Proses Pelet dan Pelet Bijih Besi
Proses Pelet dan Pelet Bijih Besi
Pelletisasi bijih besi dimulai pada 1950-an untuk memfasilitasi pemanfaatan konsentrat bijih besi yang digiling halus dalam produksi baja. Untuk pelletizing bijih besi terdapat dua jenis proses utama yaitu, proses straight traveling grate (STG) dan proses grate kiln (GK). Dalam proses STG, unggun pelet stasioner diangkut pada jeruji berjalan tanpa akhir melalui zona pengeringan, oksidasi, sintering, dan pendinginan. Dalam proses GK, pengeringan dan sebagian besar oksidasi dilakukan dalam unggun pelet stasioner yang diangkut pada jeruji keliling. Setelah itu, pelet dimuat dalam rotary kiln untuk sintering dan kemudian pada pendingin melingkar untuk pendinginan.
Proses pembuatan pelet dibahas dalam artikel di bawah tautan http://www.ispatguru.com/iron-ore-pellets-and-pelletizing-processes/.
Pelet dapat berupa pelet asam atau fluks.
- Pelet asam – Kebasaan pelet asam biasanya kurang dari 0,1. Kekuatan pelet yang ditembakkan, sampai tingkat tertentu, disebabkan oleh jembatan hematit dari struktur polikristalin. Pelet ini biasanya memiliki volume besar pori-pori terbuka. Gas reduksi dengan cepat menembus pori-pori ini ke inti pelet dan secara bersamaan menyerang struktur di banyak tempat. Ini menghasilkan perubahan struktural awal yang dimulai pada suhu rendah di seluruh volume pelet.
- Pelet fluks – Ini juga dikenal sebagai pelet dasar. Kebasaan pelet fluks lebih besar dari 0,1 dan dapat bervariasi. Kebasaan pelet basa normal berkisar antara 0,1 hingga 0,6 dan memiliki persentase CaO yang rendah. Selama pembakaran pelet ini, fase terak kaca yang terdiri dari SiO2, CaO, dan Fe2O3 dengan persentase yang bervariasi. Karena penambahan fluks yang meningkat, ada pembentukan beberapa terak dan karena itu, ada ikatan terak sampai batas tertentu dengan kristal bijih besi. Pelet kebasaan tinggi memiliki tingkat kebasaan lebih besar dari 0,6. Pelet ini mengandung tingkat CaO yang lebih tinggi. Pelet ini tidak hanya memiliki fase glassy yang terutama terdiri dari SiO2, CaO, dan Fe2O3, tetapi juga kalsium ferit (CaO.Fe2O3). Selama pembakaran pelet ini, ketersediaan CaO sangat mendukung pertumbuhan kristal hematit. Pelet ini biasanya memiliki kekuatan mekanik yang tinggi setelah penembakan pelet.
Pabrik pelet biasanya terintegrasi dengan pabrik benefisiasi bijih besi. Dalam hal mereka tidak terintegrasi maka bijih besi pekat dalam bentuk bubur biasanya dipompa ke pabrik pelet oleh pipa bubur. Pabrik pelet yang berbahan dasar bijih besi halus sangat jarang dan tidak terlalu ekonomis. Keseluruhan proses pelletizing dapat dibagi menjadi dua segmen utama sub proses yaitu (i) segmen sub proses dingin dan (ii) segmen sub proses panas.
Segmen proses dingin memiliki sub proses berikut.
- Tangki lumpur untuk penyimpanan bubur bijih besi pekat dari pabrik benefisiasi. Ukuran partikel bijih besi dalam bubur bijih kurang dari 45 mikro meter untuk sekitar 80% partikel.
- Bahan aditif (seperti dolomit, batu kapur, kapur atau olivin dll. tergantung pada kualitas pelet yang akan diproduksi) ditambahkan ke bubur.
- Sebagian besar air dikeluarkan dari bubur dengan menggunakan filter. Kadar air bijih besi setelah disaring adalah sekitar 9%.
- Mixer digunakan untuk penambahan bahan pengikat (bentonit atau bahan pengikat organik) untuk mendapatkan kekuatan mekanik yang cukup dari pelet hijau
- Cakram pelet atau drum baling digunakan untuk produksi pelet hijau. Cakram pelet lebih populer untuk produksi pelet hijau.
- Saringan getar biasanya digunakan untuk memisahkan fraksi pelet hijau yang berbeda. Pelet berukuran kecil didaur ulang kembali ke proses, sedangkan pelet berukuran besar dihancurkan sebelum didaur ulang.
- Selebihnya berupa pellet berukuran (8 mm hingga 16 mm) yang diangkut dengan conveyor ke proses pengeringan di segmen proses panas.
Segmen proses panas memiliki sub proses berikut.
- Tungku pengering untuk menghilangkan sebagian besar kandungan air dari pelet hijau dengan aliran udara panas melalui tempat tidur. Pelet kering kemudian memasuki tungku pelet.
- Pelet kering dibakar (1250 derajat C hingga 1300 derajat C) di tungku pelet untuk mengubah pelet hijau menjadi produk akhir
- Pendinginan pelet panas yang mengeras hingga sekitar 200 derajat C dilakukan dalam pendingin dengan meniupkan udara dingin.
Sebagian besar sub proses di atas dioperasikan hari ini dengan bantuan teknik kontrol menggunakan kontrol otomatis. Beberapa sub proses sangat bergantung pada berfungsinya sub proses sebelumnya dengan baik. Misalnya, jika ukuran partikel terlalu besar, atau butiran terlalu kering, atau pengeringan tidak berjalan, maka tidak ada pelet yang dapat dihasilkan. Situasi yang kurang kritis adalah ketika beberapa segmen bekerja kurang optimal. Sebagai contoh Jika proses penambahan binder pencampuran binder tidak merata, maka proses pembentukan green pellet akan terganggu. Oleh karena itu, proses pelletizing bijih besi merupakan rangkaian dari beberapa sub-proses yang sangat bergantung pada kinerja masing-masing.
Penambahan bahan pengikat pada bijih memiliki dua tujuan utama, yaitu (i) membuat bijih plastis sehingga dapat membentuk inti biji yang tumbuh menjadi pelet yang terbentuk dengan baik, dan (ii) untuk menyatukan pelet selama penanganan, pengeringan dan pemanasan awal atau sampai cukup diperkuat dengan pengerasan selama pembakaran. Pengikat yang optimal harus menghasilkan pelet berkualitas tinggi dengan biaya minimum dan memasukkan kontaminan sesedikit mungkin. Pengikat juga harus tidak beracun, mudah ditangani dan tidak memerlukan sistem pemberian makan yang canggih. Penambahan kecil bentonit meningkatkan ikatan dengan pembentukan ikatan keramik dan dengan pemadatan partikel yang lebih besar selama penggulungan bola hijau.
Kualitas pelet hijau tergantung pada parameter input seperti mineralogi, kimia dan granulometri bijih halus, parameter balling seperti ukuran partikel pakan, jumlah air yang ditambahkan selama peletisasi, kecepatan putar cakram, sudut kemiringan dasar cakram dan waktu tinggal material di dalam cakram. dll.
Dalam pelet hijau, air memainkan peran penting. Ini menggumpalkan bijih dan melakukan fungsi mengikat cairan. Aglomerat basah dapat berada di sejumlah keadaan yang berbeda tergantung pada jumlah air yang ada. Ini ditunjukkan secara skematis pada Gambar. 1. Tingkat pengisian cairan pengikat atau saturasi cairan menggambarkan bagian dari volume pori yang diisi dengan cairan pengikat.
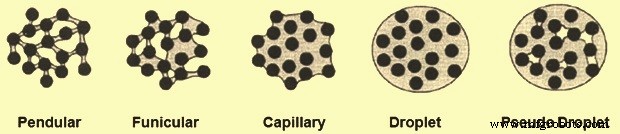
Gbr 1 Tampilan skematis dari keadaan aglomerat basah yang berbeda
Pada saturasi rendah, partikel disatukan oleh jembatan cair (ikatan pendular, keadaan pendular). Dalam keadaan tegang (funicular), baik kapiler berisi cairan dan jembatan cairan hidup berdampingan. Dalam keadaan kapiler, semua kapiler diisi dengan cairan dan permukaan cekung terbentuk di lubang pori karena gaya kapiler.
Keadaan tetesan terjadi ketika aglomerat dipertahankan bersama oleh gaya kohesif cairan. Dalam keadaan pseudo-droplet, rongga yang tidak terisi tetap terperangkap di dalam tetesan. Fitur yang umum adalah
dalam keadaan kapiler dan tetesan, baik bukaan kapiler cekung atau air dangkal bebas, di atas seluruh permukaan luar yang menggumpal diharapkan. Teori kapiler untuk kekuatan aglomerat basah sudah mapan sekarang.
Aditif telah digunakan untuk meningkatkan operasi dan ekonomi dari proses peletisasi. Kapur (CaO) dan kapur terhidrasi [Ca(OH)2] terbukti menjadi aditif yang bermanfaat selama produksi pelet. Sifat pelet hijau dan kering serta dipecat meningkat secara signifikan dengan penambahan kapur atau kapur terhidrasi
Kualitas fisik dan metalurgi pelet produk secara luas tergantung pada kualitas pelet hijau, jenis dan jumlah pengikat, fluks dan aditif yang digunakan, dan parameter indurasi seperti kondisi pembakaran (suhu dan waktu, dll.). Bahan pelet hijau bereaksi bersama, selama pembakaran, untuk membentuk fase dan mikrostruktur yang berbeda dalam pelet produk.
Jenis dan jumlah fase ini, kimia dan distribusinya memainkan peran penting dalam menentukan sifat metalurgi pelet produk selama reduksi dalam proses pembuatan besi berikutnya. Studi pelet hijau dan indurasi magnetit dan bijih besi hematit bermutu tinggi dengan alumina rendah telah dilakukan di berbagai belahan dunia. Namun hasil penelitian tersebut tidak dapat diinterpretasikan secara langsung terhadap bijih besi dengan kandungan alumina (Al2O3) yang lebih tinggi karena perbedaan kimia dan mineralogi. Denda bijih besi dengan kandungan Al2O3 yang relatif tinggi menunjukkan karakteristik pelet yang berbeda.
Adapun pembakaran bijih besi hematit, lebih banyak panas diperlukan untuk disuplai dari sumber eksternal karena tidak adanya reaksi eksotermik oksidasi magnetit berikut.
4FeO + O2 =2Fe2O3
Konsumsi energi yang dibutuhkan untuk produksi pelet dari butiran halus bijih hematit lebih besar daripada yang dibutuhkan untuk membuat butiran butiran halus magnetit. Selain itu, pelet yang dibuat dari bijih hematit memiliki sifat pemanggangan yang buruk dan tidak mencapai kekuatan fisik yang memadai sampai suhu pemanggangan lebih tinggi dari 1300 derajat C. Hal ini diamati bahwa partikel hematit dan struktur pelet mempertahankan bentuk aslinya jika suhu di bawah 1200 derajat. C. Ukuran partikel hematit tidak membesar, atau cacat kisi kristal Fe2O3 dihilangkan sampai suhu lebih tinggi dari 1300 derajat C. Pada suhu tinggi, jembatan penghubung awal terbentuk antara butiran kristal dan rekristalisasi Fe2O3 terjadi. Namun, jika suhu pemanggangan lebih besar dari 1350 derajat C, maka hal itu merugikan karena Fe2O3 terurai menjadi Fe3O4 seperti yang ditunjukkan oleh reaksi berikut dan ini berakibat buruk pada hilangnya kualitas pelet.
6Fe2O3=4Fe3O4+O2
Termodinamika reaksi ini menunjukkan bahwa suhu dekomposisi Fe2O3 meningkat dengan meningkatnya tekanan parsial oksigen. Oleh karena itu suhu pembakaran tinggi yang berlebihan dan tekanan parsial oksigen rendah harus dihindari untuk mencegah dekomposisi Fe2O3. Dengan demikian, perlu untuk mempertahankan suhu pemanggangan yang lebih tinggi untuk pelet hematit serta kisaran suhu pembakaran yang lebih sempit. Hal ini mempersulit pengoperasian peralatan tembak.
Untuk meningkatkan indurasi pelet hematit, baik metode penambahan magnetit dan karbon ditemukan sebagai teknik yang menguntungkan dalam praktik.
Dalam kasus peletisasi bijih magnetit, ketika pelet mulai teroksidasi, cangkang hematit terbentuk sementara inti pelet masih magnetit. Perubahan volume termal pada kedua fase ini menunjukkan bahwa sintering pada fase magnetit dimulai lebih awal (950 derajat C) dibandingkan dengan fase hematit (1100 derajat C). Perbedaan laju sintering antara fase magnetit dan hematit lebih pada sekitar 1100 derajat C. Tingkat sintering meningkat di kedua fase dengan meningkatnya kehalusan dalam konsentrat magnetit. Oleh karena itu, penggilingan yang lebih halus pada bahan mentah mendorong pembentukan struktur dupleks yang tidak diinginkan dengan inti sinter yang lebih berat yang terlepas dari cangkangnya. Pada porositas asli konstan dalam pelet hijau, laju oksidasi menurun karena konsentrat magnetit menjadi lebih halus, karena peningkatan sintering. Namun, dalam balling praktis, bahan baku yang lebih halus memerlukan penggunaan lebih banyak air dalam balling, yang menghasilkan peningkatan porositas pelet hijau. Kedua efek yang berlawanan ini sama rata dan waktu oksidasi menjadi konstan. Dalam kondisi proses industri, perbedaan dalam struktur dupleks masih diharapkan. Ini karena hanya oksidasi parsial yang terjadi sebelum indurasi.
Penambahan kapur (CaO) pada butiran halus bijih besi sedikit menurunkan produktivitas pelet hijau, tetapi meningkatkan ketahanan jatuh dan kuat tekan pelet hijau. Selanjutnya kekuatan pelet berbanding lurus dengan penyusutan yang terjadi selama pembakaran pelet. Dalam kasus pelet fluks, penambahan kapur meningkatkan penyusutan pelet dan karenanya meningkatkan kekuatan pelet. Hal ini disebabkan adanya interaksi antara kapur, silika dan oksida besi membentuk kalsium silikat dan kalsium ferit. Penambahan kapur menghasilkan sintering partikel hematit halus yang didukung oleh ikatan mineral sekunder yang sangat terlokalisasi di dekat lokasi partikel kapur asli. Dengan meningkatnya suhu dan konsentrasi kapur, lebih banyak terak yang terbentuk yang mengkonsolidasikan struktur dan menurunkan porositas yang dapat diakses.
Penggunaan kapur terhidrasi [Ca(OH)2] memiliki pengaruh positif terhadap ketahanan jatuh dan kuat tekan pelet hijau dan kering. Juga terdapat pengaruh yang baik dari Ca(OH)2 pada kekuatan akhir pelet yang dibakar.
Penambahan Ca(OH)2 mengakibatkan penurunan efisiensi bentonit sebagai pengikat dengan mengganti ion natrium yang lebih efisien dengan ion kalsium, mengubahnya menjadi lebih berkalsium dan kurang efisien, yang menyebabkan penurunan sifat pelet. oleh karena itu dalam beberapa kasus tidak diinginkan untuk menambahkan lebih dari satu pengikat pada waktu yang sama selama proses peletisasi karena dapat mengakibatkan penurunan sifat pelet alih-alih peningkatannya. Setelah sejumlah Ca(OH)2 ditambahkan, beberapa peningkatan sifat pelet dicapai yang dapat dikaitkan dengan efek Ca(OH)2 sebagai pengikat selama proses peletisasi. Kinetika reduksi pelet yang mengandung 0,4% bentonit dan 4% Ca(OH)2 yang memiliki sifat fisika-kimia tertinggi, menunjukkan bahwa reduksi pelet ini dikendalikan oleh reaksi kimia antar muka.