Optimasi Produksi dan Proses dalam Manufaktur
Teknik perbaikan proses sangat penting untuk mengoptimalkan tugas manufaktur. Dan bila dilakukan dengan benar, proses yang dioptimalkan ini menghasilkan efisiensi yang lebih besar. Tapi apa hubungannya? Dan mengapa pengoptimalan proses sangat penting untuk mencapai efisiensi yang lebih besar?
Jawabannya terletak pada efektivitas suatu kegiatan. Tidaklah cukup untuk memiliki banyak hal yang diproduksi. Tugas, pemeriksaan, penyesuaian, dan gerakan yang diperlukan untuk memproduksi barang jadi harus diatur untuk menemukan input yang paling sedikit.
Banyak perusahaan menggambarkan ini sebagai "jalan menuju perbaikan berkelanjutan". Dan dalam kasus sebagian besar operasi manufaktur, jalur itu berpusat di sekitar mesin. Orang-orang, seperti operator, mekanik, dan teknisi, berinteraksi dengan mesin mereka karena kebiasaan dan pelatihan. Sebagian besar upaya mereka ditujukan untuk memastikan jumlah waktu aktif maksimum. Tetapi apakah data itu manual atau elektronik, efektivitas tindakan mereka adalah yang terpenting. Dan tindakan membuat penyesuaian yang membuat interaksi itu lebih efektif disebut pengoptimalan proses .
Apa itu Pengoptimalan Produksi?
Optimalisasi produksi adalah kumpulan kegiatan yang dirancang untuk meningkatkan produktivitas dalam sistem produksi. Ini terpisah dari pengoptimalan proses, di mana upaya pengoptimalan difokuskan untuk membuat produk jadi lebih efisien secara bertahap.
Optimalisasi produksi menggunakan model, analisis, prioritas, dan pengukuran untuk meningkatkan produktivitas. Pengoptimalan ini mencakup peralatan, area pementasan, protokol inventaris, tata letak fasilitas, pengangkutan, dan banyak lagi.
Mengoptimalkan produksi adalah taktik yang digunakan dalam industri tapak besar seperti produksi minyak dan konstruksi gas. Namun pengoptimalan dapat digunakan di sebagian besar operasi manufaktur untuk hampir semua proses produksi guna menghasilkan nilai yang lebih besar.
Seiring berkembangnya teknologi IoT, perusahaan telah menemukan bahwa informasi yang disampaikan dari analisis data waktu nyata memungkinkan mereka untuk memahami kondisi dan aliran sistem yang berubah dan bagaimana hal itu dapat digunakan untuk meningkatkan produktivitas. Perusahaan harus menggunakan wawasan ini untuk mengoptimalkan tingkat produksi di seluruh proses produksi.
Contoh area di mana wawasan dapat menghasilkan pengoptimalan produksi dan nilai yang lebih besar meliputi:
- Bekerja dalam Proses – Banyak perusahaan yang berfokus pada teknologi "perbaikan proses" memusatkan upaya mereka sepenuhnya pada produk itu sendiri. Tetapi pekerjaan dalam proses dapat memengaruhi produktivitas secara signifikan. Terlalu banyak persediaan yang diikat terlalu lama akan merugikan arus kas dan dapat menimbulkan potensi masalah perpajakan. Karena banyak pemindahan, hal ini juga dapat meningkatkan biaya tenaga kerja untuk memindahkan produk dari stasiun ke stasiun yang tidak perlu.
- Audit Stasiun Kerja – Karena teknologi telah membuat dasbor interaktif dan papan pabrik menjadi digital, penempatan HMI ini mungkin perlu dipertimbangkan kembali. Apa yang masuk akal dalam lingkungan pelacakan manual dapat meningkatkan beban kerja atau mengurangi efektivitas dalam lingkungan digital. HMI, layar, monitor, dan perangkat lain tidak mencolok dan dapat ditempatkan dengan cara yang meningkatkan produktivitas.
- Ruang yang Tidak Perlu – Dalam manufaktur, ruang mati akan sering berakhir sebagai rumah bagi WIP tanpa tempat untuk dituju. Ini berarti lebih banyak penanganan dan meningkatkan biaya pengoperasian.
- Hambatan – Kemacetan dapat memicu penghentian pekerjaan dalam proses produksi hulu. Jika platform pemantauan pabrik telah mulai memaksimalkan output dari beberapa stasiun kerja, manajer mungkin perlu mengatasi hambatan yang diakibatkan oleh peningkatan hulu ini.
- Komunikasi Inventaris yang Ditingkatkan – Karena data real-time menyoroti masalah dan menentukan solusi, teknologi akan memungkinkan protokol baru untuk pergudangan dan inventaris guna menghasilkan peningkatan produksi. Komunikasi adalah kunci aliran materi di lingkungan baru.
Perjalanan menuju digitalisasi dan produksi berbasis data mencakup persyaratan untuk membuat perubahan guna mengoptimalkan kinerja produksi dan menurunkan biaya. Untuk memanfaatkan teknologi yang tersedia, beberapa perusahaan mungkin menyadari kebutuhan untuk memindahkan mesin atau mengubah seluruh tata letak pabrik saat kekuatan platform pemantauan produksi yang digerakkan oleh IoT mulai memberikan nilai.
Alasan waktu henti teratas dianalisis di bagan pareto Waktu Henti MachineMetrics.
Perbedaan Antara Pengoptimalan Proses dan Produksi
Perbedaan paling signifikan antara optimasi proses dan produksi adalah bahwa optimasi proses menghilangkan langkah-langkah yang tidak perlu dalam langkah proses tertentu dalam sistem produksi. Ini adalah pengoptimalan produk yang dirancang untuk memaksimalkan pengoptimalan produksi melalui peningkatan efisiensi untuk langkah atau sub-proses tersebut. Di sisi lain, optimasi produksi berupaya mengoptimalkan sistem itu sendiri. Ini dapat menggunakan model berdasarkan data waktu nyata untuk melihat laju aliran, tata letak mesin, pemanfaatan tenaga kerja, dan faktor lain untuk meningkatkan kinerja fisik dan tata letak seluruh sistem produksi.
Pengoptimalan proses akan mencakup langkah-langkah seperti:
- Mengidentifikasi masalah khusus untuk proses
- Menganalisis keadaan saat ini untuk membuat keadaan yang diinginkan
- Mengaudit perubahan untuk melihat hasil
- Memantau perubahan agar tetap pada jalurnya
Optimalisasi produksi akan mencakup langkah-langkah seperti:
- Mengubah tata letak pabrik
- Mengubah atau mengatur ulang mesin dan peralatan saat digunakan
- Menerapkan prosedur WIP baru
- Melatih operator dan teknisi tentang cara merespons alarm otomatis dan wawasan tentang sistem pemantauan untuk menghilangkan kebiasaan lama
- Mengembangkan prosedur pengiriman inventaris internal baru
- Menilai monitor dan tata letak HMI
Sasaran dan Manfaat Produksi dan Pengoptimalan Proses
Optimalisasi Produksi dan Proses terdiri dari melakukan perbaikan di beberapa area kritis. Masing-masing area ini secara kumulatif menambahkan hingga proses yang lebih efisien dan output yang lebih signifikan dengan sumber daya yang dikeluarkan paling sedikit. Dengan terlibat dalam pengoptimalan proses, produsen dapat mencapai:
Waktu Kerja Mesin yang Lebih Baik
Downtime adalah kutukan dari keberadaan setiap manajer manufaktur. Dan banyak yang menghabiskan banyak waktu mereka untuk mengelola penyebabnya, serta menangani konsekuensinya Dengan mengambil pendekatan berbasis data, perusahaan dapat mengurangi waktu henti dan meningkatkan waktu kerja peralatan mereka secara keseluruhan.
Salah satu cara untuk mencapai ini adalah dengan menganalisis dan memberi peringkat alasan utama untuk waktu henti yang tidak direncanakan dalam proses produksi. Informasi ini kemudian dapat digunakan untuk mengadaptasi atau menyesuaikan proses untuk mengurangi atau menghilangkan banyak kejadian waktu henti. Karena daftar tersebut diurutkan dari yang terburuk hingga yang paling tidak, pelaku yang paling mengerikan dapat ditangani terlebih dahulu.
Setelah waktu aktif meningkat dan stabil, manajer dapat secara metodis melanjutkan daftar, mengubah parameter proses sesuai kebutuhan untuk membawa setiap item sesuai dengan persyaratan. Namun, kunci daftar dan peringkat ini adalah data yang bersih dan jelas yang membantu memprioritaskan apa yang perlu diperhatikan terlebih dahulu.
Respons Lebih Cepat untuk Masalah di Tingkat Mesin
Terkadang, masalahnya bukan pada mesinnya; itu adalah proses hulu yang memberi makan mesin. Dengan menangkap data untuk memvisualisasikannya, perubahan aliran WIP atau bahan baku lainnya dapat diterapkan untuk meningkatkan waktu kerja. Contoh lain adalah pelatihan, atau kurangnya pelatihan, dengan operator yang berpotensi berada di posisi yang salah pada waktu yang salah untuk menghapus alarm dan menyetel ulang alat berat sesuai kebutuhan.
Sekali lagi, data menjadi penting dalam membantu para pemimpin mengembangkan pelatihan yang lebih baik untuk memastikan operator tidak pernah keluar dari posisi. Intinya adalah mengoptimalkan proses meningkatkan waktu respons di tingkat mesin ketika masalah terjadi. Menggunakan data untuk mengidentifikasi area ini, beberapa area dapat dioptimalkan sekaligus untuk efek pengganda pada waktu aktif. Pelatihan, alur kerja, tata letak peralatan, kualitas material, dan banyak lagi masalah lainnya dapat dioptimalkan dengan data yang divisualisasikan dengan jelas.
Bacaan lebih lanjut: Cara Merespon Waktu Henti Lebih Cepat dengan MachineMetrics
Peningkatan Pemeliharaan
Program pemeliharaan tradisional bergantung pada tindakan reaktif. Entah peralatan tersebut dibiarkan gagal, atau pemeliharaan preventif digunakan untuk menjaga mesin berjalan dengan baik.
Tetapi pemeliharaan preventif dibangun di atas asumsi berbasis waktu. Diasumsikan bahwa sabuk dan puli akan putus pada waktu tertentu berdasarkan rata-rata luas yang ditetapkan oleh produsen peralatan asli (OEM). Tapi ini tidak memperhitungkan peralatan industri di mana produk yang dihasilkan adalah tugas ringan, memungkinkan rentang hidup yang lebih lama untuk suku cadang. Dan itu tidak memperhitungkan produksi tugas berat seperti konstruksi, produksi minyak, atau minyak dan gas secara umum dan fasilitas permukaan lainnya di mana suku cadang dapat aus lebih cepat dari yang direncanakan. Dalam kasus yang pertama, uang dibelanjakan ketika bisa ditangguhkan. Dalam kasus terakhir seperti minyak dan gas , waktu henti dapat terjadi pada saat yang paling tidak diharapkan.
Teknologi canggih seperti pengumpulan data otomatis dapat meningkatkan fungsi pemeliharaan dan meningkatkan waktu kerja peralatan. Dengan mengaktifkan pemantauan berbasis kondisi, pemeliharaan dapat berupa preskriptif atau prediktif berdasarkan kondisi aktual. Dengan menerapkan sistem penginderaan canggih, data dapat membantu perusahaan memahami keadaan peralatan saat ini secara real-time. Seiring waktu, analisis mendalam dapat membantu mengembangkan peluang baru, memprediksi kegagalan secara akurat, dan menjadwalkan penggantian pada waktu yang paling masuk akal, seperti periode pergantian atau penghentian.
Bacaan lebih lanjut: Berbagai Jenis Pemeliharaan di Manufaktur
Sasaran pengoptimalan proses harus mencakup beberapa area:
- Yang pertama adalah meningkatkan proses awal. Menggunakan data, tren, dan pola dapat diidentifikasi untuk membantu mengubah atau memutar lebih baik dalam proses yang ada. Ini mungkin melibatkan masalah tata letak, aliran material, atau komunikasi.
- Kedua, parameter dan kondisi pengoperasian harus ditangani. Sekali lagi, data membuat ini lebih mudah dikenali dan lebih mudah ditangani berdasarkan tingkat keparahannya. Ini mungkin berarti pengaturan mesin, kecepatan optimal, dll.
- Pertimbangan ketiga adalah bahwa peralatan harus diaudit untuk menentukan pendekatan pemeliharaan terbaik untuk meningkatkan proses dan waktu kerja peralatan. Bagian dapat dipentaskan dan disiapkan sebelumnya untuk meningkatkan runtime lebih lanjut.
- Terakhir, data akurat dan visualisasi kondisi alat berat dapat membantu manajer mengembangkan instruksi kerja yang praktis dan ergonomis serta pelatihan yang lebih baik untuk operator, teknisi, dan mekanik.
Metode dan Teknik Pengoptimalan Proses dan Produksi Manufaktur
Untuk produsen yang ingin meningkatkan efisiensi proses mereka, ada banyak solusi yang tersedia:
Dasbor MachineMetrics menampilkan data produksi waktu nyata yang telah dikumpulkan secara otomatis dari peralatan manufaktur di seluruh lantai toko.
Mengumpulkan Data Mesin Waktu Nyata
Pelacakan tradisional untuk pengoptimalan proses biasanya berarti lembar kertas manual dan entri data ke Excel. Ini memakan waktu, rawan kesalahan, dan sulit untuk dipertahankan. Plus, analisis biasanya didasarkan pada wawasan manusia, yang bisa bias atau salah. Inilah sebabnya mengapa perusahaan mulai tidak menggunakan kertas.
Mengumpulkan data waktu nyata dan mengontekstualisasikannya untuk visibilitas oleh manajer dan operator memungkinkan wawasan untuk mengoptimalkan produksi tidak mungkin di masa lalu; wawasan yang dapat memungkinkan pemahaman yang tepat tentang kemajuan produksi dan kinerja peralatan di lantai pabrik. Dengan dasbor serta analisis dan laporan produksi yang relevan, SOP dapat diubah lebih cepat dan menghasilkan kualitas yang lebih tinggi efisiensi dan peningkatan produksi.
Bacaan lebih lanjut: Pengumpulan Data Manufaktur:Kunci untuk Mengoptimalkan Lantai Toko
Analisis Kemacetan
Setiap manajer tahu apa itu bottleneck dan bahayanya bagi proses produksi. Dan sebagian besar dapat mengidentifikasi beberapa area kritis dalam operasi mereka di mana penyumbatan ini terjadi. Namun, seperti halnya data real-time yang memberikan wawasan dan solusi untuk mengoptimalkan proses pada tingkat mesin, data tersebut juga dapat memberikan wawasan tentang kemacetan yang mungkin atau mungkin tidak jelas. Operator manusia dapat menetapkan cadangan untuk satu penyebab ketika data mungkin telah ditentukan itu lain.
Dengan data dan analitik real-time, mesin dan data proses dapat mengidentifikasi hambatan dan kendala dalam seluruh ekosistem. Data ini memungkinkan operator melacak proses untuk fokus pada kemacetan yang menyebabkan waktu henti paling banyak. Baik hambatan tersebut berupa kendala fisik atau kendala operasional seperti penjadwalan atau peluang yang terlewatkan untuk meningkatkan waktu penyiapan dan mengurangi pergantian, data berbasis cloud yang diberdayakan dengan perangkat lunak analitik dan OEE dapat membebaskan gangguan tersebut.
Analisis Waktu Henti
Analisis waktu henti mesin adalah pendekatan yang berguna untuk menyoroti area yang perlu segera ditangani. Dengan memanfaatkan data waktu henti yang ditangkap dengan alasan, manajer dan operator dapat memulai dengan pelanggar terburuk. Tetapi kunci dari analisis ini adalah kemampuan untuk mengakses dan menanyakan data, sehingga memahami penyebabnya.
Penggunaan grafik Pareto, persentase waktu henti yang tidak direncanakan, shift berperforma tinggi dan rendah, dan operator, Waktu Rata-Rata Antara Kegagalan, Waktu Rata-Rata untuk Perbaikan, dan KPI lainnya dapat diperoleh dari data. Melalui dasbor ini, alat dan solusi yang lebih berkembang dikembangkan untuk membangun pendekatan umum guna mengurangi atau menghilangkan penyebab dan mengoptimalkan proses dalam jangka panjang.
Analisis Prediktif
Mungkin salah satu alat paling berharga saat menggunakan perangkat lunak berbasis data, analitik prediktif dapat meningkatkan proses Anda. Perangkat lunak ini menggunakan data mesin untuk mendiagnosis dan memprediksi kegagalan. Dan karena dapat menghubungkan semua peralatan dalam lantai toko, prediksi di seluruh ekosistem dapat dibuat, dan solusi diterapkan lebih cepat, jika tidak segera untuk area masalah yang menarik minat perusahaan. Ini juga dapat melakukan hal yang sama untuk industri besar seperti produksi minyak dan produksi gas.
Algoritme mesin mendeteksi pola yang tidak bisa dilakukan manusia. Hal ini memungkinkan intervensi proaktif sebelum masalah terjadi atau pemeliharaan terencana dan solusi penggantian saat masalah itu terjadi. Analitik prediktif ini bahkan dapat digunakan untuk memperpanjang masa pakai alat dengan memantau keausan alat dan memprediksi kapan alat akan gagal. Aplikasi khusus bahkan memungkinkan solusi otomatis dan semi-otonom dibuat di tingkat alat berat untuk membebaskan operator dari tugas lain guna lebih meningkatkan kualitas dan memaksimalkan produksi.
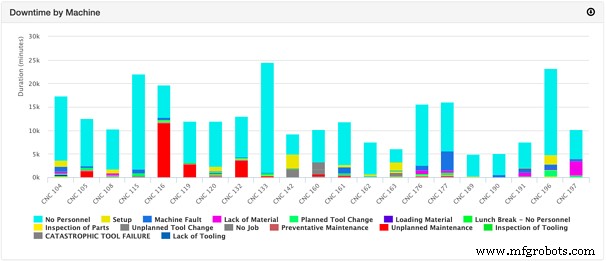
Menganalisis alasan waktu henti di tingkat mesin memberikan wawasan tingkat terperinci tentang mengapa peralatan tertentu dapat menyebabkan masalah. Digambarkan adalah laporan "Waktu Henti oleh Mesin" dari MachineMetrics..
Mengoptimalkan Proses Toko Anda dengan MachineMetrics
Dengan menggunakan Platform Data Industri MachineMetrics, produsen dapat mengoptimalkan proses mereka tidak seperti sebelumnya. Pengoptimalan ini dicapai dengan berbagai cara:
Waktu Henti Mesin Pelacakan Secara Akurat dan Waktu Nyata
Pelacakan manual data secara inheren cacat. Meskipun dimaksudkan dengan baik, pelacakan kertas dapat rawan kesalahan dan dapat meningkat mempertaruhkan. Ini juga menantang untuk mengikuti, dan kesenjangan dan data yang hilang adalah hal biasa. Selain itu, kemungkinan data akan dibulatkan dan, oleh karena itu, akan jauh lebih tidak akurat.
Pelacakan manual sering kali memerlukan entri data ke Excel atau spreadsheet lain untuk memahami data tersebut, artinya data tersebut sudah usang pada saat sampai di tangan mereka yang membutuhkannya. Tetapi kedalaman analisis itu terbatas. Dan interpretasi manusia bisa menjadi bias.
Dengan MachineMetrics, operator, manajer, dan pemangku kepentingan utama lainnya memiliki visibilitas langsung dengan data alat berat yang akurat dan real-time. Karena data dalam waktu nyata, mereka memiliki akses ujung jari melalui tablet dari jarak jauh atau dasbor di mesin dan di atas lantai bengkel untuk memahami penyebab sebenarnya dari kegagalan.
Dasbor dan laporannya intuitif, memberikan wawasan cepat tentang penyebab waktu henti dan memberikan solusi cepat untuk tindakan dan menurunkan biaya pengoperasian.
Mengaktifkan Alur Kerja dan Notifikasi Berdasarkan Peristiwa Mesin
Dengan perangkat lunak MachineMetrics, data mesin dapat digunakan untuk memicu alur kerja. Alat canggih ini memastikan bahwa informasi yang benar dikirim ke orang yang tepat atau sistem otomatis untuk diimplementasikan tindakan. Tindakan ini berupa insiden, notifikasi, tautan bermanfaat, atau webhook, dan masing-masing dapat mengoptimalkan proses dengan mengaktifkan tindakan cepat saat masalah muncul.
Bacaan lebih lanjut: 10 Alur Kerja Teratas untuk Produsen
Sebuah insiden dapat memicu email atau pemberitahuan teks ke orang yang tepat. Di masa lalu, operator perlu mengandalkan isyarat visual, telepon, sistem PA, atau metode komunikasi lain untuk memberi tahu orang lain tentang suatu masalah. Seringkali, risikonya adalah bahwa orang yang diberitahu adalah orang yang salah untuk tugas itu. Dalam banyak kasus , operator mungkin tidak tahu apa masalahnya. Dengan insiden, masalah yang benar dilaporkan menghemat waktu untuk memulai ulang atau memperbaiki.
Pemberitahuan memungkinkan komunikasi segera, menghemat waktu dan mengurangi jumlah langkah untuk mengidentifikasi dan memecahkan masalah. Jika supervisor mengetahui pesan yang menunjukkan kurangnya bahan baku, mereka dapat melewati perjalanan ke mesin dan langsung melanjutkan ke proses yang macet di hulu.
Webhook mengambil tingkat tindakan lebih jauh. Paket data kecil ini dapat digunakan untuk memicu tindakan perbaikan oleh mesin itu sendiri. Atau mereka dapat digunakan bersama dengan sistem manajemen pemeliharaan terkomputerisasi (CMMS) untuk memberi tahu tim pemeliharaan secara otomatis, memeriksa stok suku cadang dan memesannya kepada teknisi, meningkatkan integritas sistem dan mempercepat waktu perbaikan dan restart.
Meningkatkan Perawatan dengan Kondisi Mesin
MachineMetrics dapat memberdayakan produsen untuk memanfaatkan kondisi alat berat yang akurat untuk mengembangkan program perawatan berbasis kondisi, prediktif, atau preskriptif. Kesehatan peralatan dapat dinilai kapan saja, dan operator serta manajer dapat menghemat waktu dan biaya perawatan dengan meninggalkan program perawatan reaktif.
Hasilnya adalah Overall Equipment Effectiveness (OEE) yang jauh lebih baik yang mengurangi waktu henti dan membantu meningkatkan proses dengan menambahkan strategi pemeliharaan yang dirancang secara strategis ke dalam aliran nilai. Data ini kemudian ditambahkan ke analitik untuk memungkinkan pengoptimalan yang lebih tepat dari semua area manufaktur dan membangun kepercayaan pada integritas sistem.
MachineMetrics memungkinkan produsen memanfaatkan kekuatan data di tingkat mesin dan pabrik. Dengan rangkaian perangkat Edge yang canggih yang dipadukan dengan platform data berkemampuan AI, MachineMetrics dapat menyediakan aplikasi atau membantu Anda membangun aplikasi dan model Anda sendiri untuk mendorong wawasan yang efisien dan dapat ditindaklanjuti berdasarkan data dan kondisi waktu nyata untuk mengoptimalkan proses di lingkungan apa pun. Hubungi kami hari ini jadi kami dapat menunjukkan cara mendapatkan hasil maksimal dari data Anda.
Optimalkan Proses Anda dengan MachineMetrics
Pesan Demo Hari Ini