Apa itu Pengecoran Pasir?
Cara membentuk coran kompleks dengan cetakan pasir
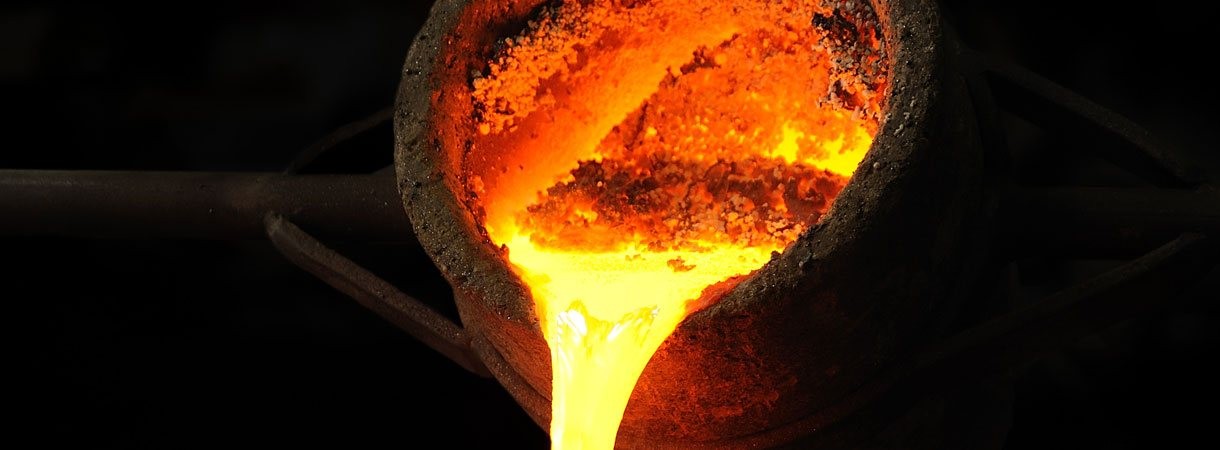
Pengecoran pasir adalah proses yang memanfaatkan cetakan pasir yang tidak dapat digunakan kembali untuk membentuk coran logam. Di satu sisi, casting adalah proses pembuatan yang tampak sederhana:siapa pun yang telah membentuk kastil di pantai tahu pasir dapat digunakan untuk membuat bentuk detail. Namun dalam pengecoran, berurusan dengan panas logam cair, banyak faktor yang harus dipertimbangkan untuk sukses. Pengecoran digunakan untuk membuat komponen logam dari semua ukuran, mulai dari beberapa ons hingga beberapa ton. Cetakan pasir dapat dibentuk untuk membuat coran dengan detail eksterior halus, inti dalam, dan bentuk lainnya. Hampir semua paduan logam dapat dicor pasir. Lubang dibuat di pasir yang dibasahi, diisi dengan logam cair, dan dibiarkan dingin.
Apa itu Pasir Cetakan?
Pasir cetakan memiliki tiga keunggulan penting dibandingkan bahan cetakan lainnya:
- tidak mahal,
- mudah didaur ulang, dan
- dapat menahan suhu yang sangat tinggi.
Pengecoran pasir adalah salah satu dari sedikit proses yang tersedia untuk logam dengan suhu leleh tinggi seperti baja, nikel, dan titanium. Karena fleksibilitasnya, tahan panas, dan biaya yang relatif rendah, pengecoran pasir adalah proses pengecoran yang paling banyak digunakan.
Coran diproduksi dengan menuangkan logam cair ke dalam rongga cetakan. Agar pengecoran berhasil, rongga cetakan harus mempertahankan bentuknya sampai logam mendingin dan mengeras sepenuhnya. Pasir murni mudah pecah, tetapi pasir cetakan mengandung bahan pengikat yang meningkatkan kemampuannya untuk menahan panas dan menahan bentuk.
Pasir hijau (agregat pasir, batu bara bubuk, tanah liat bentonit, dan air) secara tradisional telah digunakan dalam pengecoran pasir, namun sistem pencetakan ikatan kimia modern menjadi lebih populer. Pasir cor yang paling banyak digunakan adalah silika (SiO2 ).
Moulding Sand Properties
Kekuatan
Kemampuan cetakan pasir untuk mempertahankan bentuk geometrisnya di bawah kondisi tekanan mekanis.
Permeabilitas
Kemampuan cetakan pasir untuk memungkinkan keluarnya gas dan uap selama proses pengecoran.
Konten Kelembaban
Kadar air mempengaruhi kekuatan dan permeabilitas cetakan:cetakan dengan kadar air yang terlalu sedikit dapat pecah, sedangkan cetakan dengan kadar air yang terlalu banyak dapat menyebabkan gelembung uap terperangkap dalam pengecoran.
Kemampuan mengalir
Kapasitas pasir untuk mengisi rongga-rongga kecil pada pola. Kemampuan mengalir yang tinggi menciptakan cetakan yang lebih presisi, dan karenanya berguna untuk pengecoran mendetail.
Ukuran Butir
Ukuran partikel individu pasir.
Bentuk Butir
Properti ini mengevaluasi bentuk butiran pasir individu berdasarkan seberapa bulatnya mereka. Umumnya, tiga kategori butir digunakan dalam pasir pengecoran:
- Biji Bulat pasir memberikan kekuatan ikatan yang relatif buruk, tetapi kemampuan mengalir dan permukaan akhir yang baik.
- Butir Sudut memiliki kekuatan ikatan yang lebih besar karena saling mengunci, tetapi kemampuan alir dan permeabilitas lebih rendah daripada pasir berbutir bulat.
- Butir Sub-sudut adalah jalan tengah. Mereka memiliki kekuatan yang lebih baik dan permeabilitas yang lebih rendah dibandingkan dengan butiran bulat, tetapi kekuatan dan permeabilitas yang lebih rendah daripada butiran bersudut.
Kolapsbilitas
Kemampuan campuran pasir untuk runtuh di bawah kekuatan. Keruntuhan cetakan yang lebih besar memungkinkan pengecoran logam menyusut dengan bebas saat mengeras, tanpa risiko robek atau retak karena panas.
Kekuatan Tahan Api
Cetakan tidak boleh meleleh, terbakar, atau retak saat logam cair dituangkan ke dalamnya. Kekuatan refraktori mengukur kemampuan pasir cetak untuk menahan panas yang ekstrem.
Dapat digunakan kembali
Kemampuan pasir cetak untuk digunakan kembali (setelah pengkondisian pasir) untuk menghasilkan coran pasir lainnya dalam operasi manufaktur berikutnya.
Banyak sifat pasir cetak tergantung pada ukuran butir dan distribusi partikel pasir:ukuran butir kecil meningkatkan kekuatan cetakan, tetapi ukuran butir besar lebih permeabel. Pasir berbutir halus memberikan hasil akhir yang baik pada coran, tetapi memiliki permeabilitas yang rendah, sedangkan pasir berbutir halus memberikan kebalikannya.
Aditif khusus atau pengikat dapat ditambahkan ke agregat dasar pasir, tanah liat, dan air untuk meningkatkan kohesi. Pengikat ini dapat berupa organik atau anorganik. Pengikat umum termasuk sereal, pitch tanah, batu bara laut, gilsonit, bahan bakar minyak, tepung kayu, tepung silika, oksida besi, perlit, tetes tebu, dekstrin, dan bahan kepemilikan.
Menemukan kombinasi yang sempurna tidaklah mudah. Beberapa sifat agregat pasir bertentangan satu sama lain:pasir cetakan dengan sifat kolapsitas yang lebih besar memiliki kekuatan yang lebih kecil, dan pasir yang memiliki kekuatan lebih besar memiliki sifat kolaps yang lebih kecil. Pertukaran sering diperlukan untuk mencapai kompromi yang menyediakan properti yang sesuai untuk bagian tertentu dan aplikasi pengecoran. Kontrol yang tepat dari properti pasir cetakan sangat penting sehingga lab pasir telah menjadi tambahan umum untuk pengecoran modern.
Bagian dari Cetakan Pengecoran Pasir
Pengecoran logam dibentuk oleh cetakan yang digunakan untuk memproduksinya – cetakan yang baik merupakan prasyarat untuk pengecoran yang baik. Cetakan memiliki beberapa bagian yang bekerja sama untuk memengaruhi produk akhir.
Rongga cetakan dibentuk oleh pola , model ukuran penuh bagian yang membuat kesan di cetakan pasir. Beberapa permukaan internal tidak disertakan dalam pola, dan sebaliknya akan dibuat oleh inti terpisah.
Sebuah inti adalah bentuk pasir yang dimasukkan ke dalam cetakan untuk membentuk interior pengecoran, termasuk fitur seperti lubang atau lorong. Inti biasanya terbuat dari pasir cetak sehingga dapat diguncang keluar dari pengecoran. cetakan inti adalah wilayah yang ditambahkan ke pola, inti, atau cetakan untuk menemukan dan mendukung inti di dalam cetakan.
Dukungan inti lebih lanjut disediakan oleh chaplet - potongan logam kecil yang diikat antara inti dan permukaan rongga. Untuk mempertahankan dukungan itu, kaplet harus terdiri dari logam dengan suhu leleh yang sama atau lebih tinggi daripada logam yang dicetak. Setelah pemadatan, kaplet akan terbungkus di dalam casting.
Inti pasir dapat diproduksi menggunakan banyak metode yang sama seperti cetakan pasir:karena cetakan dibentuk oleh suatu pola, inti pasir dibentuk oleh kotak-inti; mereka mirip dengan dadu dan dapat dibuat dari kayu, plastik, atau logam. Kotak inti juga dapat berisi banyak rongga untuk menghasilkan beberapa inti yang identik.
Bangun adalah rongga ekstra di dalam cetakan yang dirancang untuk menampung kelebihan logam. Ini mencegah pembentukan rongga susut di pengecoran utama dengan memasukkan logam cair ke rongga cetakan saat mengeras dan menyusut.
Seluruh cetakan pasir ditampung dalam sebuah kotak yang disebut labu . Dalam cetakan dua bagian, yang merupakan tipikal dari pengecoran pasir, bagian atas (berisi bagian atas pola, labu, dan inti) disebut cope . Bagian bawah disebut seret . garis perpisahan adalah garis atau permukaan yang memisahkan cop dan drag.
Cara Membuat Pengecoran Pasir
Pengecoran pasir melibatkan empat langkah dasar:merakit cetakan pasir, menuangkan logam cair ke dalam cetakan, membiarkan logam menjadi dingin, kemudian memisahkan pasir dan melepaskan coran. Tentu saja, prosesnya lebih kompleks daripada kedengarannya.
Langkah pertama perakitan cetakan adalah mengisi sebagian drag dengan pasir. Pola, core print, core, dan sistem gating ditempatkan di dekat garis perpisahan. Cope kemudian dirakit menjadi drag. Pasir tambahan dituang pada bagian atas sampai pola, inti, dan sistem gating tertutup, kemudian pasir dipadatkan dengan cara vibrasi atau mekanis. Pasir berlebih dihilangkan dengan batang pemogokan.
Sekarang setelah cetakan terbentuk, tutupnya dilepas dari tarikan sehingga polanya bisa dikeluarkan dari cetakan.
Ekstraksi pola dilakukan dengan hati-hati untuk menghindari pecah atau rusaknya rongga cetakan yang baru terbentuk. Ini difasilitasi dengan merancang draf :lancip vertikal tegak lurus terhadap garis perpisahan. Draft taper biasanya minimal 1°. Semakin kasar permukaan pola, semakin banyak draf yang akan diberikan.
Sebelum dapat diisi dengan logam cair, cetakan lengkap perlu disiapkan; rongga cetakan sering dilumasi dengan pencucian cetakan untuk memudahkan pelepasan pengecoran. Kemudian inti ditempatkan, bahan cetakan tambahan seperti tali penahan ditambahkan untuk membantu mencegah run-out, dan bagian cetakan ditutup dan dijepit dengan aman; bagian mengatasi dan menyeret mempertahankan keselarasan yang tepat dengan bantuan pin dan pemandu.
Bagian cetakan harus tetap aman sehingga logam cair tidak bocor melalui garis perpisahan. Sebelum menuangkan cetakan tanpa labu, tuang kayu atau logam jaket sering ditempatkan di sekitar cetakan dan pemberat dipasang di atasnya untuk menjaga agar tutup tidak terangkat.
Logam cair memasuki rongga cetakan melalui sistem gerbang :logam cair dituangkan ke dalam cetakan melalui cangkir tuang , berlanjut ke sariawan (bagian vertikal dari sistem gating), dan kemudian melalui runner (bagian horizontal). Gas yang terkumpul dan udara yang dipindahkan keluar melalui ventilasi . Beberapa titik di mana logam dimasukkan ke dalam rongga cetakan dari runner disebut gerbang .
Setelah casting mendingin, itu pecah dari cetakan pasir. Proses menghilangkan pasir dari coran disebut shakeout . Pengecoran dapat dilepas secara manual atau dengan mesin otomatis. Meja agitasi dan gelas putar biasanya digunakan.
Ada variasi pada proses dasar ini tergantung pada pola, jenis labu, dan tingkat mekanisasi:
- Pencetakan Bangku lebih disukai untuk pekerjaan kecil. Seluruh operasi dilakukan di bangku dengan ketinggian yang nyaman.
- Pembentukan Lantai digunakan untuk pekerjaan ukuran sedang dan besar. Seperti namanya, cetakan diletakkan di lantai sebelum dituang.
- Mesin Cetakan digunakan untuk produksi massal. Pencetakan mesin menghemat tenaga kerja dan menawarkan akurasi dan keseragaman yang unggul, sehingga memungkinkan untuk mempertahankan toleransi dalam batas yang sempit dengan kecepatan tinggi. Operasi utama yang dilakukan oleh mesin cetak adalah menyeruduk pasir cetak, menggulingkan cetakan, membentuk gerbang, mengetuk pola dan penarikannya.
Mendaur Ulang Pasir Cetakan
Setelah pasir dikocok dari pengecoran lengkap, gumpalan didinginkan dan dihancurkan. Semua partikel dan butiran logam dihilangkan, seringkali dengan bantuan medan magnet. Semua pasir dan konstituen disaring dengan shaker, layar putar, atau layar bergetar. Pasir yang telah dibersihkan kemudian dapat dimasukkan kembali ke awal siklus produksi pasir cetak.
Pasir cetakan disiapkan dalam muller, yang mencampur pasir, bahan pengikat, dan air. Aerator digunakan bersama untuk melonggarkan pasir agar lebih mudah dibentuk.
Pasir yang sudah jadi dikirim ke lantai cetakan, biasanya dengan truk gayung atau dengan konveyor sabuk, di mana pasir tersebut dibentuk menjadi cetakan; cetakan dapat ditempatkan di lantai atau dikirim dengan konveyor ke stasiun penuangan. Setelah penuangan, coran dikeluarkan dari pasir yang menempel di stasiun pengocokan. Pasir bekas, pada gilirannya, dikembalikan ke tempat penyimpanan dengan konveyor sabuk atau cara lain.
Pasir pengecoran biasanya didaur ulang dan digunakan kembali melalui banyak siklus produksi. Menurut perkiraan industri, sekitar 100 juta ton pasir digunakan dalam produksi setiap tahunnya. Dari jumlah itu, hanya empat sampai tujuh juta ton yang dibuang, bahkan pasir itu sering didaur ulang oleh industri lain.
Proses dan Metode Pencetakan Pasir
Cetakan Pasir Hijau
Campuran pasir hijau yang khas mengandung 89 persen pasir, 4 persen air, dan 7 persen tanah liat. Pasir hijau adalah favorit industri karena biaya rendah dan kinerja keseluruhan yang solid. "Hijau" di pasir hijau mengacu pada kadar air yang ada dalam campuran selama penuangan.
Cetakan pasir hijau memiliki kekuatan yang cukup untuk sebagian besar aplikasi pengecoran pasir. Mereka juga menyediakan collapsibility, permeabilitas, dan reusability yang baik. Kesulitan utama muncul pada kadar air. Kelembaban yang terlalu banyak dapat menyebabkan cacat pada pengecoran, dengan toleransi kelembapan tergantung pada logam yang dicor.
Proses Pengaturan Dingin
Terkadang pengikat non-tradisional digunakan dalam pengecoran pasir industri. Pengikat pengecoran konvensional membutuhkan panas untuk menyembuhkan, sementara pengikat alternatif ini mengikat secara kimia pada suhu kamar ketika dicampur dengan pasir - maka istilah proses pengaturan dingin. Secara teknis maju, proses pengecoran pasir yang relatif baru ini semakin populer. Proses pengaturan dingin lebih mahal daripada cetakan pasir hijau, tetapi mereka menghasilkan coran dengan akurasi dimensi yang luar biasa.
Pencetakan Cangkang
Pengecoran cetakan cangkang adalah penemuan yang relatif baru dalam teknik pencetakan untuk produksi massal dan hasil akhir yang halus; itu pertama kali digunakan oleh Jerman selama Perang Dunia Kedua. Bahan cetakannya adalah campuran pasir silika halus yang kering dengan kandungan tanah liat minimal dan resin termoset 3-8 persen (fenol formaldehida atau gemuk silikon). Ketika campuran cetakan jatuh ke pelat pola yang dipanaskan, cangkang keras dengan ketebalan sekitar 6 mm terbentuk. Untuk menyembuhkan cangkang sepenuhnya, cangkang harus dipanaskan hingga 440 hingga 650 °F (230 hingga 350 ton) selama beberapa menit.
Layanan Casting Kustom
Reliance Foundry bekerja sama dengan klien untuk merancang pola dan metode pencetakan untuk setiap pengecoran khusus. Minta Penawaran untuk mendapatkan informasi lebih lanjut tentang bagaimana layanan casting kami dapat memenuhi persyaratan proyek Anda.
Artikel Terkait
- Panduan Casting Mendalam:Kehidupan Serial Casting
- Masyarakat Pengecoran Amerika. “Proses Pencetakan Pasir”.
Kredit Gambar
- Isi kotak cetakan:OKFoundry, CC BY 2.0, melalui Flickr
- Cope diambil dari kotak cetakan:OKFoundry, CC BY 2.0, melalui Flickr
- Buka cetakan pasir:OKFoundry, CC BY 2.0, melalui Flickr
- Cetakan tertutup:OKFoundry, CC BY 2.0, melalui Flickr