Praktik operasi dan Kehidupan Kampanye Tungku Ledakan
Praktik operasi dan Kehidupan Kampanye Tungku Ledakan
Biaya pembangunan kembali atau pelapisan ulang tanur sembur (BF) sangat tinggi. Oleh karena itu, teknik untuk memperpanjang usia kampanye BF adalah penting dan perlu dilakukan dengan sangat aktif.
BF besar biasanya memiliki hasil kampanye yang sedikit lebih tinggi per unit volume. Perbedaan ini karena BF yang lebih besar umumnya memiliki desain yang lebih modern dan terotomatisasi dengan baik. Karena kelangsungan hidup pabrik baja terintegrasi bergantung pada pasokan logam panas (HM) yang berkelanjutan, yang di pabrik dengan sejumlah kecil tungku besar sangat mementingkan masa pakai kampanye yang panjang.
Teknik untuk memperpanjang masa kampanye BF (Gbr 1) termasuk dalam tiga kategori berikut.
- Praktik operasional – Kontrol proses BF memiliki pengaruh besar pada kehidupan kampanye. BF akan dioperasikan tidak hanya untuk memenuhi kebutuhan produksi tetapi juga untuk memaksimalkan umurnya. Oleh karena itu, perlu untuk memodifikasi praktik operasi saat kampanye berlangsung dan sebagai tanggapan terhadap area masalah untuk memaksimalkan masa pakai kampanye.
- Tindakan perbaikan – Setelah keausan atau kerusakan yang memengaruhi masa pakai BF terbukti, teknik perbaikan teknik harus digunakan atau dikembangkan untuk memaksimalkan masa pakai kampanye.
- Desain yang ditingkatkan – Seiring dengan pengembangan material dan peralatan yang lebih baik, ini akan dimasukkan ke dalam pembangunan kembali di masa mendatang untuk memperpanjang masa pakai area kritis BF, yang hemat biaya untuk melakukannya.
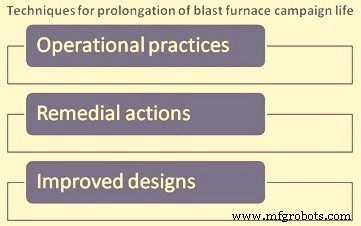
Gbr 1 Teknik untuk memperpanjang masa pakai kampanye tanur sembur
Praktik operasional untuk masa pakai kampanye yang lebih baik dibahas dalam artikel ini. Praktik pengoperasian yang memengaruhi masa pakai kampanye BF dijelaskan di bawah.
Produktivitas
Produktivitas BF biasanya dinyatakan dalam ton (t) HM per unit volume BF (cum) per hari. Produktivitas tinggi melibatkan peningkatan throughput material pada tingkat penurunan beban yang lebih tinggi, dengan peningkatan aktivitas perapian untuk menghilangkan jumlah yang lebih besar dari produk cair Stabilitas operasi dipengaruhi ketika BF didorong dengan keras maka penurunan beban kurang mulus dan zona leleh lebih tinggi Ini mempengaruhi keausan dinding BF Peningkatan throughput produk cair mempercepat keausan tungku dan menghasilkan kondisi lubang keran yang lebih sulit.
Produktivitas rendah melibatkan periode volume ledakan panas rendah yang diperpanjang, yang mengakibatkan berkurangnya penetrasi ledakan dan peningkatan aliran gas ke dinding BF, kecuali modifikasi yang sesuai untuk distribusi beban dibuat. Biasanya jeda produksi yang lama memiliki efek merugikan pada kondisi perapian.
Saat mempertimbangkan tingkat produktivitas BF yang telah mencapai masa kampanye yang panjang, jelas bahwa BF ini belum dioperasikan secara maksimal untuk sebagian besar kampanye. Hal yang umum faktor stabil, operasi yang konsisten, dengan praktik yang digunakan untuk memantau dan melindungi dinding dan perapian. Operasi tersebut lebih mudah dicapai pada tingkat produksi di bawah output maksimum. Namun, sulit untuk menentukan nilai universal indeks produktivitas (t/cum/ hari) untuk mencapai hal ini, karena indeks juga dipengaruhi oleh beberapa faktor selain laju penggerak BF. Ini adalah bentuk internal BF, keadaan keausan tahan api, kondisi pengoperasian lokal, dan periode perawatan, dll.
Untuk memaksimalkan masa pakai kampanye, diperlukan strategi agar BF dapat dioperasikan secara stabil dan terkendali. Banyak pembangunan ulang BF melibatkan peningkatan volume dalam, bukan untuk meningkatkan output tetapi untuk memungkinkan pencapaian target produksi pada tingkat produktivitas yang lebih rendah dan karenanya menawarkan potensi operasi yang lebih stabil dan masa pakai kampanye yang lebih lama.
Fakta bahwa penghentian BF yang sering mengurangi produktivitasnya, tetapi masa pakai kampanye juga berkurang karena jumlah operasi stop/start yang berlebihan. Output kampanye per unit volume berkurang secara tidak proporsional dengan persentase waktu henti. Kampanye yang panjang, diukur dengan kriteria ini, paling baik dicapai dengan pengoperasian BF yang berkelanjutan tanpa penghentian yang lama.
Pengurangan produktivitas jangka pendek juga diperlukan untuk menangani area masalah yang diidentifikasi pada BF, untuk melindungi integritas tungku, sehingga menghindari akhir kampanye yang terlalu dini.
Beban
Untuk operasi BF yang stabil pada tingkat produktivitas yang wajar, kokas berkualitas baik diperlukan. Faktanya, kokas adalah salah satu alasan utama untuk periode operasi yang buruk. Periode operasi yang buruk sering mengakibatkan operasi yang tidak menentu, dan bahkan dingin yang berpotensi merusak lapisan BF dan juga kehidupan kampanye.
Kokas harus kuat dan stabil untuk menopang berat beban dengan kerusakan mekanis minimal. Kokas harus cukup besar dan berukuran rapat, dengan butiran halus minimum untuk membuat lapisan permeabel yang dilaluinya cairan dapat menetes ke dalam tungku tanpa membatasi gas yang naik. Ukuran yang konsisten diperlukan untuk menghindari variasi permeabilitas yang tidak diinginkan dan untuk mendukung konsep variasi ketebalan lapisan kokas melintasi radius BF untuk mengontrol aliran gas radial. Kokas harus cukup tidak reaktif terhadap kehilangan larutan, mempertahankan kekuatannya dalam kondisi seperti itu, dan rendah alkali untuk meminimalkan gasifikasi alkali di raceway, yang memiliki efek merusak pada pemecahan kokas dan pada refraktori tungku. Variasi kadar air dan kandungan karbon kokas perlu dikontrol untuk meminimalkan efeknya pada keadaan termal proses.
Pada tingkat injeksi hidrokarbon tuyere yang tinggi, ada pengurangan yang sesuai dalam proporsi muatan kokas dan akibatnya kualitas kokas menjadi lebih penting.
Kualitas kokas universal, untuk operasi stabil yang kompatibel dengan masa pakai tanur sembur yang lama, sulit ditentukan, karena tidak hanya jenis operasi yang berbeda memiliki persyaratan kokas yang berbeda tetapi juga sifat fisiknya bervariasi sesuai dengan titik pengambilan sampel antara oven kokas dan BF.
Dalam hal penggunaan kokas dari lebih dari satu sumber, diperlukan pencampuran yang memadai atau pengisian secara terpisah kokas yang berbeda sangat penting, karena proporsi kokas yang berfluktuasi dari sifat yang berbeda menghasilkan kondisi yang tidak stabil di BF.
Coke di pusat BF secara bertahap menggantikan orang mati dan coke di perapian, yang harus tetap permeabel untuk memungkinkan cairan mengalir di tengah perapian. Ini menghindari aliran perifer yang berlebihan dari HM di perapian yang dapat mengakibatkan keausan tahan api yang parah di dasar dinding samping. Peningkatan suhu pusat alas perapian biasanya diamati dengan peningkatan ukuran coke orang mati, yang menunjukkan peningkatan aktivitas pusat perapian. Ukuran aperture dari saringan kokas merupakan parameter penting untuk pemeliharaan permeabilitas perapian. Biasanya bermanfaat untuk meningkatkan ukuran saringan dan mengisi tambahan kokas kecil yang timbul, bercampur dengan beban bijih, jauh dari garis tengah BF.
Tujuan penggunaan kokas berkualitas tinggi adalah untuk memastikan bahwa kokas berukuran besar mencapai daerah BF yang lebih rendah. Untuk memantau hal ini, sebaiknya sampel kokas diambil dari waktu ke waktu pada tingkat tuyere untuk menilai kerusakan kokas melalui tungku. Ini biasanya dilakukan selama pemeliharaan yang direncanakan. Sampel besar kokas diambil dari lubang tuyere dan propertinya dibandingkan dengan sampel kokas umpan yang sesuai. Dengan cara ini, faktor lain yang mempengaruhi ukuran kokas juga dapat diidentifikasi.
Coke berkualitas baik dan konsisten serta pemantauan stok dan bosh coke jelas merupakan strategi penting untuk masa pakai kampanye yang panjang.
Campuran beban bijih
BF sedang dioperasikan dengan berbagai macam komponen beban bijih seperti sinter, pelet dan bijih besi berukuran (SIO) dll. Berbagai fluks juga digunakan dalam beban bijih.
Jumlah yang lebih kecil dari bahan lain seperti skrap yang dipulihkan, butiran besi, skala pabrik, terak konverter, ilmenit, limbah daur ulang atau bahkan besi tereduksi langsung atau besi butiran juga kadang-kadang digunakan dalam beban bijih. Penggunaan bahan-bahan ini biasanya tergantung pada faktor lokal.
Pabrik baja terintegrasi biasanya memiliki pabrik sinter sehingga BF di pabrik ini menggunakan sebagian besar beban sinter, dengan keseimbangan beban terutama terdiri dari SIO dan/atau pelet. Pelet lebih disukai lebih dari SIO di beberapa tanaman untuk keseimbangan beban karena sifat unggul mereka.
Di seluruh dunia, persentase pelet dalam beban BF bervariasi dari 0 % hingga 100%. Pengalaman di berbagai pabrik menunjukkan bahwa BF yang menggunakan persentase pelet yang tinggi mengalami variasi beban panas yang lebih tinggi di bagian bawah tumpukan dan bosh, menyebabkan keausan tumpukan dan bosh yang lebih rendah dan masa pakai kampanye yang lebih pendek. Salah satu alasannya adalah kontrol distribusi beban yang tidak memadai. Pelet memiliki sudut istirahat yang jauh lebih rendah daripada sinter atau kokas dan, saat mendarat di garis stok miring, cenderung mudah menggelinding. Hal ini menghasilkan lapisan bijih yang relatif tebal menuju pusat BF yang mendorong aliran gas berlebihan di dinding BF.
Situasi ini diatasi dengan penambahan pendinginan kepadatan tinggi di poros bawah dan peralatan distribusi beban yang ditingkatkan. Temperatur stave yang berfluktuasi, peningkatan selip, dan fluktuasi suhu HM dapat diamati dengan muatan pelet yang akan dikendalikan oleh kontrol distribusi beban, dengan pengisian coke pusat dan penambahan nut coke ke pelet.
Sebuah aspek penting dari komponen beban individu adalah karakteristik pelunakan dan leleh. Bagian utama dari penurunan tekanan di BF adalah di wilayah di mana beban bijih melunak, meleleh, dan menetes ke bawah tempat tidur kokas di mana gas naik. Kisaran pelelehan dan pelunakan yang luas menyebabkan penurunan tekanan yang meningkat dan akar zona kohesif yang besar menimpa bata poros bawah, dengan refraktori terkena suhu tinggi di area yang lebih luas daripada yang diinginkan. Suhu dinding yang lebih rendah dan/atau fluktuasi termal yang lebih sedikit membantu memperpanjang umur pekerjaan bata poros.
Sifat pelelehan dan pelunakan beban komponen ganda berbeda dari masing-masing komponen. Oleh karena itu, data uji pelunakan dan pelelehan harus dipertimbangkan tidak hanya untuk masing-masing konstituen beban tetapi juga untuk campuran bijih yang diusulkan untuk membantu pemilihan beban bijih.
Untuk meminimalkan variasi termal dan kimia, beban homogen diinginkan. Komponen beban harus dicampur sedekat mungkin. Ini tergantung pada jumlah komponen beban dan sistem pengisian individu, tetapi biasanya dapat dicapai hingga tingkat yang wajar dengan pemilihan bunker penyimpanan dan urutan pembuangan material.
Hal ini dimungkinkan untuk mencapai operasi BF yang stabil dan masa pakai kampanye yang panjang menggunakan beban yang berbeda asalkan kualitas materialnya konsisten dan tersedia kapasitas pendinginan dinding yang memadai dan kontrol distribusi yang tepat.
Kualitas beban bijih
BF yang permeabel diperlukan untuk operasi yang stabil. Beban bijih harus kuat, berukuran rapat, dan disaring secara efisien untuk menghilangkan butiran halus. Tidak boleh terlalu hancur di tumpukan dan menghasilkan butiran tambahan Itu harus cukup berpori, dapat direduksi dan ukuran yang memungkinkan untuk dikurangi secara efektif pada saat mencapai zona pelunakan. Dengan cara ini zona kohesif kurang restriktif, dengan sedikit terak kaya FeO, dan beban termal di bawah wilayah BF lebih rendah, mendorong kelancaran operasi.
Sifat pelunakan dan pelelehan komponen bijih memiliki efek penting pada pengoperasian BF. Pembatasan di zona kohesif dan karakteristik leleh yang buruk dapat mengakibatkan penurunan beban yang tidak menentu, operasi yang tidak stabil, dan termal fluktuasi. Kondisi ini cenderung mempersingkat masa pakai dinding BF.
Tidak ada uji pelunakan dan pelelehan standar dan ada banyak indeks yang dikutip untuk mewakili suhu pelunakan dan leleh seperti mulai reduksi langsung, penurunan tekanan selama peleburan, dan jumlah bahan yang menetes, dll.
Distribusi beban
Distribusi beban adalah salah satu faktor utama yang mempengaruhi umur kampanye BF. Tidak hanya dapat mempengaruhi stabilitas operasi tetapi, dengan menentukan aliran gas radial di BF, itu salah satu faktor utama yang mengendalikan tingkat keausan dinding BF.
Umumnya aliran gas radial dikendalikan oleh rasio bijih terhadap kokas dalam beban, karena ukuran kokas biasanya lebih besar. Hal ini biasanya dicapai dengan mengisi bahan dalam lapisan terpisah dan memvariasikan ketebalan lapisan di seluruh radius BF. Oleh karena itu, perlindungan dinding BF dicapai dengan meningkatkan proporsi lapisan bijih di dinding, yang menghasilkan pengurangan jumlah panas yang dikeluarkan oleh sistem pendingin dinding. Namun, ada batasan proporsi dari bahan bijih dekat dengan dinding BF untuk menghindari pembentukan lapisan tidak aktif, yang dapat mendorong pembentukan akresi dinding dan memungkinkan beban yang tidak siap ke daerah bawah BF dan meningkatkan kerugian tuyere. BF harus cukup untuk memungkinkan operasi BF yang stabil pada tingkat produksi yang diinginkan Sebagian besar kokas menciptakan daerah yang relatif permeabel dengan cairan yang turun lebih sedikit, memungkinkan penggunaan volume ledakan maksimum dengan hout fluktuasi besar dalam tekanan ledakan dan penurunan beban yang tidak menentu.
Kokas di tengah BF menggantikan kokas di perapian dan pusat permeabel kaya kokas mendorong perapian permeabel, yang menghubungkan aliran cairan melintasi perapian. Cerobong kokas pusat tidak menjadi terlalu lebar. Dalam kasus seperti itu, hasil yang tidak efisien dan kerusakan dapat terjadi pada bagian-bagian tertentu dari tungku karena kapasitas panas yang terlalu tinggi dari gas yang naik.
Pengisian ukuran terpisah
Sistem distribusi yang lebih canggih memungkinkan kontrol tambahan distribusi beban dengan memanfaatkan lebih dari satu rentang ukuran bahan tertentu. Salah satu praktik yang paling umum digunakan adalah pengisian bahan bijih halus, seringkali dari penyaringan beban bijih utama. Denda dibebankan secara terpisah dalam jumlah kecil di dekat dinding BF, untuk memberikan pengurangan permeabilitas lokal dan dengan demikian melindungi dinding. Mengisi bahan yang lebih halus dalam jumlah kecil yang terpisah biasanya mengurangi kapasitas pengisian BF.
Kokas kacang
Sistem pengisian yang fleksibel memungkinkan penggunaan nut coke nut (ukuran tipikal berkisar antara 10 mm hingga 30 mm). Pengisian nut coke, dicampur dalam beban bijih dan ditempatkan di sepanjang radius tengah, meningkatkan operasi dengan meningkatkan efisiensi reduksi dan permeabilitas lapisan bijih di zona kohesif. Ada peningkatan permeabilitas dan penurunan suhu perut dengan pengisian nut coke. Coke kacang dibebankan di dinding, diapit di antara dua muatan bijih mencegah wilayah dinding tidak aktif ketika bijih halus dibebankan di dinding. Nut coke ditambahkan ke pelet untuk meningkatkan sudut istirahatnya, sehingga mengurangi proporsi beban bijih di pusat BF.
Pemisahan ukuran
Banyak sistem pengisian membuat beberapa derajat pemisahan ukuran dalam bahan masukan. Jika bahan awal yang dibuang lebih halus dan bahan akhir lebih kasar, karakteristik ini dapat dimanfaatkan untuk keuntungan distribusi ukuran radial, dan karenanya distribusi aliran gas radial. Jenis segregasi ini umumnya terjadi pada tungku yang diisi sabuk daripada di tungku yang diisi dengan lompatan dan lebih dapat dikontrol dengan bagian atas yang lebih sedikit lonceng. Modifikasi yang sesuai juga dapat ditambahkan ke sistem pengisian untuk meningkatkan karakteristik pemisahan yang diinginkan.
Segregasi ukuran radial tambahan juga dapat terjadi dengan menggulirkan garis stok miring. Pemisahan ukuran juga dapat mengubah karakteristik leleh dan pelunakan beban di sepanjang radius BF, ketika satu komponen memiliki rentang ukuran dan kimia yang berbeda.
Beberapa sistem pengisian menghasilkan variasi melingkar dalam distribusi beban. Variasi ini harus diminimalkan dengan desain atau operasi.
Pusat pengisian kokas
Sebagian besar kokas biasanya dibutuhkan di pusat BF, untuk mendorong pusat yang cukup bekerja untuk operasi yang stabil. Hal ini terutama terjadi pada produktivitas yang lebih tinggi dan ketika beroperasi dengan injeksi hidrokarbon tuyere tingkat tinggi. Namun, untuk beroperasi dengan kokas seluruhnya di tengah tungku kurang hemat bahan bakar dan teknik telah dikembangkan untuk meminimalkan lebar wilayah pengisian kokas pusat ini. Pada puncak tanpa lonceng, ini dicapai dengan mengisi sejumlah kecil kokas dengan saluran yang berputar diturunkan sepenuhnya.
Tempat tidur kokas permeabel diperlukan di perapian, untuk mendorong aliran cairan melintasi pusat perapian dan mengurangi aliran perifer, yang dapat menyebabkan keausan dinding samping yang berlebihan. Kokas di orang mati dan perapian secara bertahap digantikan oleh kokas dari pusat tungku. Pengisian kokas pusat mengurangi persentase bahan bijih di pusat BF dan meningkatkan permeabilitas perapian. Permeabilitas perapian dapat lebih ditingkatkan dengan pengisian kokas stabil yang lebih besar di pusatnya.
Kehidupan pelindung tenggorokan
Untuk masa pakai kampanye yang panjang, penting untuk meminimalkan keausan pada pelindung tenggorokan tetap yang disebabkan oleh dampak langsung material beban. Meskipun dimungkinkan untuk memperbaiki pelindung tenggorokan atau menggabungkan pelat pelindung, ini mungkin melibatkan penghentian perawatan yang lama, yang dengan sendirinya dapat merusak masa pakai tungku. Oleh karena itu distribusi beban dan tinggi jalur stok yang digunakan harus dipilih untuk menghindari dampak beban tersebut.
Kualitas logam panas
Ketika beroperasi tanpa tengkorak pelindung di perapian, karbon perapian biasanya dihilangkan dengan serangan larutan besi dan terak. Karburisasi awal pada besi, sebelum kontak dengan tungku tahan api meminimalkan keausan tungku tersebut.
Untuk karburisasi awal, diperlukan periode kontak yang lebih lama antara cairan dan kokas. Pada produktivitas tertentu, ini mungkin didorong oleh zona tetesan yang lebih tinggi dan orang mati, dengan zona kohesif yang lebih tinggi. Ini biasanya menghasilkan peningkatan silikon HM (Si). Umumnya tingkat kejenuhan karbon menurun dengan meningkatnya kandungan Si. Akibatnya, HM lebih dekat ke saturasi pada tingkat Si yang lebih tinggi, untuk ukuran BF tertentu dan suhu HM.
Selain itu, peningkatan HM Si meningkatkan suhu liquidus HM dan dengan demikian mengurangi fluiditasnya. Hal ini cenderung mengurangi kecepatan aliran di perapian dan mendorong pembentukan lapisan padat di perapian tahan api.
Pada suhu HM yang lebih rendah, tingkat saturasi karbon dari besi lebih rendah dan dicapai lebih awal. Suhu HM yang rendah memiliki manfaat tambahan berupa peningkatan viskositas besi yang mengurangi aliran perifer, mengurangi kecenderungan untuk melarutkan tengkorak pelindung dan menembus retakan dan pori-pori halus.
HM Si yang lebih tinggi dan suhu HM yang lebih rendah sulit dicapai bersama-sama, karena zona kohesif yang lebih tinggi biasanya menghasilkan tungku yang lebih hangat, tetapi efek keseluruhannya adalah HM yang memasuki perapian menjadi lebih dekat dengan saturasi karbon. Pengurangan tekanan atas yang tinggi kemungkinan akan menghasilkan sedikit peningkatan Si tanpa mempengaruhi keadaan termal BF. Probabilitas pelarutan karbon tungku lebih rendah pada tingkat Si yang lebih tinggi.
Diameter Tuyere
Diameter Tuyere dipilih untuk memastikan penetrasi ledakan yang memadai untuk kondisi operasi tertentu dan untuk mencegah gas yang berlebihan naik ke dinding BF. Pemilihan ukuran tuyere mempengaruhi tingkat kerja tengah BF dan tingkat perlindungan dinding batang dan poros bawah. Biasanya diperlukan untuk memvariasikan diameter tuyere di sekitar BF untuk memastikan keseimbangan aliran gas melingkar.
Meskipun ukuran tuyere dipilih dengan hati-hati, peningkatan diameter yang signifikan sering diamati ketika tuyere diubah, terutama ketika umur panjang tercapai. Hal ini mempengaruhi kedua faktor di atas dan menguntungkan dalam hal masa kampanye untuk mengganti tuyer setelah jangka waktu tertentu, tidak hanya untuk meminimalkan efek keausan tuyere tetapi juga untuk mengurangi kemungkinan kebocoran air ke dalam BF dan jumlah kerusakan yang tidak terjadwal. periode ledakan untuk mengubah tuyeres yang gagal.
Diameter tuyer tepat di atas lubang keran sering kali diperkecil, atau bahkan ditutup, untuk meningkatkan kelancaran pengecoran dan mengurangi pembuatan besi di atas lubang keran.
Diameter Tuyere sering dikurangi secara lokal, sebagai tanggapan terhadap suhu dinding samping perapian yang tinggi, untuk mengurangi cairan yang menetes dan aktivitas perapian di area yang bermasalah. Hal ini dilakukan dengan penambahan sisipan tuyere atau dengan penggantian tuyere. Dalam kasus yang parah, atau sebagai tindakan darurat jangka pendek, tuyer yang bersangkutan dapat ditutup dengan menyumbatnya dengan tanah liat. Ini sering memiliki efek cepat dalam mengurangi suhu dinding samping perapian yang sesuai.
Praktek cast house
Praktek rumah cor memainkan peran penting dalam mengendalikan aliran cairan di perapian dan menghindari tingkat cairan yang tinggi yang dapat menimpa raceway, mempengaruhi distribusi ledakan atau bahkan menyebabkan kerusakan tuyere atau sumpitan. Faktor-faktor ini dapat memengaruhi stabilitas operasi, mengakibatkan periode tidak aktif, dan berpotensi memengaruhi masa pakai kampanye.
Panjang lubang keran
Dengan lubang keran yang lebih panjang, produk cair tidak hanya ditarik dari bagian bawah perapian, tetapi juga dari titik yang lebih dekat ke pusat perapian. Ini mengurangi aliran periferal di dekat lubang keran dan karenanya keausan dinding samping perapian. Untuk memperpanjang panjang lubang keran, perlu untuk meningkatkan jumlah massa lubang keran yang disuntikkan selama periode waktu tertentu, untuk secara progresif meningkatkan ukuran jamur di bagian dalam BF, yang juga melindungi refraktori di bawah lubang keran. Dengan panjang lubang keran yang pendek dan pengecoran secara bergantian dari lubang keran dengan jarak yang luas, fluktuasi suhu dinding samping meningkat, berpotensi meningkatkan erosi tahan api.
Temperatur alas tungku yang tinggi dapat terjadi karena hilangnya lapisan beku dan/atau pelarutan karbon tungku, sementara temperatur dinding samping tungku cukup memuaskan. Dalam kasus seperti itu, mungkin perlu untuk memperpendek lubang keran, dengan mengurangi jumlah massa lubang keran yang disuntikkan dan mungkin dengan mengurangi kemiringan lubang keran. Ini membantu dalam pengurangan aliran HM di dekat pusat BF dan meningkatkan cairan yang tertahan di alas perapian.
Diameter lubang keran
Diameter lubang keran yang diperlukan untuk mempertahankan produktivitas tertentu tergantung pada parameter BF, seperti proporsi waktu pengecoran, tekanan atas, volume terak, ukuran kokas perapian, viskositas cairan dan sifat massa lubang keran. Jika lubang keran terlalu kecil untuk laju produksi tertentu, maka tungku tidak dapat dikeringkan. Jika lubang keran terlalu besar, lebih sedikit produk cair yang dapat dikeluarkan dari tungku selama pengecoran karena lubang keran akan meledak sebelum waktunya, karena cairan di atas lubang keran dikeluarkan sebelum cairan di sisi berlawanan dari perapian dapat turun melalui tempat tidur kokas. Dalam kedua kasus ini, tingkat cairan di perapian tetap tinggi dan pada akhirnya mempengaruhi operasi yang stabil. Oleh karena itu, ukuran lubang keran yang optimal diperlukan yang diperoleh dari pengalaman.
Ketika lubang keran tunggal digunakan, ukuran harus dipilih untuk memungkinkan BF menjadi kering dan memberikan waktu yang cukup untuk massa lubang keran untuk menyembuhkan antara cor. Pada BF di mana lubang keran alternatif digunakan, lubang keran dengan ukuran berbeda mungkin diperlukan dalam kondisi operasi tertentu, untuk memastikan drainase melintasi tungku.
Pada lubang multi tap BF yang mengalami keausan pada bantalan perapian, mungkin diinginkan untuk menambah diameter lubang tap. Hal ini, bersama dengan penurunan panjang lubang keran, mengurangi aliran besi melintasi alas perapian dan meningkatkan sisa besi di perapian di ujung cor, sehingga mendorong pembentukan lapisan beku pada alas perapian.
Massa lubang keran
Properti massa lubang keran penting untuk operasi BF. Massa harus diatur dengan cepat dan sembuh sepenuhnya di antara gips untuk membuat lubang keran yang kuat dan tahan lama. Massa lubang keran harus memiliki sifat adhesi yang baik, untuk membangun struktur permanen yang kuat yang menahan aliran cairan dan juga melindungi refraktori perapian di bawah lubang keran.
Jumlah, posisi, dan kinerja
Produktivitas tinggi dapat dicapai pada tanur sembur lubang tunggal berukuran sedang. Namun, ada keuntungan ketika lebih dari satu lubang keran tersedia, ini menjadi kebutuhan pada tingkat produksi yang lebih tinggi. Pengecoran alternatif dari lubang keran di sisi yang berlawanan dari tungku menghasilkan drainase perapian yang lebih efektif, dan juga memberikan periode yang lebih lama untuk massa lubang keran untuk menyembuhkan sepenuhnya, menghasilkan lubang keran yang lebih tahan lama. Adanya dua lubang keran memungkinkan perbaikan besar-besaran dari pelari besi utama tanpa memerlukan periode off blast. Jika titik panas terjadi pada dinding perapian lubang multi tap BF, dimungkinkan untuk menggunakan lubang tap alternatif yang tidak mendorong aliran periferal di area yang tererosi. Keausan dinding samping akibat aliran periferal akan menyebar lebih merata di sekitar keliling pada tungku lubang multi-tap.
Untuk BF yang besar dan produktivitas tinggi, lebih disukai memiliki empat lubang keran, yang memungkinkan pasangan yang berlawanan untuk dioperasikan sementara satu pelari diperbaiki dan yang lainnya dalam keadaan siaga. Untuk meratakan keausan dinding samping dan mendorong drainase perapian yang lengkap, ini idealnya ditempatkan pada interval 90 derajat.
Frekuensi dan kecepatan transmisi
Laju pengecoran ditentukan oleh ukuran bor lubang keran yang digunakan, karakteristik keausan massa lubang keran, tekanan atas, viskositas cairan dan jumlah lubang keran yang digunakan. Dengan massa lubang keran kinerja tinggi modern, ada kecenderungan untuk mengurangi jumlah gips, yang mengurangi biaya pengoperasian lubang keran. Dengan menurunkan laju pengecoran, kecepatan cairan di dalam tungku berkurang tetapi mereka berlanjut untuk periode yang lebih lama. Pada rumah multi cast BF, ada kemungkinan untuk melakukan casting dari lubang tap yang berlawanan secara bersamaan (lap casting), memberikan penyembuhan massal lubang tap sepenuhnya dalam waktu yang lebih singkat daripada durasi cor dan tenaga kerja serta logistik memungkinkannya. Teknik ini mengurangi kecepatan aliran di perapian, meskipun sering hanya digunakan pada saat tingkat cairan tinggi atau sebelum melepas BF dari ledakan.
Penundaan pengecoran yang lama harus dihindari dengan segala cara, untuk meminimalkan gangguan pada operasi BF. Hal ini membutuhkan desain yang baik dan pengoperasian peralatan rumah cor yang andal, praktik rumah cor yang baik, dan pengangkutan sendok HM yang terkoordinasi dengan baik.
Alkali dan seng
Logam alkali dan seng memiliki efek merusak pada proses BF dan refraktori. Bebannya adalah memiliki kandungan alkali dan seng pada tingkat ekonomi minimum. Biasanya alkali dan seng dikendalikan pada tingkat kurang dari 5 kg/tHM (praktik terbaik adalah 2 kg/tHM), tetapi dengan kondensasi uap alkali pada beban yang menurun, beban resirkulasi yang besar dapat menumpuk di BF. Hal ini menyebabkan peningkatan degradasi sinter dan kerusakan kokas, dan mendorong pembentukan akresi dinding, yang semuanya dapat mengakibatkan penurunan beban yang tidak teratur dan pengoperasian BF yang tidak stabil.
Alkali dan seng, dalam bentuk gas, menembus retakan dan pori-pori di dinding refraktori BF. Serangan kimia yang dihasilkan dan siklus termal melemahkan lapisan permukaan refraktori, yang pada akhirnya dihilangkan oleh beban yang menurun, memungkinkan proses untuk diulang.
Pembedahan perapian setelah akhir kampanye telah menunjukkan bahwa keausan berlebihan terjadi di dasar dinding samping dan bahwa zona rapuh biasanya terbentuk antara cangkang dan permukaan karbon yang panas. Alkali dan seng sering ditemukan pada tingkat tinggi di zona rapuh ini. Berbagai mekanisme pemecahan telah diusulkan yang melibatkan senyawa ini. Stres dan retak termal di dinding samping memungkinkan gas alkali dan seng menembus dan mengendap di pori-pori. Hal ini menyebabkan ekspansi batu bata, penggetasan, pembengkakan lebih lanjut dan akhirnya penghancuran massa tahan api. Tingkat perlindungan refraktori yang signifikan dari alkali dan seng dicapai jika akresi atau tengkorak membeku di permukaan refraktori yang panas, sehingga melindungi refraktori dari serangan kimia.
Mayoritas alkali dihilangkan dalam terak dan sisanya di gas atas. Namun, praktik terak, keadaan termal dan distribusi beban memainkan peran utama dalam penghilangan alkali. Pengurangan kebasaan terak meningkatkan jumlah alkali yang dihilangkan dalam terak sebagai peningkatan tingkat termal BF atau suhu atas, dengan memperluas atau mengintensifkan tingkat kerja sentral. Selain itu, untuk pembebanan alkali tertentu, degradasi kokas cenderung lebih besar untuk operasi dengan laju injeksi hidrokarbon tuyere yang tinggi, karena peningkatan waktu tinggal beban. Penting bahwa keseimbangan input dan output alkali dan seng dipantau dan bahwa BF dioperasikan dengan rezim termal dan kimia yang kompatibel dengan tingkat input elemen-elemen ini, untuk mendorong penghapusannya dalam terak dan gas atas.
Penambahan TiO2
Sampel lapisan perapian di akhir kampanye di BF biasanya mengandung deposit bantalan titanium. Ini membentuk lapisan pelindung di daerah yang terkikis di dinding samping perapian, di salamander dan di pori-pori dan sambungan bata. Titanium biasanya dalam bentuk karbonitrida Ti(C,N), larutan padat titanium karbida (TiC) dan titanium nitrida (TiN). Oleh karena itu saat ini praktik yang terlibat untuk memasukkan titania (TiO2) ke dalam BF untuk mempromosikan lapisan pelindung ini. Tiga metode biasanya digunakan untuk pengenalan TiO2. These are (i) addition to the burden, (ii) injection at the tuyeres, (iii) addition through tap hole mass.
The most common technique has been by the addition of titaniferrous ores (usually ilmenite) to the burden. Alternatively TiO2 can be added through sinter, though at low levels.
Two strategies are generally adopted for TiO2 addition. The first one is remedial, commencing TiO2 additions only when high hearth temperatures are observed, indicating hearth wear. The other takes a preventive approach and adds a small quantity of TiO2 continuously, increasing the addition level if high temperatures are observed. The TiO2 intake for the preventive approach is generally 3 to5 kg/tHM, which usually results in up to 0.1 % Ti in the HM and 1 % to 1.5 % TiO2 in the slag. For remedial action, the TiO2 dosage can be up to 20 kg/tHM, at which level the HM may contain up to 0.3 % Ti and the slag up to 3.5 % TiO2. This creates operating problems due to high slag viscosity and scaffolding in the runner, and hence such high TiO2 levels are only used for short periods.
For promoting the precipitation of Ti(C,N), sometimes the TiO2 addition is increased before a shutdown so that the HM remaining in the hearth get saturated in Ti. As the hearth cools during the shutdown, this promotes precipitation. However the resumption of production is more difficult at high Ti levels as it creates operational problems.
TiO2 can also be added by injecting TiO2 fines through the tuyeres. The advantages of the technique are (i) application at localized positions, (ii) reduced cost due to lower TiO2 rate, and (iii) good results from short time injection, and (iv) unchanged burden properties.
The third method of TiO2 addition is by the use of tap hole mass containing TiO2. One such mass which had been tried was tar bonded with approximately 10 % TiO2. Clearly, the titania is bound in the tap hole mass in an unreduced form, and is injected in relatively small quantities. However there are doubts whether it gets reduced and dissolves in HM in sufficient quantities to be precipitated or whether it is reduced and bonded adequately to the hearth sidewall to be of benefit.
TiO2 is normally partially reduced in BF and is dissolved in the HM. The solubility is greater at higher temperatures. If the Ti in the HM is nearing saturation and the refractory hot face temperature in eroded regions, cracks and pores temperature is lower than the HM temperature, then Ti is precipitated, as Ti(C,N). The technique is more likely to succeed at higher addition rates, but there are other factors which can interfere with this basic mechanism, including thermal state of the hearth, metal/slag chemistry and liquid flow characteristics.
TiO2 additions is usually carried out in conjunction with other remedial actions such as reducing productivity, closing tuyeres and improving hearth cooling intensity. The direct effect of TiO2 addition is therefore often difficult to determine. It is essential to carry out regular, accurate Ti balances to assess the technique and modify operation to encourage Ti retention. The effect of high rate additions can even have a detrimental effect on furnace operation, negating any benefits.
The addition of TiO2 for hearth protection is normally to be considered as part of a hearth protection plan rather than in isolation.
Monitoring
Burden distribution is to be monitored regularly for ensuring the wall protection and a stable and driving BF. Changes in the operating parameters, e.g. changes in tuyere hydrocarbon injectant rate or blast volume, may need adjustments to burden distribution. The effect of burden distribution is usually monitored with various probes and instruments.
For maximizing the campaign life, it is necessary that the charging equipment is capable of controlling accurately the burden distribution. Also necessary instrumentations are to be fitted to comprehensively monitor the BF operation so that the burden distribution is changed and assessed in a controlled and technical manner.
Instrumentation and control
Early warning of hearth problem areas is vital to maximize campaign life, and thermocouples located in the hearth sidewall and in the hearth pad are absolutely necessary to monitor hearth wear. Revised operating practices and actions to protect the hearth are to be taken as a result of increasing hearth temperatures. Hearth pad and sidewall temperatures can also give an indication of liquid flow in the hearth, an important factor in hearth wear.
Temperatures recorded by thermocouples are influenced by only a small area round the thermocouple. It is therefore vitally important to locate the thermocouples in the critical wear areas. Important areas are below the tap holes and around the base of the sidewalls where the so called ‘elephant’s foot’ wear pattern is normally found. An adequate number of thermocouples are to be installed, in the best layout to give as complete coverage as far as practical. At several locations, thermocouples can be positioned at two or three different depths to allow calculation of the thermal profile in the refractory and hence the thickness of residual refractory.
Movement of carbon blocks can nip hearth pad thermocouples, causing false hot junctions or total failure. These problems can be overcome by fitting the thermocouples in sheaths. Thermocouples are also to be positioned around the tap holes, to monitor tap hole conditions and operation.
Additional thermocouples are often added part way through a campaign in areas of known refractory wear, to give a more localized picture of developing problems. Similarly, thermocouples are often added to repaired areas to monitor the repair.
Monitor hearth cooling
Heat flux in the hearth pad or stave cooling water can be determined from the water flow rates and the difference between inlet and outlet water temperature, using resistance thermometers. It can be used only to give an indication of the average hearth wear. It is particularly applicable in the later stages of a campaign, following thermocouple deterioration. Monitoring long term trends in hearth cooling water temperature may give an indication of the efficiency of the cooling system.
Furnace wall conditions
The process conditions at the furnace wall are vital to campaign life. The walls is not to be subjected to high heat loads from an excessive quantity of gas ascending at the wall or impingement of the melting zone on the wall, which results in rapid deterioration of the refractory and wear of the cooling members. On the other hand the walls must not be so inactive that large accretions are permitted to form on them, which prevents smooth burden descent, control of burden distribution and stable blast furnace operation. To monitor wall conditions a variety of methods are used.
The common method of monitoring the walls is using in-wall thermocouples, positioned in the brick work, with the tips a short distance back from the hot face to give a good thermal response. Wall activity is monitored from the temperature level and fluctuations.
There must be a good coverage of thermocouples both vertically and circumferentially to monitor the walls adequately. Typically seven levels of thermocouples, each with eight circumferential positions are used. With a large number of thermocouples, it is difficult for the operator to monitor the variation of them all. By using the temperatures at many points, an isothermal map is normally generated, identifying regions of high or low temperatures which relates to refractory wear, asymmetrical operation or accretion formation. The dynamic temperature behaviour is also be utilized to predict the formation or loss and extent of an accretion.
Throat or skin thermocouples are often installed around the periphery, just below the fixed throat armour. The thermocouple tips are installed level with the hot face of the refractory, to record gas temperature. These give a direct measure of the gas flow at the wall and are usually unaffected by deposition of material, unlike in-wall thermocouples lower in the stack.
Radial measuring probes
The use of retractable probes is one of the important techniques to monitor and optimize burden distribution, and hence campaign life. Such probes are the only method of measuring the variation in operating characteristics along the furnace radius, as opposed to relying solely on wall measurements. They are essentially of two types namely (i) overburden, and (ii) underburden.
Overburden probes have several functions. The simplest type is usually fixed, water cooled and measures the radial or diametrical top gas temperature profile and, in some instances, the gas analysis. Most retractable probes measure the stock line layer profile and can be of a mechanical type, where a weight is lowered to the stock line or a non-contact type, using radar, microwaves, lasers, etc.
Top gas velocity can also be physically determined to measure the quantity of gas flow, and top gas analysis and temperature measurement is frequently carried out in conjunction with the other functions. Probes are also used to determine the trajectory of material off the rotating chute or movable throat armour, for calibration of burden distribution predictive models and to determine the effect of charging chute wear.
Underburden, or in-burden, probes sample gas and measure temperature at a number of radial positions. They are generally positioned in the upper stack, typically 3 m to 6 m below the stock line. These probes are generally of two types. The consumable type, is typically 50 mm in diameter, bends with the descending burden and is straightened on withdrawal for subsequent re-use.
Since the top gas has to pass from the stock line up one of the four off takes, the gas flow pattern begins to distort near the stock line. A large degree of gas mixing then occurs above the burden, and overburden probes must be positioned close to the stock line, and preferably inclined, to give acceptable temperature and gas profiles. The upper stack underburden probes are more sensitive and give superior results to overburden probes. In addition, fixed overburden probes can be quite big in size and, depending on the stock line height, can create a ‘shadow’ and distort the burden distribution below them, which can give unrepresentative results.
Probes, especially underburden probes, are essential tools for prolonging BF campaign life.
Hearth models
In recent years, with increasing computing power available, many mathematical and numerical techniques have been developed to predict blast furnace hearth erosion and liquid flow in the hearth.
Hearth lining wear may be calculated by mathematical model, using temperature measurements from embedded thermocouples in the hearth bottom and sidewall. For this technique to be accurate, a good coverage of thermocouples is required and their depth of insertion needs to be known precisely, together with the thermal properties and geometry of the lining. The accuracy may also be affected by parameters that may change with time, such as the conductivity of ramming, thermal contact between courses of brickwork and the development of a brittle zone in the refractory, which can significantly change its conductivity.
Although hearth temperatures alone give a direct indication of hearth wear, this type of modelcombines information from the thermocouples, at differing distances from the hot face, to predict the extent of wear and solidified layers more accurately.
Direct measurement of hearth lining wear is difficult and undesirable since this requires test borings and embedded sensors through the full refractory thickness.
Artificial Intelligence
The blast furnace process is a complex one, with a large number of process variables. Modern, well instrumented furnaces have hundreds of sensors which require to be monitored by a decreasing number of operators. Consequently, computerized systems are being developed to process the primary information available and give secondary advice to the operators. This is based on a set of operating rules, statistical analysis of data, identifying trends that compare with historical data and use of intelligent techniques such as fuzzy logic and neural networks. The aim of these systems is to predict deviation from steady operation and to quantify the change in control parameters required to minimize the deviations in production and quality. This results in more stable BF operation, avoiding major operating problems such as erratic burden descent and chilled conditions, which is a primary requirement for long campaign life.
Furnace top sensors
Since the late 1970s, many BFs have been equipped with infra-red cameras viewing through windows in the top cone, to measure stock line temperature profile. This technique overcomes some of the disadvantages of fixed overburden temperature probes. The falling burden is not scattered as with probes, leading to a more symmetrical burden distribution, and by measuring material temperature the effects of stock line to probe distance, which can result in gas mixing and desensitizes the temperature profile, are avoided. A further benefit is that the rotation of the distribution chute in the furnace can be observed. However, these systems are expensive, difficult to maintain and experience problems in keeping the viewing window clean, due to the moist, dusty top gas. Problems have been experienced with the dust in the top gas also affecting the temperature distribution. Hence these cameras are not a standard fitment and many operators have abandoned them in favour of radial probes.
Some furnaces are equipped with non-contact stock line profile measurement systems installed in the furnace top cone. These systems effectively replace a retractable overburden probe and, although expensive, have the advantage that they measure over a larger proportion of the stock line than the single radius of a probe.
Thermography
The use of thermal imaging cameras to detect hot spots, on the furnace shell, top gas system, tuyere stocks, stoves, hot blast and bustle mains and other ancillary plant, is important. Not only does it enable early detection of problem areas and permit their systematic rectification, but it also helps prevent catastrophic failures, in which the BF has to be taken off-blast in a sudden uncontrolled manner followed by an often difficult recovery, which would have a detrimental effect on campaign life.
Leak detection
An efficient system of detecting water leaks into the BF from tuyeres and other cooling members is essential. Undetected water leaks may chill the furnace, resulting in erratic operation and difficult recovery from chilled conditions. Water leakage directly affects BF campaign life if it damages the refractories. Water leaks in lower, hotter regions of the BF, which are lined with carbonaceous materials, inevitably results in oxidation of the refractories. Rat holes in the hearth refractories can result, which can lead to breakouts. Water leakage can also result in tap hole problems which may disrupt operations.
Tuyere leak detection systems are often used. One leak detection system incorporates a system of magnetic flow meters with computer analysis of the differential flows. Another system of leak detection uses a pressurized closed circuit water system incorporating make up tanks with the makeup frequency indicating the severity of a leak. Other systems involve observation of gas bubbles or dissolved CO content in the water, differential pressure measurements etc.
A good leak detection system often warns the operator of a water leak in its early stages, before an immediate off blast is required. This gives the opportunity for the leaking member to be isolated prior to the furnace being taken off in a controlled manner, with reduction in tuyere hydrocarbon injection and ore/coke ratio adjustments, thereby minimizing detrimental effects resulting from the subsequent stoppage.
Plant maintenance
All maintenance work possible are to be carried out during production, thereby reducing the off blast time necessary. To minimize the duration of a planned stoppage, good planning and advance preparation are necessary. Although these factors are obvious for economics and to maximize plant output, their long term effect on furnace life is not always considered.
Preparations should always be in hand for maintenance to be carried out if the furnace comes off blast unplanned for other reasons. For instance, if the furnace is off for a tuyere change, it may be possible for work to be carried out on the charging system. If the furnace is off blast for problems at the steel melting shop, then it may be possible for more extensive maintenance to be performed. In this way, the total number of stoppages during a BF campaign can be reduced and their duration minimized.
Effective maintenance reduces the number of breakdowns which result in unplanned stoppages. This involve routine maintenance, regular inspections, periodic checking of important instrumentation, and condition monitoring, e.g. vibration and thermal monitoring. This is most important at later stages of a campaign, as ancillary equipment gets older and less reliable.
Similarly, improved cast house maintenance techniques can reduce off blast time, e.g. extension of the life of the main iron runner on a single tap hole furnace reduces downtime.
Off blast periods
The number of off blast periods, mainly unplanned ones, has a major effect on campaign life in terms of output per unit volume, which is reduced disproportionally to the percentage downtime. Wall damage can result from an increased degree of wall working at the lower blast volumes encountered whilst coming off and on blast, cooling and reheating of the refractories or erratic operation during recovery from the stoppage.
Some BF operators indicate that off blast periods ‘rest’ the hearth and allow a protective skull to form or thicken. In fact, taking the BF off blast is often an emergency procedure, at later stages of the campaign, when high temperatures are detected within the hearth refractory.
Short stoppages
For planned stoppages, additional coke can be charged several hours in advance, to compensate for the reduced blast conditions and the heat losses during the stoppage period. This extra coke in the lower regions of the BF assists smooth recovery from the stoppage. It is usual to decrease or remove tuyere hydrocarbon injection for a stoppage.
At high injection rates, there is a much lower proportion of coke in the BF, which is consequently less permeable and this may hinder recovery from the stoppage. In addition, at high injection rates, the BF is markedly fuel deficient during the recovery until the injection is resumed. This may not happen until the blast volume has reached about half of its full rate, when an adequate raceway is formed and the injectant can be consumed safely. In case there are operating problems in establishing raceway conditions and returning to the level of blast at which injection is possible, it can result into cold conditions or tuyere blockages with slag and the BF is fuel deficient at a time when additional fuel is needed.
In addition to ore/coke ratio compensation, a burden change is generally desirable for a stoppage period. Smaller material components of the burden is to be removed from the burden to promote permeability following the stoppage. High levels of titaniferrous ores is also to be reduced to avoid problems at lower HM temperatures after the stoppage. The proportion of burden components that deteriorate when at high temperatures over a long period, such as ores prone to decrepitation, are to be reduced in a stoppage burden. In addition, a more acid burden may be charged to compensate for higher Si content in the HM during recovery from the shut down.
During a stoppage, other deleterious factors can occur which affects the return to full blast operations. For example, this may include (i) extended periods at reduced blast volume to cast the furnace dry before the off blast, (ii) an extended stoppage period for a variety of reasons, (iii) water leakage into the BF during the shutdown, and (iv) problems during the recovery that may require several off blasts (may be to rectify blast leaks or charging faults etc.). Under such circumstances, the undesirable operating conditions are extended and the additional coke charged may not be adequate, leading to a less smooth recovery from the stoppage.
To ensure smooth operation and minimize the effect of a stoppage on the life of BF, some operators believe a slow start after a planned stoppage. A typical of this is to control output to 90 % on the day before a stoppage and resume at 80 %, then 90 % output on the two days following the stoppage. However, this may not be acceptable to other operators, under conditions where high output is needed.
Unplanned stoppages are undesirable and, if possible, many BF operators try to delay taking the BF off blast for long enough to allow a compensated burden to descend to bosh level. Attempt is usually made to cast the BF as dry as possible, to avoid getting slag back into the tuyeres and blowpipes, which may freeze and further prolong the stoppage. This also gives time to prepare for the repair work due to be carried out and to minimize the time of off blast. To compensate for the heat lost due to an unplanned stoppage, the tuyere hydrocarbon injection is generally increased after coming back on blast, providing it is not already at its maximum level.
Production stoppages can also occur due to the problems in the steel melting shop or during periods of low demand. These occurrences are to be coordinated so as to get advanced warning wherever possible, and to give the option of a compensated burden. The pig casting machine (PCM), torpedo ladle fleet or steel melting shop mixers are to be used as a buffer for short stoppages. In certain circumstances, when there is minimal advance warning of a shutdown, the BF is not dry and there is little empty ladle capacity, and there is no PCM available, it is preferable to dump the HM.
Stack spray techniques for the repair of wall refractories have advanced, enabling the walls to be gunned in a relatively short stoppage, by blowing the burden down to a low level. Although this allows a large quantity of coke to be charged at the lower levels of the furnace to aid start up, there is often difficulty due to the quantity of rebounded refractory falling into the furnace. Start up is easier if a low rebound material is used and the BF is blown down to tuyere level, enabling the rebound material to be raked from the furnace. This can be achieved more effectively by the use of T shaped sheets of corrugated sheeting, inserted rolled up through the tuyere cooler apertures. The blow-in burden chemistry is also to be adjusted to give a slag chemistry that enables the residual rebound material to be melted.
There is a difference of opinion as to whether or not cooling water flows should be decreased for stoppages of greater than a given duration. Some operators prefer reduced flows to maintain refractory temperatures. The majority prefer the hearth cooling water on full flow to promote a thicker protective skull, whilst others who reduce the water flow suggest that by removing less heat it assists a smooth start up.
Another factor which affects the recovery from a stoppage is the removal of an accretion from the BF walls, resulting from the additional wall working and erratic burden descent. This can results into chilled conditions at a time when they are least desirable. If an accretion is known to have formed, it is desirable to try and remove it before a long stoppage. A good system of accretion monitoring provide immediate warning in case of its occurrence, to enable thermal compensation as soon as possible.
Long stoppages
Depending on the duration of the stoppage, the BF may be filled with a coke blank and a low ore/coke burden, or the burden may be blown down to tuyere level. For stoppages of several weeks or longer, the salamander is to be tapped. If this is not done, not only will a considerable amount of process heat be needed, during the recovery, to melt it, but it will expand whilst still solid and create undue stresses on the hearth refractories and shell, shortening their life. This is even more important with those BFs, where the sump depth has been increased to reduce peripheral iron flow in the hearth. It is desirable to monitor these stresses with strain gauges attached to the hearth jacket, and to develop procedures to minimize such stresses.
To recover from longer stoppages, when the BF is in a cold condition, it is necessary to’ warm the hearth and establish an early link between the tap hole and the tuyeres to allow liquids to be removed. This may be done by the use of a blast pipe at the tap hole or the use of an oxy-fuel lance. It is important to prevent the oxygen, entering at the tap hole, damaging the hearth carbon, which can directly shorten the campaign life. Recovery from chilled hearth conditions, following major water ingress during a routine maintenance stop, has been reported to have resulted in severe hearth erosion. Recovery from long shutdowns, with a large quantity of solid metal in the hearth and an impermeable dead man, may result in excessive peripheral flow in the hearth with accelerated hearth sidewall erosion.
Production rules
Being a continuous process, the BF is operated by a number of different operators who, without a set of rules to operate to, would react differently to a given situation. The individual actions taken may not be the correct one and, as a result, the process can be more variable than if the ideal action was taken. The majority of BFs are therefore operated according to set procedures that have been developed and improved from experience. These rules cover a wide area, including practical procedures and process control.
To maximize BF stability, it is necessary to control accurately both the thermal state and the aero-dynamics of the furnace. Steel plants usually devise their own rules to control thermal state, which generally involve the HM Si and temperature as indicators, with the use of top gas analysis and calculation of the quantity of heat available in the BF for silica reduction and to superheat the liquid products. Control of thermal state is usually by adjustment of conditions at the tuyere or by small changes in the quantity of coke charged. Furnace aero-dynamics are monitored by rules relating to furnace pressure drops and burden descent rates, with adjustment to blast volume, burden distribution or burden properties to achieve stability.
Operating rules are also necessary for non-routine operations, where damage to the BF may result from incorrect procedures, for instance in the recovery from chilled hearth conditions, where damage to refractories can happen.
Specific rules for prolongation of BF life
Many operators have a specific set of operating practices for the prolongation of campaign life, which are in place to minimize damage to or prevent further deterioration of the BF. As the hearth is the critical region of the BF which cannot be repaired without a long shutdown, these rules or action plans often relate to hearth conditions. Typically, the actions are defined according to hearth temperatures or refractory thickness.