Cakrawala baru dalam pengelasan komposit termoplastik
Blog ini menyertai fitur Sep 2018 “Pengelasan komposit termoplastik”. Ini adalah kompilasi gambar dan detail yang tidak sesuai dengan artikel cetak, termasuk garis waktu perkembangan pengelasan induksi dan rincian kualifikasi untuk pesawat komersial masa depan, serta bagian singkat tentang perbaikan, perkembangan otomotif dan termoset hingga termoplastik (TS -TP) pengelasan.
Hanya untuk menegaskan kembali mengapa rakitan komposit termoplastik las (TPC) menarik untuk struktur ringan dirgantara dan otomotif, bandingkan dua gambar di bawah sekat tekanan belakang Airbus A320. Gambar atas adalah versi saat ini yang terbuat dari aluminium. Perhatikan jumlah paku keling yang banyak. Sekarang bandingkan dengan demonstran TPC yang dilas yang disajikan oleh Premium Aerotec di pameran udara ILA 2018 di Berlin. Perhatikan tidak adanya paku keling. Untuk komposit, ini tidak hanya menghilangkan berat, waktu dan biaya pengencang, tetapi juga waktu dan biaya penempatan dan lubang pengeboran, ditambah pembersihan dan pemeriksaan lubang tersebut. Ini juga berarti struktur yang jauh lebih ringan tanpa bantalan laminasi yang diperlukan untuk mengimbangi pemotongan melalui serat bantalan beban.
Sekat tekanan belakang komposit termoplastik A320 yang dilas (bawah) menawarkan solusi tanpa paku keling vs. konstruksi aluminium saat ini (atas).
SUMBER:RUAG (atas) dan Aerotec Premium (bawah), Pusat Teknologi Produksi Ringan DLR (Augsburg, Jerman)
“Manfaat lainnya adalah pemeriksaan untuk struktur yang dilas lebih mudah dibandingkan dengan rakitan yang direkatkan dengan perekat,” kata Dr. Hans Luinge, R&D komposit termoplastik dan direktur pengembangan produk untuk pemasok bahan TPC TenCate-Toray Group. “C-scan bekerja dengan baik, menunjukkan jika tidak ada porositas pada laminasi, yang berarti lasannya bagus. Untuk struktur yang diikat dengan perekat, Anda dapat memiliki ikatan ciuman atau kontaminan yang sulit dideteksi.” Meskipun TenCate-Toray tidak mengembangkan teknologi pengelasan itu sendiri, itu mendukung berbagai proyek industri dan pelanggan. “Kami mengoptimalkan material kami sesuai kebutuhan,” kata Luinge, “dan mencoba membantu mengarahkan pengembangan ke arah yang benar berdasarkan partisipasi lama kami dalam upaya seperti TAPAS dan dengan mitra seperti KVE Composites, TPRC, pemasok tingkat, dan OEM.”
Perkembangan pengelasan induksi
KVE Composites telah mengembangkan pengelasan induksi untuk TPC sejak tahun 2001. Aplikasi awal menggunakan kain serat karbon/laminasi PPS, termasuk elevator dan kemudi untuk pesawat jet bisnis Gulfstream G650 dan Dassault Falcon 5X.
Komposit KVE membantu untuk mengembangkan produksi elevator dan kemudi las induksi GKN Fokker (kiri) untuk pesawat Gulfstream G650 (kanan) dan Dassault Falcon 5X.
SUMBER:KVE Composites, GKN Fokker (kiri) dan Gulfstream (kanan).
Aplikasi TPC las induksi lainnya termasuk pintu akses tangki bahan bakar yang diproduksi oleh AVIACOMP S.A.S. (Launaguet, Prancis dan sekarang bagian dari Sogeclair Group) untuk sayap Airbus A220 (sebelumnya Bombardier CSeries). (Aviacomp juga memproduksi stringer untuk badan pesawat TPC yang dilas STELIA yang ditampilkan di Paris Air Show 2017.)
Aviacomp menggunakan induksi teknologi pengelasan yang dikembangkan oleh KVE Composites dalam produksi pintu akses tangki bahan bakar TPC untuk pesawat berbadan sempit Airbus A220.
SUMBER:Aviacomp, bagian dari Grup Sogeclair.
Kategori umum pintu akses ini merupakan peluang bagi pengelasan TPC untuk menghemat biaya, yang ditunjukkan dalam studi desain dan manufaktur yang diselesaikan oleh KVE Composites. Bahkan pesawat yang lebih kecil dapat memiliki hingga 60 panel akses ini, semuanya berbentuk berbeda, dan biasanya dibuat menggunakan konstruksi sandwich komposit dengan inti sarang lebah mesin. “Jika Anda menggunakan rakitan termoplastik yang dilas, Anda dapat membuat semua panel akses yang berbeda untuk sebuah pesawat hanya dengan $100.000 dalam biaya perkakas, yang merupakan penghematan yang dramatis,” kata direktur pelaksana KVE Composites Harm van Engelen. “Kami tidak perlu membuat inti mesin, kami hanya menggunakan komponen 'seperti lego' — lembaran datar dan pengaku yang dicap — dilas bersama untuk membentuk berbagai bentuk. Juga, perkakas kami lebih seperti jig las, jadi biayanya relatif rendah vs. apa yang mereka gunakan saat ini. Semua panel akses untuk pesawat dapat dibuat dalam satu sel las.”
Perakitan termoplastik yang dilas untuk panel overhang pesawat dapat dibuat menggunakan sel pembentuk dan pengelasan otomatis dan hemat $100.000 untuk biaya perkakas. SUMBER:Komposit KVE.
KVE Composites terus mengembangkan teknologi pengelasan TPC, seperti yang diilustrasikan dalam garis waktu di bawah ini. Sel produksi yang ditampilkan di bawah untuk tahun 2019 adalah mesin Falko ATL (peletakan pita otomatis), diproduksi oleh Boikon (Leek, Belanda) menggunakan efektor ujung pengelasan ultrasonik yang dikembangkan oleh GKN Fokker. “Sel robot ini memungkinkan proses dan sistem kontrol yang lebih efisien untuk tingkat produksi suku cadang TPC volume berikutnya vs. metode pengambilan dan penempatan yang digunakan saat ini,” jelas kepala R&D KVE Composites Maarten Labordus. “Misalnya, Anda dapat sepenuhnya otomatis meletakkan laminasi kulit dan tulang rusuk untuk permukaan kontrol jet regional (yang kira-kira berukuran 60mm x 3m), menerapkan langkah konsolidasi dan pembentukan di luar autoklaf, dan kemudian menyelesaikan perakitan dalam sel las yang bersebelahan.” Mesin ATL Falko juga mendemonstrasikan kontrol loop tertutup yang telah dikembangkan oleh GKN Fokker untuk pengelasan ultrasonik. “Mesin ini mampu mengontrol tingkat energi sesuai kebutuhan per jenis material, ketebalan dan bentuk, namun konsolidasi lelehan penuh dari bentuk awal datar diperlukan setelah itu selama pencetakan bagian TPC yang sudah jadi,” jelas Arnt Offringa, kepala R&T Aerostruktur untuk GKN Fokker.
SUMBER:KVE Composites Kualifikasi
Ditampilkan di atas sebagai inisiatif pengembangan utama pada tahun 2017, kualifikasi proses pengelasan induksi untuk aerostruktur TPC merupakan prioritas berkelanjutan. Menurut abstrak untuk presentasi KVE Composites yang akan datang pada tanggal
4
Int. Kon. dan Pameran Komposit Termoplastik (ITHEC, 30-31 Oktober 2018 di Bremen, Jerman), selama beberapa tahun terakhir pengelasan komposit termoplastik (TPC) telah melihat pergeseran dari polimer seperti PPS dan PEI menuju polimer kelas atas seperti MENGINTIP , PEKK dan sekarang Low Melt PAEK (LM PAEK, baca lebih lanjut di blog saya "PEEK vs. PEKK vs. PAEK ..."), serta ke kaset UD yang ditempatkan secara otomatis dan laminasi yang lebih tebal untuk struktur yang lebih banyak dimuat. Sebagai tanggapan, KVE Composites telah berusaha untuk meningkatkan dan menstandarisasi perkakas dan peralatan serta model simulasi berbasis FEA.
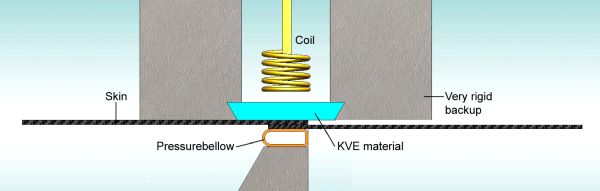
Pengaturan standar untuk kualifikasi pengelasan induksi dengan material baru.
SUMBER:Komposit KVE
Untuk membantu pematangan dan kualifikasi proses pengelasan induksi dengan laminasi komposit baru ini, KVE Composites telah mengembangkan set-up standar untuk pengelasan geser putaran tunggal dan juga kupon uji tarik-L dan T. Pengaturan ini mencakup:
- Rangka kaku untuk menahan beban akibat tekanan pada laminasi selama pengelasan.
- Blok pahat bawah yang dapat ditempatkan di bawah rangka untuk memungkinkan pengelasan panel standar yang dapat direproduksi.
- Mandrel tiup (tekanan di bawah pada gambar di atas) di blok alat bawah yang dapat mengembang hanya dalam satu arah untuk menekan laminasi yang dilas terhadap heatsink khusus (“bahan KVE” pada gambar di atas) untuk membatasi panas pada pengelasan antarmuka.
Dengan menukar blok alat yang lebih rendah, berbagai kupon standar dapat dilas dan kemudian diperiksa secara ultrasonik, setelah itu kupon yang lebih kecil dapat dipotong dan diuji secara mekanis. Pengaturan standar ini telah diinstal oleh:
- Pusat Penelitian Termoplastik (TPRC, Enschede, Belanda)
- McNair Center di University of South Carolina (Columbus, SC, AS)
- Pusat Dirgantara Belanda (NLR, Marknesse, Belanda).
Pengelasan induksi standar set-up di KVE (kiri) dan sampel serat karbon UD/PEKK yang dilas dengan termokopel untuk merekam suhu pada garis las (kanan).
SUMBER:Komposit KVE.
Perbaikan
Area pengembangan utama lainnya adalah bagaimana memperbaiki aerostruktur TPC. “Kami fokus dulu pada struktur CF fabric/PPS yang berkualitas dan terbang,” kata Labordus. “Prosesnya pada dasarnya sama dengan yang digunakan untuk perbaikan komposit termoset:lepaskan bahan yang rusak, siapkan area itu dengan selendang lancip dan kemudian rekatkan dalam tambalan perbaikan prepreg. Labordus mengatakan salah satu masalahnya adalah prepreg termoplastik pada suhu kamar berbentuk papan dan tidak lengket, "jadi sulit untuk mendapatkan geometri yang cocok." Namun, dia yakin sistem perbaikan robot yang dikembangkan oleh Airbus, Lufthansa, dan lainnya menawarkan solusi.
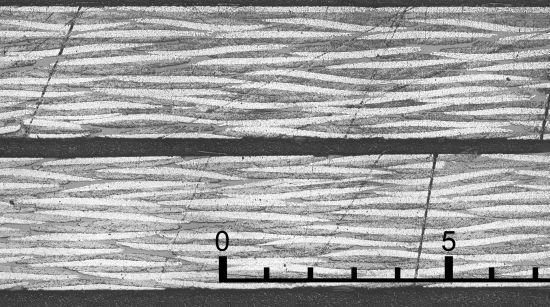
Sebagai bagian dari pengembangan lanjutan perbaikan komposit termoplastik struktural yang dilas, Komposit KVE telah mencapai sambungan lancip linier 2D yang dilas induksi pada kain CF/laminasi PPS dengan ketebalan yang seragam dan 90% sifat material murni.
SUMBER:Komposit KVE.
Sistem seperti itu menggunakan metrologi untuk mengukur selendang lancip yang dikerjakan secara robotik dengan tepat dan kemudian merekatkan tambalan yang telah dibuat dengan mesin lancip agar sesuai. “Kami ingin menggunakan pengelasan induksi untuk mengelas tambalan termoplastik ke struktur aslinya,” kata Labordus, tetapi masih ada masalah yang harus diselesaikan. “Tergantung pada bentuk part dan patchnya, arus eddy tidak terbentuk di mana-mana, jadi kita bisa mendapatkan area yang dingin atau terlalu panas. Komposit KVE telah bekerja melalui ini dan mampu mencapai sambungan lancip linier 2D pada kain CF/laminasi PPS dengan ketebalan yang seragam dan las yang sempurna. “Kami berada dalam 10% dari sifat material perawan,” kata Labordus.
Langkah selanjutnya adalah mengelas induksi dua bagian persegi panjang masing-masing dengan tepi berkerut dan kemudian mengelas tambalan tirus ke lubang melingkar/elips dengan syal meruncing, yang pada dasarnya adalah metode yang digunakan untuk perbaikan komposit termoset. “Jika itu berhasil, kami akan beralih ke laminasi UD yang dibuat dengan MENGINTIP dan PEKK,” kata Labordus. Dia mencatat bahwa sistem untuk menggunakan kumparan induksi untuk melakukan perbaikan di lapangan belum ditunjukkan, "tetapi dapat melakukannya di laboratorium." Masalah lainnya adalah bagaimana menerapkan tekanan untuk kontak yang cukup dekat antara patch perbaikan dan permukaan runcing. “Saat ini tekanan yang digunakan pada alat lab adalah 5 bar. Saya tidak yakin apakah tekanan dari kantong vakum saja sudah cukup, tetapi dengan bahan UD yang lebih rata, 1 batang dari kantong vakum saja mungkin tidak masalah.”
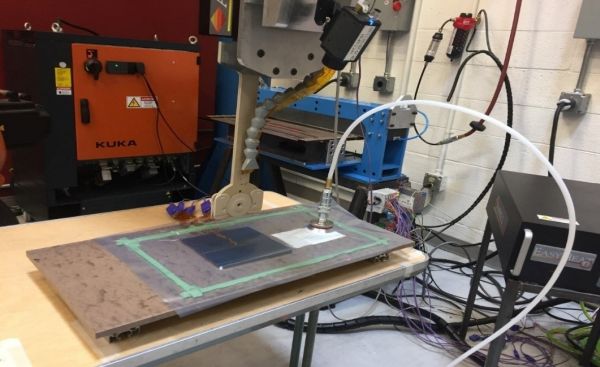
Pengelasan induksi di bawah kantong vakum – kemungkinan memungkinkan untuk perbaikan komposit termoplastik di lapangan di masa depan – sedang dikembangkan oleh Michel van Tooren dan timnya di University of South Carolina McNair Center. SUMBER:Michel van Tooren.
Pekerjaan di KVE Composites ini diperluas oleh Michel van Tooren, direktur SmartState Center for Multifunctional Materials and Structures, bagian dari McNair Center di University of South Carolina (Columbia, SC, AS). “Kami adalah komposit termoplastik pengelasan induksi di bawah kantong vakum, yang sangat mirip dengan bagaimana perbaikan komposit di lapangan saat ini dilakukan dengan pengikat panas dan selimut panas,” jelasnya. “Kantong vakum berperilaku seperti perkakas lunak untuk kompresi kedua bagian. Anda menerapkan arus induksi dan mencapai perbaikan leleh. Anda hanya perlu mendefinisikan batasan proses dan parameter. Dalam beberapa hal ini lebih mudah daripada perbaikan termoset karena Anda selalu dapat mencairkan kembali perbaikan jika diperlukan, bahkan di belahan dunia lain atau setelah 20 tahun layanan. Dan hasilnya bukan ikatan perekat melainkan bagian kohesif, sehingga Anda menghilangkan semua masalah dengan ikatan dan bagaimana mengetahui apakah Anda memiliki ikatan yang baik dalam perbaikan termoset.” Dia juga percaya bahwa dengan teknologi perbaikan robot otomatis sedang dikembangkan sekarang, "pengelasan induksi perbaikan akan relatif mudah."
Pengelasan termoset ke termoplastik
Van Tooren juga mengembangkan pengelasan induksi untuk menggabungkan termoset dan komposit termoplastik. “Kami memperkenalkan termoplastik ke komposit termoset, tetapi hanya di tempat yang ingin kami las,” jelasnya. “Kami mencangkok pada nanopartikel dan melakukan sedikit polimerisasi silang. Hasilnya adalah pulau termoplastik yang ditanamkan ke dalam dan dilebur secara kimia dengan komposit termoset. Saya kemudian bisa mengelas ke pulau termoplastik. ” Sekali lagi, visinya adalah metode alternatif untuk penggabungan dan perakitan komposit yang menghindari lubang pengeboran dan masalah yang terkait dengan ikatan perekat konvensional.
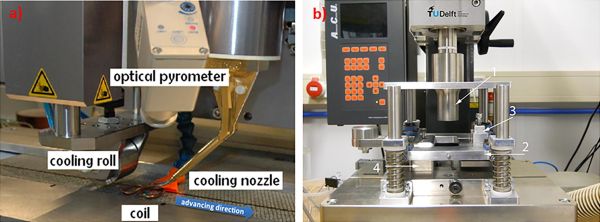
Skema sambungan TSC-TSC melalui lapisan kopling termoplastik PVB sebelum pengelasan (atas). Pengaturan (bawah) untuk pengelasan Induksi (kiri) dan pengelasan ultrasonik (kanan).
SUMBER:“Pengelasan hibrida komposit berbasis CF/epoksi”.
Pengelasan laminasi komposit termoset (TSC) ke laminasi TPC (atau pengelasan TS-TP) sedang dilakukan oleh beberapa organisasi penelitian. Irene Fernandez Villegas di TU Delft — yang disebutkan dalam artikel cetak sebagai pemimpin dalam mengembangkan pengelasan ultrasonik berkelanjutan TPC — ikut menulis makalah tahun 2017 berjudul “Pengelasan hibrida komposit berbasis epoksi yang diperkuat serat karbon” bersama dengan Francesca Lionetto di Universitas Salento (Lecce, Italia), Silvio Pappad di CETMA Composites (Brandisi, Italia), dan lainnya. Dasar-dasarnya adalah sebagai berikut:
- Polyvynilbutyral (PVB) adalah semi-kristal, polimer termoplastik berbiaya rendah dengan suhu leleh 150-170 °C yang ditandai dengan kemampuan mengikat dan pembentukan film yang sangat baik serta daya rekat ke banyak permukaan.
- PVB (Mowital, dipasok oleh Kurakay) digunakan sebagai lapisan penghubung, ditambahkan dan diawetkan bersama ke kain serat karbon 14-lapis/laminasi TSC epoksi (prepreg Hexcel 3501-6 dengan kandungan volume serat 58% dan 180 penyembuhan °C).
- Interlocking makro-mekanis antara lapisan kopling PVB dan komposit CF/epoksi dicapai melalui penetrasi sebagian resin PVB ke dalam lapisan pertama TSC (biasanya antara 10 dan beberapa ratus mikron dengan ketebalan) selama co-curing dan difusi monomer epoksi ke dalam film termoplastik PVB.
- Pengelasan induksi dan proses pengelasan ultrasonik menghasilkan sambungan las yang cukup kuat, dengan sambungan CF/epoksi ke CF/epoksi yang dihasilkan dilas melalui lapisan kopling PVB yang menunjukkan kekuatan geser putaran 25 MPa, yang berada dalam kisaran tipikal nilai kekuatan untuk sambungan berperekat CF/epoksi.
Otomotif
Hampir semua perusahaan yang termasuk dalam artikel cetak las termoplastik sedang melihat aplikasi otomotif serta dirgantara. “Pengelasan membantu membuat komposit menjadi kompetitif dibandingkan aluminium,” kata Offringa di GKN Fokker. “Otomotif juga melihat pengelasan sebagai alternatif cepat untuk bonding. Kami telah berbicara dengan beberapa perusahaan otomotif mengenai pemrosesan komposit yang cepat.” Dia menunjukkan bahwa bodi mobil komposit serat karbon sebagian besar termoset, terikat dengan ketebalan perekat tertentu. “Jika Anda bisa membuat bagian ini menggunakan termoplastik komposit dan menghilangkan celah di antara komponen dengan mengelas rakitan, lalu Anda dapat membuat struktur bodi yang lebih kaku, yang memberikan manfaat bobot, biaya, dan kinerja.”
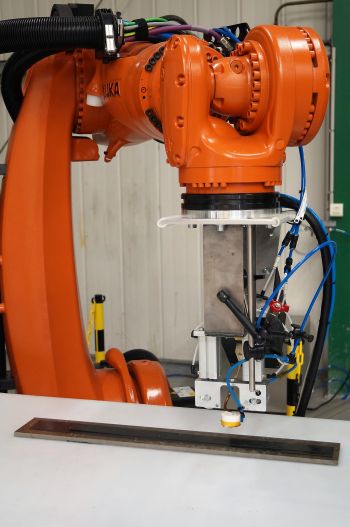
Dinamika Integritas Komposit pengaturan proses pengelasan induksi.
SUMBER:Integritas Gabungan.
Jérôme Raynal, manajer pengembangan bisnis untuk Integritas Komposit juga melihat potensi. Perusahaannya bekerja sama dengan STELIA Aerospace untuk mengembangkan proses pengelasan induksi dinamis yang digunakan untuk menyambung pita stringer CF/PEKK UD dan kulit badan pesawat di demonstran TP, yang diresmikan di Paris Air Show 2017. “Kami telah mengembangkan pengelasan resistif untuk otomotif dengan komposit poliamida [PA, nilon] dan polipropilen [PP],” kata Raynal. “Kami memiliki berbagai teknologi berbeda untuk ini. Misalnya, kita dapat menyematkan kawat logam di satu bagian, menghubungkannya dengan bagian lain dan menyuntikkan arus. Kami juga dapat menempatkan patch resistif serat karbon pada antarmuka pengelasan untuk menghasilkan panas pengelasan yang dibutuhkan.” Dalam satu pengembangan, dua komponen yang terbuat dari CF/PA dilas menggunakan tambalan resistif yang dirancang khusus yang dibuat dengan polimer yang sama dan bulu serat kaca untuk mengisolasi secara elektrik laminasi yang bersebelahan dan memusatkan energi pada garis las. Bagaimana dengan sisipan logam yang sangat khas di suku cadang otomotif? “Bagian dengan sisipan logam tidak ada masalah dengan pengelasan resistansi, dan dengan pengelasan induksi Anda akan menggunakan koil yang dirancang khusus atau memodifikasi medan elektromagnetik dan arus dengan cara lain,” jawab Raynal. “Ini harus dikembangkan, tetapi mirip dengan apa yang telah kami tunjukkan untuk produksi otomatis struktur pesawat.”
Perkembangan lebih lanjut dan proyek lainnya
Satu catatan tentang gambar pembuka. Ini menunjukkan rendering CAD dari proses otomatis yang dikembangkan oleh Pusat Teknologi Produksi Ringan DLR (DLR ZLP, Augsburg, Jerman) menggunakan pengelasan ultrasonik menuju robot industri KUKA Quantec KR210 untuk menggabungkan delapan bagian TPC menjadi sekat tekanan belakang (RPB) untuk pesawat tipe A320. Dalam artikel cetak terlampir tentang pengelasan TPC, saya membahas pengembangan pengelasan resistansi DLR ZLP. metode yang digunakan pada demonstran A320 RPB Premium Aerotec yang dipamerkan pada pameran udara ILA 2018 di Berlin. Menurut Lars Larsen, manajer grup untuk teknologi perakitan dan penyambungan di DLR ZLP, “Sejajar dengan proses pengelasan resistansi menggunakan 'jembatan las', kami juga telah mengembangkan kepala pengelasan ultrasonik yang digerakkan secara robotik. Kami telah menyelesaikan tes pendahuluan untuk menentukan parameter proses pengelasan yang relevan, dan dalam beberapa bulan ke depan kami akan menyempurnakan integrasi end-effector pengelasan ultrasonik dalam robot kami. Tujuan kami adalah mengembangkan proses industri tunggal untuk mengelas stringer badan pesawat dan sekat tekanan belakang yang dibuat menggunakan komposit termoplastik.”
Proyek lain yang tidak sempat saya bahas kali ini termasuk EireComposites dan partisipasinya dalam proyek Ybridio dan Innova, mengejar potensi pengelasan untuk mengurangi biaya dan meningkatkan otomatisasi. Perusahaan melaporkan pengelasan induksi dan kemampuan pengelasan resistansi untuk komposit CF/PEEK, CF/PEKK dan GF/PP dan bahwa pengelasan termoplastik dievaluasi untuk sayap Bombardier CSeries (sekarang Airbus A220).
Tods Aerospace, sekarang bagian dari Unitech Aerospace, berpartisipasi dalam Program Eksploitasi Teknologi Dirgantara Nasional (NATEP) yang disponsori oleh Rolls-Royce yang melihat pengembangan teknik pengelasan resistensi yang tidak menggunakan implan tertanam logam. TenCate-Toray dan National Composites Center (Bristol, Inggris) juga merupakan mitra.
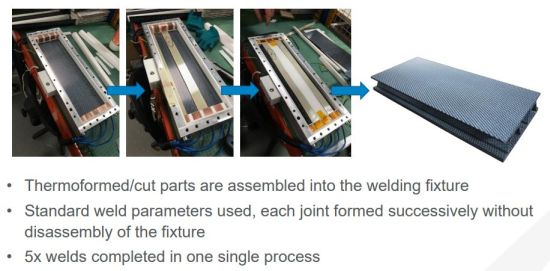
Demonstran proses ini mengeksplorasi metode untuk membuat struktur TPC kaku. SUMBER:Unitech Aerospace (mulai dari Bagian 6, hal. 39)
Nantikan, karena saya berencana untuk membahas perkembangan Laser Zentrum Hannover (LZH) dengan pengelasan laser komposit termoplastik dalam waktu dekat.
SUMBER:LZH Laser Zentrum Hannover eV