Analisis Akar Penyebab:Panduan Lengkap untuk Produsen
Menemukan Sumber Masalah di Lantai Toko
Manufaktur bisa menjadi usaha yang kacau, serba cepat, dan kompleks, memaksa produsen untuk tidak hanya mengidentifikasi tetapi juga memecahkan tantangan unik. Masalah-masalah ini dapat memperlambat produksi, menciptakan kemacetan atau penghentian pada saat yang paling tidak diharapkan. Ketika masalah seperti itu muncul, banyak yang beralih ke analisis akar penyebab (RCA) untuk membantu mengimplementasikan solusi.
Inilah yang akan kami bahas dalam panduan mendalam tentang mengidentifikasi akar penyebab. Jangan ragu untuk melompat ke bagian tertentu:
- Apa yang dimaksud dengan Analisis Akar Penyebab?
- Manfaat RCA
- Cara Melakukan Analisis Akar Penyebab
- Metode dan Alat yang Tersedia
- Menjelajahi Contoh Analisis Akar Penyebab
Apa yang dimaksud dengan Analisis Akar Penyebab?
Analisis akar penyebab, atau RCA, adalah proses spesifik yang mengenali bahwa gangguan dan masalah dapat ditelusuri ke penyebab tertentu dan bahwa solusi untuk memperbaiki penyebab tersebut akan bergema di rantai dan menghasilkan keadaan yang lebih baik. RCA berupaya mengidentifikasi penyebab cacat dan masalah, bukan sekadar mengobati gejala atau "memadamkan kebakaran".
Manfaat Analisis Akar Penyebab
Analisis akar penyebab diakui sebagai komponen penting dalam metodologi lean manufacturing dan Six Sigma. Ini mengoptimalkan waktu yang dibutuhkan untuk menelusuri penyebab masalah dan menyediakan struktur untuk pemecahan masalah dalam manufaktur.
Manfaat analisis akar penyebab meliputi:
- Penghematan Biaya
- Karena analisis akar penyebab menangani "penyakit" dan bukan gejalanya, analisis ini dapat mengurangi biaya dengan menurunkan waktu henti, mengurangi cacat, dan meningkatkan proses.
- Proses Realistis
- Banyak perusahaan manufaktur beroperasi dengan proses yang rusak sebagian. Analisis akar masalah membantu mengoptimalkan proses untuk memberikan solusi praktis dan menetapkan SOP yang dapat diikuti tanpa mengambil jalan pintas atau menyimpang dari proses.
- Otomatis
- Saat ini, pabrik memiliki akses dan wawasan ke data lebih dari sebelumnya. Data ini dapat diuraikan, dianalisis, dan dikontekstualisasikan untuk membuat analisis akar masalah dapat digunakan oleh departemen dan pabrik lain dalam perusahaan yang sama. Ini bertindak sebagai pengganda kekuatan untuk perbaikan.
- Proaktif
- Karena otomatisasi melalui analisis data sangat cocok untuk hasil analisis akar masalah, masalah keamanan, pemeliharaan, dan kualitas dapat diprediksi lebih akurat dan ditindaklanjuti dengan cepat untuk mengurangi waktu henti.
Cara Melakukan Analisis Akar Penyebab
Pendekatan analisis akar penyebab akan berbeda dari perusahaan ke perusahaan serta dari masalah ke masalah. Ini mungkin membidik pada masalah khusus mesin di seluruh jenis mesin OEM tertentu. Ini juga dapat digunakan untuk analisis kemacetan antar departemen. Atau mungkin digunakan untuk mengatasi cacat pabrik di seluruh perusahaan.
Secara umum, ada enam langkah yang terlibat dalam analisis akar penyebab:
1. Mendefinisikan Masalah
Langkah pertama adalah yang paling kritis. Semua anggota tim harus memahami masalah ini. Itu harus dinyatakan secara objektif. Dan itu membutuhkan pertanyaan klarifikasi untuk menentukan bahwa itu memang masalah atau hambatan yang mendesak. Ini adalah tahap terluas dan merupakan pernyataan masalah umum seperti tingkat kerusakan, kemacetan, atau pengiriman yang terlewat.
2. Mengumpulkan Data
Pengumpulan data sangat penting dalam analisis akar penyebab. Di sini, anggota tim berusaha membuat daftar sebanyak mungkin elemen penyebab. Semuanya ada di atas meja, dan daftarnya bisa luas dan terperinci. Saat ini, lebih mudah untuk menemukan dan memanfaatkan data dalam analisis akar masalah karena banyak produsen peralatan OEM menanamkan pengumpulan data di mesin mereka. Mungkin juga sebuah pabrik telah menyebarkan perangkat pengumpulan data untuk mesin-mesin yang tidak memuatnya secara asli.
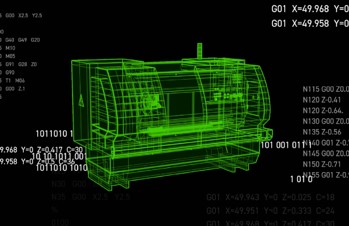
3. Memisahkan Penyebab dari Gejala
Adalah umum untuk mengacaukan gejala sebagai penyebab. Beberapa alat dan metode dapat membantu dalam menelusuri untuk memisahkan gejala dari penyebabnya. Asumsinya adalah jika penyebabnya dapat ditentukan dan diperbaiki, gejalanya akan hilang. Di sini, pengumpulan data juga penting karena banyak sistem pengumpulan data memiliki analisis yang mampu menentukan kategori masalah.
4. Menentukan Tindakan Korektif
Setelah akar penyebab ditentukan, solusi yang efektif dapat dibuat. Ini mungkin termasuk pelatihan, modifikasi mekanis, tata letak lantai, atau pengumpulan data yang lebih kuat dan kemampuan analitis. Seringkali, data dapat membantu dalam menyusun tindakan korektif. Dengan memiliki data dan wawasan real-time saat akar permasalahan ditentukan, manajer dapat membuat solusi dunia nyata yang relevan berdasarkan data aktual.
5. Menerapkan Solusi
Setelah akar penyebab ditetapkan, dan tindakan korektif diidentifikasi, tim harus menerapkan solusi. Ini berarti merevisi atau mengganti SOP lama, membuat alur kerja baru, dan mengaudit hasilnya. Semakin dalam kemampuan pengumpulan data, semakin besar dampak analisis terhadap solusi yang dipilih. Bahkan dimungkinkan untuk memprogram tindakan otonom atau semi-otonom oleh mesin untuk membantu mengimplementasikan atau memantau kemajuan solusi atau memengaruhi pertumbuhannya.
6. Memvalidasi dan Memperluas Hasil
Tidak ada solusi yang bertahan lama tanpa proses audit. Bagian audit ini harus memvalidasi efektivitas solusi. Ini dibuat lebih mudah diakses ketika pengumpulan data kuat dan tunduk pada analisis waktu nyata. Dengan demikian, validitas solusi dapat dipantau atau disesuaikan untuk meningkatkan efektivitas. Dan jika jawabannya berhasil, akar masalahnya dapat dialihkan ke proses dan departemen lain di dalam perusahaan.
Analisis akar penyebab dapat dilakukan oleh tim secara manual. Tetapi ketika dikombinasikan dengan pengumpulan dan analisis data tingkat lanjut, hal itu mempercepat dan meningkatkan dampaknya. Solusi dapat diluncurkan ke pabrik lain dan departemen lain yang mengalami masalah serupa, serta dapat meningkatkan efisiensi produksi dan mengurangi cacat produksi.
Metode dan Alat Analisis Akar Penyebab
Untuk perusahaan yang melakukan analisis akar penyebab, ada banyak alat dan metodologi yang tersedia untuk digunakan. Kami memberikan gambaran singkat tentang banyak dari strategi ini di bawah ini:
Lima Mengapa
Salah satu alat analisis akar penyebab yang paling mudah juga merupakan salah satu yang paling efektif. Cukup menanyakan "mengapa" lima kali dapat membantu menelusuri penyebabnya. Ini memaksa pemikiran yang lebih dalam dan lebih kritis sampai semua alasan telah habis. Secara realistis, mungkin diperlukan sedikit lebih atau kurang dari lima, tetapi metodologinya adalah bahwa jawaban akhir dapat diungkapkan dengan menanyakan mengapa sampai semua solusi diadopsi.
Diagram Tulang Ikan
Diagram tulang ikan, juga dikenal sebagai diagram Ishikawa, adalah diagram sebab dan akibat visual yang membantu membangun penyebab dari semua faktor yang berkontribusi. Masalahnya dianggap sebagai "kepala" ikan. Penyebab dikategorikan sebagai tulang yang lebih kecil di bawah daftar kategori penyebab. Aspek visual membantu tim menilai opsi yang mungkin tidak terjadi dalam pemikiran abstrak saja.
Sumber gambar
Mode Kegagalan dan Analisis Efek
Untuk produk dengan kompleksitas tinggi yang kinerja lanjutannya sangat penting, mode kegagalan dan analisis efek (FMEA) adalah pilihan untuk menentukan akar penyebab. Metode ini melihat area di mana kegagalan desain dapat terjadi. Dalam banyak hal, ia mencari akar penyebab cacat dan kegagalan sebelum terjadi. Ini dapat membantu dalam menentukan kegagalan proses untuk perakitan atau manufaktur.
Analisis Pohon Kesalahan
Untuk analisis akar penyebab dalam sistem keamanan kritis di mana cacat teknik dapat menyebabkan efek yang merugikan, analisis pohon kesalahan (FTA) adalah alat analisis akar penyebab yang efektif. Ini membantu memahami bagaimana kegagalan sistem dapat terjadi dan kegagalan apa yang mungkin terjadi. "Keadaan yang tidak diinginkan" ini kemudian ditetapkan ke peristiwa kegagalan tingkat rendah di pohon yang membantu mengidentifikasi kemungkinan kegagalan dan memungkinkan para insinyur merancang untuk mengkompensasi atau menghilangkan risiko kegagalan.
Bagan Pareto
Bagan Pareto adalah metode visualisasi lain yang telah dicoba dan benar yang membantu tim memahami frekuensi masalah dalam analisis akar masalah. Ini "memperingkat" masalah secara visual untuk membantu tim mengetahui apa yang harus mereka tangani terlebih dahulu. Bagan pareto juga berharga bila ada banyak penyebab yang berbeda.
Dengan mendaftar mereka dalam urutan kepentingan, solusi dapat dibuat terlebih dahulu untuk menghilangkan cacat yang paling signifikan. Analisis akar penyebab, sering kali merupakan bagian dari metodologi lean atau six sigma, kemudian dapat diulang untuk mengatasi beberapa level berikut pada bagan untuk melanjutkan perbaikan melewati fase awal.
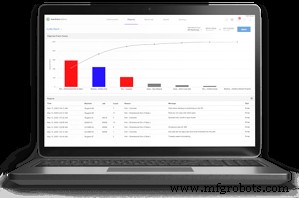
Bagan pareto memudahkan untuk menentukan 20% masalah yang menyebabkan 80% masalah.
Apakah/Bukan Analisis
Dikatakan bahwa separuh hidup adalah mengetahui apa yang tidak boleh dilakukan. Seperti lima mengapa, Analisis Is/Is Not sederhana namun kuat. Dengan membagi masalah secara visual menjadi kategori "adalah" dan "bukan", tim analisis akar masalah dapat membuat daftar fokus yang membantu mereka memahami kondisi apa yang memengaruhi situasi dan mana yang tidak. Itu membuat tim tetap pada jalurnya dan mencegah mereka mendaftar atau mengejar tujuan yang salah.
Menjelajahi Contoh Analisis Akar Penyebab dengan MachineMetrics
Menemukan akar penyebab masalah membutuhkan tim yang berdedikasi dan kerja keras. Dan semakin manual usaha, semakin banyak waktu yang dibutuhkan untuk proses modifikasi. Namun, tim pengoptimalan proses saat ini memiliki sekutu dalam perjuangan untuk menentukan akar penyebab.
Pengumpulan data dengan cepat menjadi standar di lingkungan manufaktur saat ini. Perangkat pengumpulan data yang canggih, perangkat lunak, dan program analitik menggantikan spreadsheet, bagan yang dibuat secara manual, dan sistem input berbasis manusia yang digunakan untuk analisis akar masalah.
Dengan platform seperti MachineMetrics, perusahaan kini dapat memanfaatkan pengumpulan data otomatis real-time serta analitik lanjutan untuk membuat data yang dapat digunakan, distandarisasi, dan dikontekstualisasikan bagi mereka yang mencari akar penyebab masalah. Data yang dikumpulkan langsung dari kontrol mesin ini berarti bahwa akurasi dan akar penyebab yang tidak bias dapat ditentukan lebih cepat dan lebih efektif daripada proses manual.
Mari kita jelajahi beberapa contoh bagaimana MachineMetrics dapat digunakan untuk mengidentifikasi penyebab masalah di lantai toko Anda:
RCA dalam Waktu Nyata:Dasbor Pergeseran Saat Ini
Dasbor shift saat ini adalah solusi yang bagus untuk memantau kemajuan produksi secara real-time. Ini memberikan visibilitas kinerja ke sasaran sehingga operator dapat membandingkan kinerja yang diharapkan dan yang sebenarnya. Dengan cara ini, Anda dapat memberdayakan operator dan manajer untuk mengidentifikasi masalah dengan cepat.
Ini adalah strategi jangka pendek dan waktu nyata yang bagus untuk mengatasi masalah sehari-hari, sebelum analisis yang lebih mendalam dapat diselesaikan.
Ada beberapa tampilan yang dapat digunakan untuk dasbor shift saat ini, termasuk sasaran bagian, OEE, penggunaan, dan waktu henti.
Pelanggan kami biasanya memasang monitor di seluruh lantai toko sehingga semua pemangku kepentingan memiliki visibilitas lengkap di semua mesin yang berlaku.
Identifikasi Penyebab Utama Henti dengan Laporan Pareto
Salah satu laporan yang paling berguna untuk memahami alasan waktu henti adalah Pareto Waktu Henti, yang akan menggabungkan semua alasan waktu henti yang dicatat.
Dengan laporan ini, Anda dapat dengan mudah mengidentifikasi alasan waktu henti yang paling parah. Selanjutnya, Anda dapat mengelompokkan data di antara shift yang berbeda, sel mesin, atau bahkan mesin individual untuk melihat lebih detail di mana masalah mungkin terjadi. Selanjutnya, Anda dapat melihat di mana waktu henti yang tidak direncanakan terjadi versus waktu henti yang direncanakan.
Kategori umum waktu henti meliputi pergantian alat yang berlebihan, pergantian pekerjaan yang berlebihan, kurangnya operator, dan perawatan alat berat yang tidak direncanakan. Dengan MachineMetrics, Anda tidak hanya akan memiliki tampilan waktu henti yang akurat, tetapi Anda juga dapat menentukan di mana letak masalah Anda.
Pareto Waktu Henti MachineMetrics memvisualisasikan alasan utama waktu henti di lantai toko.
Menganalisis Laporan Produksi untuk Mengidentifikasi Inefisiensi Produksi
Ada banyak metrik yang tersedia di Laporan Produksi MachineMetrics. Manajer perbaikan berkelanjutan, supervisor lantai toko, dan insinyur dapat menganalisis laporan produksi untuk lebih memahami kinerja pabrik. Dalam hal mengoptimalkan efisiensi Anda, ada beberapa metrik efisiensi produksi dan waktu pelaksanaan pekerjaan yang ingin Anda pastikan ada dalam laporan:
Efisiensi Produksi
Metrik yang tersedia dalam Laporan Produksi terkait dengan efisiensi produksi mesin untuk Pekerjaan yang diselesaikan meliputi:
- Efisiensi Produksi
- Total Paruh Waktu
- Paruh Waktu Sebenarnya
- Rata-rata PPH
- PPH Ideal
- PPH yang diharapkan
- Perkiraan Paruh Waktu
- Paruh Waktu Ideal
- Penyiapan Total
- Penyiapan yang Diharapkan
Waktu Pelaksanaan Pekerjaan
Metrik yang tersedia di Laporan Produksi terkait dengan waktu pengoperasian mesin untuk Pekerjaan yang diselesaikan meliputi:
- Waktu Mulai Pertama
- Waktu Berakhir Terakhir
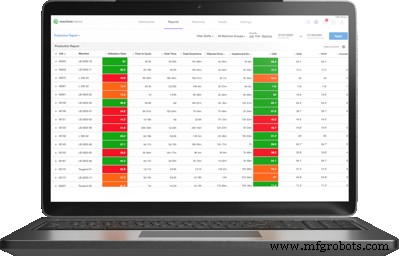
Laporan Produksi diisi dengan informasi tentang seberapa efisien bagian dan pekerjaan diselesaikan.
Mulai Identifikasi Inefisiensi Hari Ini
Dengan MachineMetrics, data lantai toko secara otomatis dikumpulkan secara real-time, dan distandarisasi untuk menyebarkan laporan dan visualisasi out-of-the-box (dan kustom). Kembalikan kekuasaan ke tangan pembuat keputusan dengan data akurat yang menjelaskan secara tepat apa yang terjadi di lantai produksi, menyediakan visibilitas untuk membuat keputusan yang lebih baik.
Mulai mengidentifikasi inefisiensi dan memperbaiki masalah hari ini. Pesan demo dengan tim kami hari ini untuk membahas bagaimana MachineMetrics dapat mengurangi waktu henti, meningkatkan kapasitas, dan mendorong dampak laba bagi organisasi Anda.
Mulai Identifikasi Masalah Produksi
Pesan Demo