Membuktikan pengelasan LM PAEK untuk Demonstrator Pesawat Multifungsi
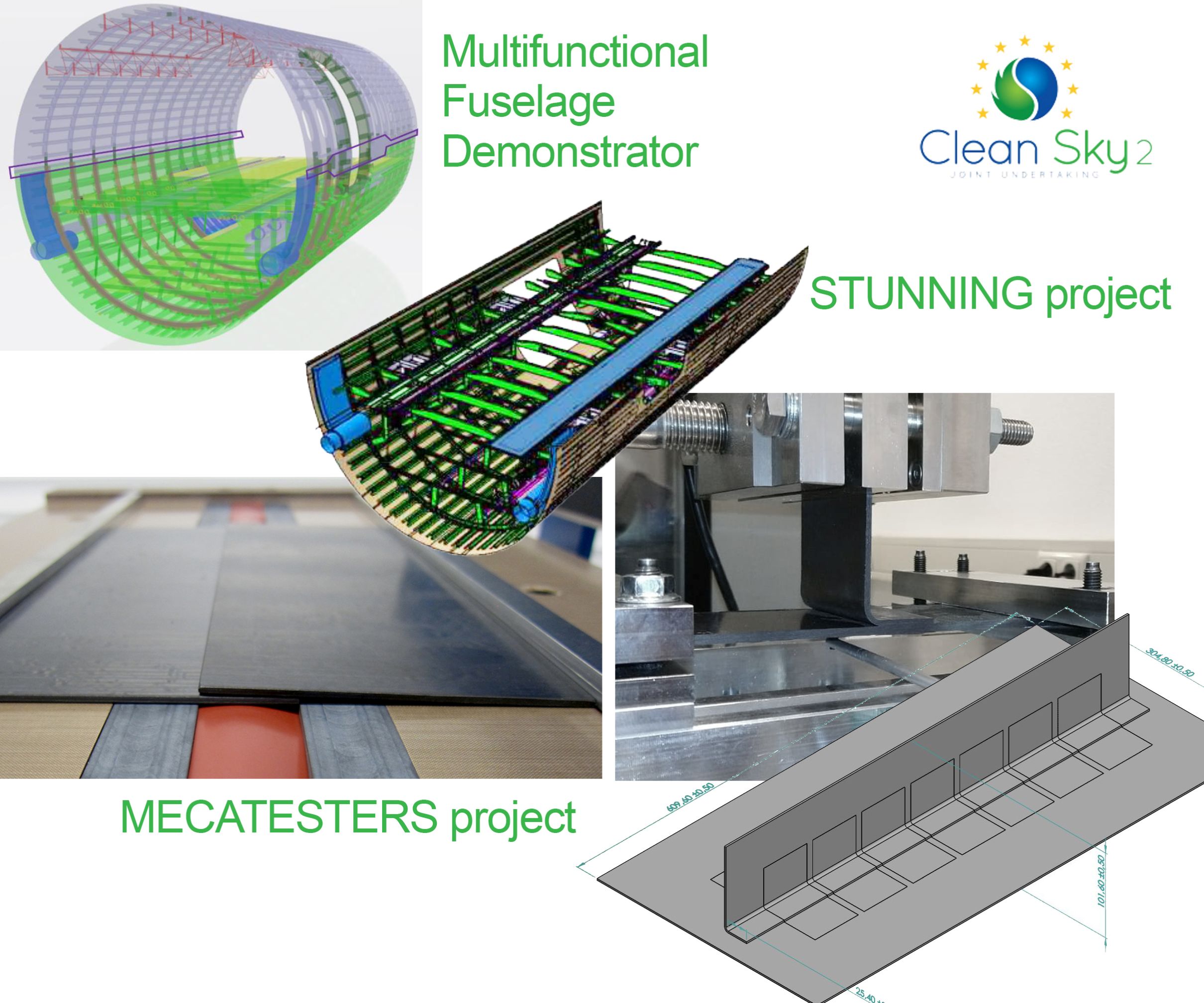
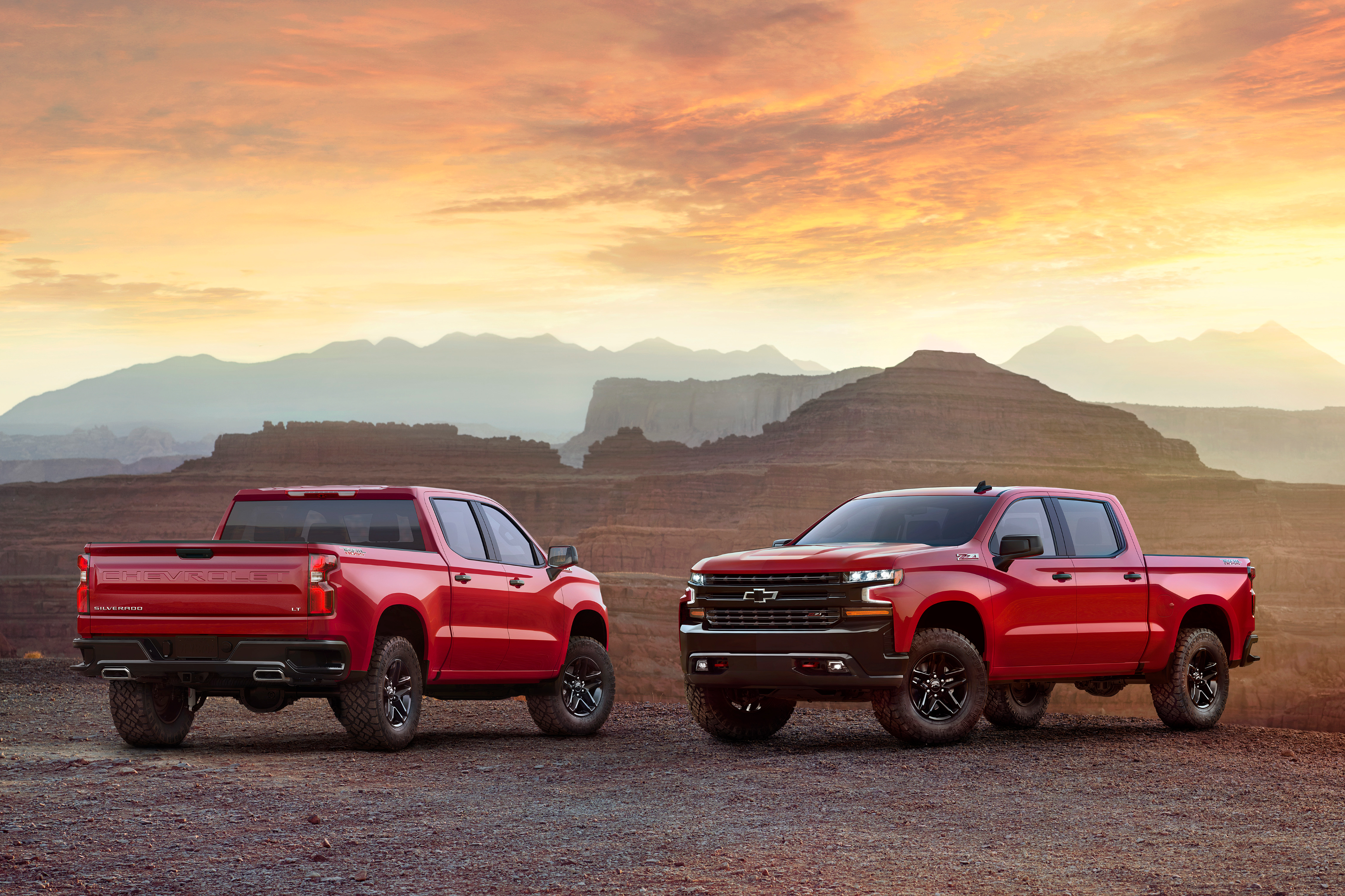
Jenis penelitian aeronautika ini dimulai dengan European Commission Framework Program (FP) untuk pendanaan R&D, mulai dari FP2 (1987-1991) hingga FP7 (2007-2013). Program-program ini telah memberikan kontribusi besar untuk mematangkan berbagai macam teknologi ke tingkat kesiapan teknologi (TRL) 6 dan implementasi di pesawat terbang seperti Airbus A350.
Salah satu perbedaan dalam Clean Sky 2 adalah organisasinya di sekitar demonstran besar. MFFD adalah salah satu dari tiga bagian pesawat skala penuh yang diproduksi di dalam Large Passenger Aircraft (LPA) Innovative Aircraft Demonstrator Platform (IADP) (lihat teks biru di atas kotak biru pada infografis di atas) . Di dalam LPA IAPD ada tiga platform. MFFD berada dalam Platform 2 “Innovative Physical Integration Cabin-System-Structure”, yang menampilkan dua demonstran besar lainnya.
Untuk memahami apa artinya ini, saya kembali ke sesuatu yang dikatakan insinyur Airbus Airframe Research &Technology (R&T) dari Getafe, Spanyol, ketika saya sedang meneliti komposit multifungsi pada tahun 2015. Mereka berkata, pada intinya, “Kami tidak lagi menginginkan duplikasi dan sisa pembuatan silinder struktur luar dan silinder dalam; kami ingin mengintegrasikan badan pesawat struktural dengan sistem kabin.” Saya berjuang untuk memvisualisasikan apa artinya ini — sampai saya melihat sketsa MFFD.
SUMBER | Penyebaran Clean Sky 2 (CS2) dan “Demonstran komposit termoplastik — peta jalan UE untuk badan pesawat masa depan”.
“Modularitas, integrasi, dan menciptakan platform bersama adalah kuncinya,” kata Ralf Herrmann, Airframe R&T Khas Pesawat di Airbus Operations GmbH (Bremen, Jerman) dan pemimpin program MFFD. Saya mengutip di sini dari halaman MFFD di situs web Clean Sky 2:
Herrmann:"Kami sudah lama mengetahui bahwa manfaat pengurangan berat badan dan penurunan biaya berulang dalam produksi pesawat — saat menggunakan komposit termoplastik — hanya dapat dicapai dengan integrasi beberapa disiplin ilmu. Ini berarti bahwa berfokus pada struktur saja tidak dapat mencapai manfaat penuh dari teknologi komposit.”
Fleksibilitas termoplastik perlu diterapkan dalam kombinasi dengan pendekatan desain, menurut petugas proyek Clean Sky 2 Paolo Trinchieri:“Hal ini diperlukan untuk menghilangkan pemisahan fungsi buatan pada tahap pra-desain pesawat dan untuk merencanakan tingkat produksi yang tinggi dari pembuatan, perakitan, dan pemasangan pesawat sejak awal.”
Herrmann sebelumnya adalah manajer proyek untuk proyek FP7 MAAXIMUS (Struktur Pesawat Lebih Terjangkau melalui Ukuran numerik yang Diperluas, Terintegrasi, &Dewasa). Berjalan dari April 2008 hingga September 2016, MAAXIMUS menyertakan 60 mitra dan bertujuan untuk mendemonstrasikan pengembangan cepat dan validasi pertama yang tepat — dengan mematangkan enabler virtual dan fisik secara bersamaan — dari pesawat komposit yang sangat dioptimalkan untuk mencapai pengurangan 50% dalam waktu perakitan bagian badan pesawat besar, 10% pemotongan biaya berulang, 10% bobot struktural lebih rendah dan siklus pengembangan 20% lebih pendek. Tujuan MFFD dapat dilihat sebagai perpanjangan:
- Aktifkan tingkat produksi 70-100 pesawat/bulan
- Kurangi bobot badan pesawat hingga 1.000 kg
- Kurangi biaya berulang sebesar 20%.
Salah satu kunci yang memungkinkan adalah gabungan tanpa debu (tanpa lubang, tanpa pengencang) melalui komponen komposit termoplastik yang dilas. Herrmann menjelaskan bahwa pendekatan berurutan saat ini untuk pembuatan pesawat — di mana struktur badan pesawat harus cukup lengkap sebelum sistem plus fitur kabin dan kargo dapat dipasang — memakan waktu dan “sensitif terhadap kegagalan”. Sebaliknya, MFFD mengejar elemen struktural yang sangat terintegrasi dan modul sistem yang telah dilengkapi sebelumnya, yang dapat dipasang cukup awal, jauh sebelum perakitan akhir.
Ubah ke sambungan longitudinal dan LM PAEK
Kegiatan proyek MFFD dimulai pada tahun 2017. Setiap tahun setidaknya ada satu panggilan untuk proposal (CFP) di mana pemimpin proyek menguraikan topik yang perlu dikembangkan lebih lanjut. Seperti terlihat pada gambar di bawah, desain sambungan bias yang ditunjukkan pada CFP08 (April 2018) telah berubah menjadi sambungan longitudinal oleh CFP09 (Sep 2018).
“Sambungan bias menyajikan masalah terkait aksesibilitas dan pemasangan struktur lantai yang kami sadari akan sulit diatasi dalam jangka waktu tertentu,” jelas Herrmann. “Jadi, kami memutuskan untuk kembali ke desain konvensional untuk menurunkan risiko. Minat utama kami adalah untuk menunjukkan bagaimana mengintegrasikan semua sistem dan elemen kabin yang dapat dipasang sebelum Main Components Assembly (MCA). Ini juga akan menjadi pertama kalinya material komposit termoplastik ini diterapkan dalam struktur badan pesawat utama skala penuh untuk pesawat penumpang besar.”
Desain MFFD berubah dari desain sambungan bias menjadi sambungan longitudinal yang lebih konvensional pada tahun 2018. SUMBER | CFP08 hal.87 (kiri) dan CFP09 hal. 133 (kanan).
Perubahan lainnya adalah pada material matriks komposit termoplastik (TPC). Topik MFFD di CFP08 dan CFP09 mengacu pada serat karbon/PEKK (polyetherketoneketone), tetapi oleh CFP10 (Maret 2019), bahan dasar digambarkan sebagai serat karbon dan PAEK (polyaryletherketone). PAEK adalah keseluruhan keluarga polimer tempat PEEK, PEKK, dan LM PAEK berada.
Seperti yang dijelaskan dalam blog saya tentang PEEK vs. PEKK vs. PAEK, pemasok bahan Cetex TenCate, sekarang Toray Advanced Composites, memproduksi ketiga polimer sebagai pita yang diperkuat serat karbon dan mengklaim bahwa sifat dasarnya sama. Namun, Cetex TC1225 CF/LM PAEK pita meleleh pada 305°C sedangkan TC1320 CF/PEKK pita meleleh pada 340 °C . Dan, menurut CTO global Toray Advanced Composites Scott Unger, “LM PAEK memiliki aliran yang jauh lebih baik … dan juga dapat diproses pada kecepatan yang lebih tinggi daripada PEKK dan PEEK.” TC1225 juga lebih murah.
Badan bawah MFFD:proyek MENAKJUBKAN
MENAKJUBKAN adalah nama proyek untuk pengembangan dan pembuatan bagian bawah MFFD yang lengkap. Proyek ini bertujuan untuk lebih matang:
- Proses perakitan otomatis
- Teknologi manufaktur dan perakitan termoplastik
- Teknologi pengembangan desain dan manufaktur terintegrasi
- Pengembangan arsitektur sistem kelistrikan yang canggih.
Bas Veldman, manajer program di GKN Fokker (Hoogeveen, Belanda) dan manajer proyek STUNNING, menjelaskan bahwa MFFD akan memiliki panjang 8 meter dan lebar 4 meter dengan radius 2 hingga 2,5 meter, yang merupakan skala nyata untuk lorong tunggal. Pesawat keluarga A320. “Ini mirip dengan A321, yang tidak benar-benar melingkar tapi kira-kira berbentuk telur (sedikit lebih tinggi dari lebarnya),” tambahnya.
Bagian badan pesawat bawah 180° akan terdiri dari cangkang badan pesawat bawah dengan stringer dan rangka yang dilas, struktur lantai kabin dan kargo, serta elemen interior dan sistem utama yang relevan. “Kami akan mengirimkan modul besar yang telah dilengkapi sebelumnya untuk perakitan plug-and-play yang sangat cepat,” kata Veldman.
GKN Fokker adalah mitra utama dalam STUNNING dan memiliki empat divisi yang berpartisipasi, termasuk Aerostruktur (Papendrecht, Belanda), Fokker ELMO (Hoogerheide, Belanda), GKN Fokker Engineering Romania (Bucharest) dan GKN Fokker Technologies (Papendredcht, Belanda). GKN Fokker ELMO adalah pemasok wiring harness pesawat dan teknologi sistem kelistrikan. “Ini bertanggung jawab atas arsitektur sistem di STUNNING dan akan fokus pada pengoptimalan sistem kelistrikan,” Veldman menjelaskan, “dan bekerja sama dengan MISI konsorsium CFP08 dalam pengembangan sistem bus daya yang inovatif.”
“Diehl Aviation (Laupheim, Jerman) bertanggung jawab atas struktur interior, termasuk subsistem dan lantai, panel dinding samping dan bagaimana mereka bergabung, antarmuka monumen dan multiport sistem pintar,” lanjut Veldman. “NLR (Netherlands Aerospace Centre, Amsterdam) bertanggung jawab untuk membuat kulit badan pesawat dan stringer, dan TU Delft membantu perakitan, berdasarkan keahliannya dengan pengelasan ultrasonik.” (Lihat “Pengelasan komposit termoplastik” untuk mengetahui lebih lanjut tentang pengelasan ultrasonik.)
Program uji las MECATESTERS
“STUNNING telah meluncurkan tujuh topik CFP dan lima telah mulai bekerja, termasuk MAYA, MISI, EMOSI, TCTool, dan MECATESTERS,” kata Veldman. Yang terakhir adalah program uji las besar dengan KVE Composites (Den Haag, Belanda) dan Rescoll (Pessac, Prancis) yang dimulai pada April 2019 dengan durasi 30 bulan. Veldman menjelaskan bahwa meskipun KVE memiliki sejarah panjang dengan pengelasan induksi dari kedua kain dan komposit termoplastik pita UD, bagian las induksi yang terbang di pesawat hingga saat ini telah menggunakan kain. “Dalam STUNNING, kami membangun praktik terbaik dengan bala bantuan UD dan material LM PAEK, dan juga membandingkan pengelasan induksi dengan pengelasan konduksi pada beban in-service dan kondisi lingkungan yang khas.” Meskipun pengelasan resistansi dan pengelasan ultrasonik termasuk dalam paket pekerjaan MFFD dan CFP lainnya (lihat “Menggabungkan dua bagian ” di bawah), pengelasan induksi dan pengelasan konduksi adalah dua teknik di MECATESTERS.
Labordus di KVE menjelaskan bahwa untuk tiga paket pekerjaan MECATESTERS (WP 1, 2 dan 3), KVE akan membuat semua laminasi uji menggunakan serat karbon TC1225 UD yang diawetkan secara autoklaf/pita LM PAEK (lihat “Laminasi LM-PAEK Toray Pertama untuk Proyek Clean Sky MECATESTERS”). KVE juga akan menyiapkan sampel las induksi untuk pengujian, sedangkan GKN Fokker akan memproduksi sampel las konduksi dan Rescoll akan melakukan semua pengujian fisik. “Nama Rescoll berasal dari penelitian dan kolase, yang merupakan bahasa Prancis untuk ikatan,” kata Labordus. “Mereka dikenal karena penelitian mereka tentang semua jenis ikatan dan menawarkan laboratorium pengujian yang lengkap untuk polimer dan komposit, termasuk mekanik, lingkungan, mudah terbakar, dan setiap tes yang mungkin untuk kualifikasi di bidang kedirgantaraan, otomotif, kereta api, dan industri lainnya.”
Parameter proses dan pengujian
“Kami sebenarnya mulai dengan WP 2 untuk mengatur parameter proses, seperti batas atas dan bawah untuk suhu dan tekanan pengelasan induksi,” kata Labordus. “Misalnya, kami memiliki nominal tekanan yang biasanya kami gunakan, tetapi kami akan menurunkan tekanan sampai kami mulai melihat cacat seperti rongga, dan kemudian kami akan mengevaluasi sifat las tersebut untuk menetapkan batas tekanan yang lebih rendah.” Pengujian juga akan mengevaluasi kecepatan las, yang mempengaruhi laju pendinginan las dan kristalinitas, dan berpotensi sifat mekanik. Parameter yang sama akan diselidiki di Fokker untuk pengelasan konduksi.
Untuk evaluasi, program MECATESTERS akan melakukan beberapa tes, termasuk:
- Uji putaran menurut ASTM D5868–01
- Uji tarik dan geser pada kupon profil-L
- GIC dan GIIC per ISO 15024 dan ISO 15114, masing-masing
(pengujian ketangguhan ini sebenarnya akan selesai di WP 1)
Kupon geser putaran tunggal dari laminasi pita UD yang siap untuk pengelasan induksi (kiri) dan perlengkapan uji untuk pengujian geser gabungan dan pengelupasan dari kupon profil-L yang dilas menggunakan alat yang dikembangkan Rescoll (kanan). SUMBER | Komposit KVE, Telusuri Kembali.
“Metode uji pull-off berasal dari standar internal yang dikembangkan GKN Fokker,” jelas insinyur Rescoll Thomas Salat. “Pengujian tarik dari profil yang dilas tegak lurus terhadap kulit untuk pemuatan kulit,” catat Labordus, “dan sejajar dengan kulit untuk beban geser. Kupas dan geser adalah dua ekstrem, tetapi kami juga akan menguji kombinasi baru ini yang mencerminkan kondisi beban dalam layanan yang praktis.” Pengujian ini akan diselesaikan untuk dua ketebalan laminasi berbeda yang berasal dari desain badan pesawat MFFD — 2,2 dan 2,8 milimeter — pada suhu kamar (RT), suhu dingin (-55 °C) dan suhu tinggi (80 °C) menggunakan pembebanan statis.
Uji tarik pada kupon profil-L di KVE Composites (kiri atas). Di MECATESTERS, jenis pengujian ini akan menggunakan gripper dan pengaturan pengujian yang dikembangkan oleh Rescoll untuk menghilangkan defleksi kulit (kanan atas). Kupon uji akan dipotong dari panel yang dilas (bawah). SUMBER | Ingat kembali, Komposit KVE.
Persiapan permukaan, penuaan dan kelelahan
WP 1 akan dimulai dengan uji ketangguhan. “Untuk pengujian fissurization (GIC dan GIIC), kami akan memulai retakan pada komposit dan mengukur bagaimana retakan ini berperilaku saat dibebani,” jelas Salat. “Salah satunya adalah uji statik yang meningkatkan beban hingga kegagalan. Kami juga akan melakukan pengujian dinamis di mana kami mengulangi beban statis satu juta kali, yang membutuhkan waktu satu hingga dua minggu untuk menyelesaikannya. Kita akan melihat apakah las komposit dapat menahan kelelahan ini. Modus II ini adalah jenis baru dari tes siklik. Kami sedang mengembangkan metode yang diambil dari makalah teknis yang diterbitkan oleh Universitas Eropa dan menyelesaikan parameternya sekarang.”
Juga di WP 1, parameter pengelasan yang ditetapkan di WP 2 akan digunakan untuk memeriksa efek persiapan permukaan serta penuaan dan kelelahan. “Kami akan melihat kontaminan permukaan dan bagaimana hal itu dapat mempengaruhi lasan,” kata Labordus. “Kami juga akan menyelidiki tiga jenis zat pelepas yang berbeda yang biasa digunakan dalam pemrosesan pers dan autoklaf; jenis persiapan permukaan tertentu termasuk pengamplasan, pengamplasan dan perawatan plasma; dan juga penggunaan film resin ekstra pada permukaan yang dilas. Selain itu, kami akan mempelajari pengaruh orientasi serat, misalnya plus/minus 45 derajat pada antarmuka las.”
Rescoll juga akan menggunakan ruang pendingin pada 70 ° C dan kelembaban 90% untuk mensimulasikan penuaan dalam layanan, kata Salat. “Kami kemudian akan melakukan tes standar untuk melihat apakah itu mempengaruhi kinerja las.” Labordus menambahkan bahwa sampel dalam jumlah terbatas akan diambil pada suhu 100 °C dan 120 °C, "untuk memvalidasi klaim bahwa komposit termoplastik tidak memiliki penurunan tajam di atas 80 °C".
Selain uji fissurisasi/GIIC dinamis, uji fatik akan dilakukan dalam mode geser dan tarikan putaran tunggal. “Kami akan mulai dari 80 persen dari beban kegagalan statis dan mencapai 50 atau 75 persen dari ini dalam kelelahan selama satu juta siklus,” kata Labordus. “Kami akan melakukan tes lain juga tetapi masih mendiskusikan ini,” tambah Salat.
Pengelasan ke kurung kompon pendek
Meskipun rincian WP 3 masih dalam tahap finalisasi, hal ini bertujuan untuk menyelidiki las braket cetakan tekan yang terbuat dari bahan serat pendek ke kulit laminasi UD. “Kami akan kembali membandingkan parameter proses dan mengkarakterisasi sifat mekanik lasan,” kata Labordus, “tetapi kami masih bekerja untuk menentukan geometri untuk pengujian.”
Stringer dan klip dilas ke badan pesawat termoplastik. SUMBER:Clean Sky 2 11
th
Panggilan untuk Proposal JTI-CS2-2020-CfP11-LPA-02-35, “Fitur penahan lepas yang inovatif untuk sambungan las termoplastik panjang”, Gambar 2, hlm. 94.
Klip dan braket yang dilas
Sebagaimana diuraikan dalam topik CFP10 JTI-CS2-2019-CfP10-LPA-02-31, semua klip bingkai dan braket sistem untuk badan bagian bawah MFFD akan diproduksi melalui pencetakan injeksi senyawa serat pendek yang dibuat dengan menggunakan kembali limbah pabrik dari produksi manajer topik GKN Fokker laminasi TPC serat berkelanjutan. CF/PAEK adalah bahan dasar dan pengelasan adalah metode penyambungan dasar, meskipun metode pengelasan khusus tidak ditentukan.
Menurut teks CFP10, badan pesawat bawah MFFD akan memiliki 13 bingkai dan sekitar 36 stringer, membutuhkan sekitar 500 klip bingkai (perhatikan ini adalah struktur utama yang memerlukan pengujian struktural dan total ini termasuk klip yang digunakan untuk pengujian) dan sekitar 270 braket sistem (yang struktur sekunder) dibagi berdasarkan jenis yang ditunjukkan di bawah ini:20 braket sistem (1), 120 braket sistem (2), 50 braket sistem (3), dan 80 braket sistem (4).
Contoh part yang akan dikirim dalam topik Clean Sky 2 JTI-CS2-2019-CfP10-LPA-02-31, Gambar 2. SUMBER | Langit Bersih 2 CFP10, hal. 146.
Juga di CFP10 adalah topik badan pesawat atas MFFD JTI-CS2-2019-CfP10-LPA-02-30, “Pengembangan sistem pengelasan inovatif untuk sambungan struktural Komposit berbasis matriks termoplastik” yang dipimpin oleh Aernnova Composites Illescas (Illescas, Spanyol). Direncanakan akan dimulai setelah 1Q 2020, ruang lingkupnya adalah mengembangkan sistem pengelasan untuk mencapai ikatan struktural antara bagian tulangan (gusset, wedges, fitting) dan rangka struktural untuk mendapatkan Door Surround Structure (DSS) yang sangat terintegrasi. Saya berharap dapat memberikan rincian lebih lanjut tentang badan pesawat atas MFFD di blog mendatang. Untuk saat ini, cukup memahami mengapa paket kerja 3 MECATESTERS itu penting dan berapa banyak yang akan dicapai setelah MECATESTERS, STUNNING, dan MFFD selesai.
Menggabungkan dua bagian
Setelah selesai, bagian bawah MFFD akan diberikan kepada Institut Fraunhofer untuk Teknologi Manufaktur dan Material Lanjutan IFAM (Stade, Jerman) untuk digabungkan dengan bagian atas, Veldman menjelaskan. “Kami berkomitmen untuk mengirimkan separuh badan pesawat kami pada akhir tahun 2021,” tambahnya.
Seperti disebutkan di atas, Ralf Herrmann di Airbus adalah pemimpin proyek MMFD; dengan demikian, Airbus mengintegrasikan pekerjaan Fraunhofer IFAM dan CFP07 MultiFAL (sistem otomasi Multifungsi untuk Jalur Perakitan Pesawat) konsorsium —yang bertugas menggabungkan dua bagian badan pesawat, bekerja sama dengan tim MENAKJUBKAN dan badan pesawat atas —untuk mengembangkan solusi untuk berbagai tantangan.
Beberapa di antaranya terungkap dalam dua topik di
ke-11
Call for Proposals (Nov 2019), keduanya dipimpin oleh Airbus akan dimulai setelah Q4 2020 dan berjudul “Perkakas, Peralatan, dan Pembantu untuk penutupan Sambungan Barel longitudinal:”
- JTI-CS2-2020-CfP11-LPA-02-33, “:Integrasi tali pantat dan kontinuitas Perlindungan Sambaran Petir”
- JTI-CS2-2020-CfP11-LPA-02-34, “:Overlap joint dan integrasi Frame Coupling”
Ditulis oleh Piet-Christof Woelcken, manajer topik di Airbus Bremen dan pemimpin paket kerja MFFD, tantangan utama dalam topik ini meliputi:
JTI-CS2-2020-CfP11-LPA-02-33
- Sambungan tali pantat (Gbr. 3 di bawah):
- Sisi kiri demonstran (dalam arah penerbangan) termasuk Penumpang Pintu Surround. Variasi ketebalan kulit di area ini memerlukan integrasi tali pantat bertahap, menggabungkan kulit atas dan bawah.
- Mengingat kerumitan sambungan, las konduksi menggunakan pelat tekanan yang dipanaskan adalah teknologi penyambungan yang disukai.
- Kontinuitas listrik dari proteksi sambaran petir (Gbr. 4 di bawah):
- Kontinuitas listrik proteksi sambaran petir logam (LSP) harus dicapai di kedua sambungan longitudinal di bagian luar badan pesawat.
- Kepala perkakas yang disediakan untuk integrasi tali pantat diharapkan dapat digunakan untuk tujuan ini.
JTI-CS2-2020-CfP11-LPA-02-34
- Sambungan yang tumpang tindih (Gbr. 2 di bawah):
- Sambungan tumpang tindih sepanjang 8 meter di sisi kanan demonstran (dalam arah terbang) menghubungkan kulit badan pesawat atas dan bawah. Dalam arah memanjang, ketebalan kulit di bawah 3mm konstan di zona pengelasan. Dalam arah melingkar, kulit menampilkan geometri bertahap untuk meningkatkan kinerja struktural.
- Pengelasan ultrasonik adalah pilihan bergabung untuk mencapai tingkat produksi yang tinggi.
Gbr. 2 (Kiri Atas) :Sambungan tumpang tindih:Pendekatan bertahap telah diambil dalam desain sambungan tumpang tindih. Perhatikan bahwa cangkang bawah terletak di sisi dalam badan pesawat. Gbr. 3 (Kiri Bawah) : Integrasi butt strap:Sejumlah strip di atasnya memerlukan integrasi di seluruh sambungan loncatan. Perhatikan bahwa tali Butt berada di bagian luar badan pesawat. Gbr. 4 (Kanan) :Kontinuitas listrik LSP logam harus dicapai di seluruh sambungan longitudinal di luar badan pesawat CFRP. Merah menunjukkan LSP yang telah dilengkapi sebelumnya, biru menunjukkan LSP yang akan diterapkan sebagai bagian dari topik ini. SUMBER | Clean Sky 2 11
th
Panggilan untuk Proposal JTI-CS2-2020-CfP11-LPA-02-33 dan -34, “Integrasi butt strap dan kontinuitas Lightning Strike Protection”, hlm. 78 dan 86.
JTI-CS2-2020-CfP11-LPA-02-34
- Integrasi kopling bingkai (Gbr. 5):
- Sambungan tumpang-tindih:Kopling rangka di bawah sambungan tumpang-tindih perlu merekatkan secara struktural rangka cangkang atas dan bawah.
- Tali pantat:Kopling bingkai di bawah tali pantat harus mengikat secara struktural rangka cangkang atas dan bawah serta menyambung ke kulit.
- Pengelasan tahanan adalah teknologi pilihan untuk tantangan teknis ini.
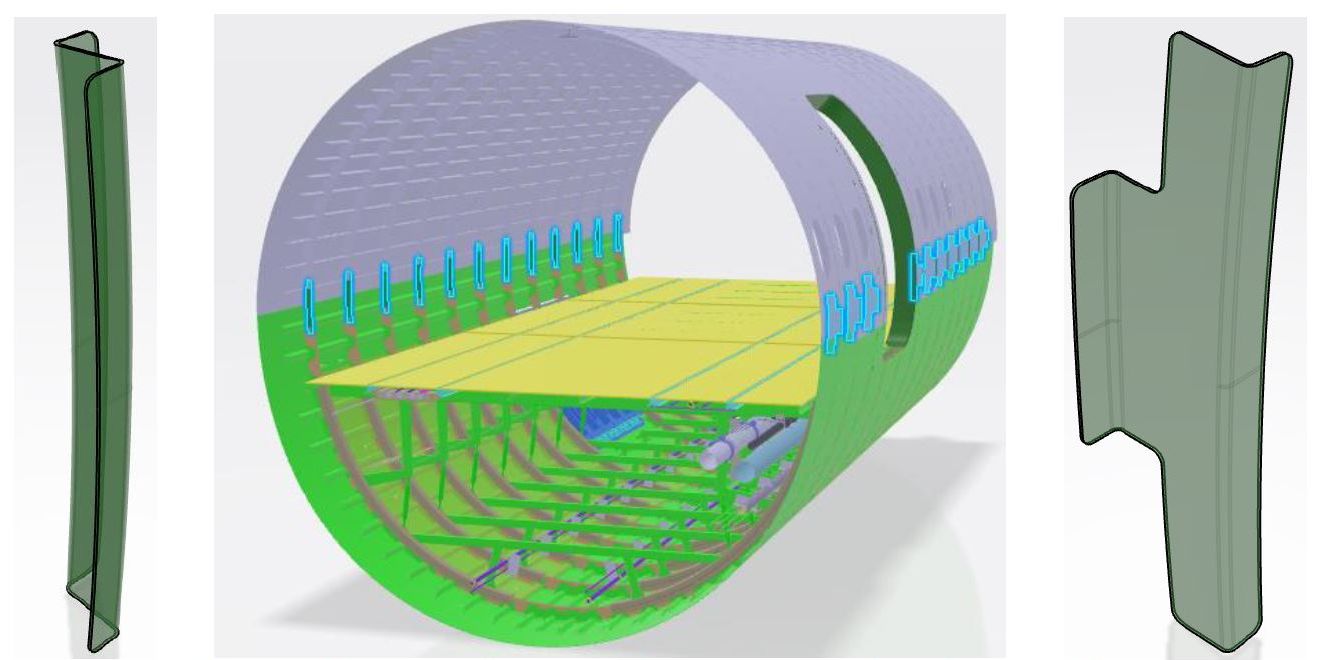
Integrasi kopling bingkai. Perhatikan bahwa kopling rangka berbeda di setiap sisinya sebagai bagian dari demonstrasi teknologi. SUMBER | Clean Sky 2 11
th
Panggilan untuk Proposal JTI-CS2-2020-CfP11-LPA-02-34, “Perkakas, Peralatan dan Pembantu untuk penutupan Sambungan Barrel longitudinal:Sambungan Tumpang Tindih dan Integrasi Kopling Bingkai”, Gbr. 5, hlm. 86.
Metode pengelasan, kepala perkakas, dan toleransi
Herrmann menjelaskan bahwa pengelasan konduksi akan didemonstrasikan di sisi kiri melalui sambungan butt strap dan pengelasan ultrasonik di sisi kanan melalui sambungan tumpang tindih sementara pengelasan resistansi akan digunakan untuk kopling rangka. “MFFD akan mendemonstrasikan banyak pendekatan teknis, jadi ini tidak sama dengan pembuatan badan pesawat yang sebenarnya, melainkan dirancang sebagai kendaraan untuk mendemonstrasikan dan mematangkan teknologi,” tambahnya.
Mengembangkan kepala perkakas las
Tujuan dari dua topik yang ditulis oleh Woelcken ini adalah untuk mengembangkan kepala perkakas yang diperlukan untuk sambungan las ini. “Saat Anda mengelas dua bagian, Anda harus menerapkan panas dan tekanan,” jelasnya. “Jadi, ini diterapkan oleh kepala perkakas saat pengelasan. Untuk proses pengelasan konduksi tipe Fokker, Anda secara aktif menerapkan panas dan tekanan di satu sisi dan tekanan pasif dari penyangga diberikan di sisi lain. Sambungan pantat adalah tumpukan enam pita, dan dalam penyambungan, kami akan menempatkan tumpukan dan memanaskannya selama pengelasan. Namun, karena bahan pita LM PAEK UD relatif baru dalam pengelasan, kita harus memahami kondisi proses dan bagaimana kita dapat mengkompensasi toleransi. Jadi, kita harus menentukan bahan dan ketebalan, serta geometri kepala perkakas.”
“Perhatikan bahwa menggunakan sambungan pantat jenis ini adalah proses standar untuk apa yang kami lakukan pada sambungan lain di pesawat kami,” kata Woelcken. “Untuk MFFD, kami ingin membiarkan badan pesawat bagian atas dan bawah tidak berubah dari praktik standar ini untuk meminimalkan jumlah material yang harus kami sesuaikan.”
Fleksibilitas dalam toleransi
Woelcken mencatat bahwa karena permukaan pengelasan paling atas pada dasarnya dilebur menjadi cairan dan kemudian ditekan bersama, "ini memberikan banyak fleksibilitas untuk mengakomodasi toleransi." Catatan, saat ini, dengan termoset sayap dan badan pesawat yang diperkuat serat karbon (CFRP), masalah toleransi ini diatasi dengan menerapkan perekat shim cair. Meskipun hanya sedikit orang yang ingin mendiskusikan hal ini secara publik, masalah umum shimming pada aerostruktur komposit telah diakui secara luas dan inisiatif untuk mengurangi dan/atau menghilangkannya telah dipublikasikan, seperti metode perakitan Flexmont untuk bidang ekor vertikal.
“ Kami berharap mendapatkan keuntungan dalam mengatasi toleransi dengan menggunakan komposit termoplastik,” kata Woelcken, “terutama dengan memanfaatkan konsep desain kami dan memanfaatkan pengalaman kami dengan CFRP termoset dan pengelasan logam. Kuncinya adalah pemantauan in situ selama pemanasan dan penerapan tekanan.” Dia menekankan bahwa panas adalah parameter nomor satu. “Saya terkejut betapa toleran proses pengelasan komposit termoplastik terhadap tekanan. Tantangan utama di sana adalah menahan tekanan itu dan bagaimana tekanan itu turun. Saat ini, kami sedang memantau sisi belakang sambungan las.”
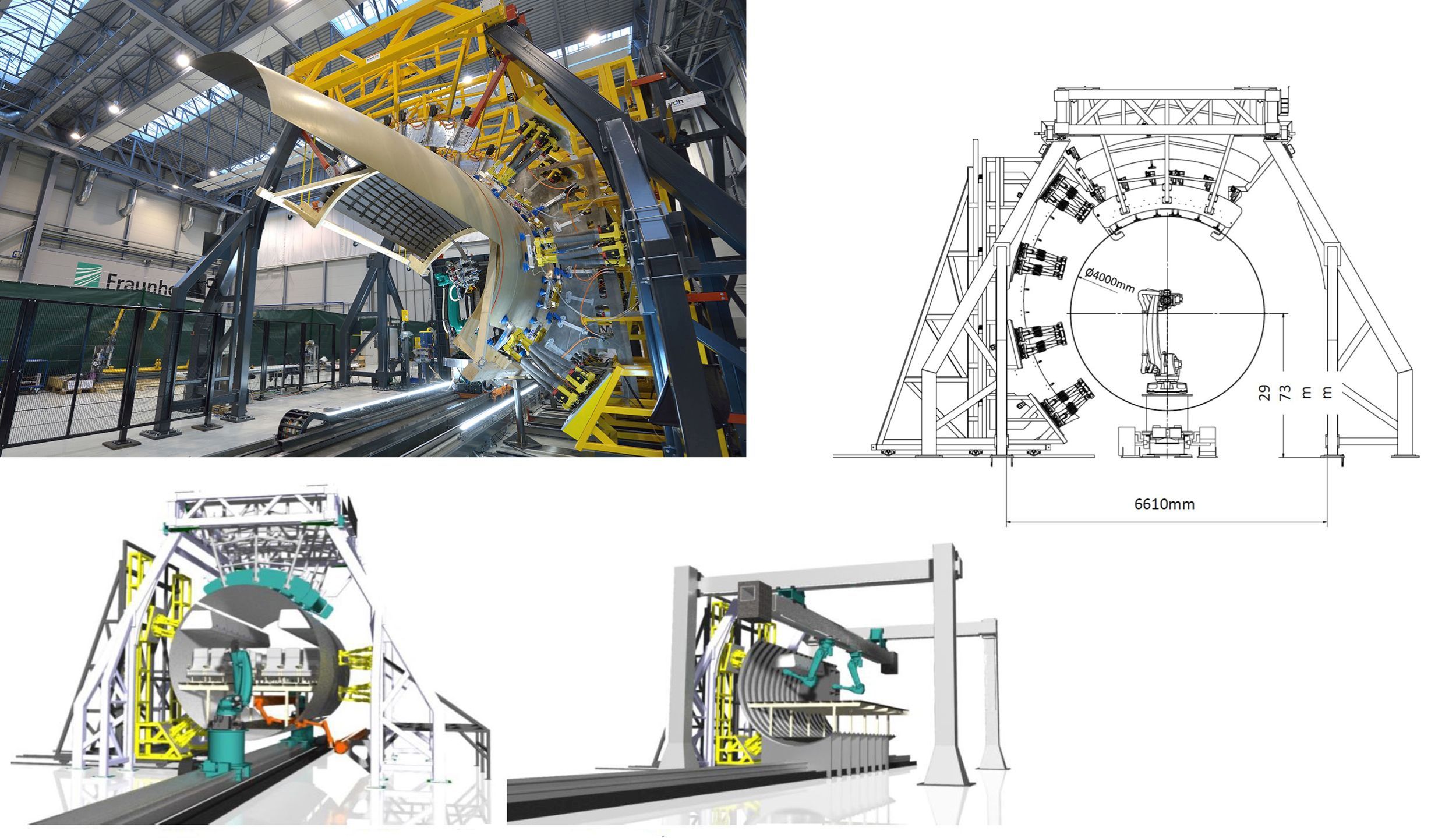
Sistem pabrik perakitan otomatis IFAM Fraunhofer (kiri atas) dengan dimensi di awal topik kerja CFP07 (kanan atas) sedang dimodifikasi untuk mengakomodasi badan pesawat 360° untuk mengelas sambungan memanjang dan melingkar MFFD. SUMBER | Fraunhofer IFAM dan cfk-valley.com, Clean Sky 2 7
th
Panggilan untuk Proposal, JTI-CS2-2017-CfP07-LPA-02-22, hal. 76.
Otomasi perakitan
Pada tanggal
7
Panggilan untuk Proposal, topik JTI-CS2-2017-CfP07-LPA-02-22, “Pengembangan sistem pabrik otomatis ukuran penuh untuk sambungan memanjang dan melingkar badan pesawat” dipimpin oleh Fraunhofer IFAM dalam konsorsium MultiFAL. Kutipan di bawah ini menjelaskan bagaimana kepala perkakas las yang dibahas di atas, yang sekarang dalam pengembangan, dapat diterapkan:
“Untuk mewujudkan proses perakitan pesawat termoplastik, toleransi menjadi topik utama. The positioning and orientation of the fuselage shells, as well as resulting deformations caused by the welding process, need to stay within the tolerances. Comparable accuracies can be oriented to the state-of-the-art process of longitudinal joint. Here, the position error in each direction should be within 0.5 mm (in some exceptions up to 1 mm). … it can be assumed that a pre-load on the joint surface from both sides of approximately 1000N (independent of the welding technology) for a welding seam of 20 mm width is required by the automation system.”
Fraunhofer IFAM — which was also CTC Stade’s partner in developing the Flexmont VTP assembly process — describes its starting point:an in-house assembly plant system which can manipulate parts from 2 to 8 meters long and up to 6 meters high, including a 180° shell of a single-aisle aircraft. The system is enabled by a flexible arrangement of 10 cooperating hexapods (see “Reconfigurable Tooling:Revolutionizing composites manufacturing”), 24 linear units and modular rack elements. Vacuum grippers with 6-axis force and torque sensors adjust the pose and shape of the part, as required, to manage tolerances during assembly. The guidance and monitoring of these rapid, iterative adjustments is achieved through optical measuring devices.
According to the CFP07 text, Fraunhofer IFAM will modify this assembly plant system for holding a complete 360° fuselage, with work scheduled to begin in Q2 2018 and completed in 36 months.
The STUNNING consortium is working with SAM|XL to develop automation for assembling the MFFD lower fuselage. SOURCE | samxl.com
Within STUNNING, activities are planned with the collaborative research center SAM|XL (Smart Advanced Manufacturing XL, Delft, Netherlands) to demonstrate automated welding techniques for assembling the lower fuselage. Specializing in automation for manufacturing large, lightweight composite structures, SAM|XL brings together TU Delft’s Aerospace Engineering group and Robotics Institute. GKN-Fokker is a major participant. One of the methods being investigated is sequential spot ultrasonic welding, which was proven in the Clean Sky 1 Eco Design project and TAPAS 2 as a fast and effective for connecting short fiber-reinforced brackets or clips to fuselage structures.
In her 2016 paper, titled “Smart ultrasonic welding of thermoplastic composites,” Villegas states that it is possible to scale up the ultrasonic welding process via sequential welding — that is, letting a continuous line of adjacent spot welds serve the same purpose as a continuous weld bead. Lab-scale sequential spot welding was used in the Clean Sky EcoDesign demonstrator’s TPC airframe panel, using flat energy directors to weld a CF/PEEK hinge and CF/PEKK clips to CF/PEEK C-frames (Fig. 6). Experimental comparisons with mechanically fastened joints in double-lap shear and pull-through tests showed promise. The process is further explored in 2018 papers {and 2019 papers} by Villegas’ TU Delft team member Tian Zhao {and in Villegas’ 2019 paper}.
— “Welding thermoplastic composites”, G. Gardiner, 2018.
The STUNNING consortium’s work with TU Delft and SAM|XL is adapting this technology to weld multiple system and semi-structural brackets, stiffening elements and stringers to the MFFD lower fuselage shell.
Work breakdown and timeline for MFFD assembly. SOURCE | Clean Sky 2 11
th
Call for Proposals JTI-CS2-2020-CfP11-LPA-02-33, “Tooling, Equipment and Auxiliaries for the closure of a longitudinal Barrel Joint:Butt strap integration and Lightning Strike Protection continuity”, pp. 79 and 82.
Digital twin phase, 2020 and beyond
According to the Clean Sky website, the MFFD program reached an important milestone in Nov 2019 with the successful passing of its Critical Design Review (CDR). In the timeline above, the MFFD design enters a “Digital Twin Phase” in 2020-2021. What does this mean? “Though we have wrapped up the majority of the design phase, we are taking it a bit further by working with a specific lifecycle management approach,” explains Herrmann. “We are modeling imperfections and nonconformities from the NDT results and process parameters during component manufacturing. We want to combine this Industry 4.0 data with lifecycle management so that we continue to tailor the design according to what we are actually manufacturing. We want to see how far we can push this and what we can accomplish by the end of Clean Sky 2.”
For 2020, the chief agenda is manufacturing. “We hope to present various parts as they come together this year,” says Veldman. What will the largest challenge be for the STUNNING program? “Assembly,” he answers. “Not so much within STUNNING, but our lower fuselage has interfaces with the door surround structure, multiple Airbus-delivered components and the whole upper fuselage. Getting everything delivered at the right time and then bringing it all together will require a number of developments yet.”
That brings us to perhaps the biggest question:Will thermoplastic composites be used on the next aircraft entering production in 2030-35? “For sure, we want to try to use the technologies we are working on,” says Herrmann, “but I cannot say if or when thermoplastic composites will be on future aircraft. The most important part for us is that they are an enabler for dustless joining regarding ramping production to more than 70 aircraft per month. We have to show that it is feasible, not only with metallics but also with thermoplastic composites.”
“By the end of this project, we will have a more complete understanding of thermoplastic composite welding and will gain approval for its use in large primary aircraft structures,” says Salat. “If we can use this for future aircraft, we can achieve significant weight savings and improved sustainability.” But perhaps just as important is Clean Sky’s ability to bring Europe’s aviation research and innovation stakeholders closer together. “We have quarterly meetings where I sit with all of the LPA steering committee,” says Veldman. “I’m talking to the whole of the European aerospace industry, and it most certainly helps to open up opportunities for the future, not only for companies who can supply to us, but for a wide range of collaborations.”