan dengan tempa, tetapi definisi penempaan tidak termasuk pelat dan batang yang digulung. Ini karena tempa, selain sesuai dengan bentuk akhir dari komponen yang diperlukan, tidak diharapkan untuk menunjukkan sifat-sifat inklusi laminar melalui kelemahan ketebalan yang kadang-kadang dikaitkan dengan pelat canai panas, atau ketidakstabilan pusat yang kadang-kadang dikaitkan dengan batang canai panas.
Baja karbon dan baja paduan biasanya merupakan bahan yang paling banyak ditempa, dan mudah ditempa menjadi berbagai bentuk dengan menggunakan proses penempaan panas, penempaan panas, atau penempaan dingin dan peralatan standar. Pemilihan suhu penempaan untuk baja karbon dan baja paduan didasarkan pada kandungan karbon, komposisi paduan, kisaran suhu untuk plastisitas optimal, dan jumlah reduksi yang diperlukan untuk menempa benda kerja. Dari faktor-faktor ini, kandungan karbon memiliki pengaruh paling besar pada suhu penempaan batas atas.
Terlepas dari banyaknya komposisi yang tersedia, semua bahan dalam kategori ini pada dasarnya menunjukkan karakteristik penempaan yang serupa. Pengecualian untuk ini adalah baja yang mengandung aditif pemesinan bebas seperti sulfida karena bahan ini lebih sulit ditempa daripada grade pemesinan tidak bebas. Biasanya, kemampuan tempa panas dari baja karbon dan baja paduan meningkat seiring dengan meningkatnya laju deformasi. Peningkatan kemampuan kerja terutama disebabkan oleh peningkatan panas deformasi yang dihasilkan pada tingkat deformasi yang tinggi.
Pembenaran untuk memilih penempaan dalam preferensi untuk yang lain, kadang-kadang lebih ekonomis, metode menghasilkan bentuk yang berguna didasarkan pada beberapa pertimbangan. Sifat mekanik dalam bahan tempa dimaksimalkan ke arah aliran logam utama selama bekerja. Untuk bentuk yang kompleks, hanya penempaan yang memberikan peluang untuk mengarahkan aliran logam sejajar dengan beban servis utama yang diterapkan dan untuk mengontrol, dalam batas tertentu, penyempurnaan struktur asli bahan tempa. Penyempurnaan struktur mikro adalah fungsi dari suhu, arah, dan besarnya reduksi dari bahan tempa ke bentuk tempa. Memaksimalkan integritas struktural material memungkinkan penyempurnaan konfigurasi desain, yang pada gilirannya memungkinkan pengurangan berat. Kontrol aliran logam yang memadai untuk mengoptimalkan properti dalam konfigurasi penempaan yang kompleks umumnya memerlukan satu atau lebih operasi yang mengganggu sebelum penempaan mati dan dapat memerlukan penempaan berongga atau ekstrusi balik untuk menghindari pembentukan kilatan pada jalur pemisahan mati.
Karena fungsi yang dimaksudkan untuk dipenuhi oleh baja tempa, desain penempaan sering kali mencakup ukuran penampang yang diberi perlakuan panas yang besar dan dapat berbentuk tidak beraturan, sehingga tegangan yang signifikan dapat diterapkan dalam pelayanan di ketiga sumbu utama yaitu (i) memanjang , (ii) melintang, dan (iii) melintang pendek. Dengan pemilihan ukuran bahan awal dan langkah penempaan yang cermat, penempaan dapat menunjukkan sifat yang menguntungkan di ketiga arah. Dalam kasus lain, misalnya, dalam penempaan piringan yang kacau, sifat mekanik yang baik dapat dicapai dalam arah radial di sekitar keliling penuh, sesuatu yang mungkin terjadi pada piringan yang hanya dipotong dari pelat yang digulung.
Perilaku menempa panas
Penempaan panas dari baja karbon dan baja paduan menjadi bentuk yang rumit jarang dibatasi oleh aspek kemampuan untuk ditempa dengan pengecualian nilai pemesinan bebas. Ketebalan bagian, kompleksitas bentuk, dan ukuran penempaan sebagian besar dibatasi oleh pendinginan yang terjadi ketika benda kerja yang dipanaskan bersentuhan dengan cetakan dingin. Karena alasan ini, peralatan yang memiliki waktu kontak die yang relatif singkat, seperti palu, sering lebih disukai untuk menempa bentuk yang rumit pada baja.
Keterbukaan – Forgeability adalah kemampuan relatif baja untuk mengalir di bawah beban tekan tanpa patah. Kecuali untuk kadar resulfurisasi dan refosforisasi, sebagian besar baja karbon dan baja paduan rendah biasanya dianggap memiliki kemampuan tempa yang baik. Perbedaan perilaku penempaan di antara berbagai tingkatan baja cukup kecil sehingga jarang mempengaruhi pemilihan baja dengan perilaku penempaan. Namun, pilihan baja yang disulfurisasi atau difosforisasi ulang untuk penempaan biasanya dibenarkan hanya jika penempaan akan dikerjakan secara ekstensif karena salah satu alasan utama untuk mempertimbangkan produksi dengan penempaan adalah untuk menghindari operasi pemesinan berikutnya, situasi ini jarang terjadi.
Salah satu cara umum untuk mengukur ketertempaan baja adalah uji hot-twist. Sesuai dengan namanya, pengujian ini melibatkan puntiran sampel batang yang dipanaskan hingga patah pada sejumlah suhu berbeda yang dipilih untuk menutupi kemungkinan kisaran suhu kerja panas dari bahan uji. Jumlah puntiran untuk patah, serta torsi yang dibutuhkan untuk mempertahankan puntiran pada laju yang konstan, dilaporkan. Suhu, di mana jumlah lilitan adalah yang terbesar, jika maksimum seperti itu ada, diasumsikan sebagai suhu kerja panas optimal dari bahan uji. Kemampuan tempa beberapa baja karbon sebagaimana ditentukan oleh pengujian hot twist ditunjukkan pada Gambar 1. Berbagai tes lain seperti yang diberikan di bawah ini digunakan untuk mengevaluasi kemampuan tempa baja.
- Uji tempa baji – Dalam uji ini, benda uji berbentuk baji ditempa di antara cetakan datar dan deformasi vertikal yang menyebabkan keretakan terjadi.
- Uji penekanan samping – Pengujian ini terdiri dari pemadatan sampel batang silinder antara cetakan datar dan paralel dengan sumbu silinder sejajar dengan cetakan. Ujung silinder tidak dibatasi, dan forgeability diukur dengan jumlah deformasi yang diperoleh sebelum retak.
- Uji kecewa – Dalam pengujian ini, sebuah silinder dikompresi antara cetakan datar dan regangan permukaan pada patahan di ekuator silinder diukur.
- Uji gangguan batang berlekuk – Tes ini serupa dengan uji gangguan kecuali takik aksial dikerjakan ke dalam sampel uji untuk menghasilkan tingkat tegangan lokal yang tinggi. Tegangan yang lebih tinggi ini dapat lebih menunjukkan tegangan yang dialami selama operasi penempaan yang sebenarnya daripada yang dihasilkan dalam uji gangguan standar.
- Uji tarik panas – Pengujian ini sering menggunakan alat uji khusus untuk memvariasikan laju regangan dan suhu pada rentang yang luas.
Pengaruh laju regangan pada daya tempa – Kemampuan untuk ditempa baja umumnya meningkat dengan meningkatnya laju regangan. Efek ini telah ditunjukkan untuk baja karbon rendah dalam pengujian hot-twist (Gbr1), di mana jumlah puntiran hingga kegagalan meningkat dengan meningkatnya laju puntiran. Dipercaya bahwa peningkatan kemampuan forgeabilitas pada laju regangan yang lebih tinggi ini disebabkan oleh peningkatan panas deformasi yang dihasilkan pada laju regangan yang lebih tinggi. Akan tetapi, peningkatan suhu yang berlebihan dari panas deformasi dapat menyebabkan pelelehan yang baru dimulai, yang dapat menurunkan kemampuan untuk ditempa dan sifat mekanik.
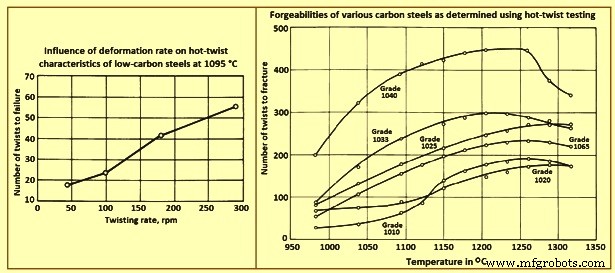
Gbr 1 Pengaruh laju deformasi dan forgeabilitas berbagai baja karbon
Tekanan aliran dan tekanan tempa – Tegangan aliran dan tekanan tempa dapat diperoleh dari kurva torsi yang dihasilkan dalam pengujian hot-twist atau dari pengujian kompresi atau tegangan panas. Data dari kurva ini menunjukkan bahwa persyaratan tekanan tempa relatif untuk kelompok paduan ini tidak bervariasi secara luas pada suhu tempa panas normal. Tekanan yang jauh lebih besar diperlukan untuk material dengan paduan yang lebih tinggi, dan material paduan ini juga menunjukkan peningkatan tekanan tempa yang lebih signifikan seiring dengan peningkatan reduksi.
Pengaruh laju regangan pada tekanan tempa – Tekanan penempaan yang dibutuhkan untuk baja tertentu meningkat dengan meningkatnya laju regangan. Studi baja karbon rendah menunjukkan bahwa pengaruh laju regangan lebih jelas pada suhu penempaan yang lebih tinggi. Efek ini ditunjukkan pada Gambar 2, yang memberikan kurva tegangan-regangan untuk baja karbon rendah yang ditempa pada berbagai suhu dan laju regangan. Efek serupa telah diamati pada baja paduan.
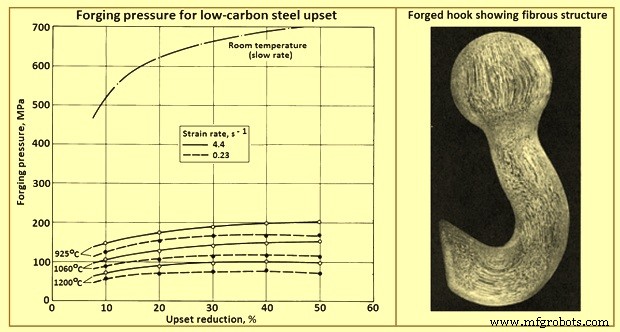
Gbr 2 Tekanan tempa untuk gangguan baja karbon rendah pada berbagai suhu dan dua laju regangan
Pemilihan baja untuk penempaan
Karbon dan baja paduan ingot, mekar, billet, dan pelat untuk penempaan adalah canai panas atau cor untuk perkiraan dimensi penampang, dan karenanya, kelurusan, camber, twist, dan toleransi kerataan tidak berlaku. Produk baja setengah jadi untuk penempaan diproduksi dengan berat potongan tertentu atau panjang tertentu.
Pengkondisian permukaan – Produk baja setengah jadi untuk penempaan dapat dikondisikan dengan menggores, memotong, atau menggiling untuk menghilangkan atau meminimalkan ketidaksempurnaan permukaan. Namun, perlu diingat bahwa, terlepas dari pengkondisian permukaan, produk kemungkinan masih mengandung beberapa ketidaksempurnaan permukaan.
Toleransi berat – Toleransi untuk billet, bloom, dan slab sering +/- 5% untuk potongan individu atau untuk lot dengan berat kurang dari 18 ton. Banyak yang berbobot lebih dari itu sering kali dikenai toleransi berat +/- 2,5%.
Memotong – Produk baja setengah jadi untuk penempaan umumnya dipotong memanjang dengan geser panas. Tergantung pada komposisi baja, penggergajian panas atau pemotongan api juga dapat digunakan.
Kualitas – Kualitas seperti istilah yang diterapkan pada produk baja setengah jadi untuk penempaan, bergantung pada banyak faktor yang berbeda, termasuk tingkat kesehatan internal, keseragaman relatif komposisi kimia, dan relatif bebas dari ketidaksempurnaan permukaan.
Penempaan baja setengah jadi berkualitas digunakan dalam aplikasi penempaan panas yang dapat melibatkan perlakuan panas atau operasi pemesinan berikutnya. Aplikasi semacam itu memerlukan kontrol yang relatif ketat terhadap komposisi kimia dan produksi baja.
Pemilihan baja untuk komponen tempa merupakan bagian integral dari proses desain, dan kinerja yang dapat diterima bergantung pada pilihan ini. Pemahaman yang cermat tentang penggunaan akhir bagian akhir berfungsi untuk menentukan sifat mekanik yang diperlukan, persyaratan permukaan akhir, toleransi terhadap inklusi non-logam, dan metode serta kriteria pemeriksaan yang menyertainya.
Baja kualitas tempa diproduksi untuk berbagai komposisi kimia. Dengan setiap praktik peleburan dan penggulungan, tingkat pengujian dan evaluasi kualitas dilakukan. Jika diperlukan, maka satu atau lebih batasan kualitas khusus dapat ditentukan untuk baja seperti tingkat terjadinya inklusi non-logam. Kadang-kadang, untuk aplikasi keandalan yang lebih tinggi, baja perlu menjalani proses peleburan kembali busur vakum atau peleburan elektroslag.
Penggunaan baja paduan mikro telah berkembang dalam beberapa tahun terakhir aplikasi seperti poros engkol otomotif. Baja ini biasanya memiliki tambahan kecil (0,05% hingga 0,1%) vanadium atau niobium dan dapat mencapai sifat yang dapat diterima dalam kondisi tanpa perlakuan panas (seperti yang ditempa). Akibatnya, paduan ini mempertahankan keunggulan proses penempaan sambil bersaing secara ekonomis dengan coran karena penghapusan siklus perlakuan panas.
Persyaratan desain – Pemilihan baja untuk bagian yang ditempa biasanya memerlukan beberapa kompromi antara faktor-faktor yang berlawanan, misalnya, kekuatan versus ketangguhan, ketahanan korosi-tegangan versus berat, biaya produksi versus kemampuan membawa beban yang berguna, biaya produksi versus biaya pemeliharaan, dan biaya bahan baku baja versus total biaya produksi penempaan. Pemilihan material juga melibatkan pertimbangan praktik peleburan, metode pembentukan, operasi pemesinan, prosedur perlakuan panas, dan penurunan sifat seiring waktu, serta sifat mekanik dan kimia konvensional dari baja yang akan ditempa.
Desain penempaan yang efisien mencapai kinerja maksimum dari jumlah minimum material yang konsisten dengan beban yang diterapkan, produktivitas, dan harapan hidup yang diinginkan. Untuk mencocokkan baja dengan komponen desainnya, baja pertama-tama dinilai kekuatan dan ketangguhannya, kemudian memenuhi syarat untuk stabilitas terhadap suhu dan lingkungan. Baja yang optimal kemudian dianalisis untuk produksi dan akhirnya untuk ekonomi.
Analisis kegagalan adalah sumber data yang berguna untuk mencocokkan sifat baja dengan persyaratan. Kegagalan komponen dapat terjadi selama operasi dalam rentang tegangan desain. Salah satu penyebab kegagalan prematur adalah kurangnya orientasi yang tepat dari tegangan desain kritis dengan aliran butir yang disukai dari tempa. Kegagalan tak terduga juga dapat terjadi karena kerusakan properti seiring waktu dan layanan. Misalnya, retak korosi tegangan, yang dihasilkan dari tegangan tarik yang berkelanjutan, dapat terjadi bahkan dalam suasana lingkungan yang khas. Dalam kondisi ini, kegagalan paling mungkin terjadi di lokasi penempaan yang bertepatan dengan ujung butir yang terbuka. Analisis kegagalan dapat mengungkap penyebab lain dari kegagalan prematur, seperti pertumbuhan butir yang berlebihan, masuknya pengotor non-logam, pelipatan aliran butir dari praktik penempaan yang tidak tepat, kurangnya struktur metalurgi tempa, dan produksi penambah tegangan yang tidak disengaja dengan pemesinan terlalu lama. fillet tajam atau kurang pas dalam perakitan.
Efek penempaan pada properti
Pembentukan konfigurasi kompleks dari batang atau billet baja karbon atau paduan perlu terlebih dahulu agar baja 'diatur' menjadi bentuk awal yang sesuai (dibentuk sebelumnya) dan kemudian dialirkan ke konfigurasi bagian akhir. Penataan ulang logam ini memiliki sedikit efek pada kekerasan dan kekuatan baja, tetapi sifat mekanik tertentu (seperti keuletan, kekuatan impak, dan kekuatan lelah) ditingkatkan. Peningkatan sifat ini (Gambar 2) terjadi karena penempaan (i) memecah segregasi, menyembuhkan porositas, dan membantu homogenisasi, (ii) menghasilkan struktur butiran berserat yang meningkatkan sifat mekanik sejajar dengan aliran butir, dan (iii) berkurang seiring -ukuran butir cor.
Perbaikan khas dalam daktilitas dan kekuatan impak baja perlakuan panas sebagai fungsi reduksi tempa ditunjukkan pada Gambar 3. Data ini menggambarkan bahwa peningkatan maksimum dalam setiap kasus terjadi dalam arah perpanjangan maksimum. Ketangguhan dan keuletan mencapai maksimum setelah sejumlah pengurangan tertentu, setelah itu pengurangan lebih lanjut hanya bernilai kecil.
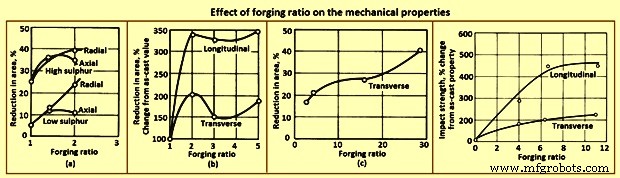
Gbr 3 Pengaruh rasio penempaan pada sifat mekanik
Tab 1 memberikan sifat mekanik longitudinal khas dari tempa baja karbon rendah dan karbon sedang dalam kondisi anil, normalisasi, dan padam dan temper. Seperti yang diharapkan, kekuatan meningkat dengan meningkatnya kandungan karbon, sementara keuletan menurun. Diakui bahwa tempa die tertutup sebagian besar dibuat dari billet tempa yang telah menerima pekerjaan sebelumnya yang cukup besar. Tempa cetakan terbuka, bagaimanapun, dapat dibuat dari billet tempa atau produk as-cast.
Tab 1 Sifat longitudinal tempa baja karbon pada empat kandungan karbon |
No. Sl. | Konten karbon | Kekuatan tarik tertinggi | Kekuatan hasil, offset 0,2% | Perpanjangan | Pengurangan luas | Kekuatan kelelahan * | Kekerasan |
% | MPa | MPa | % | % | MPa | HB |
| Anil |
1 | 0,24 | 438 | 201 | 39 | 59 | 185 | 122 |
2 | 0,30 | 483 | 245 | 31.5 | 58 | 193 | 134 |
3 | 0,35 | 555 | 279 | 24.5 | 39 | 224 | 157 |
4 | 0,40 | 634 | 348 | 24 | 42 | 248 | 180 |
| Dinormalisasi |
1 | 0,24 | 483 | 247 | 34 | 56,5 | 193 | 134 |
2 | 0,30 | 521 | 276 | 28 | 44 | 209 | 148 |
3 | 0,35 | 579 | 303 | 23 | 36 | 232 | 164 |
4 | 0,40 | 690 | 355 | 22 | 36 | 255 | 196 |
| Oli dipadamkan dan ditempa pada 595 derajat C |
1 | 0,24 | 500 | 305 | 35,5 | 62 | 193 | 144 |
2 | 0,30 | 552 | 301 | 27 | 52 | 224 | 157 |
3 | 0,35 | 669 | 414 | 26,5 | 49 | 247 | 190 |
4 | 0,40 | 724 | 386 | 19 | 31 | 277 | 206 |
* Rotating beam test pada 10.000.000 batas daya tahan |
Logam mengalir ke berbagai arah selama penempaan mati tertutup. Sebagai contoh, dalam penempaan rib dan bentuk web seperti komponen rangka udara, hampir semua aliran logam dalam arah melintang. Aliran transversal tersebut meningkatkan daktilitas ke arah itu dengan sedikit atau tanpa pengurangan daktilitas longitudinal. Daktilitas transversal dapat dianggap sama atau melampaui daktilitas longitudinal jika reduksi penempaan cukup besar dan jika aliran logam terutama dalam arah melintang. Efek serupa diamati dalam mengganggu billet tempa. Dalam kasus ini, bagaimanapun, sumbu longitudinal asli dari bahan dipersingkat oleh upsetting, dan perpindahan lateral logam dalam arah radial. Ketika reduksi yang terganggu melebihi sekitar 50%, keuletan dalam arah radial biasanya melebihi keuletan dalam arah aksial (Gbr 4).
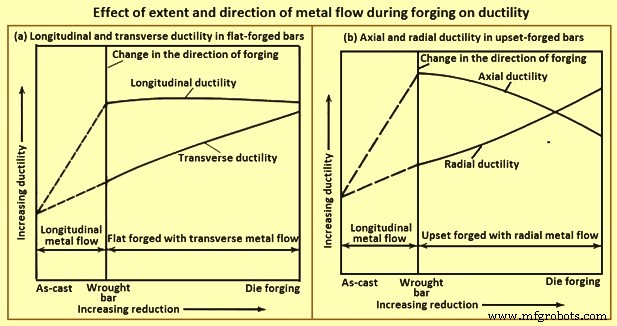
Gbr 4 Pengaruh khas reduksi gangguan pada daktilitas aksial dan radial baja tempa
Struktur dan keuletan tempa – Aspek lain dari kontrol material memastikan bahwa penempaan akhir telah mengalami deformasi plastis yang cukup untuk mencapai struktur tempa yang diperlukan untuk pengembangan sifat mekanik yang menjadi dasar desain. Meskipun beberapa deformasi plastis dicapai selama pemecahan produk cor menjadi billet tempa, jauh lebih banyak yang diberikan selama proses penempaan die tertutup. Kontrol material untuk forging berkekuatan tinggi memerlukan penentuan sifat mekanik dari forging billet, serta forging.
Ukuran keuletan atau ketangguhan ditentukan dengan mengukur pengurangan luas yang diperoleh dalam sampel uji tarik melintang. Ketika pengujian yang sesuai dibuat dari sampel transversal dan longitudinal yang diambil dari tempa yang diberi perlakuan panas dengan tingkat kekuatan yang sama, adalah mungkin untuk membandingkan sifat mekanik dari stok billet dan tempa dan untuk memperkirakan proporsi struktur metalurgi tempa akhir yang disumbangkan oleh masing-masing.
Daktilitas dan jumlah pengurangan tempa – Tujuan utama dari kontrol material adalah untuk memastikan bahwa sifat mekanik yang optimal dicapai dalam penempaan jadi. Jumlah pengurangan yang dicapai dalam penempaan memiliki efek yang nyata pada keuletan, seperti yang ditunjukkan pada Gambar 4, yang membandingkan keuletan pada ingot cor, batang atau billet tempa (digulung), dan penempaan. Kurva pada Gambar 4(a) menunjukkan bahwa ketika batang tempa atau billet ditempa rata dalam cetakan, peningkatan reduksi penempaan tidak mempengaruhi daktilitas longitudinal, tetapi menghasilkan peningkatan bertahap dalam daktilitas transversal. Ketika batang atau billet serupa ditempa dalam cetakan, peningkatan pengurangan penempaan menghasilkan penurunan bertahap dalam daktilitas aksial dan peningkatan bertahap dalam daktilitas radial.
Daktilitas ingot cor bervariasi dengan komposisi kimia, praktek peleburan, dan ukuran ingot. Daktilitas ingot baja dengan komposisi paduan yang sama juga bervariasi, tergantung pada apakah mereka dituangkan dari baja lebur udara atau baja peleburan busur vakum. Saat memulai dengan ingot besar dari paduan tertentu, terkadang praktis untuk menggulung bagian ingot ke berbagai ukuran billet atau batangan dengan jumlah pengurangan penempaan yang bervariasi. Jumlah minimum pengurangan tidak standar, tetapi jarang kurang dari 2:1 (perbandingan luas bagian ingot dengan luas bagian billet). Reduksi ingot baja menjadi billet biasanya jauh lebih besar dari 2:1. Sebaliknya, beberapa tempa paduan tahan panas ditempa langsung dari ingot cor.
Seringkali, tidak layak untuk menyiapkan billet untuk tempa yang begitu besar sehingga membutuhkan seluruh berat ingot. Jumlah reduksi tempa yang diwakili oleh struktur metalurgi tempa paling baik dikendalikan dengan pengamatan dan pengujian sampel makro-etch dan uji tarik yang diambil dari tempa yang telah selesai. Sampel ini memungkinkan eksplorasi area kritis dan, umumnya, seluruh penempaan. Mereka dipilih dari arah butir memanjang, melintang panjang, dan melintang pendek, sesuai kebutuhan. Tes etsa memungkinkan pengamatan visual aliran butir. Uji mekanis menghubungkan kekuatan dan ketangguhan dengan aliran butir.
Aliran butiran – Makro-etsa memungkinkan pengamatan langsung arah dan kontur butir dan juga berfungsi untuk mendeteksi lipatan, putaran, dan aliran masuk kembali. Dengan sampel yang cocok dengan etsa makro, aliran butir dapat diperiksa dalam arah memanjang, melintang panjang, dan melintang pendek. Makro-etsa juga memungkinkan evaluasi bagian lengkap, ujung ke ujung dan sisi ke sisi, dan peninjauan keseragaman ukuran butiran makro. Gambar 2 menunjukkan aliran butir di bagian tempa yang representatif.
Ukuran butir dan konstituen mikro – Pemeriksaan metalografi, menggunakan mikroskop, paling cocok untuk memeriksa area yang dipertanyakan yang diungkapkan oleh makro-etsa, untuk mengukur ukuran butir, dan untuk menentukan sifat dan jumlah konstituen mikro.
Kekuatan kelelahan – Uji kelelahan digunakan dalam pengendalian bahan di bawah kondisi dan untuk tujuan seperti (i) pengujian laboratorium sampel kecil untuk pengembangan atau kualifikasi bahan, (ii) pengujian laboratorium komponen lengkap atau sub-rakitan untuk pengembangan desain, dan (iii) pengawasan komponen atau rakitan di lapangan untuk memastikan keandalan layanan yang berkelanjutan.
Pengujian kelelahan laboratorium sampel kecil untuk kualifikasi atau pengembangan material dilakukan dengan metode standar. Sampel uji diambil baik dari produk pabrik atau dari tempa die tertutup, sesuai kebutuhan. Sampel standar cukup kecil untuk memungkinkan pemilihan dari banyak lokasi dalam penempaan dan untuk berkorelasi dengan berbagai arah aliran butir. Pengujian umumnya dilakukan pada suhu kamar di udara, meskipun pengujian pada suhu yang lebih tinggi atau lebih rendah dan di atmosfer khusus dapat dilakukan.
Penerapan pengujian kelelahan laboratorium skala kecil untuk analisis komponen atau rakitan memperkenalkan variabel tambahan. Salah satunya adalah efek dari kondisi permukaan. Kurva pada Gambar 5(a) menunjukkan bahwa kekuatan lelah sampel baja sangat bervariasi, tergantung pada apakah permukaannya dipoles, dikerjakan dengan mesin, digulung panas, atau ditempa. Baja yang diuji adalah baja paduan rendah tempa yang diberi perlakuan panas 269 HB sampai 285 HB, setara dengan kekuatan tarik 876 MPa dan kekuatan luluh 696 MPa. Persiapan sampel mengharuskan sampel dimesin dan dipoles setelah perlakuan panas dan penggulungan atau penempaan mendahului perlakuan panas. Untuk umur kelelahan 106 siklus, batas kelelahan adalah 395 MPa untuk sampel tanah, 315 MPa untuk sampel mesin, 205 MPa untuk sampel as-rolled, dan hanya 150 MPa untuk spesimen as-forged.
Kurva pada Gambar 5(b) berlaku untuk baja dengan kekuatan tarik berkisar antara 345 MPa hingga 2.070 MPa dan merupakan perkiraan dari beberapa pengujian. Persiapan sampel untuk sampel yang ditempa atau didekarburasi pada tingkat kekuatan tarik 965 MPa mencakup baja yang dikerjakan secara kasar dari batangan, dipanaskan hingga sekitar 900 derajat C dalam tungku peredam berbahan bakar gas selama 20 menit hingga 30 menit, sangat sedikit digosok dari aslinya Diameter 7,47 mm hingga diameter akhir 7,16 mm, dan berpendingin udara. Perlakuan panas terdiri dari austenitisasi dalam penangas garam pada suhu sekitar 830 derajat C selama 45 menit, pendinginan minyak, tempering di udara selama 1 jam pada suhu sekitar 620 derajat C, dan pendinginan air. Penempaan dan perlakuan panas menghasilkan dekarburisasi permukaan hingga kedalaman sekitar 0,064 mm. Sampel ini telah menunjukkan kekuatan lelah, pada 106 siklus, sekitar 310 MPa, dibandingkan dengan 470 MPa untuk sampel yang tidak ditempa tetapi dikerjakan atau dipoles dan bebas dari dekarburisasi. Dekarburisasi menurunkan tingkat kekuatan yang diperoleh dengan perlakuan panas. Kontrol laboratorium terhadap kondisi permukaan sulit diduplikasi dalam kuantitas produksi komponen palsu. Oleh karena itu, kekuatan lelah komponen ukuran penuh bervariasi pada rentang yang lebih luas daripada sampel kecil, karena variasi kondisi permukaan.
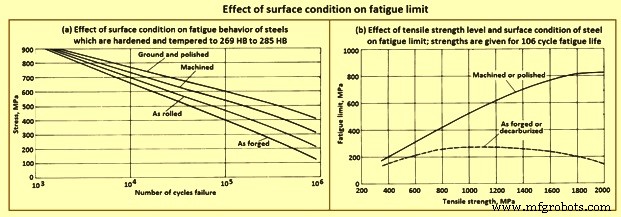
Gbr 5 Pengaruh kondisi permukaan terhadap batas kelelahan
Ketangguhan retak – Fraktur getas pada tempa dan komponen lain sebagai akibat dari perambatan retak pada tingkat tegangan yang jauh di bawah kekuatan luluh baja telah menyebabkan studi luas tentang karakteristik fraktur dan metode evaluasi ketangguhan fraktur. Hasil studi ini sangat penting untuk pengendalian material, terutama yang berkaitan dengan pengembangan pengujian untuk mengevaluasi ketangguhan retak yang menjadi dasar standar pengendalian material.
Di bidang pengujian laboratorium dan teknik analisis, penekanan utama telah ditempatkan pada pengembangan metode yang dapat diandalkan untuk mengevaluasi kekuatan baja yang mengandung retak atau cacat seperti retak. Secara khusus, minat telah berpusat pada metode untuk menentukan ketangguhan patah bidang-regangan. Komponen yang ditempa dievaluasi dengan menguji sampel kecil yang diambil dari lokasi terpilih pada penempaan yang mewakili berbagai arah butir.
One test procedure comprises the bend testing of the notched and fatigue-cracked samples in a neutral environment. The objective of this test is to get a lower limiting value of fracture toughness which can be used to estimate the relationship between stress and defect size in a metal under service conditions in which high constraint is expected. In the test procedure referred to, a test sample with a chevron notch is suitably pre-cracked in fatigue. It is then tested in a bend test fixture provided with support rolls which rotate and move apart slightly to permit rolling contact and virtually eliminate the friction effect. The sample is subjected to three-point bending, and the imposed load versus displacement change across the notch is recorded on an autographic recorder. Fracture toughness is rated by a calculated parameter, the critical stress intensity.
End-grain exposure – Lowered resistance to stress-corrosion cracking in the long-transverse and short-transverse directions is related to the end-grain exposure. A long, narrow test sample sectioned so that the grain is parallel to the longitudinal axis of the sample has no exposed end grain, except at the extreme ends, which are not subjected to the loading. In contrast, a corresponding sample cut in the transverse direction has end-grain exposure at all points along its length. End grain is especially pronounced in the short-transverse direction on die forgings designed with a flash line. Consequently, forged components designed to reduce or eliminate end grain have better resistance to stress-corrosion cracking.
Residual stress – The sustained tensile stress at the surface of a forging which contributes to stress-corrosion cracking is the total of applied and residual stresses. When the residual stress constitutes a significant percentage of the total stress, it is to be reduced or eliminated. Common sources of residual tensile stresses include quenching, machining, and poor fit in assembly. Each can be suitably modified to reduce or eliminate tensile stresses, especially those present in an exposed surface. As an example, drastic quenching places the surface of a heat-treatable alloy in a state of compression and the core in a state of tension. Furthermore, the compressed surface can be entirely removed during rough machining, exposing the tension-stressed core material. This hazard can be avoided by quenching after, rather than before, rough machining. In some applications, a surface in tension is placed in compression by shot peening.
Hydrogen-stress cracking occurs without corrosion. Hence, its initiation is not confined to exterior surfaces in contact with a corrosive medium. It can start at any suitable nucleus, such as an inclusion or void, as well as at a surface notch or other irregularity. Hydrogen-stress cracking at the interior is described as hydrogen embrittlement or hydrogen flaking. Hydrogen-stress cracking has been observed, studied, and brought under control in most high-strength steels. The modern practice of vacuum melting can reduce residual hydrogen to negligible amounts. A hydrogen content of 3 ppm to 6 ppm in air-melted steel can be readily lowered to 0.6 ppm to 1 ppm by vacuum arc remelting. Provided that the initial hydrogen content of the steel is acceptably low, material control procedures are to ensure that hydrogen pickup is avoided in all subsequent processing, including forging, heat treating, hot salt bath descaling, pickling, and plating. During forging, steels develop a surface scale and a decarburized surface layer, both of which are subsequently removed by grit blasting and machining. Unless the steel is acid pickled, there is no possibility of hydrogen pickup.
Many of the critical parts made from steel forgings are protected by a coating of cadmium. Steel parts heat treated to strength levels higher than 1,655 MPa are especially sensitive to hydrogen pickup, in case they are coated with cadmium, the coating is deposited in vacuum. Parts heat treated to strength levels lower than 1,655 MPa can be cadmium plated electrolytically, provided that a titanium-containing plating bath is used and the parts are subsequently baked at around 190 deg C for 12 hours.
Mechanical properties – A major advantage of shaping metal parts by rolling, forging, or extrusion stems from the opportunities such processes offer the designer with respect to the control of grain flow. The strength of these and similar wrought products is almost always greatest in the longitudinal direction (or equivalent) of grain flow, and the maximum load-carrying ability in the finished part is achieved by providing a grain-flow pattern parallel to the direction of the major applied service loads when, in addition, sound, dense, good-quality metal of sufficiently fine grain size has been produced throughout.
Grain flow and anisotropy – Steel which is rolled, forged, or extruded develops and retains a fiber like grain structure aligned in the principal direction of working. This characteristic becomes visible on external and sectional surfaces of wrought products when the surfaces are suitably prepared and etched. The fibers are the result of elongation of the micro-structural constituents of the steel in the direction of working. Hence, the phrase ‘direction of grain flow’ is normally used to describe the dominant direction of these fibers within wrought metal products.
In wrought steel, the direction of grain flow is also evidenced by measurements of mechanical properties. Strength and ductility are almost always greater in the direction parallel to that of working. The characteristic of showing different strength and ductility values with respect to the direction of working is referred to as mechanical anisotropy and is exploited in the design of wrought products. Although the best properties in wrought steels are most frequently the longitudinal (or equivalent), properties in other directions can yet be superior to those in products not wrought, that is, in cast ingots or in forging stock taken from a lightly worked ingot.
Rectangular sections show anisotropy among all the three principal directions i.e. longitudinal, long transverse, and short transverse. A design which employs a rectangular section involves the properties in all these directions, not just the longitudinal. Hence, the longitudinal, long-transverse, and short-transverse service loads of rectangular sections are analyzed separately.
Anisotropy in high strength steel – Although all wrought steels are mechanically anisotropic, the effects of anisotropy on mechanical properties vary among different metals and alloys. For example, a vacuum-melted steel of a given composition is generally less mechanically anisotropic than a conventionally killed, air-melted steel of the same composition. Response to etching to reveal the grain flow characteristic of anisotropy also varies. Steels with poor corrosion resistance are readily etched, while those with good corrosion resistance need more corrosive etchants and extended etching times to reveal grain flow. In general, fatigue properties are markedly affected by the relation of flow-line direction to direction of stresses from applied loads. When flow lines are perpendicular to load stresses, a stress-raising effect is produced.
Forging lubricants
For many years, oil-graphite mixtures have normally being used as lubricants for forging carbon and alloy steels. Recent advances in lubricant technology, however, have resulted in new types of lubricants, including water/graphite mixtures and water-base synthetic lubricants. Each of the normally used lubricants has advantages as well as limitations (Tab 2) which is required to be balanced against process requirements.
Tab 2 Advantages and limitations of the main lubricants used for hot forging of steels |
Sl. No. | Type of lubricant | Advantages | Limitations |
1 | Water-base micro-graphite | Eliminates smoke and fire; provides die cooling; is easily extended with water | Must be applied by spraying for best results |
2 | Water-base synthetic | Eliminates smoke and fire; is cleaner than oils or water-base graphite; aids die cooling; is easily diluted, and needs no agitation after initial mixing; reduces clogging of spray equipment; does not transfer dark pigment to part | Must be sprayed; lacks the lubricity of graphite for severe forging operations |
3 | Oil-base graphite | Fluid film lends itself to either spray or swab application; has good performance over a wide temperature range (upto 540 deg C). | Generates smoke, fire, and noxious odours; explosive nature may shorten die life; has potentially serious health and safety implications for workers |
Selection criteria – Lubricant selection for forging is based on several factors, including forging temperature, die temperature, forging equipment, method of lubricant application, complexity of the part being forged and environmental and safety considerations. At normal hot-forging temperatures for carbon and alloy steels, water-base graphite lubricants are used almost exclusively, although some hammer shops still employ oil-base graphite.
The most common warm-forming temperature range for carbon and alloy steels is 540 deg C to 870 deg C. Because of the severity of forging conditions at these temperatures, billet coatings are often used in conjunction with die lubricants. The billet coatings used include graphite in a fluid carrier or water-base coatings used in conjunction with phosphate conversion coating of the work piece. For still lower forging temperatures (less than around 400 deg C, molybdenum disulphide has a greater load-carrying capacity than does graphite. Molybdenum disulphide can either be applied in solid form or dispersed in a fluid carrier.
Heat treatment of carbon and alloy steel forgings
Normally steel forgings are specified based upon one of four man conditions namely (i) as forged with no further thermal processing, (ii) heat treated for machinability, (iii) heat treated for final mechanical / physical properties, or (iv) special heat treatment to enhance dimensional stability, particularly in more complex part configurations.
As forged with no further thermal processing – Although the vast majority of steel forgings are heat treated before use, a large tonnage of low carbon steel (0.1 % to 0.25 % C) is used in the as-forged condition. In such forgings, machinability is good, and little is gained in terms of strength by heat treatment. In fact, a number of widely used specifications permit this economic option. It is also interesting to note that, compared to the properties produced by normalizing, strength and machinability are slightly better, which is most likely attributable to the fact that grain size is somewhat coarser than in the normalized condition.
Heat treated for machinability – When a finished machined component is to be produced from a roughly dimensioned forging, machinability becomes a vital consideration to optimize tool life, increase productivity, or both. The specification or forging drawing can specify the heat treatment. However, when specifications give only maximum hardness or micro-structural specifications, the most economical and effective thermal cycle is to be selected. Available heat treatments include full anneal, spheroidize anneal, sub-critical anneal, normalize, or normalize and temper. The heat treatment chosen depends on the steel composition and the machine operations to be performed. Some steel grades are inherently soft while others become quite hard in cooling from the finishing temperature after hot forging. Some type of annealing is usually required or specified to improve machinability.
Heat treated for final mechanical / physical properties – Normalizing or normalizing and tempering can produce the needed minimum hardness and minimum ultimate tensile strength. However, for most steels, a hardening (austenitize) and quenching (in oil, water, or some other medium, depending on section size and hardenability) cycle is employed, followed by tempering to produce the proper hardness, strength, ductility, and impact properties. For steel forgings to be heat treated above the 1,035 MPa strength level and having section size variations, it is general practice to normalize before austenitizing to produce a uniform grain size and minimize internal residual stresses. In some instances, it is normal practice to use the heat for forging as the austenitizing cycle and to quench at the forge unit. The forging is then tempered to complete the heat treat cycle. Although there are obvious limitations to this procedure, definite economies are possible when the procedure is applicable (usually for symmetrical shapes of carbon steels which need little final machining).
Special heat treatment to enhance dimensional stability – Special heat treatments, particularly in more complex part configurations, are sometimes used to control dimensional distortion, relieve residual stresses before or after machining operations, avoid quench cracking, or prevent thermal shock or surface (case) hardening. Although most of the heat-treating cycles can apply, very specific treatments can be needed. Such treatments normally apply to complex forging configurations with adjacent differences in section thickness, or to very high hardenability steels and alloys. When stability of critically dimensioned finished parts permits only light machining of the forging after heat treatment to final properties, special treatments are available, including mar-quenching (mar-tempering), stress relieving, and multiple tempering.
Many applications, such as crankshafts, camshafts, gears, forged rolls, rings, certain bearings, and other machinery components, need increased surface hardness for wear resistance. The important surfaces are normally hardened after machining by flame or induction hardening, carburizing, carbo-nitriding, or nitriding. These processes are listed in the approximate order of increasing cost and decreasing maximum temperature. The latter consideration is important in that dimensional distortion normally decreases with decreasing temperature. This is particularly true of nitriding, which is usually performed below the tempering temperature for the steel used in the forging.
Micro-alloyed forging steels
Micro-alloying (the use of small amounts of elements such as vanadium and niobium to strengthen steels) has been in practice since the 1960s to control the micro-structure and properties of low carbon steels. Most of the early developments have been related to plate and sheet products in which micro-alloy precipitation, controlled rolling, and modern steelmaking technology combined to increase strength significantly relative to that of low carbon steels.
The application of micro-alloying technology to forging steels has lagged behind that of flat-rolled products because of the different property requirements and thermo-mechanical processing of forging steels. Forging steels are normally used in applications in which high strength, fatigue resistance, and wear resistance are needed. These requirements are most often filled by medium carbon steels. Thus, the development of micro-alloyed forging steels has been based around the grades containing 0.3 % to 0.5 % C.
The driving force behind the development of micro-alloyed forging steels has been the need to reduce the production costs. This is accomplished in these materials by means of a simplified thermo-mechanical treatment (that is, a controlled cooling following hot forging) which achieves the desired properties without the separate quenching and tempering treatments required by conventional carbon and alloy steels. In Fig 6, the processing sequence for conventional (quenched and tempered) steels is compared with the micro-alloyed steel-forging process.
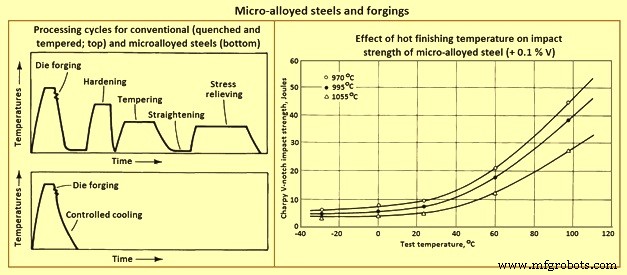
Fig 6 Micro-alloyed steels and forgings
Effects of micro-alloying elements
Carbon – Most of the micro-alloyed steels developed for forging have carbon contents ranging from 0.3 % to 0.5 %, which is high enough to form a large amount of pearlite. The pearlite is responsible for substantial strengthening. This level of carbon also decreases the solubility of the micro-alloying constituents in austenite.
Niobium, vanadium, and titanium – Formation of carbo-nitride precipitates is the other major strengthening mechanism of micro-alloyed forging steels. Vanadium, in amounts ranging from 0.05 % to 0.2 %, is the most common micro-alloying addition used in forging steels. Niobium and titanium enhance strength and toughness by providing control of austenite grain size. Frequently niobium is used in combination with vanadium to achieve the benefits of austenite grain size control (from niobium) and carbo-nitride precipitation (from vanadium).
Manganese – Manganese is used in relatively large amounts (1.4 % to 1.5 %) in many micro-alloyed forging steels. It tends to reduce the cementite plate thickness while maintaining the inter-lamellar spacing of pearlite developed. Hence, high manganese levels require lower carbon contents to retain the large amounts of pearlite required for high hardness. Manganese also provides substantial solid solution strengthening, enhances the solubility of vanadium carbonitrides, and lowers the solvus temperature for these phases.
Silicon – The silicon content of most commercial micro-alloyed forging steels is around 0.3 %. Some grades contain upto 0.7 %. Higher silicon contents are associated with significantly higher toughness, apparently because of an increased amount of ferrite relative to that formed in ferrite-pearlite steels with lower silicon contents.
Sulphur – Many micro-alloyed forging steels, particularly those needed for use in automotive forgings in which machinability is critical, have relatively high sulphur contents. The higher sulphur contents contribute to their machinability, which is comparable to that of quenched and tempered steels.
Aluminum and nitrogen – As in hardenable fine-grain steels, aluminum is important for austenite grain size control in micro-alloyed steels. The mechanism of aluminum grain size control is the formation of aluminum nitride particles. It has been shown that nitrogen is the major interstitial component of vanadium carbo-nitride. For this reason, moderate to high nitrogen contents are needed in vanadium containing micro-alloyed steels to promote effective precipitate strengthening.
Controlled Forging
The concept of grain size control has been used for many years in the production of flat rolled products. Particularly in plate rolling, the ability to increase austenite recrystallization temperature using small niobium additions is well known. The process used to produce these steels is usually referred to as controlled rolling. The benefits of austenite grain size control are not, of course, limited to flat rolled products. Although the higher finishing temperatures needed for rolling of bars limit the usefulness of this approach to micro-structural control, finishing temperatures for micro-alloyed bar steels is nonetheless to be controlled.
It has been shown that, although strength is not significantly affected by finishing temperature, toughness of vanadium-containing micro-alloyed steels decreases with increasing finishing temperature. This effect is shown in Fig 6, which compares Charpy V-notch impact strength for a micro-alloyed steel finished at three temperatures. This detrimental effect of a high finishing temperature on impact toughness also carries over to forging operations, that is, the lower the finish temperature in forging, the higher the resulting toughness, and vice versa. After extensive testing, it has been shown that the finishing temperature for forging if reduced to near 1000 deg C, results in impact properties equal to or better than those of hot rolled bar. It is also shown that rapid induction preheating is beneficial for micro-alloyed forging steels, and that cost savings of 10 % (for standard micro-alloyed forgings) to 20 % (for resulphurized grades) are possible.
Lower finishing temperatures, however, take their toll in terms of higher required forging pressures (and thus higher machine capacities needed) and increased die wear. The improved toughness resulting from lower finishing temperatures, as well as any cost savings which can be achieved as a result of the elimination of heat treatment, is to be weighed against the cost increases caused by these factors.
Micro-alloyed cold heading steels -Steels used in the production of high-strength fasteners by cold heading have been earlier produced from quenched and tempered alloy steels. To obtain sufficient strength with adequate ductility needed six processing steps. Recent developments have led to the use of micro-alloyed niobium-boron steels which need no heat treatment. These steels make use of niobium and boron additions to develop bainitic structures with high work-hardening rates. In most cases they use the deformation of cold heading to achieve the required strength levels without heat treatment.