Sorotan:Konvensi Komposit 2019
Prototipe Flappybot (Robot produksi, penempatan, dan perakitan otonom fleksibel) DLR yang menarik adalah keberangkatan radikal dari mesin statis besar dan mahal yang umum dalam pembuatan komponen kedirgantaraan besar. Unit AFP otonom yang ringkas ini dirancang untuk 'berkendara' langsung di atas cetakan. Sumber | DLR
Jika industri komposit ingin terus tumbuh dan meningkatkan daya saingnya, ia harus memanfaatkan peluang yang dibawa oleh digitalisasi dan otomatisasi. Dua konferensi yang berfokus pada kedirgantaraan baru-baru ini di Jerman membahas masa depan manufaktur komposit.
Mengunjungi pabrik masa depan di Stade
Future Factory for Composites menjadi tema dari Composites Convention tahun ini di Stade, Jerman, yang diadakan pada 12-13 Juni. Diselenggarakan bersama oleh CFK Valley e.V. (Stade, Jerman) dan Komposit Karbon e.V. (Augsburg, Jerman), acara tersebut menarik rekor kehadiran hampir 450 orang. Kehadiran AS yang kuat dihasilkan dari kolaborasi dengan Utah Advanced Materials and Manufacturing Initiative (UAMMI, Kaysville, Utah, AS) sebagai jaringan mitra dan Amerika Serikat sebagai negara mitra.
Dalam presentasi utama pembuka, berjudul “Digitisasi:Transisi dari Computer Aided Manufacturing ke Human Aided Automation,” Dr. Jan Stüve, kepala Pusat Teknologi Produksi Ringan di Pusat Dirgantara Jerman (Deutsches Zentrum für Luft- und Raumfahrt; DLR; Stade, Jerman) menawarkan cita rasa dari program yang akan datang. Teknologi pabrik masa depan yang sedang dikembangkan di DLR mencakup beberapa robot yang bekerja sama untuk mengurangi waktu produksi dan mesin kembar digital yang memungkinkan optimalisasi proses. Area utama lainnya menyangkut robot otonom seluler untuk skenario produksi yang fleksibel. Ini termasuk prototipe FlappyBot, kompak unit penempatan serat yang bergerak di atas cetakan. Stüve memperingatkan potensi bahaya dari otomatisasi yang berlebihan dan membahas bagaimana digitalisasi seharusnya melibatkan kembali manusia dalam proses manufaktur.
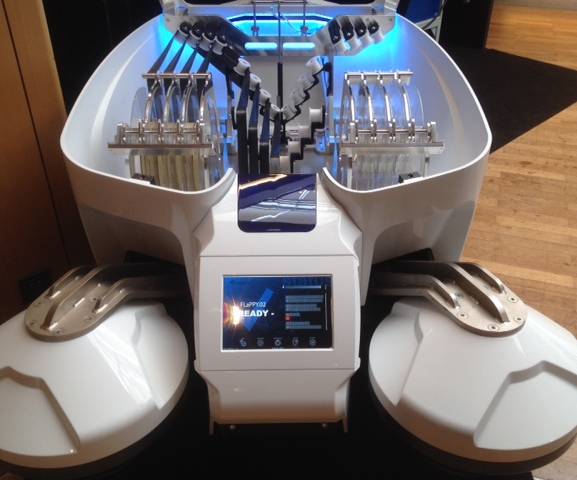
Dinding belakang Audi A8 CFRP, komponen terbesar dari sel penumpang, diproduksi oleh Voith Composites dalam proses yang sangat otomatis yang memungkinkan volume produksi 65.000 komponen per tahun. Sumber | Lembah CFK
Dalam keynote kedua, “Rapid Manufacturing and Thermoplastic Composites – Trends and Technologies,” Dr. Robert G. Bryant, insinyur material senior di NASA Langley Research Center (Hampton, Va., AS), membawa delegasi menjauh dari batasan pabrik terestrial menuju bangunan di ruang angkasa. Kehadiran manusia dalam jangka panjang di luar angkasa akan membutuhkan tempat berteduh dan platform sebagai langkah awal. Pengembangan roket yang semakin besar untuk menempatkan struktur yang semakin kompleks di luar planet tidak berkelanjutan secara ekonomi. Solusi membutuhkan manufaktur dekat atau di tempat. Penggunaan proses penempatan pita canggih tanpa alat (ATP) yang memungkinkan konsolidasi in-situ dari bagian komposit termoplastik bisa menjadi jawabannya. Dalam teknik baru ini, dua robot ATP bekerja berlawanan satu sama lain, satu untuk menyimpan pita prepreg termoplastik, yang lain bertindak sebagai alat. Fabrikasi tanpa alat dapat menurunkan biaya pembuatan kedirgantaraan, meningkatkan ekonomi eksplorasi ruang angkasa serta menguntungkan sektor pasar lainnya (pelajari lebih lanjut di “General Atomics Aeronautical mengembangkan proses komposit termoplastik tanpa alat”).
Keberlanjutan
Kemajuan di bidang manufaktur juga harus dibarengi dengan pengurangan dampak lingkungan. Sejalan dengan itu, pada sesi berikutnya, Jörg Spitzner, pendiri Spitzner Engineers GmbH (Finkenwerder, Jerman), berpendapat bahwa untuk memenuhi target iklim, diperlukan teknologi emisi negatif. Perusahaan Spitzner mengklaim bahwa konsep turbin angin Blancair yang dipatenkan meningkatkan efisiensi turbin dan menghilangkan CO2 dari atmosfer. Udara ditarik ke modul filter yang dipasang di nacelle, di mana CO2 dipisahkan untuk penyimpanan dan daur ulang dalam produksi bahan bakar sintetis dan aplikasi lainnya. Udara bersih dilepaskan melalui bukaan di ujung bilah rotor. Video yang menjelaskan konsep tersebut tersedia di situs web Blancair.
Penyelenggara sesi juga mempresentasikan konsep penilaian eko-efisiensi cerdas dalam produksi komposit (DLR), dan suhu ruangan di luar autoklaf, prepreg yang diperkuat dengan kemampuan api, asap dan toksisitas (FST) (Komposit TCR; Ogden, Utah, AS).
Pemberdayaan melalui simulasi
Selama sisa hari pertama konferensi, perhatian beralih ke simulasi.
Dr. Lars Herbeck, chief technology officer di Voith Composites (Garching, Jerman), membahas bagaimana mesin penempatan serat otomatis (AFP) Voith Roving Aplikator menyederhanakan rantai proses, memungkinkan proses pembentukan awal otomatis yang efisien dengan waktu siklus yang berkurang. Dia menguraikan simulasi struktural dan proses yang dilakukan untuk jalur manufaktur otomatis yang mampu memproduksi 65.000 komponen per tahun untuk dinding belakang belakang plastik yang diperkuat serat karbon (CFRP) Audi A8.
Mark Bludszuweit dari MET Motoren- und Energietechnik GmbH (Rostock, Jerman) menjelaskan bagaimana simulasi menawarkan wawasan tentang cara terbaik untuk memuat suku cadang ke dalam autoklaf, memungkinkan optimalisasi proses pengawetan dan produktivitas yang lebih besar. Kembar digital yang dikembangkan untuk autoklaf terbesar di fasilitas Stade DLR dapat berjalan secara paralel dengan proses sebenarnya, atau lebih cepat untuk menawarkan prediksi perilaku bagian.
Topik pengembangan proses virtual lebih lanjut mencakup pemodelan proses SMC (ESI Group; Chartres-de-Bretagne, Prancis) dan simulasi proses panel sandwich untuk memahami masalah core crush dan prepreg wrinkling di autoclave (Airbus Helicopters; Marignane, Prancis).
Beralih ke pemodelan keselamatan virtual, Jochen Rühl dari Reichenbacher Hamuel GmbH (Dörfles-Esbach, Jerman), bagian dari Scherdel Gruppe, membahas bagaimana pendekatan berbasis simulasi untuk mengelola debu dan partikel yang dihasilkan selama pemesinan suku cadang CFRP telah memberikan manfaat bagi pelanggan seperti seperti Airbus dan Premium Aerotec (Augsburg, Jerman). Simulasi pemesinan dan visualisasi distribusi partikulat membantu produsen mematuhi undang-undang kesehatan dan keselamatan yang diperketat dan meningkatkan hasil pemesinan, serta mengurangi waktu henti dan perawatan alat berat, yang pada akhirnya menghasilkan biaya per suku cadang yang lebih rendah.
Sesi simulasi juga memamerkan proyek yang disponsori Boeing tentang pemodelan biaya virtual manufaktur komposit, dengan mempertimbangkan interaksi kompleks antara desain, produksi, dan keuangan untuk mengidentifikasi pemicu biaya (Massachusetts Institute of Technology; Cambridge, Mass., US), dan konsep perencanaan pabrik digital berdasarkan pemodelan simulasi rantai nilai komposit yang optimal (Fraunhofer IGCV; Augsburg, Jerman).
Konsep permesinan seluler MBFast18 terdiri dari kendaraan berpemandu otomatis, robot, dan mesin CNC portabel dan menawarkan peningkatan produktivitas dalam pembuatan suku cadang pesawat CFRP besar. Sumber | Fraunhofer IFAM
Pemenang penghargaan
Tahun ini, dua proyek berbagi Penghargaan Inovasi Lembah CFK dan uang hadiah €7.500.
Tempat pertama (dan €4.500) diraih oleh proyek sistem robot seluler MBFast18, yang mengembangkan sistem permesinan CNC seluler berbasis kendaraan terpandu otomatis (AGV) untuk suku cadang pesawat CFRP besar.
Sumber | Fraunhofer IFAM
Dibandingkan dengan sistem permesinan statis yang mahal saat ini untuk struktur pesawat besar, sistem robot bergerak yang lebih kecil memungkinkan manufaktur yang fleksibel dan produktivitas yang lebih tinggi.
Sistem MBFast18 menggunakan platform otonom sepanjang 4,6 meter yang dibangun oleh FFT Produktionssysteme GmbH &Co. KG (Fulda, Jerman), sensor navigasi dan keselamatan yang dipasok oleh SICK AG (Waldkirch, Jerman), dan mesin CNC 5-sumbu dari SAUER /DMG MORI (Suhl dan Bielefeld, Jerman). Pelacak laser seluler yang dikembangkan oleh Fraunhofer Institute for Manufacturing Technology and Advanced Materials (IFAM; Stade, Jerman) memposisikan robot dengan tepat. Unit pengeboran, dengan ruang kerja hingga 0,5 meter persegi, dijepit ke komponen menggunakan gripper vakum; posisi pengeboran dihitung dan dikirimkan ke mesin menggunakan perangkat lunak yang dikembangkan oleh BCT GmbH (Dortmund, Jerman). Konsep ini juga berlaku untuk operasi penanganan dan perakitan serta industri lain seperti energi angin dan kereta api.
Tonton video tentang proyek MBFast18:
Tempat kedua diraih oleh perusahaan rintisan Hyconnect GmbH (Hamburg, Jerman) untuk teknologi penyambungan logam-komposit FAUSST. Perusahaan ini awalnya menargetkan sektor pembuatan kapal, di mana penggabungan komposit dengan logam merupakan penghalang utama untuk adopsi komposit yang lebih luas. Solusi FAUSST menggunakan kain hibrida yang terdiri dari kaca rajutan lusi dan serat logam yang memungkinkan logam dan komposit digabungkan dengan kuat secara mekanis. Sisi serat logam disambungkan ke profil baja yang dapat dilas ke struktur logam, dan sisi lainnya dilaminasi ke komponen komposit. Teknologi yang dipatenkan dikatakan mempercepat proses desain dan ikatan secara signifikan. Aplikasi prototipe awal saat ini sedang diuji.
Tonton pengantar proses bergabung dengan FAUSST:
Pengaktifan melalui otomatisasi
Hari Kedua melihat proyek MBFast18 pemenang penghargaan dieksplorasi secara lebih rinci dalam presentasi dari Christoph Brillinger, manajer proyek di Fraunhofer IFAM, dan Dr. Gregor Graßl dari FFT, yang membahas tantangan pengembangan proses cerdas dan sistem kontrol pabrik untuk operasi multi-robot . Jerome Berg, staf insinyur di Northrop Grumman Innovation Systems (Clearfield, Utah, AS), menjelaskan pembuatan otomatis stringer pesawat Airbus di fasilitas perusahaan Utah menggunakan proses AFP yang dikembangkan sendiri, dan Uwe Lang dari Evonik Resource Efficiency GmbH (Darmstadt , Jerman) memperkenalkan “Sandwich Technology 4.0,” sebuah teknologi manufaktur otomatis untuk tingkat produksi tinggi yang menggunakan bahan inti busa ROHACELL perusahaan. Proses pembentukan awal yang sangat otomatis untuk pintu roda pendarat hidung pesawat telah didemonstrasikan dalam kolaborasi dengan DLR dan hub teknologi Airbus CTC GmbH (Stade, Jerman).
Tonton video proses pembentukan awal:
Melakukan perjalanan ke realitas virtual, Felix Hünecke, kepala pengembangan bisnis di ABSOLUTE Reality GmbH (Hamburg, Jerman), menunjukkan bagaimana model bangunan 3D dapat dibuat, diedit, dan dilengkapi dengan gambar, dokumen, dan video untuk menciptakan lingkungan virtual yang dapat dilihat dari mana saja di dunia. Perusahaan membuat tur 3D dari aula produksi DLR di Stade.
Berjalan-jalan melalui ruang produksi DLR:
Felix Schreiber, CEO, ARK Group (Aachen, Jerman), membahas proses dan manfaat biaya dari data mesin terstruktur dalam lini produksi pencetakan transfer resin otomatis (RTM), sementara Sascha Backhaus dari CTC GmbH membahas otomatisasi modular dalam pembuatan komposit dan Hybr -iT project, yang mengembangkan tim di mana manusia dan robot bekerja sama dengan sistem bantuan berbasis perangkat lunak.
Tidak ada peristiwa tentang pabrik masa depan yang dapat mengabaikan topik kecerdasan buatan (AI), dan Amir Ben-Assa, CMO Plataine (Waltham, Mass., AS) membahas peluang dan tantangan penerapan AI dalam pembuatan komposit. Dia mempresentasikan aplikasi praktis AI, mulai dari peringatan (misalnya, penundaan produksi atau masalah kualitas) hingga rekomendasi (misalnya, pemilihan material yang dioptimalkan). Asisten digital berbasis AI di Google Glass bisa menjadi kemungkinan lain, menawarkan interaksi pengguna "bebas genggam" dengan AI di lantai produksi dan presentasi audio dan visual real-time dari peringatan.
Sel Robot Multifungsi di ZLP Augsburg dirancang untuk memungkinkan pengembangan proses terintegrasi untuk pembuatan komponen komposit besar pada skala industri. Sumber | DLR
Topik lebih lanjut termasuk:
- Penginderaan serat optik untuk pemantauan proses cerdas dalam struktur komposit besar (MT Aerospace AG; Augsburg, Jerman);
- Sistem kontrol cerdas untuk pembuatan komposit otomatis (National Composites Centre, Bristol, Inggris);
- Sistem kontrol kualitas berbasis model untuk thermoforming komponen kecil (Faserinstitut Bremen e.V.; FIBRE, Bremen, Jerman);
- Proses untuk pencetakan kompresi termoplastik yang diperkuat serat diskontinyu untuk aplikasi pesawat terbang, berdasarkan otomatisasi fleksibel dan dapat diskalakan hingga ukuran bagian besar (ACT Aerospace; Gunnison, Utah, AS);
- Proses RTM isotermal yang menawarkan pengurangan waktu siklus untuk produksi suku cadang CFRP (Helikopter Airbus) volume tinggi
- Produksi besar-besaran profil termoplastik kompleks, serat karbon, kinerja tinggi untuk strut, pipa, dan driveshaft menggunakan pita preform berbentuk jaring dan pembentukan injeksi (herone GmbH; Dresden, Jerman). Pelajari lebih lanjut tentang herone dan proses ini di “Pembentukan injeksi untuk struktur termoplastik terpadu berkinerja tinggi”.
10 tahun kemajuan di Augsburg
Dalam acara terpisah, Kolokium ke-5 DLR tentang Teknologi Produksi pada 15 Mei melihat hampir 200 tamu berkumpul di Pusat Teknologi Produksi Ringan (Zentrum für Leichtbauproduktionstechnologie, ZLP) di Augsburg. Acara ini merayakan tahun ke-10 ZLP di Augsburg, di mana hari ini sekitar 60 staf fokus pada otomatisasi dan digitalisasi produksi komposit.
Sebuah gripper robot untuk draping otomatis, bagian dari proses manufaktur terintegrasi ZLP Augsburg untuk komponen struktural skala penuh. Sumber | DLR
Hari dimulai dengan dua presentasi dari University of British Columbia (UBC; Vancouver, Kanada), yang memulai kerjasama dengan DLR pada tahun 2016. Prof. Dr. Anoush Poursartip, co-director Digital Learning Factory Initiative UBC, memperkenalkan konsep tersebut. dari pabrik pembelajaran untuk komposit yang terinspirasi oleh rumah sakit pendidikan medis. Pabrik pembelajaran komposit, yang berlokasi di kampus Okanagan UBC, akan dirancang untuk mengintegrasikan penelitian dan pendidikan dengan kegiatan industri. Kembar digital yang diselenggarakan di UBC Vancouver akan menggabungkan data dari pabrik fisik dengan simulasi untuk mengoptimalkan proses produksi komposit kedirgantaraan. Selanjutnya, Prof. Dr. Homayoun Najjaran dari UBC dan Marian Körber dari DLR membahas optimalisasi proses manufaktur yang kompleks dalam lingkungan virtual, dan bagaimana keahlian UBC dalam teknik pembelajaran mesin dan kecerdasan buatan digunakan untuk mengurangi waktu dan biaya pengembangan sistem robot di DLR . Metode pembelajaran mendalam digunakan untuk melatih gripper robot ZLP untuk draping otomatis, bagian penting dari rantai proses otomatis fasilitas Augsburg untuk pembuatan suku cadang CFRP besar. Gripper, yang memiliki 127 modul hisap dengan gaya hisap variabel, mengenali dan mengambil material yang dipotong; modul mengasumsikan geometri yang diperlukan untuk mengalungkannya ke posisinya di dalam cetakan.
Komponen komposit termoplastik untuk desain sekat tekanan belakang Premium Aerotec digabungkan menggunakan teknik pengelasan resistansi yang dikembangkan di ZLP Augsburg. Sumber | Aerotec Premium
Teknologi termoplastik adalah fokus lain untuk ZLP Augsburg. Sebuah proyek untuk mengembangkan sekat tekanan belakang termoplastik (RPB) pertama di dunia untuk pesawat lorong tunggal digariskan oleh Ralph Männich dan Alexander Snger dari Premium Aerotec GmbH. Perusahaan ini bekerja sama dengan ZLP Augsburg, Toray Advanced Composites dan Institute for Composite Materials (IVW) pada desain yang terdiri dari delapan segmen CFRP dengan stringer terintegrasi yang digabungkan menggunakan teknologi pengelasan resistansi yang dikembangkan ZLP. Proses otomatis dengan waktu siklus pendek memungkinkan produksi volume tinggi. Penyelesaian teknologi (ke TRL 6) dijadwalkan pada 2020 dengan target implementasi pada 2021/2022. Pada Paris Air Show bulan Juni, Premium Aerotec menampilkan demonstrasi 1:1 untuk pesawat seri Airbus A320. Dibandingkan dengan sekat tekanan A320 saat ini yang terbuat dari komponen aluminium terpaku, bagian termoplastik dikatakan menghasilkan sifat mekanik yang sama dengan penghematan berat 10-15% dan pengurangan waktu produksi sebesar 50%. Dalam pembicaraan berikut, Dr. Stefan Jarka dan Manuel Endraß dari DLR melanjutkan tema pengelasan termoplastik, menggali lebih dalam kemampuan penyambungan dan NDT ZLP Augsburg, dan perannya dalam proyek RPB.
ZLP Augsburg sedang menyelidiki AFP in-situ komposit termoplastik berbasis lampu flash, solusi energi berdenyut yang menghilangkan penutup pengaman yang diperlukan untuk AFP berbasis laser. Sumber | DLR
Komposit termoplastik juga menawarkan peluang dalam aplikasi luar angkasa. Presentasi dari Ralf Hartmond, MT Aerospace AG dan Lars Brandt, manajer proyek untuk aplikasi terkait ruang angkasa di DLR, menguraikan pengembangan tahap atas termoplastik yang diperkuat serat karbon untuk generasi berikutnya Ariane peluncur roket. Brandt merinci pekerjaan DLR pada penyaringan bahan untuk tangki hidrogen cair (LH2 ) tangki — di mana serat karbon PEEK dan low-melt (LM) PAEK menjanjikan — dan pengembangan proses AFP komposit termoplastik in-situ untuk memungkinkan pendekatan manufaktur aditif ramping. ZLP sedang membandingkan proses AFP in-situ berbantuan lampu flash baru dengan AFP berbantuan laser tradisional.
Menggabungkan teknologi akan menjadi kunci keberhasilan pengenalan komposit termoplastik dalam aplikasi luar angkasa masa depan. ZLP di Augsburg telah mengembangkan sistem pengelasan ultrasonik kontinu berbasis robot yang terdiri dari end-effector yang dipasang pada robot KUKA QUANTEC KR210 pada lintasan linier 7 m. Hal ini telah dibuktikan pada komponen termasuk panel badan pesawat yang kaku dan sekat tekanan belakang. Sumber | DLR
Hari itu ditutup dengan keynote yang menggugah pikiran dari Prof. Dr. Michael Kupke, kepala ZLP Augsburg, berjudul “Digitalisasi dan Produksi Fleksibel.” Dia bertanya apakah kebangkitan ekonomi platform digital menghadirkan peluang atau risiko bagi produsen komposit, dan menunjukkan bahwa TI menjadi kompetensi inti dan harus diperlakukan sebagai keunggulan kompetitif nilai tambah daripada pusat biaya. Dia juga mengatakan ada perubahan paradigma yang sedang berlangsung dari perencanaan terperinci ke pengaturan mandiri (produksi ramping) dan otomatisasi yang dikombinasikan dengan digitalisasi. AI, katanya, memungkinkan produksi yang otonom dan fleksibel. Namun, Kupke menyimpulkan, penting untuk menghargai dan mengintegrasikan keterampilan manusia, yang sangat penting untuk pengambilan keputusan dan peningkatan proses.