Proses produksi untuk Pipa Welded
Proses produksi untuk Pipa Las
Pipa baja panjang, tabung berongga yang digunakan terutama untuk menyalurkan cairan atau produk terfluidisasi dari satu lokasi ke lokasi lain. Mereka diproduksi terutama oleh dua proses produksi berbeda yang menghasilkan pipa yang dilas atau pipa yang mulus.
Pipa baja yang dilas diproduksi dengan jahitan memanjang atau jahitan spiral (heliks). Diameter pipa ini berkisar dari sekitar 6 mm hingga 2.500 mm dengan ketebalan dinding berkisar antara 0,5 mm hingga sekitar 40 mm.
Bahan awal untuk produksi pipa las adalah produk gulungan datar yang tergantung pada proses produksi pipa, dimensi dan aplikasi pipa, dapat berupa strip baja canai panas (HR) atau canai dingin (CR), dan strip lebar HR atau piring. Bahan awal ini dapat dibentuk menjadi bentuk pipa baik dalam kondisi panas maupun dingin. Proses pembentukan dapat berupa proses kontinu atau proses pembentukan pipa tunggal.
Dalam proses pembentukan pipa kontinu, bahan strip yang tidak digulung diambil dari akumulator, dengan ujung depan dan ujung belakang dari kumparan berurutan dilas bersama. Dalam proses pembentukan pipa tunggal, operasi pembentukan dan pengelasan pipa dilakukan dalam satu panjang pipa.
Ada dua jenis proses pengelasan yang terutama digunakan untuk produksi pipa las. Ini adalah (i) proses pengelasan tekanan, dan (ii) proses pengelasan fusi. Proses pengelasan tekanan yang umum digunakan adalah (i) proses pengelasan tekanan mis. Proses Fretz-Moon, (ii) pengelasan hambatan listrik DC (arus searah), (iii) pengelasan hambatan listrik frekuensi rendah (LF), (iv) pengelasan induksi frekuensi tinggi (HF), dan (v) pengelasan konduksi HF . Proses pengelasan fusi yang umum digunakan adalah (i) pengelasan busur terendam (SAW), dan (ii) pengelasan pelindung gas.
Tab 1 Proses produksi pipa las | |
Proses pembentukan | Proses pengelasan | Jenis pengelasan | Jenis las | Rentang ukuran pipa (OD) dalam mm | |
Proses berkelanjutan | Pengelasan tekanan tinggi | Bulan Fretz | Membujur | 13-115 | |
Pengelasan tahanan listrik (ERW) | 1. Arus searah (DC)
2. Frekuensi rendah (LF)
3. Frekuensi tinggi (HF) | Bujur | 10-20 | |
10-115 | |
20-600 | |
Pengelasan busur listrik (las fusi) | 1. Busur terendam (SAW)
2. Busur logam gas (MAG) (untuk pengelasan paku) 3. Busur logam gas (TIG, MIG, ERW)* | Spiral Spiral/ membujur | 168-2.500 | |
405-2030 | |
|
30-500/ 10-420 | |
1. Operasi pembentukan tunggal 2. Mesin bending 3-roll 3. C-ing press | 1. Busur terendam (SAW)
2. Busur logam gas (TIG, MIG, ERW)* | Bujur | 500 dan lebih tinggi | |
200-600 | |
1. Operasi pembentukan tunggal 2. Tekan U/O-ing | 1. Busur terendam (SAW)
2. Busur logam gas (MAG) (untuk pengelasan paku) | Bujur | 455-1625 | |
|
|
*Pipa baja tahan karat (SS) | |
Proses pengelasan tekanan
Proses pengelasan tekanan yang populer adalah proses Fretz-Moon.
Proses Fretz-Moon – Fretz-Moon adalah nama penemu proses. Dalam proses ini, strip baja dalam bentuk strip kontinu dipanaskan hingga suhu pengelasan dalam garis pembentukan dan pengelasan (Gbr 1). Rol terus menerus membentuk strip menjadi pipa jahitan terbuka. Setelah ini, tepi kawin ditekan bersama dan dilas dengan proses yang didasarkan pada teknik las tempa. Pipa dari 40 mm hingga 115 mm diameter luar (OD) dapat diproduksi dengan metode ini. Kecepatan pengelasan berkisar dari 200 m/mnt (meter per menit) hingga 100 m/mnt.
Saat ini pipa tak berujung dari pabrik Fretz-Moon langsung diumpankan ke pabrik pengurang peregangan. Penggilingan ini disediakan di garis run out untuk menggulung pipa dengan panas yang sama ke berbagai diameter hingga sekitar 13 mm. Pipa kemudian dipotong menjadi panjang individu untuk penempatan di tempat tidur pendingin. Kombinasi ini memberikan keuntungan bahwa pabrik Fretz-Moon dapat digunakan untuk diameter pipa tunggal yang konstan, sehingga menghilangkan biaya penggantian gulungan dan pekerjaan penyetelan ulang.
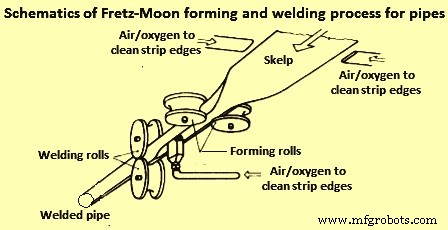
Gbr 1 Skema proses pembentukan dan pengelasan Fretz-Moon untuk pipa
Kumparan HR digunakan sebagai bahan awal. Kumparan dibuka dengan kecepatan tinggi dan strip disimpan dalam akumulator loop. Bahan yang disimpan bertindak sebagai penyangga selama proses produksi berkelanjutan. Ini memungkinkan ujung ekor strip yang sedang berjalan dilas ke ujung kepala strip kumparan berikutnya. Strip kontinu kemudian dibawa ke tungku terowongan di mana dipanaskan sampai suhu tinggi. Pembakar yang diatur secara lateral meningkatkan suhu di tepi strip ke suhu pengelasan sekitar 100 derajat C hingga 150 derajat C lebih tinggi dari suhu yang berlaku di pusat strip. Dudukan rol pembentuk terus menerus membentuk strip masuk menjadi pipa jahitan terbuka, yang kelilingnya sedikit berkurang (sekitar 3%) di dudukan las rol pemeras hilir. Dudukan las diimbangi pada 90 derajat ke dudukan sebelumnya. Dudukan las menghasilkan tekanan yang mengganggu yang menyebabkan ujung-ujungnya ditekan bersama dan dilas. Struktur lasan selanjutnya dikompresi dalam dudukan rol pereduksi hilir lagi diimbangi dengan 90 derajat. Roller pereduksi ini mengukur ukuran pipa. Jika tidak ada pabrik pengurang regangan maka gergaji terbang yang terletak di hilir memotong pipa tak berujung menjadi panjang individu. Pipa-pipa yang dipotong ini disalurkan melalui tempat tidur pendingin ke bagian penyelesaian pipa.
Proses produksi pipa ERW
Baik arus searah (DC) dan arus bolak-balik (AC) digunakan untuk produksi pipa ERW. Dalam proses pengelasan AC digunakan arus LF atau arus HF.
proses DC – Proses DC menggunakan efek arus searah (sistem gelombang persegi). Karakteristik utama tukang las gelombang persegi adalah hanya tegangan tinggi/arus rendah yang digunakan sampai titik las tercapai. Secara elektrik, perbedaan utama antara DC dan gelombang persegi adalah bahwa arus saluran disearahkan (melalui penyearah gelombang penuh) tanpa melalui transformator step-down. Proses DC digunakan untuk pengelasan longitudinal pipa kecil hingga 20 mm OD (30 mm OD dalam kasus khusus), dengan ketebalan dinding tipis mulai dari 0,5 mm hingga 2 mm. Strip CR digunakan sebagai bahan awal untuk proses ini karena persyaratan toleransi.
Keuntungan dari pengelasan DC dibandingkan dengan metode pengelasan LF dan HF adalah hasil akhir yang halus dari lintasan bagian dalam dengan ridge (penguatan) yang kecil. Ini penting ketika pipa membutuhkan las bagian dalam yang halus dan di mana tidak mungkin untuk melepaskan flash las (contoh pipa penukar panas).
Rentang aplikasi untuk proses DC dibatasi oleh daya listrik yang dapat ditransmisikan oleh elektroda cakram yang digunakan dalam proses tersebut. Kecepatan pengelasan yang diperoleh pada proses ini berkisar antara 50 m/menit sampai dengan 100 m/menit. Pipa yang dihasilkan oleh proses DC biasanya akan direduksi dingin. Karena itu, ketebalan badan utama pipa meningkat sedikit lebih dari zona las yang mengakibatkan pipa hampir tidak menunjukkan tonjolan las internal sama sekali.
proses LF –Pada proses LF, pengelasan dilakukan dengan AC pada rentang frekuensi antara 50 Hz (hertz) hingga 100 Hz. Elektroda yang terdiri dari dua cakram terisolasi dari paduan tembaga (Cu) digunakan tidak hanya untuk catu daya tetapi juga sebagai alat pembentuk dan elemen yang menghasilkan tekanan pengelasan yang diperlukan (Gbr 2). Proses ini digunakan untuk memproduksi pipa las longitudinal dengan diameter 10 mm hingga 115 mm dengan kecepatan pengelasan hingga 90 m/menit tergantung pada ketebalan dinding.
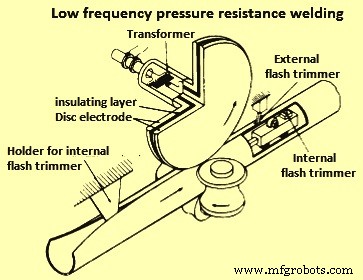
Gbr 2 Pengelasan resistansi tekanan frekuensi rendah
Elektroda adalah komponen penting dari proses karena harus dilengkapi dengan alur yang sesuai dengan diameter pipa yang diproduksi. Selain itu, alur ini harus terus dipantau untuk keausan selama pengoperasian.
Bahan selama proses pengelasan tekanan membentuk kilatan bagian dalam dan luar di sepanjang zona las yang harus dilepas di jalur hilir oleh pemangkas internal dan eksternal. Proses tersebut dapat menghasilkan lasan dengan tingkat kesempurnaan yang tinggi dengan tunduk pada proses yang dipantau dengan cermat untuk memenuhi berbagai persyaratan.
Proses HF – Proses pengelasan hambatan listrik HF untuk produksi pipa diperkenalkan pada tahun 1960-an. Prosesnya melibatkan penerapan arus listrik AC HF dalam kisaran 200 kHz (kilo hertz) hingga 500 kHz. Operasi pembentukan pipa dan input energi dilakukan oleh unit terpisah. Strip dibentuk di pabrik roll forming atau di roll stand yang dapat disesuaikan (pembentukan fungsi alami) menjadi pipa jahitan terbuka untuk berbagai produk pipa. Ini termasuk pipa saluran dan pipa struktural dalam kisaran ukuran sekitar 20 mm hingga 600 mm OD dan kisaran ketebalan dinding 0,5 mm hingga 16 mm, dan pipa kosong untuk pabrik pengurang peregangan hilir. Bahan awalnya adalah strip baja lebar HR atau skelp. Bergantung pada dimensi dan aplikasi pipa, dan khususnya dalam kasus pipa presisi, strip baja dapat menjalani operasi pickling hulu, atau digunakan strip CR. Kumparan dibuka dengan kecepatan tinggi dan strip disimpan dalam akumulator loop. Bahan yang disimpan bertindak sebagai penyangga selama proses produksi berkelanjutan. Hal ini memungkinkan ujung trailing dilas ke ujung terkemuka strip kumparan berikutnya. Mesin las pipa beroperasi terus menerus pada kecepatan mulai dari 10 m/menit hingga 120 m/menit dengan menarik strip dari akumulator loop.
Gambar 3 menunjukkan prinsip pabrik roll forming. Roll forming mill digunakan untuk diameter pipa hingga maksimum 600 mm. Biasanya terdiri dari 8 hingga 10 dudukan pembentuk gulungan yang sebagian besar digerakkan di mana strip secara bertahap dibentuk secara bertahap (1 hingga 7 dudukan) menjadi pipa jahitan terbuka. Tiga lintasan terakhir (8-10 dudukan) biasanya merupakan lintasan akhir yang memandu pipa jahitan terbuka menuju meja pengelasan (11). Gulungan pembentuk harus dicocokkan secara tepat dengan diameter pipa akhir. Untuk pipa berdiameter besar, proses pembentukan fungsi alami juga dapat diterapkan.
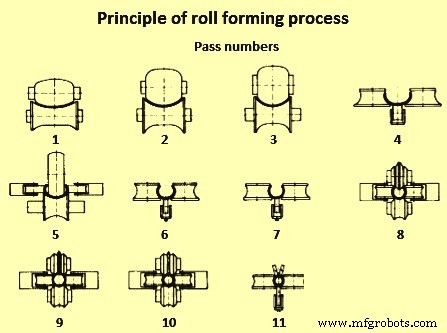
Gbr 3 Prinsip proses roll forming
Fitur utama dari dudukan rol pembentuk adalah bahwa sejumlah rol pembentuk internal dan eksternal yang tidak digerakkan, dapat disesuaikan dalam rentang diameter produk yang luas, disusun dalam garis pembentuk berbentuk corong yang secara bertahap menekuk strip menjadi bentuk pipa jahitan terbuka. Hanya penyangga penghancur di saluran masuk dan penyangga lintasan akhir di ujung keluar yang benar-benar digerakkan. Gambar skematis dari stand rol di pabrik pembuat rol diberikan pada Gambar 4. Pada gambar, detail penampang tertentu diperlihatkan yang menunjukkan tingkat deformasi n dan susunan rol pembentuk di berbagai bagian di sepanjang garis.
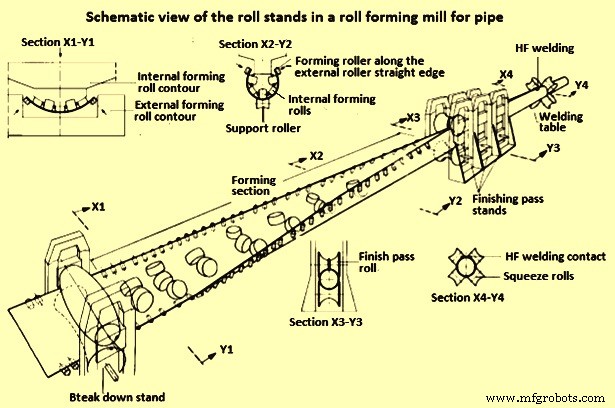
Gbr 4 Tampilan skema rol berdiri di pabrik pembuat rol
Proses pengelasan menggunakan tekanan dan panas secara bersamaan untuk menyatukan tepi strip dari jahitan terbuka tanpa menggunakan bahan pengisi. Peras dan gulungan tekanan di dudukan pengelasan menyatukan tepi pipa jahitan terbuka secara bertahap dan menerapkan tekanan yang diperlukan untuk pengelasan. Ada beberapa keuntungan dengan penggunaan daya listrik HF AC sebagai sumber energi untuk menghasilkan panas yang dibutuhkan untuk proses pengelasan. Sebagai contoh, ia memiliki keunggulan dibandingkan daya AC normal dalam menghasilkan kerapatan arus (fluks) yang sangat tinggi di atas penampang konduktor. Karena HF-nya, arus HF memiliki efek membangun medan magnet di inti tengah konduktor. Hambatan ohmik konduktor paling tinggi di medan ini, sehingga elektron mengikuti jalur dengan hambatan paling kecil di daerah permukaan luar konduktor (efek kulit). Oleh karena itu, arus mengalir di sepanjang tepi strip dari pipa jahitan terbuka ke titik di mana tepi strip berdampingan (titik las), dan konsentrasi berikutnya, didorong oleh kedekatan konduktor negatif, menghasilkan tingkat pemanfaatan energi yang tinggi. . Di bawah titik Curie (768 derajat C), kedalaman penetrasi arus hanya beberapa ratus mm. Setelah baja dipanaskan di atas suhu ini, baja menjadi non-magnetik dan kedalaman penetrasi arus naik menjadi beberapa persepuluh milimeter pada frekuensi di wilayah 450 kHz.
Arus pengelasan dapat dimasukkan ke dalam jahitan terbuka baik dengan cara konduktif dengan menggunakan kontak geser atau dengan cara induktif menggunakan kumparan angin tunggal atau multi. Oleh karena itu, perbedaan dibuat dalam nomenklatur antara pengelasan induksi HF (HFI) dan pengelasan konduksi HF. Tampilan skema pengelasan pipa HF ditunjukkan pada Gambar 5.
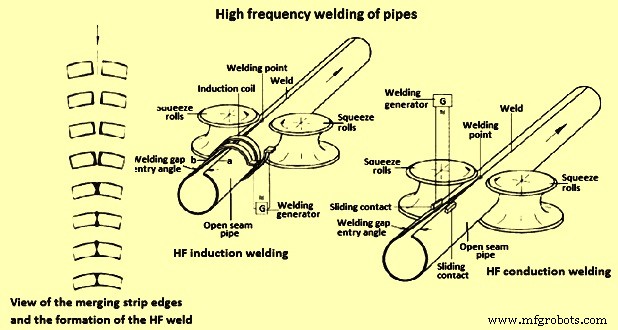
Gbr 5 pengelasan pipa HF
Belakangan ini, untuk mengakomodasi batch produksi kecil, grade baja paduan rendah kekuatan tinggi (HSLA), dan rasio ketebalan/diameter dinding yang ekstrem, proses pembentukan tepi lurus telah dikembangkan. Dalam proses ini, alih-alih rol pembentuk bawah, digunakan tepi lurus rol. Ini telah menghasilkan pengurangan substansial dalam panjang garis pembentukan. Proses ini dapat membentuk pipa dengan perbandingan ketebalan/diameter dinding mulai dari 1:8 hingga 1:100.
Peningkatan efisiensi pabrik dicapai dengan mengurangi waktu konversi dari satu ukuran pipa ke ukuran pipa lainnya melalui pengenalan proses pembentukan alat terpusat (CTA). Semua rol garis pembentuk dipasang dalam balok dan disetel melalui proses CTA oleh satu motor. Ini berarti bahwa di seluruh rentang ukuran tidak diperlukan perubahan roller (alat) pembentuk. Ini menghasilkan pengurangan yang cukup besar dalam konversi ukuran dan waktu penyiapan.
Sebelum masuknya strip di bagian pembentuk, strip diluruskan dan dipangkas hingga lebar konstan dengan pemangkas tepi memanjang. Tepi yang dipotong juga dapat dimiringkan untuk persiapan pengelasan. Strip kemudian dibentuk menjadi pipa jahitan terbuka dan dengan celah yang masih relatif lebar, diumpankan melalui dudukan pas finishing ke meja las. Gulungan finishing overhead, yang lebarnya meruncing ke arah titik pengelasan menentukan sudut masuk celah dan mengontrol posisi sentralnya di meja pengelasan. Di sana tepi strip konvergen didorong satu sama lain oleh gulungan pemerasan berbentuk dan kemudian dilas melalui proses hambatan listrik HF. Arus dapat ditransfer baik secara induktif melalui kumparan induksi yang diatur di sekitar pipa jahitan terbuka atau secara konduktif melalui kontak geser yang mengalir di sekitar pipa jahitan terbuka.
Bubungan eksternal dan internal yang terjadi selama pengelasan tekanan pipa dengan (ID sekitar 30 mm dan lebih tinggi), biasanya dipangkas dengan merencanakan atau menggores material saat masih panas. Pipa kemudian dibulatkan dan berukuran antara dua hingga enam dudukan ukuran. Dudukan ini biasanya dirancang untuk pengurangan melingkar. Proses tersebut juga menyebabkan efek pelurusan pada pipa. Penambahan unit ukuran gulungan pembentuk multi-untai di bagian pipa habis di pabrik juga dapat memungkinkan pipa bundar untuk langsung dibentuk menjadi bagian khusus.
Las yang dipangkas diperiksa melalui pengujian non-destruktif dan pipa dipotong menjadi panjang yang diinginkan dengan mesin pemotong terbang. Pemotongan pipa dapat dilakukan dengan salah satu metode yaitu (i) dengan memutus pipa di zona panas induktif yang sempit, (ii) pemotongan rotasi dengan bilah jenis cakram, atau (iii) dengan gergaji pemisah dingin atau gesekan .
Lasan tekanan HF dapat dibiarkan dalam kondisi seperti dilas atau selanjutnya dipanaskan dalam kisaran normalisasi tergantung pada aplikasi pipa. Anil induktif parsial dari lasan juga dapat dilakukan pada pipa kontinu, atau pipa individual dapat dikenai perlakuan panas terpisah setelah dipotong memanjang.
Dalam proses pengelasan induksi HF, kecepatan pengelasan hingga 120 m/menit dapat diperoleh tergantung pada ketebalan dinding dan aplikasinya. Prosesnya ditunjukkan pada Gambar 5. Pengelasan konduksi HF juga dikenal sebagai proses 'Thermatool'. Dalam proses ini, kecepatan pengelasan hingga 100 m/menit dapat dicapai tergantung pada ketebalan dinding dan aplikasinya. Prosesnya juga ditunjukkan pada Gambar 5.
Proses pengelasan fusi
Pipa baja las fusi biasanya digunakan untuk produksi pipa berdiameter besar untuk konstruksi pipa. Proses pembentukan pipa yang digunakan untuk pengelasan fusi adalah (i) proses pelengkungan tiga gulungan untuk pembentukan pelat, digunakan sebagai proses pembentukan dingin atau panas, (ii) proses pengepresan C-ing untuk pembentukan pelat dingin, (iii) ) proses pengepresan U-ing dan O-ing untuk pembentukan pelat dingin, dan (iv) proses pembentukan pipa spiral untuk pembentukan strip lebar atau pelat secara dingin. Proses ini ditunjukkan pada Gambar 6.
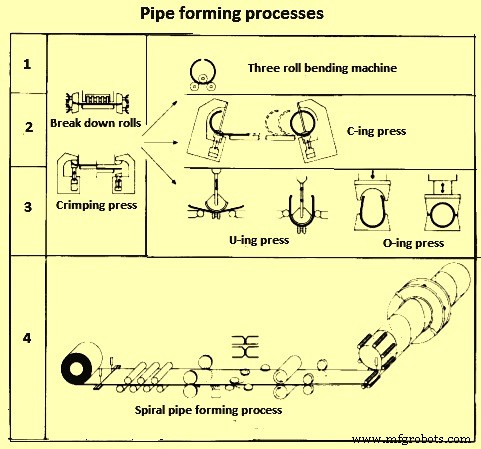
Gbr 6 Proses pembentukan pipa
Dari keempat proses di atas, dua proses terakhir yaitu (i) proses U-ing dan O-ing press untuk cold forming plate, dan (ii) proses spiral pipe forming untuk cold forming wide strip atau plate. proses yang sering digunakan di sebagian besar fasilitas produksi saat ini.
Proses las busur terendam (SAW) atau kombinasi pengelasan tack terlindung gas dengan las busur terendam hilir diterima secara luas sebagai metode standar untuk pengelasan pipa berdiameter besar. Proses pengelasan fusi juga digunakan dalam produksi pipa las spiral dan longitudinal dari baja tahan karat paduan tinggi. Produk dalam hal ini berupa pipa berdinding tipis dengan diameter berkisar antara 10 mm sampai dengan 600 mm. Selain proses TIG murni (tungsten inert gas welding), berbagai metode pengelasan gabungan juga digunakan. Misalnya, ini adalah pengelasan busur TP (plasma tungsten) + TIG, pengelasan TP + MIG (gas inert logam), dan proses TP + SAW.
Proses SAW – Proses SAW adalah metode pengelasan fusi listrik yang dilakukan dengan busur tersembunyi. Dibandingkan dengan pengelasan busur dengan elektroda las, busur dalam proses SAW tersembunyi di bawah selimut terak dan fluks. Salah satu fitur karakteristik dari proses SAW adalah laju pengendapannya yang tinggi, yang pada dasarnya berasal dari kekuatan arus tinggi yang diterapkan dikombinasikan dengan keseimbangan panas yang menguntungkan.
Logam pengisi yang digunakan berbentuk kawat las terang melingkar yang diumpankan terus menerus di kolam logam cair yang ditentukan oleh laju pengendapan. Tepat di atas logam induk (pipa), arus pengelasan dilakukan oleh kontak geser ke elektroda kawat dan dikembalikan melalui kabel ground yang terhubung ke material pipa (Gbr 7)
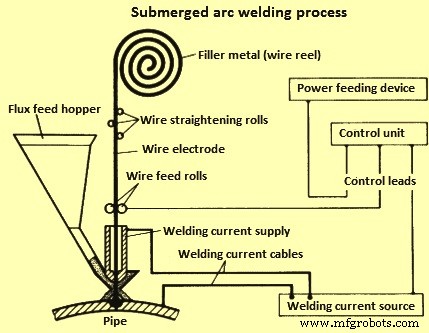
Gbr 7 Proses pengelasan busur terendam
Busur menyebabkan kawat masuk dan tepi jahitan terbuka meleleh. Bagian dari fluks pengelasan yang terus-menerus diumpankan juga dilebur oleh panas busur, menyebabkannya membentuk lapisan terak cair yang melindungi kolam las, elektroda kawat leleh, dan busur itu sendiri dari pengaruh atmosfer.
Selain itu, fluks pengelasan juga memfasilitasi pembentukan manik las dan berfungsi sebagai donor elemen paduan untuk mengkompensasi kehilangan leleh dan oksidasi. Dalam banyak kasus, itu juga digunakan secara khusus untuk paduan logam las untuk memberikan sifat kimia dan mekanik tertentu. Setelah pergerakan busur, terak cair, yang tertinggal, membeku. Fluks pengelasan yang tidak meleleh dipulihkan dengan ekstraksi vakum dan digunakan kembali. Terak mudah dihilangkan setelah dipadatkan. Komposisi kimia elektroda kawat dan fluks las diperlukan agar sesuai dengan bahan yang dilas. Pengelasan pipa SAW biasanya dilakukan dengan metode two pass (yaitu first run diikuti dengan sealing atau backing run) dan umumnya dilakukan dengan inside pass terlebih dahulu diikuti dengan outer pass kedua. Ini memastikan bahwa keduanya cukup tumpang tindih.
Hasilnya adalah las fusi yang umumnya tidak memerlukan perlakuan panas lebih lanjut. Pengelasan dengan SAW dapat dilakukan baik dengan AC dan DC dan dalam sistem multi-kawat di mana kombinasi AC dan DC dapat digunakan. Efisiensi proses SAW diberikan oleh laju pengendapan logam pengisi per satuan waktu (laju pengendapan). Hasilnya, kecepatan pengelasan yang sangat tinggi dimungkinkan.
Laju deposisi dapat ditingkatkan dengan meningkatkan arus pengelasan. Namun, karena daya dukung arus yang terbatas dari fluks, kinerja dapat ditingkatkan dalam pengelasan kawat tunggal hingga input maksimum sekitar 1200 A (ampere). Setiap peningkatan laju di luar batas ini membutuhkan pemasangan beberapa elektroda kawat. Hal ini kemudian memungkinkan arus keseluruhan yang lebih tinggi untuk diterapkan untuk pekerjaan pengelasan tanpa bahaya daya dukung arus dari fluks yang terlampaui pada salah satu elektroda kawat individu. Dalam operasi praktis, peningkatan kinerja diperoleh dengan menggunakan konfigurasi pengelasan multi-kawat dengan 2, 3 atau 4 elektroda. Tingkat pengendapan yang lebih tinggi dicapai dengan hasil pengelasan multi-kawat menjadi kecepatan pengelasan yang lebih tinggi dalam kondisi pengelasan praktis.
Dengan penggunaan fluks kinerja tinggi, proses pengelasan tiga kawat biasanya cukup efisien untuk ketebalan dinding hingga 20 mm. dalam hal ketebalan dinding lebih tinggi dari 20 mm; kawat keempat diperlukan untuk pemeliharaan kecepatan pengelasan dan dengan demikian untuk mencapai efisiensi produksi. Persyaratan untuk aplikasi pengelasan multi-kawat yang hemat biaya adalah bahwa parameter proses harus dioptimalkan untuk memastikan pencapaian yang andal dari persyaratan kualitas las yang ditentukan. Dalam praktiknya, kecepatan pengelasan yang berkisar antara 1 m/menit hingga 2,5 m/menit dapat dicapai tergantung pada proses pengelasan, ketebalan dinding, dan jenis fluks yang digunakan.
Pengelasan busur berpelindung gas – Ini juga merupakan proses pengelasan fusi listrik. Dalam proses ini, kolam las dihasilkan oleh efek busur listrik. Busur cukup terlihat karena terbakar di antara elektroda dan benda kerja. Elektroda, busur, dan kolam las dilindungi dari atmosfer oleh gas pelindung inert atau aktif yang terus-menerus diumpankan ke area las.
Proses pengelasan busur pelindung gas diklasifikasikan menurut jenis elektroda dan gas yang digunakan. Ini biasanya dibagi menjadi dua kategori utama. Kategori tersebut adalah (i) las busur tungsten gas (GTAW) yaitu las busur TIG, TP, dan THG (tungsten hidrogen gas), dan (ii) las busur logam gas (GMAW) yaitu las MIG, dan MAG (metal active gas). . Proses yang terutama digunakan untuk produksi pipa adalah proses pengelasan TIG, MIG, dan MAG. Proses pengelasan TIG dan MIG terutama digunakan untuk produksi pipa SS. Dalam proses pengelasan TIG, busur terbakar antara elektroda tungsten yang tidak meleleh dan benda kerja. Setiap logam pengisi diumpankan terutama tanpa input DC. Gas pelindung mengalir dari nosel gas dan melindungi elektroda, logam pengisi, dan kumpulan cairan dari kontak dengan udara atmosfer.
Gas pelindung biasanya bersifat inert argon (Ar), helium (He), atau campuran dari gas-gas ini. Dalam proses MIG dan MAG, berbeda dengan proses TIG, busur terbakar di antara benda kerja dan elektroda habis pakai yang meleleh yang menyediakan logam pengisi. Gas pelindung yang digunakan dalam pengelasan MIG biasanya bersifat inert Ar, He, atau campuran dari gas-gas tersebut. Dalam proses pengelasan MAG, gas pelindung aktif dan terdiri dari CO2 murni (karbon di-oksida), atau campuran gas yang terdiri dari CO2, Ar, dan O2 (oksigen). Proses MAG semakin banyak digunakan untuk pengelasan paku dalam produksi pipa las memanjang dan spiral berdiameter besar. Las tack juga berfungsi sebagai backing kolam las untuk proses SAW berikutnya. Persyaratan las yang optimal adalah persiapan tepi yang presisi (sambungan butt V ganda dengan permukaan akar lebar), dan las tack kontinu yang baik. Dalam produksi pipa berdiameter besar, kecepatan pengelasan untuk tack weld berkisar dari sekitar 5 m/mnt hingga 12 m/mnt.
Produksi pipa las memanjang (proses U-ing/O-ing)
Pelat yang digunakan untuk pipa yang dilas secara longitudinal dibentuk pada pengepres yang memiliki cetakan terbuka untuk U-ing dan cetakan tertutup untuk operasi O-ing. Proses ini juga disebut proses pembentukan UOE (U-ing, O-ing dan perluasan) dan digunakan untuk produksi pipa berdiameter besar yang dilas secara longitudinal dengan panjang individu hingga 18 m. Pabrik modern yang menggunakan proses ini dirancang untuk diameter pipa mulai dari sekitar 400 mm hingga 1.620 mm, dan ketebalan dinding mulai dari 6 mm hingga 40 mm. Bahan awalnya adalah pelat baja. Aliran material dalam proses yang menunjukkan tahapan operasional dan inspeksi yang penting selama produksi pipa berdiameter besar dengan proses pembentukan UOE ditunjukkan pada Gambar 8.
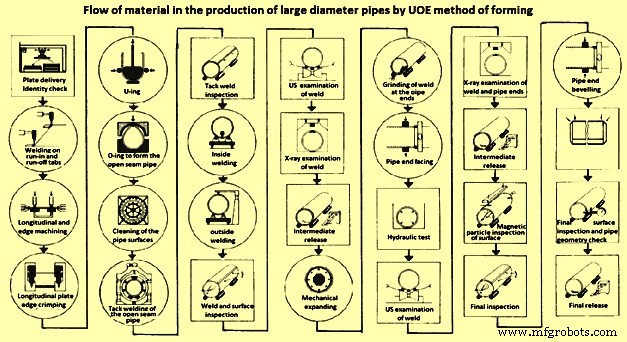
Gbr 8 Aliran material dalam produksi pipa berdiameter besar dengan metode pembentukan UOE
Pada awal proses pengelasan, tab run-in dan run-off dilas pada pelat datar untuk memastikan fenomena timbal dan ekor yang terkait dengan proses SAW terjadi di luar logam pipa. Sebelum pelat ditekuk menjadi pipa jahitan terbuka dengan berbagai tahapan dan penekan pembentuk yang digunakan, kedua tepi memanjang menjalani pemesinan oleh mesin planer untuk memastikan bahwa keduanya sejajar. Bevel las yang dibutuhkan untuk ketebalan pelat yang bersangkutan juga dipotong.
Pada tahap pembentukan pertama, pelat dikerutkan di area tepi memanjangnya. Rasio lentur sesuai secara kasar dengan diameter pipa jahitan terbuka. Crimping dilakukan dalam mesin cetak khusus. Pada tahap kedua, pelat ditekuk menjadi bentuk U dalam satu operasi yang melibatkan alat radius melingkar yang mendorong pelat ke bawah di antara dua penyangga. Menjelang akhir operasi, jarak antara penyangga dikurangi untuk menerapkan sedikit tekukan berlebih untuk melawan efek pegas. Dalam operasi pembentukan ketiga, bentuk U ditempatkan di mesin pres O-ing untuk menghasilkan dalam satu operasi, pipa jahitan terbuka bundar.
Proses pembentukan yang dilakukan pada penekan U-ing dan O-ing dikoordinasikan untuk memastikan bahwa efek pegas dilawan secara efektif dan pipa jahitan terbuka dibuat melingkar mungkin dengan tepi memanjang. Operasi ini membutuhkan beban tekan yang tinggi.
Tepi jahitan terbuka kemudian ditekan bersama-sama (menghilangkan offset apapun) di tack-welding berdiri, yang biasanya dirancang dalam bentuk sangkar roller, dan kemudian bergabung dengan jahitan terus menerus disimpan oleh mesin las MAG otomatis. Tergantung pada ketebalan pipa, kecepatan pengelasan yang diterapkan dapat berkisar antara 5 m/mnt hingga 12 m/mnt.
Pipa-pipa yang dilas dengan paku kemudian dibawa dengan meja rol dan sistem distribusi ke stan SAW, di mana, pada jalur terpisah, pipa-pipa tersebut pertama-tama dilengkapi dengan bagian dalam dan kemudian dengan jalur luar. Jalan ini disimpan dengan memindahkan pipa pada kereta di bawah kepala las stasioner. Untuk lintasan dalam, kepala las dipasang pada lengan yang memanjang di dalam pipa, Untuk mencegah kemungkinan offset las; baik kepala luar dan dalam terus dipantau dan dikendalikan untuk keselarasan sempurna ke garis tengah las. Semua proses SAW multi kawat dapat digunakan, tergantung pada dimensi pipa (diameter dan ketebalan dinding). Setelah pengelasan, pipa dikirim ke bagian finishing.
Pipa setelah pengelasan biasanya tidak memenuhi persyaratan toleransi sehubungan dengan diameter dan kebulatan. Oleh karena itu, di departemen finishing, pipa menjalani pemeriksaan menyeluruh, dan diukur dengan ekspansi dingin. Operasi ini dilakukan oleh ekspander mekanis atau hidrolik. Jumlah ekspansi yang diterapkan sekitar 1%, dan nilai ini dipertimbangkan saat menentukan keliling awal pipa jahitan terbuka. Proses produksi diselesaikan di departemen finishing dengan pemesinan ujung pipa dan melakukan pengerjaan ulang yang diperlukan.
Pipa-pipa tersebut menjalani uji hidraulik sebelum operasi pemesinan ujung pipa. Kemudian, pemeriksaan ultrasonik (US) akhir dilakukan di seluruh panjang zona las. Indikasi yang diungkapkan oleh pemeriksaan AS otomatis ini dan juga daerah las di ujung pipa diperiksa lebih lanjut dengan pemeriksaan sinar-X. Semua ujung pipa juga diperiksa di AS untuk lap dan laminasi.
Produksi pipa spiral
Pipa spiral juga dikenal sebagai pipa jahitan heliks. Selama produksi pipa spiral, strip atau lembaran panas terus menerus dibentuk menjadi pipa dengan fasilitas pembentukan spiral yang menerapkan radius tekukan yang konstan, dengan tepi strip yang berbatasan juga terus dilas sejajar.
In comparison to the longitudinally welded pipe production, in which each pipe diameter needs a certain width of the strip, spiral pipe production is characterized by the fact that pipes with different diameters can be produced from a single strip width. This is because the approach angle of the strip as it is fed to the forming unit can be changed. The smaller is this inlet angle, the larger is the diameter of the pipe from the same strip. The technical optimum ratio of the pipe diameter and the strip width ranges from 1:2 to 1:2.2. There is mathematical dependence between feed angle, strip width, and pipe diameter which apply in case of spiral pipe production. This mathematical dependence is shown in Fig 9.
The range of pipe diameters produced by the spiral welding process technology lies in the range of around 500 mm to 2,500 mm. The starting material used for spiral welded pipe production is normally wide HR strip with upto 20 mm wall thicknesses. For pipe thicknesses in excess of 20 mm, plates in individual lengths upto 30 m are generally needed.
There are two types of facilities associated within the production of spiral pipes. These facilities can consist of (i) integrated forming and SAW pipe processing line, and (ii) separated forming and SAW pipe processing lines (Fig 9).
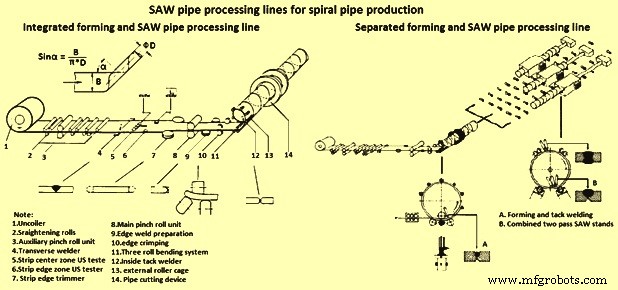
Fig 9 SAW pipe processing lines for spiral pipe production
Integrated forming and SAW welding line – The integrated forming and SAW welding line is the conventional production facility for the spiral pipe production. In this type of facility, the production process consists of (i) a strip preparation stage, and (ii) a pipe forming operation combined with simultaneous inside and outside pass SAW unit. Apart from the welding the strips together, the strip preparation stage also straightens the strip and trim it to the exact width. The strip edges need to be accurately machined within close tolerances, and a defined edge crimping is also needed to be performed in order to prevent impermissible ridge formation/peaking if pipe formation is to be successful.
The strip being fed in from the uncoiler is joined to the trailing end on the previous coil by SAW process. The weld is deposited along the face which later is going to form the inside surface of the pipe. The outside SAW pass is deposited in a separate line on the finished pipe. The strip then run through a straightening mill and is cut to a constant width by an edge trimmer. Additional device also bevel the edges in preparation for the main SAW welding operation. Before entry in the forming section, the strip edges are crimped in order to avoid ridging/peaking at the join.
In the integrated line, the strip preparation stage is immediately followed by the forming process with simultaneous inside and outside welding by the SAW process. A pinch roll unit feeds the strip at a predetermined entry angle into the forming section of the machine.
The purpose of the forming section is to bend the exactly prepared strip of width ‘A’ at a certain feed angle into a cylindrical pipe of diameter ‘D’ in line with the mathematical relationships as given in Fig 9.
There are many forming methods which are used to produce the spiral weld pipes. Apart from the direct shoe method which has its limitations, the two main spiral welding techniques (Fig 10) which are normally used are (i) three roll bending with an inside diameter roller cage, and (ii) three roll bending with an outside diameter roller cage. In a three roll bending system, several individual and guiding rollers are used rather than a single forming roll.
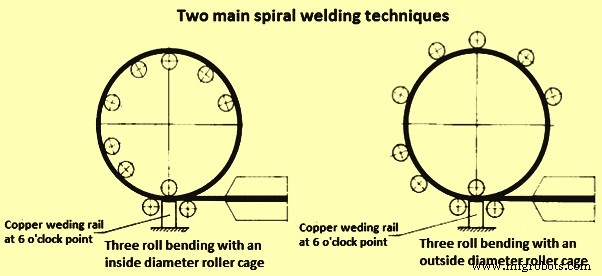
Fig 10 Two main spiral welding techniques
The roller cage serves to fix the pipe axis and maximize the roundness of the pipe in order to ensure offset free convergence of the strip edges at the welding point. This facilitates attainment of accurate pipe dimensions, so that the pipe leaving from the machine is already produced to within the standardized diameter, roundness, and straightness tolerances. Hence, expansion/sizing of the pipes after welding is not necessary.
In the spiral pipe forming and SAW machine, the converging strip edges are first inside welded at around the 6 o’clock position and then, half a pipe turn further, outside welded in the 12 o’clock position. Welding head alignment to the weld centre and gap control is performed automatically.
The produced pipe string is subsequently cut to length by a flying parting off device. The individual pipe is then sent to the finishing section where the production process is completed by machining of the pipe ends and by the performance of any rework. Before the pipe edge machining, a hydraulic test is conducted on the pipe. The entire weld region is then US inspected, with the weld zone at the pipe ends are also examine by X-ray. In addition, each pipe is US inspected over its full circumference for laps/laminations. If needed, the weld zone and the parent metal are also US inspected before the hydraulic test.
The productivity of this process is determined by the speed of the SAW operation. The pipe formation is normally capable of substantially higher production rates. In order to utilize the efficiency of the spiral pipe forming section, the plants are now designed on the basis of separate forming and SAW lines. In such plants, the forming line features a tack welding facility which has a capability of production speed matching with the speed of the forming line. The SAW line performs the seam welding off line in a number of several separate welding stands which match the forming line productivity.
Separated forming and SAW welding lines – The main feature of plants having separated forming and SAW welding lines is that there are two independent production units consisting of (i) pipe forming with internal tack welding, and (ii) inside and outside SAW operation on separate welding stands.
Apart from higher cost efficiency of such plant achieved due to the faster forming and tacking operation, there are also technical advantages of separating the two operations. These advantages are since both the operations can be individually optimized.
In the spiral pipe forming section, the merging strip edges (one on the already formed pipe section and the second on the incoming strip) are continuously joined by the inside tack welding. The tack welding process is performed by MAG welding at a speed of 12 m/min in the region of 6 o’clock position. CO2 is normally used as shield gas. The weld edges below the welding position run with virtually no gap over a rigidly fixed guide roller.
A parting- off device cuts the tack welded pipe string into the required individual lengths. This pipe cutting process is the last operation performed in the spiral forming line. Since the tack welding speed is high, it is necessary to use high speed plasma torch operating with water injection in place of conventional oxy-acetylene torch. The cut to length pipes are sent for the SAW operation downstream which is carried out in combined two pass SAW stands for final welding.
A special roller table rotates the pipe in precise accordance with its spiral joint, thus enabling SAW heads to perform first the inside welding and then the welding outside. Precise weld centre line alignment control of the inside and the outside welding heads is needed in this operation in order to minimize weld offset. The two wire or three wire methods are used for the inside and outside pass welding operations.
Apart from a few modifications, the subsequent stages of production such as pipe end machining, hydraulic testing as well as non destructive examinations and mechanical tests are in principle the same as those used in the integrated spiral welding lines. The feedbacks of these tests and inspections are immediately given to the individual production stages in order to ensure continuous product quality optimization.