Batesville Casket:Kasus ditutup
Departemen pemeliharaan tanaman yang baik, di beberapa hormat, seperti wasit sepak bola profesional yang baik.
"Jika kita melakukan pekerjaan kita dengan benar, tidak ada yang tahu bahwa kita ada." Demikian kata George Doll, manajer pemeliharaan di pabrik perakitan Batesville Casket Company di Batesville, Ind.
Dalam kutipan itu, "tidak ada" yang benar-benar seseorang. Untuk Batesville, itu adalah pelanggan - sebuah keluarga yang telah memesan tempat peristirahatan terakhir untuk orang yang dicintai. Pelanggan mengharapkan peti mati Batesville, yang telah dibuat dan dipersonalisasi khusus untuk yang meninggal, tiba di rumah duka tepat waktu dan bebas cacat. Itu adalah tugas yang menantang mengingat pesanan dilakukan pada hari sebelumnya.
Anda tidak membeli peti mati "dari rak" - tidak di zaman ini ketika orang Amerika menghargai individualitas dan mencari kenangan. Orang ingin diingat karena siapa mereka dan apa yang mereka perjuangkan. Tujuh puluh lima persen dari semua produk Batesville dipersonalisasi berdasarkan daftar permintaan pelanggan standar dan non-standar (warna eksterior, etsa eksterior, pegangan, warna interior, kain, bordir, dll.). Sebuah keluarga dapat menghormati kakek, lulusan dan pendukung University of Texas, dengan memesan peti mati dengan bagian luar logam berwarna oranye yang terbakar, logo sekolah terukir di panel sudut perak dan "Hook 'em, Horns" disulam ke kain di tutup bagian dalam. Ini akan dibuat pada satu jalur produksi (di mana setiap peti berbeda dari yang ada di depannya dan yang di belakangnya) dan dikirimkan dalam 24 jam.
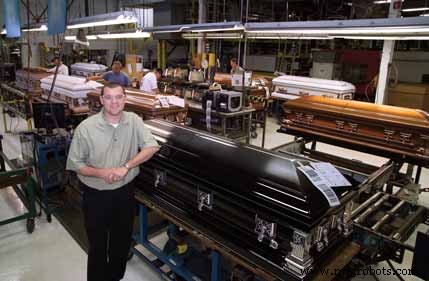
Pengawas perakitan Joe Dwenger percaya pada kekuatan pemeliharaan.
"Pelanggan mengharapkan lebih dari kami," kata manajer pabrik Todd Dennis. "Seiring meningkatnya permintaan, itu meningkatkan tekanan pada sistem kami."
Tidak memenuhi harapan berarti tekanan mendapatkan yang terbaik dari sistem pabrik. Peralatan gagal. Waktu henti menyebabkan pengiriman terlambat. Peralatan dilakukan dengan tidak benar atau di luar spesifikasi. Itu menyebabkan masalah kualitas. Jika tertangkap di lantai pabrik, masalah kualitas berarti pengerjaan ulang dan pengiriman mungkin terlambat. Masalah yang tertangkap di rumah duka berarti ketidakpuasan pelanggan. Ketika Anda gagal, pelanggan tahu siapa Anda - mungkin bukan dari nama, tapi pasti dari fungsinya. Tanyakan saja kepada wasit sepak bola yang menghadapi catcall dan bola es setelah meniup keputusan pada permainan yang menentukan.
"Jika Anda tidak memenuhi tanggung jawab Anda," kata sensei lean perusahaan Mike Wroblewski, "Anda menggali lubang yang dalam untuk diri Anda sendiri."
Di fasilitas Batesville ini, yang menampung hampir 1.000 aset produksi utama, departemen profesional multi-kerajinan Doll menjaga tekanan tetap terkendali. Uptime di lantai pabrik seluas 300.000 kaki persegi sangat tinggi. Hasilnya, kualitas dan hasil first-pass menjadi tinggi. Siklus dan pengembalian yang hilang sangat rendah.
"Apakah pelanggan mendapatkan apa yang dia inginkan di penghujung hari?" kata inspektur pemeliharaan Butch Flasphohler. "Itu adalah penghakiman terakhir."
Organisasi pemeliharaan Batesville transparan kepada pelanggan. Mereka tidak tahu siapa George Doll, Butch Flasphohler atau salah satu dari 32 rekan departemen lainnya, dan itu bagus. Namun, rekan kerja di pabrik dan perusahaan berusia 123 tahun menyadari kontribusi tim terhadap keandalan sistem, aliran produk, peningkatan berkelanjutan setiap hari, operasi ramping, dan reputasi cemerlang dalam industri. Dan, itu bagus.
Keunggulan pemeliharaan dan keandalan merupakan faktor dalam memenangkan IndustryWeek Penghargaan Pabrik Terbaik pada tahun 2006 dan gelar regional dalam kompetisi Association for Manufacturing Excellence 2007 untuk pabrik dengan kinerja terbaik.
Pencapaian adalah, dan masih, merupakan usaha besar.
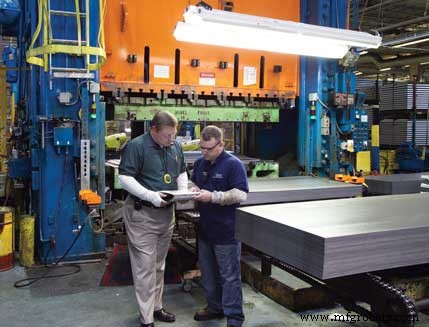
Mike Wroblewski (kiri), lean sensei Batesville Casket Company, memeriksa beberapa data produksi dengan operator di garis stamping.
DNA DAN PEMBEBASAN
Batesville adalah pembuat peti mati No. 1 di Amerika (penjualan $659 juta pada tahun 2006), dan telah berada di puncak untuk waktu yang sangat lama. Perusahaan mengaitkan kesuksesannya dengan lingkungan yang dibangun di atas perbaikan terus-menerus.
"Perubahan telah menjadi bagian dari budaya Batesville selama 123 tahun. Itu ada dalam DNA kami," kata Dennis. "Kami memiliki hasrat membara untuk membuat segalanya lebih baik."
Baik itu terkait dengan peralatan, proses, produk, atau logistik, perusahaan tidak dapat berhenti mengutak-atik.
"Kami akan melihat sesuatu dan berkata, 'Secara keseluruhan, ini bekerja dengan baik. Tapi apa yang tidak bekerja dengan baik?' Kami akan mengupas bawang dan melihat komponen yang tidak bernilai tambah," kata Dennis. "Banyak perusahaan akan berkata, 'Itu bekerja dengan baik. Mengapa merusaknya?' Kami tidak mendekatinya seperti itu. Kami benar-benar ingin menjadi lebih baik setiap tahun. Dibutuhkan sikap seperti itu. Terkadang menyakitkan, tetapi itulah yang membuat kami istimewa."
Alasannya sederhana:Anda bisa proaktif dan melihat peluang yang ada dalam perubahan, atau reaktif dan dipaksa untuk berubah sebagai akibat dari tekanan internal atau eksternal. Ini masalah kendali. Kendalikan aset pabrik, atau mereka akan mengendalikan Anda.
Perubahan dan peningkatan berkelanjutan diformalkan dalam prakarsa lean manufacturing dan peningkatan keandalan perusahaan. Dijalin bersama hampir dua dekade lalu, ikatan itu tumbuh lebih kuat setiap tahun.
"Ramping dan keandalan berjalan seiring," kata Doll. "Untuk menjadi ramping, Anda harus menjalankan lini produksi Anda secara alami. Jika Anda memiliki waktu henti atau kerusakan yang tidak direncanakan, itu mengganggu aliran. Itu kemudian memengaruhi kualitas, produktivitas, semuanya. Anda benar-benar perlu mengontrol frekuensi kerusakan dan jumlah waktu yang Anda paksa untuk beralih ke mode turun atau siaga. Bisa dibilang kontinuitas produktivitas adalah bagian terpenting dari organisasi lean yang baik."
Itu bukan hanya sikap pemeliharaan.
"Anda tidak dapat memiliki lean tanpa keandalan," kata Dennis. "Jika kami tidak memiliki sistem yang andal, perhatian Anda beralih ke perbaikan peralatan dan proses. Anda berjuang untuk menjadi stabil. Lean benar-benar dibangun di atas stabilitas."
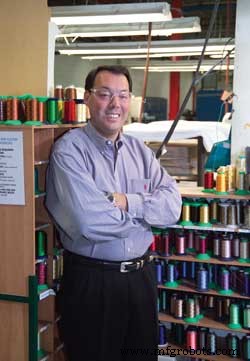
Manajer pabrik Todd Dennis mengatakan, "Perubahan telah menjadi bagian dari budaya Batesville selama 123 tahun. Itu ada dalam DNA kami."
Fasilitas di Indiana memproduksi peti mati perunggu, tembaga, baja tahan karat dan baja.
Foto oleh Bill Krider, Krider Photography
Pengukur keunggulan keandalan dan pemberdayaan lean lainnya adalah:
Waktu beroperasi: Area kritis dari proses produksi pabrik membanggakan 99 persen uptime. Di daerah yang kurang kritis, angkanya 96 persen.
Siklus yang hilang: Takt time adalah detak jantung dari jalur perakitan. Pada hari biasa, garis maju setiap 56,5 detik. Hilangnya 56,5 detik waktu produksi berarti satu siklus telah hilang. Produk terlambat dari jadwal.
"Kehilangan 56 detik produksi dianggap sebagai kegagalan besar di sini," kata pengawas perakitan Joe Dwenger. "Pada sebagian besar pabrik, efisiensi 85 persen baik-baik saja. Di sini, 100 persen. Tidak ada tunjangan harian untuk tidak menghasilkan 100 persen. Kami memegang pemeliharaan itu dengan sangat tegas. Mereka meresponsnya dengan baik."
Tingkat persentase kehilangan siklus pabrik kurang dari 1 persen.
Perpaduan kerja proaktif/reaktif: Pekerjaan proaktif terdiri dari 75 persen dari total beban kerja di area misi-kritis. Di area yang tidak terlalu kritis, campurannya adalah 50/50.
"Sebagian besar pekerjaan reaktif dilakukan pada barang yang lebih kecil dan dapat dibuang," kata insinyur keandalan Steve Noel. "Anda dapat membuang banyak uang pada gearbox $50 dan masih tidak tahu kapan itu akan berhenti. Kami tidak terlalu memperhatikan hal-hal kecil yang dapat ditangani dengan perubahan cepat."
Pekerjaan reaktif sebelumnya merupakan 75 persen dari semua kegiatan pemeliharaan.
Kualitas: "Kualitas mencegah kami mendapatkan aliran yang baik. Saya memiliki siklus kehilangan terkait kualitas sebanyak yang saya lakukan pada waktu henti peralatan. Saya tidak ingin melewatkan produk buruk apa pun melalui pabrik," kata Dennis.
Apa tautan pemeliharaan kualitas?
"Jika Anda mengalami gangguan terus-menerus dengan kerusakan atau peralatan yang tidak berfungsi, itu akan merusak produk atau cukup mengganggu aliran sehingga operator tidak melakukan pekerjaan mereka dalam pengaturan kerja standar," kata Doll. "Jika Anda mengganggu aliran, Anda akan mengganggu kualitas."
KISAH PERBAIKAN TERUS MENERUS DARI TAPE:DITCA VERSUS DITKA
Nama: DITCA (Analisis Penanggulangan Target Peningkatan Harian)
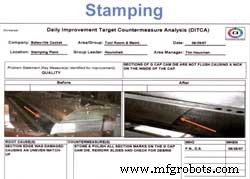
Nama Panggilan: Formulir
Klaim ketenaran: Rekanan di pabrik Batesville Casket di Batesville, Ind., telah mengirimkan ribuan formulir DITCA sejak dibuat pada akhir 1990-an (biasanya 500 hingga 750 per tahun). Batesville menghemat lebih dari $1 juta per tahun dari 2002 hingga 2006 dari DITCA.
Dapat dikutip: "Setiap hari, seorang pemimpin tim atau pemimpin tim cadangan harus memberikan peningkatan," kata pengawas perakitan Joe Dwenger. "Tidak harus mendidihkan lautan. Ini bisa menjadi ide yang sangat sederhana. Bentuk yang akan digunakan orang-orang ini untuk menangkap dan membagikan perbaikan 'sebelum dan sesudah' ini adalah bentuk DITCA." Nama: Ditka (Mike Ditka)
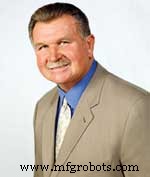
Nama Panggilan: Dan Pelatih
Klaim ketenaran: Mike Ditka adalah satu dari hanya dua pria yang memenangkan Super Bowl sebagai pemain (Dallas Cowboys), asisten pelatih (Dallas) dan pelatih kepala (Chicago Bears). Sebuah akhir yang ketat selama 12 musim National Football League, ia diabadikan ke dalam Hall of Fame Sepak Bola Pro pada tahun 1988. Ia memiliki rekor kepelatihan NFL 121-95.
Dapat dikutip: "Mereka yang hidup di masa lalu adalah pengecut dan pecundang."
"Jika Anda cukup bertekad dan bersedia membayar harganya, Anda bisa menyelesaikannya."
"Jika Anda tidak bermain, maka jangan mengambil gaji."
"Jika Anda bisa membuat sejarah, lakukanlah."
FIVE-WHYS AND RCA
Organisasi pemeliharaan Batesville menggunakan berbagai strategi - sebut saja lean, reliability, atau sekadar smart - untuk mengukur dan membuat segalanya lebih baik setiap hari.
Mungkin metodenya yang paling efektif adalah melepaskan kekuatan otak anggota timnya. Karyawan per jam dan gaji didorong untuk berpikir:
kritis untuk menentukan jawaban berdasarkan fakta untuk masalah lantai pabrik; dan,
secara kreatif untuk mengembangkan solusi inovatif untuk kebutuhan lantai pabrik.
Individu dan kelompok kecil menggunakan lembar analisis lima alasan dan prinsip analisis akar penyebab (root cause analysis/RCA) untuk sampai ke akar masalah.
"Kami telah menggunakan diagram tulang ikan, tetapi kami menemukan pendekatan lima alasan menjadi sedikit lebih efisien bagi kami," kata Flasphohler. "Ketika Anda selesai dengan latihan, Anda memiliki jawaban yang lebih faktual."
Sistem finish turun, menyebabkan hilangnya 70 siklus. Apa yang terjadi? Gunakan analisis lima alasan untuk mengetahuinya.
Mengapa peralatan gagal? Papan sirkuit terbakar.
Mengapa papan sirkuit terbakar? Ini terlalu panas.
Mengapa terlalu panas? Udara tidak cukup.
Mengapa tidak mendapatkan cukup udara? Filter tidak diubah.
Mengapa filter tidak diubah? Tidak ada jadwal pemeliharaan preventif untuk melakukannya.
"Ketika kami tiba di suatu penyebab, kami melakukan analisis akar penyebab dan membuat perbaikan permanen sehingga tidak terjadi lagi," kata Doll. "Kami ingin fokus memperbaiki sistem, bukan hanya menghilangkan gejala."
Anggota tim mengatakan pendekatan lima alasan harus digunakan setiap kali suatu masalah menyebabkan hilangnya lima siklus atau lebih. Insinyur keandalan Noel memimpin penyelidikan, seperti yang dikatakan Doll, "jika ada petunjuk bahwa ini akan menjadi kerusakan berulang."
ANALISIS MENDALAM
Pemimpin pemeliharaan menerapkan pemikiran kritis untuk membedah lanskap pabrik dan menentukan cara terbaik untuk menggunakan sumber dayanya yang terbatas (tenaga, waktu, perhatian, teknologi, dan anggaran).
"Fokus kita harus pada apa yang paling penting," kata Doll.
Pabrik melakukan analisis kekritisan formal untuk menentukan peralatan dan proses yang paling penting dan mahal.
"Kami tahu peralatan apa yang harus berfungsi, apa yang harus dipertahankan, agar produk tetap mengalir," kata Doll. "Itu diukur dengan dampak fisik dan finansial."
Biaya memainkan peran besar dalam tingkat keparahan. Siklus yang hilang sangat mahal dari titik transfer cat hingga akhir proses perakitan. Di sini, perawatan mendapat pukulan setinggi $125 per siklus yang hilang. Lima belas dolar, bagaimanapun, adalah label harga untuk siklus yang hilang di departemen fabrikasi. Fakta dan angka - interaksi biaya dan kinerja aset - menentukan rencana pertempuran pemeliharaan.
"Saya memiliki daftar spreadsheet untuk setiap peralatan dan jumlah siklus yang saya keluarkan selama sebulan, bersama dengan angka dolar terkait," kata Doll. "Anda dapat memilih jika ada bagian tertentu dari peralatan yang menyebabkan masalah. Anda kemudian dapat mengarahkan keandalan untuk mengerjakannya."
Ini juga membantu untuk menentukan apakah aset paling baik dilayani melalui cara proaktif (pemeliharaan preventif dan/atau pemeliharaan prediktif, dan sejauh mana) atau cara reaktif (jalankan hingga gagal).
Terkait dengan itu, maintenance juga telah melakukan analisis criticality untuk tenaga kerja. Anda hanya memiliki begitu banyak jam kerja dalam sehari. Bagaimana Anda akan menggunakannya? Proses tersebut menetapkan parameter dan menghasilkan pemahaman yang lebih baik tentang pekerjaan bernilai tambah vs. pekerjaan tidak bernilai tambah.
"Jika Anda memiliki orang-orang yang berlarian melihat rol individu di konveyor, Anda akan menghabiskan tenaga kerja Anda," kata Doll. "Bandingkan dengan memiliki tim yang bekerja untuk meningkatkan cara produk melewati konveyor itu atau menghilangkan potensi masalah kualitas di sepanjang konveyor itu. Anda mendapatkan lebih banyak hasil dari investasi dolar Anda. Anda dapat meningkatkan kualitas dan aliran produk."
Produk sampingan dari pekerjaan ini adalah peningkatan perencanaan dan penjadwalan, serta pengurangan waktu lembur.
Analisis lain, yang satu ini menargetkan pemeliharaan preventif (PM), mempengaruhi tenaga kerja dan strategi perawatan aset. Departemen telah membanggakan dirinya sebagai "pemasok berat" kegiatan PM. Studi formal menentukan bahwa banyak peralatan menerima terlalu banyak perhatian melalui PM. Alih-alih melakukan tugas setiap enam minggu, fakta mungkin menunjukkan jadwal 12 minggu yang lebih tepat.
"Apakah Anda kurus saat melakukan semua pekerjaan ekstra itu? Saya rasa tidak," kata Doll. "Saya pikir untuk PM hari ini, kami berjalan sebaik atau lebih baik dari sebelumnya. Cara sebelumnya membuat kami terhambat."
BERPIKIR KREATIF
Rekan pemeliharaan juga menggunakan kreativitas untuk menyulap dengan cara yang lebih baik. Setiap hari, karyawan operasi meminta tim Doll untuk merancang solusi yang rapi untuk masalah kualitas, produktivitas, keselamatan, dan ergonomis.
Ini bukan tentang memasang rantai tarik untuk lampu atau kipas (permintaan sebelumnya yang sering dilakukan).
Komponen yang lebih kecil dimasukkan ke dalam peti dengan arah yang salah. Pemeliharaan mendesain "pengukur go/no-go" (perangkat poke-yoke) yang hampir tidak memungkinkan untuk menempatkan komponen secara tidak benar.
Sulit untuk melihat apakah "debu" dari kain katun menumpuk di dalam mesin. Pemeliharaan membuat jendela Plexiglas untuk memastikan visibilitas dan pengenalan saat terjadi penumpukan.
Sebuah mesin memiliki masalah harmonik yang substansial. Pemeliharaan membuat sistem pendukung yang inovatif untuk menghentikan getaran.
Tutup peti mati muncul di stasiun perakitan akhir. Pemeliharaan memasang "kantong pasir di atas katrol" untuk menjaga tutupnya.
Seorang operator harus menjangkau ke bawah untuk mengambil bagian. Pemeliharaan membangun bangku yang dapat diisi yang menempatkan produk pada ketinggian yang tepat.
Tujuannya adalah solusi tahan lama dan berbiaya rendah, bukan monumen baja tahan karat yang mahal.
Pembuat alat, teknisi CAD, dan anggota Grup Layanan Teknik situs adalah beberapa sumber daya yang berharga bagi teknisi pemeliharaan dalam hal ini dan lainnya.
"Tantangannya adalah membuat segalanya menjadi sederhana," kata Dennis. "Ide dan kecerdikan kompleks yang memungkinkan Anda mencapai kesederhanaan. Produsen dipaksa untuk menjadi kreatif. Itu datang bersama bisnis."
Solusi kreatif dan solusi yang merupakan hasil dari pemikiran kritis inti didokumentasikan dalam lembar Analisis Penanggulangan Target Peningkatan Harian. DITCA memberikan penjelasan "sebelum dan sesudah" tentang proyek perbaikan. Ini menguraikan masalah, gejala, akar penyebab dan tindakan pencegahan, dan mencantumkan semua rekan yang berperan dalam perbaikan.
"Orang-orang mengisi formulir mereka sendiri, mengambil gambar mereka sendiri dan mendokumentasikan semua tabungan mereka sendiri," kata insinyur listrik John Busek. "Setiap hari Jumat, kami mengadakan pertemuan di mana orang-orang yang menyelesaikan DITCA minggu itu mempresentasikan studi kasus mereka. Pekerjaan mereka diakui."
Perbaikan bisa kecil atau besar.
Batesville, sebuah perusahaan dengan tujuan keberlanjutan yang kuat, telah mendapat manfaat dari proyek-proyek yang telah memperbaiki kebocoran udara terkompresi, menghemat air, dan mengurangi konsumsi listrik. Busek telah mengarahkan peralihan penerangan pabrik dari lampu merkuri ke lampu neon berteknologi tinggi. Ini akan meningkatkan pencahayaan dan menghemat banyak uang.
JAM BERKENTIT
Penyelamatan lainnya lebih dramatis. Organisasi pemeliharaan Batesville menjawab panggilan tersebut bila diperlukan. Respon cepat, mentalitas kru pit bekerja keras untuk memulihkan aliran dan memastikan kepuasan pelanggan.
Seperti yang dinyatakan sebelumnya, insiden produksi dan kualitas (tekanan untuk sementara mengalahkan sistem) berarti waktu henti dan siklus yang hilang. Setiap menit turun adalah kerugian. Lean telah menurunkan tingkat persediaan buffer ke titik di mana kegagalan lima menit menciptakan reaksi yang signifikan. Hal ini berpotensi memberikan dampak negatif bagi pelanggan. Apa yang akan kamu lakukan?
"Atasi masalah secepat mereka datang. Jangan biarkan berlarut-larut," jawab lean sensei Wroblewski dengan nada filosofis.
Hasilnya diatur dengan cara yang akan membuat kepala kru NASCAR bangga. Inspektur Majelis Dwenger menyebutnya "sangat menakjubkan".
"Begitu terjadi sesuatu, saya memiliki tiga hingga lima orang pemeliharaan yang berkumpul di tempat dan memulai prosesnya," kata Doll. "Mereka dengan cepat memeriksa masalahnya. Jika mereka tidak dapat menyelesaikannya, lapisan dukungan tambahan dibawa masuk. Orang-orang ada di lokasi, di radio, di komputer. Kami memiliki meja pemecahan masalah pusat yang memberikan saran ahli. Prosesnya bergerak cepat sampai mereka mencapai solusi. Ketika Anda menjadi anggota kru ini, Anda bukanlah sebuah pulau, Anda adalah sebuah tim."
Operator adalah peserta aktif dalam proses tersebut, mengambil peran investigasi, teknis, dan logistik untuk mengembalikan dan menjalankan alat berat.
"Kunci keandalan bukan hanya kemampuan prosesnya," kata Dennis. "Juga ketika sesuatu keluar dari penyesuaian, bagaimana kita bereaksi?"
TEKAN PROAKTIF
Bor kru pit sangat mengesankan, tetapi tidak digunakan sebanyak hari ini seperti lima tahun atau lebih yang lalu. Teknologi pemeliharaan prediktif (PdM), diterapkan bersama dengan atau sebagai hasil dari analisis kritis, lima alasan dan/atau akar penyebab, membuat departemen lebih proaktif.
Serupa dengan cara lain untuk mendekati keunggulan keandalan, tim Doll menggunakan PdM sebagai alat untuk membuat keputusan berdasarkan fakta.
"Kami tahu persis apa yang dilakukan mesin itu," kata Busek. "Alih-alih keluar dan mengganti beberapa komponen dan berharap Anda menemukan yang benar, kami dapat mempersempitnya menjadi komponen yang rusak atau meragukan."
Noel mengawasi program PdM, yang meliputi termografi inframerah, analisis getaran, pelurusan laser, dan analisis oli. "Anda tidak bisa kurus tanpa hal-hal ini," katanya.
Rekanan pemeliharaan menggunakan alat pada shift pertama (07.00 hingga 15.30) dan shift kedua (16.30 hingga 01.00) saat mesin sedang berjalan untuk mengidentifikasi peralatan dan komponen yang menyimpang dari kinerja optimal.
Koreksi dan penggantian selanjutnya dilakukan saat produk tidak berjalan - baik pada pukul 15:30. sampai 16:30 kesenjangan pemeliharaan atau shift ketiga pukul 1 pagi hingga 7 pagi. PM yang lebih besar dan perubahan sistem juga dilakukan selama shift kuburan itu.
PEKERJAAN PROAKTIF
Pemeliharaan proaktif bukan hanya tentang PM dan gadget berteknologi tinggi. Ini juga cara Anda memecahkan masalah tenaga kerja Anda. Pabrik Batesville memiliki persentase pekerja yang besar dengan pengalaman 25 tahun atau lebih. Awak pemeliharaan memiliki bagian dari pekerja senior. Gelombang pensiun dimulai beberapa tahun yang lalu, meninggalkan pabrik dengan tantangan:Bagaimana Anda mempertahankan keuntungan ketika pekerja kunci Anda pergi?
Doll, karyawan Batesville 40 tahun, menjadi proaktif. Delapan tahun yang lalu, dia mulai mempekerjakan pekerja muda untuk mempelajari tali dari para veteran tua.
"Kami memulai mereka dengan tingkat yang lebih rendah, tetapi mereka berkembang menjadi posisi petugas pemeliharaan penuh," katanya. "Dibutuhkan tiga hingga lima tahun dari saat kami merekrut orang baru hingga saat kami merasa percaya diri padanya, bahwa ia dapat menambah tim. Waktu dan pengalaman, ditambah sejumlah besar pelatihan, mengarah pada keselamatan, buku -pengetahuan berbasis dan pengetahuan langsung."
Doll mengatakan 30 persen timnya termasuk dalam kategori "muda, sedang naik daun".
"Harus ada penumpukan pengetahuan dan pengalaman dan keterampilan. Itu tidak bisa terjadi dalam semalam," katanya. "Jika Anda tidak memulai sampai orang-orang Anda berjalan keluar dari pintu, Anda tidak akan pernah keluar dari lubang itu."
Untuk menemani serentetan perekrutan, departemen telah menerapkan pekerjaan standar. Perintah kerja sekarang mencakup instruksi keselamatan standar untuk tugas tertentu. PMs will outline items such as proper lubricant types and amounts; greasing specifications; and correct belt types and sizes.
"We have digital pictures with arrows pointing, for instance, to where the grease zerks are," says Noel. "Some of that stuff can be hard to find, especially if you are a less experienced technician."
GROUNDED
Doll thinks highly of his maintenance department and the work that crew members do to eliminate system pressures and enable unhindered production of a very special product. They remain a quiet, unknown entity outside of manufacturing industry circles, and that's good. As a team, this "nobody" is truly something.
"In terms of delivering reliability to the plant and to the company, I think we are an 8 to a 9 on a scale of 1 to 10," he says. "I would like to think that we are a 10, but we have some opportunities."
Ah, continuous improvement. That must be the DNA kicking in.
"We still have downtime. We can still cut out some of the reactive work. We can do more training," he says. "We are not there yet."
Plans for the near future include the following:
make greater use of design for maintainability and reliability principles when purchasing new equipment;
enhance existing efforts to standardize parts and reduce inventory in the tool crib;
reduce the "deadly waste" of waiting by making critical systems more robust; Doll states, "250 production workers waiting because the line is down - that is a terrible amount of waste"
continue to hire people who will make a difference to the plant and the company; says Dennis, "We want to hire people who are problem-solvers"
Achievements will be a major undertaking, and they will be accomplished through personal accountability.
That goes for managers.
"The simplest and best way is to lead by example," says Wroblewski. "If you don't have actions behind your words, then they are going to be hollow. People aren't going to follow and they aren't going to listen to you. Leading by example is truly the best way that any leader can help show that this is the path that we want to take."
And, it goes for every associate.
"We always have something in front of us that we haven't yet achieved. It keeps pushing us forward," says Dennis. "None of us are paid for past performance. It is dependent on what each of us does today."
The plant gained sizable ground in 2007, the year after winning a major North American award. The same should hold true in 2008, the year after capturing another big honor.
"We have been recognized by industry. That puts responsibility and pressure on us," says Wroblewski. "We must strive and do all we can to live up to these accolades."
A final resting place? Hardly.
"Our goals don't allow us to rest," says Dennis.
The push to continuously improve can be painful, but it is what makes Batesville Casket Company so special.
THE DIRT ON BATESVILLE
Plant: Batesville Casket Company plant in Batesville, Ind.
Plant size: The assembly plant encompasses 300,000 square feet.
Plant employment: Approximately 600 associates, including 34 in the maintenance department. The maintenance total includes 29 hourly associates and five salary associates. The facilities group has an additional three workers. The plant is an open union shop. Employees can opt, if they choose, to be members of a union.
Products: The facility manufactures bronze, copper, stainless steel, steel and hardwood caskets.
Production: The plant completes one casket every minute of a production shift.
FYI: Batesville Casket Company is an operating unit of Hillenbrand Industries, which is also based in Batesville, Ind. ... The Indiana assembly plant won an IndustryWeek Best Plants award in 2006 and was the Great Lakes Region winner of the Association for Manufacturing Excellence's Award for Manufacturing Excellence in 2007. ... Batesville's sister plant in Manchester, Tenn., was the national winner of AME's Award for Manufacturing Excellence in 2006.