Persiapan dan Pengisian Beban Blast Furnace
Persiapan dan Pengisian Beban Blast Furnace
Tungku sembur (BF), kecuali di perapiannya, pada dasarnya adalah saluran untuk gas dan partikel beban yang bergerak berlawanan arah arus di BF. Persyaratan dasar untuk operasi BF yang stabil adalah untuk mempertahankan dalam tungku lapisan beban yang bergerak yang tidak banyak berfluktuasi. Secara khusus, untuk membentuk aliran gas yang stabil dan struktur lapisan beban bebas dari lapisan beban campuran. Ini terkait erat satu sama lain. Stabilitas aliran gas hampir seluruhnya bergantung pada permeabilitas beban, yang ditentukan oleh struktur pengepakan beban (ukuran partikel, distribusi ukuran partikel, dan rasio partikel halus, dll.), dan perilaku penurunan beban, yang merupakan aliran padat.
Pada prinsipnya, pemrosesan BF adalah sistem aliran 4 fase kontra-arus, ko-arus, dan/atau lintas-arus yang kompleks yang terdiri dari padatan, gas, cairan, dan bubuk. Interaksi fase berbeda dan terlokalisasi di berbagai wilayah BF. Biasanya ada lima zona yang berbeda (Gambar 1) dalam BF yaitu (i) zona kental, (ii) zona kohesif, (iii) zona aktif kokas, (iv) zona pembakaran (raceway), dan (v) zona orang mati ( wilayah pusat perapian). Karena perbedaan fase beban dan interaksi khas di wilayah tertentu dari BF, tidak ada gerakan beban tunggal atau pola aliran di seluruh volume BF.
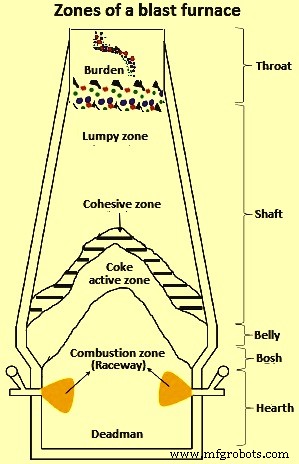
Gbr 1 Zona tanur tinggi
Secara umum ada empat jenis daerah aliran padat yang berbeda di BF. Ini adalah (i) daerah aliran sumbat yang terkait dengan kecepatan seragam beban turun dari garis stok dan posisi tepat di atas zona kohesif atau leleh, (ii) daerah aliran stagnan (dead-man) yang merupakan massa diskontinu sebagian partikel kokas yang bereaksi di bagian tengah perapian, (iii) daerah aliran sebagian-stagnasi yang berdekatan dengan orang mati di mana ada pergerakan lambat partikel-partikel kokas yang bereaksi sebagian, dan (iv) wilayah aliran konvergen yang ada di sekitar raceway dengan variasi kecepatan partikel yang signifikan dalam jarak dinding zona-tungku stagnan.
Mekanisme penurunan beban melibatkan hilangnya bijih dan kokas melalui reaksi, peleburan dan pembakaran, pergerakan partikel beban di bagian atas lapisan beban dan dekat dinding tungku, dan infiltrasi bahan mentah berbutir halus ke dalam lapisan berbutir kasar dll. Faktor-faktor yang mempengaruhi penurunan beban di BF meliputi kondisi bahan baku (ukuran partikel, kekuatan, distribusi beban – rasio bijih/kokas), kondisi raceway (injeksi bahan bakar tambahan), dan tungku profil dinding bagian dalam dll.
Operasi BF cukup sensitif terhadap profil, distribusi ukuran partikel, dan semua faktor yang mempengaruhi kinerja dan produktivitas. Untuk memastikan kelancaran operasi BF, penting untuk mengoptimalkan distribusi material beban padat (bijih besi, kokas dan fluks) di jalur stok. Penting untuk mengontrol keadaan internal BF melalui kontrol yang tepat dari distribusi beban di tingkat lini persediaan.
Bahan beban BF adalah untuk memenuhi persyaratan tertentu yang diperlukan untuk kelancaran operasi BF. Itu untuk memenuhi persyaratan mekanik, kimia dan termal. Bahan yang dibebankan adalah untuk membentuk struktur yang kuat dan permeabel untuk membawa beban dan memungkinkan lewatnya gas pereduksi di poros BF. Disintegrasi awal beban harus dihindari karena pembentukan butiran halus mengganggu aliran gas pereduksi di poros sehingga menurunkan efisiensi proses. Oleh karena itu, pengisian bahan beban halus di BF harus dihilangkan.
Pergerakan beban ke bawah, reaksi kimia, profil termal, dan pergerakan cairan di zona perlu dioptimalkan dengan tujuan memaksimalkan produktivitas dan memastikan operasi tungku yang stabil. Pencapaian operasi produktivitas BF yang stabil dan tinggi dapat diwujudkan melalui optimalisasi proses in-furnace dan operasi periferal seperti kontrol menyeluruh terhadap sifat fisik dan kimia bahan baku serta distribusi partikel. Baik proses in-furnace (perubahan fisik material yang dibebankan dan reaksi kimia) dan operasi tambahan perifer (penimbunan beban, reklamasi, transportasi, penyimpanan, pelepasan, pengangkutan, dan pengisian) adalah fungsi yang tumpang tindih untuk kelancaran fungsi proses BF yang tidak dapat ditangani terpisah karena merupakan proses yang saling terkait.
Bahan muatan BF yaitu bijih besi, kokas dan fluks diklasifikasikan sebagai padatan curah karena memiliki kemiripan dengan partikel padat diskrit yang bersentuhan satu sama lain. Bahan-bahan ini seperti bahan granular lainnya terbuat dari partikel yang berinteraksi. Umumnya, struktur internal bahan-bahan ini cukup evolusioner. Menurut klasifikasi material padat curah yang diberikan di Tab 1, material muatan untuk BF diklasifikasikan sebagai padatan pecah/terputus.
Tab 1 Istilah kualitatif untuk klasifikasi ukuran padatan curah |
Nomor Sl. | Rentang ukuran dalam mm | Istilah umum |
Komponen | Massal |
1 | Kurang dari 0,1 | Partikel | Bubuk |
2 | 0,1 hingga -1 | Butiran | Bentuk padat |
3 | 1 sampai -3 | Biji-bijian | Rusak padat |
4 | 3 dan lebih tinggi | Benjolan | Rusak padat |
Secara umum, penanganan padatan curah dalam bentuk apapun memiliki tantangan dalam hal pemeliharaan homogenitas. Mengingat partikel dengan sifat fisik dan kimia yang sama sebagai komponen diskrit dari padatan curah, telah ditunjukkan bahwa pencampuran (baik disengaja atau tidak disengaja) dari padatan curah pasti menghasilkan partisi alami komponen. Konsep ini umumnya dikenal sebagai segregasi (de-mixing). Secara alami dan / atau industri, pemisahan di antara komponen-komponen terpisah dari padatan curah dapat bermanfaat (misalnya dalam proses pemisahan fisik) atau merugikan (misalnya dalam proses pencampuran) tergantung pada fungsi yang dimaksudkan dari produk atau operasi sub-unit.
Aspek teoritis penanganan material beban
Material beban BF terdiri dari coke, sinter, pellet, calibrated lump ore (CLO), batugamping, dolomit, bijih mangan, dan kuarsit. Karena sifat prosesnya, proses BF pada dasarnya sensitif terhadap ukuran material beban, distribusi, dan kekuatannya. Distribusi bahan beban di BF mempengaruhi gerakan aliran gas ke atas serta kimia proses, perpindahan panas dan massa antara fase yang berbeda dalam proses. Kekuatan material cukup penting karena saat material turun, beban bertambah. Integritas beban selanjutnya dikompromikan oleh reaksi kimia berikutnya yang terjadi pada suhu dan tekanan tinggi, di mana gesekan dan kerusakan sering terjadi.
BF coke berfungsi sebagai bahan struktur pendukung selama operasi BF karena merupakan satu-satunya bahan beban yang turun ke perapian BF dengan reaksi larutan parsial. Ini merupakan proporsi yang tinggi dari biaya produksi logam panas (HM). Dalam beberapa tahun terakhir ada dorongan untuk mengganti kokas dengan sumber karbon alternatif yang murah. Alternatif yang biasanya digunakan adalah injeksi langsung batubara di raceways dalam proses yang umumnya dikenal sebagai injeksi batubara bubuk (PCI). Namun, ada batasan teoretis untuk tingkat penggantian karena BF tanpa kokas yang memadai mengalami penurunan permeabilitas beban, posisi yang menyebabkan tungku tersedak dan menggantung, sebuah skenario yang selanjutnya mengakibatkan terjadinya slip tungku.
Komposisi beban BF menentukan variabel proses dalam tungku seperti suhu leleh, pelunakan serta beberapa parameter pengurangan, yang mempengaruhi produksi jika distribusi beban tidak dioptimalkan. Dengan keterbatasan dan tantangan seperti itu, ada kebutuhan untuk pengendalian distribusi beban yang tepat. Kisaran ukuran tipikal bahan beban BF diberikan di Tab 2.
Tab 2 Kisaran ukuran tipikal bahan beban BF |
Nomor Sl. | Komponen material | Ukuran dalam mm |
Minimum | Maksimum |
1 | Kokas BF | 25 | 50 |
2 | Bijih lump yang terkalibrasi | 10 | 30 |
3 | Sinter | 5 | 30 |
4 | Pelet bijih besi | 8 | 20 |
5 | Batu Kapur | 10 | 40 |
6 | Dolomit | 10 | 40 |
7 | Bijih mangan | 10 | 40 |
8 | Kuarsit | 10 | 40 |
9 | Kokas kacang | 10 | 25 |
Fenomena fisik dan struktur aliran aliran granular, termasuk bahan muatan BF, tampak sederhana pada pertimbangan pertama tetapi dalam kenyataannya, mereka menunjukkan perilaku kompleks yang sulit untuk dipahami dan diprediksi. Situasi ini semakin diperumit oleh kurangnya informasi langsung tentang parameter pencampuran dan pemisahan untuk proses tersebut. Namun, karena ukuran agregat material muatan BF dan distribusi ukuran material yang besar, kecenderungan segregasi merupakan masalah operasional yang serius yang harus dikurangi sebanyak mungkin.
Penanganan material curah dan perilaku aliran
Pemahaman mendasar tentang perilaku dan aliran bahan curah tetap tidak memadai terlepas dari kenyataan bahwa unsur-unsur mekanika serbuk telah lama dikenal sejauh pertengahan abad ke-19. Hal ini terutama disebabkan oleh karakteristik yang unik dan kompleks dari fisika aliran. Penanganan material curah menunjukkan perilaku yang menarik. Salah satu aspeknya adalah kemampuan campuran makroskopik dari partikel yang tidak bercampur karena sifat partikel individu. Pengamatan ini terutama sebagai akibat dari kecenderungan alami bahan-bahan ini untuk pengembangan pola dan pengorganisasian diri. Fenomena ini terutama disebabkan oleh perilaku material curah yang menyerupai karakteristik seperti cairan.
Sebanyak materi curah menyerupai karakteristik seperti cairan dan dengan sendirinya lebih mirip padatan, perilaku dan karakteristik keseluruhan sepenuhnya paralel dengan pengamatan dalam bentuk materi umum ini. Biasanya, tidak seperti bentuk materi lain di mana dinamikanya dipengaruhi oleh suhu biasa, efek itu dapat diabaikan dalam dinamika material curah. Sangat membantu untuk mengetahui bahwa persaingan untuk adveksi kacau atau efek pencampuran yang khas dari fluida bertanggung jawab atas kecenderungan pengorganisasian diri yang diamati pada material curah, sementara segregasi yang diinduksi aliran tidak memiliki fenomena fluida.
Perilaku makro dari proses fundamental terutama diatur oleh kontak antar partikel mikro dan gaya gesekan. Mengingat ukuran bahan muatan BF yang lebih tinggi dari 5 mm, efek gaya permukaan yaitu elektrostatik, van der Waals dan efek kapiler dapat diabaikan. Selanjutnya, perilaku aliran bahan beban sesuai dengan padatan non-kohesif karena kecenderungan kohesif khas untuk bahan serbuk prima atau ultra halus dengan ukuran partikel kurang dari 10 mikro meter.
Klasifikasi aliran material curah
Aliran bahan curah dapat diklasifikasikan menurut komponennya, yang dapat didefinisikan sebagai sekelompok partikel dengan karakteristik fisik yang sama seperti ukuran partikel, kerapatan, dan bentuk. Struktur aliran seringkali sulit untuk dianalisis dan secara signifikan dipengaruhi oleh interaksi partikel ke partikel serta eksitasi eksternal dan kondisi batas. Akibatnya, tidak ada metode yang mencakup dan generik untuk sepenuhnya menggambarkan semua struktur aliran bahan curah. Bergantung pada segmen waktu di mana partikel-partikel tersebut bersentuhan, beberapa jenis struktur aliran yang berbeda dapat dibuat.
Dalam kasus aliran material curah, aliran granular menunjukkan sejumlah variabel keadaan tidak stabil metastabil. Keadaan tidak stabil metastabil ini berlangsung tanpa batas jika tidak ada gangguan eksternal seperti getaran. Rezeki keadaan seperti itu sangat tergantung pada segmen waktu partikel dan batas bersentuhan. Hal ini tergantung pada fraksi volume padatan relatif terhadap total volume cairan (gas atau cairan). Akibatnya, aliran bahan granular umumnya diklasifikasikan sebagai encer atau padat (kontak-dominasi), tergantung pada fraksi volume padatan. Tergantung pada segmen waktu dalam kontak, aliran padat dapat dikategorikan sebagai didominasi-tabrakan atau didominasi-kontak. Dalam ketiga klasifikasi ini, perilaku dan aliran karakteristik berbeda dengan klasifikasi tertentu. Interaksi fluida-partikel (yaitu gaya angkat dan gaya hambat) mendominasi gerakan partikel dalam aliran encer sedangkan tumbukan partikel ke partikel atau partikel ke dinding atau kontak partikel ke partikel terus menerus mendominasi aliran padat.
Representasi skema klasifikasi material curah antara aliran encer, aliran padat yang didominasi tumbukan dan aliran padat yang didominasi kontak ditunjukkan pada Gambar 2. Klasifikasi bahan curah encer yang diberikan pada Gambar 2 dapat diamati pada pemisah siklon, unggun terfluidisasi, dan hopper material BF aliran masing-masing. Aliran padat (tabrakan dan didominasi kontak) khas untuk material curah BF selama proses pembuangan, penyimpanan, dan transportasi.
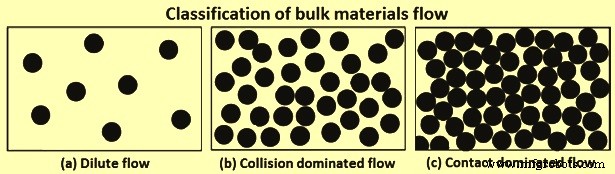
Gbr 2 Klasifikasi aliran material curah
Dua klasifikasi aliran material padat
Fitur bersama dari dua rezim aliran padat adalah perkembangan struktural sebagai fungsi dari skala panjang dan waktu. Biasanya, ini mengarah pada pembentukan pola karena reorientasi partikel. Orientasi material seperti itu didorong oleh struktur skala menengah. Skala partikel individu, lebih dikenal sebagai skala mikro, dipisahkan dari skala makro atau kontinum oleh skala menengah. Memahami interaksi partikel kompleks dari rakitan aliran granular sangat penting dalam mengukur fenomena segregasi atau de-pencampuran. Dalam hal ini, hubungan antara perilaku makro-struktural (massal) dengan dinamika mikro-struktural (diskrit) yang mendasari harus ditetapkan.
Aliran yang didominasi tabrakan – Dalam aliran yang didominasi tumbukan, aliran tersebar, tersebar, dan energik, dengan partikel berinteraksi terutama oleh tumbukan hampir seketika dan tumbukan biner. Efek inersia dapat diabaikan. Tumbukan tidak elastis dan energi hilang selama interaksi partikel ke partikel atau partikel ke batas. Karena tumbukan bersifat disipatif, sumber kerja agak diperlukan untuk mempertahankan 'fluiditas' bahan granular. Karena sifat disipatif dari tumbukan, perilaku dan pola aliran yang berbeda seperti gelombang pengelompokan dan kepadatan diamati. Gelombang densitas adalah fenomena yang terkait dengan suhu granular, di mana partikel tidak mengalir secara seragam melainkan ke daerah dengan kecepatan yang berbeda dari kecepatan rata-rata.
Alur yang didominasi kontak – Dalam aliran yang didominasi kontak, tumbukan partikel ke partikel berkorelasi kuat, baik biner maupun instan, melainkan bertahan lama dan berlipat ganda. Aliran ini menunjukkan dua skenario karakteristik yang menarik di mana terdapat tegangan geser kritis di bawah aliran yang memungkinkan dan ketergantungan yang rumit pada laju geser ketika aliran dimulai. Sebagai akibat dari ketergantungan tersebut, struktur aliran yang lengkap memerlukan pencantuman fitur visko-plastik yang terkait dengan aliran yang didominasi oleh kontak.
Ada beberapa hukum konstitutif yang diusulkan berdasarkan perlakuan yang berbeda dan beberapa pertimbangan seperti menambahkan derajat kebebasan melalui rotasi lokal, pengenalan aturan aliran stokastik dan modifikasi koefisien transportasi teori kinetik seperti istilah viskos, frekuensi tumbukan, dan istilah disipasi. Formulasi baru-baru ini di mana parameter yang disebut bilangan inersia tampaknya merupakan formulasi yang kuat, mampu mereproduksi berbagai karakteristik visko-plastik dari aliran yang didominasi kontak. Bilangan inersia adalah laju geser dikalikan akar kuadrat dari massa partikel dibagi dengan tekanan.
Pencampuran dan pemisahan bahan granular
Penanganan material granular cukup rumit terutama ketika homogenitas dan distribusi keseragaman diperlukan karena kecenderungan alami untuk segregasi (de-mixing), terutama jika ukuran material sangat bervariasi. Tidak seperti proses cairan di mana pencampuran mempromosikan homogenitas, aliran granular menyerupai pencampuran dan pemisahan gambar cermin di mana kecenderungan pencampuran berkepanjangan mempromosikan de-pencampuran (segregasi). Dengan demikian, kasus material beban BF yang melalui proses penanganan berulang, akan berguna untuk memperlakukan pencampuran sebagai fitur diam.
Urutan alami bahan granular memisahkan atau menyimpang dari perilaku seragam. Tergantung pada keadaan sistem (pengisian, penyimpanan, pemakaian dan transportasi) di mana bahan granular terkena, ada berbagai bentuk mekanisme dimana segregasi terjadi. Penggerak utama segregasi adalah perbedaan ukuran partikel, perbedaan densitas serta perbedaan sifat mikro seperti efek gesekan, koefisien restitusi dan sudut istirahat. Di antara pendorong ini, ukuran partikel tampaknya menjadi faktor terpenting yang menentukan perilaku pemisahan partikel granular.
Mekanisme pemisahan material granular
Dalam sebuah studi untuk meminimalkan segregasi, tiga belas mekanisme pemisahan material granular telah diusulkan. Namun, sebagian besar mekanisme ini adalah kasus khusus atau tumpang tindih dari mekanisme lain. Mempertimbangkan hal ini dan memiliki fleksibilitas, pemisahan material granular klasifikasi telah disederhanakan menjadi lima mekanisme utama. Dalam lima mekanisme yang disederhanakan ini, mekanisme pemisahan fluidisasi dan aglomerasi mengacu pada partikel halus dan kohesif masing-masing dan tidak berlaku untuk bahan muatan BF. Dengan demikian, tiga mekanisme pemisahan utama yang berlaku untuk pengisian, penyimpanan, pengosongan, dan transportasi material pengisian BF dijelaskan di bawah ini.
Mekanisme perkolasi atau penyaringan dinamis – Ketika partikel dengan rentang distribusi ukuran dibuat untuk berinteraksi (misalnya dalam wadah penyimpanan material), tetesan konsolidasi spontan dapat terjadi dengan partikel yang lebih kecil meresap dan menyaring ke bawah melalui celah fraksi besar. Secara alami, ketika bahan granular mengalir, celah granular melebar dan ketika ini terjadi, celah dibuat. Partikel kecil dapat masuk ke celah kecil di bawah partikel besar, tetapi kebalikannya jauh lebih kecil kemungkinannya terjadi sehingga menghasilkan fluks pemisah bersih dari partikel yang lebih kecil ke bawah, menjauh dari permukaan bebas. Tindakan ini biasanya dikenal sebagai perkolasi. Pada kondisi tunak, partikel-partikel terpisah dengan lapisan bawah yang memiliki banyak partikel halus. Mekanisme perkolasi ditunjukkan pada Gambar 3. Dalam sistem biner dengan diameter partikel, d1 dan d2, di mana d2 lebih tinggi dari d1, pengayakan spontan terjadi ketika d1/d2 kurang dari atau sama dengan 0,1547. Penggunaan pertama dari rasio kritis ini dilakukan untuk mendapatkan model rinci untuk segregasi karena perbedaan ukuran partikel dalam aliran saluran berdasarkan mekanisme perkolasi.
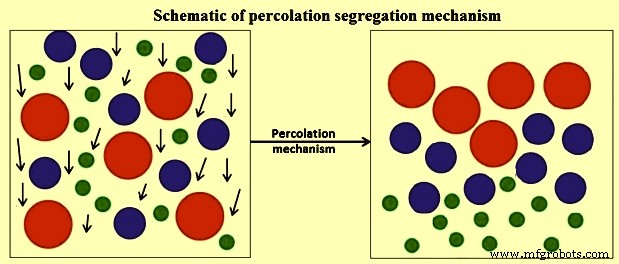
Gbr 3 Skema mekanisme segregasi perkolasi
Mekanisme segregasi perkolasi diintensifkan dengan induksi geser melalui gerakan getaran seperti vibro-screen dengan partikel berukuran besar dan berdensitas tinggi yang bermigrasi ke atas. Ini menunjukkan bahwa hanya pertimbangan geometris yang diperlukan untuk pemisahan dalam sistem bergetar. Singkatnya, agar mekanisme segregasi perkolasi terjadi, tiga kondisi terutama harus dipenuhi yaitu (i) rasio ukuran kritis untuk pengayakan, (ii) partikel kecil harus non-kohesif untuk melewati celah, dan (iii) adanya regangan yang cukup atau gerakan antar partikel untuk meningkatkan kemungkinan orientasi partikel halus ke beberapa celah.
Mekanisme lintasan – Mekanisme segregasi yang digerakkan oleh lintasan biasanya terlihat pada titik transfer material muatan yang terutama mengisi ke tempat penyimpanan, mengeluarkan dari gerbong penyimpanan, dan mengeluarkan di ujung sabuk konveyor seperti yang ditunjukkan pada Gambar 4. Dalam sebuah penelitian yang menyelidiki kondisi aliran untuk memastikan aliran yang lancar bahan granular, telah ditunjukkan bahwa bahan dengan ukuran yang berbeda bergerak pada kecepatan yang berbeda karena gaya gesek yang berbeda yang menyebabkan segregasi material. Mekanisme pemisahan lintasan telah dijelaskan secara matematis dengan mempertimbangkan partikel yang diproyeksikan secara horizontal ke dalam fluida. Mengingat partikel kecil berdiameter d, rapatan Dp, dan gaya hambat yang diatur oleh hukum Stokes, telah ditunjukkan bahwa jarak maksimum X, yang ditempuh oleh partikel dengan kecepatan proyeksi awal Vi, ke dalam fluida dengan viskositas Vf, dan rapatan Df, adalah seperti yang diberikan dalam Persamaan X =Dp.Vi.(Dp)2/18 Vf. Namun, ketika mempertimbangkan ukuran bahan muatan BF dan dengan asumsi gaya hambat dapat diabaikan, lintasan partikel diberikan oleh persamaan lintasan tak berdimensi. Persamaan lintasan tak berdimensi adalah y/x =tan A – [g/2 (cos A)2]. x/Vi, di mana x dan y masing-masing adalah koordinat spasial horizontal dan vertikal, A adalah sudut kemiringan, g adalah percepatan gravitasi dan Vi adalah kecepatan awal saat terbang bebas. Dari persamaan tersebut, dapat dilihat bahwa lintasan partikel tidak tergantung pada ukuran (massa) melainkan kecepatan acak pada awal jatuh bebas yang terkait dengan masing-masing partikel individu.
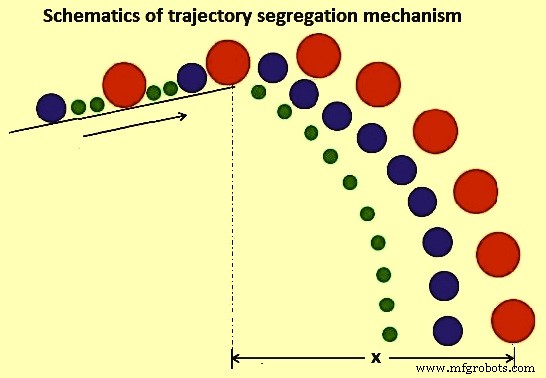
Gbr 4 Skema mekanisme pemisahan lintasan
Mekanisme perbedaan properti mikro – Berdasarkan mekanisme ini, terdapat tiga efek yaitu (i) efek gesekan (ii) koefisien efek restitusi, dan (iii) efek sudut istirahat.
Studi tentang efek gesekan pada bahan granular telah menunjukkan bahwa bahan granular dengan dua komponen yang memiliki koefisien gesekan statis F yang berbeda, biasanya terpisah. Selama studi, sebuah kasus telah dipertimbangkan untuk sebuah partikel bola dengan massa m pada ketinggian h, koefisien gesekan geser Fs, koefisien gesekan menggelinding Fr, dan jari-jari r, yang meluncur di atas lereng dengan sudut kemiringan A, sebagai ditunjukkan pada Gambar 5. Mempertimbangkan prinsip kekekalan energi, jika sebuah partikel pada kesetimbangan tidak stabil memenuhi persamaan momentum yang diberikan dalam persamaan m.g.sin A.r =m.g.cos A. Fr. Dalam persamaan ini, jarak tempuh partikel, X dapat diperoleh dengan persamaan X =(h/Fs).(Cos A)2.(1-Fs/tan A) dan X =(r.h/Fr).(cos A) 2. (1- Fr/r.tan A). Kedua persamaan ini memberikan jarak tempuh partikel yang diturunkan dengan mempertimbangkan koefisien gesekan geser dan gelinding masing-masing. Dari persamaan ini, dapat dilihat bahwa jarak tempuh partikel bergantung pada diameter partikel ketika koefisien gesekan guling dipertimbangkan dan ini menghasilkan segregasi. Sebaliknya, efek gesekan geser menunjukkan independensi ukuran dan massa partikel.
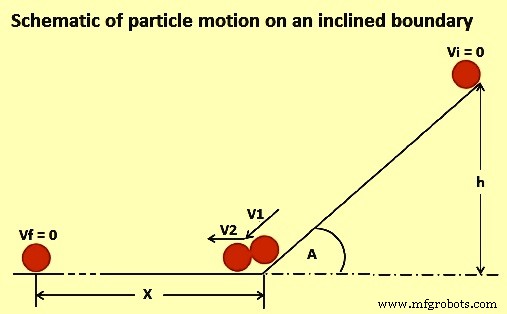
Gbr 5 Skema gerak partikel pada bidang miring
Mekanisme koefisien efek restitusi pada prinsipnya merupakan efek dinamis. Ketika partikel bertabrakan atau partikel menabrak batas sistem, mereka memantul pada kecepatan yang berbeda dan posisi akhir ditentukan oleh ketahanan antarmuka. Contoh mekanismenya adalah pengisian partikel pada tumpukan atau ke tempat penyimpanan. Pada tumbukan di bagian atas tumpukan, partikel dengan sedikit ulet tidak terpental tetapi terjebak pada posisinya. Sebaliknya, partikel-partikel dengan ketahanan tinggi tersebut memantul dan menemukan posisi akhir di suatu tempat yang jauh dari tempat pengendapan dan mungkin terkonsentrasi di tepi tumpukan.
Dalam hal efek sudut istirahat, mekanisme segregasi diamati selama pemancangan material granular. Saat membangun timbunan, terlihat bahwa sudut kemiringan (sudut istirahat) tergantung pada jenis material dan tidak tergantung pada jumlah partikel. Dalam studi tentang efek batas pada sudut diam pada drum yang berputar, telah ditunjukkan bahwa segregasi aksial dipengaruhi oleh sudut diam statis atau dinamis. Pada prinsipnya, sudut efek istirahat tergantung pada parameter material seperti ukuran partikel, distribusi, bentuk dan gaya gesekan dan dengan demikian, menjadi mekanisme campuran karena dimasukkannya variabel lain untuk efek.
Klasifikasi pemisahan material granular
Pemisahan bahan granular diklasifikasikan berdasarkan variabel yang dipertimbangkan untuk proses yang dipertimbangkan. Terutama, itu diklasifikasikan berdasarkan (i) sifat fisik partikel (yaitu ukuran, kepadatan, atau segregasi bentuk), (ii) input energi (yaitu getaran, gravitasi, atau segregasi geser), (iii) orientasi gerakan partikel (yaitu horizontal). , atau pemisahan vertikal), dan (iv) peralatan yang digunakan (yaitu hopper, chute, atau conveyor).
Namun, proses alami atau mapan yang lebih dikenal sebagai mekanisme yang menciptakan segregasi tampaknya merupakan pendekatan klasifikasi yang paling umum. Segregasi secara luas dianggap sebagai fenomena permukaan. Dengan demikian, mekanisme yang berbeda diamati tidak tergantung pada partikel di bawah lapisan permukaan. Pada prinsipnya, mekanisme tersebut dapat dipertanggungjawabkan dengan hanya mempertimbangkan perilaku partikel lapisan permukaan yang bergerak. Dalam berbagai jenis segregasi, pada prinsipnya dan dalam banyak kasus, mekanisme segregasi secara keseluruhan merupakan kombinasi dari beberapa mekanisme yang saling berinteraksi. Misalnya, segregasi pengayakan dapat dianggap sebagai kasus khusus segregasi perkolasi dan perpindahan/migrasi karena keduanya berbagi prinsip penyaringan partikel kecil ke bawah relatif terhadap partikel besar.
Kuantifikasi pemisahan
Meskipun ada beberapa pemahaman tentang mekanisme dan efek segregasi pada aliran material granular, masalah yang timbul dari fenomena ini harus dibatasi secara memadai, ada kebutuhan untuk beralih dari penghindaran terjadinya ke arah kontrol segregasi. Dalam hal ini, metode pengukuran segregasi kualitatif dan kuantitatif yang tepat diperlukan untuk sepenuhnya memahami dan mengendalikan efeknya, terutama dalam kasus material beban BF, yang menjalani proses penanganan berulang. Deskripsi lengkap dari distribusi partikel adalah latihan non-sepele dalam keadaan seperti itu. Namun, untuk secara tepat membebani lini stok tungku, sangat penting untuk memiliki pengetahuan tentang distribusi material partikel bersama dengan kuantifikasi pencampuran dan pemisahan dalam aliran granular.
Indeks pengukuran pemisahan – Pada prinsipnya, segregasi adalah sebagian kecil dari aliran material granular yang kompleks. Selanjutnya, ketidakjelasan aliran granular membuat praktis sulit jika bukan tidak mungkin untuk mengekstraksi data yang berguna secara fisik selama studi segregasi. Penggabungan yang sesuai dari formulasi teoretis ke dalam simulasi pemodelan matematika dapat memudahkan untuk mengkarakterisasi pencampuran aliran granular dan pemisahan sistem tersebut dengan lebih baik. Kuantifikasi segregasi adalah tugas penting karena melibatkan inklusi lengkap hubungan timbal balik antara faktor-faktor yang menyebabkan segregasi dan persamaan gerak partikel. Namun, sejumlah indeks untuk mengukur kualitas pencampuran granular, yang dapat digunakan sebagai ukuran kuantitatif segregasi, telah diusulkan dan umumnya dinyatakan dalam istilah statistik atau istilah bilangan tak berdimensi. Metrik pencampuran dan pemisahan yang umum digunakan adalah standar deviasi relatif (RSD) yang hanya memperhitungkan sistem komponen tunggal. Metrik segregasi RSD ini adalah metrik aplikasi industri reflektif karena menyediakan keadaan pencampuran makro untuk keseluruhan sistem.
Metrik pengukuran pencampuran dan pemisahan adalah tulang punggung dari banyak indeks yang digunakan. Penting untuk dipahami bahwa sampel yang disatukan dan ukuran varians tertentu digunakan untuk menentukan indeks pencampuran dan/atau pemisahan. Meskipun kuantifikasi cukup informatif, kelemahan utama dari karakterisasi tersebut adalah rata-rata atas domain pengukuran sementara mengabaikan partikel ke partikel variasi distribusi yang tetap belum ditemukan. Selain itu, dalam konsep klasik dan fundamental yang telah dikembangkan tentang pencampuran dan pemisahan bahan granular, proses pemisahan granular telah didefinisikan dan disimpulkan sebagai fenomena permukaan.
Sejumlah penelitian telah menunjukkan dan membuktikan bahwa berbagai bentuk peralatan penanganan, mode operasi, dan sifat material dapat dikorelasikan dengan perilaku pencampuran dan pemisahan material. Tantangan utama yang masih tersisa adalah untuk memiliki metodologi karakterisasi pemersatu, yang tidak hanya menggambarkan dinamika pencampuran tetapi juga pada dasarnya menangani fenomena segregasi yang lebih rumit. Sebuah pendekatan baru adalah untuk mengkarakterisasi evolusi partikel ke hubungan partikel dalam bahan baku dalam sistem pengisian sehingga dapat menginformasikan sejauh mana pencampuran dan pemisahan dalam ruang dan waktu. Poros metode ini didasarkan pada gagasan bahwa beberapa aspek hubungan antara partikel dan tetangga terdekatnya dapat digunakan untuk menyimpulkan wawasan yang berguna ke dalam proses dinamika partikel yang berkembang.
Model segregasi mekanistik aliran granular
It has been seen that segregation kinetics is widely and in general framed into a mathematical statistics and probability framework. The apparent limitation to this approach is that the absolute reflection of the physical nature of the process is precluded coupled with the failure to prescribe the direction in which segregation is taking place. This limits the possibility of a generalization since the knowledge is quite empirical. In the first pioneering study to develop mechanistic models which incorporate all the physics surrounding the prevalent de-mixing tendencies that occur in real granular flow system, the application of kinetic theories for mixtures of granular materials has been applied to study segregation tendencies based on percolation mechanism. Using a combination of statistical and dimensional analysis, the developed formulations hold for negligible enduring frictional contacts with shear rates sufficiently high so that the dominant contributions to the total stresses are due to particle to -particle and particle to boundary collisions. In this study, it has been observed that in a chute flow with high solids volume fractions, there is a high probability of small voids formation relative to big ones. The resulting effect of such a postulation is that small particles sieves through and collects at the base of the bed. This results in a net segregation flux in a direction normal to the chute surface of the small particles.
In as much as the mechanistic models described above give some intended physical appreciation in segregation description, evaluation of key fundamentals such as dispersion coefficients of such granular flows are not small and cannot be established by the above models. In this direction, one study suggested mixed statistical and mechanical interactions based on the kinetic theory of dense gas systems since they give a general understanding of causes of granular flow segregation.
Clustering occurs as granular flow experiences damping as energy is lost after collisions. The change in velocity and movement is non-uniform hence the clusters are formed. Hence, constitutive equations have been proposed based on a kinetic theory for collisional rapid flows. The utilization of the kinetic theory expressions for the analysis of granular segregation shows that it can be used only for inelastic and different sized particles at low volume fractions. This is a limitation as typical granular flow systems are contact-dominated flows with high solids volume fractions. The application of the theory is more useful in case there are established constitutive equations for inelastic, different sized particles and high solids volume fractions.
It is seen that the granular flow resembles mixing and segregation mirror image in which the prolonged mixing tendency promotes segregation. The concentration gradients results in mixing whereas the individual contributions of pressure and temperature gradients produce segregation in granular flow systems characterized by particles with particle size range distributions and material density differences.
The theoretical aspects of the bulk handling of the materials have given a general but compact back ground on granular flow, free surface segregation, mechanisms and theoretical approaches in granular material processes. BF burden material storage, handling and transportation processes are susceptible to the fate associated with segregation. For example, the BF sinter material is known to have more in-bin size segregation and more out of bin size variation than the BF coke.
BF charging system
The charging system of the BF iron-making process can generally be described as a network of equipment and mechanisms designed to charge materials into the BF in a certain sequence, quantity and at a rate which ensure that the specified furnace productivity and prescribed stock-line level is maintained. The charging system consists of three sub-systems which are essentially responsible for (i) batching (ii) transportation, and (iii) charging into the furnace respectively. Batching is done in the stock-house which receives the bulk solid feed materials from their various sources (stockpiles, sinter plant, and coke ovens), storing each material in individual bins to provide several hours of feed material for usual BF operations. The batching process includes screens, weigh-hoppers, conveyor belts, feeders and control systems to prepare batches of charge materials. Transportation provides the means for the delivery of the materials to the top of the furnace. Normally, this is done with either by the belt conveyor system or the skip hoist arrangement. The third sub-system consists of a network of equipment and mechanisms for the charging and control equipment. The overall charging system is interconnected and controlled by an automated charge programme.
Under some conditions, furnace productivity can be limited due to the capacity of the batching (stock-house) process to deliver charge materials. This occurrence is mainly due to transient charge materials flow, equipment settings and charge requirement (burden ratios). A typical source of transient change in charge composition is caused by changes in materials delivered to the stock-house bins and is usually referred to as ‘stock transitions’. This normally occurs when the reclaimed material is used such as the substitution of fresh coke and sinter with stored coke and stored sinter respectively. Such reclaimed materials are known to alter furnace performance compared with the fresh materials. Hence, there is need and usefulness of knowing the different materials and to have their accurate tracking through the charging system so that burdening and blast parameters can be controlled optimally to maintain furnace operational stability.
One other important feature of the charging system is the mixing and segregation of charge material. For example, accurate weighing of several materials in the same hopper requires sequential delivery of the material. However, when the weigh hopper discharges, the materials inherently intermingle to some extent, yielding a time-varying composition of the delivered stream. It is imperative to have an accuracy of time-varying composition in order to estimate the radial variation in burden chemistry and physical properties of the material delivered to the furnace.
Since the burden materials undergo multi-stage handling, hence the processing of different types of charge materials need greater control for high productivity and stable operation of the BF. Also, charge material batching and transportation phenomena are required to be the key focus area for BF operator. For smooth BF operation, the operator is to be position to accurately track the burden materials upto their delivery to the furnace charging system.
The overall charging system is interconnected and controlled by an automated charge program which is coordinated by discrete event processes. Previously, BFs were generally small compared to the modern-day large capacity BFs. In small furnaces, the theoretical amount of coke was normally determined as the controlling charging factor as such, with skip charged furnaces, the optimum charging capacity is reached with full skips of coke.
In the modern BF operations, over and above the need to cope with burden material requirements of larger BF capacity, there are two additional operational factors which are (i) sustenance, and (ii) environmentally friendly operations. Sustenance is mainly through the realization of high furnace productivity which currently has been achieved by an array of technology uses. With this added dimension, the total skip weight is now normally the controlling charging factor and thus modern furnace can work with full skips of iron-bearing burden component. Considering the large size of the present day BFs, the required skip capacities become extremely large and as a result, the design and installation of such skip charging facility to cater for such a huge continuously charging system pose a challenge. Such commensuration of modern large furnaces can only be achieved with sufficient burden delivery capacity. As a result, the modern furnaces are equipped with the conveyor belts charging system. The modern BFs charging facilities consist of a stock-house with a conveyor belt transportation of burden materials to the BF bell-less top (BLT) charging system.
BLT charging system
The charge material is conveyed to the BLT charging system where it is eventually charged into BF top material hoppers (bins) which are alternately used. While one hopper is being filled, the other one is being discharged. The operation of weigh-hoppers and material hoppers is essentially the same and thus, the further description gives an account of particle behaviour during conveyance (conveyor belt), intermediate storage (material bins and weigh hoppers) and eventual discharge (chute or free fall).
Conveyor belt particles behaviour – It is seen that the granular material of varying size fractions and density cause segregation. The detailed phenomenon of the transport mechanism of granular material on a conveyor belt remains limited. However, segregation phenomena on a conveying system are difficult to explain without elaborate simplification of the problem. The system under study has to be defined in terms of mass flow rate and the conveyor speed which promote particle bed development. Operative mechanism of segregation can be established only if the system is well defined. In Fig 6, a schematic representation of the particle size segregation at the transfer point of a moving conveyor belt is shown.
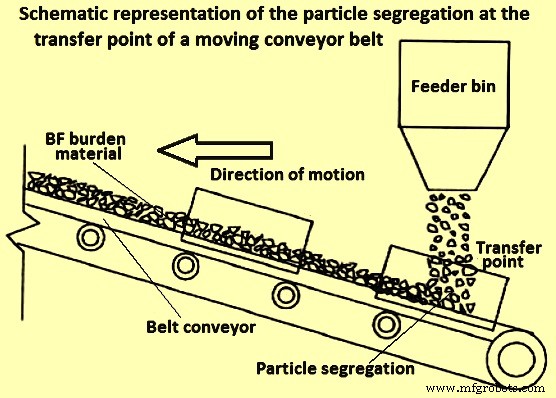
Fig 6 Schematic representation of the particle segregation at the transfer point of a moving conveyor belt
It has been established that there are four main mechanisms to be considered in conveyor belt material movement segregation namely (i) percolation, (ii) particle migration, (iii) trajectory, and (iv) free surface segregation.
Material bins and weigh-hoppers particles behaviour
Granular material bins and weigh hoppers are often used for storage and eventual discharge of material to the subsequent process step. They both in principle have (i) a form of defined material feeding or filling mechanism, (ii) some retention time of material, and (iii) a defined discharge region below. All the three steps have a contribution to the overall material flow behaviour at discharge. Physical and numerical simulations have been done to clarify the relevant information about particle segregation in different kind of hoppers namely cylindrical, bins, conical, and wedge-shaped. The desirable operation is a proportionate outflow from these devices. However, since the flow is gravity induced, the outflow is not easily controlled and there are an inherent induced shear and dynamic effects which cause segregation.
The main prevalent mechanisms of segregation in material storage bins and hoppers are free surface (during feeding), percolation (during retention) and trajectory (during discharging). There is also the importance of particle size and boundary geometry dimensions during the emptying and discharge phases.
In a study to investigate how the internal angle of hoppers affect the granular flow, it has been identified some significant hindrance to free-flow for cohesion-less solids using digital particle image velocimetry (PIV) measurements. As a rule of thumb, to avoid mechanical arching (particle interlocking), the ratio Do/dp (max) is to be satisfied in the range of 5 to 10. Here Do is the boundary outlet diameter and dp (max) is a suitable maximum particle diameter. The ratio is the dimensionless characteristic scale number and it is mostly influenced by the angle of repose as well as the particle size distribution of the material.
In another study, it has been suggested that at least eight elements are to fit across the total width of any granular material handling devices in order to capture accurately the material flow rheology. This means that the diameter of the largest particle fractions in physical or theoretical experimentation is to be at most an eighth the width of a hopper, conveyor belt or any other granular material handling device outlet.
Chute flow particles behaviour
Granular material chute flow is a common feature of stock-house and BLT charging system. With the BLT charging system which comprises of the charge receiving system, material hoppers and rotating chute (distributor), chute flow has assumed additional importance. However, the core principles of the chute flow in the BF top charging system are the same as the one in the stock-house.
Chute flow can be characterized by defining three steps which are (i) burden movement before the chute, (ii) on the chute, and (iii) after the chute, as shown schematically in Fig 7. These three steps constitute three different flow classifications and as such, different considerations need to be employed to study the flow behaviour in this system. When considering burden movement before the chute, any particle collisions in this region can be ignored due to the dilute nature of the flow. When burden material is on the chute, a mathematical description can be used with velocity component along the chute being used as the initial velocity of the material flow. At the chute tip, the trajectory of the materials determines the impact point which in turn the final scatter and distribution of the material in the subsequent handling boundary/ equipment. It is possible that the mechanisms of segregation postulated for conveyor belts systems also apply to chute flow as such and segregation shown schematically in Fig 7 is possible. Three flow streams can be identified with the core flow sandwiched between lower and surface flow. At this stage, the main force considered is gravity.
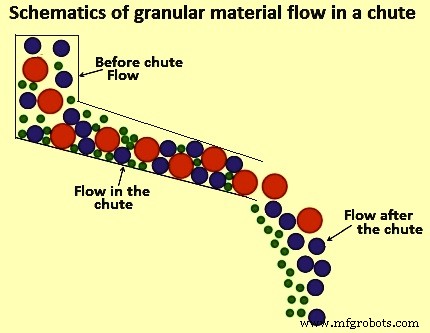
Fig 7 Schematic of granular material flow in a chute
The knowledge of segregation associated with charge material is useful for understanding the charge proportioning in addressing one of the aspects of BF process intensification. However, process intensification in BF processing requires an optimized charging system capacity as BF productivity can be limited by the capacity of stock-house to supply the charge. There is a need to address and optimize multiple-handling operation stages in the product chain.
Charging system capacity analysis
The operation of the BF charging system is as critical as the design of the BF. As can be seen in the schematic representation of a typical modern BF charging system equipped with a conveyor belt delivery system in Fig 8, the material flow sequence is quite complex.
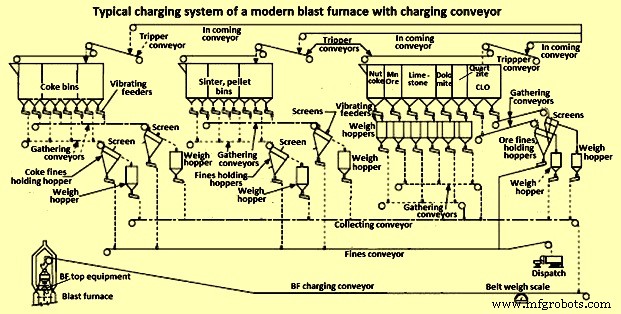
Fig 8 Typical charging system of a modern blast furnace with charging conveyor
In the interest of high productivity, the design of a BF charging system require attention to operating flexibility, availability of extra charging capability, high screening efficiency as well as a limited number of filling, discharge and transfer operations as these cause segregation problems. One important route to increase the efficiency of the BF is full utilization of the charging system capability. Further to this, if the stock-house is not adequately designed and optimal burden delivery is not achieved, the starvation of the BF take place due to the non-availability of the burden materials which consequently results into the loss of BF productivity.
As seen in Fig 8, there are numerous unit operations in a stock-house assembly and all of them have a cascading effect on the overall performance and output delivery to the BLT charging system. In order to understand the macro-behaviour of the burden movement and overall system performance, effective and comprehensive representation of salient system elements and their relationships are to be established. Technically, this involves a description of the various handling steps, materials requirements, duration and sequencing of operations. However, for complex systems such as the stock-house, it is a huge task to clarify all the unit process information. A blend of engineering judgement, experience from similar processes, and reasonable assumptions are used for model development input data and the stock house design.
Modelling of BF charging system optimization
BF charging system involves multiple-handling material movement. The major challenge associated with multiple-handling during materials movement is the timely fulfilling of the requirement and sudden change in the process. Simulations are often used to optimize materials handling systems. Such systems generally use computer-aided process design simulators. These simulators are generally designed to model transient and continuous processes and as such they cannot be used for BF charging system operations which is a batch and semi-continuous process at best. Two available options for modelling batch and semi-continuous processes like BF charging system are spreadsheets (Microsoft Excel) and discrete event simulation (DES).
Spreadsheet models are a common platform that focuses on material balances, equipment sizing and cost analysis. Typically, the development of such a model involves writing an extensive code (in the form of macros and subroutines) in visual basic for applications (VBA) which are incorporated in Microsoft Excel. They are easy to build, much applicable to simple systems but they lack robustness and become unwieldy for large and complex systems. DES is a mathematical/ logical model of a physical system which portrays state changes at precise points in simulated time. Both, the nature of the state change and the time at which the change occurs, mandate precise description. The main feature for a successful DES is an upfront requirement of precise details regarding system and interruptions. Typically, a DES can statistically account for downtime and events. Also, modules can be created and reused while multiple grades or change in process input can be easily handled. Hence, generally the DES-based model is normally used for the BF charging system.
Cyclograms analysis is a modest DES modelling technique which has been often used in BF charging systems for its optimization. The concept evolves on the minimization function of overall start – end sequence (delivery time) of a charging cycle. The delivery time is determined by the order of activation of the mechanisms, the duration of their sequence and the length of the intervals between individual operations. It is easy to follow that the minimum cycle duration occurs when the system is devoid of pauses between the operating cycles of individual mechanisms, as well as when the mechanisms are activated in an efficient sequence.
With cyclograms analysis, it is difficult to incorporate real-time changes in system input conditions. Furthermore, the structure of the analysis precludes detailed in-cooperation of micro-system variables such as discharge behaviour and segregation tendency of materials. Due to these weaknesses of the cyclograms analysis, a DES charge material delivery model based on a mathematical/ logical representation is the better choice for the BF stock house optimization