Panduan pemesinan CNC terbaik
Pemesinan Computer Numerical Control (CNC) adalah proses manufaktur subtraktif modern, efisien, dan otomatis yang memungkinkan produsen membuat komponen berulang dengan kualitas konsisten dari berbagai bahan, termasuk plastik, logam, dan komposit. Saat ini, suku cadang mesin CNC dapat ditemukan di berbagai industri yang berbeda, mulai dari luar angkasa hingga otomotif hingga medis.
Awal mula teknologi CNC dapat ditelusuri kembali ke beberapa titik berbeda dalam sejarah. Alat permesinan modern pertama muncul pada tahun 1775 ketika para industrialis mengembangkan alat bor yang memungkinkan produsen memproduksi silinder mesin uap dengan tingkat akurasi dan presisi yang lebih konsisten.
Namun, nenek moyang teknologi komputasi modern muncul di awal abad ini, muncul dari industri tekstil. Pada 1725, Basile Bouchon mulai menggunakan sistem lubang berlubang di pita kertas untuk menyandikan data. Puluhan tahun kemudian pada tahun 1805, Joseph Marie Jacquard menyempurnakan prosesnya, menukar pita kertas dengan kartu punch yang kokoh. Ketika diikat secara berurutan, kartu punch mengarahkan bagaimana kain ditambahkan ke alat tenun, menyederhanakan proses dan memberikan salah satu contoh pemrograman pertama. Mesin ini, alat tenun Jacquard, merupakan cikal bakal solusi komputasi dan otomatisasi modern kami.
Panduan untuk semua hal yang terkait dengan pemesinan CNC ini akan menjelaskan cara kerja proses pemesinan CNC modern, termasuk opsi material, pertimbangan desain, penggerak biaya, dan banyak lagi. Teruskan membaca atau klik di sini untuk mengunduh PDF.
Jenis mesin CNC
Saat ini, ada beberapa proses teknis yang disertakan di bawah payung permesinan CNC.
Pemesinan 3-sumbu:Penggilingan dan pembubutan
Setelah operator memasukkan instruksi pemesinan, mesin CNC 3-sumbu akan melakukan operasi input dengan menggunakan alat pemotong untuk memotong sepanjang tiga sumbu:X (kiri ke kanan), Y (depan ke belakang), dan Z (atas-dan- turun). Penggilingan CNC dan pembubutan CNC adalah dua contoh umum pemesinan 3-sumbu.
Penggilingan CNC 3-sumbu melibatkan pemasangan blok material — juga disebut benda kerja atau “kosong” — dengan wakil atau alas mesin. Ini menahan benda kerja tetap sebagai alat pemotong dan bor berputar, yang dipasang pada poros tengah, membuat potongan untuk menghilangkan material dan membentuk komponen akhir. Mesin penggilingan CNC 3-sumbu mudah diprogram dan dioperasikan dan dapat digunakan untuk membuat sebagian besar bagian dengan desain geometris sederhana.
Karena pahat dan bor terbatas pada tiga sumbu, beberapa fitur desain atau area kosong mungkin sulit untuk diselesaikan atau dijangkau (misalnya, bentuk yang tidak konvensional atau rongga yang dalam dan sempit). Namun, beberapa pengaturan dapat membantu mengarahkan benda kerja agar alat berat mencapai fitur ini. Meskipun hampir setiap pekerjaan pemesinan 3-sumbu memiliki lebih dari satu pengaturan per bagian, terlalu banyak pengaturan per bagian dapat dengan cepat meningkatkan biaya produksi. Pemrosesan bagian yang rumit secara geometris dapat, misalnya, mengharuskan operator untuk memposisikan ulang benda kerja secara manual, yang dapat memengaruhi kecepatan pemrosesan, meningkatkan biaya terkait tenaga kerja, dan menciptakan lebih banyak peluang untuk kesalahan manusia.
Proses pembubutan CNC beroperasi sedikit berbeda. Kosong dipasang pada spindel yang berputar, dan mesin bubut kemudian membentuk perimeter bagian dalam dan luar atau membuat lubang di sekitar sumbu tengah benda kerja. Batasan desain yang paling signifikan dengan mesin bubut CNC adalah bahwa mereka selalu menghasilkan bagian yang simetris secara rotasi. Oleh karena itu, prosesnya ideal untuk pembuatan suku cadang seperti sekrup, mangkuk, atau kaki kursi. Untuk jenis komponen bulat ini, mesin bubut dapat menghasilkan potongan lebih cepat dan dengan biaya lebih rendah daripada mesin penggilingan CNC, terutama saat memproduksi komponen dalam volume tinggi.
Pemesinan 5-sumbu atau multi-sumbu
Proses pemesinan multi-sumbu memungkinkan pemotongan mengimplementasikan kebebasan bergerak yang lebih besar saat benda kerja digiling atau diputar. Proses 3-sumbu memungkinkan blanko atau pahat berputar, tetapi tidak keduanya. Sebaliknya, proses 5-sumbu memungkinkan benda kerja dan pahat berputar dan bergerak sepanjang sumbu X, Y, dan Z secara bersamaan. Pemesinan CNC 5-sumbu menghemat waktu dan ideal untuk membuat suku cadang yang kompleks dan presisi seperti yang ditemukan di industri medis, minyak dan gas, serta kedirgantaraan.
Keluarga mesin CNC multi-sumbu mencakup tiga proses:
- Penggilingan CNC 5-sumbu yang diindeks: Selama operasi penggilingan 5-sumbu yang diindeks, pahat pemotong tidak hanya dapat bergerak di sepanjang tiga sumbu linier, tetapi di antara operasi, meja pemesinan dan kepala pahat dapat berputar ke dua arah. Manfaat paling penting dari penggilingan 5-sumbu adalah bahwa blanko tidak perlu lagi disesuaikan secara manual di antara operasi pemotongan, yang memungkinkan untuk membuat komponen dengan geometri kompleks secara lebih akurat dan dengan efisiensi yang lebih besar. Pemesinan 5-sumbu yang diindeks sangat bagus untuk membuat komponen seperti rumahan, jig, dan perlengkapan. Prosesnya berada di antara penggilingan CNC 3-sumbu dan pemesinan CNC 5-sumbu kontinu (lihat di bawah) dalam hal kecepatan, presisi, dan kemampuan untuk menangani geometri yang kompleks.
- Penggilingan CNC 5-sumbu terus menerus: Mesin penggilingan CNC 5-sumbu kontinu dapat memindahkan dan memutar pahat dan benda kerja secara bersamaan selama setiap operasi, memungkinkan pembuatan suku cadang dengan geometri yang sangat rumit dan permukaan yang halus. Meskipun ini adalah bentuk pemesinan CNC yang paling mahal dalam basis per bagian, biaya penggilingan CNC 5-sumbu terus menerus biasanya diimbangi dengan peningkatan permukaan akhir, kecepatan, dan stabilitas dimensi.
- Pemesinan mill-turning dengan perkakas langsung: Pembubutan penggilingan menggabungkan elemen mesin bubut CNC dengan alat penggilingan. Benda kerja ditempelkan pada spindel yang berputar sementara alat pemotong mengeluarkan material dari blanko. Dengan menggabungkan elemen mesin bubut CNC dengan alat frais, CNC pembubutan gilingan menawarkan tingkat akurasi dan keserbagunaan geometris yang tinggi, sehingga cocok untuk membuat suku cadang dengan simetri rotasi yang longgar, seperti poros bubungan atau kompresor sentrifugal.
Memilih jenis mesin CNC yang tepat
Saat memilih proses manufaktur untuk bagian Anda, Anda harus mengevaluasi apakah itu lebih cocok untuk pemesinan 3-sumbu atau 5-sumbu. Umumnya, suku cadang dengan desain yang lebih sederhana dapat dibuat dengan cepat dan terjangkau menggunakan mesin 3-sumbu, sedangkan mesin 5-sumbu lebih baik untuk membuat bagian yang rumit secara geometris dengan kecepatan dan akurasi yang ditingkatkan.
Jika Anda memiliki anggaran terbatas atau hanya perlu memotong permukaan yang rata, mesin 3-sumbu adalah cara yang tepat. Selain lebih terjangkau, mesin 3-sumbu lebih mudah diprogram, jadi Anda tidak perlu mengeluarkan biaya untuk bekerja dengan programmer dan operator 5-sumbu yang mahal. Selain itu, waktu persiapan lebih singkat dengan pemesinan 3-sumbu.
Jika Anda perlu menghasilkan bagian yang lebih dalam atau bagian dengan geometri kompleks, Anda akan ingin menggunakan pemesinan 5-sumbu. Menggunakan mesin 5-sumbu memungkinkan Anda mengerjakan benda kerja dari semua sisi tanpa memerlukan rotasi manual. Dengan pemesinan 5 sumbu, Anda akan mendapatkan hasil yang lebih tinggi, akurasi yang lebih besar, dan kebebasan bergerak yang lebih baik, serta kemampuan untuk memproduksi komponen yang lebih besar dengan lebih cepat.
Material CNC umum
Salah satu keuntungan dari pemesinan CNC adalah bahwa prosesnya kompatibel dengan banyak bahan yang berbeda, plastik dan logam menjadi dua keluarga bahan yang paling umum. Berikut adalah beberapa plastik dan logam yang mungkin Anda temui.
Polimer berperforma tinggi
- Akrilonitril butadiena stirena (ABS): ABS adalah termoplastik rekayasa tahan benturan dengan sifat mekanik yang sangat baik. Kuat dan kaku sambil mempertahankan tingkat fleksibilitas, ABS patut diperhatikan karena kuat secara mekanis, memberikan insulasi yang baik, dan tahan terhadap abrasi dan ketegangan.
- Polietilen densitas tinggi (HDPE): Salah satu polimer termoplastik paling serbaguna, HDPE adalah bahan yang fleksibel dan mudah diproses yang sangat tahan terhadap keretakan tegangan, bahan kimia, dan korosif — bahkan pada suhu rendah. Ini juga menawarkan kekuatan benturan yang sangat baik. HDPE biasanya digunakan untuk membuat botol plastik, sumbat, segel, isolator, pipa, dan banyak barang lainnya.
- Polietilen densitas rendah (LDPE): Terutama digunakan untuk membuat ortotik dan prostetik, plastik yang tangguh dan fleksibel ini mudah dilas dan disegel panas. Selain memberikan ketahanan kimia yang baik, LDPE tidak ideal untuk aplikasi yang membutuhkan kekakuan, kekuatan struktural tinggi, atau ketahanan suhu tinggi.
- Poliamida (PA) atau Nilon: Nylon adalah keluarga plastik gesekan rendah yang sangat cocok untuk mengganti komponen logam, seperti bantalan atau busing, karena kombinasi unik dari elastisitas, kekakuan, dan kekakuan. Nylon dapat diperkuat dengan berbagai aditif untuk menciptakan material dan sifat kimia tertentu atau dikombinasikan dengan plastik lain untuk meningkatkan kinerja dan karakteristik material.
- Poliamida (PA) atau Nilon 30% GF: Serat kaca, salah satu aditif paling umum untuk plastik rekayasa, secara dramatis meningkatkan kekuatan dan kekakuan bagian nilon. Sayangnya, serat ini juga meningkatkan kerapuhan material dan oleh karena itu direkomendasikan hanya untuk aplikasi yang tidak melibatkan tegangan atau defleksi berdampak tinggi.
- Polikarbonat (PC): Plastik ini banyak digunakan karena beberapa alasan — keras namun tetap ringan, merupakan isolator listrik yang baik, dan tahan panas secara alami. PC secara inheren transparan dan tembus cahaya dan mengambil pigmen dengan baik. Selain itu, PC tahan terhadap asam encer, oli, dan gemuk, tetapi rentan terhadap keausan hidrokarbon dan sinar UV.
- Polyetheretherketone (PEEK): Polimer berperforma tinggi dengan kombinasi unik dari sifat mekanik, PEEK tahan bahan kimia, aus, mulur, lelah, cair, dan tahan suhu. Selain dapat didaur ulang dan biokompatibel, bahan ini juga ringan, kuat, dan tidak larut dalam semua pelarut umum. Mirip dengan nilon, MENGINTIP dapat menggantikan logam di mesin CNC. Aplikasi umum untuk bahan ini termasuk unit piston, bagian-bagian mesin pesawat yang penting, dan jarum suntik gigi. Khususnya, ini adalah salah satu plastik mesin CNC yang lebih mahal di pasaran.
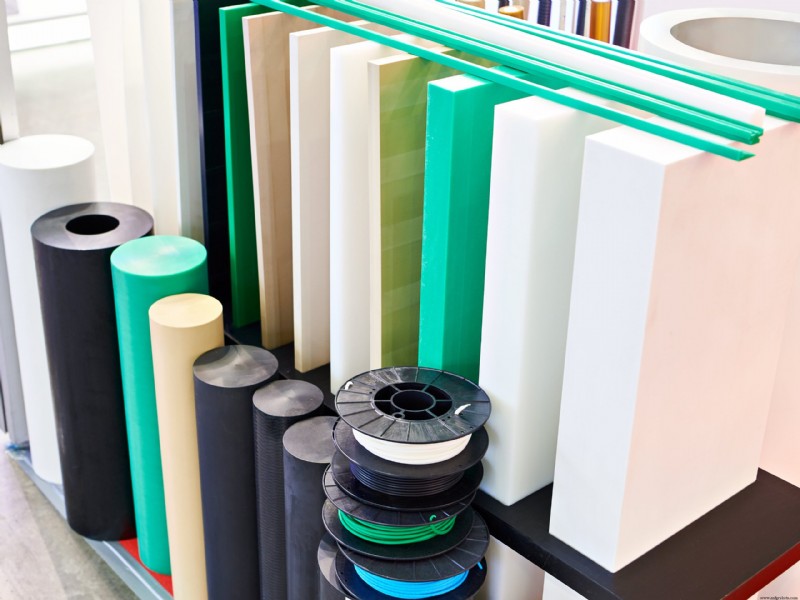
- Polieterimida (PEI): Umumnya dikenal sebagai ULTEM®, PEI adalah plastik berkinerja tinggi dan bahan pokok manufaktur. PEI tidak hanya kuat dan mudah digunakan, tetapi juga tahan terhadap bahan kimia dan api, dan dapat menahan suhu yang sangat tinggi tanpa kehilangan sifat listriknya yang stabil. Untuk alasan ini, PEI biasanya digunakan untuk membuat produk seperti papan sirkuit, kacamata, peralatan persiapan dan sterilisasi makanan, dan suku cadang pesawat. Ini adalah salah satu dari sedikit polimer termoplastik amorf yang tersedia secara komersial yang menjaga integritas mekaniknya pada suhu tinggi.
- Polimetil metakrilat (PMMA): PMMA adalah polimer termoplastik kaku yang sering disebut akrilik atau kaca akrilik. Sangat tahan pecah, bahan yang kuat dan ringan ini tembus cahaya dan tahan terhadap pelapukan dan sinar UV, membuatnya ideal untuk aplikasi tekanan rendah seperti rumah kaca, penutup lampu mobil dan lampu sein, atau panel surya. Namun, penting untuk diperhatikan bahwa PMMA rentan terhadap panas tinggi, benturan, keausan, dan abrasi, serta rentan terhadap keretakan di bawah beban berat.
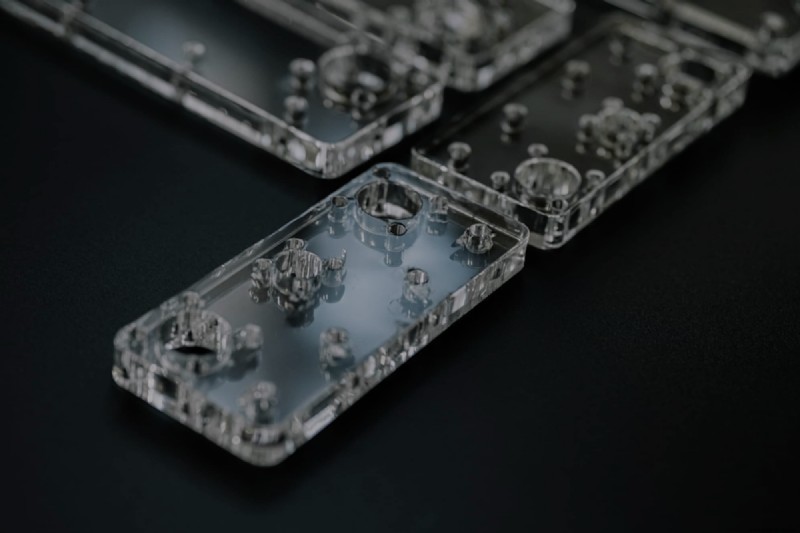
- Polioksimetilen (POM): Umumnya dikenal sebagai Acetal atau dengan nama mereknya, Delrin®, termoplastik tingkat rekayasa semi-kristal ini menawarkan stabilitas dimensi yang sangat baik, kekakuan, dan gesekan yang rendah. Karena sifat-sifat ini, asetal sering digunakan untuk membuat suku cadang yang sangat presisi yang digunakan dalam aplikasi yang memerlukan kekuatan tinggi, daya tahan, dan rentang suhu pengoperasian yang luas (-40 °C hingga 120 °C).
- Polipropilena (PP): Plastik hemat biaya ini ringan, sangat tahan terhadap bahan kimia di lingkungan korosif, dan tahan terhadap sebagian besar pelarut organik, bahan pembersih, dan elektrolit. Dibandingkan dengan LDPE dan HDPE, PP memiliki kekuatan benturan yang lebih rendah tetapi menawarkan kekuatan tarik yang lebih baik.
- Polytetrafluoroethylene (PTFE): PTFE, umumnya dikenal sebagai Teflon®, adalah polimer serbaguna yang disukai karena sifat mekaniknya. Tahan terhadap bahan kimia, suhu, cahaya, sinar UV, air, pelapukan, kelelahan, dan adhesi, PTFE umumnya ditemukan pada pelapis panci antilengket tetapi juga digunakan dalam semikonduktor, gasket, dan bahkan beberapa aplikasi medis. Meskipun PTFE adalah salah satu plastik yang paling tahan korosi, namun sensitif terhadap creep dan abrasi.
- Polivinil Klorida (PVC): PVC adalah salah satu plastik tertua di dunia. Sangat putih dan kaku, PVC adalah alternatif karet terjangkau yang telah diminati selama beberapa dekade. Menawarkan ketahanan yang kuat terhadap cahaya, bahan kimia, dan korosi, PVC adalah bahan yang populer di sektor perawatan kesehatan, TI, transportasi, tekstil, dan konstruksi.
- Polietilen dengan berat molekul ultra-tinggi (UHMW): Plastik yang tangguh, serbaguna, dan sangat mudah dikerjakan, UHMW dapat digunakan untuk membuat suku cadang dengan ketahanan abrasi dan aus yang tinggi, daya tahan, dan koefisien gesekan yang rendah. UHMW biasanya tidak cocok untuk aplikasi beban tinggi atau kondisi melebihi 80 hingga 100 °C.
Logam
Baja dan baja tahan karat, aluminium, dan logam lunak seperti kuningan, perunggu, titanium, dan tembaga adalah beberapa logam yang dapat dikerjakan dengan mesin paling populer. Meskipun baja dan aluminium adalah yang paling umum dikerjakan, setiap kelompok logam menawarkan serangkaian sifat fisik dan titik harga yang berbeda.
- Aluminium: Aluminium adalah logam non-magnetik yang lunak, berdensitas rendah, yang jauh lebih mudah dikerjakan daripada baja. Karena kekuatan tariknya yang rendah, logam ini sering dicampur dengan bahan lain untuk menonjolkan sifat fisik yang diinginkan. Aluminium umumnya sekitar 1/3 berat baja, yang berarti bahwa mereka menawarkan rasio kekuatan-terhadap-berat yang lebih baik. Ini dapat berguna dalam meringankan bagian. Mereka juga merupakan konduktor termal dan listrik yang jauh lebih baik daripada baja.
- Baja: Baja adalah logam berbasis besi yang telah dicampur dengan karbon dan logam lainnya, biasanya termasuk mangan, fosfor, atau belerang. Baja cenderung lebih kuat dan lebih tahan lama daripada aluminium. Namun, mereka juga lebih berat dan lebih sulit untuk dikerjakan tanpa menggunakan karbida atau alat khusus lainnya, yang dapat meningkatkan biaya produksi.
- Baja tahan karat: Perbedaan utama antara baja dan baja tahan karat adalah bahwa yang terakhir adalah paduan dengan kromium daripada karbon. Sementara baja standar rentan terhadap karat dan korosi saat terkena kelembaban dan oksigen, kandungan kromium dalam baja tahan karat menciptakan lapisan kromium-oksida pasif pada permukaan logam, mencegah besi di dalamnya teroksidasi lebih lanjut. Ini juga menghambat kemampuan baja untuk menghantarkan listrik. Baja tahan karat dapat dicampur dengan logam lain (termasuk molibdenum, nikel, atau titanium) untuk meningkatkan ketahanan suatu komponen terhadap korosi dan panas.
- Logam lunak: Logam lunak seperti kuningan, perunggu, titanium, dan tembaga menawarkan berbagai karakteristik fisik yang menarik untuk aplikasi tertentu. Namun, logam lunak — terutama yang memiliki kandungan tembaga tinggi — sebenarnya lebih sulit untuk dikerjakan karena keuletan tembaga yang tinggi. Pemesinan logam lunak dapat berkontribusi pada peningkatan panas di lokasi pemotongan, keausan pahat yang lebih besar, dan galling (penumpukan bergetah pada ujung tombak pahat). Titanium, khususnya, juga kurang kaku dibandingkan logam lain dan oleh karena itu memerlukan pegangan yang kuat pada benda kerja untuk memastikan presisi dan akurasi. Semua faktor ini dapat berkontribusi pada biaya pemesinan yang lebih tinggi untuk logam lunak.
Permukaan akhir CNC dan pasca-pemrosesan
Setelah bagian atau komponen dikerjakan, mungkin perlu menjalani satu atau lebih proses finishing. Proses ini dapat digunakan untuk menghilangkan cacat estetika, meningkatkan penampilan produk, memberikan kekuatan dan ketahanan tambahan, menyesuaikan konduktivitas listrik, dan banyak lagi. Proses finishing umum untuk bagian mesin adalah anodizing, powder coating, dan bead blasting. Namun, biasanya juga membiarkan suku cadang dalam keadaan dikerjakan atau sudah digiling saat penyelesaian lainnya tidak diperlukan.
Opsi penyelesaian CNC yang umum
- Anodisasi (aluminium): Anodizing adalah proses elektrokimia di mana paduan aluminium atau titanium direndam dalam bak elektrolitik untuk mengentalkan lapisan oksida alami bagian mesin agar lebih padat, non-konduktif secara elektrik, dan lebih tahan lama. Selesai anodized juga menjanjikan kontrol dimensi yang baik, yang membuatnya paling baik digunakan dalam aplikasi rekayasa kinerja tinggi, terutama untuk rongga internal dan bagian-bagian kecil. Anodisasi menawarkan salah satu hasil akhir yang paling estetis untuk suku cadang mesin CNC, tetapi harganya lebih mahal.
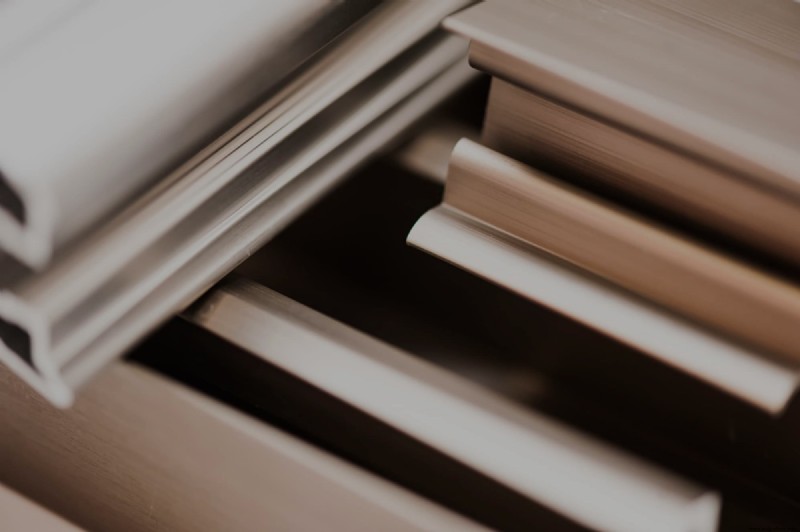
- Bead blasting (logam atau plastik): Peledakan manik menggunakan sistem udara bertekanan untuk menembakkan jutaan manik-manik kaca di bagian tersebut, yang secara efektif menghilangkan bekas dan ketidaksempurnaan alat, dan dapat digunakan untuk membuat permukaan akhir berbutir, matte, atau satin yang konsisten. Peledakan manik tidak menambahkan sifat kimia atau mekanik dan, tidak seperti lapisan bubuk yang menambahkan material ke suatu bagian, ini adalah hasil akhir yang reduktif, yang berarti bahwa proses tersebut menghilangkan material dari bagian tersebut. Ini adalah pertimbangan penting jika bagian Anda memiliki toleransi yang ketat. Peledakan manik adalah salah satu penyelesaian permukaan yang paling terjangkau tetapi harus dilakukan secara manual. Ukuran dan tingkat manik juga akan memengaruhi hasil akhir.
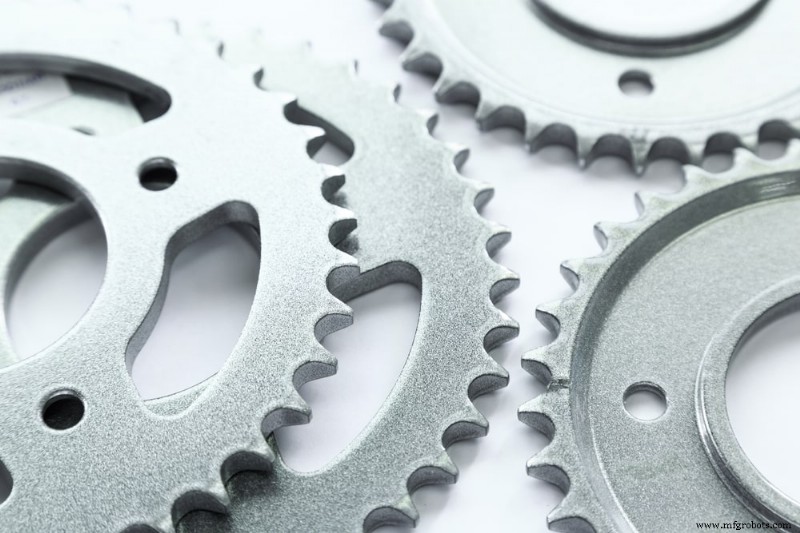
- Oksida hitam (baja, baja tahan karat, tembaga): Proses perawatan elektrokimia atau kimia ini menciptakan oksida besi hitam pada permukaan logam besi. Juga disebut menghitam, mengoksidasi, atau menghitamkan, proses ini tidak hanya menyimpan lapisan oksida hitam pada permukaan logam. Sebaliknya, reaksi kimia antara besi dalam logam dan larutan garam pengoksidasi menciptakan oksida besi yang disebut magnetit, yang memiliki penampilan hitam matte. Proses ini meningkatkan stabilitas dimensi bagian dan penampilan estetika sekaligus mengurangi pantulan cahaya permukaan, yang penting untuk bagian yang digunakan dalam aplikasi yang melibatkan radiasi. Baja pengoksidasi hitam juga dapat membantu mengasah alat seperti ujung obeng dan mata bor.
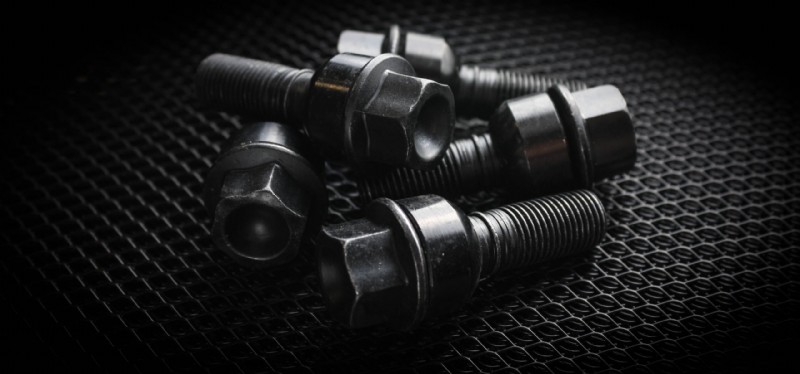
- Pelapis bubuk (semua logam): Powder coating mirip dengan lukisan semprot. Bagian mesin menerima lapisan primer untuk melindunginya dari korosi. Kemudian, bagian tersebut "dicat" dengan lapisan bubuk kering dari pistol semprot elektrostatik dan dikeringkan dalam oven yang dipanaskan hingga setidaknya 200 °C. Beberapa lapisan dapat diterapkan untuk meningkatkan ketebalan lapisan akhir, yang menciptakan lapisan pelindung tipis pada bagian yang kuat, tahan aus, dan estetis. Proses ini dapat dikombinasikan dengan peledakan manik untuk meningkatkan ketahanan korosi bagian dan menciptakan keseragaman yang lebih besar dalam tekstur dan penampilan. Tidak seperti anodizing, lapisan powder-coated kompatibel dengan semua logam, kurang rapuh, dan menawarkan ketahanan benturan yang lebih besar. Namun, powder coating umumnya menghasilkan kontrol dimensi yang lebih sedikit daripada lapisan anodik dan tidak direkomendasikan untuk digunakan pada komponen kecil atau permukaan internal. Titik harga powder coating yang lebih tinggi juga dapat membuat produksi yang lebih besar menjadi mahal.
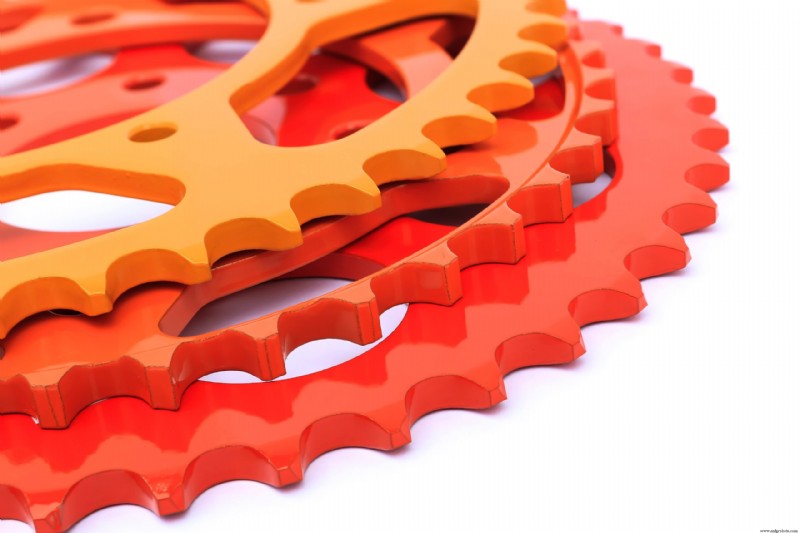
- As-machined (logam atau plastik): Tidak menerapkan proses finishing pada bagian mesin disebut sebagai hasil akhir “as-machined” atau “as-milled”. Bagian tersebut akan memiliki bekas dan noda alat yang kecil namun terlihat. Suku cadang yang dikerjakan dengan mesin memiliki toleransi dimensi yang paling ketat dan sangat terjangkau untuk diproduksi karena pasca-pemrosesan tidak diperlukan. Ini sangat ideal untuk aplikasi di mana integritas dimensi lebih penting daripada estetika. Namun, penting untuk diperhatikan bahwa tanpa lapisan akhir atau pelindung tambahan, kekerasan permukaan seperti yang dikerjakan dengan mesin membuatnya rentan terhadap goresan, lecet, dan goresan.
Memilih bahan dan finishing yang tepat
Memilih bahan dan opsi pasca-pemrosesan untuk bagian Anda sangat bergantung pada bagaimana dan di mana bagian Anda akan digunakan. Pertimbangan penggunaan akhir utama untuk memilih bahan bagian dan permukaan akhir Anda meliputi:
- Faktor lingkungan: Kondisi lingkungan dari aplikasi penggunaan akhir bagian tertentu memainkan peran penting dalam menentukan bahan dan perawatan mana yang ideal. Faktor-faktor seperti panas, dingin, nyala api, radiasi UV, paparan bahan kimia atau autoklaf, dan banyak lagi harus diperhitungkan untuk memastikan kelangsungan hidup bagian tersebut.
- Faktor listrik: Apakah suatu bagian memerlukan sifat konduktif atau isolasi adalah pertimbangan penting lainnya. Mengetahui bagian Anda harus menghantarkan listrik, Anda dapat memilih bahan konduktif seperti tembaga, sedangkan bahan seperti Nylon 66 akan sesuai saat mencari isolator yang baik.
- Faktor mekanis: Bagian yang dimaksudkan untuk menahan beban berat, keausan, atau gaya eksternal lainnya harus dibuat dari bahan yang dapat menahan gaya tersebut. Mengidentifikasi properti yang paling diinginkan atau diperlukan untuk suatu suku cadang — seperti fleksibilitas, ketahanan benturan, kekuatan tarik atau tekan — dapat membantu tim menentukan bahan mana yang paling sesuai.
- Pertimbangan kosmetik: Sementara estetika dapat menjadi prioritas kedua untuk beberapa bagian, ini tidak terjadi pada banyak produk konsumen. Beberapa bagian atau aplikasi mungkin memerlukan bahan dengan pilihan kosmetik tertentu dalam hal warna, transparansi, atau permukaan akhir.
- Toleransi: Beberapa tingkat variasi antar bagian diharapkan dalam pembuatan, dan toleransi dimensi mengacu pada kisaran variasi yang dapat diterima yang harus dimiliki oleh bagian yang layak. Toleransi yang lebih ketat membutuhkan lebih banyak tenaga kerja dan mahal untuk dicapai berulang kali, tetapi mungkin diperlukan berdasarkan cara komponen digunakan.
Merancang untuk permesinan CNC
Merancang bagian berkualitas tinggi yang akan bekerja seperti yang diharapkan hanyalah setengah dari tantangan. Anda juga harus dapat mengerjakan bagian tersebut dengan cara yang efisien dan hemat biaya. Design for manufacturability (DFM) adalah kerangka proses yang membantu mengintegrasikan bagaimana bagian akan dibuat dengan desain bagian. DFM sangat penting untuk manufaktur dan memengaruhi segalanya mulai dari jadwal produksi dan biaya hingga efisiensi operasional dan kualitas suku cadang itu sendiri. Pertimbangan desain yang paling umum untuk pemesinan CNC meliputi:
Kantong dalam:
Fitur seperti kantong dan slot yang dalam atau sempit membutuhkan alat yang lebih lama untuk dikerjakan dengan benar. Namun, alat pemotong yang lebih panjang lebih rentan patah dan seringkali kurang tepat karena getaran pemesinan, atau gesekan. Fitur-fitur yang dalam juga biasanya memerlukan beberapa pemotongan untuk mesin dengan benar, yang meningkatkan waktu pemesinan dan biaya produksi — terutama karena alat yang lebih kecil kemungkinan akan diperlukan untuk menyelesaikan lintasan finishing. Jika slot atau kantong dalam harus dikerjakan, usahakan untuk mengurangi kedalaman fitur sebanyak mungkin atau menambah luas penampang kantong. Kedalaman saku atau slot tidak boleh lebih dari 3x diameter alat terkecil yang dibutuhkan.
Wilayah sempit:
Fitur sempit membatasi ukuran alat pemotong yang layak. Hal ini dapat menjadi tantangan bagi produsen karena alat yang panjang dan berdiameter kecil rentan terhadap gangguan dan kerusakan. Sama seperti fitur dalam, area sempit harus tidak kurang dari 3x diameter pahat terkecil. Meminimalkan kedalaman fitur-fitur ini memungkinkan Anda menggunakan alat pemotong yang lebih pendek dan berdiameter lebih besar, yang membantu mengurangi obrolan mesin.
Sudut dalam yang tajam:
End mill CNC berbentuk lingkaran, yang menyulitkan pengerjaan sudut internal yang tajam karena bit akan meninggalkan radius sudut. Meskipun ada metode pemesinan sudut internal yang tajam, proses ini cenderung mahal. Secara umum, sudut internal yang tajam harus dihindari untuk bagian mesin. Jari-jari sudut internal juga harus lebih besar dari jari-jari alat pemotong yang dimaksud. Dengan merancang jari-jari internal lebih besar dari pahat, mesin dapat menciptakan transisi yang mulus antar dinding. Sebaliknya, radius internal yang berukuran sama dengan pahat pemotong akan memaksa mesin untuk membuat perubahan arah secara tiba-tiba, sehingga menghasilkan hasil akhir yang kurang mulus.
Fitur yang tidak dapat diakses:
Fitur seperti counterbores — yang terbuka di dalam saku lain atau saku dengan draf negatif — dapat menimbulkan tantangan yang signifikan bagi tim produksi. Fitur desain ini membutuhkan lebih banyak waktu untuk pengerjaan karena betapa sulitnya untuk mengizinkan akses pahat potong. Sangat penting untuk memastikan bahwa alat pemotong dapat dengan bebas mengakses semua fitur bagian tanpa terhalang oleh fitur lain.
Fillet luar:
Fillet luar, atau sudut membulat di sepanjang tepi atas kantong, bos, slot, dan fitur lainnya, memerlukan alat pemotong khusus yang didukung oleh pengaturan pemesinan yang presisi — pasangan yang dapat dengan cepat menjadi mahal. Beveling atau chamfering tepi luar dapat membantu menghindari biaya ini.
Ketebalan dinding:
Dinding tipis dapat menimbulkan masalah untuk bagian logam dan plastik dan harus dihindari sedapat mungkin. Dinding logam tipis lebih rentan terhadap gesekan, misalnya, yang berdampak negatif pada keakuratan bagian dan permukaannya. Bagian plastik dengan dinding tipis juga lebih cenderung melengkung atau melunak. Ketebalan dinding minimum untuk komponen logam harus 0,03” (0,762mm) dan 0,06” (1,524mm) untuk komponen plastik.
Lubang dengan dasar datar:
Lubang dengan dasar datar tidak hanya sulit untuk dikerjakan, tetapi juga cenderung menimbulkan kesulitan untuk operasi selanjutnya. Secara umum, tim produk harus menghindari lubang buta dengan dasar datar dan mendukung latihan memutar standar, yang membuat lubang dengan dasar berbentuk kerucut.
Bagian berulir:
Saat mengerjakan ulir internal atau eksternal, ada beberapa pertimbangan desain yang berbeda.
Untuk utas internal:
- Sertakan countersink di akhir utas internal.
- Kurangi jumlah utas jika memungkinkan. Sebagian besar tekanan bagian sebenarnya jatuh pada tiga utas pertama, jadi tingkatkan jumlahnya
- utas menghasilkan hasil yang semakin berkurang.
- Gunakan bentuk dan ukuran standar.
- Pilih benang kasar untuk menghemat biaya.
Untuk utas eksternal:
- Sertakan talang di semua desain sekrup.
- Hindari penghentian di dekat bahu area dengan diameter besar.
- Ulir eksternal yang dibalik harus memiliki alur relief.
- Gunakan utas eksternal yang lebih pendek kecuali bagian tersebut secara khusus membutuhkan kekuatan utas tinggi.
Membor pintu masuk dan keluar:
Jika permukaan benda kerja tidak tegak lurus dengan sumbu bor, ujung bor akan melenceng saat bersentuhan dengan material. Untuk meminimalkan gerinda keluar yang tidak rata dan merampingkan proses penghilangan duri, pastikan fitur lubang memiliki permukaan awal dan akhir yang tegak lurus terhadap sumbu bor.
Daftar periksa untuk mengurangi biaya
1. Buat bagian tetap sederhana
Bagian dengan desain atau proses manufaktur yang kompleks dapat memiliki sejumlah efek hilir. Kompleksitas dapat meningkatkan waktu dan biaya pemesinan, menimbulkan peluang kesalahan, dan mempersulit pengguna akhir untuk memahami penggunaan komponen atau suku cadang secara tepat. Memisahkan karakteristik dan fitur desain mana yang penting untuk kelangsungan bagian dari yang diinginkan namun tidak penting membantu menghilangkan kerumitan yang tidak perlu dari desain bagian dan operasi pemesinan.
2. Desain dengan mempertimbangkan geometri alat dan orientasi penyiapan
Meskipun sebagian besar pekerjaan pemesinan CNC memerlukan lebih dari satu orientasi penyiapan, Anda sebaiknya menjaga jumlah orientasi per bagian seminimal mungkin. Misalnya, jika Anda perlu membalik benda kerja tiga kali agar pahat dapat mengakses semua fitur, ini akan meningkatkan biaya karena setiap penyetelan memerlukan pemasangan ulang bagian tersebut, tanpa mesin untuk menetapkan sumbu yang benar, dan menjalankan program kode-G baru. Mesin 5-sumbu akan lebih mampu dalam aspek ini karena dapat menjangkau lebih banyak fitur tanpa memerlukan banyak penyiapan, meskipun ini bergantung pada geometri bagian tertentu.
Meminimalkan jumlah alat potong yang dibutuhkan adalah cara lain untuk mengurangi biaya. As much as possible, try to keep radii consistent so that fewer tools are needed to machine internal corners. Likewise, avoid very small details where possible. Smaller cutting tools aren’t able to cut as deep into the workpiece and are also more prone to breaking. Typically, the smallest internal features that can be machined are 0.0394” (1mm), though holes can go as small as 0.0197” (0.5mm).
3. Balance your tolerances
Choose your critical dimensions thoughtfully. Not every dimension requires inspection or is critical to the viability of the part, so focus your attention on those that are most essential. Determining how precise specific features need to be will allow you to adjust tolerances accordingly, reduce costs, and streamline the manufacturing process. Make sure that tolerances are still within machineable limits, adhere to given standards, and account for tolerance stacking.
Avoid over-dimensioning your part, as well. Unclear part drawings defeat the purpose of geometric dimensioning and tolerancing, which is to clarify and streamline communication. At Fast Radius, we recommend that you align drawing datums with the CNC coordinate system, as using consistent datum reference frames between machining and measurement systems is more likely to ensure parts are accurately located.
If possible, ensure all datums — points, surfaces, or axes used as references for measurement — reference the same setup. If a datum was machined in a previous setup, it becomes more difficult to hold tight tolerances after a setup change. Finally, be conscious about your datums. Choosing reference datums that are easy to measure from will ease manufacturing.
4. Tailor inspection levels
Similar to balancing your tolerances, strategically applying the right inspection levels can help reduce costs and optimize the production processes. Typical inspection options may include a visual inspection of the part, checking part dimensions using hand tools, or a first article inspection (FAI) where the first manufactured part is checked to ensure all requirements have been met. More in-depth inspections require more time and labor, which increases manufacturing costs.
Increasing the number of parts that you inspect will also increase the cost of production, so it’s important that you select the right sampling plan to ensure confidence across the entire order. At Fast Radius, our default sampling rate is based on ANSI ASQ Z1.4 Level 2.
5. Design to common stock sizes
Designing parts to common stock sizes can help streamline the manufacturing process by minimizing the amount of material that needs to be removed from the workpiece. For example:if it’s acceptable for a part surface to retain its stock finish — that is, if the surface can be rougher than 125 μin Ra — and it does not need to be machined, you have an opportunity to reduce machining time without sacrificing part quality.
This is why knowing the common stock sizes for various materials is important. Metals, for instance, are typically available in a number of stock forms, including sheets, rods, bars, or tubes, which can be purchased according to dimensions like length, width, thickness, and diameter.
Keep in mind that metric sizes are more commonly available in Asia, while imperial sizes are more commonly available in the U.S.
6. Minimize deformation risk
Removing a large amount of material from a workpiece can cause the material to deform. This requires additional processing during machining to prevent deformation, leading to higher costs. Plastics have a higher risk of deformation than metals.
7. Choose your material carefully
The material you pick has a significant impact on the overall cost of your part. For example, metals are generally more expensive than plastics. Avoid over-engineering your parts and consider whether a specific grade or material certificate is required for the part. If a generic material can fulfill the part’s requirements or multiple materials can be accepted, select the less expensive material to keep costs low.
The machinability of the material should also be taken into consideration. Steels, for example, are typically more difficult to machine, which leads to higher costs because steel parts take longer to machine and increase wear-and-tear on cutting tools.
Common applications for CNC machining
Many industries rely on CNC machining processes to produce reliable, accurate parts that meet precise specifications and regulatory requirements, including the aerospace, automotive, medical device, electronics, and commercial parts manufacturing sectors.
Aerospace parts are held to high quality, testing, and regulatory standards in order to ensure proper function, fit, and safety. CNC machining is an excellent fit for creating plastic and metal parts with extremely tight tolerances that satisfy the aerospace manufacturer’s need for an incredible degree of precision and a range of highly specialized parts. The same is true for automotive components.
CNC machining can also be used to create a variety of medical devices, from implants to surgical implements to components for medical electronics.
Care and precision are critical when producing these sorts of devices and tools, as they are held to additional safety standards and requirements. Semiconductors and electronics components also have incredibly stringent precision requirements and tolerance standards, given their size and complexity. As a process, CNC machining has few material limitations, allowing it to be used with conductive materials like silicon. Many commercial parts — from aluminum castings and extrusions to steel and plastic parts — can also be machined.
Another common application for CNC machining is tooling, or the process of creating the various components, tools, machinery, and master patterns that will be used in production. Tooling is an integral part of every manufacturing and molding process and encompasses items like molds, jigs, and fixtures.
Starting your CNC machining project with Fast Radius
At Fast Radius, we make it simple and straightforward to get quality parts through our CNC machining service. To get started, visit os.fastraidus.com, upload your part designs, and you’ll receive instant DFM feedback. The site also allows you to manage designs and orders from a single, intuitive interface.
When you choose Fast Radius, you’re choosing to work with a seasoned group of experts. You’ll receive the full support of our team of engineers, customer success managers, account executives, and others across the business. We’ll also leverage options for domestic and international CNC machining to ensure that your project is carried out as efficiently as possible, without sacrificing quality.
Contact us today to experience the Fast Radius difference or click here to download our comprehensive guide as a PDF.
Siap membuat suku cadang Anda dengan Radius Cepat?
Mulai kutipan Anda