Kimia Pembuatan Baja dengan Tungku Oksigen Dasar
Kimia Pembuatan Baja dengan Pembuatan Baja Oksigen Dasar
Pembuatan baja oksigen dasar (BOS) adalah proses pembuatan baja primer yang paling banyak digunakan untuk produksi baja mentah dari logam panas (HM). Bejana proses dikenal sebagai konverter. Ini memainkan peran utama dalam pabrik baja terintegrasi untuk produksi baja mentah. Proses ini melibatkan peniupan oksigen (O2) melalui HM dengan bantuan tombak atas untuk mengurangi kandungan karbon (C) melalui oksidasi. Saat ini pencampuran blowing diadopsi dalam proses BOS yang dikembangkan pada akhir 1970-an. Dalam peniupan campuran, peniupan terbatas gas netral, argon (Ar) atau nitrogen (N2) dilakukan melalui bagian bawah konverter tiupan atas. Ini memberikan pengadukan yang efisien.
Proses BOS memiliki dua karakteristik. Pertama, prosesnya bersifat autogenous artinya tidak diperlukan sumber panas dari luar. Reaksi oksidasi selama pukulan O2 memberikan energi yang dibutuhkan untuk melelehkan fluks dan skrap dan untuk mencapai suhu baja cair yang diinginkan. Kedua, proses memurnikan HM pada tingkat produksi yang tinggi untuk produksi baja cair. Laju reaksi yang cepat disebabkan oleh luas permukaan yang tersedia untuk reaksi. Sejumlah besar gas berkembang ketika O2 disuntikkan ke dalam bak logam. Gas ini membentuk emulsi dengan terak cair dan tetesan logam dicukur dari permukaan bak oleh pelampiasan pancaran O2. Luas permukaan yang besar yang dihasilkan oleh emulsi gas-metal-slag meningkatkan laju reaksi pemurnian.
Karena pengotor terlarut dalam logam cair, reaksi antara pengotor dan O2 terjadi dengan O2 terlarut. Selanjutnya karena oksidasi C terjadi pada suhu yang lebih tinggi, oksidasi C menjadi karbon mono-oksida (CO) sangat mungkin terjadi dan karenanya sebagian besar C dihilangkan sebagai CO.
Selama proses BOS, pengotor dalam HM seperti C, silikon (Si), mangan (Mn), fosfor (P), dll. dihilangkan dengan oksidasi untuk produksi baja cair. Oksidasi dilakukan dengan gas O2 kemurnian tinggi yang dihembuskan dalam konverter. Reaksi oksidasi menghasilkan pembentukan CO, CO2 (karbon di-oksida), silika (SiO2), oksida mangan (MnO), dan oksida besi (FeO). Sementara CO dan CO2 dalam bentuk gas dan dikeluarkan dari bagian atas konverter sebagai gas konverter, oksida lainnya dilarutkan dengan fluks yang ditambahkan ke konverter, untuk membentuk terak cair. Terak cair mampu menghilangkan P dan S (sulfur) dari logam cair.
Reaksi yang terjadi dalam proses BOS dapat dikategorikan ke dalam lima kategori. Reaksi dalam kategori pertama 'pengambilan oksigen oleh logam' adalah (i) O2(g) =2O, (ii) (FeO) =Fe + O, (iii) (Fe2O3) =2(FeO) + O, dan (iv) CO2(g) =CO(g) + O. Reaksi dalam kategori kedua 'oksidasi unsur-unsur dalam logam' adalah (i) C + O =CO(g), (ii) Fe + O =(FeO), (iii) Si + 2O =(SiO2), (iv) Mn + O =(MnO), dan (v) 2P + 5O =(P2O5). Reaksi dalam kategori ketiga 'oksidasi senyawa dalam terak' adalah (i) 2(FeO) + 1/2O2(g) =(Fe2O3) dan (ii) 2(FeO) + CO2(g) =(Fe2O3) + CO Reaksi dalam kategori keempat 'reaksi fluks' adalah (i) MgO(s) =(MgO), dan (ii) CaO(s) =(CaO). Reaksi dalam kategori kelima 'reaksi gas' adalah CO(g) + O2(g) =CO2.
BOS adalah proses kinetika yang sangat tinggi, reaksi berlangsung di beberapa lokasi. Interaksi cairan jet dan reaksi C-O menghasilkan produk gas memiliki efek besar pada dinamika proses secara keseluruhan. Proses ini dicirikan oleh laju reaksi yang tinggi, proses pemurnian diselesaikan biasanya dalam 12 menit (menit) hingga 15 menit. Untuk pengendalian proses untuk kualitas dan produktivitas dalam kerangka waktu yang singkat ini, pemahaman yang baik tentang dinamika proses adalah penting.
Konverter BOS tipikal terdiri dari tong silinder dengan bagian bawah yang membulat, dan bagian atas berbentuk kerucut (sudut setengah kerucut 25 derajat hingga 30 derajat) untuk mengarahkan gas ke kap gas buang. Tubuh didukung pada poros, yang disebut trunnion, sehingga tungku dapat diputar untuk pengisian, pengambilan sampel, penyadapan, dan penghapusan terak. Bagian dalam biasanya dilapisi dengan refraktori magnesia-karbon, dengan kualitas dan ketebalan yang berbeda agar sesuai dengan pola keausan. Volume tipikal yang disediakan di dalam konverter adalah sekitar 1 meter kubik (cum) per ton baja cair yang diproduksi. Jika berat terak adalah 100 kilogram per ton (kg/t) sampai 120 kg/t, maka freeboard di atas bak tidak aktif lebih dari 80%. Ini mengakomodasi reaksi kuat yang terjadi selama bagian tengah pukulan biasa. Bagian bawah konverter dilengkapi dengan beberapa (biasanya 6 hingga 8) elemen berpori, yang melaluinya gas Ar dilewatkan untuk pencampuran rendaman dan membantu reaksi terak-logam. Sebuah lubang keran disediakan di satu sisi di bagian bawah kerucut untuk mengetuk baja cair. Terak dituangkan di sisi lain melalui mulut.
Proses BOS adalah proses pemurnian yang sangat cepat yang membutuhkan kontrol dinamis yang baik dan model dinamis untuk pemahaman proses yang lebih baik. Proses ini dicirikan oleh reaksi pada beberapa skala seperti pada skala rendaman logam dan terak dan pada skala tetesan dan gelembung. Reaksi juga berlangsung di beberapa situs reaksi. Kehadiran jet supersonik yang berinteraksi dengan rendaman logam dan lapisan terak, menghasilkan ukuran tetesan yang berbeda dalam emulsi yang pada reaksi menghasilkan gelembung berlebihan pada antarmukanya, masalah pelarutan kapur, dll., Membuat deskripsi dinamika proses kompleks.
Bahan baku utama adalah HM pada suhu sekitar 1.300 derajat C hingga 1.400 derajat C. Karena panas yang dihasilkan lebih dari yang dibutuhkan, skrap baja bersama dengan bijih besi digunakan sebagai pendingin. Batu kapur (CaCO3) ditambahkan di beberapa toko peleburan baja sebagai pendingin untuk menyesuaikan suhu akhir. Kapur terkalsinasi (CaO) digunakan sebagai fluks untuk mencapai kebasaan tinggi yang diperlukan untuk penyisihan P. Memo ditambahkan terlebih dahulu ke konverter kosong (setelah penyadapan terak dari panas sebelumnya), di mana jumlah HM yang diperlukan ditambahkan. Bijih besi saat digunakan ditambahkan secara terdistribusi biasanya selama paruh pertama pukulan.
Sebagian atau seluruh kapur yang diperlukan ditambahkan sebelum penambahan skrap untuk bertindak sebagai bantalan benturan untuk melindungi lapisan dari jatuhnya skrap. Sisa kapur biasanya ditambahkan secara terdistribusi selama pukulan. Beberapa penambahan magnesium (MgO) terjadi dalam bentuk dolomit terkalsinasi (CaO.MgO), untuk meminimalkan disolusi refraktori ke dalam terak. Kuantitas bahan muatan yang berbeda dihitung secara teoritis dengan model kontrol muatan berdasarkan keseimbangan material dan panas, dengan mempertimbangkan komposisi input, suhu HM, serta komposisi dan suhu baja keluaran.
Semua reaksi pemurnian adalah pengoksidasi. Hal ini dicapai dengan meniup oksigen tonase melalui tombak atas yang dilengkapi dengan 3 hingga 6 nozel aliran supersonik (2,0 Mach hingga 2,1 Mach, dipasang pada sudut sumbu tombak). Ujung tombak dipegang pada jarak antara 1,8 meter (m) hingga 2,5 m di atas permukaan penangas logam yang tenang dalam konverter berukuran besar. Ketinggian tombak adalah salah satu parameter operasi untuk mengontrol proses
Siklus tap-to-tap yang khas terdiri dari langkah-langkah seperti yang dijelaskan di sini. Urutan pengisian adalah kapur, skrap, dan HM. Setelah konverter dibuat tegak, tombak O2 diturunkan ke ketinggian yang diperlukan (awalnya, nilai tertinggi, 2,2 m hingga 2,5 m) dan penghembusan dimulai. Selama paruh pertama pukulan, kapur tambahan jika ada bersama dengan bijih besi, dolomit yang dikalsinasi, dan aditif lainnya ditambahkan. Penambahan bahan yang mengandung uap air dihindari selama bagian akhir pukulan untuk menjaga hidrogen (H2) dalam baja yang dihasilkan tetap rendah. Operasi tombak tinggi dilanjutkan (biasanya 3 menit sampai 4 menit) sampai terak memiliki cukup FeO untuk memfasilitasi pembubaran kapur. Setelah itu tombak diturunkan secara bertahap untuk mencapai tingkat pemurnian yang dibutuhkan. Ketinggian tombak dikurangi dalam 3 langkah menjadi 5 langkah tergantung pada praktik masing-masing tanaman.
Pada sekitar 80% sampai 90% dari pukulan (berdasarkan aliran O2) sampel diambil untuk analisis dan suhu diukur sehingga ketika seseorang menyelesaikan pukulan, komposisi dan suhu yang diperlukan tercapai secara bersamaan. Pengambilan sampel dan pengukuran suhu dapat dilakukan baik secara manual, yaitu menghentikan pukulan, memutar konverter ke posisi hampir horizontal dan mengambil sampel melalui sendok dan mengukur suhu, atau melalui sub-tombak yang diturunkan ke konverter bertiup (dalam -pengambilan sampel pukulan). Berdasarkan analisis sampel dan suhu, bagian pukulan yang tersisa dilengkapi dengan penambahan trim yang diperlukan. Setelah pukulan selesai, konverter diputar ke sisi sadapan untuk menuangkan baja cair keluar, dan kemudian ke sisi lain untuk sadapan terak. Dalam praktek modern, beberapa terak dipertahankan, konverter dibuat tegak, beberapa magnesit (MgO) ditambahkan dan kemudian terak dipercikkan ke permukaan bagian dalam dengan meniup N2 kecepatan tinggi. Secara berkala, konverter kosong diperiksa untuk kerusakan refraktori, baik secara manual atau melalui pemindai laser. Kerusakan diperbaiki dengan menembakkan senjata refraktori massa. Setelah ini konverter siap untuk pukulan berikutnya.
Proses BOS adalah proses kompleks yang berlangsung dalam rentang waktu yang singkat, dengan sangat sedikit informasi umpan balik langsung yang tersedia saat proses berlangsung. Proses tersebut terdiri dari beberapa sub-proses yang kurang dipahami atau hanya ada pemahaman semi-kuantitatif. Karena prosesnya adalah proses autogenous, ada kelebihan panas bahkan setelah input HM sekitar 1.350 derajat C dan baja keluaran di-tap pada 1.650 derajat C hingga 1.700 derajat C. Oleh karena itu, pendingin yang berbeda digunakan, skrap dan bijih besi menjadi yang utama. O2 dikirim ke proses melalui pancaran supersonik yang dikeluarkan ke dalam gas panas dan sarat debu atau di bawah emulsi gas cair dengan perilaku pancaran dipengaruhi oleh lingkungan sekitar. Gambar 1 menunjukkan representasi skema dari proses BOS dan fitur dasarnya dijelaskan di bawah ini.
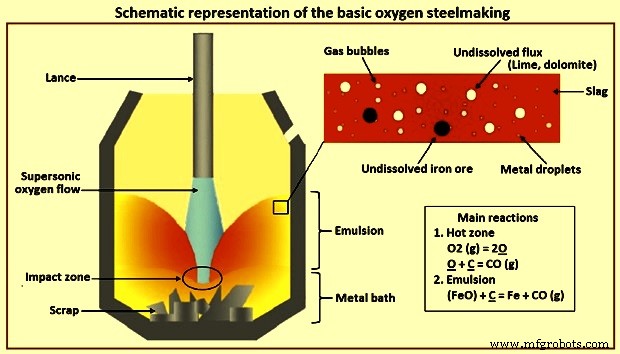
Gbr 1 Representasi skematis dari pembuatan baja oksigen dasar
Oksidasi karbon – Dekarburisasi C yang tersedia dalam bak adalah reaksi yang paling ekstensif dan penting selama proses BOS. Ada tiga tahap berbeda selama reaksi dekarburisasi ini. Pada tahap pertama yang terjadi selama beberapa menit pertama pukulan, dekarburisasi berlangsung pada kecepatan yang lambat, karena sebagian besar O2 yang disuplai bereaksi dengan Si penangas. Selama tahap kedua, yang terjadi pada kandungan C tinggi dari bak mandi, dekarburisasi terjadi pada tingkat yang lebih tinggi dan dikendalikan oleh tingkat O2 yang dipasok. Tahap ketiga terjadi ketika kandungan C dari bak mandi mencapai sekitar 0,3%. Pada tahap ini, laju dekarburisasi turun karena C lebih rendah tersedia untuk bereaksi dengan semua O2 yang dipasok. Pada tahap ini, laju dikendalikan oleh perpindahan massa C, dan O2 sebagian besar bereaksi dengan besi (Fe) untuk membentuk FeO. Pada tahap ini, karena laju pembentukan CO turun, nyala api di mulut konverter menjadi kurang bercahaya dan praktis menghilang ketika C turun ke tingkat sekitar 0,1%.
Oksidasi silikon – Kondisi yang menguntungkan untuk oksidasi silikon adalah (i) suhu rendah, dan (ii) jumlah SiO2 yang rendah dalam terak. Terak dasar mendukung oksidasi Si. Dalam terak dasar, oksidasi Si terjadi secara praktis ke nilai yang sangat rendah karena SiO2 bereaksi dengan CaO dan menurunkan aktivitas SiO2 dalam terak. Hampir semua Si teroksidasi dan dihilangkan di awal pukulan karena afinitas O2 yang kuat untuk Si. Si dari HM teroksidasi ke tingkat yang sangat rendah (kurang dari 0,005 %) dalam 3 menit pertama sampai 5 menit pukulan. Oksidasi Si menjadi SiO2 bersifat eksotermik dan menghasilkan panas dalam jumlah besar yang meningkatkan suhu bak. Ini juga membentuk terak silikat yang bereaksi dengan tambahan kapur dan dolomit terkalsinasi untuk membentuk terak dasar. Karena oksidasi Si adalah sumber panas utama, kuantitasnya dalam HM menentukan jumlah muatan dingin (bekas, dan besi kasar, dll.) yang dapat ditambahkan ke konverter. Ini juga menentukan volume terak dan karenanya mempengaruhi defosforisasi rendaman dan hasil. Sesuai aturan praktis, jumlah terak yang lebih tinggi menghasilkan P yang lebih rendah tetapi juga hasil yang lebih rendah.
Oksidasi besi – Oksidasi besi (Fe) adalah yang paling penting untuk proses BOS karena mengontrol (i) kandungan FeO terak dan kandungan O2 dalam baja, (ii) hilangnya Fe dalam terak dan karenanya mempengaruhi produktivitas pembuatan baja proses, (iii) potensi oksidasi terak, dan (iv) FeO membantu dalam pelarutan CaO dalam terak.
Oksidasi mangan – Reaksi oksidasi Mn pada proses BOS agak kompleks. Dalam konverter tiup atas, Mn dioksidasi menjadi MnO oksida pada tahap awal pukulan dan setelah sebagian besar Si teroksidasi, maka Mn kembali ke bath metal. Akhirnya, pada akhir pukulan ketika lebih banyak O2 tersedia untuk oksidasi, Mn tereduksi dalam bath metal. Dalam kasus tiupan bawah atau tiupan gabungan dalam konverter, oksidasi Mn memiliki pola yang sama tetapi kandungan Mn sisa dari baja cair dalam wadah konverter lebih tinggi daripada konverter tiup atas.
Oksidasi fosfor – Kondisi pengoksidasi dalam konverter mendukung defosforisasi bath metal. Reaksi defosforisasi terjadi karena interaksi logam dan terak di bak mandi. Parameter seperti suhu rendaman yang lebih rendah, kebasaan terak yang lebih tinggi (rasio CaO/SiO2), kandungan FeO yang lebih tinggi dalam terak, fluiditas terak yang lebih tinggi, dan pengadukan yang baik dari rendaman mendukung reaksi defosforisasi. Kandungan fosfor dari bath metal berkurang pada awal pukulan, kemudian selama periode dekarburisasi utama ketika FeO berkurang, P kembali ke bath metal dan akhirnya berkurang lagi pada akhir blow. Pengadukan mandi meningkatkan pencampuran logam dan terak dan membantu dalam laju defosforisasi. Pengadukan yang baik dengan penambahan bahan fluks seperti tepung spar dll., juga meningkatkan penyisihan P dengan meningkatkan pelarutan CaO, menghasilkan terak cair yang sangat basa dan cair.
Reaksi belerang – Penghilangan S tidak terlalu efektif dalam proses BOS karena kondisi pengoksidasi yang tinggi. Rasio distribusi S (% S dalam terak / % S dalam logam) adalah sekitar 4 hingga 8 yang jauh lebih rendah daripada di sendok baja (sekitar 300 hingga 500) selama proses pembuatan baja sekunder. Selama proses BOS, sekitar 10% sampai 20% S dalam bak bereaksi dengan O2 secara langsung membentuk SO2 (sulfur di-oksida). S yang tersisa dihilangkan dengan reaksi terak – logam S + CaO =CaS + FeO. Penghapusan S oleh terak dibantu oleh kebasaan yang tinggi dan kandungan Fe yang rendah dari terak. Kandungan S dari baja cair sangat dipengaruhi oleh S yang terkandung dalam HM dan scrap yang diisikan pada konverter.
Reaksi yang terjadi selama proses BOS bersifat heterogen dan pada skala panjang yang berbeda. Ada fase mandi logam curah, fase terak curah, dan fase gas. Di sisi lain, sebagian besar reaksi terjadi pada skala tetesan halus dan gelembung yang didistribusikan dalam fase emulsi terak / logam / gas. Perbedaan skala panjang juga mengakibatkan perbedaan skala waktu. Penangas logam melihat perubahan selama seluruh siklus panas dari 12 menit hingga 15 menit sedangkan tetes dapat menjalani siklus pemurnian lengkap dalam waktu sekitar satu menit. Oleh karena itu, gambaran dinamika proses telah berkembang selama beberapa tahun berdasarkan pengamatan dan pengukuran di pabrik komersial dan percontohan, eksperimen yang dirancang dengan cermat, dan pemodelan matematika.
Komposisi khas HM dapat berupa C – 4,5%, Si – 0,3% hingga 0,5%, Mn – 0,2% hingga 0,7%, P – 0,1% hingga 0,18 %, S – 0,02 % hingga 0,03 %, dan suhu 1.350 derajat C Karena S hanya dapat dihilangkan menjadi terak dalam keadaan tereduksi dengan adanya besi cair, proses oksidasi dalam pembuatan baja oksigen dasar tidak menghilangkan sejumlah besar S. Reaksi keseluruhan yang signifikan dapat ditulis sebagai (i) [Si] + {O2} =(SiO2), (ii) [Mn] + 1/2 {O2} =(MnO), (iii) [C] + 1/2 {O2} ={CO}, (iv ) 2[P] + 5/2 {O2} =(P2O5), (v) Fe (l) + 1/2 O2(g) =(FeO). [-],{-}, dan (-) masing-masing digunakan untuk metaloid yang terlarut dalam rendaman logam, gas, dan konstituen dalam terak. Gambar 2a memberikan kemajuan reaksi dalam konverter 200 t. Pengukuran yang dilakukan pada konverter yang berbeda juga menunjukkan pola yang serupa. Gambar 2b memberikan evolusi yang sesuai dari komposisi terak.
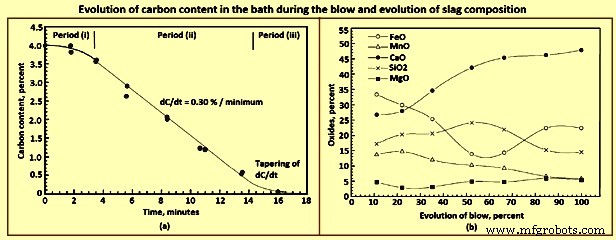
Gbr 2 Evolusi kandungan karbon dalam bak selama pukulan dan evolusi komposisi terak
Salah satu ciri penting dalam evolusi komposisi logam adalah penghilangan C dalam jumlah yang cukup besar secara simultan bahkan sebelum Si turun ke tingkat yang sangat rendah. Hal ini juga dibuktikan dengan pengamatan bahwa nyala CO menyembur ke atas di mulut konverter dalam waktu singkat sejak dimulainya hembusan O2. Ini berbeda dengan pengamatan pada konverter Bessemer atau proses OBM yang sekarang sudah usang, di mana udara / O2 dihembuskan dari bawah. Dalam dua proses ini, munculnya nyala api yang signifikan membutuhkan beberapa waktu, yang diasumsikan menunjukkan bahwa oksidasi C tidak dimulai sampai Si turun ke nilai yang cukup rendah.
Secara termodinamika, urutan reaksi oksidasi zat terlarut pada setiap lokasi lokal untuk kondisi masukan yang disebutkan di atas adalah Si, Mn, C, dan P. Artinya, pada kondisi yang berlaku di bagian awal pukulan, Si teroksidasi sebelum C. Suhu awal yang rendah itu sendiri membuat reaksi Si menjadi menguntungkan. Selain itu, produk SiO2 berada pada aktivitas yang sangat rendah dalam kondisi sangat dasar yang dipertahankan sejak awal. Tekanan parsial CO di sisi lain tetap hampir 0,1 MPa (satu atmosfer). Misalnya, jika aktivitas 0,001 untuk SiO2 diasumsikan maka pO2 dalam kesetimbangan dengan 4,5 % C dan 0,5 % Si adalah masing-masing 1MPa hingga 1,7 MPa, dan 1 MPa hingga 1,9 MPa. Fitur ini membuat analisis dinamika proses dan mekanisme reaksi menjadi menarik.
Karakteristik proses
Karena informasi umpan balik dari proses terbatas, maka perlu membangun model untuk dinamika proses dari karakteristik yang diamati dari informasi yang diperoleh. Fitur penting dari proses BOS dijelaskan di bawah ini.
Laju reaksi sangat cepat. Selama dekarburisasi puncak, C dihilangkan dengan laju sekitar 0,3% per menit, yaitu sekitar 600 kg C per menit dalam konverter 200 t (Gbr 2a). Reaksi C menunjukkan tiga periode tipikal (Gbr 2a) yaitu (i) periode awal ketika laju meningkat, (ii) periode antara ketika laju relatif konstan terlepas dari kenyataan bahwa kandungan C dalam bak terus menerus turun dari sekitar 3,5% menjadi 4,0% selama periode ini, dan periode ketiga terakhir di luar kandungan C kritis ketika tingkat berkurang. Kandungan C kritis biasanya berada pada kisaran 0,2% hingga 0,5%.
Namun, pemanasan individu dengan kondisi tiupan yang identik menunjukkan ireproduksibilitas yang luas. Dua pukulan berurutan dengan input dan parameter proses yang identik dapat menunjukkan perilaku yang sangat berbeda, dengan beberapa pukulan menunjukkan slopping (emulsi logam-terak-gas mendidih di atas mulut konverter) atau terak kering dan meludah (mengakibatkan pembentukan tombak dan mulut) . Ketidakterproduksian jauh lebih umum pada hari-hari awal proses BOS, ketika peniupan bawah gas pengadukan belum dimasukkan. Penggunaan skrap yang lebih sedikit sebagai pendingin juga dapat menghasilkan lebih banyak reproduktifitas dan penurunan slopping.
Setelah mempelajari beberapa toko BOS, telah ditunjukkan bahwa laju dekarburisasi puncak berbanding lurus dengan laju hembusan O2. Hal ini juga telah ditunjukkan selama peniupan dalam konverter ukuran laboratorium, bahwa efek peningkatan laju penghembusan O2 dan penurunan ketinggian tombak pada laju dekarburisasi puncak adalah serupa.
Selama percobaan pada konverter pilot di MEFOS (sebuah lembaga penelitian di Swedia), telah ditunjukkan bahwa ada variasi konsentrasi di sepanjang ketinggian konverter tiup atas. Hal ini menunjukkan bahwa hembusan atas tidak mencampur mandi logam dengan baik meskipun ada momentum yang sangat besar di pancaran atas. Namun, perbedaan ini menghilang dengan meniupkan sejumlah kecil gas inert dari bawah.
Telah diketahui dengan baik bahwa terak dalam proses BOS mengandung sebagian besar logam dalam bentuk tetesan dalam fase terak. Jumlahnya bervariasi selama pukulan, yang tertinggi selama bagian tengah pukulan. Perkiraan bervariasi dalam kisaran 10% hingga 25%. Tetesan ini cukup halus, sebagian besar kurang dari 1 mm hingga 2 mm. Jumlah tetesan dalam emulsi turun menjelang akhir pukulan. Tetesan biasanya dalam keadaan pemurnian yang jauh lebih maju dibandingkan dengan rendaman logam curah.
Ada emulsi terak-logam-gas selama sebagian besar pukulan. Sekitar sepertiga pukulan, ketinggian emulsi melebihi sekitar 2 m, sehingga menenggelamkan ujung tombak dan meredam suara pancaran supersonik. Kadang-kadang, emulsi dapat mengisi seluruh tungku, mendidih di atas mulut (slopping). Menjelang akhir pukulan di luar C kritis di bak mandi, emulsi runtuh menunjukkan bahwa emulsi adalah sementara yang membutuhkan pembangkitan gas terus menerus untuk kelangsungan hidupnya.
Sebagaimana dinyatakan, C, Mn, dan P dioksidasi secara simultan dengan Si di bagian awal pukulan, berlawanan dengan harapan bahwa reaksi Si lebih disukai daripada reaksi lain berdasarkan komposisi rendaman logam curah. Reaksi Mn dan P dapat dijelaskan sampai batas tertentu oleh fakta aktivitas di terak. Reaksi C tidak dapat dijelaskan, kecuali seseorang menggunakan hipotesis bahwa komposisi logam curah tidak berlaku di lokasi reaksi.
Ada pembalikan Mn dan P selama bagian tengah pukulan (Gbr 3a). Ini juga tercermin dalam jalur terak (Gbr 2b). Namun, jelas bahwa pembalikan berkorelasi dengan kandungan FeO dalam terak. Pelarutan CaO berlanjut hampir sampai akhir meskipun kapur ditambahkan di awal atau di awal pukulan. C menentukan dinamika keseluruhan proses dan reaksi ini berlangsung dengan penuh semangat. Gambar 3a menunjukkan perubahan komposisi lelehan selama pukulan.
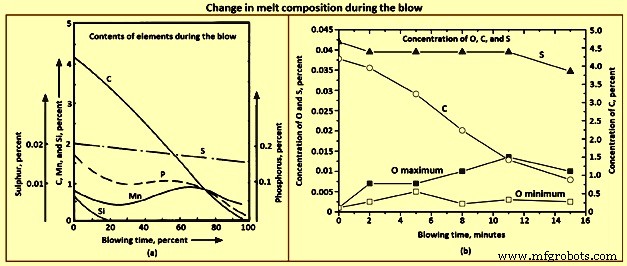
Gbr 3 Perubahan komposisi lelehan selama pukulan
Dinamika proses BOS bergantung pada reaksi C yang berlangsung dengan giat. Dinamika lengkap dapat dibagi menjadi beberapa situs. Reaksi lain dapat dipahami pada kerangka ini. O2 jet yang hampir murni, molekul mencapai permukaan mandi secara langsung tanpa penghalang perpindahan massa yang cukup besar. Ketika sebuah molekul menyerang, ia dapat melakukan salah satu hal berikut.
Molekul O2 bereaksi dengan C di lokasi tumbukan. Reaksi dapat berupa [C] + 1/2{O2} ={CO}, dan [C] + {O2} ={CO2}. Ini dapat larut dalam logam sebagai [O]. Ini kemudian dapat melakukan perjalanan di tempat lain dan bereaksi dengan elemen teroksidasi lainnya seperti O2 =2[O]. Beberapa di antaranya dapat bereaksi dengan Fe dalam bak menghasilkan FeO sesuai persamaan Fe + 1/2{O2} =(FeO). FeO dapat melakukan perjalanan ke fase terak dan bereaksi dengan logam di tempat lain. Masing-masing dari ini mengarah pada reaksi pemurnian yang terjadi di kemungkinan lokasi yang berbeda di konverter, yang mengarah ke, pada pencampuran, pemurnian mandi secara keseluruhan. Situs-situs yang berbeda ini ditunjukkan secara skematis pada Gambar 4.
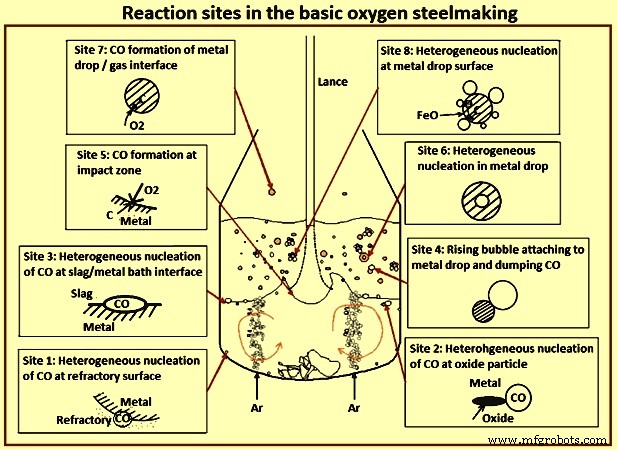
Gbr 4 Tempat reaksi dalam pembuatan baja oksigen dasar
Harus diingat bahwa reaksi C-O bersifat heterogen. Setidaknya ada satu langkah perpindahan massa yang dapat membatasi laju. C harus berdifusi dalam logam ke antarmuka. Transfer O2 dalam fase gas, O2 terlarut dalam fase logam, atau FeO dalam fase terak juga dapat terlibat tergantung pada sumber O2 untuk reaksi. O2 terlarut dapat melakukan perjalanan ke bagian lain di dalam mandi logam dan bereaksi dengan C terlarut untuk melepaskan CO ke pori-pori berisi gas di refraktori (situs 1). CO juga dapat terbentuk pada partikel padat yang mengambang di bak logam dengan nukleasi heterogen (situs 2). Nukleasi heterogen juga dapat terjadi pada lapisan terak / antarmuka penangas logam (situs 3). Nukleasi homogen di dalam bath sangat tidak mungkin kecuali jika supersaturasi CO sangat tinggi. Seperti dijelaskan sebelumnya, reaksi CO dapat langsung terjadi di lokasi tumbukan (situs 5). Beberapa FeO yang terbentuk di atau dekat lokasi tumbukan dapat masuk ke bawah permukaan penangas logam dan berjalan di sepanjang antarmuka terak / logam, bereaksi dengan C menghasilkan antarmuka teremulsi (seperti pada situs 3). Namun, sebagian besar FeO yang terbentuk mungkin berpindah ke fase terak.
Ini sekarang memberikan beberapa kemungkinan. Pada antarmuka antara terak dan rendaman logam, reaksi dapat berlangsung seperti yang dijelaskan sebelumnya (situs 3), O2 sekarang berasal dari fase terak dan C dari logam. Seperti dijelaskan sebelumnya, fase terak mengandung sejumlah besar tetesan logam, yang terus menerus dihasilkan oleh momentum pancaran di lokasi tumbukan. Oleh karena itu, FeO dalam terak dapat bereaksi dengan tetesan ini melalui mekanisme yang berbeda seperti (i) gelembung CO dapat nukleasi secara heterogen pada antarmuka (situs 8), (ii) CO dapat ditransfer ke gelembung yang lewat yang bersentuhan dengan droplet (situs 4), dan (iii) gelembung CO dapat bernukleasi secara homogen di dalam tetesan, jika super saturasi sangat tinggi (situs 6). Jika beberapa tetesan logam dilemparkan ke papan bebas, ia dapat bereaksi langsung dengan O2 atau CO2 dalam gas (situs 7).
Meskipun semua situs ini dapat aktif selama pukulan sampai tingkat tertentu, ada kebutuhan untuk mengidentifikasi mekanisme dominan yang menentukan dinamika keseluruhan. Kontribusi dari masing-masing situs ini dapat dievaluasi berdasarkan pengamatan. Fakta bahwa rendaman menunjukkan gradien konsentrasi tanpa adanya injeksi gas bawah, yang menghilang dengan sedikitnya 1% dari gas inert yang dihembuskan dari bawah dibandingkan dengan aliran gas atas, mekanisme di situs 1 dan situs 2 dapat didiskon karena tidak penting.
Suhu di permukaan di zona tumbukan diperkirakan di atas 2.120 derajat C. Oleh karena itu, laju reaksi kimia diperkirakan akan sangat tinggi. Area situs dampak relatif kecil dan tingkat kedatangan O2 sangat tinggi. Namun, zat terlarut perlu berdifusi ke antarmuka dan panas harus masuk ke logam. Logam segar dibawa ke antarmuka yang tersapu ke luar oleh kecepatan permukaan yang besar. Dalam keadaan ini, dapat diperkirakan bahwa permukaan tumbukan kekurangan zat terlarut yang meninggalkan lapisan Fe yang bereaksi dengan O2. Pada akhirnya dapat masuk akal untuk mengasumsikan bahwa lapisan logam dari komposisi logam curah seluruhnya teroksidasi, oksida fase terkondensasi dipindahkan ke lapisan terak. Ketika kandungan C sekitar 5% (20 sampai 25 mol %), perkiraan ini berarti bahwa sekitar 25% dari O2 yang dipasok dikonsumsi untuk C (CO dan CO2) di situs ini. Kontribusinya diperkirakan sekitar 40% berdasarkan perhitungan dengan asumsi perpindahan massa sisi logam tidak menjadi pengendali laju. Pada suatu waktu, itu dianggap sebagai mekanisme utama (zona panas atau teori zona dampak). Lapisan logam yang mengalir keluar di situs ini juga bisa jenuh dengan O2 seperti yang disebutkan sebelumnya.
Reaksi dalam emulsi tampaknya mengandung situs utama untuk reaksi (situs 4, 6 dan 8). Tetesan dalam emulsi memiliki luas permukaan spesifik yang sangat besar. Dengan adanya FeO dalam jumlah yang wajar dalam terak, semua reaksi pemurnian dalam tetesan dapat berlangsung dalam hitungan puluhan detik, bukan menit. Tetesan 3 mm logam yang mengandung 4,5 % C dapat berkembang sekitar 3.000 kali volume CO2. Ini saat lolos melalui terak kental mengemulsi itu. Interaksi kompleks dari pembentukan emulsi, generasi tetesan, waktu tinggal tetesan, dll., Oleh karena itu, berkontribusi besar pada dinamika keseluruhan. Reaksi tetesan yang bereaksi dengan fase gas secara langsung penting terutama dalam beberapa menit pertama pukulan ketika lapisan terak yang lengkap belum terbentuk.
Pandangan komprehensif pada keseluruhan dinamika proses ini memerlukan latar belakang pancaran gas supersonik, interaksinya dengan rendaman logam / terak, generasi tetesan dan waktu tinggalnya, pelarutan CaO, dan pencampuran rendaman, dll.
Sebuah jet gas-in-gas entrains gas ambien di pinggirannya. Lapisan terganggu mencapai sumbu jet beberapa diameter nosel hilir (daerah inti potensial) di luar mana aliran menjadi berkembang penuh dengan profil kecepatan radial yang serupa. Kecepatan aksial berbanding terbalik dengan jarak untuk menjaga kekekalan momentum. Biasanya, pancaran mengembang pada sudut setengah kerucut sekitar 10 derajat hingga 12 derajat, jika gas sekitar memiliki kerapatan yang sama dengan gas pancaran. Jika ambien lebih ringan, ekspansinya lebih kecil karena efek massa.
Dalam jet supersonik, faktor kompresibilitas mempengaruhi ekspansi jet. Telah ditunjukkan bahwa pancaran tidak banyak mengembang sampai kecepatan aksial melambat ke kecepatan sonik (inti supersonik). Setelah itu pancaran mengembang sebagai pancaran subsonik seperti yang ditunjukkan pada Gambar 5. Studi terbaru CFD (dinamika fluida komputasi) dari pancaran O2 ke dalam konverter BOS telah menunjukkan bahwa kecepatan aksial hampir konstan untuk jarak sekitar 1 m dan suhu gas pada sumbu tetap di sekitar -170 derajat C di wilayah ini. Setelah itu suhu meningkat terus karena entrainment gas panas. Oleh karena itu, tombak O2 dioperasikan pada jumlah Mach keluar sekitar dua sehingga dapat dijaga pada jarak tertentu dan masih menghasilkan interaksi jet / logam yang baik.
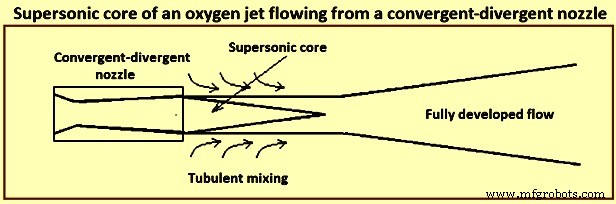
Gbr 5 Inti supersonik dari pancaran oksigen yang mengalir dari nozzle konvergen-divergen
Dapat dicatat bahwa jika pancaran O2 terendam dalam atmosfer CO seperti pada konverter BOS, konsentrasi O2 dapat turun secara substansial.
Ketika pancaran kecepatan tinggi mengenai permukaan logam, sebuah kawah terbentuk, ujung-ujungnya sangat tidak stabil karena kecepatan tinggi pancaran yang dibelokkan, mengeluarkan tetesan logam. Pada nilai yang cukup tinggi jet menjadi re-entrant, di mana beberapa tetesan dilemparkan ke dalam jet itu sendiri yang mengarah ke kawah yang sangat tidak stabil berosilasi dan berputar. In the presence of a slag layer these droplets are trapped by the slag leading to droplet-in-slag emulsion.
The crater depth can be calculated by performing a momentum balance at the stagnation point at the centre of the crater. In further studies with a constant based on the experiments with various liquids and gases at room temperature and quantitatively studying the emulsification phenomena with the help of a 2-dimension, two phase model of mercury and glycerol, it has been found, as expected, that the droplets in the emulsion are increased with gas flow rate and varies inversely with stand-off distance of the lance tip from the liquid surface (lance height). While experimenting with a 3-dimension model of water to determine the droplet generation rate with a top layer representing slag, it has been found that there are two regions, one at a lower flow rate where the rate increases nonlinearly with flow rate and the second where the rate varies almost linearly with the flow rate. The Weber number has been used to characterize the flow phenomena. Droplet generation rate (kg/second) is correlated experimentally as a function of the blow number. It has been shown that simultaneous bottom gas injection can increase droplet generation especially when they are nearly coaxial with the top jet. The presence of slag phase can change the rate of generation substantially.
In a supersonic jet, say of Mach 2, the exit gas temperature is around -100 deg C. Thereafter, it entrains lower density converter gas. The temperature, velocity, and composition of the gas change as the jet strikes the bath. Hence this correlation has large uncertainties, because of which usefulness of the correlation in the BOS model is less than adequate. Since there is no other correlation, one normally uses the above correlation for generation of droplets and tunes it as needed.
The reaction rates also depend on the droplet sizes. Several studies have obtained emulsion samples from the working converters or laboratory hot models. These studies have found in general the sizes to be in the range of 0.05 mm to 3 mm. In a study experimenting with pig iron and O2, there were large chunks of liquids thrown out, which normally spend negligible quantity of time in the emulsion. Though these approximations and correlations are clearly inadequate, most models use these for lack of better correlations.
One of the studies found large quantities of metallic droplets in the foamy slag formed during high P iron refining. Another study made similar observations by collecting samples ejected through the tap hole in a 230 t converter and analyzing them. Several other studies have also made similar observation.
As mentioned earlier, the droplets are in various states of advanced refining, some of them being almost completely refined, though the bath still had considerable quantity of C. The fraction of metal in the emulsion has been estimated to be large, being almost 25 % of the bath weight. This corresponds to a surface area of around 40,000 square metres (sqm) if one assumes an average size of 1 mm for the droplets. It has been proposed in one of the studies that refining in the converter takes place primarily in the emulsion phase, the bath seeing refining by dilution from droplets falling back (emulsion theory). Emulsion in the converters refers to a slag-metal-gas system. One can visualize it as slag-gas foam in which metal droplets are distributed.
It has been also reported that several of the droplets display high O2 super-saturation and this has postulated that the finer droplets can have been generated by homogeneous nucleation of CO droplet bursting. Some droplets show evidences of being attached to gas bubbles and some are even hollow. There have been several experiments with magnetically levitated and freely falling droplets reacting with oxidizing gases. The results of these experiments are interesting. When the C content is high, one can see reactions taking place at the surface, as evidenced by CO burning. As the C content comes down, small droplets are thrown out indicating sub-surface nucleation. Further lower in C content, the droplets sometimes burst, indicating O2 super-saturation and nucleation deep within the droplet. Super-saturation to the extent of around 5 MPa (for equilibrium CO) had been reported at the time of droplet bursting.
In one of the studies, the residence time of the droplets in a converter has been measured by radioactive gold isotope tracer technique. The maximum residence time of droplets which are in advanced state of decarburization has been estimated to be around 2 minutes. Residence time calculated on the basis of free fall is of the order of a few seconds even while considering the slag to be emulsified to a much greater height. The high residence time hence needs an explanation.
Several experiments using X-rays for visualization of a single Fe-C droplet reacting in molten oxidizing slags have shown that the droplet gets buoyed up to the surface as soon as decarburization starts, and stays at the surface till the CO bubbling subsides. Further, it has been shown that the droplet residence time is dependent on bubble formation which keeps the droplet afloat.
There are two views on how the CO formation keeps the droplet buoyant. One of the studies has formulated a bloated droplet theory wherein CO forms homogeneously inside the droplet and this hollow droplet has a low apparent density, due to which it remains afloat. The other view is that the bubbles form heterogeneously at the droplet / slag interface and as long as the bubbles stay attached to the droplet they keep it afloat. The visual evidences from X-ray fluoroscopic studies cannot clearly distinguish between these two. The fact that there does not seem to be a nucleation barrier during vigorous deoxidation as evidenced by copious evolution of bubbles suggests interface nucleation.
At high C concentrations when C mass transfer within the drop is not rate controlling, the highest CO super-saturation is to be seen at the droplet surface. Hence, it can be expected that for the nucleation to take place heterogeneously at the surface, the bubble is to spend some time at the interface before detaching. Since there can be several bubbles attached, the droplet remains buoyed. As C falls to low values, nucleation at the interface becomes sporadic, and in periods when there is no bubble attached, O2 dissolves into the metal and diffuses in. Hence, the highest super-saturation region moves inward, first to sub-surface and then to deep inside the droplet. One can thus see sub-surface nucleation initially throwing out small droplets and then deep inside. These homogeneous nucleation events are probably sporadic, with a stochastic nature.
Simultaneously, the apparent density of the droplet with no or few bubbles is now high and it falls down into the metal bath. The critical C content when the droplet falls down depends on droplet size, the oxidizing potential of the slag (and the rate of mass transfer of FeO), and the sporadic nucleation event either at the surface or inside the droplet. Empirical work to correctly predict the critical C content is lacking. Evidence from levitated droplet experiments also point towards these series of events, though the stirring due to the electro-magnetic field makes the condition different from that in the converter especially with respect to mass transfer within the droplet.
In the context of converter, the droplet surface is continuously disturbed by the bubbles. This has two counteracting effects. Part of the droplet surface is covered by the gas bubble and is not available for mass transfer from the slag to the droplet. The droplet surface is also vigorously stirred by the formation and detachment of bubbles, enhancing mass transfer locally. Several indirect estimations have been made. In one of the studies, indirect estimation of mass transfer coefficient has been made for FeO in slag for P transfer rate in high temperature single droplet experiments, and the values obtained are between (10)−5 metres per second (m/s) and (10)−4 m/s . Another study estimated similar values. Proper experimental studies, both in cold and hot models, are necessary to get reasonable correlations in terms of dimensionless variables.
Though the slag is very well stirred in the converter due to the gas jet and a large quantity of gas passing through it, the metal bath in top blown converters is comparatively poorly mixed. Measurement of mixing time (t95 which is the time to get 95 % homogeneity) in top blown converter can be as high as 150 seconds (s) to 180 s, as compared with 10 s to 20 s in bottom blown OBM converters. This has consequence on the reaction dynamics, since the metal droplets are removed from the top layer and the refined droplets from the emulsion fall back at the top. Since much of the heat is also released in the slag, the slag and the droplets falling back are also hotter. There can also be composition and temperature stratification due to the scrap at the bottom slowly dissolving into the liquid metal.
High mixing times also correspond to high irreproducibility in mixing times, leading to irreproducible blow behaviour in the absence of bottom blowing. For example, a large eddy of liquid metal containing higher C from the bottom being brought to the surface of the metal bath can suddenly increase the rate of decarburization leading to instabilities. Hence, inert gas injection from the bottom of the converters to bring down the mixing time has become the standard practice.
Since the rate of bottom gas injection and the position of the porous elements through which the gas is introduced have a bearing on the reaction dynamics, it is necessary to quantify the mixing behaviour for quantitative predictions of composition and temperature evolution. A single average t95 value is inadequate for incorporation into a comprehensive model of the converter, since two different mixing curves can give the similar t90 (time to get 90 % homogeneity) and different t95 values. The compromise can hence be a two parameter model, based on estimation of two mixing times (t90 and t95). One can then idealize the metal bath as consisting of two stirred tank reactors (STR), exchanging metal continuously. The bottom part sees only scrap melting and the top part sees all other phenomena explained earlier. The two parameters of this model, ratio of reactor sizes and the metal exchange rate can then be fitted to the mixing times of the converter under various conditions of operation.
Formation of slag and dissolution of fluxes
Fluxes (lime and calcined dolomite) which are charged early in the blow dissolve with the developing oxides to form a liquid slag. The rate of dissolution of these fluxes strongly affects the slag-metal reactions occuring during the blow. At the beginning of the blow, the lance height above the bath is kept high which causes an initial slag rich in SiO2 and FeO. During this period large quantities of fluxes are charged in the converter. The lance is then lowered and the slag starts to foam at around one third of the blow due to the reduction of FeO in the slag in conjunction with CO formation. As the blow progresses, the CaO dissolves in the slag, and the active slag weight increases. After the blow has progressed around three fourth of the time, the FeO content in the slag increases because of a decrease in the rate of decarburization.
During the blow, the temperature of the liquid steel gradually increases from around 1,350 deg C to 1.650 deg C at turndown of the converter, and the slag temperature is around 50 deg C higher than that of the liquid steel. The slag at turndown can contain regions of undissolved lime mixed with the liquid slag, since the dissolution of lime is limited by the presence of dicalcium silicate (2CaO.SiO2) coating, which is solid at steelmaking temperatures and prevents rapid dissolution. The presence of MgO in the flux weakens this coating. Hence, earlier charging of MgO speeds up slag formation due to quicker solution of lime.
The converter needs to maintain a good fluid slag of high basicity (high CaO content) so that the large quantity of CO generated can be handled, and P can be removed efficiently. Hence, the converter operator tries to achieve a CaO / SiO2 ratio in excess of 3.0 in the final slag.
Fig 6a shows the liquidus contours in a CaO-SiO2-FeO ternary diagram. It is clearly seen that a CaO / SiO2 ratio which can be achieved in this system at 1,350 deg C, i.e. at the beginning of a blow this ratio is limited to around 1.6 to 1.7. Marginal improvement can take place with MgO additions (Fig 6b) and some Al2O3 coming from the carry over slag. In the final slag also at 1,650 deg C with 25 % to 30 % FeO, the maximum CaO / SiO2 remain less than 3.0. This is also borne out by the slag analyses which frequently show un-dissolved lime. Apart from the issue of solubility of CaO in the converter slags, the lime particles get passivated in the presence of highly siliceous slags. Since the CaO concentration is the highest at the surface of a dissolving lime particle, di-calcium silicate forms here. This compound is not only highly refractory but it forms an adherent layer retarding further dissolution.
A lime particle remaining undissolved for long at the high temperatures also sinters and becomes less reactive. One way of breaking the adherent layer is to have high FeO content in the slag. This is the reason for the practice of raised lance blowing in the first few minutes of the blow, when the FeO is built up to 25 % to 35 % or higher. Though the effect on solubility of CaO is marginal (Fig 6), this facilitates breaking of the adherent di-calcium silicate layer permitting further dissolution.
Additives like fluorspar (CaF2) can bring about this effect much more efficiently, though this is not an acceptable plant practice in recent times for various reasons. Fig 6 shows phase diagrams with Fig 6a showing liquidus isotherms of CaO-SiO2-FeO system and Fig 6b showing tffect of MgO addition on the liquidus.
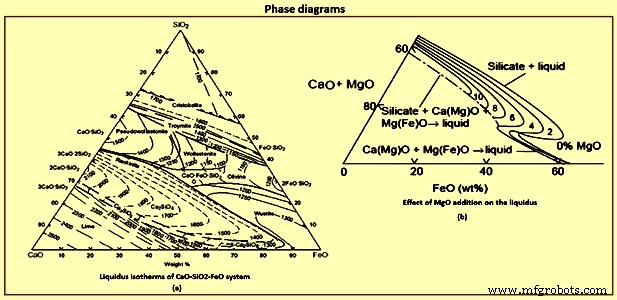
Fig 6 Phase diagrams
Process flow and reaction dynamics
The contents of the converter can be divided into several important regions such as (i) the metal bath, which itself can be divided into the bottom and top part between which there is exchange of metal, (ii) the O2 jet and the impact region, and (iii) the slag region which mostly is in the form of a slag-metal-gas emulsion. There are three distinct regimes in the blow. The initial part is characterized by a bare metal bath covered with islands of solid lime and some slag carried over from the previous heat. Jet of O2 hits the metal bath and does two primary things. First, it oxidizes almost an entire layer of the metal giving CO, SiO2, MnO, P2O5 and lots of FeO. Not all O2 is consumed in this location, and the gas above hence can contain high ratio of CO2 / CO and some O2 as seen in exhaust gas analysis. The jet also throws droplets into the gas phase, which after free flight fall back. Since the gas is oxidizing, the droplets get refined during the flight. At the surface of the droplets, the order of reactions is dictated by the thermodynamics.
For each of the solutes, reaction involves mass transfer steps such as mass transfer of CO2 / O2 in the gas phase and of the solutes in the liquid phase. The interfacial chemical reactions are expected to be very fast at this temperature. The order of the reactions can be achieved by solving the mass transfer equations along with free energy minimization for the interface reactions competing for O2. The order is normally Si and Mn followed by C and P. Since the time of flight is typically of the order of a second or lower, the droplets fall back probably completing only part of the Si reaction. Smaller the droplet, further the refining proceeds because of the larger specific surface area. Reaction at the rest of the surface of the metal bath is small because of the smaller surface area compared to that of the droplets.
The mass transfer in the gas phase can easily be calculated by Ranz-Marshall type correlations. At this initial phase of the process droplets are high in solutes, and the gas phase mass transfer is expected to be rate controlling. The small droplets can be considered as rigid and one can assume pure diffusion of solutes inside the droplets. When the droplets fall back, the condensed phase oxide products in the droplets remain at the top of the bath, and on combining with the oxides from the impact site and the fluxes added start forming a liquid slag. As mentioned earlier, good quantity of FeO is formed at the impact site, and hence liquid slag formation is easy. After sometime, there is a liquid slag layer covering the metal bath. Increasingly more and more droplets are thrown to the slag. The droplets ejected into the gas phase now have to pass through the slag phase before reaching the metal bath. Further refining hence takes place in the slag.
Initially when the slag layer is thin and the droplets are high enough in Si and Mn, the droplets fall through before the C reaction starts, that is, with no gas evolution, especially for larger droplets. Smaller droplets high in C can however start to decarburize early releasing CO, and slowly emulsifying the slag. This early phase is characterized by a low flame at the mouth, since CO formation is comparatively low. Once the Si in the metal bath falls down to some extent, the desiliconization progresses considerably, before the droplet has fallen down. C reaction starts and the droplet stays now buoyed in the emulsion till its C content reaches the critical C content as explained earlier. In the slag phase, the rate is expected to be controlled by slag phase mass transfer of FeO, as long as C in the droplet remains high enough. Once a critical C is reached in the droplet, bubbling slows down and then ceases, and the droplet falls down. The critical C is largely determined by the FeO content in the bath. Quickly the emulsion builds up and the second phase of reactions in the emulsion starts. The flame at the converter mouth becomes large. The lance tip gets dipped into the emulsion.
In the second phase almost all of the droplets are ejected into the emulsion, and the gas phase reactions become unimportant. It is to be noted that the residence times of the quiescent droplets in the slag are only of the order of a few seconds unless decarburization reaction starts. Hence, for maximizing the refining, the operator is to quickly reach a stage where the decarburization reaction starts before the droplets fall back. One way to accelerate the reactions is to keep the FeO content in the slag high. Another reason why FeO is to be increased as early as possible is to have a fluid slag by the time decarburization rate reaches its highest value, since the large quantity of gasses are to quickly escape from the slag. Else, the emulsion height gets build up uncontrollably leading to overflow, and slopping.
The FeO content in the slag is a balance between its generation at the point of impact and its consumption by the droplets in the emulsion. The FeO generation is probably weakly dependent of the lance height, whereas a high lance leads to less droplet generation due to lower force with which the jet strikes the metal bath, and vice versa. Hence a raised lance practice, called the soft blow, leads to quick increase in the FeO content in the slag. This facilitates CaO dissolution and formation of a fluid slag. The initial soft blow, normally 3 min to 4 min, is the normal plant practice.
At an optimum moment, the lance is lowered to induce high rates of reactions. Droplet generation rates are high, the bath is already desiliconized, and hence the droplets undergo vigorous decarburization till C goes to low values before falling back. During this period of peak decarburization rates, hence a large part of the metal bath remains in the emulsion as droplets. These droplets have spent different times in the emulsion and hence are in different stages of refinement. The degree of refinement also depends on the droplet size. The droplet are hence characterized by two variables namely the time it has been formed (and hence its age) and the size of the droplet. The droplet starts to fall back when a characteristic C content is reached, which depends on its size, the slag FeO, and the temperature. During this last phase of the droplets, the O2 potential at the interface is also high and hence P is also removed if other conditions are favourable. Falling droplets result in apparent refinement of the top of the metal bath, which on mixing lead to refinement of the rest of the bath. Since the time for refinement of a droplet can be of the order of 0.5 min to 2 min, one sees drop in C, Mn and P in the bulk metal sample even if Si in the sample is still of considerable quantity (Fig 3a).
The overall rate of reaction, to some extent, is self-correcting. If the number of droplets in the emulsion come down decreasing the rate, the level of the metal bath increases leading to lower effective lance distance, which in turn causes droplet generation to increase. This is one of the reasons for the near constant decarburization rate during middle part of the blow. It is however is to be noted that the C content of droplets entering into the emulsion keeps falling down, and hence their residence time. The operator is required to correspondingly increase the droplet generation rate by progressively lowering the lance. Fig 7a indicates the lance height variation during a typical blow.
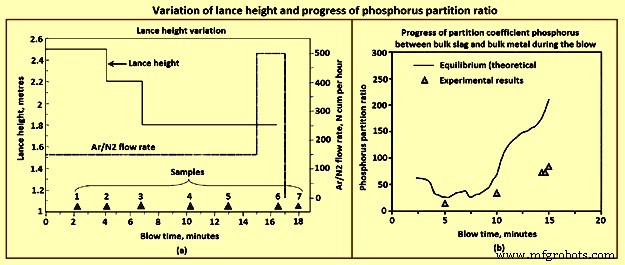
Fig 7 Variation of lance height and progress of phosphorus partition ratio
As the bath becomes low in C in the final phase of the blow, the rate now gets limited by C diffusion within the droplet even as it enters the emulsion. The CO generation is low and is not able to keep the droplets floated. The residence time drops down to a few seconds, and hence number of droplets in the emulsion comes down even though the lance height has been brought down to the lowest level permissible for lance health. The emulsion dies down. At this time there is falling rates of decarburization and fast buildup of FeO in the slag. Since the rates are low, the FeO content and the O2 dissolved in steel increase much beyond what is dictated by C-O equilibrium. Hence, at this period, the operator raises the argon stirring rate, increasing thereby the droplet generation rate without adding extra O2. This helps to some extent.
Phosphorus removal is sometimes an issue in the BOS process and can result in re-blows, especially when the input P in the hot metal is high (around 0.2 %). Though the conditions are normally favourable in the final slag with high FeO and high basicity, the converter operator can land in adverse situation if the slag regime is not carefully managed throughout the blow. The thermodynamics of P is well known. The reaction is written either in terms of molecular species or in the ionic form. The reaction is 2P + 5/2 O2(g) =P2O5(l), P + 5/4 O2(g) + 3/2 (O)2− =(PO4)3−. In the former case one writes an equilibrium constant, and expresses the Raoultian activity coefficient as a function of slag composition. If one adopts an ionic form of the equation, one instead writes an equation for a phosphate capacity of slag and correlates the phosphate capacity to the slag composition empirically. Both these approaches are conceptually similar. The partial pressures of P and O2 can easily be converted to percent dissolved in metal or activity of FeO in slag with known thermodynamic data. The slag data as a function of composition either as Raoultian activity coefficient or as phosphate capacity have been empirically determined in several studies. The progress of partition coefficient for P between bulk slag and bulk metal can be calculated when the slag analysis during the blow is known.
In the initial period of the blow, the bath C is quite high and also contains Si. Hence at the slag / metal interface, the O2 potential remains low. Therefore, very high rate of dephosphorization at the bulk metal / slag interface is not expected. The metal droplets, on the other hand, get highly refined in a matter of 1 min to 2 min, and before returning to the metal bath, have high O2 potential at its interface. Further the partition coefficient at this time is high since FeO content is high due to soft blow, temperature is low, although with some CaO yet to dissolve. The number of droplets in the emulsion is also very large. Hence, the dephosphorization rate is very high which can be seen in Fig 3a. Towards the end of the blow again, the conditions in the slag are favourable with high FeO and high basicity, though now the temperature has risen substantially. The rate of phosphorus removal however is not very high in this period, since the number of droplets is not very high, surface area is quite small and hence all reactions are slow.
Vigorous Ar stirring is helpful at this time of the blow, and for some time after the O2 flow is stopped, though to a limited extent. It is in the middle part of the blow the operator has the highest opportunity for efficient overall dephosphorization. After the soft blow when the lance is lowered progressively for effecting high rates of decarburization, FeO content in the slag drops considerably and remains low till the emulsion starts collapsing. The slag becomes comparatively ‘dry.’ The partition coefficient becomes adverse, and one can easily get P reversal to the metal. Lower is the FeO level, higher is the reversal. This reversal increases the load on the last part of the blow where the rates of reactions are anyway low as explained earlier.
Hence, close control of the FeO content during the middle part of the blow is necessary if the operator is required to make low P steel. Premature lowering of the lance in each stage can lead to very low FeO content (less than 12 % to 15 %). FeO content is determined by the balance between droplet generation rate (consumption rate) and the FeO generation rate. However, it is to be noted that very low FeO in the slag also lowers the decarbonization rate. Very high FeO on the other hand leads to sloppy conditions.
Higher levels of FeO content can be achieved by modifying the lance practice. The lance height for the intermediate levels can be kept slightly higher than the normal. The operator can also slightly delay lowering of the lance, taking care to see that it does not lead to uncontrolled emulsion build up. The operator can also achieve this by distributed ore addition during this period.
The chemistry of steelmaking in BOS converter is summarized here. From the thermodynamics of the O2 steelmaking process, it can be seen that, at the beginning, the O2 blown onto the HM preferably reacts with the dissolved Si, forming SiO2 which floats on the surface of the metal. From kinetics, it is expected that a part of the O2 blown reacts with the dissolved C and Fe atoms. The formation of CO gas occurs instantaneously on process ignition. Calcined lime is added to neutralize the acid slag, which initially includes a liquid mixture of FexOy and SiO2. Several chemical reactions take place in the BOS converter. The main reactions are dissolution of O2 into the metal from O2 gas, decarburization through dissolved O2, and oxidation of Fe, [Si], [Mn], [P], [V] and [Ti]. Solid or liquid oxides are formed as reaction products during blowing, and they are bound with the lime which is added at the start of blowing to form a liquid slag in the converter. Due to intensive CO gas formation, droplets of liquid metal are introduced into the slag, which tends to foam. Hence, the slag in the converter during O2 blowing is actually an emulsion of liquid slag and metal droplets, foaming because of the influence of gas bubbles. The emulsion is also a favourable site for reactions. For example, a considerable fraction of C oxidation can occur in the metal droplets in the emulsion although the majority takes place in the impact zone of the O2 jets. The rest of the O2 is used to burn Fe into FexOy. During blowing, O2 penetrates the metal droplets and can react with the CO gas. The total slag-gas system behaves as foam and rises quickly to the cone of the converter. Hence, the O2 inflow and the reaction rates have to be adjusted so that foam is not spilled from the converter. Slopping frequently occurs even though the inner volume of the converter is almost nine times larger than the volume of the inactive metal and slag bath.