Proses Penempaan Logam
Proses Penempaan Logam
Penempaan logam adalah proses deformasi di mana logam ditekan, ditumbuk atau diperas di bawah tekanan besar menjadi bagian kekuatan tinggi yang dikenal sebagai tempa logam. Proses penempaan sama sekali berbeda dari proses pengecoran (atau pengecoran), karena logam yang digunakan untuk membuat bagian yang ditempa tidak dilebur atau dituangkan seperti dalam proses pengecoran.
Penempaan didefinisikan sebagai proses pengerjaan logam di mana bentuk spesifik benda kerja logam diperoleh dalam keadaan padat dengan gaya tekan yang diterapkan melalui penggunaan cetakan dan alat. Selama proses penempaan, deformasi logam yang terkontrol terjadi. Proses penempaan dilakukan dengan cara memalu atau menekan logam. Di zaman modern, penempaan industri dilakukan baik dengan pengepres atau dengan palu yang ditenagai oleh udara bertekanan, listrik, hidrolik, atau uap.
Semua logam dan paduan dapat ditempa, tetapi peringkat ketertempaan logam dan paduan yang berbeda dapat bervariasi dari tinggi ke rendah atau buruk. Faktor-faktor yang terlibat adalah komposisi, struktur kristal dan sifat mekanik semua dipertimbangkan dalam kisaran suhu. Semakin lebar rentang suhu, semakin tinggi peringkat forgeability. Sebagian besar penempaan dilakukan pada benda kerja yang dipanaskan. Penempaan dingin juga dapat dilakukan pada suhu ruangan.
Proses penempaan adalah salah satu proses pengerjaan logam tertua yang diketahui dengan asalnya sekitar ribuan tahun yang lalu. Prosesnya kembali ke 8000 SM dan berevolusi dari seni manual pandai besi sederhana. Secara tradisional, penempaan dilakukan oleh seorang pandai besi menggunakan palu dan landasan. Menggunakan palu dan landasan adalah bentuk kasar dari penempaan. Bengkel atau bengkel telah berevolusi selama berabad-abad. Kemudian seperti sekarang, serangkaian pukulan palu tekan melakukan pembentukan atau penempaan bagian tersebut. Penempaan modern menggunakan palu atau penekan yang digerakkan oleh mesin yang mengubah bentuk benda kerja dengan tekanan yang terkontrol.
Proses penempaan lebih unggul daripada pengecoran karena bagian yang terbentuk memiliki struktur mikro yang lebih padat, pola butir yang lebih jelas, dan porositas yang lebih sedikit, membuat bagian tersebut jauh lebih kuat daripada pengecoran.
Penempaan menghaluskan struktur butir dan meningkatkan sifat mekanik logam. Dengan desain yang tepat, aliran butir dapat diorientasikan ke arah tegangan utama yang dihadapi dalam penggunaan sebenarnya. Aliran butir adalah arah pola yang diambil kristal selama deformasi plastis. Sifat mekanik (seperti kekuatan, keuletan dan ketangguhan) jauh lebih baik dalam penempaan daripada di logam dasar, yang memiliki kristal yang berorientasi secara acak. Aliran butir terarah penempaan memastikan kekuatan bagian yang tinggi dengan ketahanan lelah yang unggul, sifat mekanik, dan kesehatan metalurgi. Penempaan menghilangkan rongga internal dan porositas, dan menghasilkan integritas struktural yang tak tertandingi.
Proses penempaan menghasilkan bagian-bagian dengan sifat mekanik yang unggul dengan limbah material yang minimum. Bahan awal dalam proses penempaan memiliki geometri yang relatif sederhana. Material ini mengalami deformasi plastis dalam satu atau beberapa operasi menjadi produk dengan konfigurasi yang relatif kompleks. Penempaan biasanya membutuhkan perkakas yang relatif mahal. Oleh karena itu, proses ini menarik secara ekonomi ketika sejumlah besar komponen akan diproduksi dan/atau ketika sifat mekanik yang dibutuhkan dalam produk jadi hanya dapat diperoleh dengan proses penempaan.
Klasifikasi proses penempaan
Proses penempaan dapat diklasifikasikan dengan cara yang berbeda berikut ini.
Berdasarkan suhu benda kerja
Berdasarkan temperatur benda kerja yang ditempa, proses penempaan dapat berupa (i) penempaan panas, (ii) penempaan hangat, dan (iii) penempaan dingin.
Penempaan panas
Penempaan panas adalah proses penempaan yang paling banyak digunakan. Pada proses hot forging, penempaan dilakukan pada suhu di atas suhu rekristalisasi logam yang berarti pada suhu di mana butir-butir baru terbentuk pada logam. Panas ekstrem semacam ini diperlukan untuk menghindari pengerasan regangan logam selama deformasi.
Dalam kondisi nyata selama manufaktur industri, gesekan berperan dalam proses. Gaya gesekan pada antarmuka die-work menentang penyebaran material di dekat permukaan, sedangkan material di tengah dapat mengembang lebih mudah. Hasilnya adalah membuat bentuk barel pada bagian tersebut. Efek ini disebut barreling dalam istilah penempaan logam. Barreling umumnya tidak diinginkan dan dapat dikontrol dengan menggunakan pelumasan yang efektif. Pertimbangan lain, selama pembuatan hot forging, yang biasanya meningkatkan efek barreling, adalah perpindahan panas antara logam panas dan die yang lebih dingin. Logam yang lebih dekat ke permukaan cetakan mendingin lebih cepat daripada logam di bagian tengah. Material yang lebih dingin lebih tahan terhadap deformasi dan mengembang lebih sedikit daripada material yang lebih panas di bagian tengah, juga menyebabkan efek barreling.
Keuntungan dari penempaan panas adalah (i) laju regangan tinggi dan karenanya aliran logam mudah, (ii) rekristalisasi dan pemulihan dimungkinkan, dan (iii) gaya yang dibutuhkan lebih sedikit. Kerugian dari penempaan panas adalah (i) pelumasan pada suhu tinggi sulit; (ii) oksidasi dan penskalaan terjadi pada benda kerja, (iii) permukaan akhir yang buruk, (iv) toleransi presisi yang lebih rendah, dan (v) kemungkinan pembengkokan material selama proses pendinginan.
Penempaan hangat
Pada proses warm forging, temperatur pada saat forging dapat berkisar dari diatas temperatur kamar sampai dibawah temperatur rekristalisasi. Dalam penempaan hangat, benda kerja dipanaskan di bawah suhu rekristalisasi logam (hingga 700 derajat C hingga 800 derajat C untuk baja), untuk menurunkan tegangan aliran dan tekanan penempaan.
Bagian dengan aliran radial seperti konfigurasi bulat dengan flensa tengah, bagian persegi panjang, dan bagian non-aksisimetris dengan simetri 3 kali lipat dan 6 kali lipat telah diproduksi oleh ekstrusi hangat. Ada kalanya praktik penempaan hangat lebih dipilih daripada penempaan dingin terutama untuk baja dengan kadar karbon lebih tinggi atau di mana anil dalam proses dapat dihilangkan.
Dibandingkan dengan penempaan dingin, penempaan hangat memiliki potensi keuntungan (i) mengurangi beban perkakas, (ii) mengurangi beban tekan, (iii) meningkatkan keuletan logam, (iv) menghilangkan kebutuhan untuk anil sebelum penempaan, dan (v) menguntungkan sifat as-forged yang dapat menghilangkan perlakuan panas. Keuntungan dari penempaan hangat adalah (i) tingkat produksi yang tinggi, (ii) toleransi dimensi yang baik dan permukaan akhir untuk bagian yang ditempa, (iii) penghematan yang signifikan dalam material dan permesinan, (iv) aliran butir yang baik untuk meningkatkan kekuatan, dan (v) ketangguhan yang lebih besar dari bagian yang ditempa.
Penempaan dingin
Sebagian besar penempaan dilakukan sebagai pekerjaan panas, pada suhu hingga 1250 derajat C. Penempaan dingin mencakup banyak proses seperti pembengkokan, penarikan dingin, pos dingin, meninju, ekstrusi, penggulungan benang dan banyak lagi, untuk menghasilkan beragam bentuk bagian. Ini termasuk berbagai komponen seperti poros, geometri berbentuk cangkir, bagian berongga dengan batang dan poros, semua jenis konfigurasi kesal (berkepala) dan bengkok, serta kombinasi. Dengan penempaan dingin batang baja, kawat, atau batangan, bagian seperti poros dengan 3-bidang tikungan dan fitur desain kepala tidak jarang. Suku cadang tipikal paling hemat biaya dalam kisaran 5 kg atau kurang. Bagian simetris hingga 3 kg siap untuk pemrosesan otomatis. Pilihan material berkisar dari baja paduan rendah dan baja karbon hingga baja tahan karat seri 300 dan 400, paduan aluminium pilihan, kuningan, dan perunggu.
Dalam prosesnya, bar slug yang dilumasi secara kimia dipaksa masuk ke dalam die tertutup di bawah tekanan ekstrem. Logam yang tidak dipanaskan dengan demikian mengalir ke dalam bentuk yang diinginkan. Dalam kasus ekstrusi maju, baja mengalir ke arah gaya ram. Ini digunakan ketika diameter batang dikurangi dan panjangnya bertambah. Ekstrusi mundur, di mana logam mengalir berlawanan dengan gaya ram, menghasilkan bagian berongga. Dalam gangguan, logam mengalir pada sudut yang tepat terhadap gaya ram sehingga meningkatkan diameter dan mengurangi panjangnya.
Selama proses penempaan dingin, penempaan dilakukan pada atau mendekati suhu kamar dari logam. Baja karbon dan baja paduan standar paling sering ditempa dingin. Penempaan dingin umumnya lebih disukai saat logam sudah lunak, seperti aluminium. Proses ini biasanya lebih murah daripada penempaan panas dan produk akhir membutuhkan sedikit atau tanpa pekerjaan finishing. Penempaan dingin juga kurang rentan terhadap masalah kontaminasi, dan komponen akhir memiliki permukaan akhir yang lebih baik secara keseluruhan. Keuntungan dari penempaan dingin termasuk (i) tingkat produksi sangat tinggi dengan umur cetakan yang luar biasa, (ii) meningkatkan sifat mekanik, (iii) lebih sedikit gesekan antara permukaan cetakan dan benda kerja, (iv) pelumasan mudah, (v) tidak ada oksidasi atau penskalaan pada pekerjaan. Kerugian dari penempaan dingin termasuk (i) dapat terjadi tegangan sisa, (ii) peralatan tempa yang lebih berat dan lebih kuat diperlukan, (iii) perkakas yang lebih kuat diperlukan, dan (iv) desain dan manufaktur pahat sangat penting.
Sering dipilih untuk fitur desain integral seperti flensa dan bos built-in, tempa dingin sering digunakan di bagian kemudi dan suspensi otomotif, sistem pengereman anti-lock, perangkat keras, komponen pertahanan, dan aplikasi lain di mana kekuatan tinggi, toleransi dekat dan produksi volume membuat mereka pilihan yang ekonomis.
Berdasarkan peralatan penempaan
Komponen yang ditempa dibentuk baik dengan palu atau tekan. Penempaan pada palu dilakukan secara berurutan dari cetakan cetakan menggunakan pukulan berulang. Kualitas penempaan, dan ekonomi serta produktivitas proses hammer bergantung pada perkakas dan keterampilan operator. Dalam penempaan tekan, benda kerja umumnya hanya dipukul sekali dalam setiap cetakan cetakan dan desain setiap cetakan menjadi lebih penting sementara keterampilan operator kurang penting.
Penempaan palu
Jenis peralatan tempa yang paling umum adalah palu dan landasan. Palu adalah jenis peralatan yang paling murah dan paling serbaguna untuk menghasilkan beban dan energi untuk melakukan proses penempaan. Teknologi ini dicirikan oleh beberapa pukulan tumbukan antara cetakan berkontur. Palu terutama digunakan untuk penempaan panas.
Tekan penempaan
Dalam penempaan tekan, logam dibentuk tidak dengan serangkaian pukulan seperti dalam penempaan palu, tetapi dengan satu tindakan pemerasan terus menerus.
Berdasarkan pengaturan dadu
Berdasarkan susunan die, proses forging dapat berupa (i) open die forging, dan (ii) die forging tertutup. (Gbr 1)
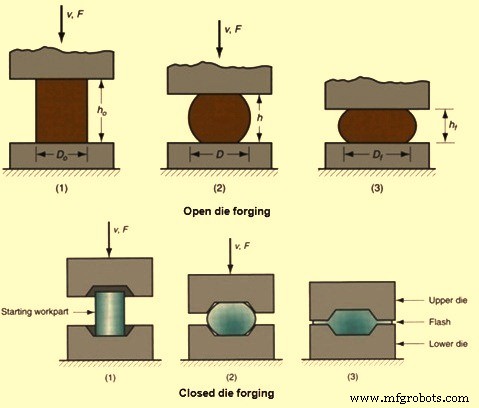
Gbr 1 Penempaan logam dengan cetakan terbuka dan cetakan tertutup
Buka penempaan mati
Penempaan die terbuka adalah jenis proses penempaan di mana cetakan datar tanpa profil precut pada cetakan digunakan. Dies berbentuk sederhana dan digunakan untuk memungkinkan material berubah bentuk secara bebas ke arah lateral dari beban yang diterapkan. Gerakan benda kerja adalah kunci dari metode ini. Benda kerja yang lebih besar dengan berat lebih dari 100 ton dan panjang sekitar 25 m dapat dipalu atau ditekan menjadi bentuk dengan cara ini. Penempaan die terbuka hanya cocok untuk bentuk sederhana karena prosesnya memberikan akurasi dimensi yang lebih rendah. Dibutuhkan keterampilan operator yang tinggi. Dies dari tempa die terbuka sederhana dan lebih murah. Proses forging paling sederhana jika dibandingkan dengan proses forging lainnya.
Penempaan cetakan terbuka disebut cetakan terbuka karena logam tidak dibatasi secara lateral oleh cetakan cetakan selama penempaan. Proses ini secara bertahap mengerjakan stok awal ke dalam bentuk yang diinginkan, paling umum di antara cetakan berwajah datar. Dalam praktiknya, penempaan die terbuka terdiri dari banyak variasi proses, memungkinkan berbagai bentuk dan ukuran yang sangat luas untuk diproduksi. Faktanya, ketika kriteria desain menentukan integritas struktural optimal untuk komponen logam besar, kemampuan ukuran tipis dari penempaan die terbuka menjadikannya pilihan proses yang jelas daripada alternatif non penempaan. Pada kisaran ukuran akhir yang tinggi, tempa die terbuka hanya dibatasi oleh ukuran bahan awal, yaitu, ingot terbesar yang dapat dicor.
Hampir semua bahan besi dan non-ferro yang dapat ditempa dapat ditempa dengan cetakan terbuka, termasuk beberapa bahan eksotis seperti paduan super pengerasan usia dan paduan tahan api tahan korosi.
Kemampuan bentuk open-die memang lebar di garis lintang. Selain bulat, persegi, persegi panjang, batang heksagonal, dan bentuk dasar lainnya, proses cetakan terbuka dapat menghasilkan hal berikut.
- Poros padat injak (spindel atau rotor) yang diameternya bertambah atau berkurang (turun) di beberapa lokasi di sepanjang sumbu longitudinal.
- Bagian berongga yang berbentuk silinder dan umumnya panjangnya jauh lebih tinggi dari diameternya. Dimungkinkan untuk mengubah panjang, ketebalan dinding, ID (diameter internal) dan OD (diameter luar) sesuai kebutuhan.
- Bagian yang mirip dengan cincin dapat menyerupai ring atau mendekati bentuk silinder berongga, bergantung pada rasio tinggi terhadap ketebalan dinding.
- Cangkang logam berbentuk kontur seperti bejana tekan, yang dapat menggabungkan nozel yang diekstrusi dan fitur desain lainnya.
Tidak seperti operasi penempaan berturut-turut dalam urutan cetakan, beberapa operasi penempaan cetakan terbuka dapat digabungkan untuk menghasilkan bentuk yang diperlukan. Pada saat yang sama, metode penempaan ini dapat disesuaikan untuk mencapai jumlah deformasi total yang tepat dan struktur aliran butir yang optimal, sehingga memaksimalkan peningkatan properti dan kinerja akhir untuk aplikasi tertentu. Menempa kosong roda gigi dan hub integral, misalnya, mungkin memerlukan beberapa operasi menggambar atau penempaan padat, kemudian mengganggu. Demikian pula, blanko untuk cincin dapat disiapkan dengan memasang ingot, lalu menusuk bagian tengahnya, sebelum menempa cincin.
Penempaan cetakan tertutup
Penempaan mati tertutup juga disebut penempaan cetakan cetakan. Proses penempaan terdiri dari menumbuk atau menekan logam antara dua cetakan (disebut perkakas) yang berisi profil precut dari bagian yang diinginkan. Dalam penempaan die tertutup, material dibatasi sepenuhnya dalam rongga yang dibuat oleh bagian die atas dan bawah. Bagian dengan berat beberapa gram hingga lebih dari 25 ton dapat dibuat menggunakan proses ini. Beberapa bagian yang lebih kecil juga dapat ditempa dingin. Penempaan mati tertutup dari baja, aluminium, titanium, dan paduan lainnya dapat menghasilkan variasi bentuk 3-D yang hampir tak terbatas. Penempaan ini secara rutin diproduksi pada pengepres hidrolik, pengepres mekanis, dan palu.
Sesuai dengan namanya, dua atau lebih cetakan yang mengandung cetakan bentuk bagian disatukan karena bahan tempa mengalami deformasi plastis. Karena aliran logam dibatasi oleh kontur die, proses ini dapat menghasilkan bentuk yang lebih kompleks dan toleransi yang lebih dekat daripada proses penempaan die terbuka. Penempaan die tertutup memungkinkan bagian yang berbentuk lebih akurat untuk dibentuk. Proses ini membutuhkan tekanan antarmuka yang lebih tinggi, kontrol volume material yang sangat akurat, dan desain die yang tepat.
Penempaan die tertutup adalah bentuk penempaan cetakan-cetakan, yang tidak bergantung pada pembentukan flash untuk mencapai pengisian cetakan yang lengkap. Material mengalami deformasi dalam rongga yang memungkinkan sedikit atau tidak ada keluarnya material berlebih, sehingga memberikan tuntutan yang lebih besar pada desain die.
Fleksibilitas tambahan dalam membentuk baik bentuk simetris maupun non-simetris berasal dari berbagai operasi pra-pembentukan (terkadang pembengkokan) sebelum penempaan di finisher dies. Geometri bagian berkisar dari beberapa yang paling mudah untuk menempa bentuk bola sederhana, padatan persegi panjang seperti balok, dan konfigurasi seperti cakram hingga komponen paling rumit dengan bagian tipis dan panjang yang menggabungkan jaring tipis dan proyeksi vertikal yang relatif tinggi seperti rusuk dan bos. Meskipun banyak bagian biasanya simetris, yang lain menggabungkan segala macam elemen desain (flensa, tonjolan, lubang, rongga, kantong, dll.) yang digabungkan untuk membuat penempaan menjadi sangat tidak simetris. Selain itu, bagian-bagian dapat ditekuk atau dilengkungkan dalam satu atau beberapa bidang, baik pada dasarnya memanjang, berdimensi sama, atau datar.
Dalam penempaan die tertutup, benda kerja pertama-tama ditempa kasar mendekati bentuk akhir dengan memblokir die. Benda kerja kemudian ditempa menjadi bentuk dan dimensi akhir dengan finishing die. Baik mati pemblokiran dan cetakan akhir dikerjakan ke dalam blok cetakan yang sama. Jumlah dies yang dibutuhkan lebih banyak tergantung pada kompleksitas pekerjaan. Dua bagian die mendekat dan pekerjaan berubah bentuk di bawah tekanan tinggi. Penempaan die tertutup memberikan akurasi dimensi tinggi/kontrol ketat pada toleransi dan cocok untuk bentuk kompleks. Dies rumit dan lebih mahal serta tingkat produksi yang besar diperlukan untuk membenarkan biaya tinggi.
Desain die tergantung pada pengetahuan tentang kekuatan dan keuletan material benda kerja, kepekaan material terhadap laju deformasi dan suhu, karakteristik gesekan, bentuk dan kompleksitas benda kerja, dan distorsi die di bawah beban tempa yang tinggi. Material die membutuhkan kekuatan dan ketangguhan pada suhu tinggi, kemampuan pengerasan dan kemampuan untuk mengeras secara seragam, ketahanan terhadap guncangan mekanis dan termal, dan ketahanan aus untuk menahan keausan abrasi karena adanya timbangan pada benda kerja. Pemilihan bahan die yang tepat tergantung pada ukuran die, komposisi dan sifat benda kerja, kompleksitas bentuk, jumlah langkah yang dilakukan, suhu penempaan, jenis operasi penempaan, biaya material die, jumlah penempaan yang dibutuhkan, dan perpindahan panas dari pekerjaan. piece to die dll. Material die normal adalah tool dan die steel.
Sebagian besar logam dan paduan rekayasa dapat ditempa melalui proses penempaan mati tertutup konvensional. Ini termasuk baja karbon dan paduan, baja perkakas, dan paduan stainless, aluminium dan tembaga, dan paduan titanium tertentu. Bahan yang peka terhadap suhu dan laju regangan (magnesium, paduan super berbasis nikel paduan tinggi, paduan tahan api, dan beberapa paduan titanium) memerlukan proses penempaan yang lebih canggih dan/atau peralatan khusus untuk penempaan dalam cetakan cetakan.
Proses penempaan lainnya
Penempaan cincin gulung mulus
Penempaan cincin gulung yang mulus biasanya dilakukan dengan melubangi potongan logam bulat yang tebal (membuat bentuk donat), lalu menggulung dan meremas (atau dalam beberapa kasus, menumbuk) donat menjadi cincin tipis. Diameter cincin bisa berkisar dari beberapa sentimeter hingga sekitar 10 meter.
Ring yang ditempa dengan proses rolling ring yang mulus dapat memiliki berat mulai dari kurang dari 1 kg hingga hingga 150 ton. Dari segi kinerja, tidak ada bandingannya untuk cincin penampang melingkar yang ditempa yang digunakan dalam pembangkit energi, pertambangan, aerospace, peralatan off-highway, dan aplikasi penting lainnya.
Konfigurasi cincin mulus bisa datar (seperti mesin cuci), atau memiliki dinding vertikal yang lebih tinggi (di sekitar bagian silinder berongga). Ketinggian cincin yang digulung berkisar dari beberapa sentimeter hingga lebih dari 3 meter. Tergantung pada peralatan yang digunakan, rasio ketebalan dinding terhadap tinggi cincin biasanya berkisar dari 1:16 hingga 16:1, meskipun proporsi yang lebih besar telah dicapai dengan pemrosesan khusus. Faktanya, tabung mulus dengan diameter hingga 1200 mm dan panjang lebih dari 6 meter diekstrusi pada mesin tempa.
Meskipun bentuk dasar dengan penampang persegi panjang adalah norma, cincin yang menampilkan penampang kompleks dan fungsional dapat ditempa untuk memenuhi hampir semua persyaratan desain. Dinamakan dengan tepat, cincin gulung berkontur ini dapat diproduksi dalam ribuan bentuk berbeda dengan kontur di bagian dalam dan/atau diameter luar. Keuntungan utama dari cincin berkontur adalah pengurangan yang signifikan dalam operasi pemesinan. Tidak mengherankan, cincin berkontur khusus dapat menghasilkan konsolidasi bagian yang hemat biaya. Dibandingkan dengan cincin gulung mulus muka datar, dimensi maksimum (tinggi muka dan OD) cincin gulung berkontur agak lebih rendah, tetapi ukurannya masih sangat mengesankan.
Kekuatan tangensial dan keuletan yang tinggi membuat cincin tempa cocok untuk komponen tahan torsi dan tahan tekanan, seperti roda gigi, bantalan mesin untuk pesawat terbang, bantalan roda, kopling, spacer rotor, cakram dan kotak tertutup, flensa, bejana tekan, dan badan katup. Bahan tidak hanya mencakup baja karbon dan paduan, tetapi juga paduan aluminium, tembaga, dan titanium non-ferrous, serta paduan berbasis nikel
Operasi penempaan
Berbagai operasi penempaan adalah menggambar, swaging, upsetting, fullering, forged welding, flatting and setting down, edging, bending, cutting, dan punching.
- Menggambar – Operasi menggambar dilakukan untuk memanjangkan benda kerja dan mengurangi luas penampang. Operasi penarikan terjadi ketika gaya bekerja menuju arah tegak lurus sumbu longitudinal.
- Swaging – Swaging dilakukan dengan proses cold forging. Operasi ini digunakan untuk mengubah dimensi benda kerja dan dilakukan dengan menggunakan gaya dies yang diterapkan pada material.
- Upsetting – Upsetting dilakukan untuk menambah luas penampang benda kerja. Untuk mendapatkan hasil yang diinginkan, operasi upsetting dilakukan sepanjang arah paralel dari sumbu longitudinal. Operasi upsetting biasanya dilakukan dalam produksi mur dan baut.
- Fullering – Ini adalah proses penempaan die terbuka yang khas. Fullering banyak digunakan sebagai langkah awal untuk membantu mendistribusikan material pekerjaan sebagai persiapan untuk operasi penempaan logam selanjutnya. Ini sering terjadi ketika proses manufaktur membutuhkan beberapa operasi penempaan untuk diselesaikan. Dalam fullering, die terbuka dengan permukaan cembung digunakan untuk mengubah bentuk benda kerja. Hasilnya adalah menyebabkan logam mengalir keluar dari satu area dan ke kedua sisi.
- Pengelasan tempa – Ini adalah operasi untuk menambah panjang dengan menggabungkan dua potongan logam. Ini dilakukan dengan menerapkan pukulan palu atau tekanan ketika benda kerja mencapai suhu penempaan.
- Perataan dan pemasangan – Fullering meninggalkan permukaan bergelombang pada benda kerja. Bahkan setelah pekerjaan ditempa menjadi bentuk dengan palu, bekas palu tetap ada di permukaan atas pekerjaan. Untuk menghilangkan palu dan tanda kerutan dan untuk mendapatkan permukaan yang halus pada pekerjaan, palu yang lebih datar atau set digunakan. Proses ini dikenal sebagai flatting atau setting down.
- Edging – Selama proses pengerjaan benda kerja ditempatkan di antara dua cetakan dan ada pemukulan pada tepi bahan untuk mendapatkan bentuk yang diinginkan. Merayap sering kali merupakan operasi penempaan jatuh yang utama.
- Bending – Ini adalah operasi penempaan yang sangat umum. Ini adalah operasi untuk memberi giliran pada batang dan pelat logam. Operasi ini diperlukan jika bagian yang ditempa memiliki bentuk bengkok.
- Pemotongan – Dengan bantuan palu dan pahat, batang dan pelat dapat dipotong menjadi dua bagian. Operasi penempaan ini dilakukan pada saat rod dalam kondisi panas.
- Punching – Ini adalah operasi penempaan dimana lubang dibuat dengan bantuan silinder berongga. Ketika kita menerapkan tekanan pada lubang mati silinder kemudian bergerak ke bawah untuk membuat lubang di piring.
Peralatan penempaan
Perkembangan teknologi penempaan yang berkelanjutan membutuhkan pemahaman yang baik dan mendasar tentang kemampuan dan karakteristik peralatan. Peralatan yang digunakan dalam penempaan mempengaruhi proses penempaan karena mempengaruhi laju deformasi dan kondisi suhu serta menentukan laju produksi. Persyaratan dari proses penempaan yang diberikan juga harus sesuai dengan karakteristik beban, energi, waktu, dan akurasi dari mesin tempa yang diberikan.
Jenis peralatan tempa yang paling umum adalah palu dan landasan. Pilihan peralatan penempaan tergantung pada sejumlah faktor, termasuk ukuran dan kompleksitas bagian, bahan, dan kualitas bagian yang akan diproduksi. Palu sering lebih disukai untuk batch kecil hingga menengah karena alat yang lebih cepat. Peralatan penempaan ini dapat dibagi menjadi dua tipe dasar yaitu (i) mesin terbatas kerja, dan (ii) mesin terbatas langkah.
Mesin yang dibatasi kerja
Dalam mesin yang dibatasi kerja, jumlah deformasi yang dapat dicapai selama setiap pukulan atau pukulan mesin dibatasi oleh energi atau gaya maksimum yang tersedia. Jika energi atau kapasitas gaya kurang dari yang dibutuhkan untuk merusak bagian tersebut, maka diperlukan lebih dari satu pukulan atau pukulan. Mesin yang termasuk dalam kategori ini adalah hammer, friction screw press, dan hydraulic press.
Palu
Palu adalah jenis mesin yang paling umum digunakan. Mereka sering lebih disukai untuk batch kecil hingga menengah karena penyiapan alat yang lebih cepat dan biaya overhead yang lebih rendah. Mereka juga digunakan untuk tempa memanjang dan tipe cabang karena area cetakan dapat disediakan untuk jumlah cetakan awal yang lebih banyak yang diperlukan untuk bentuk tersebut. Berbagai jenis palu yang digunakan adalah sebagai berikut.
- Palu penjatuh gravitasi – Mereka adalah jenis peralatan tempa tertua yang tersedia. Prinsip operasinya adalah balok mati yang bergerak diangkat dengan mekanisme pengangkatan dan kemudian dilepaskan, sehingga jatuh ke cetakan tetap yang menempel pada landasan. Besarnya deformasi yang dapat dilakukan ditentukan oleh energi potensial balok mati yang bergerak pada ketinggian maksimumnya. Energi potensial ini diubah menjadi energi kinetik ketika balok mati jatuh dan kemudian dihamburkan dalam deformasi benda kerja. Berbagai mekanisme pengangkatan digunakan, termasuk alat gesekan dengan papan, rem pita atau sabuk, atau silinder pengangkat yang menggunakan uap, udara tekan, atau cairan hidrolik. Mesin ini tersedia dalam berbagai energi pukulan dari 0,6 kNm hingga 400 kNm.
- Double acting atau power hammer – Mesin ini mirip dengan palu gravitasi di mana silinder pengangkat menaikkan tup yang bergerak, tetapi daya juga diterapkan pada tup yang bergerak ke bawah untuk meningkatkan kapasitas energi. Peringkat energi untuk bobot tup serupa jauh lebih besar daripada untuk palu gravitasi, dan kecepatan penutupan die juga lebih tinggi. Tenaga berasal dari uap kerja ganda, udara tekan, atau silinder hidrolik. Palu kerja ganda diproduksi dalam kisaran peringkat energi dari 3 kNm hingga 830 kNm.
- Palu pukulan counter vertikal – Pada mesin ini, dua putaran dengan massa yang hampir sama digerakkan oleh silinder kerja ganda ke arah satu sama lain dan bertubrukan di tengah mesin. Lebih banyak energi dihamburkan di benda kerja daripada di fondasi dan tanah di bawahnya dibandingkan dengan palu kerja tunggal. Kapasitas energi yang sangat tinggi tersedia di mesin ini yang berkisar dari 30 kNm hingga 2000 kNm.
- Palu serangan balik horizontal – Mesin ini juga disebut penabrak dan dua ram digerakkan oleh silinder kerja ganda. Stok yang dipanaskan diposisikan secara vertikal di antara cetakan dengan mekanisme transfer otomatis. Peringkat energi tipikal berkisar dari 4 kNm hingga 55 kNm.
Penekan sekrup
Dalam pengepresan sekrup, ram atas dan die dihubungkan ke sekrup vertikal besar yang dapat diputar oleh roda gila, sehingga ram dapat bergerak ke atas dan ke bawah relatif terhadap die tetap di dasar mesin. Ram memiliki jumlah energi yang terbatas untuk setiap pukulan, sehingga beberapa pukulan biasanya digunakan mirip dengan palu. Pengepres sekrup tersedia dalam peringkat dari 63 ton -6300 ton.
Press hidrolik
Pengepres hidrolik tersedia dalam berbagai ukuran hingga yang terbesar dengan kapasitas 50.000 ton atau lebih. Die yang bergerak dilekatkan pada ram yang digerakkan oleh silinder hidrolik besar. Berbagai pukulan, gaya, dan kecepatan penutupan dapat diperoleh pada pengepres hidrolik. Dalam beberapa kasus, penekan hidraulik dilengkapi dengan ram bantu yang bergerak secara horizontal, dan ini memungkinkan depresi samping ditempa menjadi beberapa bagian, meskipun hal ini tidak dilakukan secara luas.
Mesin yang dibatasi stroke
Pada mesin dengan langkah terbatas, jumlah deformasi yang dapat dilakukan ditentukan oleh langkah mesin. Jika tenaga atau energi yang cukup untuk melakukan operasi tidak tersedia, maka mesin akan mati dan mesin yang lebih besar akan digunakan. Pengepres mekanis termasuk dalam kategori ini, karena engkol atau eksentrik menentukan jumlah gerakan ram.
Tekan mekanis
Pengepres mekanis termasuk dalam kelas peralatan mesin yang mencakup berbagai jenis mesin yang berbeda. Terutama, tekan mekanik mengubah gaya rotasi motor menjadi vektor gaya translasi yang melakukan tindakan menekan. Oleh karena itu, energi dalam pers mekanis berasal dari motor. Jenis pengepresan ini umumnya lebih cepat dari pengepres hidrolik atau pengepres ulir, (sebenarnya pengepresan ulir juga dapat digolongkan sebagai pengepres mekanis). Tidak seperti beberapa tekanan, dalam tekanan mekanis, penerapan gaya bervariasi dalam kecepatan dan besarnya sepanjang jarak stroke. Saat melakukan operasi manufaktur menggunakan mesin press mekanis, rentang pukulan yang benar sangat penting. Dalam pengepresan mekanis, mekanisme engkol, sambungan buku jari, scotch yoke, atau baji bergerak digunakan untuk menerapkan gerakan meremas vertikal antara die yang bergerak atas dan die tetap yang lebih rendah.
Cacat penempaan
Selama proses penempaan ada kemungkinan terjadinya beberapa cacat. Dalam proses penempaan panas, cacat yang umum adalah hot shortness, shear band, kavitasi batas butir. Dalam proses penempaan dingin, cacat yang umum adalah retak permukaan, pita geser dan ledakan pusat. Cacat umum selama operasi penempaan adalah (i) pengisian die yang tidak lengkap, (ii) ketidaksejajaran die, (iii) putaran penempaan, (iv) penetrasi penempaan yang tidak lengkap, (v) perbedaan struktur mikro yang mengakibatkan variasi properti yang jelas, (vi) hot shortness , karena konsentrasi sulfur yang tinggi dalam baja dan nikel, (vii) permukaan berlubang karena kerak oksida yang terjadi pada suhu tinggi menempel pada cetakan, (viii) tekuk, dalam penempaan yang mengganggu, karena tegangan tekan yang tinggi, (ix) retak permukaan, karena perbedaan suhu antara permukaan dan pusat, atau kerja permukaan yang berlebihan pada suhu yang terlalu rendah, dan (x) retakan mikro karena tegangan sisa. Juga cacat seperti (i) penutupan dingin, (ii) pergeseran mati, (iii) aliran butir yang tidak tepat, (iv) serpihan, (v) lubang kerak, dan (vi) retak pada flash dapat terjadi.
Cold shut disebabkan oleh proses pengelasan yang tidak sempurna. Kedua permukaan material benda kerja saling bersentuhan. Penyebab utama penutupan dingin adalah pendinginan yang berlebihan, sudut tajam dan gesekan yang tinggi. Untuk menghindari radius tutup dingin fillet dinaikkan pada cetakan.
Pergeseran die disebabkan oleh ketidaksejajaran bagian dies. Untuk memperbaiki bentuknya, dadu dibuat menjadi dua bagian. To avoid the die shift, it is necessary to align the die halves properly and provide half notches on the upper and lower side of the die. So during the alignment, if the notch is matched on both the sides then proper shapes can be achieved.
In case of unfilled section defect, the moving metal does not fill the die chamber completely. It can be due to the improper design of the forging die, poor heating and lesser amount of the raw material.
Scale pits are due to the irregular cleaning on the exterior surface of forging. The scales and oxide are get rooted in to the finished surface.
The defect of improper grain flow is due to improper design of the die because of which the flowing material does not flow downwards. To avoid the improper grain flow, proper design of die is important.
Flakes are the internal disagreements which are basically found in the arrangement. They are mainly cause because of improper cooling. To avoid the flakes defect, proper cooling procedures are to be followed.
Residual stresses are due to the improper cooling and non-uniform deformation of the forging. To avoid this defect during a period of time slow cooling in a furnace or under ash the forging is done.
Surface cracking is due to low temperatures and excessive work. To avoid the surface cracking, suitable temperatures are used for the forging process.
Incomplete forging is mainly due to the forging taking place at the surfaces which causes no break-up of the interior of the forging. To avoid, it is preferable to use light hammer blowers for the process.
Cracking at the flash is due to the incomplete thickness of the flash. Hence to avoid the cracking at the flash, it is necessary to increase the thickness of the flash.