Berapa biaya pelumasan?
Dengan harga minyak mentah yang meroket, kita semua sangat menyadari bahwa harga bensin terus naik, dengan gas akan tetap menjadi komoditas mahal di masa mendatang. Sayangnya, hal yang sama berlaku untuk pelumas. Kebanyakan minyak pelumas berbasis mineral dan, seperti bensin, berasal dari minyak mentah. Jadi ketika harga bensin naik, begitu juga harga pelumas. Bahkan sintetis tidak kebal terhadap masalah ini. Kebanyakan sintetis dibuat baik dari produk sampingan minyak atau gas alam dan telah mengalami kenaikan harga yang serupa dengan minyak mineral dalam beberapa tahun terakhir. Tetapi dalam skema, apakah ini benar-benar penting? Lagi pula, untuk sebagian besar pabrik, jumlah yang dihabiskan untuk pembelian pelumas biasanya kurang dari 1 hingga 2 persen dari anggaran pemeliharaan pabrik. Tentunya ada hal yang lebih besar yang perlu kita perhatikan selain biaya satu galon minyak pelumas?
Meskipun berdasarkan komoditas, ini mungkin benar, bukan biaya pelumas itu sendiri yang harus kita perhatikan, melainkan efek dari cara pelumas diterapkan (atau, lebih umum, disalahgunakan) ke mesin kita. . Jadi, bagaimana kita bisa melacak berapa banyak pelumasan yang buruk merugikan organisasi? Bagi sebagian besar, ini bisa menjadi tugas yang sulit, seringkali tidak mungkin. Alasan yang sama mengapa banyak praktik pemeliharaan pabrik terperosok dalam keadaan biasa-biasa saja adalah persis mengapa kita tidak dapat dengan mudah menentukan efek merusak dari pelumasan yang buruk:pencatatan yang buruk dan sedikit atau tidak ada standarisasi pekerjaan menyebabkan kurangnya data dasar untuk mendasarkan keputusan kita.
Sebaliknya, yang diperlukan adalah "tebakan yang terpelajar". Dengan pendekatan ini, kami menggunakan kerangka kerja yang sederhana namun realistis dalam hubungannya dengan pengetahuan dan pengalaman mereka yang terlibat langsung dalam pemeliharaan untuk "menebak" serangkaian pertanyaan yang lebih jitu secara berurutan (Gambar 1). Begini cara kerjanya.
Kita mulai dengan memperkirakan, dalam angka bulat, biaya pemeliharaan tahunan saat ini. Untuk mengelompokkan peluang (memberikan perkiraan rendah dan tinggi), kami kemudian meninjau riwayat anggaran pemeliharaan untuk menetapkan batas rendah dan tinggi. Dari riwayat ini, kami sekarang dapat memproyeksikan skenario kasus terbaik (biaya lebih rendah dari yang diharapkan), kemungkinan kasus (biaya sesuai harapan) dan kasus terburuk (biaya lebih tinggi dari yang diharapkan karena pengeluaran yang tidak direncanakan).
Selanjutnya, kami menentukan total biaya downtime tahunan. Di sinilah hal itu bisa mulai rumit. Meskipun angka ini relatif mudah di beberapa pabrik, jadwal produksi yang bervariasi, kondisi pasar (tidak semua produk dapat dijual) dan pencatatan yang buruk dapat membuat perkiraan yang realistis menjadi sulit. Dalam memperoleh perkiraan biaya waktu henti, seringkali merupakan ide yang baik untuk melibatkan produksi dan manajemen pabrik; lagi pula, orang-orang inilah yang kami coba jual. Libatkan manajemen dalam proses sejak awal dengan mencari perkiraan biaya terbaik mereka. Ini menciptakan buy-in dan kepemilikan dalam prosesnya. Ini juga mencegah sinisme ketika tiba waktunya untuk menyajikan analisis biaya manfaat akhir. Skenario kasus "rendah", "kemungkinan" dan "tinggi" sangat membantu di sini. Jika biaya waktu henti sudah diketahui, jendela yang cukup sempit dapat dipilih, dikurung oleh perkiraan biaya rendah dan tinggi. Jika biaya waktu henti sulit diperoleh, jendela yang cukup luas dapat dipilih.
Langkah selanjutnya adalah mengidentifikasi, dari angka pemeliharaan dan waktu henti, berapa banyak biaya ini yang dapat dihilangkan melalui program pelumasan yang dirancang dengan baik dan dijalankan dengan baik. Ini menguntungkan untuk melibatkan orang-orang dengan kepentingan dalam membuat penilaian ini. Lagi pula, sulit untuk membantah angka yang telah Anda bantu tentukan sejak awal!
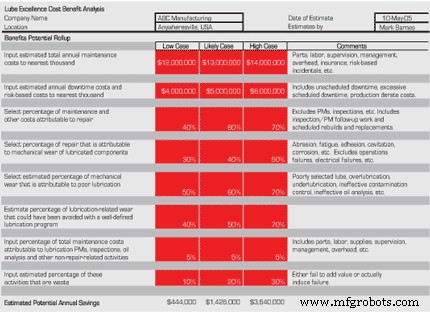
Gambar 1. Menilai biaya pelumasan yang buruk.
Untuk memperkirakan biaya peluang (pemeliharaan dan pengurangan biaya waktu henti) yang disebabkan oleh perbaikan yang diperlukan sebagai akibat langsung dari pelumasan yang buruk, kita perlu memperkirakan hal berikut (lihat Gambar 1):
-
Persentase biaya karena perbaikan (A): Ini termasuk suku cadang, tenaga kerja, pengawasan dan manajemen, overhead, asuransi, biaya berbasis risiko, dan biaya tak terduga.
-
Persentase karena komponen aus atau dilumasi (B): Penting untuk merinci dan mempertimbangkan biaya penggantian untuk komponen berpelumas dan komponen tidak berpelumas terkait (poros, rumah, sangkar, kipas, kopling, dll.) yang terpengaruh oleh kegagalan komponen berpelumas. Perkiraan ini harus mencakup semua pekerjaan perbaikan terjadwal dan tidak terjadwal, seperti penggantian dan pembangunan kembali, serta pekerjaan tindak lanjut untuk commissioning dan penilaian peralatan yang baru digunakan.
-
Persentase masalah keausan karena pelumasan yang buruk (C): Ini adalah perkiraan dampak negatif dari praktik saat ini pada komponen yang dilumasi. Pengaruhnya dapat mencakup:pemilihan pelumas yang salah, pelumas yang terlalu banyak dan terlalu sedikit, frekuensi pelumasan yang salah, kontrol kontaminasi yang tidak efektif (cukup untuk mempertahankan target praktik terbaik) dan praktik analisis oli yang buruk.
-
Persentase keausan yang bisa dihindari (D): Ini bisa menjadi angka yang sulit untuk diperkirakan. Namun, kombinasi dari tebakan terbaik tim pelumas ditambah informasi berbasis studi kasus dari sumber lain dapat berguna dalam "menebak" angka ini.
Setelah perkiraan ini dibuat, biaya peluang yang dihasilkan dari perbaikan komponen yang dilumasi sebagai akibat langsung dari pelumasan yang tidak efektif adalah:Biaya peluang (perbaikan) =(biaya pemeliharaan + biaya waktu henti) x A x B x C x D
Atribut biaya terakhir yang perlu dipertimbangkan adalah biaya inefisiensi yang terkait dengan penerapan praktik pelumasan yang dirancang dengan buruk. Sementara efek dari desain yang buruk (misalnya, frekuensi regrease yang salah, volume dan pemilihan produk) diperhitungkan dalam biaya peluang perbaikan, Anda juga harus mengenali waktu dan upaya yang terbuang terkait dengan desain tersebut. Nilai ini diperoleh dengan memperkirakan persentase anggaran pemeliharaan yang terkait dengan PM pelumasan dan aktivitas non-perbaikan berbasis pelumasan lainnya (X, termasuk tenaga kerja dan material), dan kemudian memperkirakan persentase nilai ini yang tidak perlu (Y). Ini adalah:
Biaya peluang (inefisiensi) =(biaya pemeliharaan) x X x Y
Dengan menggunakan contoh di Gambar 1, diperkirakan bahwa berdasarkan anggaran pemeliharaan tahunan (kemungkinan kasus) sebesar $13 juta dan perkiraan biaya waktu henti tahunan sebesar $5 juta, kami memiliki total $1,426.000 untuk biaya perbaikan dan inefisiensi yang dapat dihilangkan melalui program praktik terbaik yang dirancang dengan baik dan dijalankan dengan baik.
Jadi, apa hasil bersihnya? Ketika sebagian besar perusahaan menjalani latihan ini, mereka dikejutkan oleh hasilnya. Sebagian besar perusahaan (khususnya di industri berat seperti baja, logam dasar, pulp dan kertas, dll.) menyadari bahwa kerugian akibat pelumasan berjumlah 10 hingga 20 persen dari anggaran perawatan mereka - 10 kali lipat biaya komoditas, pelumas.