Produksi DRI dengan Gas Coke Oven sebagai Reduktor
Produksi DRI dengan Gas Coke Oven sebagai Reduktor
Direct Reduced Iron (DRI) secara teknis didefinisikan sebagai bijih besi yang telah direduksi menjadi logam tanpa melelehkannya. Proses produksi DRI adalah proses di mana besi logam padat diperoleh langsung dari bijih besi padat tanpa menundukkan bijih atau logam untuk fusi. Proses produksi DRI utama adalah berbasis gas atau berbasis batubara. Bahan pakan dalam proses DRI adalah bijih besi berukuran 10 hingga 30 mm atau pelet bijih besi yang diproduksi di pabrik pelet bijih besi.
Di pembangkit berbasis gas, reaktor, tempat reaksi reduksi berlangsung, adalah tungku poros. Tungku poros bekerja pada prinsip arus berlawanan di mana bahan umpan bantalan besi bergerak ke bawah di tungku dengan gravitasi dan dikurangi oleh gas pereduksi yang mengalir ke atas. Dalam proses berbasis gas, bahan bakar gas digunakan. Bahan bakar ini harus mampu mereformasi atau retak untuk menghasilkan campuran gas H2 (hidrogen) dan CO (karbon monoksida). Gas alam yang mengandung metana tinggi merupakan gas yang paling umum digunakan. Gas alam direformasi untuk diperkaya dengan campuran H2 dan CO dan campuran gas yang diperkaya dan direformasi ini dipanaskan terlebih dahulu.
Gas oven kokas (COG) merupakan produk sampingan dari proses pembuatan kokas pada produk sampingan baterai oven kokas. COG terdiri dari campuran kompleks berbagai gas. Komposisinya biasanya terdiri dari 55% H2, 6% CO, 25% CH4 (metana), ditambah persentase kecil CO2 (Karbon dioksida), H2O (kelembaban), tar berat, hidrokarbon yang mudah menguap, dan pengotor belerang. Ini juga mengandung beberapa N2 (nitrogen). COG biasanya digunakan sebagai bahan bakar gas untuk berbagai aplikasi pemanasan di dalam pabrik baja, dan kelebihan COG digunakan untuk menghasilkan uap, tenaga listrik atau dibakar. Penggunaan COG untuk produksi DRI selalu menarik, tetapi tantangannya adalah mengubah metana menjadi CO dan H2 serta pembersihan tar dan hidrokarbon yang mudah menguap. Setiap ton kokas yang dihasilkan menghasilkan COG yang cukup untuk menghasilkan satu ton DRI.
Produksi DRI dalam rute baja terintegrasi berdasarkan pemanfaatan COG produk sampingan yang tersedia adalah fenomena yang sangat baru. Penggunaan COG memiliki beberapa keuntungan baik dari segi ekonomi maupun lingkungan.
Menggunakan kelebihan COG sebagai gas pereduksi untuk menghasilkan DRI memulihkan 97% energi yang tersedia dibandingkan dengan memulihkan 30% hingga 40% dengan membakar COG untuk menghasilkan tenaga listrik.
Dua proses utama yaitu Midrex dan HYL telah mengadopsi dua pendekatan berbeda untuk penggunaan COG untuk produksi DRI berbasis gas.
Proses Midrex
Midrex pertama kali mulai melihat metode penggunaan gas oven kokas dalam reduksi langsung pada tahun 1970-an. Masalah utama yang terlibat adalah adanya hidrokarbon tak jenuh, tar dan cairan, serta tingkat tinggi senyawa metana dan sulfur dalam gas mentah. Studi paling awal berfokus pada pengkondisian gas untuk digunakan sebagai komponen gas umpan untuk reformer Midrex.
Berdasarkan perkembangan teknologi oksidasi parsial, Midrex memutuskan untuk menyelidiki kemungkinan penggunaan teknologi ini untuk mengkondisikan COG sebagai gas pereduksi yang sesuai untuk proses MXCOL. Namun kelemahan dari oksidasi parsial selalu menjadi penambahan uap yang diperlukan ke reaktan untuk mengurangi pembentukan jelaga yang dihasilkan dari reaksi oksigen.
Sekitar pertengahan 2011, Praxair telah mengembangkan teknologi oksidasi parsial yang mereka tawarkan secara komersial.
Teknologi oksidasi parsial ini memiliki fitur unik yang menawarkan potensi untuk melakukan oksidasi parsial hidrokarbon, bebas jelaga, tanpa injeksi uap. Ketika teknologi ini digabungkan dengan ruang reaksi termal yang diperluas di mana aliran gas oven kokas yang dipanaskan sebelumnya disuntikkan, produk gas yang meninggalkan reaktor cocok untuk digunakan sebagai sumber pereduksi untuk reduksi langsung. Semua pengelompokan peralatan ini, termasuk kompresi gas, pemanasan awal, dan reaksi membentuk sistem reaktor termal (TRS).
TRS menggunakan teknologi Praxair untuk oksidasi parsial COG. Sistem ini menghasilkan pancaran oksigen berkecepatan ekstrim panas dan insitu yang dengan cepat memasukkan COG yang telah dipanaskan sebelumnya, mereformasi metana, memecah hidrokarbon berat, dan menghancurkan tar tanpa memerlukan katalis apa pun. Syngas yang direformasi kemudian keluar dari TRS dan diumpankan ke tungku poros untuk menghasilkan DRI.
Selama uji skala percontohan, lebih dari 96% penghancuran tar dicapai bersama dengan reformasi metana yang dioptimalkan. Selain itu, kondisi pengoperasian dikembangkan untuk menghindari pembentukan jelaga bersih.
Hasil uji skala pilot ini ditingkatkan di pabrik demonstrasi skala 1/20 di fasilitas penelitian ekstensif Midrex di Charlotte, NC. Hasil khas yang diperoleh dari operasi uji demo COG diberikan di Tab 1.
Tab 1 Hasil umum yang diperoleh dari operasi uji demo COG
Saluran Masuk TRS Analisis Gas COG Saluran Keluar TRS Analisis Syngas
CO 4 hingga 6 % 22 hingga 28 %
CO2 1 hingga 3 % 1 hingga 3 %
H2 55 hingga 65 % 55 hingga 65 %
H2O 0,4 hingga 0,8% 0,5 hingga 2,5 %
CH4 20 hingga 30 % 0,5 hingga 3,0 %
N2 2 hingga 4 % 3 hingga 8 %
BTX 0,3 hingga 2,0 % 0,0 %
HHC 0,2 hingga 0,6 % 0,0 %
Jelaga ? 0,01 mg/N cum
Dua opsi TRS utama yang tersedia untuk penggunaan COG adalah dengan flow sheet MXCOL dan dengan reformer Midrex.
- Penggunaan COG dengan proses MXCOL – Proses MXCOL awalnya dikembangkan untuk memanfaatkan syngas dari gasifier batubara untuk menghasilkan DRI. Proses ini menggabungkan penggunaan sistem penghilangan CO2, biasanya menggunakan teknologi penghilangan berbasis larutan amina, dan pemanas proses tabung radiasi untuk memanaskan gas pereduksi dan syngas sebelum hiruk pikuk tungku. Lembar aliran khas proses MXCOL dengan penggunaan COG diberikan pada Gambar 1.
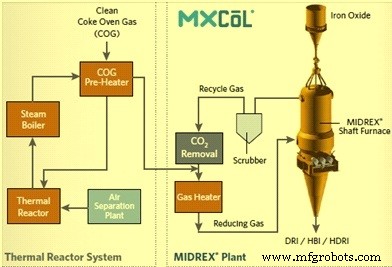
Gbr1 Flow sheet khas proses MXCOL dengan penggunaan COG
- Penggunaan COG dengan reformer Midrex – TRS dapat melengkapi pasokan syngas yang ada yang dibutuhkan untuk setiap ton DRI. Penambahan COG langsung di lembar aliran proses Midrex standar dapat dilakukan dengan menambahkan gas ke zona transisi atau gas hiruk pikuk seperti yang ditunjukkan pada 1 dari Gambar 2. Dalam melakukan ini, suhu zona pertemuan, dan aktivitas reformasi zona bertemu menghancurkan dan mengubah tar dan hidrokarbon volatil di COG. Namun masalahnya adalah ketika laju penambahan COG mencapai titik kritis, pembangkit mencapai kondisi bahan bakar ekspor di mana lebih banyak bahan bakar gas yang dihasilkan daripada yang dapat dikonsumsi oleh reformer. COG juga dapat digunakan sebagai pembakar sebagai bahan bakar pembakar (2), tetapi efek bersihnya adalah bahwa COG yang dipasok ke pembakar akan menghasilkan ekspor bahan bakar gas dalam jumlah besar. Penambahan COG pada bustle gas (3) atau feed gas (4) dapat dilakukan dengan menggunakan TRS yang juga memerlukan penambahan sistem CO2 removal untuk mengontrol ekspor bahan bakar yang akan dihasilkan dari penambahan COG.
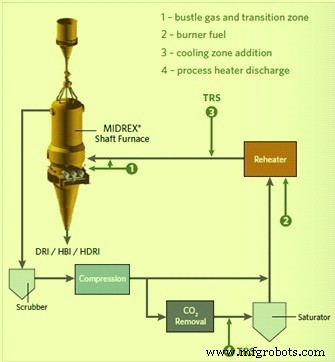
Gbr 2 Flow sheet tipikal yang menunjukkan penggunaan COG (TRS) dengan reformer Midrex
Proses HYL
Sesuai dengan status teknologi saat ini, proses HYL ZR (Self reforming) dikembangkan untuk memungkinkan reduksi bijih besi di tungku poros tanpa peralatan reformasi gas eksternal. Skema proses ini memiliki kemampuan untuk menghasilkan DRI karbon tinggi, yang memungkinkan produsen memperoleh manfaat karbon yang maksimal dalam proses pembuatan baja. Aliansi baru-baru ini antara Tenova HYL, Techint dan Danieli membawa nama merek baru untuk proses ini. Prosesnya sekarang dikenal sebagai 'Energiron'.
Di daerah di mana gas alam mahal atau ketersediaannya rendah, prosesnya dapat dengan mudah dikonfigurasi untuk beroperasi menggunakan COG, syngas dari gasifier batubara dan sumber hidrokarbon lainnya.
Karena semua gas pereduksi dihasilkan di bagian reduksi, dengan memanfaatkan efek katalitik besi logam di dalam tungku poros, efisiensi reduksi optimum dicapai dalam proses ini. Dengan demikian, reformer gas pereduksi eksternal tidak diperlukan.
Skema dasar Energiron memungkinkan pemanfaatan langsung gas alam. Tentu saja, pembangkit Energiron juga dapat menggunakan peralatan reformasi uap-gas alam konvensional, yang telah lama menjadi ciri proses tersebut. Agen pereduksi lainnya seperti COG, hidrogen, gas dari gasifikasi batubara, kokas hewan peliharaan dan bahan bakar fosil serupa, antara lain, juga merupakan sumber potensial untuk mengurangi gas tergantung pada situasi dan ketersediaan tertentu. Flowsheet prosesnya ada di Gambar 3.
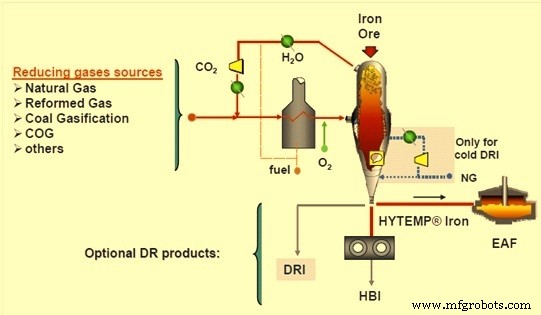
Gbr 3 Flow sheet proses HYL-ZR
Selain itu, pabrik DR dapat dirancang untuk menghasilkan DRI karbon tinggi, DRI panas, yang dapat langsung diumpankan ke EAF yang berdekatan melalui Sistem HYTEMP atau ke unit briket untuk menghasilkan HBI atau kombinasi produk ini.
Efisiensi energi keseluruhan dari proses ZR dioptimalkan dengan integrasi suhu reduksi tinggi (di atas 1050 derajat C), reformasi 'in-situ' di dalam tungku poros, serta dengan pemanfaatan peralatan termal yang lebih rendah di pabrik. Oleh karena itu, produk mengambil sebagian besar energi yang dipasok ke proses, dengan kehilangan energi minimum ke lingkungan.
Proses ini memungkinkan pencapaian tingkat karbon hingga 5,5%, karena potensi karburasi gas yang lebih baik di dalam reaktor dan sebagian besar karbon hadir dalam bentuk besi karbida.
Meskipun komposisi kimia COG dan gas alam (NG) cukup berbeda, COG dapat digunakan langsung pada proses ZR dengan konfigurasi dasar yang sama, sebenarnya komposisi gas yang masuk ke reaktor sangat mirip seperti yang ditunjukkan pada Gambar 4 untuk keduanya. ZR berdasarkan gas alam atau ZR berdasarkan COG. Persyaratan umum COG untuk produksi DRI, berdasarkan proses HYL-ZR adalah sekitar 9,5 GJ/t DRI, untuk DRI 94% metalisasi dan 4% karbon.
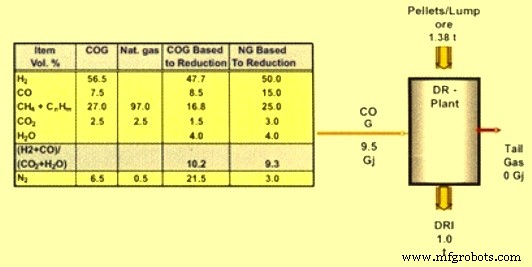
Gbr 4 Perbandingan reduksi berbasis COG dan NG