Sistem Otomasi, Kontrol, dan Pengukuran Pabrik Coke Oven
Sistem Otomatisasi, Kontrol, dan Pengukuran Pabrik Coke Oven
Kokas metalurgi digunakan dalam proses industri besi dan baja (terutama dalam tanur tinggi) untuk mereduksi bijih besi menjadi besi dan dalam pengecoran. Lebih dari 90% dari total produksi kokas didedikasikan untuk operasi tanur sembur. Kokas pengecoran terdiri dari sebagian besar keseimbangan dan digunakan oleh pengecoran di tungku untuk melelehkan logam untuk pengecoran. Produksi kokas pengecoran menggunakan campuran batu bara kokas yang berbeda, waktu kokas yang lebih lama, dan suhu kokas yang lebih rendah dibandingkan dengan yang digunakan untuk kokas metalurgi.
Coke menyebabkan hingga 50% dari biaya selama produksi logam panas. Dengan demikian, produksi kokas berkualitas tinggi yang hemat biaya sangat penting untuk kemampuan kompetitif produksi besi. Mayoritas kokas diproduksi di dunia menggunakan produk sampingan baterai oven kokas dan sebagian besar pabrik oven kokas terintegrasi dengan fasilitas produksi besi dan baja. Di bawah kondisi persaingan yang tajam saat ini dan basis batubara yang berfluktuasi, penurunan biaya produksi kokas merupakan salah satu tantangan terpenting yang dihadapi oleh industri besi dan baja.
Proses dasar produksi kokas di pabrik coke oven (COP) cukup kompleks. Distilasi termal berlangsung dalam kelompok oven yang disebut baterai. Baterai terdiri dari sejumlah oven yang berdekatan dengan dinding samping yang sama yang terbuat dari silika berkualitas tinggi dan jenis batu bata tahan api lainnya. Dinding yang memisahkan oven yang berdekatan, serta setiap dinding ujung, terdiri dari serangkaian cerobong pemanas. Setiap saat, setengah dari cerobong asap di dinding tertentu adalah gas yang terbakar sementara separuh lainnya membawa limbah panas dari cerobong pembakaran ke penukar panas 'batu bata pemeriksa' dan kemudian ke tumpukan pembakaran. Setiap 20 menit hingga 30 menit baterai 'mundur', dan cerobong buang panas menjadi cerobong pembakaran sedangkan cerobong asap pembakaran menjadi cerobong panas buang. Proses ini memberikan pemanasan massa batubara yang lebih seragam.Otomasi, kontrol
Pengoperasian setiap oven adalah siklus, tetapi baterai berisi cukup banyak oven untuk menghasilkan aliran gas oven kokas mentah yang pada dasarnya terus menerus. Oven individu diisi dan dikosongkan pada interval waktu yang kira-kira sama selama siklus kokas. Kokas berlangsung secara normal selama 15 jam hingga 18 jam untuk menghasilkan kokas tanur tinggi. Selama periode ini, bahan volatil batubara tersuling sebagai gas oven kokas. Waktu kokas ditentukan oleh campuran batubara, kadar air batubara, kecepatan pembakaran, dan sifat kokas yang diinginkan. Ketika permintaan coke rendah, waktu coking dapat ditingkatkan menjadi 24 jam. Temperatur kokas biasanya berkisar antara 900 derajat hingga 1.100 derajat C dan dijaga pada kisaran yang lebih tinggi untuk menghasilkan kokas tanur tinggi. Udara dicegah agar tidak bocor ke dalam oven dengan mempertahankan tekanan balik positif di saluran pengumpul gas. Oven dipertahankan di bawah tekanan positif sekitar 10 mm kolom air dalam baterai dengan mempertahankan tekanan utama hidraulik yang tinggi. Gas dan hidrokarbon yang berkembang selama distilasi termal dikeluarkan melalui sistem pengambilan dan dikirim ke pabrik produk sampingan untuk pemulihan.
Coking selesai ketika suhu pusat dalam oven sekitar 950 derajat C sampai 1.000 derajat C. Pada titik ini oven diisolasi dari listrik hidrolik dan setelah ventilasi yang tepat dari gas sisa, pintu dibuka untuk mendorong coke. Pada akhir periode kokas, massa kokas memiliki penyusutan volume tinggi yang menyebabkan terlepasnya massa dari dinding sehingga memudahkan mendorong.
Karakteristik penting dari produksi kokas adalah (i) proses kokas adalah proses batch dan pengoperasian setiap oven kokas harus didasarkan pada perencanaan operasional yang terintegrasi, (ii) proses kokas membutuhkan waktu minimum yang cukup besar dan oleh karena itu pabrik oven kokas memiliki inersia yang tinggi, (iii) proses kokas memiliki aliran yang terarah dan bergantung pada suhu dan waktu, (iv) ada banyak variabel yang tersedia yang mengganggu proses kokas, (v) proses kokas tidak linier dengan angka parameter yang mempengaruhi proses, dan (vi) proses kokas berlangsung di ruang tertutup dengan pemanasan tidak langsung melalui dinding pemanas membuat pengukuran suhu menjadi sangat kompleks.
COP merupakan unit yang penting karena menghasilkan kokas untuk reduksi bijih besi dalam tanur tinggi. Juga memproduksi gas coke oven yang digunakan sebagai bahan bakar gas di berbagai unit pabrik baja terintegrasi. Kualitas dan output produk COP penting karena memberikan stabilitas pada operasi pabrik besi dan baja. COP lebih lanjut sangat intensif energi dan ada beberapa masalah lingkungan yang terkait dengan pabrik. COP perlu dilengkapi dengan otomatisasi, kontrol proses, dan sistem pengukuran untuk mencapai efisiensi yang optimal. Desain modular dari sistem otomatisasi, kontrol, dan pengukuran memberikan fleksibilitas untuk memenuhi persyaratan khusus yang dibutuhkan oleh COP tertentu. Mengotomatiskan urutan proses juga memfasilitasi penyesuaian panjang yang diperlukan untuk memenuhi persyaratan perlindungan lingkungan.
Sistem otomatisasi, kontrol, dan pengukuran adalah alat modern yang ramah pengguna yang membantu meningkatkan produktivitas dan stabilitas COP. Ini membantu dalam meningkatkan kinerja COP dengan memenuhi kebutuhan pabrik. Ini menstabilkan produksi oven kokas, membantu dalam mencapai hasil yang diharapkan dan memiliki nilai praktis yang sangat besar. Manfaatnya termasuk konsumsi energi yang lebih rendah melalui pengurangan konsumsi bahan bakar gas, menstabilkan kondisi dan pengoperasian baterai oven kokas, menghasilkan kualitas kokas yang konsisten, mengurangi emisi lingkungan, meningkatkan masa pakai baterai, dan menghasilkan kemudahan dalam pelaporan dan analisis data operasional dan pemeliharaan.
Sistem otomatisasi, kontrol, dan pengukuran terstruktur dalam level klasik, dari Level 0 (Level bidang) hingga Level 3 (Level manajemen). Desain otomatisasi COP biasanya dibagi menjadi enam lapisan peralatan dasar. Gambar 1 menunjukkan hierarki sistem otomasi pabrik oven kokas.
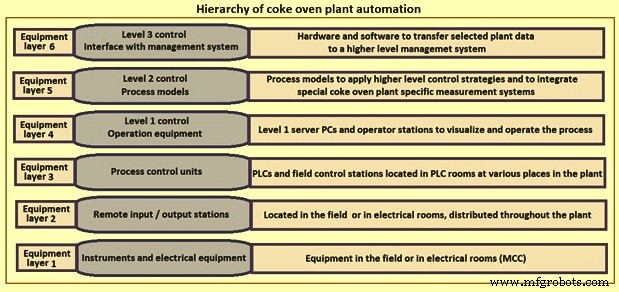
Gbr 1 Hirarki otomatisasi pabrik oven kokas
Peralatan listrik, elemen kontrol dan instrumentasi biasanya terhubung ke unit I/O (input/output) jarak jauh redundan yang dilakukan dengan antarmuka standar 4-20 mA dan 24 DC. Subsistem cerdas biasanya digabungkan dengan Profibus atau Modbus. Semua peralatan otomatisasi terhubung melalui jaringan pabrik serat optik yang berjalan melalui semua lokasi pabrik di mana peralatan yang relevan ditempatkan. Semua data dikumpulkan dan didistribusikan melalui jaringan ini, di mana sumber data dan target data dapat saling terhubung secara fleksibel menggunakan koneksi fisik dengan panel patch dan sakelar serta koneksi logis menggunakan sistem manajemen jaringan. Melalui jaringan ini semua sistem dapat berkomunikasi satu sama lain.
Peralatan instrumentasi dan kontrol modern yang terhubung ke 'pengontrol logika yang dapat diprogram' (PLC) atau 'sistem kontrol terdistribusi' (DCS) (Level 1) dengan stasiun operasi adalah fasilitas standar di COP saat ini. Beberapa COP memiliki otomatisasi tambahan untuk kontrol lanjutan dan fungsi pengoptimalan. Otomatisasi pabrik produk sampingan (BPP) biasanya dilakukan oleh DCS lain yang mengkhususkan diri pada fungsi kontrol berkelanjutan. Kedua sistem biasanya digabungkan satu sama lain melalui Modbus dan dirancang sebagai sistem kontrol terintegrasi untuk mencapai kontrol untuk peralatan listrik dan instrumentasi.
Sistem otomatisasi, kontrol, dan pengukuran memungkinkan pengoperasian COP melalui stasiun kontrol operator, yang terletak di ruang kontrol terpisah. Selain memiliki stasiun kontrol operator untuk semua unit pabrik utama, biasanya ada sejumlah ruang kontrol yang dilengkapi dengan layar video ukuran besar, termasuk kapasitas layar terpisah, sistem paging audio, dan akses intranet, dll. Konfigurasi jaringan dan sistem yang lengkap ' untuk COP dan BPP mencakup level I/O (input/output) jarak jauh COP, level COP-PLC, level operasi COP, dan level administrasi sistem dengan peralatan server dan jaringan. Juga, ada antarmuka ke sistem Level 3. .
Di bidang COP, DCS terintegrasi digunakan pada tingkat kontrol proses. Banyak aplikasi di COP adalah fungsi kontrol urutan, yang paling baik dijalankan oleh PLC. Otomatisasi dan kontrol proses untuk pemanas dan mesin baterai oven kokas dicapai dengan menggunakan sistem kontrol level 2 yang melakukan berbagai perhitungan model proses berdasarkan data yang diproses yang dikumpulkan dari sistem otomatisasi level 1. Sistem kontrol level-2 memberi operator oven kokas alat pendukung yang canggih, akurat, dan mudah digunakan, yang dapat berhasil digunakan untuk meningkatkan kinerja operasional dan lingkungan pabrik. Gambar 2 menunjukkan otomatisasi Level 2 dan sistem kontrol proses untuk COP.
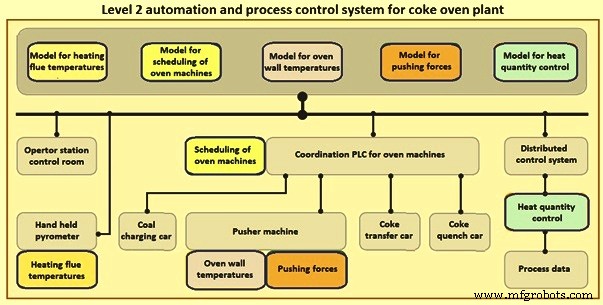
Gambar 2 otomatisasi Level 2 dan sistem kontrol proses untuk pabrik oven kokas
Teknologi kontrol proses yang umum digunakan untuk otomatisasi, kontrol, dan sistem pengukuran COP dijelaskan di bawah ini.
Sistem pengaturan tekanan oven
Pada titik waktu tertentu, tekanan di dalam oven individu berbeda karena mereka berada pada tahap periode kokas yang berbeda. Ini adalah fakta yang diketahui bahwa oven yang baru diisi dayanya mengalami tekanan tertinggi sementara oven yang mendekati waktu pemanggangannya mengalami tekanan terendah. Ini memiliki dua efek yaitu (i) oven pada tekanan yang lebih tinggi dibandingkan dengan pengumpul gas utama lebih rentan untuk memiliki emisi fugitive, dan (ii) oven yang berdekatan yang beroperasi pada tekanan yang berbeda memiliki tingkat tegangan yang berbeda pada dinding ruang oven sehingga, mengurangi kehidupan refraktori secara signifikan. Untuk mengatasi masalah serius ini, penting untuk mengatur tekanan di masing-masing oven untuk mempertahankan tekanan yang sedikit negatif selama periode kokas. Ini dapat dengan mudah dicapai dengan memasang sistem pengaturan tekanan oven.
Pada tahun 1990-an, versi pertama dari sistem pengaturan tekanan oven tunggal dikembangkan oleh perusahaan DMT (Deutsche Montan Technologie GmbH) di Jerman. Sejak itu sistem telah diperbaiki terus menerus berdasarkan pengalaman praktis. Sistem pengaturan tekanan oven yang ditingkatkan membantu mengurangi emisi buronan di COP. Sistem pengaturan tekanan oven telah diterima sebagai 'teknik terbaik yang tersedia' (BAT).
Peningkatan teknologi yang paling penting karena sistem pengaturan tekanan oven adalah (i) tekanan oven dipisahkan dari tekanan utama pengumpul, (ii) pipa pengumpul beroperasi dengan tekanan negatif, (iii) tekanan di dalam setiap oven dikontrol secara individual, (iv) pengisian gas disedot oleh tekanan utama pengumpul negatif, dan (v) katup konvensional diganti dengan apa yang disebut katup 'fix cup'.
Dalam sistem pengaturan tekanan oven, 'fix cup' dipasang di antara pipa tegak dan saluran pengumpul gas mentah. Melalui steker penutup dilengkapi dengan perangkat pengatur dan terhubung ke batang kendali. Dalam perpanjangannya, gooseneck pipa tegak berakhir dalam apa yang disebut tabung mahkota, menonjol dengan slot mahkota yang ada di dalamnya ke dalam 'cup fix'. Juga dipasang di gooseneck pipa tegak adalah dua nozel penyemprot yang di satu sisi berfungsi untuk mendinginkan gas mentah yang panas dan di sisi lain untuk membasahi pipa pengumpul gas untuk mencegah pembentukan tar dan endapan lainnya. Selain itu, melalui katup pengisian cepat, 'fix cup' dapat dengan cepat dibanjiri saat oven kokas telah diputuskan dari saluran pengumpul gas. Gambar 3 menunjukkan sistem pengaturan tekanan oven.
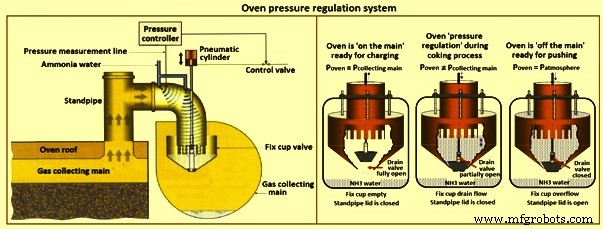
Gbr 3 Sistem pengaturan oven
Pengaturan tekanan oven dilakukan oleh resistensi tekanan variabel untuk gas mentah yang dihasilkan, yang dibuat oleh slot di tabung mahkota. Slot dibuka kurang lebih melalui tingkat air variabel di 'cangkir fix'. Ketinggian air dipengaruhi oleh perangkat pengatur luapan, yang mempertahankan ketinggian air tertentu di dalam 'cup fix' tergantung pada titik setel tekanan ruang oven. Ketinggian air di 'cup fix' berhubungan langsung dengan posisi piston bagian dari perangkat pengatur luapan. Penggerak perangkat pengatur luapan adalah silinder pneumatik yang dihubungkan dengan perangkat pengatur luapan dengan sebuah batang. Silinder pneumatik dikendalikan oleh pengatur posisi kerja kedua sisi, menerima informasinya dari sistem kontrol, yang memproses pengukuran tekanan oven.
Tekanan oven diukur di dalam gooseneck, dari mana ia ditransmisikan ke sistem kontrol. Selama waktu karbonisasi tekanan oven meningkat bertahap dari sekitar +3 mm H2O (0,3 mbar) pada awal waktu karbonisasi, ketika jumlah gas mentah yang dihasilkan dan bahaya emisi berada pada tingkat tertinggi, menjadi sekitar +16 mm H2O (1,6 mbar) pada akhir waktu karbonisasi, ketika jumlah gas mentah yang dihasilkan turun menjadi nol dan karenanya bahaya emisi sangat rendah. Penyesuaian akhir dari set-point biasanya dilakukan setelah pengukuran tekanan di belakang pintu oven pada tingkat sol oven pada saat commissioning COP. Tujuannya adalah untuk menyesuaikan tekanan oven sedemikian rupa sehingga tekanan serendah mungkin di dalam oven dapat dicapai setiap saat tanpa menimbulkan pengisapan di balik pintu pada tingkat sol oven.
Pengumpul gas utama biasanya terletak di sisi pendorong baterai oven kokas. Ini terdiri dari tiga bagian. Setiap bagian utama pengumpul biasanya dilengkapi dengan dua pemeras gas untuk dapat membuang gas mentah langsung ke baterai jika terjadi keadaan darurat. Katup tertutup air membentuk penutupan antara pengumpul gas utama dan atmosfer. Katup pemeras digerakkan secara pneumatik dan terbuka secara otomatis pada tekanan maksimum yang telah ditentukan sebelumnya di saluran pengumpul gas. Pengapian gas mentah dipengaruhi oleh sistem busur listrik yang memulai pengapian segera sebelum pembukaan katup pembuangan. Tekanan utama pengumpul dikendalikan oleh katup kontrol di masing-masing sumber listrik off-take. Tekanan negatif yang dihasilkan dari exhauster, di-throttle ke hulu dari tutup kontrol sehingga gas oven kokas mentah dilepaskan sebanyak yang diperlukan untuk mempertahankan tekanan yang ditentukan di saluran pengumpul gas.
HMI (antarmuka mesin manusia) dari sistem pengaturan tekanan oven terdiri dari beberapa tampilan operator yang memungkinkan operator baterai untuk memantau dan menyesuaikan sistem (dalam mode otomatis) dan jika perlu mengoperasikan sistem dalam mode manual (yaitu dalam keadaan darurat ). Semua nilai proses seperti tekanan oven, ketinggian air di dalam wadah tetap, status semua elemen kontrol, waktu pemasakan terakhir, pesan status, dll. akan ditampilkan. Jika dialihkan ke operasi manual, semua fungsi operasi seperti 'sambungkan untuk mengisi daya', 'kembali untuk mengatur', 'tutup tutup pipa tegak', dll. dapat dimulai secara manual dalam urutan operasi yang benar. Beberapa urutan interlocking masih aktif untuk menghindari kesalahan operasi yang berbahaya. Pengoperasian manual tanpa rangkaian kontrol PLC dan interlocking hanya dapat dilakukan dari panel kontrol pneumatik yang terletak tepat di depan masing-masing pipa tegak. Tampilan tren untuk setiap oven dapat dipilih di HMI, yang menunjukkan nilai proses utama dalam hal waktu.
Analisis kelembaban batubara
Sejumlah sistem pengukuran kelembaban tersedia. Namun, metode yang dapat diandalkan untuk mengukur kelembaban batubara secara online adalah dengan menggunakan 'microwave dengan kompensasi berat area'. Gelombang mikro adalah cara yang sangat akurat untuk mengukur kelembapan karena fakta bahwa gelombang mikro sangat selektif terhadap air. Mereka menembus bahan yang akan diukur. Molekul air secara alami bersifat polar yang menyebabkan gelombang mikro melemah dan melambat secara signifikan. Konstanta dielektrik bahan menunjukkan pengaruh pada gelombang mikro. Konstanta dielektrik air adalah 20 kali lebih besar dibandingkan dengan bahan lain. Hal ini menghasilkan interaksi yang kuat antara gelombang mikro dengan air yang kemudian diukur sebagai redaman dan pergeseran fasa.
Untuk memastikan bahwa refleksi dan resonansi tidak mempengaruhi pengukuran, beberapa frekuensi digunakan dan dievaluasi. Oleh karena itu pengaruh perubahan geometri yang tidak teratur, karena ketebalan lapisan material terlepas dari kompensasi untuk berat area di dekatnya dihilangkan. Pengukuran pergeseran fasa juga diperlukan karena lebih sedikit dipengaruhi oleh beberapa gangguan dan menghasilkan akurasi yang lebih baik. Oleh karena itu, kombinasi redaman dan pergeseran fasa lebih lanjut menghasilkan pengurangan gangguan, yang juga meningkatkan akurasi. Dengan menggabungkan untuk mengukur pergeseran fase dan redaman, presisi yang lebih baik dari 0,2 % dapat dicapai yang dari 'sudut pandang' pengukuran cukup untuk menggunakan nilai kelembapan untuk kontrol pemanasan.
Jika densitas curah bervariasi, yang merupakan kasus operasi dengan campuran batubara yang berbeda dan distribusi ukuran butir yang berbeda, unit pengukuran radiometrik tambahan diperlukan. Ketebalan lapisan dan kerapatan curah berdampak pada hasil pengukuran. Ini sebagian besar dapat dihilangkan dengan menormalkan redaman dan pergeseran fasa ke massa per satuan luas, yang ditentukan oleh pengukuran transmisi sinar gamma. Dalam pengukuran transmisi ini, melemahnya intensitas sinar gamma, yang tergantung pada berat area, diukur. Hasilnya, sinyal kelembapan yang tidak bergantung densitas dapat diperoleh, memastikan presisi setinggi mungkin untuk kontrol proses yang optimal. Jika pada saat yang sama ketebalan lapisan batubara diukur dekat dengan sumber sinar gamma mis. dengan sensor level ultrasonik, densitas curah batubara dapat ditentukan (berat area dikalikan dengan ketebalan lapisan adalah densitas curah). Set-up sistem pengukuran kadar air batubara ditunjukkan pada Gambar 4. Selain peralatan yang ditunjukkan pada set-up, beberapa item lagi diperlukan untuk membuat sistem bekerja.
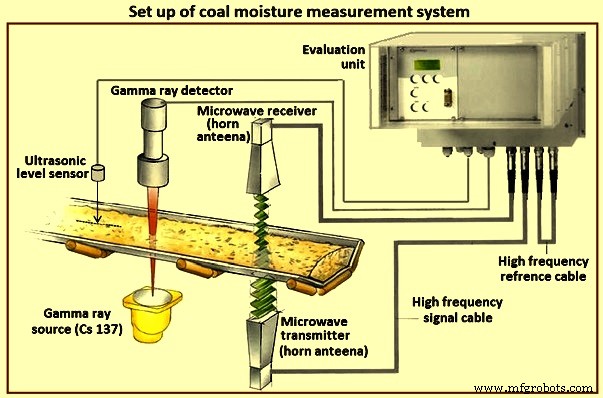
Gbr 4 Pengaturan sistem pengukuran kelembaban batubara
Gelombang mikro ditransmisikan menggunakan sepasang antena tanduk. Satu dipasang di atas sabuk dan yang lainnya dipasang di bawah sabuk. Karena geometri transmisi ini, persentase besar dari keseluruhan volume diukur. Ini memberikan representasi yang sangat akurat dari kadar air di seluruh lapisan batubara. Oleh karena itu, kelembaban di dalam lapisan batubara penuh diukur dan tidak hanya kelembaban permukaan.
Sumber sinar gamma (Nuclide Cs 137) dipasang di bawah sabuk. Itu harus sedekat mungkin dengan antena klakson pemancar gelombang mikro sehingga porsi batubara yang sama di tempat dan waktu yang sama direferensikan satu sama lain (atenuasi dan pergeseran fasa berkorelasi dengan berat area secara real time). Dipusatkan secara vertikal ke sumber sinar gamma adalah detektor sinar gamma (detektor kilau) yang dipasang di atas sabuk. Dua antena tanduk, sumber sinar gamma dan detektor sinar gamma dihubungkan dengan kabel sinyal frekuensi tinggi khusus ke unit evaluasi yang menghubungkan dan menghitung kelembaban dan kerapatan curah secara real time. Kurva referensi yang diperoleh dari beberapa uji kalibrasi (kelembaban on-line di atas kelembapan laboratorium) disimpan di unit evaluasi untuk konsistensi atau campuran beberapa batubara. Garis referensi terintegrasi ini memastikan kompensasi pengaruh lingkungan yang andal. Dengan cara ini kandungan air dan densitas curah batubara dapat ditentukan dengan sangat akurat.
Pengukuran bekerja paling baik, jika permukaan batubara lurus dan rata. Oleh karena itu, perlu untuk meletakkan beberapa peralatan perataan di depan set-up pengukuran. Perataan permukaan batubara dilakukan dalam dua tahap. Pertama, pelat baja berat digunakan sebagai pengikis. Ekskursi maksimum scraper dibatasi oleh rantai untuk menghindari scraper bersentuhan dengan sabuk karet. Bobot dapat ditambahkan ke scraper untuk mengatur gaya gesekan dan menyesuaikan jalur paving. Kedua, kereta luncur, yang juga dibatasi pergerakannya oleh rantai, meratakan gundukan yang tersisa. Jika level batubara pada belt sangat tinggi atau tumpukan batubara mendekat, scraper atau sledge dapat menumpahkan batubara dari belt. Oleh karena itu, penahan yang terbuat dari bahan sabuk karet ditempatkan di setiap sisi sabuk. Permukaan batu bara yang rata diperlukan untuk mendapatkan sinyal yang andal.
Sistem pengukuran suhu dinding ruang otomatis
Sistem pengukuran suhu dinding ruang otomatis terdiri dari sistem pengukuran suhu dinding ruang kokas melalui kabel serat optik berpendingin udara dan pirometer terpasang yang dipasang pada balok ram bagian belakang 'dingin' dari mobil pendorong. Suhu dinding diukur ketika ram melewati oven. Mereka dikonversi dan dievaluasi untuk memungkinkan pengawasan suhu dan distribusi panas baterai dalam arah longitudinal, transversal dan vertikal. Ini dapat dilakukan dengan memeriksa suhu dinding silang, suhu baterai longitudinal, distribusi panas vertikal, pengembangan suhu dalam hal waktu, pemeriksaan pemanasan dinding, dll. Gambar 5 menunjukkan prinsip sistem pengukuran suhu dinding ruang otomatis.
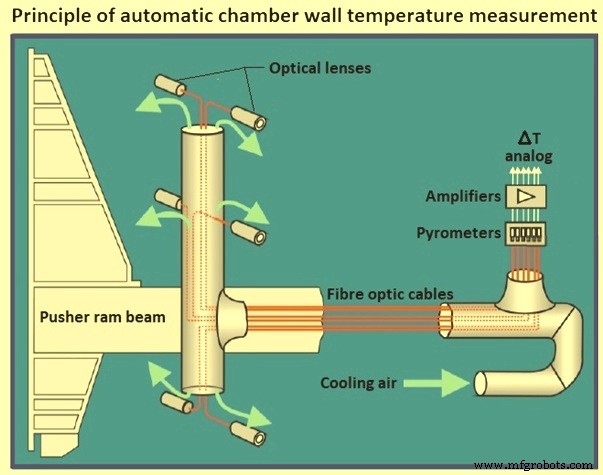
Gbr 5 Prinsip pengukuran suhu dinding ruang otomatis
Intensitas cahaya yang terpancar dari dinding oven dideteksi oleh kabel serat optik di setiap titik pengukuran. Titik pengukuran ini terdiri dari rumahan yang diisolasi secara termal terhadap radiasi dan panas yang dilakukan oleh kepala ram. Perumahan mengakomodasi dudukan kabel serat optik, sistem perutean udara untuk efek pendinginan yang optimal, kabel serat optik, dan koneksi umpan udara terkompresi. Kabel serat optik terpasang secara permanen dalam kaitannya dengan ram. Udara terkompresi dibiarkan mengalir di sepanjang kabel serat optik yang melindunginya dari panas berlebih dan kotoran, dan membersihkan saluran di antara cahaya pada rumah pemandu saat dihembuskan ke ruang oven.
Beberapa ratus titik data (data mentah) diukur oleh setiap pirometer selama satu proses dorong yang ditransmisikan ke PLC di ruang listrik mesin penekan dan dikorelasikan dengan informasi jarak terkait dari sistem penggerak ram. Nilai mentah dikompresi untuk membangun satu nilai suhu rata-rata per cerobong pemanas untuk setiap pirometer. Nilai-nilai ini (total 6 x jumlah cerobong pemanas) bersama dengan nomor oven masing-masing dorongan, waktu mendorong, dan leveling disimpan sementara di media penyimpanan stasiun PLC sistem pengukuran suhu dinding ruang otomatis yang ditunjuk pada mesin pendorong. Nilai yang ditentukan ditransmisikan melalui serat optik dari mesin pendorong ke PLC COP untuk mesin oven yang menerima data dan menyimpan data tersebut dalam database.
Kapan pun diperlukan, operator dapat memilih dan mengevaluasi data suhu dari arsip dengan menggunakan sistem menu komprehensif yang terintegrasi dalam HMI COP PLC untuk mesin oven yang tersedia di semua PC klien server. Alarm otomatis dihasilkan jika nilai ambang batas terlampaui. Operator dapat memeriksa secara berkala atau jika ada peringatan distribusi suhu di dalam blok baterai untuk mendeteksi ketidaksesuaian sistem pembakaran yang dapat menyebabkan kokas batubara di area tertentu dari massa kokas yang mengakibatkan kokas buruk kualitas dan polusi selama mendorong.
Selain memperingatkan masalah di dinding silang, distribusi suhu vertikal sangat penting di ruang oven tinggi. Ini dicapai dengan nyala api yang panjang di atas ketinggian penuh cerobong asap. Nyala api dipengaruhi oleh distribusi gas dan udara ke cerobong pemanas yang harus disesuaikan dengan benar. Perubahan dalam distribusi udara (yaitu perubahan dalam rancangan tumpukan) tanpa tindakan balasan yang tepat dapat memiliki pengaruh yang mengganggu pada panjang api (distribusi panas vertikal) dan pada akhirnya dapat menyebabkan kokas yang tidak merata, karbon atap, dan yang paling buruk pada akhirnya. untuk 'oven stiker'. Sistem pengukuran suhu dinding ruang otomatis dapat dengan cepat mendeteksi masalah pemanasan vertikal saat mengambil suhu di tiga tingkat ruang oven selama setiap dorongan. Deteksi masalah ini membantu meningkatkan sistem pemanas yang mengarah pada perlindungan lingkungan yang lebih baik, kualitas kokas yang lebih tinggi, efisiensi produksi yang lebih tinggi (penghematan gas / energi) dan lebih sedikit tekanan pada bata (masa pakai baterai lebih lama).
Evaluasi pemanasan dinding tunggal atau oven, suhu dinding oven dari sistem pengukuran suhu dinding ruang otomatis dapat dipadatkan untuk memberikan suhu baterai rata-rata, yang dapat digunakan sebagai masukan untuk kontrol pemanasan baterai.
Sistem pemantauan otomatis gaya dorong
Bersamaan dengan pengukuran suhu dinding ruang, sementara ram pendorong mendorong kokas keluar dari oven, secara bersamaan torsi yang diperlukan untuk tindakan ini diukur pada motor penggerak ram. Nilai-nilai ini diukur saat ram pendorong mendorong kokas panas keluar dari oven. Torsi disediakan dari unit konverter frekuensi yang mengontrol kecepatan motor dan torsi motor dan diubah dalam PLC untuk mesin oven menjadi gaya dorong. Sistem ini disebut 'sistem pemantauan otomatis gaya dorong' dan memberikan informasi yang luar biasa tentang situasi pemeliharaan mekanis sistem penggerak ram dan kondisi kokas dari kue kokas. Jika kekuatan ram meningkat selama periode waktu tertentu, masalah mekanis atau pemanasan dapat diperkirakan yang memerlukan perhatian dan evaluasi lebih lanjut untuk pemecahan masalah.
Grafik pemantauan otomatis gaya dorong dapat dipanggil pada HMI PLC untuk mesin oven oleh operator untuk kontrol proses dan sebagai alat pemecahan masalah. Manajer pabrik memilih data pemantauan otomatis gaya dorong dari arsip jangka panjang untuk pemantauan proses, pengoptimalan, dan survei historis. Kurva gaya dorong menunjukkan profil yang sama yang berarti puncak gaya dorong pada awalnya untuk melepaskan kokas dari dinding dan membuat kue kokas bergerak. Setelah puncak awal ini, gaya dorong jauh lebih rendah, hanya cukup untuk membuat kue kokas bergerak sepanjang oven. Segera setelah sepatu ram pendorong memasuki oven, puncak baru namun lebih kecil berkembang. Sepatu penopang ini meluncur di atas sol oven dan memberikan gesekan tambahan ke batu bata yang harus dilawan oleh ram drive, yang mengarah ke peningkatan gaya dorong yang dibutuhkan. Ini adalah situasi normal setiap kali mendorong.
Jika grafik menonjol dari profil biasa dengan beberapa puncak dorong di sepanjang jalur dorong, maka puncak pertama berulang beberapa kali selama satu dorong. Alasannya bisa karena dorongan berhenti beberapa kali dan dilanjutkan lagi saat ram melewati oven. Masalah mekanis pada panduan coke membutuhkan penghentian ini. Dengan setiap restart, sistem penggerak pendorong harus mendapatkan kembali kekuatan untuk membuat kue kokas bergerak lagi. Empat puncak menunjukkan bahwa ram pendorong berhenti dan memulai kembali empat kali setelah 'puncak putus' awal. Contoh ini menunjukkan bahwa pengukuran gaya dorong adalah alat yang berguna untuk mendeteksi dan mendokumentasikan masalah operasional selama mendorong.
Sistem penjadwalan dan kontrol otomatis mesin oven
Kontrol proses dan pemantauan operasi COP juga mencakup penyusunan jadwal dorong dan tampilan layar kinerja operasi mesin oven. Untuk tujuan ini, program jadwal mendorong dan mengisi daya yang sangat canggih yang disebut 'penjadwalan otomatis dan sistem kontrol mesin oven' sebagai bagian dari sistem otomasi COP digunakan. Waktu mendorong dan mengisi daya untuk setiap oven dihitung dan dioptimalkan, ditransfer ke mesin oven dan diberi sinyal ke operator. Data aktual dari operasi mendorong dan mengisi daya diumpankan kembali ke sistem penjadwalan untuk memperbarui perhitungan.
'Sistem kontrol dan terjadwal otomatis dari mesin oven' dapat menangani perencanaan produksi normal serta semua jenis operasi khusus (yaitu kompensasi kerusakan atau penurunan produksi). Perhitungan ulang dapat dipicu dan dibuat ulang kapan saja ketika ada perubahan dalam data produksi atau ada masalah pengoperasian. Beberapa strategi tersedia untuk menangani kerugian produksi. Kerugian dapat diterima atau diganti dengan meningkatkan produksi dengan memperpendek waktu penggorengan secara hati-hati dan aman untuk menjaga kinerja dan produksi pemanasan terbaik. Oleh karena itu, perubahan jadwal secara otomatis memengaruhi panas nominal yang dihitung dalam model kontrol pemanas.
Jadwal mendorong dan pengisian dapat dihitung untuk beberapa hari sebelumnya dalam mode simulasi khusus untuk perencanaan produksi lanjutan. Sistem ini saling terkait dengan sistem pengaturan tekanan oven untuk menangani pemutusan dari saluran pengumpul untuk mendorong dan penyambungan kembali ke saluran pengumpul untuk pengisian. Gambar 6 menunjukkan fungsi utama dan filosofi sistem operasi serta tampilan operasi. Layar komputer di sisi kanan biasanya memiliki tiga tampilan. Tampilan pertama disebut 'status oven', yang menampilkan untuk setiap oven waktu tekan/pengisian berikutnya, waktu tekan/pengisian terakhir, waktu dalam siklus sebagai grafik batang dengan berbagai warna, dan bobot pengisian daya, dll. Tampilan kedua adalah untuk jadwal yang dihitung yang menunjukkan siklus mendorong dan mengisi dalam urutan kronologis untuk beberapa hari ke depan sebelumnya. Tampilan ketiga menunjukkan riwayat mendorong dan mengisi sebagai laporan.
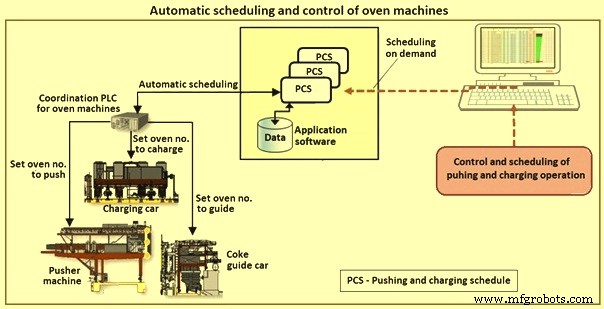
Gbr 6 Penjadwalan dan kontrol otomatis mesin oven
Sistem kontrol otomatis pemanasan baterai
Sistem kontrol otomatis pemanasan baterai adalah model perhitungan teoritis yang menentukan energi yang dibutuhkan untuk pemanasan baterai. The model is dynamically updated by the actual production performance (adapting to delays, ‘speed up’, lost production, etc.) and the actual heating performance (adapting is based on actual heating flue, coke or wall temperatures which are outside of the target range). The energy requirements determined by the ‘automatic control system of battery heating’ model are the set point for the heating system. The energy needed for the battery heating in this case is controlled by changing the heating time (varying a pause time between reversals).
Automatic control system of battery heating is shown in Fig 7. The figure also shows a trend graph of the heating control results. Whenever the coking time changes (green arrow), the energy quantity control reacts by creating a new set point for the energy input (yellow arrow), mainly by changing the pause time (blue arrow). In the example given, the pause time is increased from around 200 seconds to around 275 seconds by the model to match a declining energy demand (red curve)) due to a general increase in the coking time (green curve) from 28.9 hours to 30.1 hours. The rise of the ‘mean battery temperature’, measured by the automatic chamber wall temperature measurement system (pink dotted arrow), also needs a reduction of heat, which lowers the energy set point even further. The total reduction of energy (yellow curve) leads to a reduction of the ‘mean battery temperature’ (pink arrow). However, this happens with a time delay due to the reaction time needed to bring the energy from the heating flue to the coke.
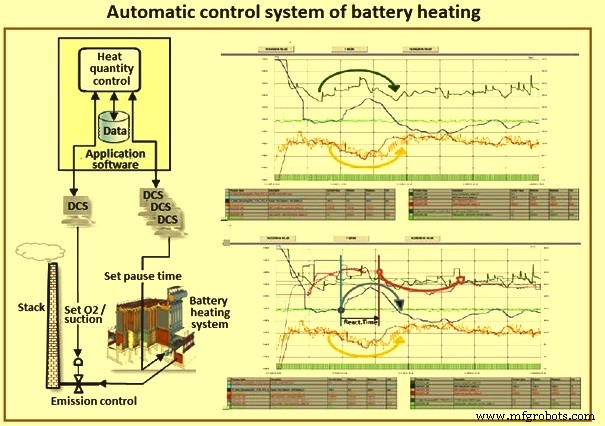
Fig 7 Automatic control system of battery heating
For making both temperatures measured at different places in the brickwork comparable to each other, the heating flue temperatures are extrapolated by the heat transfer rate to oven wall temperatures. The ‘automatic control system of battery heating’ model is able to keep the quantity of heating energy under control, ensures less energy consumption and a quick and automatic response to operation troubles which holds the battery temperatures in balance, reducing heating problems and pushing emissions.