Tur Pabrik:Holland Composites, Lelystad, Belanda
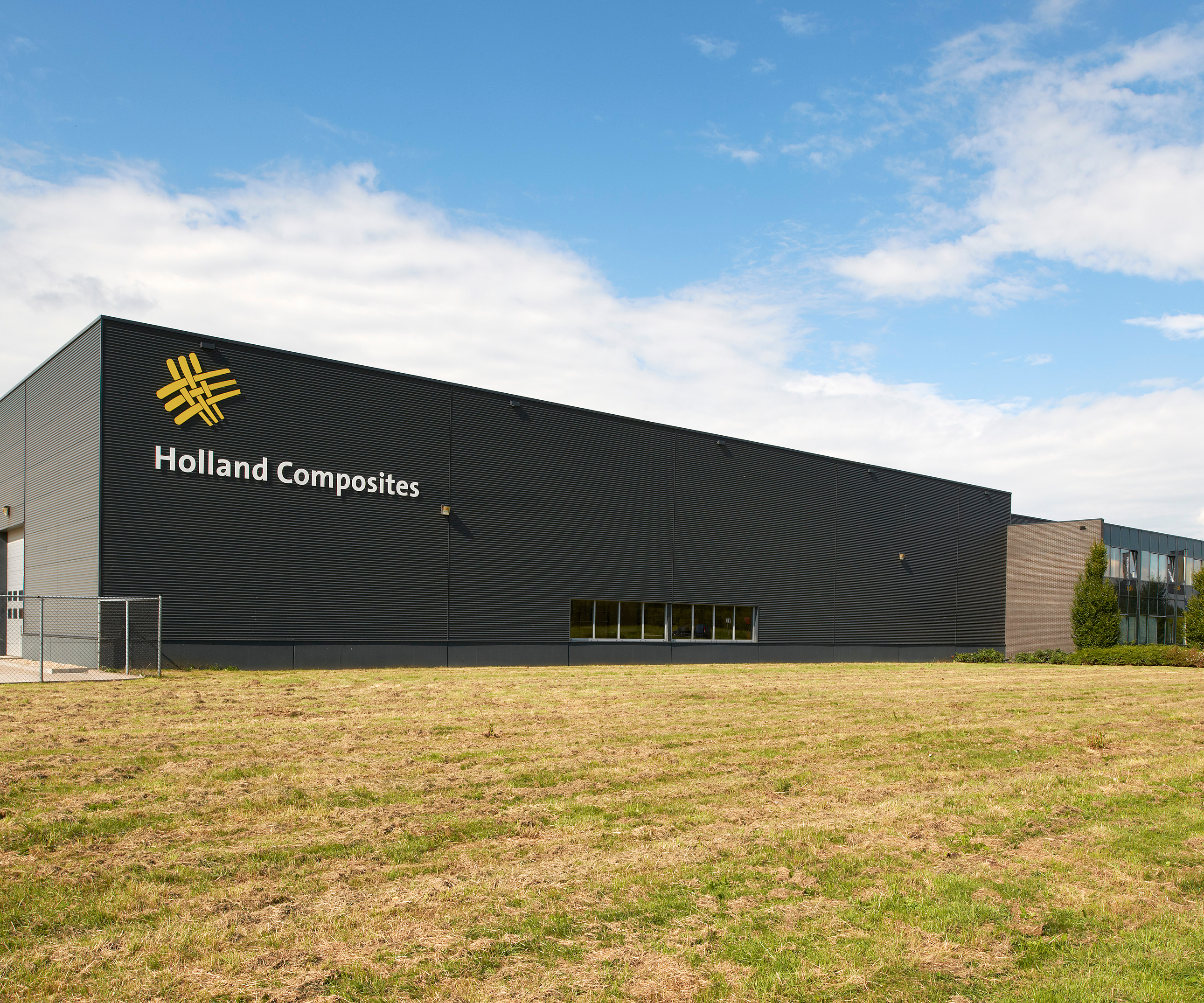
Menggagalkan katamaran, fasad bangunan, dan lainnya. Terletak kurang dari satu jam berkendara dari Amsterdam, Holland Composites mengerjakan berbagai macam proyek yang sangat teknis di 4.500 m
2
fasilitas. Sumber, semua gambar | Komposit Belanda
Terletak di gedung seluas 4.500 meter persegi, kurang dari satu jam perjalanan dari Amsterdam, Holland Composites (Lelystad, Belanda) berfokus pada empat pasar:kelautan/lepas pantai, arsitektur, energi terbarukan, dan proyek khusus. Holland Composites menggunakan campuran prepreg carbon fiber-reinforced polymer (CFRP) dan Nomex honeycomb untuk suku cadang dengan beban tinggi, dan infus resin dan serat kaca untuk industri bangunan dan proyek dengan margin lebih rendah. “Kami masih dapat menghasilkan kinerja tinggi bahkan dengan konstruksi yang lebih hemat biaya ini, dan kami mempertahankan overhead yang rendah untuk suku cadang menggunakan bahan canggih,” kata Sven Erik Janssen, mitra pengelola bersama Holland Composites, bersama dengan pendiri Pieterjan Dwarshui. “Ini unik.”
Perusahaan juga mengoperasikan merek DNA Performance Sailing, memproduksi kapal layar multihull foiling, termasuk katamaran F1X 5,5 meter, trimaran TF10 11 meter, dan katamaran F4 14 meter. Catamaran G4 12 meter tidak lagi diproduksi, "tetapi ini menunjukkan kemampuan kami untuk pembuatan kapal pesiar komposit canggih dan kinerja tinggi," catat Janssen. “Perahu ini adalah pembalap ganda dan penjelajah keluarga dengan tempat berlabuh, dapur dan kepala, namun mencapai kecepatan lebih dari 35 knot. Kemampuan untuk menggagalkan dengan berat lebih dari 4.000 kilogram dan hanya enam orang awak — masih belum ada persaingan di bidang ini selain kapal pesiar America's Cups yang bernilai jutaan dolar.”
Transportasi laut ke darat dan udara
Sebelum tur dimulai, Janssen memberikan sejarah perusahaan dan struktur komposit yang dihasilkannya. Holland Composites dibentuk pada tahun 1992 oleh Janssen dan Dwarshuis, yang pada saat itu adalah mahasiswa di Universitas Teknik di Delft (TU Delft, Belanda). Mereka membangun tiang serat karbon untuk katamaran berlayar Hobie, tender kapal pesiar 18 meter menggunakan CFRP dan sarang lebah Nomex pada tahun 1993, dan kapal pesiar layar 100 kaki menggunakan pemrosesan infus resin pada tahun 1994. “Pada saat itu, semua yang kami bangun terbuat dari serat karbon menggunakan prepreg atau infus,” kenang Janssen. Namun, ia menambahkan, karena bisnis ini tunduk pada pasang surut khas pasar kelautan dan proyek satu kali, “Kami ingin melakukan diversifikasi, tetapi ingin tetap menggunakan komposit canggih versus FRP [artinya serat kaca komoditas yang kurang maju, lebih banyak dan resin poliester].”
Perusahaan mulai menjajaki solusi ringan untuk transportasi jalan raya, memproduksi 35 truk trailer dengan sasis monocoque komposit kaca/serat karbon, yang mengurangi bobot hingga 3.500 kilogram. “Truk-truk itu membawa muatan padat, seperti kentang, dan beratnya akan maksimal sebelum mengisi volumenya,” Janssen menjelaskan. Holland Composites juga membuat trailer berpendingin, ia menambahkan, “Tapi kami terlalu dini; pasar belum siap — perusahaan belum dapat menghitung keuntungan tahunan dari pengangkutan lebih banyak kargo dan penghematan pemeliharaan trailer komposit versus biaya awal yang lebih tinggi.”
Pada waktu yang hampir bersamaan, VRR (Rotterdam, Belanda), pemasok solusi kargo udara khusus, mendekati perusahaan tersebut. “Mereka melakukan pekerjaan untuk Airbus, Boeing, dan maskapai penerbangan,” kenang Janssen. “Kami mengembangkan wadah kelas bulu dengan monocoque komposit serat karbon/aramid, yang masih belum sebanding dengan bobot rendah saat ini,” katanya. Meskipun Holland Composites membuat beberapa ribu ini, pasar dengan cepat menjadi jenuh dengan produk FRP murah.
Struktur yang diawetkan dengan OOA. Struktur komposit karbon besar untuk DNA Performance Sailing merek menggagalkan perahu layar multihull disembuhkan dalam oven fleksibel (kanan) yang terdiri dari panel berinsulasi dengan pemanas dan sirkulasi udara yang dikendalikan komputer dari unit eksterior (inset).
Kelautan tetap menjadi kekuatan inti
Pada tahun 1999, Angkatan Laut Belanda mendekati Holland Composites untuk memproduksi kubah sonar komposit serat kaca padat untuk kapal selam. “Ini secara tradisional dibangun dalam dua bagian yang diikat menjadi satu,” kata Janssen, “tetapi jahitannya menyebabkan gangguan di bidang 'pandangan'. Kami diminta untuk membuat ini utuh. Kubah sonar ini berukuran besar — 11,5 kali 3 kali 3 meter dan tebal 45 hingga 110 milimeter — dan sulit dipasang, terdiri dari 5.000 kilogram resin hibrida vinil ester/epoksi yang dipasok oleh Romar-Voss Composites (Roggel, Belanda). Struktur yang sudah jadi memiliki berat 6.500 kilogram. Mereka harus kaku dan menahan beban bantingan karena mereka terletak di bagian depan lambung. “Kami juga harus mencocokkan kerapatan dan transparansi sonar air,” kata Janssen. “Kami melakukan ini untuk kapal tipe perusak untuk beberapa angkatan laut di seluruh dunia.”
Di ujung lain dari spektrum berat adalah kinerja DNA yang menggagalkan multihulls. “Perahu kecil kami adalah katamaran pertama yang menggagalkan kompetisi,” kata Janssen. Holland Composites juga memproduksi hidrofoil komposit untuk yacht balap yang memecahkan rekor seperti MOD70's Team ARGO dan Beau Geste . “Kami memiliki teknik in-house yang dapat membuat suku cadang dengan muatan yang sangat tinggi tanpa kegagalan, dan metode produksi sekali pakai yang unik untuk foil berperforma sangat tinggi ini,” tambahnya. “Kami bekerja dengan pelaut terbaik di dunia untuk mencapai tingkat kinerja menggagalkan berikutnya dan memproduksi semua foil untuk kapal kelas Olimpiade NACMA17.”
Rumah geladak CFRP ringan yang diproduksi Holland Composites untuk kapal layanan/dukungan ladang angin Windcat Workboats (lihat “Rumah geladak komposit mengurangi bobot”) menggunakan konstruksi sandwich busa CFRP yang diresapi resin untuk kekakuan guna mencapai bentang terbuka yang besar tanpa pilar di dalam kabin. “Rumah geladak monocoque cukup ringan sehingga kami dapat memasangnya di peredam yang baik untuk mengisolasinya dari mesin dan getaran gelombang di lambung kapal,” kata Janssen. “Windcat dikenal karena perjalanannya yang sangat tenang, dan perahunya sangat disukai oleh OEM turbin angin besar. Semua ladang angin ini harus dipertahankan, sehingga ada pasar baru untuk katamaran berkecepatan tinggi sepanjang 50 hingga 60 kaki.”
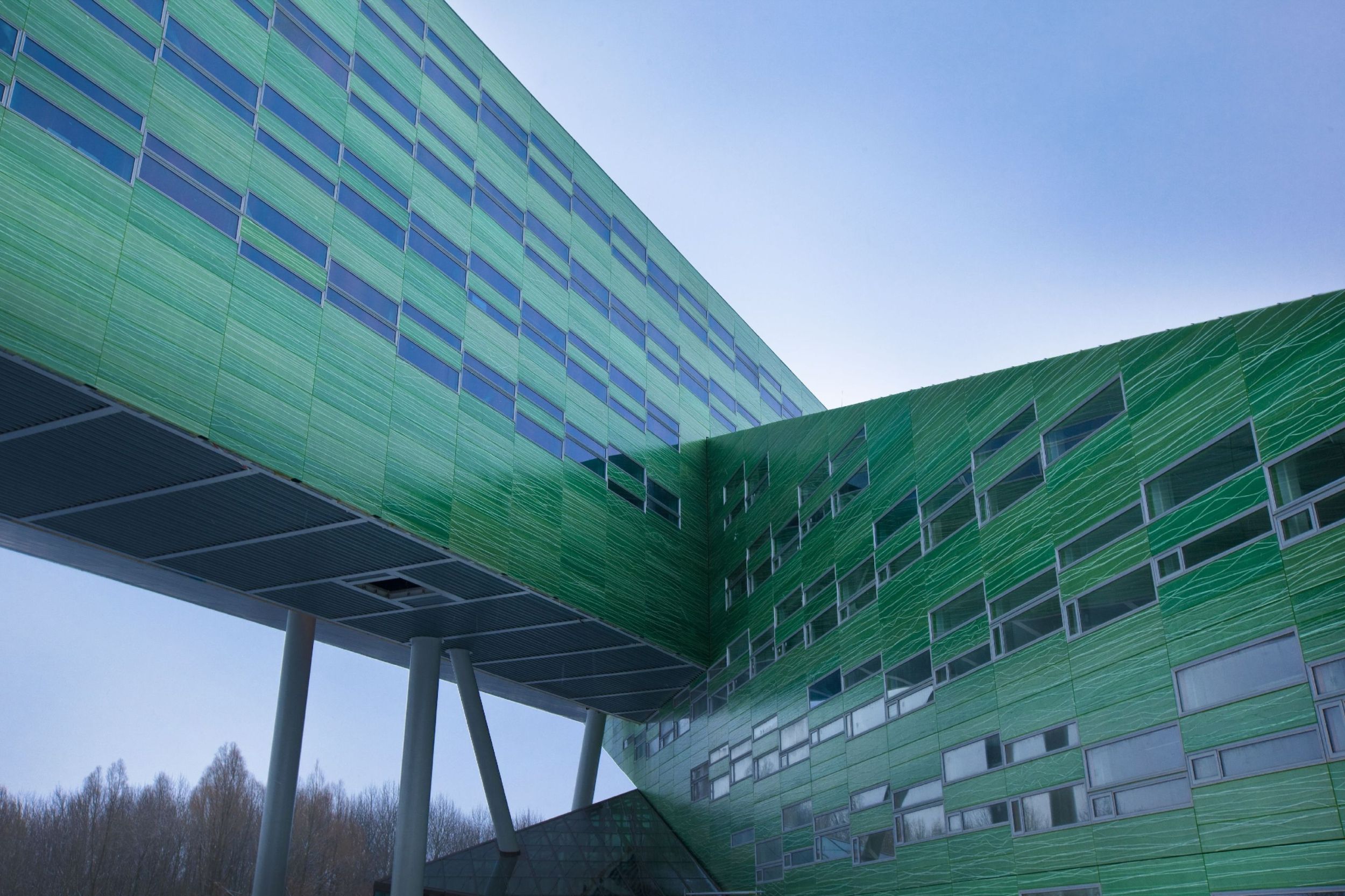
Holland Composites memasok fasad komposit struktural untuk University of Groningen Life Bangunan sains, menggunakan sistem panel RAFICLAD yang tembus cahaya dan ukuran panel yang besar (3,6 kali 3,3 meter), menghasilkan penghematan berat dan insulasi termal maksimum.
Tujuh puluh lima bagian komposit berukuran 40 kali 60 meter dikirim ke Israel, dilaminasi bersama dan diangkat ke tempatnya untuk membuat bagian atap seperti sayap untuk Yitzak Rabin Center di Tel Aviv.
“Semua yang kami lakukan bersifat struktural”
Untuk Yitzak Rabin Center (Tel Aviv, Israel), perusahaan diminta untuk membangun struktur atap seperti sayap yang akan terlalu berat jika terbuat dari beton. “Sekali lagi, kami membuat bagian terbesar mungkin,” kata Janssen. Tujuh puluh lima bagian berukuran 40 kali 60 meter diresapi dengan resin menggunakan serat kaca dan resin vinil ester berbasis epoksi, dan kemudian dikirim ke Israel. Di lokasi, ini diletakkan terbalik menjadi jig untuk dilaminasi bersama menjadi "atap sayap" dengan rentang maksimum 31 meter. Janssen mencatat bahwa proyek ini sangat menantang secara struktural. “Panel ini memiliki ketebalan 200 hingga 300 milimeter dan menyatukan fasad kaca, termasuk bagian kantilever sepanjang 11 meter. Material komposit dapat menahan semua gaya, memberi Anda kemungkinan untuk merancang bentang atap yang dapat digantung bebas.”
Menara Fletcher Hotel adalah proyek serupa lainnya, yang selesai pada 2012-2013. Itu dimulai sebagai pusat perbelanjaan di sebelah jalan raya tetapi membutuhkan redaman akustik yang substansial dalam struktur setelah keputusan dibuat untuk mengubah bangunan menjadi hotel kelas atas. “Kerangka beton tidak dapat menahan banyak beban tambahan, jadi kami dipanggil untuk memberikan solusi yang ringan,” kata Janssen. Holland Composites merancang panel komposit berukuran 8,5 kali 3 meter yang dapat dipasangi fasad kaca pelat. "Kaca benar-benar menggantung ke panel kami, yang membantu menangani beban," dia menunjukkan. “Kami kemudian mengikat panel kami ke kerangka beton. Kombinasi kaca di depan panel sandwich komposit dengan celah udara di antaranya menciptakan penghalang akustik yang sangat besar.” Setiap panel komposit siap dicat untuk dinding interior di satu sisi dan selesai dengan lapisan tahan UV di sisi eksterior yang menghadap kaca.
“Ini juga merupakan cara yang sangat cepat untuk memasang kelongsong ke bangunan berbentuk bulat,” kata Janssen. “Kami memasang fasad lengkap dalam satu langkah dan mencapai nilai R insulasi dari 8, yang merupakan dua kali peringkat bahan eksterior bangunan normal.” Memperluas ide ini, Janssen mengatakan dia percaya netralitas energi sangat penting untuk konstruksi bangunan di masa depan. “Tidak banyak energi yang dibutuhkan untuk memanaskan bangunan yang menggunakan kelongsong komposit struktural kami, jadi pendekatan kami sangat efisien untuk mencapai jejak nol bersih. BREEAM adalah sertifikasi Belanda untuk efisiensi energi, dan dua bangunan pertama yang mencapainya menggunakan komposit kami.”
Untuk Fletcher Hotel, Holland Composites mewujudkan eksterior yang estetis dan mengurangi kebisingan dengan menempelkan panel komposit melengkung ke kerangka beton bangunan, di mana fasad kaca dapat diikat tanpa menambahkan beban mati yang berlebihan.
Janssen memilih Museum seni kontemporer Stedelijk di pusat kota Amsterdam sebagai puncak proyek bangunan teknis Holland Composites (lihat “Museum besar, struktur besar”). “Itu adalah latihan ekstrem dalam mengelola ekspansi termal dan menggambarkan apa yang kami lakukan.” Holland Composites juga telah mempelopori fasad struktural tahan gempa, yang sekarang dibutuhkan di beberapa bagian Belanda, Janssen menjelaskan, karena tanahnya telah tidak stabil akibat rekahan hidrolik (fracking). Gedung Wiebenga di Groningen memiliki fasad tahan gempa yang dapat bergerak 30 sentimeter tanpa kegagalan. “Baja dan beton biasa tidak dapat menangani jenis gerakan ini,” tambahnya.
Meskipun menyeimbangkan banyak sekali persyaratan dengan biaya dan jadwal merupakan tantangan saat membangun struktur, Janssen mencatat masalah terbesar saat ini adalah ketahanan api. “Implementasi komposit yang salah telah membawa nama buruk pada industri komposit dalam hal ini,” jelasnya. “Kami sekarang hanya menggunakan bahan tahan api pada proyek bangunan ini dan menyelesaikan pengujian api sesuai peraturan yang disetujui.”
Holland Composites membuat bilah untuk generator turbin pasang surut menggunakan prepreg serat karbon, yang diolah dalam autoklaf, untuk menangani beban besar yang ditempatkan pada struktur berkecepatan rendah dan torsi tinggi ini.
Energi lepas pantai dan terbarukan
Holland Composites juga memiliki kontrak jangka panjang di industri minyak dan gas lepas pantai. “Komposit di sini tidak hanya menawarkan bobot yang ringan dan ketahanan terhadap korosi, tetapi juga perbaikan yang mudah,” kata Janssen. “Rig dan kapal lepas pantai tidak diperbolehkan downtime. Namun, perbaikan struktur logam membutuhkan pengelasan dan percikan api, sehingga produksi harus dihentikan karena bahaya kebakaran. Kami dapat menambal komposit tanpa gangguan ini.” Perusahaan memiliki klien baru yang meminta produk tersebut untuk berbagai konstruksi lepas pantai.
Ini juga telah memproduksi bilah untuk turbin pasang surut. Pemanenan energi pasang surut masih baru, kata Janssen, tetapi proyek pertama telah selesai dan hasilnya mengesankan. “Turbin pasang surut menawarkan sumber energi yang andal,” jelasnya. “Pasang pasang selalu ada, dibandingkan dengan angin dan matahari, sehingga Anda dapat dengan andal memprediksi output daya, yang merupakan kunci bagi perusahaan listrik.” Holland Composites menggunakan prepreg serat karbon yang diawetkan dengan autoklaf untuk bilah ini karena bebannya sangat besar. “Bilah bergerak pada kecepatan rendah tetapi dengan torsi tinggi,” kata Janssen. “Anda ingin translasi maksimum kecepatan rotor ke motor untuk menghasilkan tenaga, jadi produsen turbin membutuhkan struktur yang kuat namun efisien yang dibentuk untuk mendapatkan energi sebanyak mungkin dari gerakan pasang surut.”
Setiap turbin memiliki dua bilah sepanjang 3 meter dengan tebal 18 milimeter. Ada lima turbin per generator pasang surut. “Beban pada bilah turbin ini digambarkan sama dengan kapal tunda 13.600 tenaga kuda yang melaju dengan kekuatan penuh,” kata Janssen, “tetapi pelanggan juga membutuhkan bilah yang kaku, ringan, dan perawatan rendah dengan ketahanan lelah yang baik untuk daya tahan. Baja akan terlalu berat, membuat generator kurang efisien.” Holland Composites hanya membuat bilahnya; fairings, nose cone dan cladding non-struktural dibuat oleh fabrikator FRP.
Fasilitas berorientasi masa depan
Tur dimulai di area layup, yang memiliki meja layup besar, suku cadang untuk performa perahu layar DNA dan berbagai foil CFRP yang sedang disiapkan untuk pemasangan. Langit-langitnya rendah di sini karena mezzanine untuk penyimpanan material. Ini membuka ke lantai produksi dengan langit-langit tinggi, yang menampilkan mesin pemotong otomatis Zünd (Altstätten, Swiss) tepat di luar area layup. Pemotong memiliki rentang pemotongan 5,7 kali 2,8 kali 0,3 meter untuk memproses bahan prepreg, serat kering, dan busa hingga setebal 25 milimeter.
Pemotong otomatis Zünd di latar depan memasok bala bantuan dan busa potong ke area layup, yang dapat dilihat di belakang, di kanan, dengan mezanin penyimpanan material di atas. Area perkakas tertutup terletak di belakang pintu gulung kuning, terlihat di sini di belakang sisi pusat permesinan CMS, yang berada di sebelah meja potong Zünd.
Berbalik dari pemotong Zünd, kami berjalan ke ruang perkakas tertutup kaca yang berbatasan dengan area layup. Masuk melalui pintu gulung kuning, ada beberapa alat yang sedang diproses dan suku cadang sedang diproses di bawah kantong vakum. “Kami membuat cetakan sendiri,” kata Janssen. “Untuk suku cadang CFRP, kami menggunakan CFRP atau aluminium untuk perkakas, serta lubang ventilasi untuk sirkulasi udara di dalam perkakas, yang membantu memastikan pemeraman merata di seluruh bagian.”
Pusat pemesinan CMS terletak di antara meja potong di sebelah kirinya (tidak terlihat) dan autoklaf (paling kanan, menempel di dinding).
Kembali dari ruang perkakas, kami melewati pusat penggilingan CNC 5-kali-2-kali-1,8 meter 5-sumbu (CMS SpA, Zogno, Italia) dan dapat melihat autoklaf berukuran 6,5 kali-2,2 meter (Tankbouw Rootselaar, Nijkerk, Belanda). “Kami biasanya menyembuhkan pada 125° C dengan tekanan 6 bar,” catat Janssen.
Autoclave juga terlihat di bawah dengan alat CFRP (perhatikan lubang untuk ventilasi udara) dan foil CFRP besar yang diawetkan di bawah kantong vakum untuk kinerja perahu layar multihull.
Dinding di samping autoclave memotong area produksi menjadi dua bagian, membentang sepanjang bangunan di sepanjang ruang perkakas. Kami berbalik dan melewati pintu ke paruh kedua fasilitas Holland Composites, yang berisi mesin pemotong waterjet (jarak pemotongan 8-kali-2-kali-0,5 meter), beberapa oven berukuran hingga 15-kali-10 -kali-3,5 meter, dan stan cat perusahaan berukuran 19x12x3,5 meter. “Saat ini, kami memproduksi panel besar untuk sebuah proyek di Qatar dan serangkaian rumah geladak CFRP untuk kapal Windcat,” kata Janssen.
Rumah geladak CFRP yang diproduksi Holland Composites untuk katamaran Windcat Workboats dicat di bilik cat perusahaan berukuran 19 kali 12 kali 3,5 meter.
Instalasi terbaru Holland Composites adalah printer Massivit 3D (Lod, Israel) 1800 Pro dengan volume build 145 kali 111 kali 180 sentimeter. “Kami adalah mitra yang berinovasi dalam pencetakan cetakan 3D menggunakan tiga kepala cetak, di mana dua mencetak kulit sandwich dan nosel tengah mencetak struktur pengisi atau kisi di antaranya,” Janssen menjelaskan. “Kami akan menggunakan material yang diperkuat serat dalam pengembangan mendatang, tetapi untuk saat ini, kami dapat mencetak perkakas yang akurat dengan kebutuhan penggilingan yang minimal. Kami menggunakan lebih sedikit bahan dan melihat waktu produksi cetakan yang sangat cepat. Kami sekarang memiliki rantai proses yang lengkap, dengan kemampuan untuk beralih dari desain ke cetakan hingga bagian yang dicat dalam waktu singkat.”
Dia mencatat bahwa perusahaan masih menjajaki bagaimana meningkatkan penggunaan otomatisasi untuk lebih memajukan produknya, tetapi tanpa menaikkan biaya. “Itu bermuara pada kecerdikan. Kami tertarik pada masalah yang sangat kompleks yang hanya berani ditangani oleh sedikit orang lain, tetapi sebagai pembuat kapal, kami selalu harus sangat kreatif dengan sumber daya yang terbatas. Untuk apa yang kami lakukan dalam komposit, kami melihat banyak peluang di masa depan.”