Proses untuk Benefisiasi Bijih Besi
Proses Pemanfaatan Bijih Besi
Besi adalah unsur yang melimpah di kerak bumi rata-rata dari 2% sampai 3% di batuan sedimen sampai 8,5% di basalt dan gabro. Karena besi terdapat di banyak daerah, nilainya relatif rendah dan dengan demikian deposit harus memiliki persentase logam yang tinggi untuk dianggap sebagai kadar bijih. Biasanya, deposit harus mengandung setidaknya 25% besi untuk dianggap dapat diperoleh secara ekonomis.
Lebih dari 300 mineral mengandung besi tetapi lima mineral merupakan sumber utama bijih besi. Mereka adalah (i) magnetit (Fe3O4), (ii) hematit (Fe2O3), (iii) goetit (Fe2O3.H2O), (iv) siderit (FeCO3), dan (v) pirit (FeS2). Penambangan bijih besi memerlukan pengeboran, peledakan, penghancuran, penyaringan, dan pencampuran bijih.
Penghancuran dan penyaringan merupakan bagian integral dari fasilitas produksi bijih. Penghancuran biasanya melibatkan penghancur primer dan penghancur sekunder yang beroperasi di sirkuit tertutup dengan layar bergetar. Pemilihan peralatan sangat ditentukan oleh kerapuhan bijih. Sebagian besar operasi penyaringan pada bijih kadar tinggi kering kecuali jika fraksi halus dapat ditingkatkan secara efektif dengan desliming.
Bijih besi biasanya termasuk dalam salah satu dari tiga kategori yaitu (i) pengiriman langsung, atau bijih bermutu tinggi, yang mengandung cukup besi untuk dibebankan ke tungku pembuatan besi secara langsung dan mungkin hanya memerlukan penghancuran, penyaringan, dan pencampuran, (ii) terkait bijih niaga kadar rendah yang terjadi di sekitar bijih kadar tinggi yang dapat ditambang secara bersamaan dan yang memerlukan sedikit peningkatan dengan pencucian untuk meningkatkan kandungan besinya, (iii) bijih kadar rendah yang memerlukan penghancuran, penggilingan dan konsentrasi yang ekstensif untuk menghasilkan konsentrat yang dapat diterima. Bijih besi yang termasuk dalam ketiga kategori ini memiliki persyaratan pemrosesan yang sangat berbeda. Untuk mendapatkan produk yang seragam, bijih dengan kadar, komposisi, dan ukuran yang berbeda biasanya dicampur.
Istilah benefisiasi sehubungan dengan bijih besi mencakup semua metode yang digunakan untuk memproses bijih untuk meningkatkan karakteristik kimia, fisik, dan metalurginya dengan cara yang membuatnya menjadi umpan yang lebih diinginkan untuk tungku pembuatan besi. Metode tersebut meliputi penghancuran dan penggilingan, pencucian, penyaringan, penyortiran, ukuran, konsentrasi gravitasi, pemisahan magnetik, flotasi bersama dengan aglomerasi. Operasi benefisiasi menghasilkan dua produk yaitu (i) konsentrat, dan (ii) tailing (limbah), yang dibuang.
Menghancurkan dan menggiling
Benefisiasi dimulai dengan penghancuran dan penggilingan bersama dengan klasifikasi basah atau kering dari bijih yang diekstraksi sebagai persiapan untuk kegiatan lebih lanjut untuk peningkatan kandungan besi bijih. Penghancuran dan penggilingan adalah proses multi-tahap dan dapat menggunakan umpan bijih kering atau basah. Tergantung pada kekerasan bijih, dua, tiga, dan terkadang empat tahap penghancuran, digunakan untuk mengurangi run of mine (ROM) bijih ke ukuran umpan yang dibutuhkan. Penghancuran primer dan sekunder biasanya dilakukan dengan penghancur gyratory atau cone. Jaw crusher jarang memiliki kapasitas atau daya tahan untuk digunakan sebagai unit penghancur utama kecuali bijihnya sangat lunak. Penghancuran tersier hingga ukuran atas 25 mm biasanya dilakukan dengan penghancur kepala pendek yang beroperasi di sirkuit tertutup dengan saringan. Biasanya, penghancuran primer, penghancuran sekunder, dan penyaringan dilakukan di lokasi tambang.
Investasi modal dan biaya operasi penghancuran dan penggilingan sangat besar. Oleh karena itu, ekonomi memainkan peran penting dalam menentukan penggunaan peralatan ini dan tingkat penghancuran dan penggilingan yang akan dilakukan dari bijih untuk pemanfaatan lebih lanjut. Faktor penting lainnya termasuk konsentrasi nilai bijih, mineralogi, kekerasan, dan kadar airnya.
Setelah penghancuran awal, penggilingan halus mengurangi partikel bijih menjadi konsistensi bubuk halus (325 mesh, 0,44 mikron). Pilihan sirkuit penggilingan didasarkan pada kepadatan dan kekerasan bijih yang akan digiling. Meskipun penggunaan penggilingan rod atau ball mill cukup umum, beberapa fasilitas menggunakan sistem penggilingan autogenous atau semi autogenous. Penggilingan autogenous menggunakan potongan kasar bijih itu sendiri sebagai media penggilingan di pabrik penggilingan. Operasi semi autogenous menggunakan bola logam dan/atau batang untuk melengkapi aksi penggilingan dari potongan bijih. Penggilingan autogenous paling cocok untuk bijih yang disemen lemah yang mengandung beberapa bahan keras. Manfaat penggilingan autogenous adalah lebih sedikit modal dan padat karya. Penggilingan semi autogenous menghilangkan kebutuhan akan sirkuit penghancur sekunder. Keausan batang dan bola, biaya perawatan utama penggiling tradisional, juga dihilangkan dengan metode ini.
Pabrik batang biasanya dirancang untuk menggiling secara normal dengan umpan minus 35 mm hingga minus 3 mesh. Mereka adalah pabrik tumbling dengan rasio panjang terhadap diameter 1,5 hingga 2,0. Media penggilingan adalah batang baja dengan diameter hingga 100 mm. Bijihnya digiling basah dengan kandungan padat sekitar 68% sampai 80%. Ukuran produk dikendalikan oleh kombinasi laju umpan, karakteristik pengisian batang, kecepatan penggilingan, kerapatan bubur, dan viskositas.
Ball mill adalah sarana utama penggilingan halus bijih besi. Mereka adalah pabrik yang jatuh seperti pabrik batang, tetapi biasanya dengan rasio panjang dan diameter yang lebih kecil yang berkisar hingga 1,5. Media penggilingan adalah bola baja, bukan batang. Efisiensi penggilingan sangat dipengaruhi oleh efisiensi klasifikasi dan parameter operasi penggilingan seperti kecepatan penggilingan, pengisian media, kepadatan bubur dan viskositas.
Pabrik kerikil juga digunakan untuk penggilingan halus. Mereka mirip dengan pabrik bola kecuali bahwa mereka diisi dengan kerikil 25 mm sampai 100 mm daripada bola baja. Keuntungan utama mereka adalah bahwa media penggilingan baja tidak diperlukan dan keausan mill liner berkurang. Namun mereka biasanya memiliki konsumsi daya yang tinggi.
Di antara setiap operasi unit penggilingan, hidro-siklon digunakan untuk mengklasifikasikan partikel kasar dan halus. Partikel kasar dikembalikan ke pabrik penggilingan untuk pengurangan ukuran lebih lanjut. Bijih giling dalam bentuk slurry dipompa ke tahap benefisiasi berikutnya. Jika bijih yang digiling dimaksudkan untuk kegiatan flotasi, reagen kimia yang digunakan selama proses biasanya ditambahkan ke bubur selama tahap ini.
Flotasi
Flotasi efektif untuk konsentrasi bijih besi halus (minus 100 mesh). Proses flotasi tergantung pada fakta bahwa reagen tertentu yang ditambahkan ke suspensi air dari bijih besi yang digiling halus secara selektif menyebabkan mineral oksida besi atau partikel gangue menunjukkan afinitas terhadap udara. Mineral yang memiliki afinitas untuk melekat pada gelembung udara dan melewati suspensi, dikeluarkan dari suspensi sebagai produk buih. Faktor penting untuk keberhasilan kegiatan flotasi meliputi keseragaman ukuran partikel, penggunaan reagen yang kompatibel dengan bijih, dan kondisi air yang tidak mengganggu perlekatan reagen ke bijih atau gelembung udara.
Empat jenis reagen kimia berikut biasanya digunakan dalam flotasi.
- Kolektor/amina – Mereka adalah reagen yang ditambahkan untuk menginduksi afinitas preferensial terhadap udara. Mereka menyebabkan perlekatan antara partikel padat dan gelembung udara dalam sel flotasi.
- Buih – Mereka adalah zat yang ditambahkan untuk menyebabkan pembentukan gelembung atau buih yang stabil. Mereka digunakan untuk menstabilkan gelembung udara dengan mengurangi tegangan permukaan, sehingga memungkinkan pengumpulan material berharga dengan membaca sekilas dari bagian atas sel.
- Antifoams – Mereka bereaksi dengan permukaan partikel di sel flotasi untuk menjaga bahan agar tidak tertinggal di buih. Sebaliknya, material jatuh ke dasar sebagai tailing.
- Zat lain – Mereka ditambahkan untuk tujuan kontrol seperti penyesuaian pH, atau untuk menyebabkan dispersi atau flokulasi yang lebih baik dikenal sebagai pengubah, dispersan, dan depresan.
Faktor penting ketika mengkondisikan bijih untuk flotasi dengan reagen kimia, termasuk pencampuran menyeluruh dan penyebaran reagen melalui pulp, kontak berulang antara reagen dan semua partikel bijih yang relevan, dan waktu untuk pengembangan kontak dengan reagen dan partikel bijih untuk menghasilkan reaksi yang diinginkan.
Reagen dapat ditambahkan dalam beberapa bentuk termasuk padatan, cairan yang tidak dapat bercampur, emulsi, dan larutan dalam air. Konsentrasi reagen biasanya dikontrol ketat selama pengkondisian. Penambahan reagen lebih dari yang dibutuhkan dapat memperlambat reaksi dan mengurangi efisiensi.
Tren saat ini adalah menuju pengembangan sel flotasi yang lebih besar dan lebih hemat energi. Pulp yang mengandung bijih giling, reagen flotasi, dan air diumpankan ke sel flotasi. Biasanya, 10 hingga 14 sel disusun secara berurutan dari yang lebih kasar ke pemulung. Kasar digunakan untuk membuat pemisahan kasar mineral logam bantalan besi (nilai) dari gangue. Pemulung memulihkan jumlah yang lebih kecil dari nilai yang tersisa dari pulp. Pulp bergerak dari sel yang lebih kasar ke pemulung saat nilainya dihilangkan. Konsentrat yang diperoleh kembali dari buih di sel roughing dan scavenging dikirim ke sel pembersih untuk menghasilkan konsentrat mineral logam bantalan besi akhir.
Kolektor flotasi terdiri dari dua jenis umum yaitu (i) anionik, dan (ii) kationik. Kolektor anionik terionisasi dalam larutan sehingga spesies aktif (yang menempel pada permukaan mineral bermuatan positif) bermuatan negatif. Sebaliknya, spesies ion aktif dalam pengumpul flotasi kationik bermuatan positif.
Aplikasi utama dari flotasi anionik adalah untuk mengapungkan mineral bantalan besi dari material gangue. Kolektor yang paling umum digunakan adalah asam lemak atau petroleum sulfonat. Bahan bakar minyak sering ditambahkan bersama dengan pengumpul untuk mendorong pemulihan partikel oksida besi yang lebih halus dari sekitar 10 mikron. Sebaliknya, flotasi kationik digunakan untuk mengapungkan gangue menjauh dari bijih mentah yang digiling halus dan untuk menghilangkan sejumlah kecil material gangue dari beberapa konsentrat bijih. Kolektor kationik adalah amina atau diamina alifatik primer, beta-amina, atau amina eter, umumnya dalam bentuk asetat.
Limbah dari sel flotasi dikumpulkan dari bendung pelimpah tailing. Tergantung pada tingkat buih, itu didaur ulang untuk pemulihan lebih lanjut dari unit besi atau dibuang sebagai ekor. Tailing mengandung gangue yang tersisa, mineral besi yang belum ditemukan, reagen kimia, dan air limbah proses. Umumnya, tailing diproses ke pengental sebelum pergi ke penimbunan tailing. Kandungan padatan dari bubur bervariasi berkisar antara 30% sampai 60%. Setelah pengentalan, tailing dipompa ke penampung dan padatan didaur ulang untuk pemanfaatan lebih lanjut guna mengumpulkan nilai yang tersisa, dan air yang telah dijernihkan dikembalikan ke proses penghancuran dan penggilingan. Di kolam tailing, padatan dikeluarkan dari suspensi dan komponen cair didaur ulang ke pabrik penggilingan. Reagen kimia yang digunakan dalam flotasi umumnya menempel pada partikel tailing dan tetap berada di penahan tailing.
Penebalan/pemfilteran
Pengental digunakan untuk menghilangkan sebagian besar cairan dari konsentrat bubur dan bubur limbah (tailing). Teknik pengentalan biasanya digunakan dalam dua fase produksi bijih besi yaitu (i) konsentrat dikentalkan untuk mengurangi kadar air dan mendapatkan kembali air, dan (ii) tailing yang dibubur dikentalkan untuk mendapatkan kembali air. Fasilitas biasanya menggunakan sejumlah pengental secara bersamaan.
Biasanya, operasi bijih besi menggunakan pengental terus menerus yang dilengkapi dengan mekanisme penggaruk untuk menghilangkan padatan. Beberapa variasi garu biasanya digunakan dalam pengental. Ketika konsentrat dikentalkan, aliran bawah dari pengental (konsentrat) dikumpulkan dan diolah lebih lanjut dalam filter vakum cakram keramik. Filter menghilangkan sebagian besar sisa air dari konsentrat. Komponen cair yang dihilangkan selama proses pengentalan dapat mengandung reagen flotasi, dan/atau produk mineral terlarut dan tersuspensi. Cairan biasanya didaur ulang ke kolam penampungan untuk digunakan kembali di pabrik penggilingan. Ketika konsentrat dikentalkan, bahan padat yang dihasilkan dari operasi ini dikumpulkan sebagai konsentrat akhir untuk aglomerasi dan pemrosesan lebih lanjut. Tailing yang kental dibuang ke penampungan tailing.
Konsentrasi gravitasi
Konsentrasi gravitasi secara luas digunakan dalam benefisiasi bijih besi hematit. Teknologi ini digunakan untuk menangguhkan dan mengangkut gangue yang lebih ringan dari mineral berharga yang lebih berat. Proses pemisahan ini terutama didasarkan pada perbedaan berat jenis bahan dan ukuran partikel yang dipisahkan. Nilai dapat dihilangkan bersama dengan bahan gangue (tailing) meskipun ada perbedaan densitas jika ukuran partikel bervariasi. Karena masalah potensial ini, ukuran partikel harus dijaga tetap seragam dengan penggunaan pengklasifikasi (seperti saringan dan siklon hidro). Tiga metode pemisahan gravitasi secara historis telah digunakan untuk bijih besi yaitu (i) pencucian, (ii) jigging, dan (iii) pemisah media berat. Spiral dan kerucut reichert adalah dua metode lain untuk pemisahan gravitasi.
Limbah dari konsentrasi gravitasi adalah tailing yang terdiri dari gangue berupa partikel berbutir kasar dan halus serta air proses. Bahan ini dipompa sebagai bubur ke kolam tailing. Kandungan padat dari bubur bervariasi dengan setiap operasi, berkisar antara 30% sampai 60%. Setelah pemisahan padatan di kolam tailing, air tailing dapat didaur ulang atau dibuang.
Mencuci
Pencucian adalah proses konsentrasi bijih besi paling sederhana yang memanfaatkan gravitasi spesifik yang tinggi dan ukuran mineral bantalan besi yang relatif kasar untuk memisahkannya dari gangue silika yang lebih halus, lebih ringan, yang didominasi mineral kuarsa dan lempung. Bijih disiapkan untuk pencucian dengan menghancurkan dalam satu atau dua tahap hingga ukuran lebih halus dari 50 mm. Bijih yang dihancurkan diumpankan ke mesin cuci log. Agitasi bijih yang intens dengan dayung (mirip dengan pabrik pug modern) dikombinasikan dengan aliran balik air secara efisien bolak-balik dan menghilangkan silika halus untuk meninggalkan produk kaya besi residu kasar. Luapan mesin cuci log sering kali mundur dalam pengklasifikasi penggaruk atau spiral untuk memulihkan besi halus tambahan. Beberapa pabrik pencucian menggunakan pengklasifikasi spiral dalam satu atau dua tahap tanpa mesin cuci log pada bijih yang mengandung jumlah minimum gangue tanah liat lengket. Pengklasifikasi pengendapan terhalang dari berbagai jenis juga terkadang digunakan untuk memulihkan besi halus.
Berjoget
Jigging adalah bentuk benefisiasi yang lebih kompleks daripada pencucian sederhana dan digunakan pada bijih yang lebih keras yang memerlukan penghancuran untuk memecah lapisan kaya gangue. Jig yang digunakan untuk benefisiasi bijih besi pada dasarnya adalah layar horizontal yang membawa lapisan bijih sedalam 150 mm sampai 250 mm. Bijih diumpankan di salah satu ujungnya dan distratifikasi oleh aksi denyut air, baik yang disebabkan oleh pompa berosilasi atau oleh gerakan fisik naik turun dari jig screen itu sendiri. Saat bijih bergerak ke bawah geladak, denyutan tersebut memungkinkan partikel yang lebih ringan untuk bekerja ke atas lapisan, sementara partikel kaya besi yang lebih berat terpisah di sepanjang dasar. Kedua produk dipisahkan di ujung jig, partikel yang lebih ringan di atas bendungan pelepasan dan konsentrat bijih besi di bawah bagian bawah. Jig bijih besi bekerja paling baik pada partikel mulai dari 1 mm hingga 25 m.
Pemisahan media berat
Perangkat pemisahan media berat telah dikembangkan pada 1950-an sebagai alternatif yang lebih efektif untuk jigging untuk peningkatan bijih besi. Proses pemisahan media berat beroperasi pada prinsip wastafel dan pelampung. Suspensi ferosilikon halus (minus 200 mesh) dalam air digunakan untuk membuat media fluida dengan berat jenis sekitar 3,0. Partikel kaya silika dengan berat jenis sekitar 2,6 mengapung di permukaan media tersebut sementara partikel bijih besi yang lebih padat dan lebih berat dengan berat jenis lebih dari 4,0 mengendap di dasar. Media konvensional untuk pemekatan bijih kasar adalah ferosilikon yang mengandung 15% silikon dan 85% besi. Suspensi air yang mengandung 64% hingga 85% dari ferrosilicon yang digiling halus memiliki berat jenis berkisar antara 2,2 hingga 3,6.
Bejana pemisah untuk bijih kasar (ditambah 9 mm) biasanya adalah pengklasifikasi spiral, pengklasifikasi rake atau drum berputar. Bijih yang lebih halus dari 9 mm dan lebih kasar dari 3 mm dapat dipisahkan dalam siklon media berat dimana gaya gravitasi tinggi mempercepat pengendapan partikel bijih besi berat. Magnetit yang digiling halus digunakan untuk membuat media berat untuk pemisah siklon daripada ferosilikon. Dinamika siklon menciptakan kepadatan dan fluiditas media yang dibutuhkan meskipun gravitasi spesifik magnetit lebih rendah. Selanjutnya biaya magnetit jauh lebih murah daripada ferrosilicon tanah.
Medium, ferosilikon dan magnetit, dicuci dari bak cuci dan produk terapung pada saringan halus yang dilengkapi dengan bak cuci dan semprotan air dan diambil dari air cucian dengan pemisah magnetik dan didaur ulang.
Spiral
Spiral, pertama kali dikembangkan untuk pengolahan pasir pantai, digunakan dalam konsentrasi bijih besi untuk mengolah bijih minus 6 mesh (3,36 mm) hingga 100 mesh (0,149 mm). Efisiensi di bawah 100 mesh menurun dengan cepat dan spiral tidak efektif pada material yang lebih halus. Spiral biasanya dioperasikan pada kepadatan pulp 25% hingga 30% padatan.
Spiral banyak digunakan untuk pemulihan tambahan besi halus dari jenis bijih pedagang dan merupakan perangkat konsentrasi utama untuk bijih hematit specular dari palung Labrador dan bijih serupa yang dapat dibebaskan dengan menggiling tidak lebih halus dari 20 mesh.
Konsentrator spiral adalah perangkat pemisahan film yang mengalir. Operasi umum adalah aliran laminar gravitasi terus menerus ke bawah pada permukaan miring. Mekanisme pemisahannya melibatkan pola aliran primer dan sekunder. Aliran primer pada dasarnya adalah slurry yang mengalir menuruni palung spiral di bawah gaya gravitasi. Pola aliran sekunder adalah radial melintasi palung. Di sini lapisan fluida paling atas yang terdiri dari partikel dengan kepadatan lebih tinggi bergerak menjauh dari pusat sedangkan lapisan konsentrat paling bawah dari partikel dengan kepadatan lebih tinggi bergerak menuju pusat. Spiral memerlukan penambahan air di berbagai titik di bawah spiral untuk membantu pencucian bijih besi, yaitu memindahkan gangue ringan dari bijih padat. Jumlah air cucian dan distribusinya ke bawah melalui palung spiral dapat disesuaikan untuk memenuhi persyaratan pengoperasian. Kontrol titik meminimalkan total kebutuhan air dengan mengarahkan air secara efisien ke pulp yang mengalir pada sudut yang paling efektif.
Konsentrator spiral adalah palung bawah melengkung, melilit sumbu vertikal dalam bentuk heliks. Ketika diberi makan di bagian atas dengan bubur bijih besi dan gangue, gangue yang kurang padat, lebih mudah tersuspensi oleh air, mencapai kecepatan tangensial yang lebih besar daripada mineral besi, dan bermigrasi ke tepi luar palung spiral. Air pencuci yang ditambahkan di sepanjang tepi bagian dalam membantu menghilangkan gangue yang lebih ringan. Setelah beberapa putaran, sebuah pita mineral besi terbentuk di sepanjang tepi bagian dalam, dan gangue membentuk pita-pita ke arah tepi luar. Lubang ditempatkan di sepanjang tepi bagian dalam untuk mengumpulkan dan membuang mineral besi.
Gangue tetap berada di spiral dan terlepas di bagian bawah.
Kerucut Reichert
Keuntungan prinsip untuk kerucut Reichert adalah kapasitas dan kemampuan untuk memulihkan mineral berat halus secara efisien hingga sekitar 325 mesh, lebih halus daripada yang dapat dicapai dalam spiral. Sebuah kerucut Reichert tunggal memiliki kapasitas hingga 100 ton per jam dan dapat digunakan secara efektif untuk memulihkan denda hematit specular .
Kerucut Reichert adalah konsentrator film yang mengalir. Partikel yang lebih padat terkonsentrasi di bagian bawah film mengalir dari bubur yang memiliki kandungan padat sekitar 60% berat. Mekanisme pemisahan adalah kombinasi dari pengendapan partikel padat dan tetesan interstisial partikel halus. Elemen pemisah dalam unit Reichert adalah kerucut berdiameter 1,9 m miring ke dalam. Pulp umpan didistribusikan secara merata di sekitar pinggiran kerucut. Saat pulp mengalir secara gravitasi menuju pusat, partikel halus dan berat terkonsentrasi di bagian bawah dan dikeluarkan melalui slot annular di dekat puncak kerucut. Tailing mengalir di atas slot dan dikumpulkan di puncak atau pusat kerucut. Karena efisiensi proses pemisahan ini relatif rendah, proses ini diulang beberapa kali dalam susunan kerucut tunggal yang ditumpuk untuk meningkatkan perolehan kembali. Umumnya, konsentrat kelas tertinggi diproduksi di kerucut pemisahan utama.
Pemisahan magnet
Pemisahan magnetik biasanya digunakan untuk memisahkan bijih besi magnetik alami (magnetit) dari berbagai bahan yang kurang magnetik atau nonmagnetik. Selama pemisahan magnetik, sebagian besar unit besi yang diuntungkan hilang menjadi tailing karena hematit hanya bersifat magnetis lemah.
Pemisahan magnetik dilakukan di lingkungan kering atau basah. Sistem basah lebih umum. Pemisahan magnetik bijih besi dapat dikategorikan sebagai intensitas rendah atau tinggi. Pemisah intensitas rendah menggunakan medan magnet antara 1000 dan 3000 gauss. Teknik intensitas rendah biasanya digunakan pada bijih magnetit dan merupakan metode pemisahan yang murah dan efektif. Metode intensitas rendah hanya menangkap bahan yang sangat magnetis (magnetit). Pemisah intensitas tinggi menggunakan medan sekuat 20.000 gauss. Metode ini digunakan untuk memisahkan mineral besi magnetik lemah (hematit) dari bahan gangue nonmagnetik atau kurang magnetik. Faktor lain yang penting dalam menentukan jenis sistem pemisah magnetik yang digunakan termasuk ukuran partikel dan kandungan padatan dari umpan bubur bijih.
Beberapa jenis teknologi pemisahan magnetik digunakan. Ini dijelaskan di bawah ini.
- Basah dan kering, pemisahan magnetik intensitas rendah (LIMS)
- Pemisahan magnetik gradien tinggi (HGMS)
- Pemisahan magnetik intensitas tinggi basah (WHIMS)
- Gulung pemisah magnetik untuk memproses bijih magnetik lemah
- Pemisahan magnet rol induksi (IRMS) untuk pemekatan bijih kering
Mekanisme lain yang digunakan termasuk katrol magnetik, pemisah gulungan terinduksi, pemisah sabuk silang, dan pemisah tipe cincin.
Biasanya, pemisahan magnetik melibatkan tiga tahap pemisahan. Ini adalah (i) cobbing, (ii) pembersihan / roughing, dan (iii) finishing. Setiap tahap menggunakan beberapa drum secara berurutan untuk meningkatkan efisiensi pemisahan. Setiap tahap berturut-turut bekerja pada partikel yang lebih halus sebagai hasil dari penghilangan partikel yang terlalu besar pada pemisahan sebelumnya. Cobbers bekerja pada partikel yang lebih besar (9 mm) dan menolak sekitar 40% umpan sebagai ekor. Pemisahan kering intensitas rendah kadang-kadang digunakan dalam tahap cobbing dari proses pemisahan. Pembersih atau pemulung bekerja pada partikel dalam kisaran 48 mesh (0,32 mm) dan membuang hanya 10% hingga 15% dari umpan sebagai ekor. Terakhir, finisher mengerjakan partikel bijih kurang dari 100 mesh (0,149 mm) dan menghilangkan sisa 5% gangue. Ini karena sifat pakan yang sangat terkonsentrasi pada tahap ini.
Proses basah intensitas rendah biasanya melibatkan konveyor dan pemisah drum putar menggunakan magnet permanen dan terutama digunakan pada partikel bijih berukuran 9 mm atau kurang. Dalam proses ini, bijih diumpankan oleh konveyor ke dalam separator di mana partikel magnetit ditarik dan ditahan di sisi drum sampai dibawa keluar dari medan magnet dan dipindahkan ke penerima konsentrat yang sesuai. Bahan gangue nonmagnetik atau kurang magnetis tetap ada dan dikirim ke kolam tailing. Dalam beberapa operasi, beberapa drum dipasang secara seri untuk memaksimalkan pemulihan.
Pemisah basah intensitas tinggi menghasilkan gradien medan magnet tinggi dengan menggunakan matriks potongan besi berbentuk yang bertindak sebagai tempat pengumpulan partikel paramagnetik. Bentuk ini dapat mencakup bola, batang, pelat beralur, logam yang diperluas, dan serat.
Limbah utama dari jenis operasi ini adalah tailing yang terdiri dari gangue dalam bentuk partikel berbutir kasar dan halus, dan bubur air limbah dalam hal pemisahan basah. Limbah partikulat dari pemisahan kering juga dapat menjadi bubur. Setelah pemisahan padatan di pengental atau kolam pengendapan, padatan dikirim ke penampung tailing dan komponen cair dapat didaur ulang ke pabrik atau dibuang jika kriteria kualitas air terpenuhi.
Pemisahan magnetik intensitas tinggi basah (WHIMS) dikembangkan untuk memulihkan unit besi non-magnetik, Mereka dapat diterapkan secara efektif di berbagai ukuran partikel yang luas mulai dari 10 mesh (2 mm) hingga 500 mesh tergantung pada matriks yang digunakan. Aplikasi WHIMS termasuk pemulihan besi dari bijih halus alam, peningkatan konsentrat spiral, dan pemulihan hematit dari tailing. Dalam pemisahan magnetik intensitas tinggi basah (WHIMS), elektromagnet menghasilkan medan magnet berkekuatan sangat tinggi yang diterapkan pada matriks yang terdiri dari bola baja, pelat beralur spasi, wol baja atau potongan logam yang diperluas. Matriks terkandung dalam cincin melingkar yang diputar di antara magnet intensitas tinggi. Bubur bijih besi diperkenalkan pada titik di mana matriks berada di lapangan. Gradien magnetik tinggi yang berkembang di sekitar matriks menahan hematit sementara gangue dicuci. Konsentrat hematit dilepaskan dan dikeluarkan saat matriks bergerak keluar dari medan magnet.
Gambar 1 menunjukkan diagram skema spiral dan WHIMS.
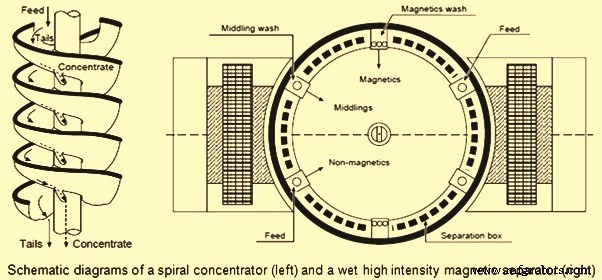
Gbr 1 Skema diagram spiral dan WHIMS