PEEK vs. PEKK vs. PAEK dan Continuous Compression Moulding
Ini adalah tindak lanjut dari seri artikel terbaru tentang komposit termoplastik (TPC) yang telah saya tulis (lihat di bawah) ditambah fitur pita termoplastik yang ditulis Jeff Sloan dalam edisi Februari.
- Mengonsolidasikan aerostruktur komposit termoplastik di tempatnya, Bagian 1
- Mengonsolidasikan aerostruktur komposit termoplastik di tempatnya, Bagian 2
- Demonstran komposit termoplastik — peta jalan UE untuk badan pesawat masa depan
- PEEK atau PEKK di aerostruktur TPC masa depan?
TPC telah terbang dengan pesawat sejak tahun 1990-an dan dalam struktur utama sejak 2010 — G650 Gulfstream dilengkapi kemudi dan elevator serat karbon/polifenilen sulfida (PPS) yang diproduksi oleh bisnis Fokker GKN Aerospace (Redditch, UK) menggunakan prepreg Cetex dari TenCate.
Saya pikir terkadang kita lupa berapa banyak pengalaman yang kita miliki dalam teknologi TPC. Di masa lalu, kami telah bertanya “mengapa tidak lebih banyak TPC terbang di pesawat?”. Mungkin sekarang, dengan persiapan Boeing untuk New Mid-market Airplane (NMA) dan kemajuan industri pesawat Eropa melalui Clean Sky 2 dan program pengembangan lainnya, kita akhirnya dapat melihat babak baru aplikasi memasuki layanan.
Sementara itu, ada rantai pasokan yang luas yang sudah terbentuk dengan berbagai perusahaan veteran. Di sini, saya akan menyentuh dasar dengan TenCate (baru-baru ini diakuisisi oleh Toray), Teijin dan Solvay. Masing-masing memiliki pandangan berbeda tentang polimer dan teknologi pemrosesan mana yang menawarkan potensi.
TenCate — veteran TPC terus memajukan teknologi
TenCate mengklaim lebih dari 40 tahun pengalaman dalam mengembangkan komposit termoplastik. Cetexnya merek terkenal untuk laminasi prepreg dan prakonsolidasi (juga disebut organosheet) tetapi juga meluas ke senyawa cetakan massal (BMC) serta searah (UD) dan pita tenunan. Perusahaan ini memiliki rekam jejak yang panjang dengan rangkaian lengkap termoplastik (lihat grafik di bawah), dan sekarang telah menambahkan Low Melt Polyaryletherketone (LM PAEK ). Bahan-bahan ini digunakan dalam aplikasi yang didukung oleh divisi Aerospace dan Industri TenCate, serta lebih banyak produk pasar massal seperti elektronik konsumen dan sepatu atletik melalui divisi Performance Composites perusahaan.

Perekat termoplastik Cetex tersedia dalam berbagai macam polimer matriks yang berkisar dari suhu leleh rendah/kinerja lebih rendah hingga suhu leleh lebih tinggi/kinerja lebih tinggi.
SUMBER:TenCate (atas), Tri-Mack Plastics Mfg. Corp . (bawah)
dengan MENGINTIP, PAEK ditambahkan oleh CW.
Selama wawancara untuk seri saya tentang termoplastik konsolidasi in-situ, PAEK Leleh Rendah muncul sebagai alternatif potensial ke polyetherketoneketone (PEKK) dan polyetheretherketone (PEEK) dalam upaya untuk pemrosesan yang lebih cepat. Ketika saya menanyakan hal ini kepada TenCate, Dr. Hans Luinge, direktur penelitian komposit termoplastik &pengembangan produk untuk TenCate, merangkum perbedaan suhu leleh :
- TC1225 Carbon fiber (CF)/LM PAEK tape 305°C
- Perekat CF/PEKK TC1320 340 °C
- Kaset TC1200 CF/PEEK 350 °C
Perhatikan bahwa suhu aktual yang digunakan saat memproses pita komposit ini mungkin lebih tinggi, tetapi TC1225 LM PAEK masih menarik karena titik lelehnya yang jauh lebih rendah.
“Cetex TC1225 LM PAEK diperkenalkan di TAPAS1 program pengembangan, di mana kami adalah peserta kunci,” kenang Luinge. Ia menggunakan polimer PAEK dari Victrex, dan dia menunjukkan bahwa pada tahun 2013 , bahan TC1225 telah digunakan dalam struktur pesawat demonstrasi . Airbus Nantes memamerkan pesawat panel dengan pengaku terintegrasi di Paris Air Show 2013. Itu dibuat menggunakan pita CF/LM PAEK yang dipasok oleh TenCate, dengan elemen stringer T omega dan butt-jointed yang dibentuk dengan tekanan yang dilas ke kulit, dibuat dengan penempatan serat otomatis (AFP).
“PAEK dengan lelehan rendah bekerja dengan baik di AFP, pembentukan stempel, dan pengelasan,” kata Scott Unger, kepala teknologi global TenCate. Tetapi dengan lebur yang lebih rendah suhu, bukan sifat mekanik untuk LM PAEK lebih rendah dari PEKK dan PEEK? Unger mengatakan tidak, mereka semuanya kira-kira sama . “PEEK, PEKK, dan LM PAEK semuanya merupakan bahan struktural yang baik, dan dari segi biaya, TC1225 diberi harga bersaing dengan TC1200 CF/PEEK dan lebih murah daripada TC1320 PEKK.”
PAEK dengan lelehan rendah mempercepat konsolidasi in-situ
Lebih lanjut, TC1225 LM PAEK menjanjikan konsolidasi in-situ, yang diakui Unger “berpotensi menjadi Cawan Suci. Namun apa yang kami lihat di masa lalu adalah kecepatan AFP Anda harus sangat lambat untuk mencapai konsolidasi in-situ .” Dia menjelaskan, “Anda tidak dapat mencapai konsolidasi in-situ tanpa menggunakan selotip yang menunjukkan tingkat rongga yang jauh lebih rendah daripada yang pada akhirnya dapat diterima di laminasi atau struktur akhir. Ada dua faktor kunci :kualitas pita dan seberapa baik resin matriks dan serat didistribusikan dalam pita UD.” Unger mengklaim proses pembuatan pita UD TenCate telah dirancang untuk menghasilkan tingkat kekosongan yang sangat rendah untuk memungkinkan proses seperti AFP cepat diikuti dengan keluar dari kantong autoklaf/vakum saja (OOA/VBO) konsolidasi serta AFP konsolidasi in-situ satu langkah.
“Kaset kami sangat konsisten dengan 0 hingga 0,5% void maksimum ,” kata Winand Kok, direktur layanan ahli TenCate EU. “Ketebalan pita kami juga sangat konsisten , itulah sebabnya kami dapat mencapai ketebalan lapisan yang sangat akurat dalam laminasi gabungan. Konsistensi ini juga penting untuk proses pengelasan termoplastik dan konsolidasi in-situ.” Unger kembali ke persyaratan kedua yang dia uraikan di atas:“LM PAEK memiliki aliran yang lebih baik dibandingkan PEKK dan PEEK. Itu juga dapat diproses pada kecepatan lebih tinggi dibandingkan PEKK dan PEEK.”
Poin terakhir ini ditunjukkan dalam perbandingan laminasi-ke-laminasi . “Kami membuat TC1320 CF/PEKK laminasi menggunakan mesin AFP laser Coriolis di ThermoPlastic composites Research Center (TPRC) di Twente, Belanda,” kata Unger, “dengan kecepatan cepat dari 600 mm/dtk . Kami kemudian mengkonsolidasikan laminasi ini menggunakan hanya kantong vakum dalam oven.” Dia mengakui ada porositas di antara lapisan karena layup AFP yang cepat, tetapi rongga ini diperbaiki selama langkah konsolidasi kedua, diilustrasikan dalam foto mikrograf laminasi. “Kami juga menempatkan material TC1320 dengan fiber pada 200 mm/s dan menemukan bahwa porositas di antara lapisan itu tidak dihilangkan dengan kecepatan yang lebih lambat. Kami kemudian membuat laminasi yang setara menggunakan mesin AFP yang sama tetapi kali ini menggunakan TC1225 CF/LM PAEK tape tanpa langkah konsolidasi OOA/VBO sekunder — yaitu, konsolidasi in-situ penuh melalui AFP. Kami mencapai properti konsolidasi yang sama seperti pada panel 2 langkah PEKK.”

CF/PAEK yang dibuat dengan konsolidasi AFP in-situ (tidak ada langkah sekunder) menunjukkan sifat konsolidasi yang sama seperti CF/PEKK yang dibuat dengan konsolidasi AFP + cepat dalam oven (atas). SUMBER:TenCate
Unger mencatat kecepatan AFP 200 mm/s untuk konsolidasi in-situ Laminasi CF/PAEK adalah lebih dari dua kali yang diklaim oleh Henri de Vries, ilmuwan senior, komposit, di Structures Technology Dept. di Netherlands Aerospace Center (NLR, Amsterdam), dalam artikel saya, “Consolidating thermoplastic composite aerostructures in place, Part 2”:
“Sekarang, kami melihat seberapa jauh kami dapat mendorong konsolidasi in-situ kecepatan AFP sambil mempertahankan tingkat rongga yang dapat diterima dan sifat mekanik dalam laminasi, ”kata Unger. “Kami telah melakukan banyak pekerjaan untuk memasang panel TPC yang kaku menggunakan proses otomatis. Sekarang tujuannya adalah untuk membangun tingkat kesiapan teknologi .” Kok mengatakan TenCate terus melakukan ini, bekerja sama dengan mitra industri, termasuk pelanggan dan lembaga R&D. Salah satu contohnya adalah pilon mesin dibuat menggunakan TC1320 CF/PEKK pita yang dipajang di stan TenCate di JEC 2018. TenCate bekerja dengan fabrikasi cangkang tiang NLR serta Komponen Termoplastik Belanda (DTC), yang membentuk rusuk tekan yang dilas ke cangkang sebagai elemen pengaku. Meskipun bagian ini dibuat menggunakan AFP dan kemudian dikonsolidasikan dalam autoklaf, Kok mencatat, “Kami juga mengeksplorasi cara lebih lanjut mengoptimalkan kaset untuk konsolidasi 2 langkah hanya dengan menggunakan kantong vakum dalam oven, bukan autoklaf.”

Slit CF/LM PEKK tape, laminasi yang dibuat menggunakan automatic tape laying (ATL) dan rib yang dibentuk dengan press, diproduksi oleh DTC. SUMBER:www.composites.nl
Unger mencatat bahwa produk CF/LM PAEK TenCate yang digunakan dalam pengembangan dan demonstrasi struktur pesawat utama memang menggunakan serat karbon tidak berukuran serta serat karbon dengan ukuran . Dia mengatakan bahwa meskipun lima tahun yang lalu mungkin tidak biasa melihat kaset prepreg LM PAEK, PEKK dan PEEK yang menggunakan serat karbon dengan sizing karena efek buruk pada sifat mekanik yang terkait dengan sizing, yang tentunya tidak lagi terjadi hari ini.
Satu poin terakhir yang menekankan potensi LM PAEK adalah bahwa NIAR dan FAA sedang dalam proses menyelesaikan database publik pertama untuk material komposit termoplastik , menggunakan TC1225 CF/LM PAEK dari TenCate. Basis data akan dirilis awal tahun depan, dan bahan ini dipilih karena sifat mekanik dan kemudahan pemrosesannya.
Teijin — Produser CF lama pindah ke TPC
Produsen serat karbon (CF) Toho Tenax Co. Ltd. (Tokyo, Jepang) sekarang berganti nama secara global menjadi Teijin Carbon, dengan tiga anak perusahaan utama:
- Teijin Karbon Eropa
- Teijin Carbon America
- Teijin Carbon Singapura.
Nama produk tetap Tenax.
“Kami menghabiskan banyak waktu mengembangkan termoplastik 15-20 tahun yang lalu,” kata Jean-Philippe Canart, sebelumnya manajer produk semi-produk termoplastik untuk Toho Tenax Eropa dan sekarang insinyur pasar kedirgantaraan untuk Teijin Carbon America. “Salah satu strategi kami adalah mengembangkan pita termoplastik (UD) searah , yang kami perkenalkan pada tahun 2013 .”
Canart menjelaskan blok bangunan untuk pengembangan ini, “Salah satu teknologi inti kami adalah pengukuran termoplastik untuk CF , yang membantu pemrosesan kaset. Ukuran CF standar harus dihilangkan karena suhu pemrosesan tinggi yang diperlukan untuk termoplastik. Selain ketahanan suhu, ukuran termoplastik juga memberikan kinerja ekstra dengan adhesi serat-ke-matriks pada komposit jadi. Salah satu lini terbesar kami di Eropa memproduksi 1.700 ton/tahun CF yang dilengkapi dengan ukuran TP. Dari sini kami mengembangkan UD tape dengan PEEK, PEKK dan PPS matriks termoplastik untuk digunakan sebagian besar dalam aplikasi luar angkasa tetapi kami juga bekerja pada aplikasi minyak &gas dan industri.”
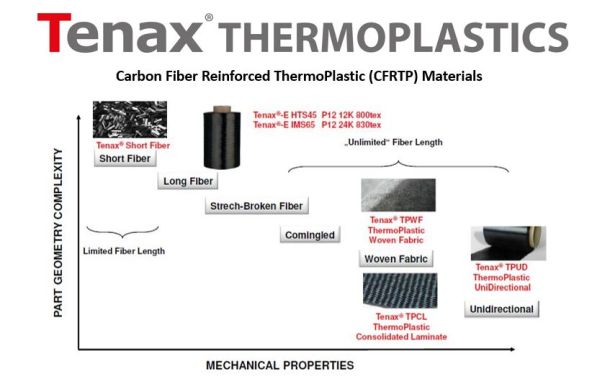
SUMBER:Teijin .
Canart mengatakan bahwa fokus pertama Teijin dengan TPC adalah pada pencetakan (stamping) klip dan braket untuk Airbus A350, menggunakan kain CF yang dilapisi dengan PEEK :“Ini adalah gelombang besar pertama dari aplikasi luar angkasa. Kami melihat ini sekarang bergerak ke bagian yang lebih besar dan lebih struktural yang diproduksi dengan campuran laminasi AFP diikuti oleh konsolidasi melalui stamping.” Canart mengakui bahwa konsolidasi in-situ (ISC) telah dikembangkan selama beberapa dekade, tetapi berpendapat, “kami belum melihatnya sebagai matang. Kami mendukung proyek dan lembaga R&D dalam pengembangan lebih lanjut.” Dia mengatakan ISC adalah mungkin, “tetapi pertanyaannya adalah seberapa cepat Anda dapat membuat suku cadang? Dan seberapa kuat prosesnya?” Dia yakin akan 2025-2030 sebelum suku cadang ISC diproduksi untuk badan pesawat komersial . Sementara itu, Teijin melihat ekspansi di kaset TPC untuk 2-langkah, lini produksi AFP + stamping. “Kami telah berinvestasi di lini pita Eropa kami dan juga mendukung kapasitas proses baru seperti continuous compression moulding (CCM) . Rantai pasokan berkembang.”
Mendukung produksi massal TPC — CCM
Pencetakan Kompresi Berkelanjutan (CCM) adalah proses yang saya tulis pada tahun 2010:“Pencetakan kompresi tingkat kedirgantaraan”. Ini adalah merek dagang sebagai X-CCM oleh Performance Polymer Compositesxperion (Markdorf, Jerman), perusahaan yang awalnya mengembangkan dan mengkomersialkan proses lebih dari dua dekade lalu. X-CCM menawarkan laminasi komposit termoplastik berkualitas tinggi menggunakan proses quasi-continuous yang cepat. “Kami bekerja sama dengan xperion sebagai pemasok material,” kata Canart. “Ini adalah teknologi dewasa , digunakan selama bertahun-tahun oleh Airbus dan Boeing . Sekarang benar-benar berkembang, digunakan untuk memproduksi laminasi konsolidasi berbentuk. CCM bagus untuk biaya, tetapi penampangnya harus tetap konstan.”
Teijin mendukung pertumbuhan TPC tape- proses manufaktur suku cadang berbasis seperti continuous compression moulding (CCM) yang dikomersialkan oleh xperion PPC.
SUMBER:Teijin, SAMPE Seattle 2014.
Menurut Laurens de la Ossa, manajer penjualan senior untuk xperion PPC, “Proses X-CCM kami sekarang lebih maju, mampu menghasilkan bentuk yang lebih kompleks, termasuk profil asimetris seperti profil T dan J .” Dia menambahkan bahwa proses tersebut dapat menghasilkan laminasi TPC terkonsolidasi hingga lebar 24 inci. “Kami adalah bagian dari keseluruhan infrastruktur teknologi yang bergerak menuju produksi massal komposit termoplastik . Kami memiliki proses yang sangat halus untuk komponen TPC yang dikonsolidasi — tidak ada kantong vakum, dan kami dapat menangani laminasi tebal 60 lapisan dan lebih , ketebalan 8-10 mm.”
Suku cadang apa yang ditargetkan oleh X-CCM? “Senar badan pesawat interior, balok lantai dan kerangka lain di sekitar lantai atau langit-langit, komponen struktural dan aplikasi semi-struktural yang menuntut kinerja material tertinggi,” kata de la Ossa. “Pada tahun 2025 , ketika platform pesawat baru mulai memasuki produksi, kami akan mencapai 6-10 kali volume material setiap tahun hanya untuk memberikan apa yang telah kami tanggapi dengan kutipan hingga saat ini.”
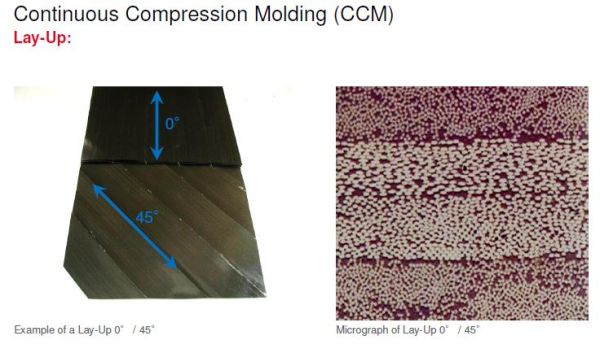
SUMBER:Teijin , SAMPE Seattle 2014
Sebagai bagian dari dorongan berkelanjutan menuju produksi volume yang lebih tinggi, Teijin berfokus pada mengurangi biaya bahan pita dan meningkatkan kapasitas , kata Canart. Bagaimana dengan permintaan industri untuk pita yang lebih tebal ? Secara khusus, de Vries di NLR mengatakan:
“Kami telah mengembangkan tape dengan berat serat areal mulai dari 145 hingga 200 g/m
2
, "jawab Canart. “Dengan produk ini, ketebalan .18mm sudah cukup standar untuk kita. Kami telah memodifikasi garis kami untuk ketebalan ini dan juga hingga 0,20 mm, jadi saya pikir 0,25 mm bahkan tidak akan menjadi lompatan besar.”
Dan bagaimana dengan kualitas kaset ? “Kami pikir semua pita perlu dimodifikasi untuk suku cadang berkualitas lebih tinggi dengan kecepatan lebih cepat,” kata Canart. “Kandungan resin mungkin tidak sesuai dengan apa yang dibutuhkan konsolidasi in-situ dan distribusi resin di dalam pita mungkin perlu dioptimalkan juga. Waktu dan kecepatan peleburan sangat berbeda untuk resin dan proses yang berbeda. Kami mendukung pengembangan lebih lanjut di berbagai bidang, termasuk sistem polimer dan arsitektur pita , termasuk permukaannya.”
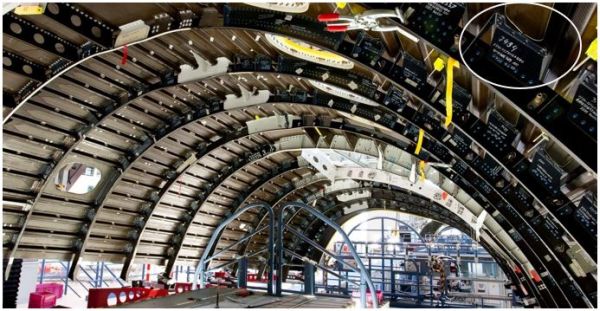
Badan pesawat Airbus A350 klip terbuat dari laminasi termoplastik TenCate Cetex C/PPS menggunakan Tenax ThermoPlastic Woven Fabric (TPWF). SUMBER:Teijin, Grup Aerotec Premium.
Solvay — pasar untuk PEEK dan PEKK
Produk termoplastik berkinerja tinggi Solvay untuk komposit termasuk Ketaspire PEEK , Novaspire PEKK , Radel Polifenilsulfon (PPSU ), dan Ryton Polyphenylene sulfide (PPS ). Dalam pernyataan yang disampaikan oleh Solvay, perusahaan menegaskan bahwa polimer ini diproduksi pada skala industri yang akan memungkinkan pertimbangan untuk aplikasi komposit kedirgantaraan volume besar dan dapat digunakan untuk menghasilkan prepreg berkualitas tinggi .
Solvay saat ini menyediakan unitape APC prepreg dengan polimer PEEK dan PEKK, dengan harga terutama dibedakan dengan biaya serat selected yang dipilih bukan polimer ketika diproduksi dan digunakan pada volume tinggi. Oleh karena itu, diyakini bahwa pemilihan matriks termoplastik yang akan digunakan untuk aplikasi tertentu akan didorong oleh preferensi pelanggan . Faktor-faktor yang mempengaruhi pilihan itu termasuk kinerja suhu, kinerja mekanik, pemrosesan bagian fabrikasi, ketersediaan basis data material dan pengalaman tenaga kerja, untuk beberapa nama. Pandangan Solvay adalah bahwa baik PEKK maupun PEEK melayani kebutuhan di pasar dan mampu menawarkan prepreg yang diperkuat serat berkualitas tinggi dengan harga yang sebanding, terlepas dari polimer mana yang dipilih.
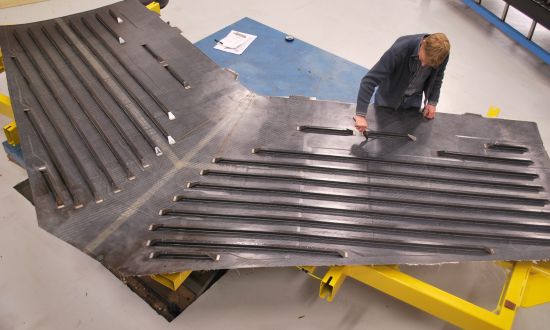
Ekor horizontal pesawat demonstran yang diproduksi oleh GKN Fokker menggunakan
Solvay APC(PEKK-FC)/AS4D. SUMBER:GKN Fokker.
Jadi untuk termoplastik, seperti pada semua komposit lainnya, pilihan bahan dan proses tidak terbatas. Bahkan, mereka tampaknya berkembang. Yang akan mendapatkan kekuasaan dalam produksi pesawat masa depan? Itu masih harus dilihat. CW akan terus mengawasi dan melaporkan apa yang kita lihat.