Memajukan komposit termoplastik dan RTM untuk Clean Sky 2 di Spanyol
EURECAT Centro Tecnológico de Catalunya (Pusat Teknologi EURECAT Catalonia, Barcelona, Spanyol) adalah organisasi Litbang swasta nirlaba dengan 11 fasilitas, 650 karyawan, dan pendapatan tahunan 50 juta euro. “Ini adalah pusat R&D terbesar kedua di Spanyol,” jelas Angel Lagraña Hernandez, direktur program untuk pasar aeronautika dan ruang angkasa di EURECAT. Dia menjelaskan bahwa sebagian dari pendapatan EURECAT berasal dari pemerintah Catalan dan sisanya, setengahnya harus berasal dari perusahaan swasta — sebagian besar usaha kecil-menengah (UKM) — sementara separuh lainnya mungkin publik, seperti yang didanai oleh Uni Eropa. Program Langit Bersih 2. “Kami sekarang memiliki 18 proyek Langit Bersih,” catat Lagraña, “yang diberikan kepada kami murni berdasarkan pengajuan kompetitif sebagai tanggapan atas permintaan proposal.”
Contoh bagaimana fitur komposit di berbagai tujuan dan demonstran teknologi yang direncanakan Clean Sky 2 meliputi:
- Demonstrator Pesawat Multifungsi generasi berikutnya — memanfaatkan termoplastik untuk langit yang lebih bersih
- Ekonomi Sirkular:Pesawat Komposit untuk pesawat regional mulai terbentuk
- Memanfaatkan keahlian balap motor untuk FastCan Clean Sky
“EURECAT sangat melintang, bekerja di industri otomotif, kereta api, dan lainnya selain pekerjaannya di ruang angkasa,” kata Lagraña. “Ini juga memiliki banyak aktivitas di bidang TI seperti analisis data dan blockchain, dll. Komposit 4.0 adalah salah satu area strategisnya.” Dalam komposit, ia mencatat bahwa EURECAT terutama bekerja di luar teknologi autoclave (OOA). “Kami fokus pada termoplastik dan cetakan kompresi cair, termasuk pemantauan proses secara real time, termasuk pemantauan suhu transisi kaca (Tg) resin selama pemrosesan.” (Lanjutkan membaca ke bagian COFRARE, di akhir blog ini, untuk mengetahui lebih lanjut tentang pemantauan Tg ini.)
Proyek terkait komposit terbaru EURECAT di Clean Sky 2 meliputi:
- KELBEMAN untuk mendemonstrasikan balok lunas komposit termoplastik (Proyek ini telah menerima dana dari Clean Sky 2 Joint Undertaking di bawah program penelitian dan inovasi Horizon Uni Eropa di bawah GAP n° 785435 KEELBEMAN);
- WINFRAME 4.0 untuk membangun bingkai jendela komposit termoplastik (TPC) untuk demonstran Green Regional Aircraft (GRA) di Clean Sky (2008-2017) dan diperluas ke Regional Aircraft IADP (Innovative Aircraft Demonstrator Platform) di Clean Sky 2 (2014-2024);
(Proyek ini telah menerima dana dari Clean Sky 2 Joint Undertaking di bawah program penelitian dan inovasi Horizon Uni Eropa di bawah GAP n° 821323 WINFRAME 4.0.)
- COFRARE 2020 untuk rangka badan pesawat termoset dibuat menggunakan resin transfer moulding (RTM) dengan ikatan geser TPC.
(Proyek ini telah menerima dana dari Clean Sky 2 Joint Undertaking di bawah program penelitian dan inovasi Horizon Uni Eropa di bawah GAP n° 821261 COFRARE 2020.)
Balok lunas komposit termoplastik
Langit Bersih 2 - JTI-CS2-2017-CFP06-LPA-02-20. Durasi proyek:Maret 2018 hingga Desember 2019
Tujuan dari proyek KEELBEMAN adalah untuk mengembangkan struktur balok lunas berorientasi manufaktur untuk pesawat jenis A320 yang memungkinkan tingkat produksi pesawat yang tinggi tetapi dengan biaya yang terjangkau melalui komposit termoplastik. Selain EURECAT sebagai koordinator proyek, mitra termasuk:
- Airbus (Toulouse, Prancis) sebagai manajer topik
- CETMA (Pusat Penelitian Eropa untuk Desain dan Material Teknologi, Brindisi, Italia)
- Grup Teknik CT (CT Ingenieros, Madrid, Spanyol), sebuah firma dengan banyak kantor global yang memiliki kontrak multi-tahun dengan Airbus untuk pengembangan pesawat seperti penelitian pada badan pesawat, sayap dan bagian belakang melalui kantornya di Hamburg, Jerman; penelitian di bagian belakang (Spanyol); penelitian tentang struktur terkait badan pesawat dan pembangkit listrik (Toulouse, Prancis) dan pengembangan sayap (Bristol, Inggris)
- Sofitec (Sevilla, Spanyol), spesialis di bidang manufaktur dan perakitan aerostruktur dengan keahlian dan kapasitas produksi dalam komposit.
CT Engineering Group menyediakan pemodelan penuh geometri balok lunas melalui kantornya di Toulouse, sementara Sofitec mengembangkan inspeksi pengujian tak rusak (NDT). “Ini sangat menantang dengan struktur kotak tertutup seperti itu,” kata Lagraña.
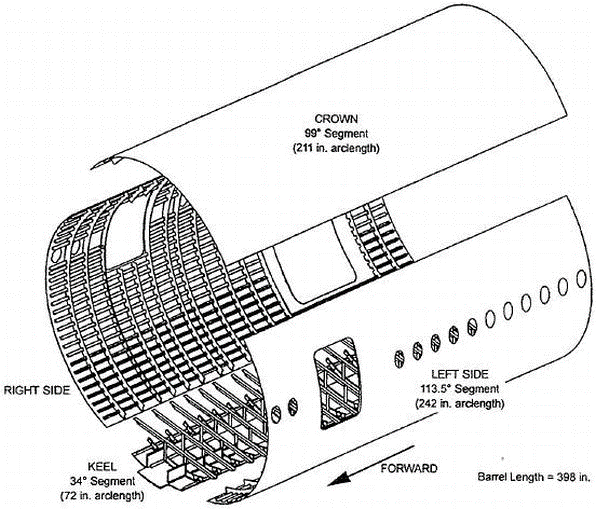
Ditampilkan di sini adalah rakitan balok lunas A320, dibuat dari logam oleh Irkut Corporation (Moskow, Rusia). Irkut dilaporkan dikontrak dengan Airbus pada tahun 2004 untuk memasok komponen termasuk hidung landing gear bay, keel beam dan flap track, yang dipasang rata-rata ke setiap pesawat keluarga A320 ketiga. SUMBER | Irkut
Pengembangan struktur balok lunas
“Saat ini, sebagian besar balok lunas pesawat dibuat dari logam kecuali Airbus
A350, yang merupakan komposit serat karbon monolitik,” kata Lagraña. “Ini membutuhkan sejumlah besar paku keling dan sejumlah besar waktu untuk perakitan.” Dia menjelaskan bahwa balok lunas adalah struktur penting di badan pesawat, “Ada beberapa kasus di mana balok lunas patah saat mendarat, menyebabkan seluruh badan pesawat retak dan pecah.
Menurut artikel 2011 oleh Steve Wilhelm, balok lunas A350 adalah 70% komposit, panjang 54 kaki (16,5 meter), disatukan dengan 10.000 pengencang, berat 1,2 ton dan membentuk tulang punggung pesawat. Wilhelm mencatat bahwa pesawat Boeing 787 yang kompetitif “tidak bergantung pada struktur lunas yang begitu kuat, karena lebih banyak kekuatan lambung berasal dari barel komposit yang diikat bersama dari ujung ke ujung.” Artikel tersebut kemudian mengutip Michel Merluzeau, mitra pengelola konsultan kedirgantaraan G2 Solutions LLC (Kirkland, Wash., AS), yang menggambarkan desain Airbus sebagai "lebih konvensional" dan "kurang berisiko" tetapi menunjukkan balok lunas "penting untuk integritas struktural pesawat itu.”
Airbus sebenarnya memelopori balok lunas komposit untuk A340 pada tahun 2001. Namun seperti dijelaskan di atas, tingginya jumlah paku keling yang diperlukan bekerja melawan penghematan berat yang mungkin dilakukan dengan menggunakan komposit. Jadi, target utama dalam proyek KEELBEMAN adalah meminimalkan pengencang dengan menggunakan komponen komposit termoplastik yang dilas bersama.
balok lunas TPC
“Pengembangan balok lunas komposit termoplastik menggunakan pengelasan untuk perakitan adalah bagian dari pengembangan pesawat masa depan Airbus, yang mencakup program seperti Wing of Tomorrow dan Fuselage of Tomorrow,” kata Lagraña. “Dalam KEELBEMAN, kami telah menghasilkan bagian demonstrasi balok lunas berukuran 250 milimeter kali 500 milimeter kali 1 meter dengan stringer dan menunjukkan kelayakan pengelasan struktur ini dengan otomatisasi sebanyak mungkin.”
Lagraña mencatat bahwa pelat dinding demonstran dan stringer dibuat menggunakan pita searah (UD) serat karbon/polieterketon (PEKK) dalam proses pencetakan kompresi kontinu (CCM) yang dikembangkan oleh CETMA (lihat “Pencetakan kompresi tingkat kedirgantaraan” dan “PEEK vs. PEKK vs. PAEK dan pencetakan kompresi kontinu"). “Ada juga rusuk untuk pengaku melintang yang dibuat menggunakan cetakan kompresi non-isotermal tradisional oleh EURECAT,” tambah Lagraña.
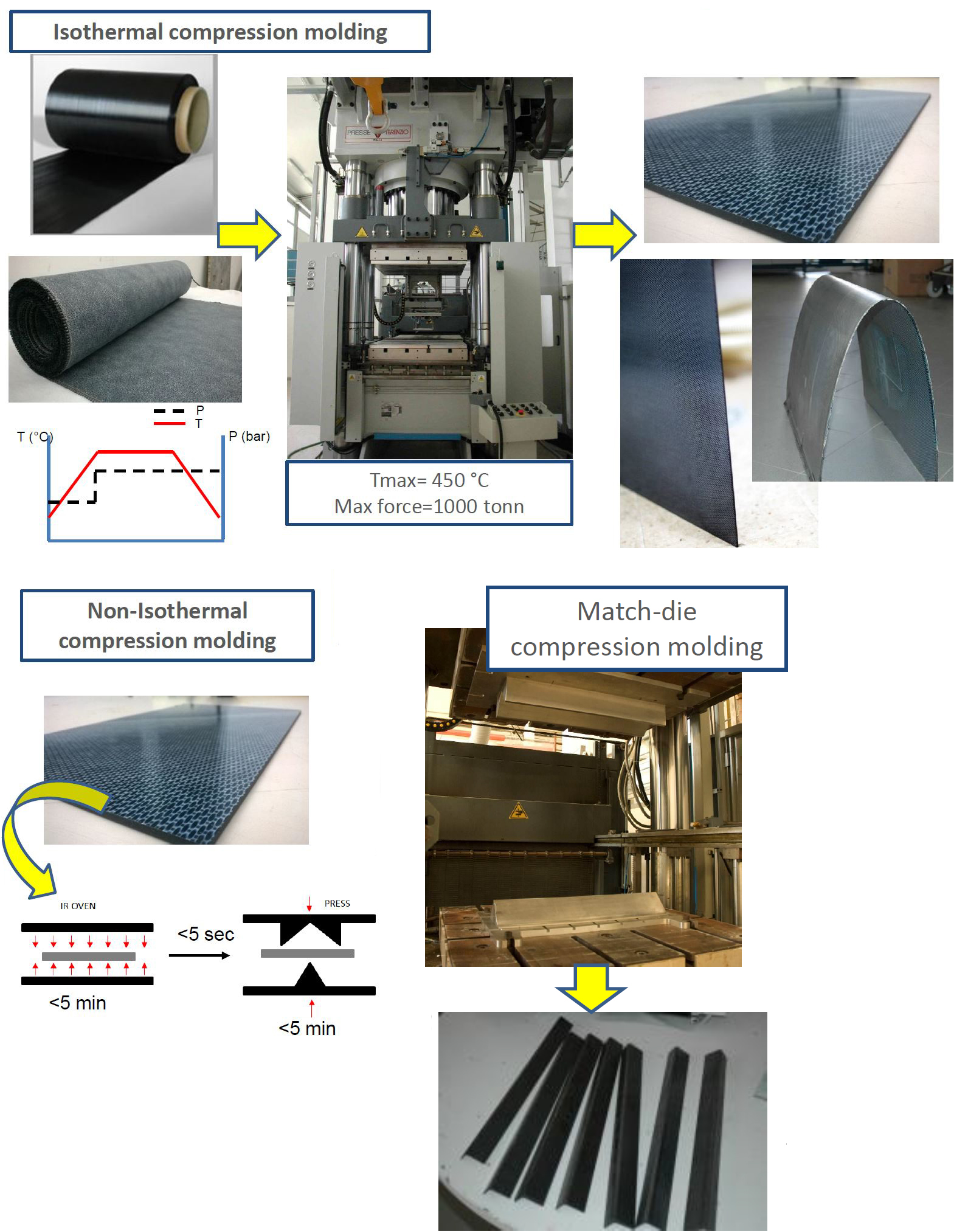
Pengelasan induksi sebagai pengaktif utama
Lagraña mencatat bahwa CETMA memainkan peran kunci tidak hanya dalam produksi suku cadang untuk KEELBEMAN, tetapi juga dalam perakitan demonstran menggunakan mesin dan teknologi las induksi yang dipatenkan. Pengelasan ini awalnya dikembangkan dalam proyek ECO FAIRS program Clean Sky pertama (2011-2014), bersama dengan cetakan kompresi isotermal dan non-isotermal dari struktur TPC yang ditunjukkan di atas. Di ECO FAIRS, CETMA menggunakan semua teknologi ini untuk menghasilkan demonstran prototipe berdasarkan panel atas yang ada (panel kulit yang diperkuat string) dari ekor helikopter Agusta Westland serta demonstran fairing sponsor melengkung. Meskipun ini dibuat menggunakan CETEX (disediakan oleh TenCate, sekarang Toray Advanced Composites) tekstil serat karbon T300 3K 5HS dengan film PPS (polifenilen sulfida) dua sisi, CETMA juga membuktikan pengelasan induksi dengan komposit PEEK dan PEI.
CETMA memilih pengelasan induksi (IW) sebagai teknik pengelasan komposit termoplastik yang paling menjanjikan dan bekerja dengan spesialis teknik pengelasan dan elektronik SINERGO srl (Valdobbiadene, Treviso, Italia) untuk mengembangkan mesin las induksi baru. Mesin SICE 1 WIDE berbasis gantry yang ditawarkan oleh SINERGO (lihat gambar di bawah) mampu mengelas suku cadang berkualitas ruang angkasa secara terus menerus hingga 1 meter kali 1 meter. Ini mencakup sistem kontrol yang kuat untuk memastikan distribusi suhu yang optimal tercapai dalam material yang dilas. Mesin dilengkapi dengan silinder berpendingin untuk menerapkan tekanan konsolidasi dan dengan sistem pendingin udara untuk menghilangkan panas jika diperlukan, seperti di bagian tepi, di mana aliran arus pusaran listrik yang diinduksi dibatasi, menghasilkan kerapatan arus yang tinggi dan panas berlebih. . Dimungkinkan juga untuk memasang kepala las induksi CETMA ke lengan robot 6-sumbu untuk mengelas bentuk geometris yang kompleks.
CETMA juga telah mengembangkan kemampuan untuk mengoptimalkan proses pengelasan induksinya dengan menggunakan alat simulasi, melakukan analisis numerik menggunakan perangkat lunak pemodelan elemen hingga (FEM) COMSOL Multiphysics (COMSOL Inc., Burlington, Mass, U.S.). Ini memverifikasi model ini melalui sejumlah besar tes fisik. CETMA mengkonfirmasi parameter proses yang dioptimalkan dengan uji putaran tunggal pada kupon yang dilas, di mana nilai kekuatan geser sangat mendekati nilai maksimum yang dilaporkan dalam literatur. Khususnya, ini juga jauh lebih tinggi daripada nilai maksimum saat menggunakan perekat struktural, kata CETMA.
CETMA telah membuktikan kemampuan pengelasannya untuk berbagai macam bahan, termasuk anyaman dan serat karbon UD, serta PEEK, PEI, PEKK, PP, PA6, PA12 dan bahkan pengelasan ke CF/epoksi menggunakan hibrida termoplastik PVB (polivinil butiral). lapisan untuk transisi dari substrat termoset ke permukaan termoplastik untuk pengelasan. (Banyak detail bagian ini diambil dari presentasi kompetensi CETMA dan Laporan akhir CORDIS untuk ECO FAIRS.) CETMA mengajukan paten Eropa pada tahun 2014 dan penemu Silvio Pappada dan Andrea Salomi dianugerahi paten EP2801472A1 pada tahun 2016. CETMA telah menerbitkan banyak makalah dan presentasi tentang teknologi ini, termasuk:
- “Simulasi elemen hingga untuk mendukung pengembangan teknologi di luar autoklaf”, A&D, 11-12 Okt 2012
- “Simulasi Elemen Hingga untuk Mendukung Pengelasan Induksi Kontinyu Komposit PPS-Karbon”, SEICO 13, 11-13 Maret 2013 “Paris”
- “Pengembangan Mesin Las Induksi Baru untuk Komposit Termoplastik di Sektor Aerospace”, Konferensi XXII Asosiasi Aeronautika dan Astronautika Italia Napoli, 9-12 September 2013
- “Pengelasan induksi di sektor kedirgantaraan”, TPRC, Konsorsium Eropa Komposit Termoplastik, Rapat web, Desember 2013.
- “Uji skala penuh pada komponen termoplastik untuk sektor kedirgantaraan”, SEICO 14, 10-11 Maret 2014 “Paris”
- “Peralatan las induksi baru untuk sektor kedirgantaraan”, majalah JEC, No. 87, Maret 2014, hlm. 89-91.
Status KEELBEMAN dan jalur ke depan
Airbus mengunjungi CETMA pada bulan Desember untuk melihat pengelasan akhir bagian demonstran 1 meter, dan tim KEELBEMAN juga mengadakan tinjauan akhir tingkat kesiapan teknologi (TRL). “Kami mendapatkan hasil yang baik dan mematangkan teknologi dari TRL 3 ke TRL 4,” kata Lagraña. Langkah selanjutnya dapat mencakup pengembangan lebih lanjut ke TRL 6 dan produksi balok lunas skala penuh untuk dipasang di salah satu demonstran Clean Sky 2, seperti badan pesawat tengah bawah ukuran penuh WP 2.3.2, tetapi ini belum diputuskan.
Proyek WINFRAME 4.0 untuk bingkai jendela TPC
Program komposit termoplastik (TPC) lainnya untuk EURECAT adalah WINFRAME 4.0, dengan tujuan untuk mengembangkan dan memproduksi 24 bingkai jendela untuk demonstrasi darat terintegrasi dengan badan pesawat/kabin pesawat regional (lihat penjelasan tentang pengembangan Clean Sky 2 untuk Pesawat Regional dan Full -Demonstrator Pesawat dan Kabin Penumpang Inovatif di bawah). Mitra WINFRAME 4.0 meliputi:
- Perusahaan kedirgantaraan multinasional Leonardo (Roma, Italia) sebagai manajer topik
- EURECAT
- Sofitec.
“Metode yang kami gunakan dapat menghasilkan satu bingkai jendela setiap 10 menit,” kata Lagraña. Langkah-langkah produksi meliputi:panaskan blanko laminasi TPC dalam oven, terjemahkan ke dalam cetakan, tutup cetakan dengan mesin press, berikan panas dan tekanan selama 10-20 menit dan cetak bagian yang sudah jadi. “Pendekatan ini tidak hanya mencapai siklus yang lebih pendek daripada cetakan cair tetapi juga perkakas yang jauh lebih murah,” tambahnya. “Prosesnya terkenal di industri otomotif, ini adalah pencetakan kompresi dalam konfigurasi yang sangat otomatis yang meningkatkan kualitas suku cadang, tetapi bahan kedirgantaraan yang digunakan berbeda, dalam hal ini PPS yang diperkuat serat karbon dan serat karbon dari Toray Komposit Lanjutan (sebelumnya TenCate). Pada akhir proyek ini, kami akan mencapai TRL 6 untuk teknologi ini,” kata Lagraña.
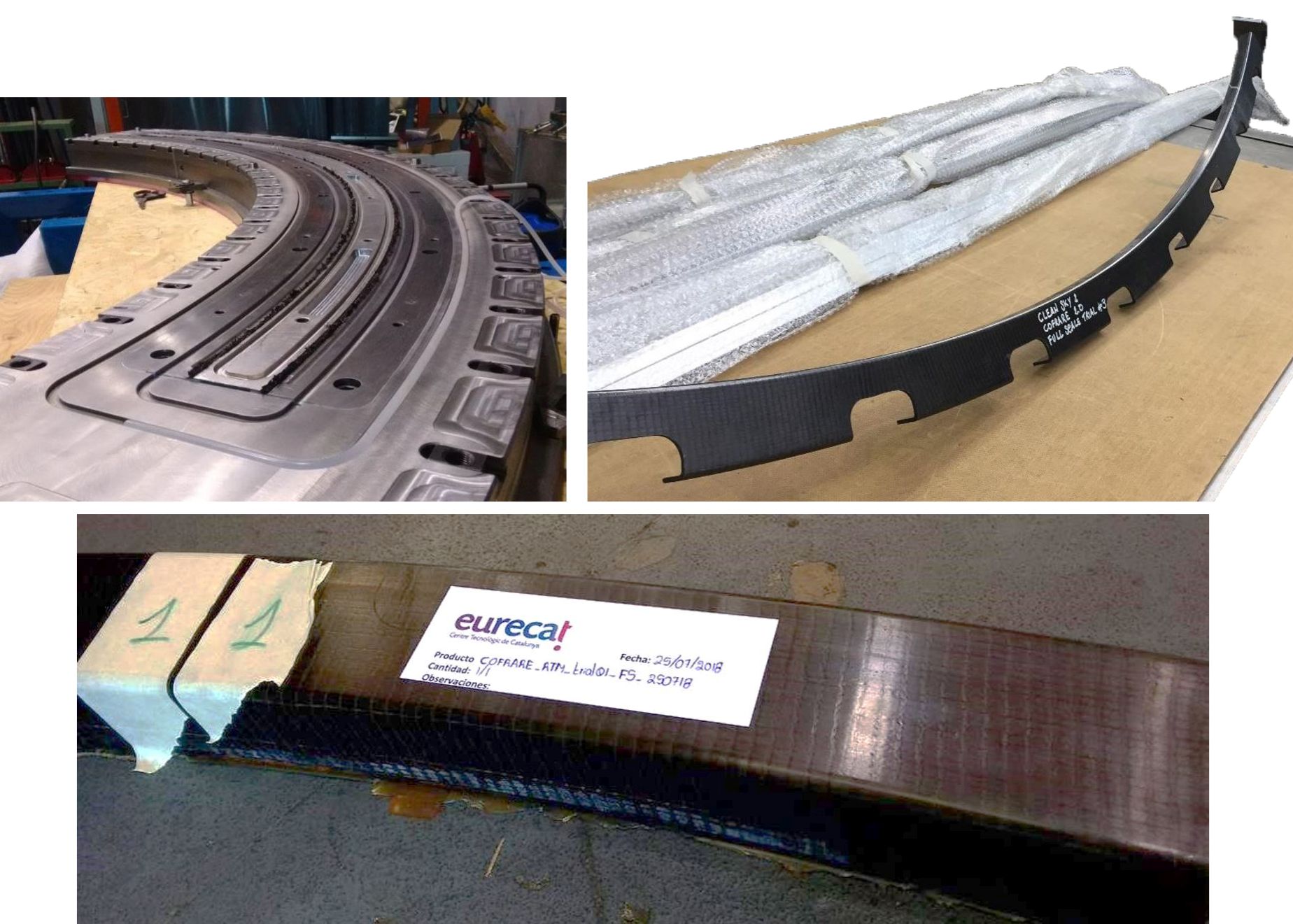
Proyek COFRARE:RTM C-frame dan ikatan geser termoplastik
Proyek COFRARE 2020 merupakan perpanjangan dari proyek awal COFRARE 2.0:
Langit Bersih 2 - JTI-CS2-2015-CFP02-AIR-02-16. “Pengembangan proses untuk pembuatan rangka komposit dengan tingkat produksi tinggi dan biaya rendah”Durasi proyek:2016 hingga 2018.
Tujuan dari proyek Clean Sky 2 COFRARE 2.0 adalah untuk mengembangkan proses manufaktur yang kompetitif dan layak untuk rangka komposit serat karbon untuk digunakan dalam badan pesawat berbasis panel komposit untuk pesawat regional. Mitra termasuk:
- Pemasok kedirgantaraan Tier 1 yang berbasis di Napoli dan perusahaan rekayasa/industrialisasi DEMA (Desain Manufaktur SpA, Somma Vesuviana, Italia)
- EURECAT
- LGAI Technological Center S.A., sebuah divisi dari Applus+ Laboratories di Barcelona, Spanyol menyediakan pengujian.
Tujuan dari proyek COFRARE 2020 generasi berikutnya adalah untuk memproduksi rangka komposit skala penuh dan ikatan geser untuk digunakan dalam demonstrasi darat terintegrasi badan pesawat/kabin Clean Sky 2. Demonstran ini diatur dalam IADP (Platform Demonstrator Pesawat Inovatif) Regional Aircraft 2 Clean Sky 2 dan dirinci dalam Bagian 5.2.2 dari dokumen Program Teknis Bersama Maret 2015:
“Pesawat regional adalah elemen kunci Langit Bersih melalui ITD (Demonstrator Teknologi Terpadu) khusus - Green Regional Aircraft (GRA) , menyediakan landasan penting menuju sistem transportasi udara yang menghormati lingkungan, memastikan mobilitas yang aman dan lancar, dan membangun kepemimpinan industri di Eropa. Di Langit Bersih 2 , … Tujuan demonstrasi IADP Pesawat Regional jauh lebih kompleks, komprehensif, dan menantang dibandingkan dengan Clean Sky saat ini Proyek GRA , yang dipaksa untuk bekerja dalam keterbatasan anggaran dan waktu. …”
Program Teknis Bersama 2015 menguraikan pengembangan Pesawat Regional untuk memasukkan dua tempat uji terbang dan lima demonstran darat terintegrasi yang besar. Yang terakhir termasuk Demonstrator Pesawat dan Kabin Penumpang Inovatif Skala Penuh :“Badan pesawat akan menjadi demonstrasi skala penuh teknologi untuk materi komposit, struktur dan manufaktur bertujuan untuk [mencapai] pengurangan berat dan biaya serta meminimalkan dampak lingkungan melalui desain ramah lingkungan dan optimalisasi konsumsi energi di sepanjang siklus hidup (menuju dampak nol).”
Mitra proyek COFRARE 2020 meliputi:
- Leonardo sebagai pengelola topik
- EURECAT
- DEMA
- Pembuatan komponen dan rakitan pesawat A. Setuju (Nola/Marigliano, Italia).
“Di COFRARE 2020, kami membuat rangka badan pesawat menggunakan RTM (resin transfer moulding), yang akan diintegrasikan ke dalam demonstrator badan pesawat,” jelas Lagraña. “Kami menggunakan teknologi Ziplus dari Shikibo (Osaka, Jepang) yang menghasilkan bentuk awal yang sangat cocok untuk injeksi dengan resin.” Shikibo Ltd. adalah bagian dari Composite Alliance Corp. (Dallas, Texas, A.S.), dan menawarkan berbagai teknologi preforming tekstil.
Salah satu aspek menarik dari program ini adalah penggunaan sensor dari Synthesites (Uccle, Belgia) untuk pemantauan real-time kedatangan resin, suhu, tekanan, Tg dan curing. “Sensor terletak di area tertentu dari bagian komposit dan alat RTM untuk mengoptimalkan strategi injeksi resin,” catat Lagraña. Injeksi dicapai dengan menggunakan sistem yang sangat otomatis yang dipasok oleh ISOJET (Corba, Prancis), yang juga merupakan bagian dari Composite Alliance Corp. Sensor sintesis adalah sensor dielektrik, tetapi tidak seperti kebanyakan analisis dielektrik (DEA), yang didasarkan pada arus bolak-balik (AC) , Synthesites menggunakan arus searah (DC). “Sensor kami bekerja dengan baik dengan bahan resistivitas tinggi seperti resin dan karena kami menerapkan tegangan tunggal, kami tidak perlu menganalisis beberapa frekuensi, namun kami mencapai akurasi tinggi, bahkan pada akhir perawatan,” jelas direktur Synthesites Dr. Nikos Pantelelis.
“Kami bertemu Synthesites pada konferensi SAMPE pada tahun 2011,” kenang Lagraña. “Mereka berbicara tentang sensor untuk memperpendek siklus penyembuhan. Kami sedang menjajaki cara mengotomatiskan bentuk awal untuk rangka badan pesawat dan bahkan menggunakan pemrosesan yang lebih cepat dengan HP-RTM (RTM tekanan tinggi), tetapi Anda masih memiliki waktu proses 3-4 jam. Namun, dengan Synthesites, kami telah memotong siklus penyembuhan hingga 50 persen dengan memantau Tg. Kami sekarang sedang menguji properti. Sensor ini dapat bekerja pada tekanan tinggi tetapi dalam pemrosesan RTM kami, kami hanya menggunakan 8 bar tekanan.”
Sensor dielektrik DC Synthesites, sistem pemantauan aliran resin cair OptiFlow, dan sistem pemantauan curing OptiMold telah didemonstrasikan dalam produksi oleh berbagai produsen bilah angin. Mereka juga digunakan oleh Bombardier Aerospace (Belfast, UK) untuk memproduksi sayap cetakan komposit cair untuk C-Series sekarang Airbus 220. Pusat Dirgantara Jerman (DLR, Stade, Jerman) telah menunjukkan pengurangan siklus penyembuhan hingga 50% dengan keduanya autoclave prepreg dan RTM, sedangkan National Composites Center (NCC, Bristol, UK) telah menunjukkan bahwa bahkan untuk resin yang sangat reaktif, perhitungan Tg real-time yang dibuat dari pengukuran sensor suhu dan resistivitas resin seakurat Tg yang diukur dari panel yang diawetkan menggunakan kalorimetri pemindaian diferensial (DSC).
Menggabungkan bingkai dengan ikatan geser TPC
Bagian penting lain dari COFRARE 2020 adalah metode produksi volume yang lebih tinggi untuk menghasilkan ratusan ikatan geser dan braket yang diperlukan untuk menggabungkan rangka C badan pesawat RTM ke panel badan pesawat komposit. “Kami sedang mengembangkan 255 geometri berbeda untuk braket komposit termoplastik yang diproduksi oleh cetakan kompresi,” kata Lagraña. (Catatan, GKN Fokker memiliki beberapa proyek Clean Sky 2 yang akan memproduksi braket TPC untuk Demonstran Pesawat Multifungsi di IADP Pesawat Penumpang Besar; pekerjaan di COFRARE 2020 ini untuk pesawat regional yang lebih kecil.) Metode dasar ditunjukkan di bawah ini, menggunakan alat baja yang cocok dan alat pres yang dipanaskan. “Biaya alat cetakan kompresi seperti itu hanya 2.000 euro, yang sangat terjangkau dibandingkan dengan perkakas RTM,” tambahnya. “Stamping juga mencapai waktu siklus yang sangat singkat.”
EURECAT diinvestasikan untuk tetap berada di garis depan pengembangan teknologi komposit, kata Lagraña. “Kami percaya bahwa tekanan untuk lingkungan yang bersih akan secara dramatis meningkatkan penggunaan komposit di semua transportasi, dan keterjangkauan dan kinerja akan berjalan bersama. Inilah sebabnya kami fokus pada teknologi otomatis yang tidak ada dalam autoklaf untuk ditawarkan kepada pelanggan kami.”
Nantikan blog saya yang akan datang di proyek Clean Sky 2 STUNNING dan MECATESTERS, yang akan membahas pengembangan braket TPC yang dilas untuk Demonstrator Pesawat Multifungsi dan karakterisasi PAEK penuh untuk proyek ini. Saya juga akan membuat blog di Synthesites secara lebih rinci serta lebih banyak perkembangan CETMA dalam komposit. 2020 akan menjadi tahun yang sangat menarik untuk komposit!