Kegagalan analisa
Analisis Kegagalan
Kegagalan komponen dan rakitan peralatan, atau struktur dalam industri dapat menyebabkan hilangnya nyawa, penghentian tidak terjadwal, peningkatan biaya pemeliharaan dan perbaikan, dan perselisihan litigasi yang merusak.
Untuk mencegah terulangnya kembali masalah yang disebabkan oleh kegagalan, penting untuk melakukan penyelidikan di setiap kegagalan. Pelaksanaan investigasi untuk suatu kegagalan dikenal sebagai analisis kegagalan.
Analisis kegagalan adalah proses pengumpulan dan analisis data dan dilakukan untuk menentukan penyebab atau faktor yang menyebabkan hilangnya fungsionalitas yang tidak diinginkan atau kegagalan komponen peralatan dan rakitan, atau struktur. Ini adalah proses bertingkat yang mencakup penyelidikan fisik. Lingkup normal dari analisis kegagalan adalah menemukan mekanisme kegagalan dan penyebab kegagalan yang paling mungkin. Istilah mekanisme kegagalan biasanya digambarkan sebagai proses metalurgi, kimia, mekanik, atau tribologi yang mengarah ke mode kegagalan tertentu.
Kegagalan komponen dan rakitan peralatan, atau struktur terjadi sebagai akibat dari semacam kesalahan yang menyebabkan mata rantai yang lemah dalam rantai proses rekayasa, desain, manufaktur, dan operasi yang berkelanjutan. Penyebab kegagalan dapat salah satu atau lebih dari berikut ini.
- Kesalahan dalam desain
- Cacat pada bahan
- Kekurangan selama pemrosesan dan pembuatan
- Cacat dalam perakitan atau pemasangan
- Kondisi layanan di luar desain atau tidak diinginkan
- Kekurangan dalam pemeliharaan (kelalaian dan prosedur, dll.)
- Pengoperasian yang salah
Langkah-langkah utama saat melakukan analisis kegagalan diberikan pada Gambar 1.
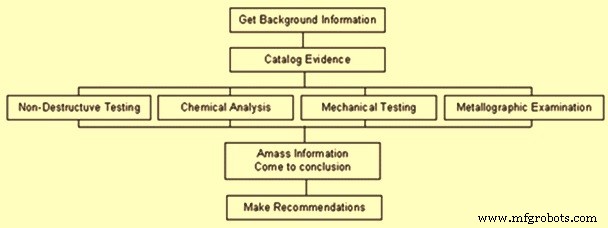
Gbr 1 Langkah-langkah utama dalam analisis kegagalan
Prinsip utama dari analisis kegagalan adalah untuk melestarikan bukti dan informasi yang diperlukan dari bagian subjek atau perakitan dalam kondisi yang diterima dan hal yang sama ditangkap sebelum sesuatu dilakukan untuk mengubah kondisinya. Selanjutnya selama analisis kegagalan perlu dilakukan pengujian dengan urutan yang tidak terlalu merusak hingga yang lebih merusak.
Analisis kegagalan dimulai dengan mengumpulkan informasi mengenai sejarah komponen yang terlibat dalam kegagalan, seperti (i) proses yang terlibat, (ii) aplikasi, (iii) jenis bahan, spesifikasinya, bentuk, dimensi, dan teknik pemrosesan, (iv) parameter desain, (v) kondisi layanan, (vi) riwayat perawatan, (vii) urutan kejadian sebelum kegagalan, (viii) frekuensi kegagalan dan apakah itu bersifat lokal, dll.
Inspeksi lokasi kegagalan merupakan langkah yang sangat penting yang membantu dalam analisis kegagalan. Pemeriksaan menyeluruh terhadap kondisi komponen yang gagal di lokasi kegagalan dapat memberikan banyak informasi. Selama inspeksi lokasi, perlu untuk memperhatikan fitur-fitur seperti lokasi retakan, karakteristik fraktur, perforasi, endapan, penipisan dinding, kendur, dan potongan yang terlepas dll. Juga, jika memungkinkan, perlu untuk memperoleh informasi sebanyak mungkin dari saksi mata tentang kondisi abnormal sebelum kegagalan. Dalam beberapa kasus, inspeksi visual dari komponen yang gagal dapat mengungkapkan informasi yang tidak dapat diperoleh dengan cara lain.
Selama inspeksi visual, penting untuk memotret mesin dan sekitarnya, bagian yang gagal dan bagian yang berpasangan. Dokumentasi fotografi dari komponen yang gagal selalu diperlukan untuk referensi di masa mendatang dan pemeriksaan lebih lanjut setelah meninggalkan lokasi. Penting untuk memotret semua fitur dari komponen yang gagal.
Pendefinisian masalah yang jelas merupakan bagian penting dari analisis kegagalan. Kedalaman informasi yang diperoleh, inspeksi lokasi, serta keterampilan dan penilaian orang yang melakukan analisis kegagalan membantu dalam mendefinisikan masalah dengan jelas. Misalnya, masalah dapat didefinisikan sebagai metalurgi, mekanik atau lingkungan atau kombinasi dari dua atau lebih dari mereka. Selanjutnya melalui diskusi dengan personel terkait di lokasi dan melalui inspeksi visual, orang yang melakukan analisis kegagalan dapat mempersempit berbagai kemungkinan. Selain itu, kegagalan mungkin menyerupai kasus kegagalan sebelumnya.
Berdasarkan kemungkinan penyebab kegagalan sesuai dengan masalah yang ditentukan selama inspeksi lokasi, program eksperimental dikembangkan untuk menentukan penyebab kegagalan. Sifat dan jumlah eksperimen yang dipilih harus sedemikian rupa sehingga mengarah pada identifikasi penyebab kegagalan. Sampel yang diperlukan untuk melakukan eksperimen yang dipilih harus diambil dengan hati-hati sedemikian rupa sehingga mewakili sebanyak mungkin semua fitur dari komponen yang gagal. Deposit atau potongan yang terlepas dari komponen dapat memberikan informasi yang berharga. Bila memungkinkan, sampel yang diambil dari bagian suara, serta sampel yang tidak pernah digunakan dalam layanan, juga harus dikumpulkan untuk tujuan perbandingan.
Alat investigasi yang digunakan dalam studi analisis kegagalan biasanya terdiri dari dua jenis yaitu (i) alat yang dapat digunakan di lokasi dan (ii) alat laboratorium.
Verifikasi material sehubungan dengan spesifikasi merupakan komponen penting dari analisis kegagalan. Analisis kimia dan analisis struktur makro serta mikro dilakukan untuk tujuan ini. Juga pengujian mekanis dilakukan jika bahan yang cukup tersedia untuk mengetahui kekuatan tarik, ketangguhan impak dll, untuk mengevaluasi sifat-sifat komponen yang gagal. Dalam banyak kasus, baik uji kekerasan permukaan maupun uji kekerasan mikro dilakukan untuk mengevaluasi kekuatan mekanik. Pengujian ini dilakukan pada komponen yang gagal untuk mengetahui kesesuaian hasil dengan spesifikasi
Analisis tegangan, mekanika patahan, dan analisis kegagalan korosi adalah kegiatan yang sangat berharga dalam penyelidikan analisis kegagalan. Analisis ini memberikan informasi kepada orang yang menyelidiki kegagalan apakah bahan yang digunakan telah menjadi pilihan yang tepat untuk memenuhi persyaratan penerapannya.
Dari pengetahuan tentang kondisi pelayanan seperti beban atau tekanan yang diterapkan, dan geometri dan ukuran komponen, adalah mungkin untuk menghitung tegangan utama yang terjadi pada bagian tersebut. Perbandingan tegangan utama maksimum dengan kekuatan material yang digunakan dalam aplikasi memberikan informasi penting kepada orang yang menyelidiki kegagalan tentang kesesuaian material untuk aplikasi dan apakah parameter desain diikuti secara ketat selama servis.
Analisis menggunakan prinsip-prinsip mekanika rekahan memberikan informasi yang berharga kepada orang yang menyelidiki kegagalan tentang tegangan yang timbul pada komponen yang gagal pada saat patah dalam kaitannya dengan tegangan desain, khususnya dalam kasus perambatan retak dengan mekanisme getas.
Dalam kasus kegagalan karena kelelahan, penting untuk menentukan jumlah siklus sebelum fraktur dengan mekanisme kelelahan. Metode yang didasarkan pada pengukuran jarak garis-garis lelah biasanya mudah dilakukan asalkan garis-garis tersebut terlihat jelas pada permukaan rekahan.
Pemeriksaan yang cermat dan menyeluruh dari struktur makro (perbesaran biasa 10) dan struktur mikro dari material yang terlibat dalam kegagalan dapat memberikan petunjuk penting. Jika memungkinkan, fitur struktural sampel yang dikeluarkan dari komponen yang gagal dengan perwakilan sampel yang dikeluarkan dari bagian suara, serta sampel yang tidak pernah digunakan dalam layanan harus dibandingkan. Anda juga perlu mengacu pada rekomendasi spesifik apa pun dari produsen peralatan terkait penggunaan material.
Pemeriksaan struktur makro dapat memberikan informasi tentang jalur rekahan dan lokasi asalnya, misalnya permukaan dalam atau permukaan luar.
Pemilihan teknik yang tepat untuk pemeriksaan struktur mikro tergantung pada jenis informasi yang dibutuhkan. Namun, mikroskop optik biasanya digunakan untuk memulai untuk mengetahui keseluruhan fitur struktural mikro seperti ukuran dan bentuk butir, endapan sekunder dan distribusinya, serta retakan mikro dan lokasinya. Ukuran butir yang luar biasa besar merupakan indikasi bahwa bahan tersebut terkena suhu yang terlalu tinggi. Bentuk butir dan bentuk kembar annealing memberikan informasi tentang jumlah pengerjaan dingin. Pemanjangan butir menunjukkan bahwa bahan yang dingin bekerja berat. Batas kembar yang bengkok menunjukkan bahwa material mengalami deformasi plastis. Garis slip halus di dalam butiran juga menunjukkan deformasi plastis material. Jika endapan sekunder terlihat pada struktur mikro maka sifat dan morfologinya perlu diperiksa.
Selama pemeriksaan fitur struktur mikro perlu diperhatikan adanya retakan mikro. Sebagai contoh, retak batas butir dapat diakibatkan oleh deformasi rangkak atau penggetasan batas butir oleh endapan fase sekunder.
Meskipun mungkin untuk mendapatkan banyak informasi tentang karakteristik fraktur dengan pemeriksaan visual, namun pemeriksaan struktur mikro permukaan fraktur menggunakan mikroskop elektron pemindaian diperlukan untuk mengetahui mekanisme yang bertanggung jawab untuk fraktur. Fraktur dapat terjadi dengan pembebanan berlebih yang tiba-tiba atau dengan propagasi retakan hingga menyebabkan fraktur. Perambatan retak dapat terjadi dengan mekanisme yang berbeda. Oleh karena itu perlu diketahui morfologi permukaan rekahan untuk mencari mekanisme penyebab terjadinya rekahan.
Selama pemeriksaan visual, jika ada endapan korosi yang terlihat, maka perlu untuk menentukan sifat endapan. Endapan tersebut dapat berupa oksida, sulfida, klorida atau karbida, dll. Dalam kasus endapan korosi, perlu diketahui sifat lingkungan operasi dan ketahanan korosi material terhadap lingkungan tersebut.
Sangat penting bagi orang yang menyelidiki kegagalan untuk membedakan antara modus kegagalan dan penyebab kegagalan. Terkadang kedua istilah tersebut bercampur, menyebabkan banyak kebingungan. Untuk mencegah kegagalan di masa depan, penting untuk mengidentifikasi penyebab kegagalan. Sebagai contoh, mode kegagalan adalah kekerasan permukaan yang tidak memadai dari komponen yang gagal, tetapi penyebab kegagalan dapat terkait dengan pemilihan material yang salah atau kondisi pengoperasian yang tidak tepat.
Interpretasi yang akurat dan rinci dari seluruh data yang diperoleh selama berbagai tahap analisis kegagalan penting untuk analisis kegagalan. Tanpa itu, kesimpulan yang tepat yang diperlukan untuk menemukan penyebab pasti kegagalan tidak dapat ditarik. Penentuan penyebab yang tidak tepat selama analisis kegagalan menyebabkan tindakan korektif yang salah yang tidak membantu dalam pencegahan kegagalan di masa depan.
Investigasi analisis kegagalan tidak akan selesai tanpa laporan terperinci. Laporan ini harus menyertakan serangkaian rekomendasi untuk mencegah kegagalan di masa mendatang. Rekomendasi harus konsisten dengan hasil investigasi. Selanjutnya rekomendasi dapat memberikan solusi jangka pendek serta solusi jangka panjang.