Bagaimana Melakukan Analisis Kapasitas Manufaktur
Produsen menghadapi segunung tantangan untuk menghasilkan barang yang kita gunakan dalam hidup kita. Dan masing-masing harus mengatasi tantangan ini dengan sumber daya yang terbatas dalam bentuk modal, keterampilan, kemajuan teknologi, dan banyak lagi. Manajer yang mengatur arena kompleks ini mencari cara terbaik untuk memaksimalkan alat yang mereka miliki dengan memahami kapasitas toko mereka. Penggunaan ruang manufaktur yang lebih baik, material, tenaga kerja, dan kinerja peralatan yang dioptimalkan sangat penting bagi perusahaan untuk mendorong produksi yang efisien dan meraih profitabilitas tertinggi.
Analisis kapasitas dapat menjadi solusi yang sangat baik untuk mengaudit pabrik manufaktur dan mendiagnosis jika ada kapasitas tersembunyi yang menunggu untuk dibuka.
Apa itu Kapasitas Manufaktur?
Tujuan setiap pabrikan adalah menjalankan operasinya dengan kapasitas penuh. Tapi apa itu kapasitas produksi? Jawaban singkatnya adalah bahwa kapasitas produksi mewakili keadaan di mana semua peralatan dan sumber daya dalam perusahaan digunakan pada tingkat operasi tertinggi untuk bauran produk dan volume yang dibutuhkan industri mereka. Ini berarti bahwa semua proses mulai dari operasi hingga pemeliharaan dioptimalkan dengan sejumlah sumber daya dan tidak ada waktu henti yang tidak perlu. Ketika kondisi ini tercapai, peralatan telah mencapai kapasitas penuh.
Banyak faktor yang semakin memperumit perjalanan menuju keadaan ideal ini. Sebuah pabrik mungkin mengalami kerugian ketersediaan seperti kegagalan mekanis di mana waktu yang berharga hilang untuk perbaikan. Atau mereka dapat kehilangan kapasitas produksi yang berharga karena pergantian, penyiapan, dan penyesuaian.
Kapasitas produksi juga dapat mengalami kerugian kinerja. Ini termasuk tindakan operator yang tidak terlatih atau tidak berpengalaman dan berhenti untuk kemacetan, pemalasan, runout. Ini sering ditangani dengan tergesa-gesa dengan sedikit analisis tentang apa yang menyebabkannya dan bagaimana mencegahnya terjadi lagi.
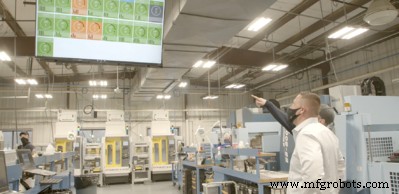
Akhirnya, kapasitas produksi dapat dipengaruhi secara negatif oleh kehilangan kualitas, termasuk cacat proses dan pengurangan hasil. Beberapa penyebab termasuk alur kerja yang kurang dioptimalkan, kesalahan manusia, atau proses yang rusak. Selain merampas kapasitas pabrik yang berharga, penurunan kualitas juga dapat menghasilkan limbah tambahan yang mungkin perlu dikerjakan ulang atau dibuang, sehingga menambah biaya pada produk.
Hambatan kapasitas ini sering disebut sebagai Enam Kerugian Besar. Dan efeknya bisa sangat menghancurkan. Paling-paling, kurangnya pemahaman tentang kapasitas dapat memicu lembur yang mahal, pemborosan, pengiriman yang terlewat, atau pengeluaran modal yang tidak perlu dalam bentuk peralatan baru untuk menebus kerugian.
Apa itu Analisis Kapasitas?
Ketika pabrikan perlu meningkatkan kapasitas, mereka sering memulai dengan respons spontan di atas. Namun, seseorang hanya dapat membeli begitu banyak mesin dan menjadwalkan begitu banyak shift sebelum fokus pada peningkatan kapasitas bergerak ke dalam. Dan cara terbaik untuk menunjukkan dengan tepat di mana tindakan yang harus diambil untuk meningkatkan kapasitas ada di data.
Proses analisis kapasitas adalah perbedaan antara kapasitas potensial dan output aktual yang dicapai perusahaan saat ini. Dengan mengumpulkan data produksi, produsen dapat mengidentifikasi proses, peralatan, atau fungsi apa yang perlu diubah untuk meningkatkan kapasitas. Ini pada dasarnya akan memungkinkan produsen untuk mendorong pemanfaatan yang lebih besar dari sumber daya yang ada melalui pengoptimalan proses.
Bacaan lebih lanjut:Cara Meningkatkan Kapasitas Produksi Manufaktur
Cara Melakukan Analisis Kapasitas Manufaktur
Perusahaan yang melakukan analisis kapasitas produksi dapat mengurangi waktu henti dan pemborosan. Mereka juga dapat menambang data untuk mengoptimalkan proses dan merampingkan alur kerja. Melakukannya dapat membantu mereka memahami apa kendala yang ada dan membuat keputusan waktu nyata untuk memecahkan masalah saat itu terjadi. Karena data mendukung solusi ini, manajer dapat mendorong peningkatan di seluruh operasi dan meningkatkan kapasitas tanpa investasi tambahan dalam peralatan atau tenaga kerja. Bagi perusahaan yang ingin meningkatkan kapasitas produksinya, berikut adalah langkah-langkah yang diperlukan untuk membuka kapasitas yang ada:
Data Tolok Ukur
Jika Anda tidak tahu di mana Anda berada, Anda tidak akan melihat ke mana Anda menuju. Adalah umum untuk melebih-lebihkan pemanfaatan peralatan saat ini karena banyak perusahaan bahkan mungkin tidak menyadari bahwa pemanfaatannya serendah itu.
Benchmarking meliputi penentuan kapasitas yang ada. Kecepatan alat berat, penurunan kualitas, waktu henti berdasarkan kategori – seperti kerusakan, pergantian, dan penurunan kinerja – semuanya harus diukur untuk menentukan kapasitas saat ini. Dan dalam banyak kasus, angka itu mengejutkan. Beberapa praktik terbaik dapat digunakan untuk membuat kerangka kerja yang solid dan praktis untuk benchmarking:
- Rapat Internal:Rapat awal internal membantu menetapkan harapan dan memastikan bahwa semua orang setuju. Dengan menyatukan tim yang tepat, semua orang akan mengetahui tujuan pemanfaatan yang seharusnya.
- Memeriksa Data:Ada kalanya data terkini yang dilaporkan tidak banyak menjelaskan tentang status mesin yang sebenarnya. Mungkin salah merekam status, atau mungkin jumlah bagian, waktu henti, atau parameter lainnya. Memastikan data benar akan membantu dalam menganalisis apa yang perlu dilakukan.
- Mengevaluasi Data:Di sinilah asumsi awal dibandingkan dengan pemanfaatan aktual saat ini. Ini mewakili titik peluncuran baru tentang peningkatan apa yang dapat dilakukan.
- Perencanaan:Dengan membuat rencana peningkatan, manajer dapat menyatukan bagian-bagian dari ekspektasi awal, status kapasitas aktual berdasarkan data, dan peningkatan apa yang dapat dilakukan.
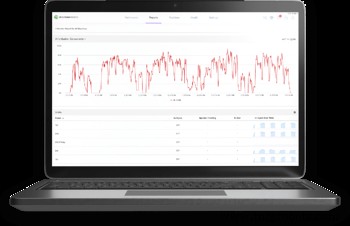
Contoh laporan penggunaan MachineMetrics, salah satu dari banyak laporan bawaan yang dapat digunakan untuk membandingkan data.
Menganalisis Waktu Henti
Setelah operasi manufaktur membandingkan datanya dan memahami pemanfaatannya yang sebenarnya, analisis waktu henti harus dilakukan. Ini melibatkan manajer, teknisi, insinyur manufaktur, operator, dan pihak lain yang dapat membantu mengidentifikasi semua alasan waktu henti dan merencanakan cara mengurangi atau menghilangkannya.
Dengan pengungkapan yang menyertai benchmarking fasilitas, anggota tim dapat melanjutkan untuk mengukur downtime yang mendorong pemanfaatan tersebut. Dengan menjawab berapa banyak downtime yang terjadi dan apa kategori downtime tersebut, langkah-langkah perbaikan menjadi lebih jelas. Hal ini paling baik dilakukan oleh perangkat lunak pengumpulan data mesin otomatis untuk memastikan bahwa data yang akurat digunakan dan distandarisasi serta waktu nyata.
Downtime juga harus mengkategorikan alasan downtime. Kategori yang perlu dipertimbangkan mungkin termasuk:
- Waktu Henti yang Direncanakan vs. Tidak Direncanakan:Masing-masing membuat mesin tidak dapat digunakan, tetapi keduanya memiliki pendekatan yang sangat berbeda untuk meminimalkan kejadian dan membuat mesin kembali online.
- Kesalahan Manusia atau Tindakan Operator:Dalam lingkungan manufaktur yang besar dan kompleks, operator mungkin memiliki tingkat pelatihan yang berbeda atau dapat melakukan tugas atau tindakan dalam urutan yang mengurangi efisiensi. Ini sering kali dapat terlihat dan menjadi tren melalui analisis waktu henti.
- Kejatuhan Kualitas:Kualitas adalah kategori luas yang harus disertakan dalam analisis waktu henti. Ini dapat menghasilkan wawasan tentang pelatihan, status mesin, dan pemeliharaan, kualitas vendor masuk, atau bahkan kondisi sekitar dalam fasilitas antara hari yang lebih hangat dan malam yang lebih dingin.
Setelah kategori ditentukan, anggota tim dapat menelusuri untuk menentukan alasan waktu henti dalam kategori. Misalnya, mungkin ada banyak jenis waktu henti yang direncanakan, termasuk pemeliharaan terjadwal, produksi musiman, dan lainnya.
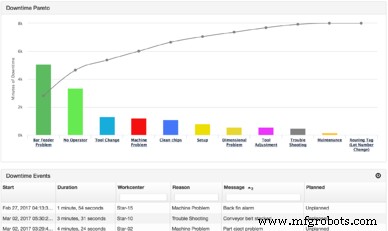
Pareto Waktu Henti MachineMetrics mengungkapkan alasan waktu henti yang paling parah dan merupakan titik awal yang bagus untuk menemukan proses yang harus diperbaiki.
Demikian juga, ada banyak alasan untuk downtime yang tidak direncanakan. Ini dapat berkisar dari bahan yang tidak ada di mesin saat dibutuhkan hingga mesin yang tidak dirawat dengan baik. Ini mungkin juga menunjukkan alur kerja yang dirancang secara salah di mana material dari hulu tidak siap saat dibutuhkan, menciptakan efek domino.
Hal yang sama berlaku untuk kesalahan manusia. Operasi manufaktur menjadi lebih otomatis, tetapi masih ada kebutuhan tenaga kerja. Kelelahan, pelatihan yang tidak memadai, kurangnya pemahaman tentang alur kerja, atau langkah-langkah proses yang rusak dapat menyebabkan pekerja melakukan kesalahan yang seharusnya tidak mereka lakukan.
Cara terbaik untuk mengumpulkan informasi ini adalah melalui otomatisasi dan perangkat lunak. Dengan membuat visualisasi data intuitif dan mudah direkam, operator dapat memanfaatkan dasbor untuk memasukkan data aktual dan melihat dampaknya. Sama seperti operator yang dapat memasukkan alasan waktu henti, alat seperti grafik Pareto dapat membantu memahami analisis waktu henti saat bergerak maju. Hal ini memberikan wawasan kepada pengguna dan sering kali membantu memicu saran peningkatan.
Pada akhir analisis downtime, biaya downtime aktual dan dampaknya terhadap bottom line dapat ditentukan. Ini juga membantu mengidentifikasi “buah yang menggantung rendah”, item tercepat dan termudah untuk diperbaiki dengan dampak paling signifikan pada penghematan dolar dan penambahan kapasitas.
Bacaan lebih lanjut:Cara Melacak dan Menganalisis Waktu Henti Mesin
Perubahan Proses Peluncuran
Manajer sekarang dilengkapi dengan data yang akurat dan dapat diverifikasi yang mendorong perubahan nyata pada titik ini dalam analisis kapasitas. Perubahan ini dapat digunakan untuk mengatasi kendala kapasitas yang paling signifikan, membuka kunci kapasitas tersembunyi untuk menghilangkan lembur, mengurangi kebutuhan belanja modal, dan mengasah program pemeliharaan yang selaras dengan pergantian dan kondisi operasi lain alih-alih berdebat dengannya.
Ada banyak contoh pengurasan kapasitas yang signifikan. Berikut adalah beberapa yang dapat ditemukan selama sebagian besar transformasi digital:
Waktu Siklus yang Diharapkan Lebih Lama dari Waktu Siklus Sebenarnya
Ukuran dan kompleksitas lingkungan manufaktur saat ini dapat berarti bahwa kinerja individu terkubur di bawah segunung data, volume, dan dorongan untuk produksi yang lebih tinggi. Ketika data benar, dan jumlah suku cadang pada alat berat akurat, operator bertanggung jawab atas output mereka alih-alih terkubur di bawahnya. Akuntabilitas ini dapat menjadi alat positif yang memungkinkan mereka menjadi bagian dari mengidentifikasi area untuk perbaikan. Saat perbaikan pada waktu henti yang paling nyata mulai bekerja, pengoptimalan waktu siklus lebih lanjut dapat dimulai untuk melanjutkan proses untuk memasukkan perubahan kecil sekalipun yang bertambah dengan cepat.
Masalah Kualitas
Seperti disebutkan sebelumnya, kualitas adalah topik luas yang berdampak pada banyak bidang. Tapi itu memberi lebih banyak kesempatan untuk perbaikan. Aturan 80/20 tidak hanya berlaku untuk kualitas, tetapi juga memengaruhi subkategori di dalamnya, termasuk kesalahan/pelatihan manusia, kualitas vendor, peningkatan pemeliharaan, desain produk, dll. pelakunya di setiap area dapat berada di bawah langkah-langkah perbaikan untuk memberikan dampak kumulatif yang lebih besar pada kualitas secara keseluruhan. Saat upaya ini berakar, kapasitas meningkat, kualitas meningkat, mengurangi biaya, dan meningkatkan kinerja pesanan dan pengiriman.
Bacaan lebih lanjut:Jaminan Kualitas dalam Manufaktur:Semua yang Perlu Anda Ketahui
Dengan MachineMetrics, Anda dapat dengan mudah melihat alasan utama mengapa suku cadang ditolak dan mengidentifikasi akar masalahnya.
Kegagalan Peralatan
Beberapa hal membuat manajer manufaktur marah sebanyak kegagalan peralatan. Dan seringkali, kegagalan ini adalah hasil dari program pemeliharaan reaktif. Dengan berlari ke kegagalan atau dengan pelacakan kondisi mesin yang tidak memadai, perusahaan menyerahkan sebagian besar kapasitas dalam bentuk waktu henti. Namun analitik data dan kondisi mesin waktu nyata menawarkan peluang baru untuk meningkatkan kapasitas. Dengan memahami status mesin dan menerapkan sensor dan teknologi IIoT, manajer dapat meninggalkan pemeliharaan reaktif dan mendorong kapasitas yang lebih tinggi dan biaya yang lebih rendah. Satu studi oleh Deloitte menunjukkan bahwa program pemeliharaan prediktif dapat meningkatkan waktu kerja peralatan sebesar 10-20%.
Alur kerja
Mengukur pemanfaatan peralatan lebih dari sekadar mengukur mesin saja. Dengan menangkap, mengontekstualisasikan, dan menganalisis data, manajer dapat melihat mesin individual dan seluruh ekosistem peralatan di dalam fasilitas. Hal ini dapat memberikan wawasan tentang tata letak peralatan, staging, WIP, dan variabel terkait proses lainnya yang dapat digunakan untuk meningkatkan kapasitas. Meskipun mungkin menunjukkan kebutuhan untuk mengatur ulang lantai atau sel produksi, mungkin juga sesederhana memindahkan beberapa mesin beberapa kaki atau mengubah cara material mengalir dari satu stasiun ke stasiun berikutnya dalam alur kerja yang membuat perbedaan.
Membuka Kapasitas Tersembunyi
Analisis kapasitas yang digabungkan dengan pengambilan data dan analitik tingkat lanjut dapat membantu perusahaan menemukan jalur mereka menuju kapasitas penuh lebih cepat daripada yang diperkirakan kebanyakan orang, dan menghasilkan produksi yang merata. Ketika Avalign Technologies berjuang untuk melacak OEE dan waktu henti, kemacetan produksi, SOP yang tidak memadai, dan faktor lainnya menghambat kapasitas.
Menggunakan MachineMetrics, Avalign memperoleh visibilitas instan di seluruh lantai toko untuk mewujudkan peningkatan OEE 25-30% dan jutaan kapasitas tambahan, tanpa penambahan tenaga kerja, peralatan, atau sumber daya tambahan.
Tonton video studi kasusnya: