Upgrade burner di pabrik Simplot menguntungkan kinerja, energi
Untuk mengurangi konsumsi energi dan biaya, Perusahaan J.R. Simplot menyelesaikan proyek beberapa tahun lalu yang meningkatkan efisiensi sistem uap di pabrik pengolahan kentang di Caldwell, Idaho. Proyek ini didasarkan pada evaluasi, yang dilakukan dengan menggunakan Steam System Assessment Tool (SSAT), oleh Bill Moir, Spesialis Berkualitas di Steam Engineering Inc. SSAT dikembangkan untuk Praktik Terbaik Program Teknologi Industri Departemen Energi AS (DOE). Perbaikan pabrik Caldwell menghemat 52.000 MMBtu dan 526.000 kilowatt-jam per tahun. Penghematan biaya energi dan pemeliharaan total $329,000 per tahun. Karena total biaya proyek adalah $373.000, pengembalian sederhana kurang dari 14 bulan. Langkah-langkah efisiensi serupa direplikasi di fasilitas Simplot lainnya, mengikuti analisis yang dilakukan menggunakan SSAT. Peningkatan efisiensi energi tersebut menghasilkan penghematan gas alam sebesar 176.000 MMBtu per tahun.
Latar Belakang Perusahaan/Tanaman
Perusahaan J.R. Simplot adalah perusahaan makanan dan agribisnis utama yang berbasis di Boise, Idaho, dengan penjualan tahunan sekitar $3 miliar. Perusahaan ini memiliki lebih dari 12.000 karyawan di Amerika Serikat, Kanada, Cina, Meksiko, dan Australia. Kegiatan usaha Simplot meliputi produksi pangan, pupuk, rumput dan produk hortikultura; pakan ternak; dan usaha agribisnis lainnya. Perusahaan memiliki program efisiensi energi berkelanjutan yang berfokus pada pelatihan karyawan. David Hawk, direktur energi dan sumber daya alam, dan Alan Christie, manajer teknik Food Group di Simplot, telah bekerja sama dengan DOE, Program Energi Universitas Negeri Washington, dan Divisi Energi Sumber Daya Air Departemen Idaho untuk meningkatkan kesadaran tentang produktivitas dan keuntungan finansial dari peningkatan efisiensi energi dalam sistem industri.
Fasilitas Caldwell adalah salah satu yang terbesar di perusahaan; itu menghasilkan sekitar 270 juta pon kentang goreng beku per tahun. Situs ini dilengkapi dengan tiga boiler pipa air berbahan bakar gas alam. Dua dinilai untuk 70.000 pound per jam (lb/jam), dan yang ketiga dinilai untuk 60.000. Uap dihasilkan pada 275 pon per inci persegi gauge (psig) jenuh. Uap penting untuk proses produksi pabrik karena secara langsung mendukung tugas mengupas, merebus, dan menggoreng kentang.
Ikhtisar Proyek
Pada tahun 2000, Simplot menugaskan Steam Engineering Inc., untuk menganalisis sistem uap di fasilitas produksinya sebagai bagian dari program efisiensi energi perusahaan. Dalam penilaian awal di lokasi Caldwell, analis menemukan bahwa beban uap rata-rata pembangkit adalah 90.000 lb/jam, dan tingkat udara pembakaran berlebih rata-rata 50 persen. Selain itu, kandungan oksigen gas buang mencapai 7,5 persen. Ketiga boiler dioperasikan pada sebagian beban untuk memenuhi permintaan uap puncak pabrik sebesar 140.000 lb/jam. Tingkat permintaan puncak dan rata-rata berfluktuasi terus-menerus karena wadah pengupas kentang harus diisi dengan cepat untuk menguapkan uap air di dalam kentang. Penggunaan kembali kondensat sangat minim; hanya kondensat bertekanan tinggi dari penukar panas minyak panas yang dikembalikan ke boiler.
Kesimpulan awalnya adalah efisiensi sistem uap dapat ditingkatkan secara dramatis dengan memasang burner baru yang dilengkapi dengan kontrol pemosisian paralel dan menambahkan sistem trim oksigen gas buang untuk mengurangi jumlah udara berlebih yang dibutuhkan untuk pembakaran berkualitas.
Pada tahun 2002, ketika perangkat lunak SSAT diluncurkan, Moir menggunakannya untuk menilai sistem uap pabrik Caldwell. Model SSAT menunjukkan potensi penghematan gas alam lebih dari 25.000 MMBtu per tahun jika boiler di fasilitas Caldwell dapat dioperasikan secara konsisten pada tingkat oksigen gas buang 3 persen. Ini dapat dicapai dengan memutakhirkan burner dan kontrol yang menua dan memasang sistem trim oksigen gas buang pada boiler, seperti yang ditunjukkan dalam analisis sebelumnya. Selain itu, model SSAT menunjukkan bahwa peningkatan sistem kondensat akan memungkinkan lebih banyak kondensat yang diperoleh kembali, bahwa boiler dapat beroperasi pada tingkat udara pembakaran berlebih sebesar 10 persen, dan bahwa hanya dua boiler yang dapat memenuhi beban uap pabrik.
Implementasi Proyek
Manajemen Simplot memutuskan untuk menerapkan rekomendasi Steam Engineering, berdasarkan analisis SSAT, di fasilitas Caldwell terlebih dahulu. Jika proyek Caldwell berhasil, maka tindakan serupa akan dilakukan di lokasi Simplot lainnya setelah evaluasi berbasis SSAT.
Untuk meminimalkan waktu henti produksi, burner dan kontrol baru dipasang pada dua boiler selama pemadaman pabrik yang dijadwalkan. Setelah burner yang ada dilepas, pelat muka baru dipasang di setiap bagian depan boiler sebelum burner baru dapat dipasang. Kemudian, kipas udara pembakaran baru, saluran resirkulasi gas buang, analisa oksigen gas buang dan sistem kontrol boiler dengan sistem trim oksigen dipasang di setiap boiler. Setelah semua perbaikan selesai, personel pabrik dapat memenuhi beban uap pabrik dengan menggunakan lebih sedikit uap dan gas alam tanpa mengurangi produksi.
Hasil Proyek
Proyek pabrik Caldwell telah meningkatkan efisiensi sistem uap pabrik secara signifikan. Karena burner baru lebih efisien dan meresirkulasi gas buang lebih baik, boiler sekarang beroperasi pada tingkat oksigen gas buang rata-rata 3 persen atau kurang. Beban uap puncak pembangkit sekarang 110.000 lb/jam, dan dua boiler mampu memenuhi beban itu, pada tingkat udara pembakaran berlebih hanya 10 persen. Proyek ini menyederhanakan proses pengembalian kondensat dengan membawa kondensat langsung ke deaerator dan membiarkan tekanan deaerator mengapung. Hal ini memungkinkan pabrik mencapai tingkat pemulihan kondensat sebesar 50 persen dan mematikan lima pompa kondensat pabrik.
Proyek pabrik Caldwell telah mengurangi konsumsi gas alam tahunan sebesar 52.000 MMBtu (7,5 persen dari konsumsi tahunan sebelumnya), dengan penghematan biaya sebesar $279.000 per tahun. Penghematan listrik tahunan mencapai 526.000 kWh, menghemat $20.000 lagi per tahun, karena pompa kondensat dan kipas draft boiler pada boiler ketiga tidak terhubung. Perubahan ini juga menghemat $30.000 dalam biaya pemeliharaan tahunan. Total penghematan proyek tahunan adalah $329,000. Karena total biaya proyek adalah $373.000, pengembalian sederhana kurang dari 14 bulan. Selain itu, produksi sekarang lebih dapat diandalkan; tidak ada pemadaman boiler yang dilaporkan sejak proyek selesai.
Sejak penyelesaian proyek, manajemen Simplot telah mengamanatkan penggunaan SSAT untuk mengevaluasi sistem uap di semua fasilitas produksinya. Hingga saat ini, langkah-langkah efisiensi berdasarkan pemodelan SSAT telah direplikasi di delapan fasilitas Simplot lainnya, menghasilkan penghematan gas alam tahunan sebesar 176.000 MMBtu. Selain itu, keterlibatan Simplot dengan Prakarsa Efisiensi Pemrosesan Makanan AS Barat (bagian dari Kolaborasi Kemajuan Teknologi Negara) telah memungkinkan keahlian yang dikembangkan dalam upaya ini untuk dimanfaatkan dengan upaya efisiensi energi sukses lainnya untuk kepentingan perusahaan pengolahan makanan lainnya di barat. Amerika Serikat.
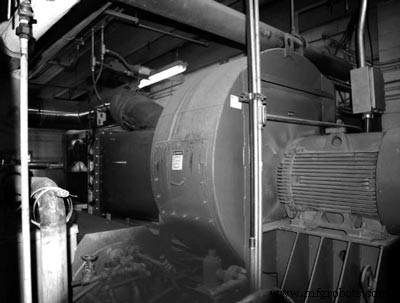
Gambar 1. Rakitan Udara Masuk
Pelajaran yang Dipetik
Menggunakan metodologi dan alat yang seragam untuk mengevaluasi dan mengoptimalkan sistem uap industri dapat menghasilkan strategi yang berharga untuk meningkatkan kinerja sistem ini dan menghemat energi. Di pabrik Caldwell J.R. Simplot, analisis berbasis SSAT memvalidasi potensi penghematan energi yang dihasilkan dari strategi konvensional untuk mengoptimalkan efisiensi sistem uap. Analisis SSAT juga mengidentifikasi manfaat tambahan dari strategi tersebut.
Setelah keberhasilan proyek, Simplot melihat SSAT sebagai alat yang efektif, “common denominator” untuk mengevaluasi peluang untuk meningkatkan semua sistem uap perusahaan. Oleh karena itu, Manajemen menetapkan kebijakan perusahaan untuk melembagakan penggunaan SSAT di semua fasilitas Simplot yang menggunakan steam. Sampai saat ini, SSAT telah digunakan di delapan fasilitas Simplot lainnya, dan analisis yang dihasilkan diperbarui setiap tahun. Alat dan metodologi yang seragam seperti ini dapat dengan mudah diterapkan di fasilitas industri mana pun yang menggunakan uap.
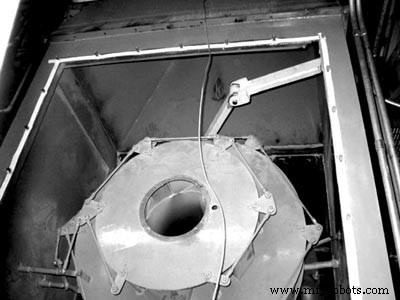
Gambar 2. Rumah Burner dan Burner
Mendefinisikan efisiensi pembakaran
Efisiensi pembakaran adalah ukuran seberapa efektif kandungan panas suatu bahan bakar dipindahkan menjadi panas yang dapat digunakan. Suhu tumpukan dan tingkat oksigen gas buang merupakan indikator utama efisiensi pembakaran. Mengoperasikan boiler dengan jumlah udara berlebih yang optimal meminimalkan kehilangan panas ke atas cerobong dan meningkatkan efisiensi pembakaran. Dalam praktiknya, kondisi pembakaran jarang ideal; udara tambahan atau "kelebihan" harus dipasok untuk membakar bahan bakar sepenuhnya.
Jumlah udara berlebih yang benar ditentukan dengan menganalisis tingkat oksigen gas buang. Udara berlebih yang tidak memadai menghasilkan bahan bakar yang tidak terbakar, sementara udara berlebih yang terlalu banyak menyebabkan panas yang hilang — menunjukkan efisiensi bahan bakar-ke-uap boiler yang lebih rendah. Boiler berbahan bakar gas alam yang beroperasi secara efisien harus memiliki tingkat udara berlebih sebesar 10 persen. Ketika komposisi bahan bakar atau aliran uap sangat bervariasi, sistem trim oksigen on-line harus dipertimbangkan. Sistem trim oksigen memberikan umpan balik ke kontrol burner untuk meminimalkan pembakaran berlebih secara otomatis
Alat Penilaian Sistem Steam Praktik Terbaik DOE ITP
BestPractices memiliki seperangkat alat untuk mengevaluasi dan mengidentifikasi peluang penghematan energi dalam sistem uap. Alat utama yang berhubungan dengan steam adalah Steam System Assessment Tool (SSAT). SSAT adalah paket perangkat lunak yang memungkinkan pengguna untuk membuat model berbagai skenario peningkatan dan secara akurat memperkirakan potensi penghematan energi dan biaya dari peningkatan sistem uap individual. Perangkat lunak ini dan perangkat lunak terkait uap lainnya dapat diperoleh melalui situs web EERE (www.oit.doe.gov/bestpractices/software_tools.shtml), atau dapat dipesan dari Pusat Informasi EERE dengan menghubungi 877-337-3463.
Untuk informasi lebih lanjut tentang Program Teknologi Industri Departemen Energi AS, kunjungi http://www1.eere.energy.gov.