Sejarah Pembuatan Baja Oksigen Dasar
Sejarah Pembuatan Baja Oksigen Dasar
Pembuatan baja oksigen dasar (BOS) adalah proses pembuatan baja dengan meniupkan oksigen murni (O2) dalam penangas logam cair yang terdapat dalam wadah yang dikenal sebagai tungku oksigen dasar (BOF), konverter LD, atau konverter sederhana.
Sejarah pembuatan baja dimulai pada abad ke-19, ketika Reaumur Perancis pada tahun 1772, Kelly dari Amerika Serikat pada tahun 1850 dan Bessemer dari Inggris pada tahun 1856 menemukan cara untuk meningkatkan besi kasar dengan mengendalikan kandungan karbon dari paduan besi, yang dengan demikian benar-benar menjadi baja. Sementara Reaumur, seorang ahli kimia, didorong oleh keingintahuan ilmiah, tetapi Kerry dan Bessemer sebagai insinyur, menanggapi kebutuhan akan baja dalam jumlah yang lebih besar dan kualitas yang lebih baik yang telah diciptakan oleh revolusi industri, dengan alat tenun, mesin uap, mesin dan relnya. . Ini telah memulai hubungan dialektis antara sains dan teknologi dan konsep dasar pemurnian logam panas (pig iron) dengan mengoksidasi karbon (C) dalam penangas cair ditemukan pada waktu itu.
Ini merupakan perubahan radikal dari reaksi gas-padat di tungku poros, pendahulu tanur sembur yang mereduksi bijih besi dengan arang, atau dari pelumpuran besi yang merupakan teknologi penempaan dan pemurnian yang dilakukan dalam keadaan padat dan telah tidak setara pada saat ini. Intensitas inovasi yang pada paruh kedua abad ke-19 sangat mengesankan dan membawa perubahan paradigma. Pembuatan baja oleh konverter Bessemer muncul pada tahun 1856, tungku perapian terbuka, yang dapat melelehkan skrap selain pemurnian logam panas, ditemukan sembilan tahun hanya setelah konverter Bessemer pada tahun 1865, dan konverter Thomas dasar dua belas tahun kemudian pada tahun 1877. Konverter Thomas menggunakan udara untuk pemurnian logam cair.
Konverter tiup udara yang ditemukan oleh Bessemer pada tahun 1856 dianggap sebagai proses pembuatan baja modern pertama. Pada tahun 1877, proses Thomas, proses Bessemer yang dimodifikasi, dikembangkan untuk memungkinkan pengolahan besi cair dengan fosfor tinggi. Dalam proses Thomas, fosfor (P) dioksidasi dalam apa yang disebut 'setelah pukulan' setelah sebagian besar C dikeluarkan dari bak. Proses perapian terbuka, juga disebut sebagai proses Siemens-Martin (SM), dikembangkan hampir bersamaan dengan proses Thomas. Proses perapian terbuka memanfaatkan perpindahan panas regeneratif untuk memanaskan udara yang digunakan dalam burner, dan mampu menghasilkan panas yang cukup untuk melelehkan dan menghaluskan skrap baja padat dan logam panas dalam tungku reverberatory. Sekitar tahun 1950-an, saat pembuatan baja oksigen dasar muncul di cakrawala, pembuatan baja terutama didasarkan pada teknologi proses perapian terbuka. Logam panas dan skrap dimasukkan ke dalam tungku horizontal besar di mana pembakar menyediakan energi untuk peleburan skrap. Tombak oksigen (O2) digunakan untuk meningkatkan efisiensi pembakar dan untuk menghilangkan C dan silikon (Si) dari logam panas. Proses perapian terbuka adalah proses allothermic dan dengan demikian energi eksternal harus dipasok ke tungku. Waktu tap-to-tap yang umum adalah delapan jam untuk ukuran panas 200 ton hingga 250 ton baja cair.
Inovasi besar berikutnya dalam pembuatan baja, yang mengikuti dengan cermat penemuan listrik, adalah proses pembuatan baja tanur busur listrik (Electric Arc Furnace/EAF). EAF diperkenalkan oleh Heroult di La Praz sekitar tahun 1900 di lembah pegunungan Alpen yang dekat dengan sumber energi baru karena pada saat itu belum layak untuk mentransmisikan listrik jarak jauh. Teknologi EAF didasarkan pada penyadapan energi yang merupakan pengganti batubara dan juga dalam peleburan sisa dalam jumlah yang lebih besar daripada perapian terbuka. Proses pembuatan baja EAF dikreditkan dengan memulai ekonomi daur ulang.
Konsep BOS kembali ke tahun 1856 ketika Henry Bessemer mematenkan proses pembuatan baja yang melibatkan peniupan O2 untuk mendekarbonisasi besi cair (Nomor Paten Inggris 2207). Pada saat itu tidak ada metode yang tersedia untuk memasok jumlah O2 yang dibutuhkan untuk proses tersebut. Jumlah komersial O2 tidak tersedia sama sekali atau terlalu mahal, dan karenanya penemuan Bessemer hanya tinggal di atas kertas dan tetap tidak digunakan. Pembuatan baja dengan meniup oksigen murni menjadi praktis pada tahun 1928, ketika perusahaan Linde berhasil mengembangkan metode (proses Linde-Fränkl) untuk memasok O2 murni dalam jumlah besar. Karena keberhasilan proses Linde-Fränkl, O2 juga menjadi sangat jauh lebih murah, sehingga kedua prasyarat (ketersediaan jumlah besar maupun ketersediaan oksigen murah) untuk pengenalan proses BOS terpenuhi.
Di Eropa dan Amerika Serikat, percobaan dengan O2 dilakukan berulang kali. Di antara mereka yang bekerja dengan O2 dengan kemurnian tinggi adalah Otto Lellep, tetapi konsepnya tentang 'meniup O2 secara vertikal ke bak besi cair' terbukti tidak berhasil. Menurut Hubert Hauttmann, yang ikut serta dalam eksperimen Lellep antara tahun 1936 dan 1939 di Gutehoffnungshütte, tempat ia bekerja pada waktu itu, tujuannya adalah untuk mengubah besi cair dengan meniupkan O2 murni melalui nosel di dasar konverter. Baja yang dihasilkan dengan cara ini memiliki kualitas yang buruk.
Selama Perang Dunia II, Insinyur dengan nama C. V. Schwartz dari Jerman, John Miles dari Belgia, dan Durrer Swiss dari dan Heinrich Heilbrugge dari Jerman mengusulkan versi pembuatan baja tiup O2 mereka, tetapi hanya Durrer dan Hellbrügge yang membawanya ke tingkat produksi skala massal .
Carl Valerian Schwarz mengajukan permohonan paten pada tahun 1939 untuk meniupkan oksigen ke dalam bak mandi dengan kecepatan supersonik. Tetapi metode ini juga 'belum mampu menghasilkan baja yang dapat digunakan'. Meskipun proses Linz-Donawitz (LD) selanjutnya memiliki kesamaan dengan paten Schwarz, ciri khasnya berbeda (misalnya 'central, vertical blowing,). Pasti karena pecahnya Perang Dunia II bahwa teknologi yang dijelaskan dalam paten Schwarz pada awalnya tidak mengarah pada aplikasi praktis apa pun. Juga pada akhir tahun 1930-an Robert Durrer dari Swiss memulai eksperimennya sendiri.
Setelah perang, Heinrich Hellbrügge dan Robert Durrer (Direktur teknis Roll'schen Eisenwerke) memulai eksperimen lebih lanjut di Roll'schen Eisenwerke di kota Gerlafingen, Swiss. Foto konverter oksigen tiup atas pertama di Gerlafingen ditunjukkan pada Gambar 1.
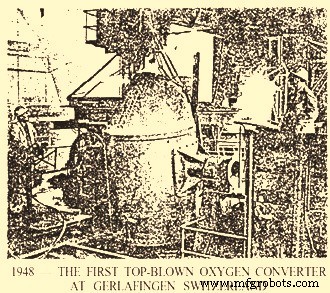
Gbr 1 Foto konverter oksigen tiup atas pertama di Gerlafingen
Durrer-lah yang meletakkan prinsip-prinsip teori dasar dan menyarankan VÖEST untuk meniup O2 dari atas di kapal terpisah, setelah kontak dibuat antara Gerlafingen dan VEST untuk kerjasama teknis skala industri. Serangkaian percobaan menggunakan konverter eksperimental 2 ton dimulai pada tanggal
3
Juni 1949 di lokasi VÖEST. Setelah tim di Linz mengalami beberapa kemunduran awal, terobosan dicapai pada awal ke-25
Juni 1949, ketika tekanan O2 diturunkan dan ujung blowing lance digeser lebih jauh dari bath, sehingga pancaran O2 tidak dapat menembus terlalu jauh. Dengan terobosan ini, dihasilkan baja yang dapat digulung menjadi lembaran tanpa masalah. Departemen eksperimental VÖEST memeriksa baja ini dan sangat positif dalam pengamatannya. Inilah saat ketika proses pembuatan baja konverter LD lahir. Eksperimen berlanjut sampai beberapa ratus panas 2 ton telah dihasilkan, setelah itu mereka dialihkan ke konverter eksperimental 15 ton yang dibangun khusus yang dipasang di udara terbuka. Batch pertama diproduksi pada tanggal 2
nd
Oktober 1949. Baja kelas baru menjalani pengujian metalurgi dan pengujian lainnya secara terus menerus.
Faktor kunci untuk inovasi ini adalah pergerakan cairan mandi. Sampai saat itu dianggap tidak mungkin untuk mendapatkan gerakan mandi yang cukup tanpa meniupkan O2 pada kedalaman yang lebih dalam. Tetapi gerakan ini dicapai dengan cara yang sangat memuaskan dengan pembentukan CO (karbon monoksida). Prinsip 'meniup lembut' juga mendorong pembentukan FeO yang pada gilirannya menyerap pengotor teroksidasi untuk membentuk terak. Ini membantu dalam produksi baja kelas baru yang sangat baik.
Selain Roll'schen Eisenwerke di Gerlafingen dan VÖEST, Mannesmann AG di Duisburg-Huckingen dan AMG (yaitu Donawitz) juga menyatakan minatnya pada Mei 1949 dalam proses peniupan O2 atau setidaknya metalurgi O2 secara umum. Selama eksperimen di Linz dan setelah demonstrasi proses, pembagian kerja yang tepat disepakati pada tanggal 17
Juni 1949. VÖEST akan melanjutkan pekerjaan dengan baja mentah dari Linz di kapal penyulingan yang jauh lebih besar sementara Mannesmann akan bereksperimen dengan peniupan O2 dari baja Thomas, Roll'schen Eisenwerke akan menyelidiki penggunaan O2 di EAF dan AMG akan melakukan tes dengan O2 dalam tungku besi kasar poros rendah. Perjanjian tersebut mewajibkan setiap orang yang terkait dengan metalurgi O2 ini 'untuk tidak mengeluarkan pernyataan atau menyampaikan informasi apa pun di luar perusahaan mereka sendiri mengenai perincian pemurnian O2 yang mereka ketahui atau kesimpulan yang mungkin telah mereka capai selama diskusi di Linz pada 17
t
Juni, 1949.
Berdasarkan kesepakatan, segera menjadi bukti dari eksperimen di Donawitz bahwa penggunaan oksigen di tungku poros tidak ada nilainya, di mana perusahaan mulai mengeksplorasi pendekatan yang berbeda. Proses yang dikembangkan di Donawitz untuk pemulihan terak dengan kandungan mangan tinggi dengan meniup dengan O2 menyebabkan kesadaran bahwa hanya penggunaan proses bertiup dengan O2 murni yang harus dipertimbangkan untuk ekspansi produksi baja dan rencana rasionalisasi di Donawitz. Setelah penyelidikan ekstensif dan pekerjaan pengembangan yang sukses pada pengaturan eksperimental 5 ton atau 10 ton, dengan oksigen yang dipasok selama pengujian pertama dari silinder yang disusun secara seri, manajemen perusahaan memutuskan untuk membangun pabrik baja baru, yang akan siap beroperasi dalam dua tahun. Insinyur Donawitz awalnya menamai proses mereka 'SK', dari inisial Jerman untuk 'Oxygen Converter'. Istilah ini membantu membedakan aktivitas VÖEST dan AMG sampai batas tertentu.
Pada tanggal 9
Desember 1949, direktur pelaksana VOEST Heinrich Richter-Brohm saat itu mengambil keputusan bukan tanpa risiko untuk pembangunan pabrik baja LD pertama. Tidak lama setelah ini dan setelah klarifikasi pertanyaan mengenai metode produksi untuk mutu baja yang lebih keras, diputuskan untuk membangun pabrik LD di Donawitz juga. Paten pertama untuk proses tersebut diajukan pada tahun 1950.
Dalam laporan penelitian dan jaminan kualitas tahunan tahun 1951, telah dinyatakan bahwa 'selama tahun peninjauan pekerjaan penelitian ekstensif dikhususkan untuk nilai baja LD, dan sebuah publikasi diterbitkan. Jenis baja ini diharapkan memiliki potensi besar dalam hal kualitas, dan khususnya akan memungkinkan baja dengan permukaan berkualitas tinggi yang dikombinasikan dengan sifat mampu bentuk dingin yang baik untuk diproduksi. Hal ini sangat penting untuk produksi lembaran logam tipis, di mana sampai sekarang sifat mampu bentuk dingin yang baik hanya mungkin jika cacat permukaan tertentu diterima (nilai baja yang terbunuh). Tetapi baja dengan kekuatan luluh yang lebih tinggi juga dapat diproduksi dengan sangat menguntungkan melalui proses pemurnian oksigen'.
Pada tahun 1951, Linz dapat memurnikan logam panas dengan O2 murni dalam pembuatan baja menjadi proses yang inovatif dan andal secara operasional untuk produksi baja berkualitas curah di Linz. Pengumuman proses baru dibuat untuk pertama kalinya pada bulan Desember 1951, pada konferensi 'Pemurnian Baja dengan Oksigen Murni' dari Masyarakat Metalurgi Austria di Leoben. Pada konferensi tersebut Robert Durrer menyatakan bahwa dua pabrik metalurgi (Linz dan Donawitz) telah mengembangkan konsep meniupkan O2 dengan kemurnian tinggi ke logam panas domestik menjadi proses industri yang layak, dan mengucapkan selamat kepada mereka atas kesuksesan besar ini. Dengan pengumuman ini Austria menjadi negara pertama yang memproduksi baja skala industri dari logam panas dengan meniupkan O2 murni. Konverter LD penampang sebelum dan selama peniupan O2 dalam penangas logam cair ditunjukkan pada Gambar 2.
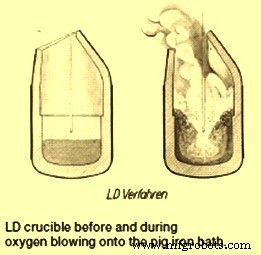
Gambar 2 Konverter LD penampang melintang sebelum dan selama peniupan O2 dalam penangas logam cair
Pada tanggal 27
November 1952 konverter pertama ditugaskan di LD Steelworks 1 (Gambar 3) di Linz yang merupakan tonggak sejarah dalam produksi baja dengan prinsip peniupan O2. Pada tanggal 5
Januari 1953 LD Steelworks yang pertama di dunia ini dibuka secara resmi. Pada tanggal 17
Juni 1953, LD Steelworks 1 di Linz telah memproduksi 100.000 ton baja LD, dan pada awal Desember 1953 250.000 metrik ton baja telah diproduksi. LD Steelworks kedua mulai beroperasi pada 22 Mei 1953 di sterreichisch-Alpine Montangesellschaft (ÖAMG) di Donawitz. Proses tersebut, yang kini dikembangkan hingga mencapai kematangan operasi penuh, melebihi semua harapan baik dalam kualitas baja yang dihasilkan maupun kelayakan ekonominya.
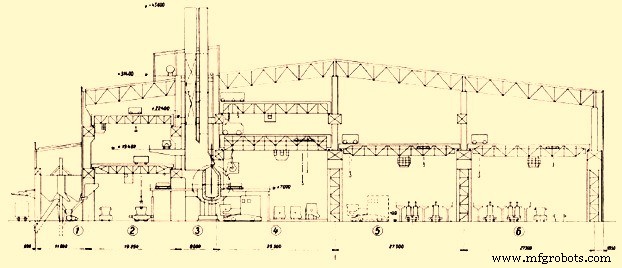
Gbr 3 Bagian melalui bangunan konverter LD Steelworks 1 di VÖEST
Kondisi metalurgi yang sangat menguntungkan dalam proses ini menghasilkan baja mentah yang bebas dari O2 sehingga tidak diperlukan deoksidasi. Baja tersebut adalah baja rendah gas, rendah nitrogen (N2), bebas dari fosfor (P), belerang (S), dan elemen penyerta yang tidak diinginkan. Dalam sifat teknisnya, terutama sifat mampu bentuk dingin, baja yang diproduksi dalam konverter LD jelas lebih unggul daripada baja yang dihasilkan oleh proses perapian terbuka. Proses LD juga mampu memasok baja struktural dengan kualitas luar biasa. Baja yang diproduksi di konverter LD telah memberikan hasil yang sangat baik pada struktur yang dilas yang mengalami beban yang sangat berat. Kumparan strip lebar dari baja yang diproduksi di konverter LD dipasok dalam jumlah besar ke pabrik penggilingan dingin baik di Jerman maupun di luar negeri.
Singkatan LD untuk Linz- Donawitz yang lazim digunakan saat ini diadopsi secara resmi pada tahun 1958. Nama LD dipilih karena VÖEST di Linz dan AMG di Donawitz telah mengembangkannya hingga skala industri.
Pada bulan Agustus 1954 Dominion Foundries &Steel, Ltd. dari Kanada menjadi perusahaan pertama di luar Jerman yang mengoperasikan pabrik baja LD. Itu memiliki dua konverter 60 ton. Itu diikuti pada tahun yang sama oleh McLouth Steel Corp. di AS, yang memulai pabrik baja LD dengan bantuan direktur pabrik VÖEST Rudolf Rinesch. Pada bulan September 1956, perusahaan ketiga di luar Jerman yang memulai operasi LD adalah Société des Aciéries de Pompey, Prancis, dengan konverter 15 ton. Pada tahun 1957, lima pabrik baja LD ditugaskan di Jerman Barat, Jepang, Brasil, dan Amerika Serikat, lima lainnya ditambahkan ke total pada tahun 1958, dua pada tahun 1959 di Rourkela India, dan delapan pada tahun 1960. Pada tahun 1960 lebih banyak pabrik baja LD sedang dibangun yang telah telah dibangun sampai saat itu, di Amerika Serikat, Jepang, Spanyol, Portugal, Italia (perluasan pabrik yang ada), Jerman Barat, Brasil, Inggris, Skotlandia, Norwegia, Argentina, Australia (1961), dan Prancis.
Inovasi teknis dalam proses manufaktur hulu, khususnya dalam proses pemurnian dan pengecoran, sangat penting untuk mencapai peningkatan berkelanjutan dalam tingkat kualitas baja yang diperlukan untuk berbagai aplikasi. Oleh karena itu, terjadi juga peningkatan terus-menerus dalam proses BOS sejak komisioning konverter LD pertama di Linz.
Proses LD asli terdiri dari meniup O2 di atas besi cair melalui nosel berpendingin air dari tombak vertikal. Pada tahun 1960-an pembuat baja mulai bekerja pada konverter yang ditiup bawah dan pengenalan hembusan gas inert untuk mengaduk logam cair dalam konverter dan penghilangan P kotoran
Pada awal 1970-an, pengembangan lebih lanjut dalam pembuatan baja BOS terjadi dengan peniupan bawah O2 dengan menggunakan tuyer yang dilindungi oleh gas hidrokarbon atau bahan bakar minyak. Setelah memiliki pengalaman dengan kedua jenis konverter ini, gabungan bejana bertiup atas dan bawah dikembangkan. Dan pada akhir 1970-an, pencampuran blowing diperkenalkan dalam konverter proses BOS. Kebanyakan konverter yang sekarang digunakan di dunia adalah tipe gabungan.
Dalam homogenitas dalam komposisi kimia dan suhu dibuat dalam lelehan selama pukulan O2 di konverter tiup atas karena kurangnya pencampuran dalam penangas logam. Ada zona yang relatif mati langsung di bawah rongga jet di konverter. Kebutuhan untuk meningkatkan proses pembuatan baja di konverter tiup atas telah menyebabkan pengembangan proses tiupan gabungan. Praktek blowing gabungan pertama yang diterima secara komersial adalah proses LBE (Lance Bubbling Equilibrium) yang dikembangkan oleh ARBE-IRSID. Proses ini jauh lebih erat kaitannya dengan proses BOF di mana semua oksigen disuplai dari tombak atas. Aspek hembusan gabungan dicapai dengan satu set elemen berpori yang dipasang di bagian bawah konverter melalui mana argon atau nitrogen dihembuskan. Dalam proses LBE, gas nitrogen biasanya digunakan hampir secara eksklusif untuk sebagian besar pukulan dalam kisaran 3 -11 N Cum/menit. Namun di bagian akhir dari pukulan ketika penyerapan nitrogen dapat menimbulkan masalah, gas argon digunakan untuk mengaduk. Selain itu, argon digunakan hampir secara eksklusif sebagai gas inert untuk pengadukan pasca tiup, saat ini kecepatannya dinaikkan menjadi 10-17 N Cum/menit.
Selama tahun-tahun awal proses konverter LD, gas atas dibakar seluruhnya di mulut konverter melalui kap terbuka dan kemudian didinginkan di dalam cerobong baik secara tidak langsung dengan air atau dengan sistem pendingin evaporasi. Saat itu sekitar 300 Kg steam dan 250 Cu m off gas per ton baja mentah diproduksi.
Aspek lingkungan merupakan tantangan serius bagi proses konverter pada saat diimplementasikan secara industri pada tahun 1950-an. Kehalusan debu di konverter off gas memaksa pemasok proses untuk mengembangkan sistem dedusting baru. 1 gram debu konverter memiliki luas permukaan yang terlihat antara 300 hingga 500 m persegi. Untuk menghindari efek optik 'asap coklat' secara umum, debu harus dibersihkan dari sistem ke tingkat kurang dari 100 mg per meter kubik. Untuk ini digunakan sistem de dusting tipe basah dan tipe kering. Tantangan menjadi lebih dan lebih dari sebuah peluang untuk proses converter sebagai jumlah isu lingkungan tumbuh. Dan kesempatan ini membantu dalam mengembangkan sistem pemulihan gas konverter dengan pembakaran yang ditekan. Saat ini ekonomi dan lingkungan menuntut agar energi dalam gas konverter dan besi yang mengandung debu dikumpulkan dan didaur ulang secara efisien.
Selama awal tahun enam puluhan, proses dikembangkan untuk memulihkan gas atas nilai kalori tinggi dari konverter sehingga hal yang sama dapat digunakan sebagai bahan bakar gas di dalam pabrik. Ini telah dicapai melalui pembakaran yang ditekan. Peralatan proses yang dipasang di atas mulut konverter berfungsi untuk mendinginkan, membersihkan dan memulihkan gas konverter dengan bantuan pembakaran yang ditekan. Dengan pembakaran gas konverter atas yang ditekan, 70-100 Cu m gas konverter per ton baja mentah dengan nilai kalor berkisar antara 1600 -2000 Kcal/N Cu m gas diperoleh kembali. Selain 80 Kg/ton uap baja mentah juga dibuat jika sistem pendingin evaporatif untuk gas atas disesuaikan.
Selama hari-hari awal pembuatan baja dengan proses konverter, asap coklat dari cerobong asap menunjukkan bahwa konverter bekerja. Saat ini sebagai hasil dari sistem pemulihan dan pembersihan gas konverter, pengoperasian konverter hanya terdeteksi dari cerobong asap.
Sejak tahun 1977, sejumlah perbaikan telah dibuat dalam desain bejana konverter itu sendiri, dalam bahan tahan api dan praktik aplikasi tahan api, dan dalam desain nozel bawah tungku dan tombak oksigen, yang berkontribusi besar pada peningkatan efisiensi pembuatan baja dan pengurangan konsumsi unit bahan mentah dan refraktori, yang semuanya berguna dalam memperpanjang masa pakai tungku hingga beberapa ribu panas.
Saat ini ukuran konverter telah meningkat dan konverter besar yang menampung hingga 350 metrik ton besi tersedia. Pada tahun 2014, dari total produksi baja mentah dunia sebesar 1669 juta ton, produksi baja mentah dengan proses BOS telah mencapai 1229 juta ton, yang berarti 73,7% dari total produksi baja global.