Penggunaan Pelet Bijih Besi dalam Beban Blast Furnace
Penggunaan Pelet Bijih Besi pada Beban Blast Furnace
Pelletizing adalah proses yang melibatkan pencampuran partikel halus bijih besi halus berukuran kurang dari 200 mesh dengan aditif seperti bentonit dan kemudian membentuknya menjadi gumpalan oval/bola berdiameter 8-20 mm dengan pelletizer dan mengeraskan bola dengan menembak dengan suatu bahan bakar. Ini adalah proses mengubah butiran bijih besi menjadi 'pelet bijih besi berukuran seragam' yang dapat diisi langsung ke dalam tanur tinggi. Gambar 1 menunjukkan pelet bijih besi.
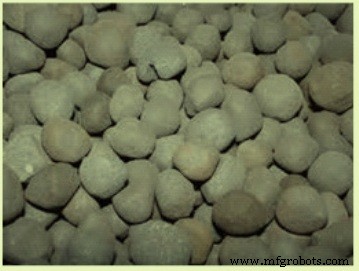
Gbr 1 Pelet bijih besi
Ada beberapa proses/teknologi pelletizing bijih besi yang tersedia. Namun, saat ini proses straight traveling grate (STG) dan grate kiln (GK) merupakan proses yang lebih populer.
Sifat fisik pelet bijih besi diberikan di bawah ini.
• Ukuran – 8-20 mm
• pH (40 gm/L, 20 derajat C; bubur dalam air) – 5,0 – 8,0
• Titik leleh – 1500-1600 derajat C
• Densitas curah – 2,0 -2,2 t/Cum
• Indeks Tumbler (+6,3 mm) – 93-94 %
• Indeks abrasi (-0,5 mm) – 5-6 %
• Kekuatan kompresi (daN/p) – Sekitar 250
• Porositas –> 18%
Analisis kimia pelet bijih besi diberikan di bawah ini.
Nilai BF Nilai DRI
Fe % 63 – 65,5 65 -67.8
SiO2 + Al2O3 % <5 <5
CaO + MgO % Hingga 3 Hingga 0,10
P, maks % 0,05 0,05
S, maks % 0,01 0,01
Dasar, min % 0,5
Disintegrasi (-3,15 mm) % 2
Indeks Pembengkakan % 13-18
Reduksibilitas % 65
Tes standar ISO yang berbeda untuk pelet diberikan di Tab 1
Pengujian standar ISO Tab 1 yang digunakan untuk pelet BF |
Uji standar ISO | Nilai pengukuran | Tujuan |
ISO 4700 /Kekuatan hancur | dan | Kekuatan dingin pelet |
ISO 3271 /Kekuatan jatuh | Pecahan +6,3 mm dan -0,5 mm | Kecenderungan abrasi |
ISO 13930 / Disintegrasi reduksi suhu rendah | Pecahan +6,3, -3,15, dan -0,5 mm | Kecenderungan penurunan suhu rendah |
ISO 4698 /Bengkak bebas | Volume % | Meningkatkan Kecenderungan pembengkakan |
ISO 4695 / Reduksibilitas | Tingkat pengurangan sebesar 40% berkurang | Reduksibilitas |
ISO 7992 / Pengurangan beban | 1. Tingkat pengurangan sebesar 40% berkurang | Reduksibilitas, Pelunakan / perilaku meleleh |
2. Penurunan tekanan pada 80% berkurang |
3. Penyusutan tempat tidur berkurang 80% |
Kualitas pelet dipengaruhi oleh sifat bijih atau konsentrat, gangue terkait, jenis dan jumlah fluks yang ditambahkan. Faktor-faktor ini pada gilirannya menghasilkan variasi sifat fisikokimia dari fase yang hidup bersama dan distribusinya selama indurasi pelet. Oleh karena itu sifat pelet sebagian besar diatur oleh bentuk dan tingkat ikatan yang dicapai antara partikel bijih dan stabilitas fase ikatan ini selama reduksi oksida besi dalam tanur tinggi. Karena pembentukan fasa dan struktur mikro selama indurasi bergantung pada jenis dan jumlah fluks yang ditambahkan, maka ada pengaruh zat fluks dalam hal rasio CaO/SiO2 dan kandungan MgO terhadap kualitas pelet.
Sejarah penggunaan pelet bijih besi di tanur tinggi
Sejarah pelet dimulai pada tahun 1912 ketika A.G. Andersson, seorang Swedia, menemukan metode pembuatan pelet.
Penggunaan komersial pelet, bagaimanapun, dimulai di Amerika Serikat setelah Perang Dunia 2. Berbagai penelitian dilakukan dengan tujuan mengembangkan cadangan taconite yang besar di daerah sekitar Great Lakes. Pada tahun 1943, Dr. Davis, seorang profesor di Universitas Minnesota, Stasiun Percobaan Pertambangan, menemukan metode untuk memproses taconite yang mengandung bijih besi kadar rendah. Prosesnya melibatkan penggilingan taconite untuk menghilangkan gangue dan meningkatkan bijih besi (yaitu, proses benefisiasi bijih). Bijih kadar tinggi yang dihasilkan dalam bentuk partikel halus, sekecil 0,1 mm atau kurang, yang tidak cocok untuk sintering. Masalah ini menyebabkan pengembangan pelet dari partikel halus ini. Pabrik pelet saat ini memainkan peran penting di era ketika cadangan global bijih lump kualitas tinggi menyusut. Pabrik mempromosikan pemekatan bijih kadar rendah menjadi pelet yang ditingkatkan, yang semakin banyak digunakan oleh tanur tinggi dan tanur reduksi langsung.
Pembuatan besi AS secara historis sebagian besar didasarkan pada pelet terutama karena semua bijih besi lokal membutuhkan benefisiasi (up grading) dengan menggilingnya menjadi partikel halus (<0,1 mm) dan mengaglomerasi butiran halus ini menjadi pelet tetapi juga karena pabrik sinter tidak digunakan karena alasan lingkungan.
Pelet bijih besi sekarang menjadi satu-satunya sumber besi terbesar untuk tanur sembur Amerika Utara. Pelet merupakan sekitar 70% dari beban tanur sembur. Awalnya pelet asam (nilai DRI) diproduksi dan digunakan dalam tanur tinggi.
Pada pertengahan 1980-an, sejumlah percobaan pelet dan tanur sembur dilakukan untuk mengevaluasi manfaat pelet fluks dolomit batu kapur. Menjelang akhir dekade, pelet fluks telah mapan sebagai produk utama, terhitung sekitar 30% dari produksi pelet Amerika Utara.
Transisi ke pelet fluks melibatkan banyak perubahan dalam peralatan pabrik (misalnya, pabrik penggilingan fluks, pembakar pra-panas) dan praktik. Setiap pabrik pelet telah menyesuaikan kimia pelet fluks untuk memenuhi operasi tanur tinggi pelanggannya. Hasilnya, ada pabrik pelet yang memproduksi pelet sebanyak empat grade. Di Amerika Utara, pelet telah berubah dari komoditas di awal 1970-an menjadi produk yang dibuat khusus, memenuhi spesifikasi spesifik pelanggan yang paling menuntut pada 1990-an. Pelet fluks Amerika Utara sekarang setara dengan sinter terbaik dalam hal sifat reduksi dan pelunakan lelehan serta lebih unggul dalam hal kekuatan dan kerusakan suhu rendah (LTD/RDI).
Keuntungan pelet
Pelet bijih besi dapat digunakan sebagai pengganti sinter dan lump ore terkalibrasi dalam beban tanur tinggi karena sifat-sifat berikut.
- Bentuk bulat dan pori-pori pelet yang terbuka memberikan permeabilitas yang lebih baik dan seragam sehingga menghasilkan operasi tungku yang lebih lancar. Pellet memiliki ukuran seragam yang umumnya berkisar antara 8 – 20 mm.
- Pelet memiliki kekuatan penghancuran dingin yang sangat tinggi sehingga menghasilkan butiran halus yang dapat diabaikan di gudang penyimpanan.
- Porositas tinggi (lebih besar dari 18%) menghasilkan pengurangan yang lebih cepat
- Kekuatan pelet yang tinggi (sekitar 250 daN/p ) memberikan ketahanan yang baik terhadap disintegrasi selama penurunan beban. Ini memiliki indeks jatuh yang lebih baik jika dibandingkan dengan bijih besi yang dikalibrasi.
- Komposisi kimia yang seragam dibandingkan dengan lump ore terkalibrasi. Tidak adanya LOI adalah keuntungan lain dari pelet.
Indeks pembengkakan pelet adalah Penting properti metalurgi. Pembengkakan menunjukkan perubahan volume pelet selama reduksi. Ekspansi volume pelet selama reduksi menghasilkan kuat tekan pelet yang lebih rendah. Pembengkakan yang tinggi di dalam tungku menyebabkan peningkatan volume palet yang pada gilirannya mengurangi rongga yang terisi. Ini Menghambat aliran gas di tungku dan menghasilkan penurunan tekanan. Hal ini pada gilirannya menyebabkan beban menggantung dan tergelincir di dalam tanur sembur. Penambahan dolomit menguntungkan untuk perbaikan sifat pengembangan pelet. Pembengkakan pelet maksimum yang diizinkan untuk tanur sembur berkisar antara 16% hingga 18%. Pelet asam (pelet DRI) dan pelet bebas MgO menunjukkan pembengkakan yang lebih tinggi.
Pelet fluks dapat diproduksi setara dengan sinter terbaik dalam hal sifat reduksi dan pelunakan lelehan dan lebih unggul dalam hal kekuatan dan kerusakan suhu rendah (LTD/RDI). Pelet terfluks menunjukkan kekuatan yang baik, sifat reduksi yang lebih baik, pembengkakan dan pelunakan pelelehan. Karena sifat-sifat ini, pelet terfluks memberikan kinerja yang lebih baik di tanur tinggi.
Logam dalam beban BF
Sinter, pelet dan bijih lump yang dikalibrasi adalah tiga logam bantalan besi yang biasanya digunakan dalam beban tanur tinggi. Penggunaan ketiga logam dalam beban tanur sembur dapat bervariasi dari nol hingga seratus persen dengan penyesuaian parameter tanur. Ketiga logam ini dapat digunakan dalam kombinasi dua logam atau tiga logam apa pun. Tidak ada formula standar untuk pemilihan logam. Pilihan logam tergantung pada beberapa faktor yang bervariasi dari tanaman ke tanaman. Beberapa faktor yang mempengaruhi pilihan logam diberikan di bawah ini.
- Ketersediaan bahan logam dengan spesifikasi yang benar
- Sifat metalurgi dari bahan logam seperti reducibility, sifat penyusutan termal dan sifat pelunakan
- Biaya relatif bahan logam
- Pengaruh penggunaan logam terhadap biaya produksi logam panas secara keseluruhan
- Kemungkinan penyesuaian berbagai parameter tungku seperti pola distribusi, tingkat bahan bakar, dll.
- Kemungkinan penyesuaian dalam parameter kontrol proses
- Fasilitas tersedia di gudang penyimpanan tungku
- Ketersediaan tanaman sinter penangkaran
- Jenis bijih besi yang tersedia di tambang tawanan atau area dekat tanur sembur
- Masalah yang terkait dengan kelancaran pengoperasian BF tanpa menggantung dan tergelincir
- Masalah terkait lingkungan
Pelet dalam tanur sembur dapat digunakan dari 0% hingga 100%. Tidak ada solusi standar untuk meningkatkan kandungan pelet dalam beban tanur sembur. Setiap lokasi dan setiap tungku akan memiliki masalah berbeda yang perlu diidentifikasi, dianalisis, dan solusi harus ditemukan untuk mencapai jumlah maksimum kandungan pelet yang dapat digunakan dalam beban BF. Tujuannya harus selalu memiliki operasi tanur sembur bebas masalah dengan biaya produksi serendah mungkin untuk logam panas.