Menghilangkan Cacat melalui Keandalan Peralatan
Sejak munculnya inisiatif bisnis yang berfokus pada kualitas seperti Total Quality Management (TQM) dan akhirnya Six Sigma, perusahaan telah berfokus pada pengurangan cacat produk akhir mereka seminimal mungkin. Definisi proses Six Sigma yang diterima secara luas adalah proses yang menghasilkan 3,4 bagian cacat per sejuta peluang (DPMO).
Satu-satunya hal yang paling penting untuk sasaran kualitas keseluruhan ini adalah variasi. Banyak profesional kualitas yang siap mengakui bahwa variasi dalam proses dan kinerja peralatan menyebabkan sejumlah besar cacat yang dialami oleh pelanggan akhir. Dalam Six Sigma, cacat didefinisikan sebagai segala sesuatu yang dapat menyebabkan ketidakpuasan pelanggan.
Untuk tujuan artikel ini, fokus penulis adalah pada korelasi antara keandalan peralatan dan cacat produk tersebut. Artikel ini juga akan mengeksplorasi beberapa akar penyebab umum dari keandalan peralatan yang buruk dan apa yang dapat dilakukan untuk mencegah atau menguranginya, sehingga mengarah pada penghapusan cacat.
Keandalan Peralatan dan Cacat Produk
Penulis Ron Moore menyarankan bahwa kesesuaian proses dapat ditingkatkan melalui keandalan peralatan, instrumentasi yang tepat, terkalibrasi, operasi yang disiplin, dan bahan baku yang berkualitas*. Keandalan peralatan memastikan bahwa subsistem dan komponen berfungsi sebagaimana dimaksud tanpa kegagalan selama periode yang diinginkan selama masa pakai desainnya.
Secara teoritis, cacat dapat dimasukkan ke dalam peralatan pada masing-masing dari enam fase utama dari siklus hidupnya:Desain, Pembelian, Penyimpanan, Instalasi/Pengoperasian, dan Pemeliharaan. Oleh karena itu, masuk akal jika Anda mengelola cacat yang menyebabkan kegagalan peralatan, maka Anda akan dapat secara langsung memengaruhi kualitas produk.
Akar Penyebab Umum dari Keandalan Peralatan yang Buruk
Akar penyebab adalah faktor mendasar yang ditemukan bertanggung jawab atas peristiwa atau kelas peristiwa tertentu yang terjadi, seperti kinerja peralatan yang buruk. Tujuan menghilangkan akar penyebab ini adalah untuk mencegah terulangnya kejadian tersebut di masa mendatang.
Seringkali, ini disalahartikan dengan intervensi manusia yang mengarah pada kegagalan, gejala kegagalan atau mekanisme fisik di mana kegagalan memanifestasikan dirinya. Sebaliknya, untuk benar-benar mencegah ketidakandalan di masa depan, Anda harus pergi ke sumber sebenarnya dari kegagalan yang dikenal sebagai penyebab laten.
Ini bersifat sistemik, dan sementara mereka menghasilkan penghargaan tertinggi dengan dicegah atau dikelola, mereka paling berisiko untuk tidak diterapkan. Hal ini disebabkan oleh fakta bahwa mereka pada umumnya mendalami organisasi dan menunjuk ke arah sistem manajemen yang telah mendarah daging dalam budaya perusahaan. Beberapa akar laten yang lebih umum** yang dapat dikutip untuk kegagalan peralatan prematur adalah:
-
Penerapan yang salah – Hal ini dapat disebabkan oleh pengoperasian peralatan di luar lingkup desain, praktik desain awal yang buruk, atau praktik pengadaan yang buruk.
-
Praktik pengoperasian – Hal ini dapat disebabkan oleh prosedur pengoperasian yang tidak memadai, kurangnya kepatuhan terhadap prosedur, atau sistem yang tidak memadai untuk tindak lanjut.
-
Praktik pemeliharaan – Hal ini disebabkan oleh prosedur pemeliharaan yang tidak memadai, tidak adanya kepatuhan terhadap prosedur, atau frekuensi tugas pemeliharaan yang tidak memadai.
-
Usia – Hal ini disebabkan oleh mekanisme keausan yang dipercepat oleh faktor lingkungan atau akhir masa pakai karena keausan normal.
-
Sistem manajemen – Hal ini karena kurangnya keterampilan atau pelatihan operator, keterlibatan karyawan yang buruk, pengenalan bahaya yang buruk, dan/atau bahaya yang diidentifikasi sebelumnya tidak ditindaklanjuti dan dihilangkan.
Setiap organisasi yang mencoba mendapatkan manfaat penuh dari pengurangan cacat dengan meningkatkan keandalan peralatan harus memiliki setidaknya empat sistem berikut.
Program RCA
Root Cause Analysis (RCA) adalah proses yang secara sistematis menggunakan salah satu atau kombinasi dari kelas metode pemecahan masalah yang bertujuan untuk mengidentifikasi akar penyebab masalah atau peristiwa.
Penatagunaan proses ini biasanya merupakan fungsi dari rekayasa keandalan. Seperti yang telah disebutkan sebelumnya, memiliki program RCA yang disiplin sangatlah penting, pertama-tama, untuk mengidentifikasi alasan di balik keandalan peralatan yang buruk dan, kedua, untuk menerapkan tindakan yang akan mencegah hal itu terjadi lagi.
Perusahaan A, produsen bahan kimia besar, memiliki lebih dari 1.150 pompa sentrifugal yang beroperasi. Waktu rata-rata antara kegagalan (MTBF) untuk pompa pada tahun 1995 diukur menjadi sekitar 0,8 tahun (9,6 bulan). RCA sistematis sebagai proses bisnis tidak dimulai di fasilitas sampai tahun 1998.
Sebelum itu, mereka melakukan analisis kegagalan dan melakukan analisis kesenjangan antara praktik pemasangan dan pemeliharaan mereka dan “terbaik di kelasnya.” Itu adalah langkah awal yang mereka butuhkan.
Sebuah proses RCA formal datang kemudian. Keputusan dibuat oleh departemen keandalan untuk melatih keahlian/perdagangan mereka dalam teknik di mana kode kegagalan akan ditetapkan untuk setiap kegagalan.
Data ini kemudian dicatat dalam sistem manajemen pemeliharaan terkomputerisasi (CMMS) dan database Analisis Pelaporan Kegagalan dan Sistem Tindakan Korektif (FRACAS) yang terpisah.
RCA dilakukan pada apa yang ditentukan sebagai mode kegagalan yang lebih dominan (seperti yang ditunjukkan oleh kode kegagalan). Tindakan kemudian diambil berdasarkan temuan dan hasil yang ditunjukkan pada Gambar 1 tercapai.
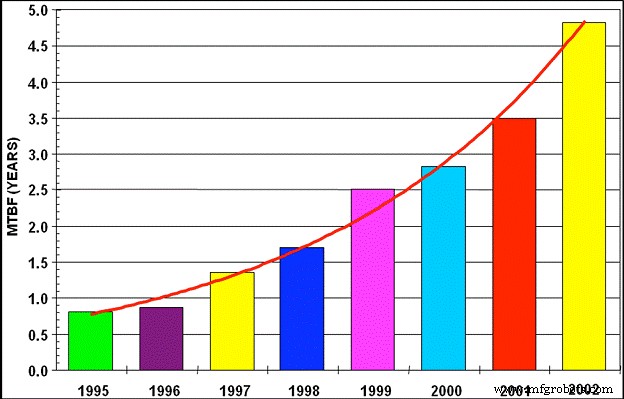
Gambar 1:Pompa MTBF untuk Tahun 1995 hingga 2002
Selama delapan tahun, MTBF untuk pompa ini meningkat 500 persen secara fenomenal. Hanya pengurangan kegagalan pompa yang menyumbang sekitar $5,5 juta per tahun pengurangan biaya pemeliharaan langsung pada akhir kumpulan data. Ada banyak inisiatif keandalan lain selain pompa yang berlangsung selama lima tahun terakhir periode data, tetapi pompa adalah yang pertama dan terbesar.
Dampak gabungan dari semua inisiatif keandalan (di mana pompa diperkirakan bertanggung jawab untuk 35 hingga 40 persen) adalah peningkatan pabrik sebesar 15 persen untuk pengeluaran modal yang pada dasarnya kecil dan peningkatan efektivitas peralatan keseluruhan (OEE) sekitar 4 persen (dari 94 persen menjadi 98,2 persen).
Pembangkit tersebut mampu melakukan debottleneck dan beroperasi pada tingkat yang ditunjukkan lebih tinggi karena stabilitas proses yang meningkat. Lebih dari tiga kegagalan pompa per hari, bahkan di mana ada suku cadang, banyak ketidakstabilan. Melemparkan beberapa kegagalan instrumen per hari dan setidaknya satu kegagalan kapal per minggu, dan orang tidak pernah tahu apa batas sebenarnya dari sebuah pabrik karena seseorang tidak akan pernah bisa 'berbaris' dan berlari.
Dampak dari pengurangan biaya dan peningkatan penjualan dari semua perbaikan membuat profitabilitas pabrik naik dari $12 juta per tahun di pasar yang terjual habis menjadi $43 juta per tahun dengan kapasitas hanya 60 persen menjadi $72 juta per tahun ketika terjual habis. tahun depan.
Praktisi Keandalan di Tempat
Life Cycle Engineering adalah pelopor Reliability Excellence (Rx), yang didefinisikan sebagai “filosofi bisnis, didorong melalui perubahan budaya yang berfokus pada keandalan peralatan dan kontrol proses sebagai dasar dari operasi manufaktur modern”.
Dalam pengalaman perusahaan, telah ditentukan bahwa keunggulan dicapai dengan menyelesaikan lima tingkat terpisah yang disebut sebagai model keunggulan yang ditunjukkan pada Gambar 2. Langkah keberlanjutan di atas model mencakup rekayasa keandalan sebagai salah satu komponen utamanya.
Apakah Anda memiliki teknisi keandalan di lokasi atau tidak, ada beberapa aktivitas utama dalam peran tersebut yang perlu dilakukan untuk memastikan bahwa hasil yang diinginkan dapat dipertahankan – hasil yang diinginkan dalam hal ini adalah peningkatan keandalan peralatan yang mengarah pada penurunan cacat.
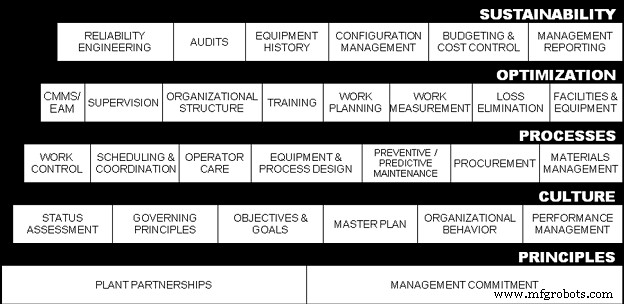
Gambar 2:Model Keunggulan Keandalan
Praktisi keandalan di lokasi Anda ditugaskan untuk memantau peralatan dan proses untuk mengidentifikasi peluang untuk peningkatan berkelanjutan. Sebagai manajer risiko untuk bisnis Anda, mereka harus secara proaktif menentukan cara terbaik untuk menangani risiko melalui penggunaan teknik pemeliharaan preventif/prediktif dan rencana risiko.
Pemeliharaan Berpusat Keandalan atau beberapa variasinya disarankan untuk setidaknya peralatan paling penting yang Anda miliki di lokasi.
Untuk keseimbangan pabrik, berbagai strategi pengoptimalan lain yang memungkinkan hasil terbaik dapat digunakan. Namun, disarankan agar seseorang menyadari keterbatasan strategi tersebut untuk secara sadar menerima risiko apa pun yang terkait dengan penggunaannya.
Proses Bisnis yang Mendukung Keandalan dan Kualitas Produk
Landasan dari setiap inisiatif keandalan dan kualitas harus merupakan proses yang stabil. Harus jelas secara mendasar bahwa tidak ada Total Productive Maintenance (TPM), lean manufacturing, atau inisiatif Six Sigma yang akan mencapai potensi penuhnya tanpa proses untuk mempertahankan peningkatan.
Ambil contoh, kasus pabrik peleburan aluminium berusia 50 tahun, yang melakukan tugas besar untuk merekayasa ulang proses kerja dan peralatan mereka.
Pada tahun 2002, tepat sebelum upaya Reliability Excellence mereka terfokus, pabrik memiliki total biaya pemeliharaan lebih dari $35 juta. Ini juga memiliki rasio lebih dari $137 dalam biaya perawatan untuk setiap metrik ton aluminium yang diproduksi (50 persen lebih tinggi dari rata-rata global pada saat itu).
Perusahaan memulai standarisasi proses kerja, mengembangkan sejarah peralatan dan memanfaatkan alat lean manufacturing untuk pemecahan masalah. Pemeliharaan dalam kemitraan dengan operasi, memutuskan untuk menggunakan metrik TPM OEE untuk mengukur kemajuan mereka.
Kinerja puncak untuk fungsi pabrik tertentu ditentukan, termasuk tingkat sisa. Pada tahun 2004, setelah menerapkan proses berbasis keandalan yang baru, peningkatan sebesar $2,4 juta dikaitkan langsung dengan perolehan OEE tersebut.
Pemantauan Hasil
Pepatah lama yang dikaitkan dengan kualitas profesional Joseph Juran menyatakan, "Jika Anda tidak mengukurnya, Anda tidak mengelolanya." Itu masih terdengar benar hari ini. Untuk memastikan bahwa Anda berada di jalur yang benar dan mencapai hasil yang diinginkan tanpa cacat, Anda harus memiliki metrik yang sesuai. Metrik pertama yang harus dipertimbangkan adalah OEE.
Ukuran ini menunjukkan seberapa efektif aset organisasi digunakan untuk mencapai tujuan bisnis. Ini mengintegrasikan tiga ukuran lain:ketersediaan peralatan, tingkat kinerja, dan kualitas produk.
Hal yang menarik tentang penggunaan OEE sebagai metrik adalah bahwa dari diskusi ini, telah ditetapkan bahwa dengan meningkatkan keandalan peralatan, ukuran ketersediaan dan ukuran kualitas juga dapat meningkat.
Kemudian akan ada efek ganda pada OEE karena peningkatan keandalan. Metrik lain yang akan berguna untuk dilacak adalah MTBF dan tingkat skrap pada peralatan tertentu yang telah ditargetkan untuk perbaikan. Dengan demikian, korelasi langsung antara kedua ukuran dapat diperiksa dan dianalisis lebih lanjut.
Seringkali, profesional keandalan mengartikulasikan hubungan antara keandalan peralatan dan hasil akhir yang penting bagi sebagian besar organisasi. Seseorang akan dengan cepat menggembar-gemborkan hubungannya dengan hasil produksi dan keselamatan, tetapi kualitas atau pemborosan proses terkadang tertinggal.
Seperti yang disarankan dalam artikel ini, ada hubungan yang jelas antara keandalan peralatan dan cacat atau pemborosan yang dibuat dalam proses manufaktur. Untuk mengelola variasi dalam proses manufaktur Anda, Anda perlu mengelola variasi dalam kinerja peralatan Anda dengan mengambil empat langkah kunci menuju konsistensi dalam produk Anda.
Pertama, Anda memerlukan program RCA dan keandalan yang kuat dan disiplin untuk mengidentifikasi sumber keandalan peralatan yang buruk.
Kedua, Anda juga perlu memiliki personel keandalan yang berdedikasi untuk tugas-tugas mempertahankan peningkatan keandalan Anda.
Ketiga, Anda perlu memahami proses bisnis Anda dan memastikan bahwa proses tersebut mendukung arah Anda. Terakhir, Anda perlu mengukur kemajuan Anda dengan metrik yang sesuai.
Referensi
* Moore, R. Memilih Alat Peningkatan Manufaktur yang Tepat , Boston, Ma, &London, Elsevier Butterworth-Heinemann Books, 2007.
** Mobley, R. K. Analisis Kegagalan Akar Penyebab , Elsevier Butterworth-Heinemann, 1999.
Tentang penulis:
Carl March memiliki banyak pengalaman di bidang pemeliharaan, rekayasa keandalan, pemodelan dan desain sistem. Carl memegang gelar sarjana di bidang teknik mesin dan gelar sarjana di bidang teknik sistem otomotif. Sebagai ahli materi pelajaran keandalan di Life Cycle Engineering, semangat dan fokusnya adalah dalam transfer pengetahuan di RCM, TPM, analisis akar masalah, dan keunggulan keandalan kepada klien di seluruh dunia yang ingin mencapai perbedaan manufaktur. Carl telah mencapai tingkat pengakuan profesional yang signifikan sebagai Certified Reliability Engineer (CRE) oleh American Society for Quality dan sebagai Certified Maintenance and Reliability Professional (CMRP) oleh Society of Maintenance and Reliability Professionals. Anda dapat menghubungi Carl di [email protected]. Untuk informasi lebih lanjut tentang LCE, kunjungi www.LCE.com atau hubungi 843-744-7110.