Refraktori untuk Tungku Oksigen Dasar
Refraktori untuk Tungku Oksigen Dasar
Tujuan utama dalam pengembangan refraktori untuk tungku oksigen dasar (BOF) adalah untuk mendapatkan umur pakai dari lapisan keausan sehingga diperoleh ketersediaan BOF yang maksimal. Umur lapisan yang lebih lama tidak hanya menghasilkan biaya refraktori yang lebih rendah tetapi juga memungkinkan produktivitas yang lebih tinggi melalui peningkatan ketersediaan tungku.
Berikut ini adalah persyaratan dasar dari refraktori BOF.
- Ketahanan spalling termal
- Ketahanan korosi
- Ketahanan abrasi
- Resistensi oksidasi
- Modulus pecah panas
BOF biasanya dilapisi dengan lapisan permanen dan di atasnya ada lapisan aus. Ketebalan lapisan permanen dapat bervariasi dari 100 mm hingga 120 mm dan terbuat dari lapisan permanen chrome-magnesit yang diberikan pada ketinggian penuh BOF.
Refraktori yang tersedia untuk digunakan dalam lapisan keausan BOF berkisar dari tar atau dolomit atau magnesia (MgO), chrome magnesit, atau magnesium chrome hingga refraktori canggih yang dibuat dengan ikatan resin, logam, grafit, dan disinter dan/atau leburan magnesia yang dapat dengan kemurnian 99%. Batu bata dirancang dengan kombinasi sifat fisik penting untuk menahan suhu tinggi dan kondisi/lingkungan yang berubah dengan cepat selama siklus panas BOF. Keseimbangan sifat yang berbeda seperti kekuatan panas, ketahanan oksidasi, dan ketahanan terak diperlukan dari refraktori BOF untuk kinerja yang baik.
Ketika proses pembuatan baja BOF diperkenalkan pada 1950-an, konverter dilapisi dengan batu bata tar dolomit dan batu bata dolomit yang dibakar dengan stabil. Refraktori ini kemudian digantikan oleh batu bata dolomit bakar semi stabil dan batu bata ikat tar dan batu bata bakar yang terbuat dari klinker dolomit magnesia sintetis. Chrome magnesit, atau refraktori magnesium krom digunakan untuk melapisi beberapa BOF. Batu bata magnesia bakar dengan kemurnian tinggi juga digunakan di beberapa lapisan BOF. Selama akhir 1970-an, batu bata magnesia-karbon dengan ketahanan korosi dan spalling dikembangkan dan dengan cepat digunakan untuk pelapis BOF. Batu bata ini memanfaatkan ketahanan magnesia terhadap terak kebasaan tinggi yang korosif dan konduktivitas termal yang tinggi dan keterbasahan grafit (karbon) yang rendah. Saat ini praktik penggunaan refraktori magnesia-karbon untuk lapisan BOF telah menjadi sangat umum.
Stabilitas magnesia – bata karbon dapat ditingkatkan dengan mencegah oksidasi grafit dan dengan meningkatkan ketahanan korosi klinker magnesia. Oksidasi grafit dicegah dengan menambahkan logam yang mudah teroksidasi seperti aluminium dan magnesium – aluminium, karbida seperti silikon karbida (SiC) dan boron karbida (B4C), dan borida seperti kalsium borida (CaB6). Penggunaan grafit kemurnian tinggi juga mencegah oksidasi. Ketahanan korosi magnesia ditingkatkan dengan menaikkan tingkat kemurnian klinker magnesia baik dengan menggunakan magnesia elektro-fusi atau magnesia air laut. Hal ini juga ditingkatkan dengan mengoptimalkan distribusi ukuran partikel klinker magnesia. Bata karbon magnesium yang ditambahkan zirkon (ZrSiO4) untuk pengurangan tegangan termal dalam layanan juga telah dikembangkan.
Magnesia kemurnian tinggi modern diproduksi dengan proses yang terkontrol dengan baik. Sumber utama magnesia adalah air asin sering dari sumur dalam atau dari air laut. Magnesium hidroksida, Mg(OH)2, diendapkan dari sumber-sumber ini melalui reaksi dengan dolomit atau batu kapur yang dikalsinasi. Bubur magnesium hidroksida yang dihasilkan disaring untuk meningkatkan kandungan padatannya. Filter cake kemudian diumpankan langsung ke rotary kiln untuk menghasilkan magnesium grade refraktori. Saat ini filter cake dikalsinasi pada suhu sekitar 900 derajat C sampai 1000 derajat C dalam beberapa tungku perapian untuk mengubah magnesium hidroksida menjadi magnesium aktif. Magnesia yang dikalsinasi ini kemudian dibriket atau dibuat pelet untuk dibakar menjadi magnesium kelas refraktori yang padat, biasanya dalam tungku pembakaran poros pada suhu sekitar 2000 derajat C. Produk akhirnya adalah magnesia yang disinter. Fused magnesia diproduksi dengan melelehkan magnesia tingkat refraktori atau prekursor magnesia lainnya dalam tungku busur listrik. Massa cair kemudian dikeluarkan dari tungku, didinginkan, dan dipecah untuk digunakan dalam pembuatan refraktori. Pengotor dalam magnesia dikendalikan oleh komposisi sumber asli magnesia (air asin atau air laut), komposisi dolomit atau batu kapur yang dikalsinasi, dan teknik pengolahannya. Secara khusus persentase dan rasio CaO dan SiO2 dikendalikan secara efektif, dan B2O3 dipertahankan pada tingkat yang sangat rendah. Magnesia refraktori bermutu tinggi yang dihasilkan digunakan untuk produksi refraktori magnesia.
Faktor yang berbeda bertanggung jawab atas keausan lapisan BOF di zona BOF yang berbeda. Oleh karena itu pelapisan zona BOF dipraktekkan di mana berbagai jenis batu bata karbon magnesia atau batu bata lainnya dipasang di zona BOF yang berbeda untuk memastikan keseimbangan keausan dan melaluinya perpanjangan umur lapisan BOF tercapai. .Pelapisan zona khas BOF ditunjukkan pada Gambar 1.
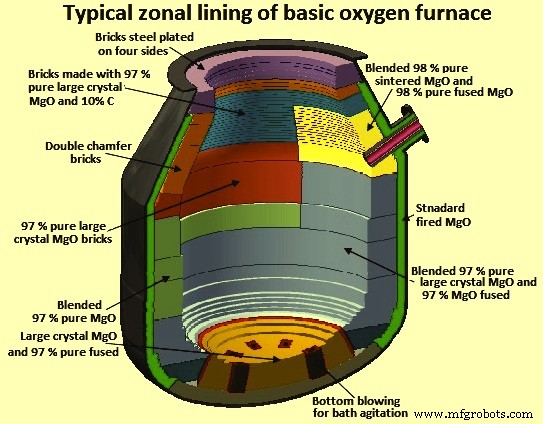
Gbr 1 Lapisan zona khas BOF
Untuk mengoptimalkan desain lapisan keausan, penting untuk mengembangkan lapisan yang seimbang, yaitu lapisan di mana kualitas dan ketebalan refraktori yang berbeda ditetapkan ke berbagai zona lapisan konverter berdasarkan studi yang cermat terhadap pola keausan. Dalam lapisan yang seimbang, refraktori dikategorikan sedemikian rupa sehingga segmen tertentu dari lapisan yang diketahui menerima lebih sedikit keausan diberikan kualitas yang lebih rendah atau ketebalan refraktori yang lebih sedikit, sedangkan refraktori dengan ketahanan aus yang lebih besar dan umumnya dengan biaya yang lebih tinggi dicadangkan untuk segmen tersebut. tungku yang akan mengalami keausan paling parah. Kondisi keausan dan refraktori yang diusulkan di zona BOF yang berbeda untuk lapisan zona diberikan pada Tab 1 di bawah ini.
Tab 1 Kondisi keausan zona konverter dan refraktori yang diusulkan |
Zona konverter | Kondisi keausan | Refraktori yang diusulkan |
Kerucut | 1) Atmosfer pengoksidasi | 1) Magnesia kualitas standar – bata karbon yang mengandung anti oksidan |
2) Penyalahgunaan mekanis | 2) Bata magnesia berikat pitch |
3) Tekanan termo mekanis | 3) Resin terikat bata karbon rendah dengan anti oksidan |
4) Suhu tinggi |
Trunnion | 1) Atmosfer pengoksidasi | 1) Magnesia kualitas premium – bata karbon yang mengandung anti oksidan |
2) Korosi terak | 2) Magnesia kualitas premium – bata karbon yang mengandung MgO dan anti oksidan yang menyatu |
3) Terak dan erosi logam | 3) Magnesia kualitas premium kekuatan tinggi – batu bata karbon |
Bantalan pengisi daya | 1) Dampak mekanis | 1) Pitch batu bata magnesia yang dibakar diresapi |
2) Abrasi dari skrap dan logam panas | 2) Magnesia kekuatan tinggi kualitas standar – bata karbon yang mengandung anti oksidan |
3) Batu bata magnesia karbon rendah berkekuatan tinggi yang mengandung anti oksidan |
Ketuk pad | 1) Erosi terak | 1) Magnesia kualitas premium – bata karbon yang mengandung anti oksidan |
2) Suhu tinggi | 2) Batu bata magnesia karbon rendah berkekuatan tinggi dengan aditif logam |
3) Erosi mekanis | 3) Magnesia kualitas standar – bata karbon yang mengandung anti oksidan |
Slagline penolakan | 1) Korosi terak yang parah | 1) Magnesia kualitas premium – bata karbon yang mengandung anti oksidan |
2) Suhu tinggi | 2) Magnesia kualitas premium – batu bata karbon yang mengandung magnesium dan anti oksidan yang menyatu |
Bawah dan Stadion (bawah bejana berpengaduk) | 1) Erosi dengan memindahkan logam, terak, dan gas | 1) Magnesia kualitas standar kekuatan tinggi – bata karbon yang mengandung anti oksidan |
2) Tegangan termo-mekanis sebagai akibat pemuaian | 2) Magnesia – bata karbon tanpa aditif logam yang dicirikan oleh ekspansi termal yang rendah dan konduktivitas termal yang baik |
3) Tegangan internal sebagai akibat gradien termal antara tuyer berpendingin gas dan lapisan sekitarnya | 3) Pitch batu bata magnesia terbakar yang diresapi |
Dengan berbagai macam kualitas batu bata yang tersedia, ada berbagai macam biaya refraktori. Bata yang lebih mahal harganya bisa mencapai enam kali lipat dari bata dolomit berikat tar/pitch konvensional. Dengan peningkatan desain lapisan, lebih banyak refraktori dengan biaya lebih tinggi digunakan dalam lapisan BOF akhir-akhir ini. Namun penggunaan refraktori berbiaya tinggi harus membenarkan ekonomi tekno keseluruhan dari toko BOF.
Misalnya, ketika biaya pelapisan meningkat sebesar 25% di toko BOF yang rata-rata 4000 panas, umur pelapis perlu meningkat menjadi 5000 panas agar biaya refraktori dapat dipertahankan. Namun, di toko-toko di mana ketersediaan tungku diperlukan untuk produktivitas, peningkatan umur lapisan yang lebih rendah dan biaya refraktori yang lebih tinggi dapat dibenarkan jika ketersediaan tungku lebih besar selama periode kebutuhan produksi tinggi.
Karena desain lapisan ditingkatkan untuk mengoptimalkan kinerja dan biaya, pengaruh variabel operasi pada keausan lapisan penting untuk diketahui. Dengan informasi ini, kemungkinan untuk mengontrol parameter-parameter yang mempengaruhi keausan lapisan secara merugikan dan keuntungan ekonomis dari peningkatan biaya operasi untuk memperpanjang umur lapisan dapat dievaluasi dengan lebih baik. Secara umum, praktik yang meningkatkan kontrol proses, seperti sub-tombak, bermanfaat bagi kehidupan lapisan. Selain itu, umur lapisan dibantu dengan pengisian kapur dolomit untuk menyediakan terak MgO, meminimalkan tingkat pengisian fluorspar, mengendalikan penambahan fluks dan praktik blowing untuk menghasilkan kadar FeO yang rendah dalam terak. Praktik ini perlu dioptimalkan untuk menghasilkan kinerja lapisan yang paling hemat biaya.
Bahkan ketika banyak kondisi operasi ditingkatkan, desain lapisan dioptimalkan untuk keausan yang seimbang, dan teknologi bata terbaik digunakan, keausan tidak terjadi secara seragam, dan, umumnya, praktik perawatan yang melibatkan penembakan refraktori dan pelapisan dengan terak digunakan untuk memperpanjang kehidupan lapisan.