Analisis bantalan:Pecahkan masalah, bukan kegagalannya
Tujuan artikel ini adalah untuk mengembangkan pola pikir dalam mendeteksi dan memperbaiki masalah dan bukan hanya mendeteksi kegagalan. Kami sering melihat contoh bantalan yang benar-benar rusak dan, di samping, data spektral dan getaran yang mendeteksi kegagalan. Untuk tujuan ini, harus ada pendekatan multi-tahap:program pemantauan getaran harus digunakan untuk mendeteksi masalah sedini mungkin, dan departemen pemeliharaan harus bertindak atas hal itu (dan itu mungkin tidak untuk mengubah bantalan; mungkin hanya menjadi masalah pelumasan). Jika bantalan diganti, penting untuk menggantinya pada waktu yang tepat. Itulah kuncinya. Jika diubah terlalu dini, orang mengatakan sistemnya cacat. Jika terlambat diubah, itu dapat merusak komponen lain, dan bukti yang dapat memberi tahu kita apa masalahnya mungkin akan dihancurkan. Tujuannya adalah untuk proaktif dan tidak reaktif.
Sistem pendukung keputusan SKF Bearing Inspector ditujukan untuk menawarkan peningkatan kecepatan, konsistensi, dan kualitas yang lebih tinggi dalam proses pengambilan keputusan bearing. Ini akan membantu mencegah kerusakan atau kegagalan bantalan berulang. Seperti halnya sistem komputer berbasis pengetahuan lainnya, SKF Bearing Inspector mengumpulkan semua informasi dan pengalaman relevan yang tersedia tentang kerusakan bantalan gelinding – mulai dari prinsip dasar hingga hasil rekayasa praktis. Hubungan sebab akibat antara gejala dan kemungkinan alasan tidak ada dalam kenyataan dan dapat dengan mudah mengarah pada kesimpulan yang salah. Ini hanya karena alasan (misalnya, pemasangan bantalan yang salah) mengakibatkan gejala kerusakan (misalnya, tanda-tanda resah) dan bukan sebaliknya. Sebuah pemodelan hubungan dari penyebab ke gejala di mana ketidakpastian melekat pada "kemungkinan keadaan kegagalan" lebih cocok dengan fenomena fisik yang terjadi selama masa pakai bantalan. Dengan bantuan teknik kecerdasan komputasi mutakhir, pendekatan ini telah diikuti untuk pengembangan program.
Artikel ini akan mengikuti standar ISO 15243:2004 sebagai referensi.
Masalahnya
Alat pemantau kondisi sering digunakan sebagai cara untuk mendeteksi cacat atau pola kegagalan pada mesin yang berputar. Kami sering menggunakan alat pemantauan kondisi untuk menjadi prediktif dalam perencanaan pemeliharaan kami untuk selanjutnya menjadi reaktif dalam apa yang sebenarnya kami lakukan. Sebelum kita dapat mempelajari bagaimana kita dapat menggunakan alat untuk mencegah kegagalan, kita perlu memahami beberapa kata kunci ini dan melihat apa yang perlu kita lakukan untuk menggunakan data yang dikumpulkan. Juga harus ada strategi untuk menentukan apa yang harus dikumpulkan dan bagaimana mengubah data menjadi informasi yang efektif. Ambil kasus bantalan (gambar di bawah):Apakah kami melakukan pekerjaan dengan baik dalam mendeteksi masalah atau kami hanya mendeteksi kegagalan? Bisa dibilang kami mencegah kegagalan mesin yang fatal, tetapi apa penyebabnya dan dapatkah kami mencegahnya terjadi lagi?
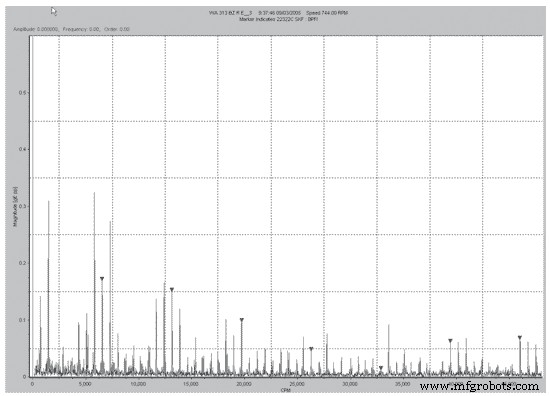
Gambar 1. Spektrum Bantalan Terbungkus
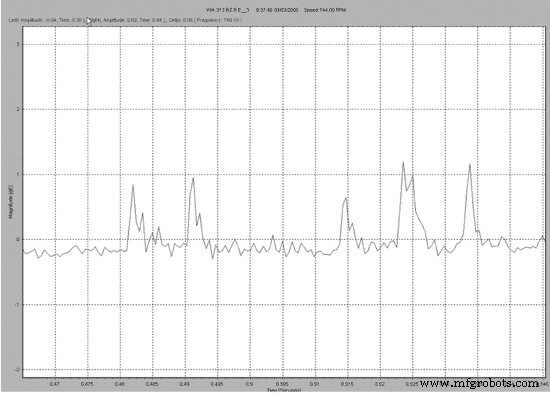
Gambar 2. Bentuk Gelombang Bantalan
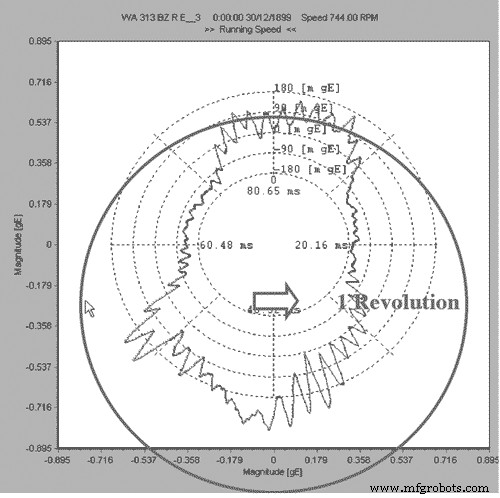
Gambar 3. Analisis Waktu Siklus Bantalan
Bantalan ini telah gagal beberapa kali, tetapi yang dilakukan hanyalah mengganti bantalan, yang merupakan pekerjaan yang sangat mahal dan memakan waktu. Dengan mengambil blok data waktu, dimungkinkan untuk menggabungkan ujung-ujungnya untuk menampilkan data dalam plot profil. Blok waktu ini mewakili satu putaran bantalan. Data tersebut kemudian dirata-ratakan waktu sinkron menggunakan pemicu virtual yang ditetapkan dengan panjang waktu 1 rpm. Data ini sekarang dengan jelas menunjukkan bahwa ada dua zona beban di bantalan ini, dan itu pada akhirnya akan menyebabkan stres di inner race dan sangkar, dan kegagalan akan terjadi. Jurnal diperiksa dan ternyata berbentuk oval; itu kemudian dikerjakan dan bantalannya dipasang dengan benar. Bantalan telah beroperasi sejak dan tidak menunjukkan tanda-tanda masalah.
Analisis kegagalan akar penyebab dan pemeliharaan proaktif berhasil. Penting untuk menggunakan teknik ini sebelum kegagalan fungsional terjadi. Kuncinya adalah memecahkan masalah, bukan kegagalannya.
Pelumasan
Ketika pelumasan bantalan mulai gagal, umumnya menyebabkan peningkatan getaran, kebisingan atau emisi akustik. Rezim manajemen pelumasan sering kali didasarkan pada mendengarkan bantalan. Ini bisa berhasil tetapi, sejauh ini, cara terbaik adalah membuat tren data terhadap unit teknik. Tren berikut menunjukkan apa yang terjadi pada bantalan saat dilumasi.
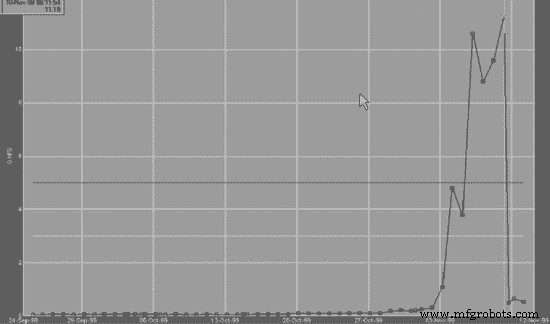
Gambar 4.
Dapat dilihat bahwa itu tampaknya memecahkan masalah, tetapi tingkat getaran tidak pernah kembali ke tingkat sebelum masalah. Peningkatan level setelah pelumasan disebabkan oleh partikel kecil dari kotoran yang masih ada di dalam gemuk. Data bentuk gelombang waktu diambil selama tindakan mengoles bantalan. Jelas terlihat bahwa masalahnya telah disembunyikan dengan mengoles.
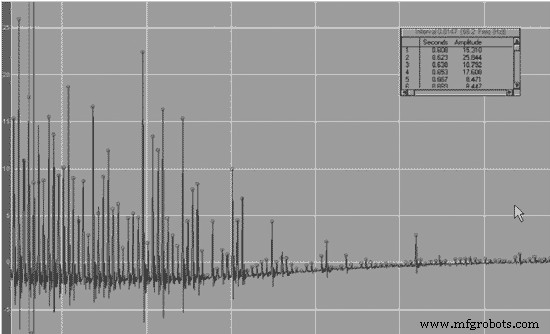
Gambar 5.
Sistem pendukung keputusan untuk analisis mode kegagalan bantalan
Memperoleh wawasan dan informasi dari kerusakan dan kegagalan bantalan gelinding adalah kepentingan strategis bagi SKF dan pelanggannya. Pengetahuan yang dikumpulkan tentang kerusakan bantalan dapat diakses oleh para insinyur SKF sebagai sistem pendukung keputusan berkemampuan Web yang disebut SKF Bearing Inspector. Dikombinasikan dengan pengetahuan tentang bagaimana pola cacat bantalan muncul dalam sistem pemantauan kondisi, analisis akar penyebab kegagalan dapat sangat ditingkatkan.
Sistem pendukung keputusan, SKF Bearing Inspector, ditujukan untuk menawarkan peningkatan kecepatan, konsistensi, dan kualitas yang lebih tinggi dalam proses pengambilan keputusan bearing. Ini akan membantu mencegah kerusakan atau kegagalan bantalan agar tidak terulang kembali. Seperti halnya sistem komputer berbasis pengetahuan lainnya, SKF Bearing Inspector mengumpulkan semua informasi dan pengalaman relevan yang tersedia tentang kerusakan bantalan gelinding – mulai dari prinsip dasar hingga hasil rekayasa praktis.
Sistem berbasis pengetahuan saat ini telah mendapat manfaat dari pengalaman sistem pakar yang dikembangkan pada 1980-an, meskipun ini mengalami kekurangan besar dalam aspek kapasitas penalaran dan kekuatan komputer. Sistem ini sering terstruktur sebagai pohon keputusan yang mengarah dari gejala ke kemungkinan penyebab. Hubungan sebab akibat antara gejala dan kemungkinan alasan tidak ada dalam kenyataan dan dapat dengan mudah mengarah pada kesimpulan yang salah. Ini hanya karena alasan (misalnya, pemasangan bantalan yang salah) mengakibatkan gejala kerusakan (misalnya, tanda-tanda resah), dan bukan sebaliknya. Sebuah pemodelan hubungan dari penyebab ke gejala - di mana ketidakpastian melekat pada "kemungkinan keadaan kegagalan" - lebih cocok dengan fenomena fisik yang terjadi selama masa pakai bantalan. Dengan bantuan teknik kecerdasan komputasi mutakhir, pendekatan ini telah diikuti untuk pengembangan program.
Sistem pengetahuan
Dalam sistem pengetahuan, umumnya membedakan antara pemodelan pengetahuan dengan representasi pengetahuan tertentu dan prinsip penalaran, untuk memperoleh kapasitas pemecahan masalah. Mengenai representasi pengetahuan, ada beberapa bentuk, seperti:
Kasus: Banyak pengalaman kegagalan bantalan dapat ditemukan dalam contoh kasus. Sayangnya, banyak kasus praktis tidak didokumentasikan dengan baik, dan tidak ada keseragaman mengenai parameter yang didokumentasikan atau kesimpulan mode kegagalan. Namun, contoh kasus dapat digunakan untuk memodelkan atau memverifikasi representasi pengetahuan lainnya.
Aturan: Dimungkinkan untuk menggeneralisasi aturan jika-maka antara gejala yang diamati dan kemungkinan penyebab. Namun, ini tidak tepat karena penyebab yang berbeda dapat memiliki efek serupa yang muncul sebagai gejala yang serupa.
Jaringan saraf tiruan: Hubungan matematis antara gejala dan penyebab dapat diturunkan dengan menggunakan contoh kasus kegagalan. Namun, jumlah kasus diskriminatif tidak cukup untuk melakukan hal ini. Selain itu, pengguna sistem memerlukan penjelasan tambahan daripada hubungan jaringan saraf tiruan "kotak hitam" yang tidak membawa penjelasan seperti itu.
Jaringan probabilitas: Dimungkinkan untuk memperoleh jaringan visual, di mana node dihubungkan oleh hubungan sebab akibat, berdasarkan teori dan pengalaman kegagalan bantalan. Selanjutnya, probabilitas ditetapkan untuk menunjukkan kelemahan atau kekuatan hubungan tersebut. Dengan memperkenalkan kausalitas yang benar dari kondisi ke pengamatan, representasi pengetahuan ini paling sesuai dengan masalah diagnosis kegagalan bantalan. Analisis kerusakan dan kegagalan bantalan pada prinsipnya merupakan tugas diagnostik. Bayangkan seorang pasien mengunjungi dokternya dengan keluhan tertentu. Dokter pertama-tama menanyai pasien tentang parameter tubuh dan gaya hidup tertentu seperti berat badan, merokok, dll. (kondisi). Berdasarkan informasi tersebut, dokter membuat hipotesis tentang kemungkinan penyakit (failure mode). Dokter memverifikasi atau menolak hipotesis ini melalui pertanyaan dan pemeriksaan lebih lanjut terhadap pasien (gejala). Proses analisis kerusakan atau kegagalan mirip dengan pendekatan dokter. Dalam diagnosis yang benar, ada dua langkah penalaran:
- Pembuatan hipotesis adalah di mana kemungkinan hipotesis kegagalan dihasilkan berdasarkan data. Misalnya, dokter mulai mengajukan pertanyaan untuk mendapatkan ide (hipotesis) tentang apa yang mungkin salah.
- Memverifikasi atau menolak hipotesis. Satu per satu, hipotesis yang dihasilkan diselidiki dan diverifikasi atau ditolak. Misalnya, dokter mulai menyelidiki penyakit yang paling mungkin dengan melakukan tes medis tertentu (tekanan darah, detak jantung, dll.).
Dengan jaringan probabilistik, penalaran dua langkah diimplementasikan dengan perhitungan probabilitas maju dan mundur.
Selengkapnya tentang jaringan probabilistik
Jaringan probabilistik adalah jaringan visual di mana node dihubungkan oleh hubungan sebab akibat, dan perhitungan probabilitas diterapkan. Jaringan untuk analisis kegagalan bantalan memiliki empat kategori simpul:kondisi, mekanisme internal, mode kegagalan dan gejala yang diamati. Kondisi mewakili kondisi dari dan di mana bantalan beroperasi. Contohnya adalah kecepatan, jenis bantalan, beban, suhu, detail pemasangan, faktor lingkungan, dll. Mekanisme internal mewakili fenomena fisik yang terjadi selama operasi, seperti pelumasan, gangguan film, kontak geser, dll. Mode kegagalan mewakili jenis kegagalan, seperti kelelahan yang dimulai di bawah permukaan dan korosi resah.
Pada Tabel 1, berbagai mode kegagalan terdaftar. Gejala yang diamati mewakili fenomena yang dapat diamati di dalam dan di luar bantalan, termasuk perubahan warna, pengelupasan, karat, dll. Sekitar 150 node dihubungkan oleh hubungan sebab akibat antara kondisi aplikasi bantalan, mekanisme tersembunyi, mode kegagalan fisik, dan gejala yang diamati. Dalam pemodelan jaringan, berbagai sumber informasi digunakan. Selain mendefinisikan node, hubungan sebab akibat dan probabilitas, teks penjelasan (untuk setiap node) termasuk contoh dan gambar dikembangkan. Secara total, sekitar 250 gambar telah dimasukkan ke dalam sistem.
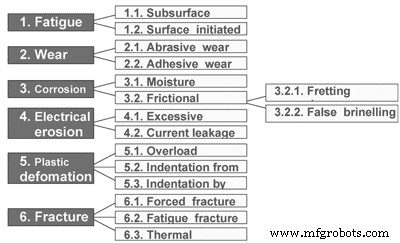
Gambar 6. ISO 15243:2004
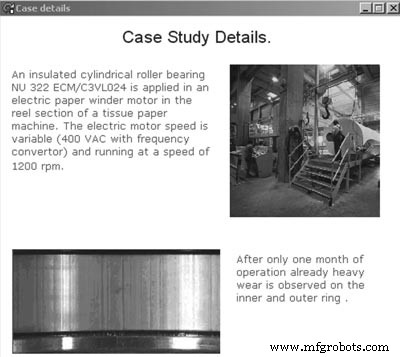
Gambar 7.
Studi kasus dari Bearing Inspector
Bearing Inspector berisi beberapa kasus kerusakan bantalan umum yang terletak di bawah "Kasus Tipikal". Ini dapat digunakan sebagai materi pelatihan untuk menunjukkan bagaimana Pemeriksa Bantalan mendukung analisis penyelidikan kerusakan bantalan. Salah satu contohnya adalah motor listrik di pabrik kertas. Dalam hal ini, bantalan rol silinder berinsulasi listrik NU 322 ECM/C3VL024 digunakan dalam motor listrik penggulung kertas di bagian gulungan mesin kertas tisu. Kecepatan motor listrik bervariasi (400 VAC dengan konverter frekuensi) dan berjalan antara 1.000 dan 1.500 menit-1. Namun, setelah hanya satu bulan beroperasi, keausan berat terlihat pada cincin bagian dalam dan luar. Memuat kasus contoh di SKF Bearing Inspector menetapkan semua kondisi aplikasi yang diketahui (Langkah 1).
Hipotesis pertama dari kemungkinan mode kegagalan dihitung berdasarkan kondisi aplikasi ini. Pada titik analisis ini, Bearing Inspector memberikan kemungkinan besar terjadinya brineling palsu, keausan perekat, dan kebocoran arus. Pada pandangan pertama, kebocoran arus dan brineling palsu tampaknya tidak mungkin karena mesin menggunakan bantalan berinsulasi dan semua mesin ditopang dengan benar dengan bantalan karet. Pengguna kemudian harus melakukan langkah kedua dari analisis dengan memeriksa bantalan pada gejala kegagalan. Mengklik "inspeksi" menghasilkan daftar gejala kerusakan yang paling relevan dengan mode kegagalan yang dipilih.
Bantalan pertama diperiksa untuk brineling palsu. Karena tidak ditemukan lekukan dangkal yang dapat memverifikasi brineling palsu, mode kegagalan ini ditolak. Analisis dilanjutkan dengan pemeriksaan gejala keausan perekat. Tidak ada gejala yang berhubungan dengan keausan perekat yang ditemukan. Akhirnya, dengan memeriksa gejala kebocoran arus listrik, keberadaan pitting kecil ditemukan setelah perbesaran permukaan raceway. Ini memverifikasi mode kegagalan kebocoran saat ini. Selanjutnya, pelanggan memang menemukan masalah pembumian pada konstruksi penggulung yang menyebabkan kebocoran arus listrik.
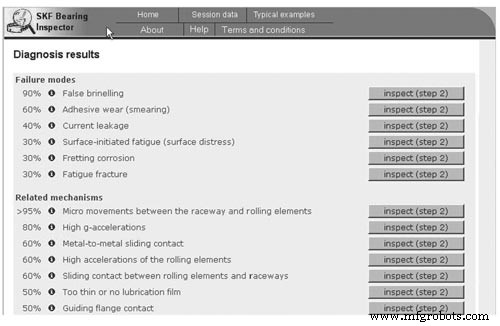
Gambar 8. Contoh Langkah 1:Kondisi aplikasi diisi dengan memuat data penggulung motor listrik antara lain jenis bantalan, lapisan, kecepatan, dll. Informasi rinci dan contoh disediakan di bawah tombol informasi.
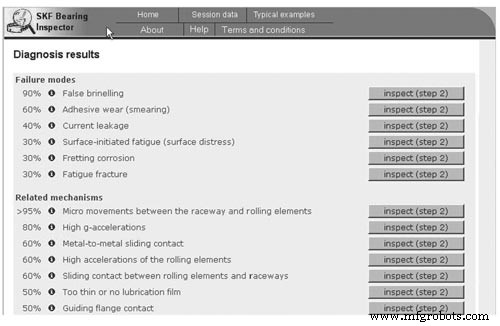
Gambar 9. Contoh Langkah 2:Bearing Inspector memberikan diagnosis awal berdasarkan informasi sejauh ini; faktor kepercayaan disertakan.
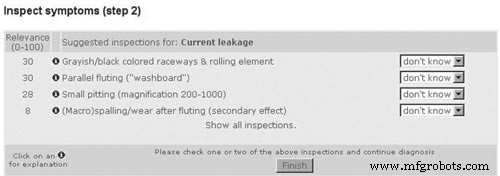
Gambar 10. Contoh Langkah 3:Pemeriksaan gejala untuk mode kegagalan kebocoran saat ini. Setelah inspeksi dan pembesaran permukaan landasan pacu, lubang kecil dipastikan. Beberapa contoh disediakan di bawah tombol informasi.
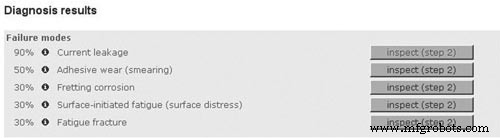
Gambar 11. Contoh diagnosis akhir:Hasil didasarkan pada kondisi aplikasi yang disediakan (Langkah 1) dan inspeksi sistem bantalan (Langkah 2). mode kegagalan yang paling relevan dan mekanisme internal terkait dicantumkan. Hasilnya dapat dicetak sebagai dokumen Microsoft Word atau laporan HTML.
Alih-alih menyelidiki semua pengamatan yang mungkin dan kondisi yang tidak terisi, yang paling relevan disarankan, tergantung pada hipotesis kegagalan (atau mekanisme internal) yang perlu diselidiki. Dengan kata lain, ini adalah kondisi aplikasi atau pengamatan yang memiliki efek paling diskriminatif pada hipotesis kegagalan. Efek pembeda ditentukan oleh ukuran matematis.
Untuk semua kemungkinan kondisi atau pengamatan yang tidak diisi, ukuran ini diskalakan antara 0 dan 100. Sebuah contoh diberikan dalam ilustrasi. Akhirnya, dengan menyelidiki kondisi dan pengamatan aplikasi, kemungkinan hipotesis kegagalan dan mekanisme internal ditentukan dan diberi peringkat. Ini kemudian membentuk kesimpulan dari analisis kerusakan bantalan. Sistem ini lebih diperluas dengan berbagai fungsi yang dapat membantu pengguna. File sederhana dengan instruksi pengguna disediakan untuk memulai. Kontrol data sesi tersedia untuk penyimpanan dan pengambilan data sesi. Juga, dalam file bertanda "Contoh Tipikal", pengguna dapat dipandu melalui aplikasi program. Untuk kenyamanan, laporan ekstensif dapat dibuat dalam format Microsoft Word atau HTML, termasuk kondisi yang relevan, pengamatan, dan probabilitas mode kegagalan.
Kesimpulan
Bearing Inspector memenuhi kebutuhan akan proses pengambilan keputusan yang cepat, lebih konsisten, dan berkualitas tinggi untuk investigasi kerusakan dan kegagalan bearing. Sistem berkemampuan Web ini tersedia bagi para insinyur SKF untuk mendukung pelanggan dalam penyelidikan kerusakan dan kegagalan bantalan. Ini dapat membantu untuk menentukan bagaimana bantalan gagal dan, oleh karena itu, bagaimana memastikan bahwa kegagalan yang sama tidak dapat terjadi lagi. Pola kegagalan ini kemudian harus digunakan untuk menentukan cara mengonfigurasi program pemantauan kondisi berbasis getaran.