Panduan Utama untuk Meningkatkan Akar Penyebab dan Proses Tindakan Korektif (RCCA)
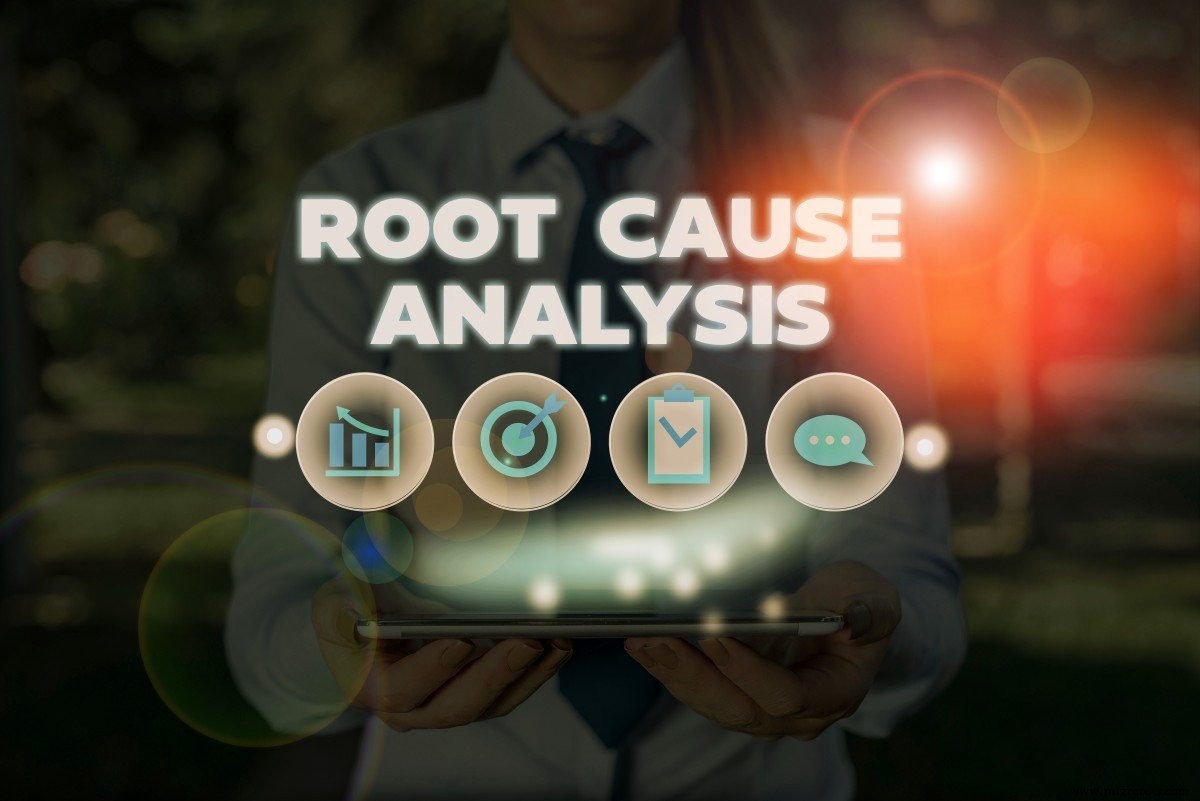.jpg)
Jika perusahaan manufaktur Anda mengalami masalah di sepanjang proses dengan salah satu proses Anda, bagaimana Anda mengatasinya? Sementara opsi jalan pintas adalah dengan hanya menambal gejala dari masalah apa pun, solusi jangka panjangnya adalah melakukan proses RCCA.
Dengan memanfaatkan akar penyebab dan proses tindakan korektif ini, organisasi manufaktur Anda memperkuat prosedur internal dan eksternalnya dengan masuk ke inti masalah daripada mengelola konsekuensinya. Tapi apa itu RCCA, dan bagaimana Anda bisa menerapkannya di organisasi Anda? Panduan komprehensif ini memiliki semua yang Anda butuhkan untuk memulai!
Tautan Cepat:
- Apa itu RCCA dan Mengapa Penting?
- Kapan Melakukan RCCA
- Ikhtisar Proses RCCA
- Menerapkan Pendekatan Berpikir Sistem pada Proses RCCA
- Alat Berkualitas untuk Digunakan dalam Proses RCCA
- CMTC Hadir untuk Membantu Mengembangkan Proses RCCA Anda!
Apa Itu RCCA dan Mengapa Penting?
RCCA adalah proses yang digunakan untuk menganalisis masalah secara sistematis untuk menentukan penyebab yang mendasarinya. Ini mengarah pada identifikasi hubungan sebab dan akibat dalam proses manufaktur.
Daripada menyalahkan orang atas kesalahan, RCCA bertujuan untuk menganalisis setiap langkah prosedur untuk benar-benar memahami di mana kesalahan mungkin muncul, melacak pola, dan banyak lagi.
Kapan Melakukan RCCA
Organisasi manufaktur Anda harus melakukan RCCA sebagai bagian dari rencana tindakan korektif, atau bila tidak melakukannya dapat memengaruhi tingkat kualitas, pengiriman, atau kepuasan pelanggan Anda. Beberapa pelanggan besar sering menjadikannya sebagai bagian wajib dari bisnis mereka; misalnya, RCCA Toyota diakui sebagai yang terbaik di kelasnya di industri otomotif.
Masalah kualitas harus selalu diselesaikan sebagai sebuah tim; kumpulkan para ahli proses yang harus membantu masalah ini dan yang memiliki berbagai keterampilan dan pengetahuan untuk memberikan perspektif yang berbeda.
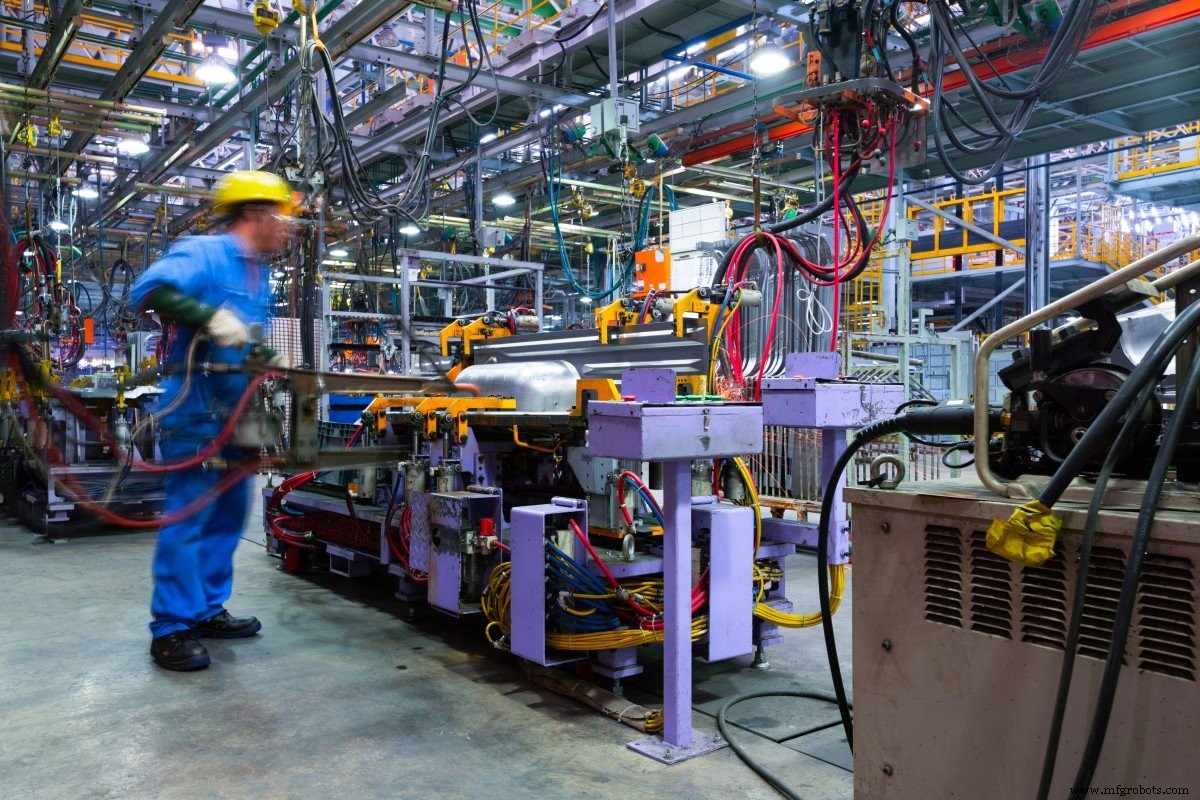.jpg)
Ringkasan Proses RCCA
Proses RCCA umumnya mengikuti langkah-langkah berikut:
- Mulailah dengan Pernyataan Masalah
- Konfirmasi dengan “Going the Gemba”
- Kumpulkan Data untuk Analisis
- Memformulasikan Teori
- Mencapai Pengendalian Jangka Pendek
- Kembangkan Teori untuk Tindakan Korektif Jangka Panjang
- Terapkan Tindakan Jangka Panjang
- Pantau Solusinya
- Verifikasi Semua Sudah Terselesaikan - Bukan Hanya Ditambal
- Perbarui Dokumen yang Relevan
Namun, sebelum menyelami setiap langkah, penting untuk menerapkan pendekatan pemikiran sistem pada keseluruhan proses.
Menerapkan Pendekatan Berpikir Sistem pada Proses RCCA
Sering kali, karena tekanan waktu dan jadwal, dan faktor lainnya, tampaknya lebih mudah untuk menyelesaikan masalah dengan mengobati gejalanya, bukan akar masalahnya. Namun, masalah yang sama akan berulang - dan jika Hukum Murphy mengatakan sesuatu tentangnya, pada saat yang paling buruk. Seiring waktu, akar penyebab yang belum terselesaikan menumpuk yang mengakibatkan situasi di mana seseorang melompat dari satu krisis ke krisis berikutnya. Dengan cepat menjadi situasi yang agak tidak efektif dan tidak efisien.
Sebaliknya, cobalah menggunakan pendekatan pemikiran sistem dengan membuat daftar semua faktor yang menciptakan situasi, mempertimbangkan gambaran yang lebih besar, memperoleh perspektif dari orang lain, dan benar-benar berusaha memahami kelemahan dalam prosesnya. Pendekatan ini lebih lambat dan lebih metodis tetapi sepadan dengan upaya untuk memahami sepenuhnya proses pembuatan dan mengurangi jumlah “kebakaran” untuk diperangi dalam jangka panjang.
Di bawah ini adalah ikhtisar dari setiap langkah Proses RCCA:
Mulailah dengan Pernyataan Masalah
Pernyataan Masalah harus:
- Fokus pada satu masalah yang didefinisikan secara sempit
- Jelas, ringkas, dan faktual
- Sebutkan hasil/konsekuensi
- Jelaskan masalah dalam istilah yang terukur
Pernyataan Masalah tidak:
- Tetapkan penyebab masalah
- Jelaskan cara memperbaiki masalah
Intinya, Anda harus bisa mendefinisikan siapa, apa, kapan, di mana, dan bagaimana masalahnya!
Konfirmasi Dengan "Pergi ke Gemba"
'Going to Gemba' adalah tindakan mengunjungi lantai toko di Lean. Diterjemahkan sebagai 'Tempat Nyata', ini mendorong pentingnya kepemimpinan memahami apa yang terjadi di setiap tingkatan.
Ini mencakup:
- Melakukan panduan proses; juga dikenal sebagai Genchi Genbutsu, yang diterjemahkan menjadi "Pergi dan Lihat" atau "Pergi ke tempat yang sebenarnya untuk melihat keadaan yang sebenarnya"
- Menganalisis proses - apa kelemahannya?
- Bertanya pada diri sendiri apakah masalahnya dapat diduplikasi? Jika tidak - apa yang harus diubah untuk mewujudkannya lagi?
Bagian dari ini juga termasuk mewawancarai pengguna proses, seperti personel lantai, pimpinan produksi, supervisor, pelanggan, dan pemasok untuk meninjau prosedur, metode, aktivitas, dan tugas.
Kumpulkan Data untuk Analisis
Setelah Anda dapat menentukan masalahnya, Anda dan tim Anda perlu menentukan mengapa itu terjadi. Langkah ini menggabungkan pengumpulan semua fakta situasi dan memprosesnya untuk menentukan hubungan sebab akibat. Ini akan mengarahkan Anda ke arah akar penyebab masalah!
Faktor-faktor tersebut untuk dipertimbangkan termasuk:
- Evaluasi Peralatan: Apakah kinerja dan perawatan mesin sudah sesuai standar? Apakah metode dan prosedur yang sesuai diikuti? Apakah kebijakan ini memiliki detail yang memadai, atau adakah ruang untuk kesalahan manusia?
- Bahan: Apakah bahan-bahan yang terlibat memiliki tingkat atau kualitas yang sesuai? Apakah mereka disimpan dan ditangani dengan benar? Apakah ada bukti kontaminasi?
Memformulasikan Teori
Setelah memperoleh fakta dan konteks masalah yang disebutkan di atas, nyatakan penyebab potensial dari ketidaksesuaian dan daftar semua tugas yang terlibat dalam proses manufaktur tertentu. Merumuskan teori akar penyebab dan menentukan bagaimana informasi - tanggal jatuh tempo, hari, penghitungan, total, dll. - akan dicatat secara objektif.
Tinjau catatan ini; apa informasi ini memberitahu Anda? Dapatkah Anda mengidentifikasi faktor-faktor penyebab potensial? Kualitas mana yang menyebabkan masalah - lingkungan kerja, alur kerja, pencahayaan, pelatihan personel, gangguan, atau yang lainnya?
Mencapai Pengendalian Jangka Pendek
Untuk "menghentikan pendarahan", Anda harus menetapkan tindakan penahanan. Ini mungkin memerlukan penggantian peralatan, pelatihan ulang operator, dan penggantian pemasok material. Penahanan jangka pendek memastikan pelanggan dilindungi agar tidak langsung terpengaruh oleh masalah; itu bukan solusi jangka panjang, juga tidak dianggap sebagai masalah yang telah diselesaikan.
.jpg)
Kembangkan Teori Untuk Tindakan Korektif Jangka Panjang
Selanjutnya, pilih dan terapkan solusi tindakan korektif jangka panjang yang sesuai. Mungkin ada beberapa solusi yang tersedia untuk Anda; pastikan untuk memilih solusi yang:
- Akan lebih baik menghilangkan akar masalahnya
- Yang paling hemat biaya
- Apakah yang paling sesuai dengan besarnya masalah
- Mengubah proses secara efektif
Dari faktor-faktor ini, identifikasi solusi terbaik dengan memeringkatnya dan menetapkan kepentingan untuk setiap jalur yang mungkin. Ini akan membantu menentukan tindakan terbaik untuk tim manufaktur Anda secara objektif.
Terapkan Tindakan Jangka Panjang
Setelah memilih solusi terbaik, Anda perlu menerapkan perubahan ini! Mulailah dengan membagi solusi menjadi tugas-tugas berurutan dan buat daftar item tindakan dengan tanggung jawab dan tanggal jatuh tempo yang ditetapkan untuk setiap anggota tim terkait. Namun, pastikan untuk memiliki rencana darurat, dan tanyakan pada diri sendiri apa yang bisa salah, bagaimana Anda tahu ada yang tidak beres, dan apa yang bisa dilakukan untuk mencegahnya? Pertanyaan semacam itu tidak pesimistis - pada kenyataannya, mereka menunjukkan inisiatif dan keterlibatan aktif dengan proses RCCA!
Pantau Solusinya
Pantau masalah untuk memastikan bahwa ketidaksesuaian tidak terulang kembali. Jika itu terulang kembali, tolak akar masalahnya, lalu terapkan solusi alternatif. Selalu tentukan apakah ketidaksesuaian mempengaruhi produk di tempat lain dalam organisasi, atau jika ada produk yang tidak sesuai dikirim ke pelanggan. Anda pasti ingin menyelesaikannya dengan mereka sesegera mungkin!
Pastikan Semua Sudah Terselesaikan - Bukan Hanya Ditambal
Berikan waktu yang cukup agar masalah muncul kembali untuk menentukan bahwa Anda telah mengatasinya dengan benar. Masalahnya mungkin tidak muncul kembali selama beberapa minggu, misalnya, tetapi itu tidak berarti itu tidak akan kembali jika tindakan korektif yang dipilih tidak bertahan lama. Verifikasi bahwa masalah yang diidentifikasi telah diatasi dan tidak lagi terjadi; tidak ada batasan waktu resmi, tetapi solusi Anda harus bekerja secara konsisten.
Perbarui Dokumen Terkait
Merevisi dokumen yang ada dengan solusi baru; pastikan untuk mengunjungi kembali:
- Prosedur &Buku Pegangan Pengguna
- Spesifikasi Pedoman
- Manual Servis
- Buat instruksi kerja baru untuk mendokumentasikan setiap proses baru
- Distribusikan Prosedur Baru
- Dokumentasikan proses RCCA dalam Permintaan Tindakan Korektif
Alat Berkualitas untuk Digunakan dalam Proses RCCA
Alat-alat berkualitas ini dapat membantu organisasi manufaktur Anda meningkatkan proses RCCA Anda:
Histogram
Histogram adalah representasi grafis yang mengatur sekelompok titik data ke dalam rentang yang ditentukan pengguna. Mirip dengan grafik batang, histogram memadatkan seri data menjadi visual yang mudah ditafsirkan dengan mengambil banyak titik data dan mengelompokkannya ke dalam rentang logis atau bin.
Brainstorming
Brainstorming adalah teknik kreativitas kelompok di mana upaya dilakukan untuk menemukan kesimpulan untuk masalah tertentu dengan mengumpulkan daftar ide yang secara spontan disumbangkan oleh anggotanya. Karyawan Anda dapat memberikan wawasan berharga tentang proses manufaktur, jadi mengumpulkan masukan mereka selama proses RCCA Anda adalah penting.
Bagan Kontrol
Diagram kontrol, juga dikenal sebagai diagram Shewhart atau diagram perilaku proses, adalah alat kontrol proses statistik yang digunakan untuk menentukan apakah proses manufaktur atau bisnis dalam keadaan terkendali. Dengan kata lain, ini adalah grafik yang digunakan untuk mempelajari bagaimana suatu proses berubah dari waktu ke waktu.
gram sebar
Plot sebar adalah jenis plot atau diagram matematika menggunakan koordinat Cartesian untuk menampilkan nilai-nilai untuk dua variabel biasanya untuk satu set data. Metode pengorganisasian data ini dapat mengungkapkan korelasi apa pun yang ada di antara variabel.
Analisis Pareto
Analisis pareto adalah teknik formal yang berguna untuk menggambarkan secara grafis dampak dari berbagai penyebab. Mereka didasarkan pada Prinsip Pareto, juga dikenal sebagai aturan 80/20. Menurut Prinsip Pareto, dari waktu ke waktu, kira-kira 80% dari cacat misalnya akan datang dari 20% penyebabnya. Jadi dengan mengumpulkan dan memetakan data, Anda mendapatkan visibilitas penyebab yang akan memiliki dampak terbesar - dengan melakukan 20% pekerjaan, Anda dapat menghasilkan 80% manfaat dari melakukan seluruh pekerjaan.
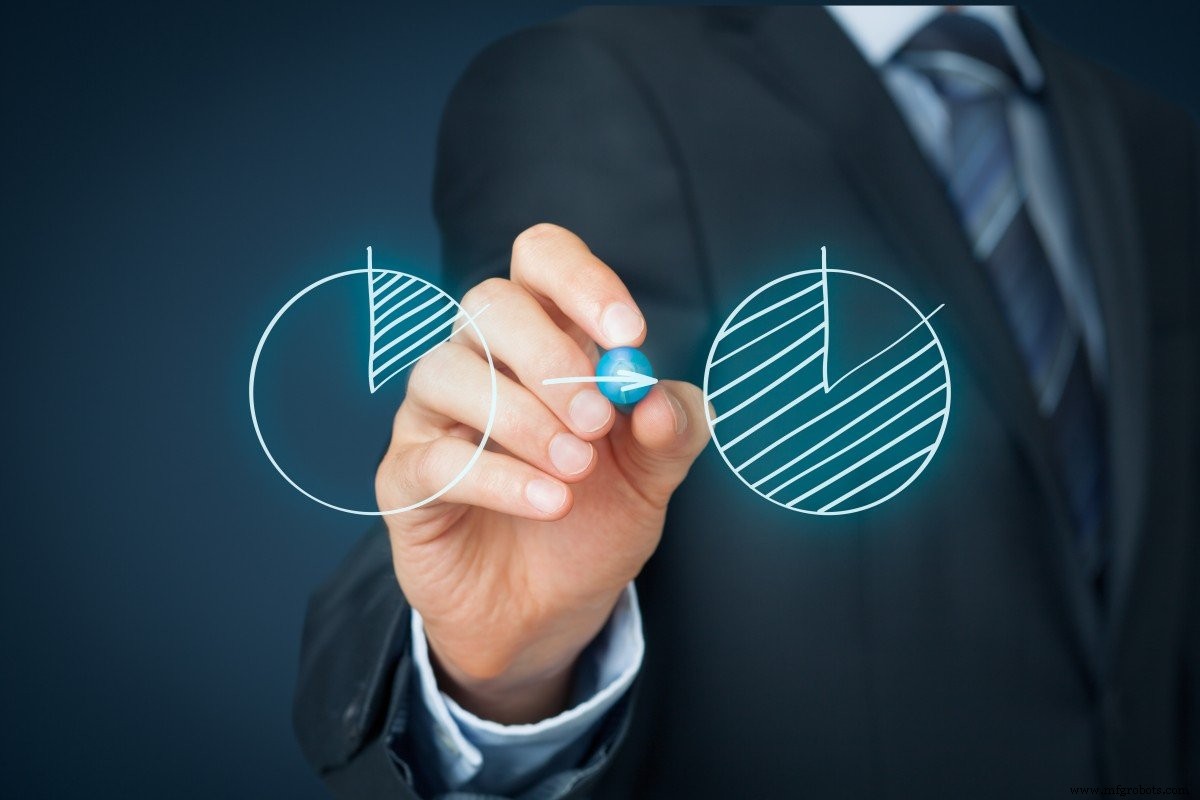
Periksa Lembar
Lembar cek tidak rumit untuk dibuat. Tapi anehnya, mereka mungkin adalah Alat Kualitas yang paling jarang digunakan dan paling berharga. Lembar periksa adalah formulir yang digunakan untuk mengumpulkan data secara real-time di lokasi di mana data dihasilkan. Data yang ditangkapnya bisa kuantitatif atau kualitatif. Jika informasinya bersifat kuantitatif, lembar cek terkadang disebut lembar penghitungan.
Diagram Alur Proses
Diagram alir proses (PFD) adalah diagram yang biasa digunakan dalam teknik kimia dan proses untuk menunjukkan aliran umum proses dan peralatan pabrik. PFD menampilkan hubungan antara peralatan utama dari fasilitas pabrik dan tidak menunjukkan detail kecil seperti detail perpipaan dan penunjukan.
Diagram Sebab &Akibat
Kadang-kadang disebut sebagai diagram tulang ikan, diagram sebab dan akibat adalah alat visual yang digunakan untuk mengatur secara logis kemungkinan penyebab masalah atau efek tertentu dengan menampilkannya secara lebih rinci, menunjukkan hubungan sebab akibat di antara teori.
5 Alasan
Tanya kenapa?" minimal 5 kali; berhenti ketika melangkah lebih jauh tidak menambah nilai lagi. Setelah selesai, tambahkan kata "jadi" atau "karena itu" di akhir setiap respons, lalu kerjakan mundur, ke bagian atas halaman, untuk mengonfirmasi logikanya.
Misalnya:Mengapa Lampu Padam?
- W1-Mengapa lampu padam? Sekring putus.
- W2- Mengapa sekring putus? Motor terlalu panas dan menyebabkan bau terbakar.
- W3- Mengapa motor terlalu panas? Bantalan motor rusak.
- W4- Mengapa bantalan motor rusak? Segel yang salah dipasang dan menyebabkan pelumas bocor.
- W5- Mengapa segel bantalan yang digunakan salah? Itu tidak dipasang dengan benar.
- W6- Mengapa bantalan tidak dipasang dengan benar? Proses perakitan tidak kuat; itu dirancang tanpa pos pemeriksaan untuk operator dan tidak ada instruksi kerja yang harus diikuti.
Diagram SIPOC
Diagram SIPOC (Pemasok, Input, Proses, Keluaran, Pelanggan) adalah alat yang digunakan oleh tim untuk mengidentifikasi semua elemen yang relevan dari proyek peningkatan proses sebelum pekerjaan dimulai. Ini membantu menentukan proyek kompleks yang mungkin tidak tercakup dengan baik dan biasanya digunakan pada fase Ukur dari metodologi Six Sigma DMAIC (Define, Measure, Analyze, Improve, Control). Ini serupa dan terkait dengan pemetaan proses dan alat 'di/di luar ruang lingkup', tetapi memberikan detail tambahan.
Analisis FMEA
Analisis mode dan efek kegagalan adalah proses meninjau sebanyak mungkin komponen, rakitan, dan subsistem untuk mengidentifikasi mode kegagalan potensial dalam suatu sistem dan penyebab serta efeknya. Ini adalah metode sistematis dan proaktif untuk mengevaluasi suatu proses guna mengidentifikasi di mana dan bagaimana proses itu mungkin gagal, dan untuk menilai dampak relatif dari berbagai kegagalan, sehingga mengidentifikasi bagian-bagian dari proses yang paling membutuhkan perubahan.
Diagram Konsentrasi
Diagram konsentrasi cacat adalah alat grafis yang berguna dalam menganalisis penyebab cacat produk atau bagian. Ini adalah gambar produk, dengan semua tampilan yang relevan ditampilkan, di mana lokasi dan frekuensi berbagai cacat ditampilkan.
Analisis 8-Disiplin
Ini adalah metode yang dikembangkan di Ford Motor Company yang digunakan untuk mendekati dan menyelesaikan masalah, biasanya digunakan oleh insinyur berkualitas atau profesional lainnya. Berfokus pada peningkatan produk dan proses, tujuannya adalah untuk mengidentifikasi, memperbaiki, dan menghilangkan masalah yang berulang.
Ada 8 disiplin pemecahan masalah:
- Bentuk Tim
- Jelaskan Masalah
- Kembangkan Tindakan Penahanan Sementara
- Menentukan dan Memverifikasi Akar Penyebab dan Titik Keluar
- Pilih dan Verifikasi Tindakan Perbaikan Permanen
- Menerapkan dan Memvalidasi Tindakan Korektif Permanen
- Mencegah Kekambuhan
- Kenali Kontribusi Tim dan Individu
CMTC Hadir untuk Membantu Mengembangkan Proses RCCA Anda!
RCCA mendukung peningkatan kualitas dengan mempromosikan budaya pemecahan masalah komunikasi tim, yang menghasilkan perubahan perilaku dan budaya perusahaan yang lebih kuat. Orang belajar untuk mengatasi "akar penyebab" dan bukan gejalanya. Garis pemikiran ini mendorong keterlibatan karyawan yang lebih dalam dan pemberdayaan keseluruhan di antara karyawan Anda!
CMTC menawarkan bantuan teknis, pengembangan tenaga kerja, dan layanan konsultasi kepada produsen kecil dan menengah (UKM) di seluruh California untuk membantu SMM meningkatkan produktivitas dan daya saing global mereka. Untuk informasi lebih lanjut tentang CMTC, kunjungi situs web kami di www.cmtc.com atau hubungi kami di 310-263- 3060.
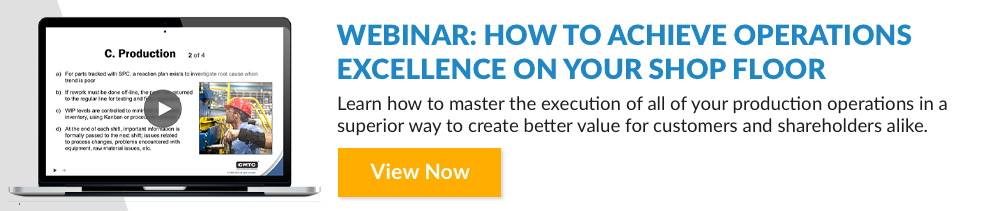